Другие работы
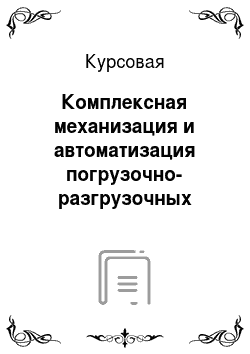
Для перевозки тарно-штучных грузов на поддонах размером 1 200 800 мм на железнодорожном транспорте выбрали четырехосный вагон модели 11−066 тип 204, а на автомобильном транспорте — полуприцеп МАЗ 5204А с металлической платформой, тремя открывающимися бортами и тентом, совместно с автомобилем МАЗ 504 В. Рассчитанная техническая норма загрузки вагона равна 61,2 т, а автомобиля — 18 т. Согласно…
Курсовая 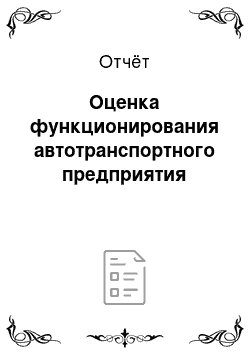
Не все шины хранятся в одинаковом положении: всё зависит от того, отдельно ли кладутся покрышки, или целым колесом (на дисках). В первом случае шины необходимо располагать вертикально (оптимальным является складирование на специальных стеллажах для шин), поворачивая каждые 4 недели по своей оси. Если же резина смонтирована на диски, то вертикальное положение крайне нежелательно; в этом случае…
Отчёт 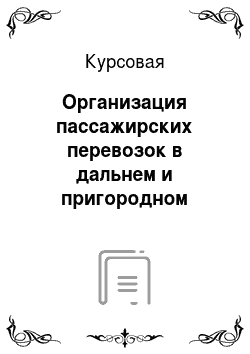
За счет сокращения числа остановок значительно возрастает участковая скорость, что позволяем сократить время проезда пассажиров и ускорить оборот составов. Поэтому при выборе типа графика следует в максимальной степени учитывать как интересы транспорта, так и интересы пассажиров, стремясь, с одной стороны, к сокращению эксплуатационных расходов и улучшению использования технических средств…
Курсовая 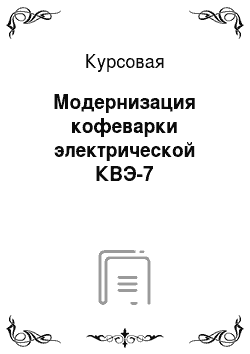
Величина фактической производительности проектируемого объекта является исходным фактором для определения основных кинематических параметров рабочих органов. Обрабатывая продукт (непрерывно и периодически), последние должны иметь определенный закон движения, двигаться с определенной скоростью или частотой вращения. Это необходимо для получения единицы продукта в строго определенный промежуток…
Курсовая 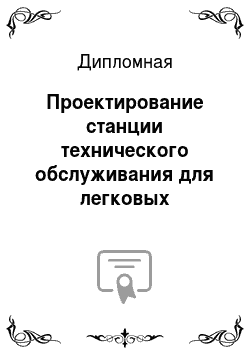
Помещение для ТО и ТР автомобилей и агрегатов обеспечивает безопасное и рациональное выполнение всех технологических операций при соблюдении санитарно-гигиенических условий труда и оборудуется автоматической пожарной сигнализацией; в производственных помещениях пол ровный и прочный, имеет покрытие с гладкой, но не скользкой поверхностью, удобной для очистки. Для работы с аккумуляторами…
Дипломная 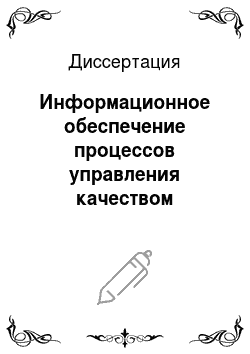
Основой реализации системы управления качеством восстановительных услуг на ремонтном предприятии является информационное обеспечение процессов управления технологическим процессом ремонта. Создание и внедрение системы качества начинается с выработки политики, доведения ее до персонала всех уровней и закрепления ответственности руководства. В соответствии с МС ИСО серии 9000 установлено, что…
Диссертация 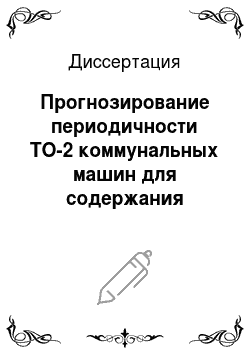
Экспериментально установлено, что при выполнении мероприятий по ТО-2 с предложенной автором периодичностью срок обкатки коммунальных машин для содержания АД уменьшен с 2.5.3.5 лет до 1.2 летпосле восьми лет эксплуатации коммунальных машин для содержания АД следует уменьшить периодичность ТО-2 (увеличить их количество), с целью продлить срок эксплуатации до наступления критического состояния…
Диссертация 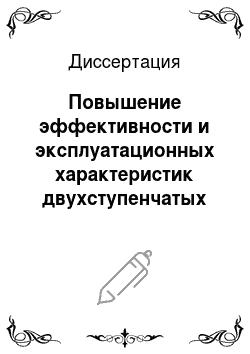
