Другие работы

Работа подземных водозаборов и водопонизительных откачек привела к нарушению естественного гидродинамического режима подземных вод. На территории области выделяются три зоны образования воронок депрессии. Самая значительная из них (протяженностью с запада на восток до 35, а севера на юг до 8−10 км) сформировалась в бассейнах pp. Осколец, Чуфичка, Убля. Здесь сосредоточены территории городов…
Диссертация 
Для яровой тритикале показано широкое использование хромосомных замещений и транслокаций с уменьшением доли генетического материала ржи (Zillinsky, 1980; Gustafson, Lukaszewsky, 1984). Замещения и транслокации хромосом позволяют решать проблемы, характерные для яровой тритикале, как показано в отношении признаков хлебопекарных качеств зерна, высоты растений, продолжительности вегетационного…
Диссертация 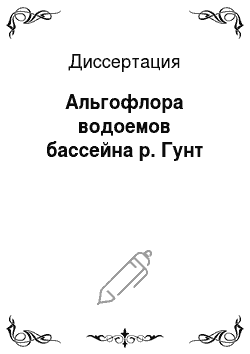
Практическая ценность. Результаты исследования таксономического разнообразия водорослей и экологических особенностей распространения видов в разнотипных водоёмах бассейна р. Гунт могут служить научной основой для разработки мероприятий по устойчивому сохранению и использованию речных экосистем. Основные результаты будут включены в лекционные и практические курсы по альгологии для студентов…
Диссертация 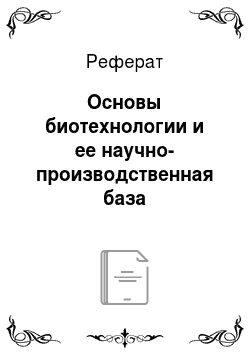
Рост народонаселения на Земле, как и десятилетия назад, опережает прирост производства сельскохозяйственной продукции. Следствие этого — хроническое недоедание, а то, а просто голод среди сотен миллионов людей. Производство удобрений, механизация, традиционная селекция животных и растений — все это составляло основу так называемой «зеленой революции», которая себя не совсем оправдала. В настоящее…
Реферат 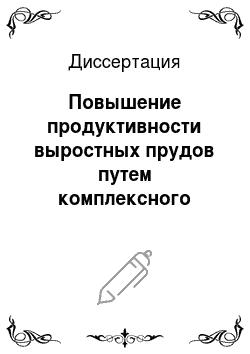
Оценивая результативность выращивания сеголетков в разных вариантах плотности в поликультуре, следует отметить, что наиболее высокие показатели общей рыбопродукции получены при выращивании сеголетков от подрощенной молоди в варианте поликультуры с общей плотностью единовременной посадки 60 тыс. шт./га в соотношении белый амур: толстолобик: карп = 1: 2: 3. В этом варианте очень высокий процент…
Диссертация 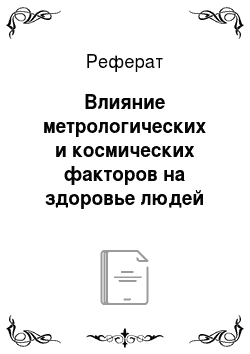
Однако, структура магнитосферы такова, что в разных местах магнитное поле Земли по-разному влияет на воздействие космических факторов, в частности солнечного ветра. Поток солнечных высокоскоростных частиц, выброшенных из атмосферы Солнца после солнечной вспышки, распространяется в межпланетном пространстве наподобие поршня. Через 12−24 часа этот поршень достигает орбиты Земли. Под его давлением…
Реферат 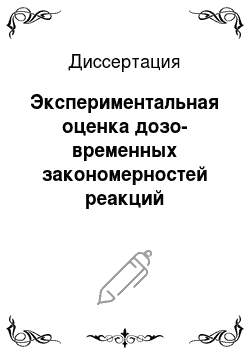
С учётом модифицирующего влияния климатических факторов (температура воздуха, относительная влажность и скорость движения воздуха) нами были произведены экстраполяционные расчёты предельно допустимого времени работы (в случае аварийной ситуации) «условного» человека в зоне воздействия ЭМИ при однократном облучении для разных условий окружающей среды и разного уровня физической нагрузки. Показано…
Диссертация 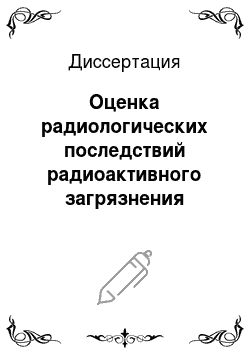
