Другие работы

Установлено, теоретически обосновано и экспериментально доказано интенсифицирующее воздействие струйного инъецирования МКС и АЖС на комплекс показателей мясного сырья, соленых полуфабрикатов и готовых изделий, заключающееся прежде всего в проникновении веществ органической и неорганической природы не только в межволоконное пространство, как при игольном способе, но и внутрь мышечного волокна…
Диссертация 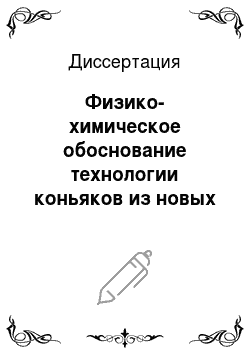
Все перечисленные процессы осуществляют в соответствии с правилами и нормативной документацией, разработанной на основе многолетнего опыта отечественных и зарубежных специалистов. Ассортимент винограда, предназначенного для получения коньячных виноматериалов, сложился исторически или был подобран в результате длительной селекционной работы. Качество коньячных спиртов неразрывно связано…
Диссертация 
Возникновение и рост напряжений в пеностекле определяется особенностями теплопереноса в поперечном сечении образца. В соответствии с полученным алгоритмом и программой расчета выявлены приоритетные способы теплопереноса через матрицу пористого тела и газовую среду порового пространства. Установлен характер распределения тепловых потоков в пеностекле в течение термообработки, их зависимость…
Диссертация 
Теоретические работы пионеров дизайна были новаторскими и носили зачастую декларативный, а иногда, и провокационный характер. Среди таковых— известная статья радикального толка «Орнамент и преступление» A. Jlooca, манифест «От футуризма и кубизма к супрематизму» К. Малевича (1915), книга-манифест «Синий всадник» В. Кандинского и Ф. Марка (1912), «Манифест неопластицизма Пита Мондриана» (1920…
Диссертация 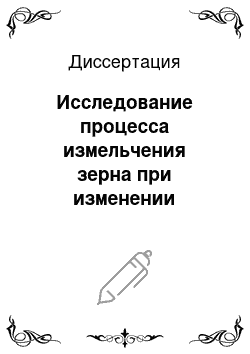
Апробация. Основные положения диссертации былиизложены на научных конференциях: Всероссийской научно-практической конференции «Вызовы 21 века и образование» (г. Оренбург 2006), Общероссийской конференции молодых ученых с международным участием «Пищевые технологии» (г. Казань 2006), Региональных конференциях молодых ученых и специалистов Оренбургской области «Наука-технологии-производство-рынок…
Диссертация 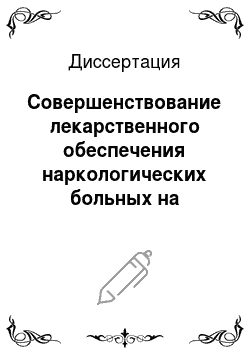
Методические рекомендации «Изучение маркетинговых характеристик номенклатуры лекарственных средств, используемых для лечения наркологических больных» (Утверждены Ученым советом ГОУ ВПО Пятигорская ГФА Росздрава 25.10.2006 г., протокол № 3). Получены акты внедрения: фармацевтического управления Ростовской области (от 15.03.2006 г.) — 1602 Окружного военного клинического госпиталя СКВО (от…
Диссертация 
Давление в конце процесса расширения Температура в конце процесса расширения Давления и температуры в цилиндре двигателя в процессах сжатия, сгорания и расширения вносятся в таблицу. По результатом расчёта рабочего процесса двигателя строятся индикаторные диаграммы, представляющие собой зависимости изменения давления газов в цилиндре от его объёма и угла поворота кривошипа. В процессе наполнения…
Курсовая 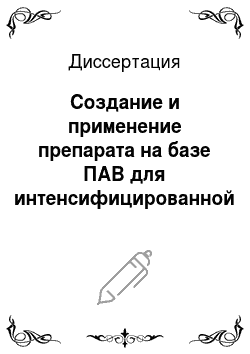
Технология интенсифицированной отварки с использованием препарата «Эмкол» прошла производственные испытания на ОАО «Самтекс» и ОАО «Шуйские ситцы». Испытания подтвердили возможность повышения качества выпускаемой продукции, при одновременном снижении расходов на проведение процессов подготовки. Ожидаемый экономический эффект от практической реализации предлагаемой технологии с использованием…