Первые обладают сложностью конструкции и технологии сборки, сравнительно высокой стоимостью, свободными от названных недостатков являются двухступенчатые ЖВН. Дальнейшее усовершенствование существующих конструкций и разработка новых машин в большей степени сдерживается отсутствием в первую очередь уточненной и универсальной методики расчета, определяемой потерями мощности в безлопаточном…
Диссертация 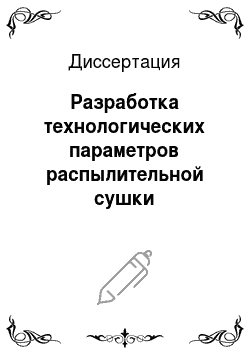
Современная наука о питании рассматривает пищу не только как источник энергии и пластических веществ, но и как сложный натуральный фармакологический комплекс. Это особенно актуально в связи с влиянием на человека загрязненной среды его обитания. Попадая в организм человека, продукты химического и микробиологического синтеза, тяжелые и радиоактивные металлы включаются в метаболические реакции…
Диссертация 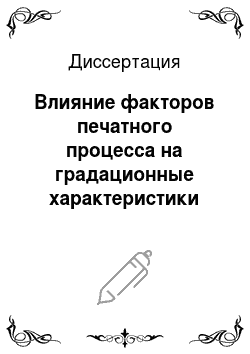
Изучено влияние скорости печатания и вязкости печатной краски, а также их совокупное влияние на краскоперенос. Выяснено, что как вязкость краски, так и скорость печатания при оптимальных условиях растровой печати не оказывают значительного влияния на краскоперенос, однако совокупное влияние этих факторов может быть существенным и, при этом, противоположным описанному в литературе. Основная…
Диссертация 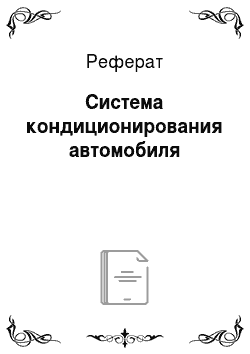
ПРИНЦИП ДЕЙСТВИЯ СИСТЕМЫ КОНДИЦИОНИРОВАНИЯ Кондиционирование воздуха — это рагулирование температуры, влажности, очищение и циркулирование воздуха. Аналогично кондиционирование автомобиля — это не просто искусственное охлаждение воздуха, но и создание комфортности для водителя и пассажиров путем поддержания микроклимата внутри салона, удаления влаги, пыли и загрязненного воздуха. При смазывании…
Реферат 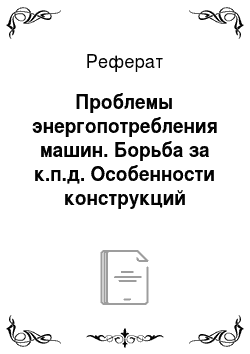
Справ. пособие для втузов/ С. А. Чернавский, Г. А. Слесарев, Б. С. Козинцев и др. — 5-е изд. перераб. и доп. — М.: Машиностроение, 1984. -. В результате можно сделать следующие выводы, о том, что современное развитие конструкций машин занимается решением задач: В результате исследования были решены следующие задачи1) Изучено понятие, структура и конструкция машин. Расширением внедрения…
Реферат 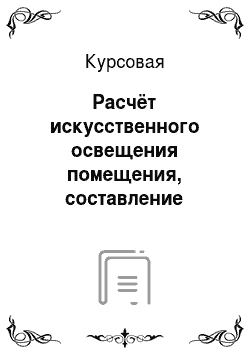
Класс энергетической эффективности здания Обозначение класса Наименование класса энергетической эффективности Величина отклонения расчетного (фактического) значения удельного расхода тепловой энергии на отопление здания qфакт от нормативного, % Рекомендуемые мероприятия органами администрации субъектов РФ Для существующих зданий D Низкий От плюс 6 до плюс 75 Желательна реконструкция здания Для…
Курсовая 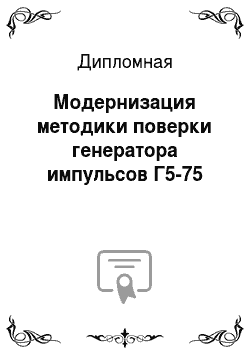
К основным новациям метрологического законодательства относятся: установление обязательных требований к измерениям в сфере государственного регулирования; сужение сферы государственного регулирования; отмена лицензирования ремонта и изготовления средств измерений и аттестации поверителей; внесение изменений в понятийный аппарат, установление принципов аккредитации в области метрологии, уточнение…
Дипломная 
Года около 07 часов 30 минут Залаев А. Е., в нарушение п. 2.7 ПДД РФ находящий в состоянии алкогольного опьянения, осознавая, что алкоголь одурманивает его, нарушает нормальное состояние психики, координацию движения, быстроту реакции, двигался на технически исправном автомобиле с пассажирами в салоне Пьянковой Я. О., Устюжанином А. К. и Мышкиным А. В. В пути следования Залаев, имея реальную…
Дипломная