Семипалатинский испытательный полигон расположен на северо-востоке Республики Казахстан на территории трех областей: Восточно-Казахстанской, Павлодарской и Карагандинской. Он являлся основным местом проведения испытаний ядерного оружия и ядерных устройств в бывшем Советском Союзе. В период с 1949 по 1989 годы здесь было проведено 456 испытаний ядерных устройств (Горин В.В., 1993; Дубасов Ю. В…
Диссертация 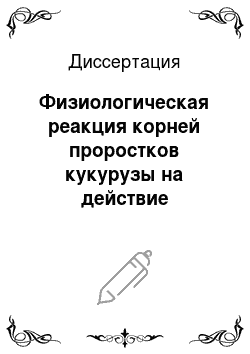
Несмотря на большое количество работ, посвященных изучению влияния гиббереллина на кукурузу, в литературе имеется сравнительно мало работ, освещающих действие ССС на эту кулыуру. Особенно неизучено влияние рассматриваемого регарданга на рост и формирование корневой системы кукурузы. По эеому вопросу встречаются только ОЕдельные работы, в которых отмечается положительное влияние хлорхолинхлоридана…
Диссертация 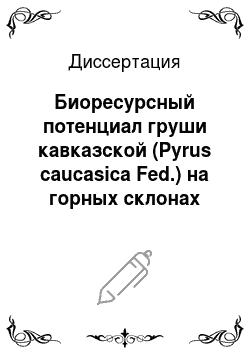
Апробация работы. Результаты исследований апробированы на различных Международных и региональных научно-практических конференциях: конференции, посвященной 120-й годовщине со дня рождения академика Н. И. Вавилова (Саратов 2007), II Международной научно-практической конференции (Саратов ИЦ «Наука» 2008), Всероссийской научной конференции «Актуальные проблемы экологии и сохранения биоразнообразия…
Диссертация 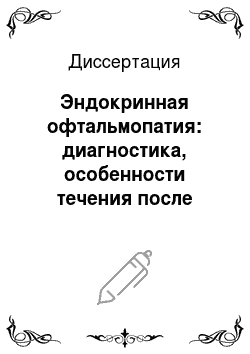
ЭОП противоречивы. Имеются сообщения о том, что в ряде случаев РИТ провоцирует развитие и ухудшает течение ЭОП. Так, например, по данным исследования, проведенного Tallstedt с соавторами, на фоне РЙТ утяжеление ЭОП происходило существенно чаще (33%), чем на фоне терапии тиреостатиками (10%) или после хирургического лечения (16%). В других исследованиях был получен противоположный результат…
Диссертация 
В естественных условиях жизни человек подвергается одновременному воздействию всех групп факторов. Отделы головного мозга, отвечающие за нейродинамику работоспособности формируются у ребенка во внутриутробном периоде, но дозревание продолжается и в процессе развития после рождения. Это обуславливает интерес научной общественности к проблемам динамики работоспособности детей и ее зависимости…
Курсовая 
Игнорируя возрастную периодизацию в онтогенезе человека, исследователи произвольно объединяют детей по паспортному возрасту и приводят основные антропометрические и функциональные показатели, скажем для детей 3−4, 6 -7 лет, объединив их в одну группу. Несомненно, такие работы не приносят новых данных и не несут новой информации о развитии соматических и функциональных показателей, 90-е годы…
Реферат 
В интерфазе клеточного деления ДНК входит в состав особого ядерного вещества — хроматина, в котором также присутствуют белки — основные (гистоны) и неосновные, а также небольшое количество РНК и липидов. Основой структуры хроматина являются нуклеосомы, которые представляют собой белковые диски из 8 молекул гистонов, по окружности которых намотана часть ДНК (140 пар оснований). Нуклеосомы…
Контрольная 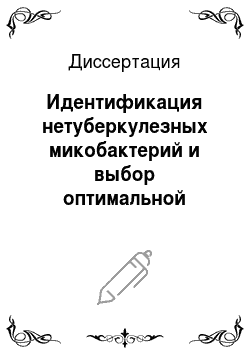
Предложены комплексы методов для идентификации нетуберкулезных микобактерий: 1) ПЦР-секвенирование гена 16S рРНК, 2) рестрикционный анализ амплифицированного фрагмента спейсерной последовательности 16S-23S рибосомной ДНК и 3) высокопроизводительная жидкостная хроматография миколовых кислот (high performance liquid chromatography — HPLC). В случаях генетически близкородственных видов, как…
Диссертация