Диссертация 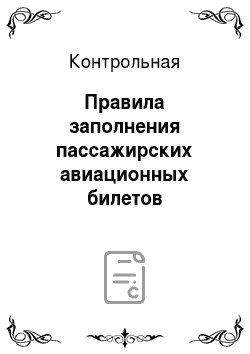
Для собственного бланка билета перевозчика, используемого для регулярных международных перевозок, указание трехцифрового расчетного кода перевозчика, присвоенного администрацией Международной Ассоциации воздушного транспорта (ИАТА), кода формы и серийного номера бланка обязательно. В указанном случае номер бланка билета должен содержать контрольный разряд цифровой части номера бланка — 1 цифра…
Контрольная 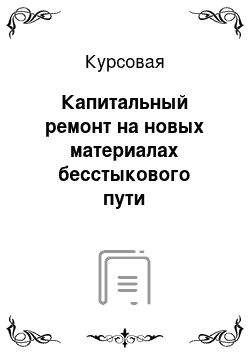
Исходя из требования по безопасности движения поездов, к концу рабочего дня на ремонтируемом участке должна быть установлена нормативная скорость движения поездов (после «окна» первые два поезда пропускаются со скоростью 25км/ч, следующие три поезда — 60км/ч, последующие со скоростью не более 100км/ч). Рельсовые плети бесстыкового пути укладываются только по стабилизации балластного слоя…
Курсовая 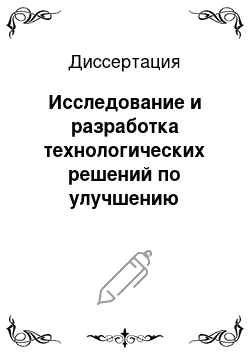
Многолетний опыт работы фабрик окомкования горно-обогатительных комбинатов России и, особенно в последние годы, Лебединского ГОКа (ЛГОК) и ОАО «Оскольский электрометаллургический комбинат» (ОЭМК) показывает, что одним из перспективных направлений повышения металлургических свойств окатышей различного назначения — для металлизации и доменной плавки является использование модифицирующих и связующих…
Диссертация 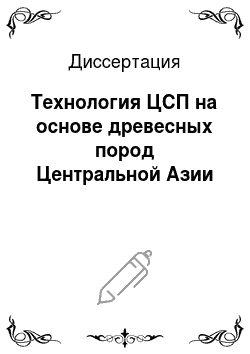
Изучено влияние водно-экстрактивных веществ древесины осины и ольхи на прочность при сжатии цементного камня и твердение цементного теста. Установлено, что водно-экстрактивное вещество из осины по сравнению с водно-экстрактивным веществом из ольхи значительно сокращает время твердения и схватывания. Так время схватывания и твердения цемента с водно-экстрактивным веществом ольхи равно 280, 430…
Диссертация 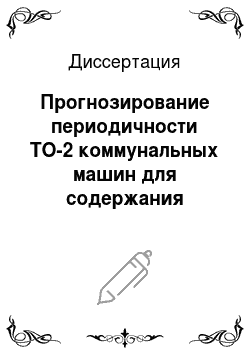
Достоверность результатов и выводов подтверждается удовлетворительной сходимостью теоретических положений и статистических данных (величина погрешности измерений основных параметров не превышает 5%), большим совпадением полученных зависимостей с ранее известными, а также работоспособностью результатов исследования в условиях производства. Практическая значимость диссертации заключается…
Диссертация 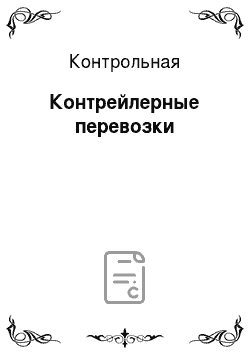
В России уже были попытки создания специализированных платформ для контрейлерных перевозок на двух российских заводах вначале 90-х годов, но конструктивные недостатки и плачевное состояние отечественной экономики не позволило применить их на Российских железных дорогах. В настоящие время осуществляются попытки организовать контрейлерные перевозки между РФ и Финляндией. В настоящий период времени…
Контрольная 
В 1804 г. Треветик испытал локомотив, который тянул 5 вагонов с 70 рабочими со скоростью 8 км/час. В последующие годы Дж. Стефенсон создал модель, которая стала с того времени прототипом последующих конструкций. В 1825 г. завершилось строительство железной дороги общего пользования Стектон-Дармингтон в основном для перевозки угля в морской порт. Последовало сооружение других железных дорог…
Реферат