Другие работы
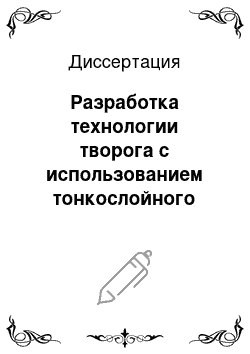
Творог относится к кисломолочным продуктам универсального применения, так как отличается высокой питательной и биологической ценностью и высокой калорийностью. Он является ценным продуктом питания для всех возрастных групп населения. Творог полезен как здоровым, так и больным. Люди, систематически потребляющие творог и продукты из него, менее подвержены заболеваниям. Он назначается при лечении…
Диссертация 
С созданием в Воронежском государственном техническом университете нового метода восстановления деталей путем гальваномеханического хромирования (ГМХ) появилась возможность осаждения на внутренних поверхностях качественных покрытий с шероховатостью менее Ra=0,l мкм. Однако традиционные ЭИ могут обеспечить нормальное давления и хороший доступ компонентов рабочей среды к различным участкам…
Диссертация 
Программное обеспечение является важным компонентом автоматизированных систем. Как было указано в предыдущем разделе, программным обеспечением автоматизированной системы упаковки предложено выбрать обеспечение Innova. Программное обеспечение Innovaэто интеллектуальнаясистема управления производством, предназначенная для контроля имониторинга процесса обработки, начиная от получения сырья…
Дипломная 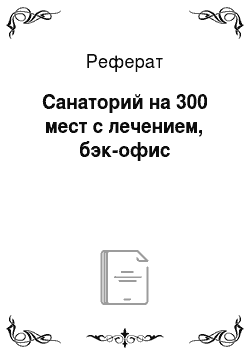
Разделение на фронт-офис и бэк-офис может быть реализовано как на программном уровне, так и на аппаратном уровне. То есть разделение может быть реализовано, как в виде нескольких совершено разных устройств, компьютеров, периферийного оборудования, так и в виде разделения функционала на одном устройстве, но с разными режимами работы. Явной границы между фронти бэк-офисом не существует, это лишь…
Реферат 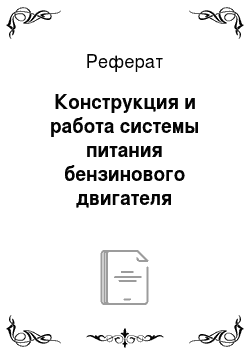
Система холостого хода включает в себя: топливный канал, берущий начало из эмульсионного колодца первичной камеры; топливный жиклер 5; воздушный жиклер 7; эмульсионный канал; винт качества (состава) смеси 35; винт количества смеси; выходное отверстие 33. На режиме холостого хода дроссельная заслонка 32 приоткрыта. При этом переходная щель 31 системы холостого хода находится над верхней кромкой…
Реферат 
Объем черновой обработки и, соответственно, величина удаляемого припуска во многом определяется существующими технологиями производства полуфабрикатов такими как литье, ковка, раскатка, сварка, а также техническим состоянием существующего оборудования. В настоящее время коэффициент весовой точности кольцевых заготовок не превышает 0,3 — 0,4 для кованных и литых. Так, например, для кованных…
Диссертация 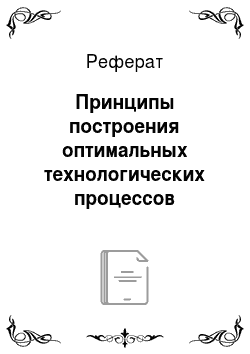
Достижение заданной точности при выполнении чистовой, либо чероновой обработки в одной операции затруднено из-за перераспределения напряжений после черновой обработки, либо повышенного износа станка из-за действующих большх сил резания. Именно в таких процессах требуется выполнять чистовую и черновую обработку детали, либо заготовки на различных станках, и рекомендуется изготавливать обязательно…
Реферат 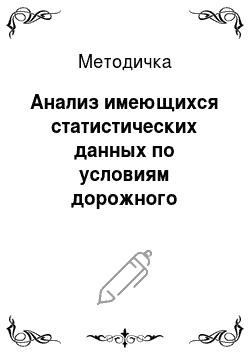
Доля тяжелых грузовых транспортных средств в составе транспортного потока будет расти пропорционально общему росту удельного веса автомобильного транспорта в общем объеме грузовых перевозок. Эта тенденция свойственна рыночной экономике из-за бесспорных преимуществ автотранспорта — гибкости, независимости от сезонов и расписаний, а главное — способности доставлять грузы от двери отправителя…
Методичка 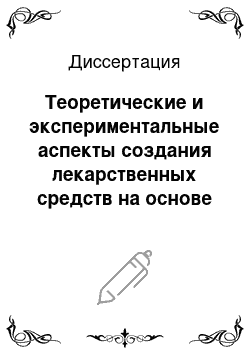
Научная новизна. На основании комплекса теоретических и экспериментальных исследований сформулированы методологические подходы к созданию лекарственных средств на основе сырья природного происхождения, включающие два основных направления. определение рациональной схемы получения оригинальных субстанций (ФЭС и НЭС). создание современных, качественных, эффективных и безопасных лекарственных форм…
Диссертация 
Существует несколько проблем, связанных с моделированием процесса непрерывной разливки и касающихся адекватности используемых моделей. Среди них большую роль играют проблемы задания теплофизических свойств разливаемых металлов и сплавов, а также проблемы формулирования граничных условий, определяющих особенности процесса затвердевания слитка и формирования качественных характеристик металла…
Диссертация 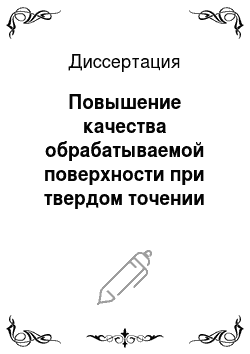
Методы исследования. Работа базируется на известных теоретических и экспериментальных работах в области динамики станков, процессов резания, теории колебаний, виброакустической (ВА) диагностики 5 механизмов, теории фотомеханики, методе конечных элементов. В исследовании применялось компьютерное моделирование с использованием современного программного обеспечения и средств вычислительной техники…
Диссертация 
Козловый кран представляет собой решетчатую ферму, опирающуюся по краям на две опоры. Опоры имеют колеса, поэтому кран может передвигаться по подкрановым рельсовым путям. На рельсах фермы установлена грузовая тележка, несущая механизм подъема груза с крюком. Тележка передвигается по рельсам фермы в пределах пролета. В результате движения крана по подкрановым рельсам и грузовой тележки по рельсам…
Контрольная 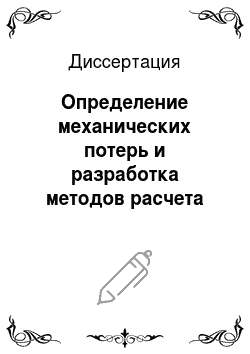
Основное содержание работы опубликовано в четырнадцати научных статьях, четырех патентах и трех свидетельствах. Это составляет 3,205 п.л. из них авторский вклад составляет около 1,36 п.л. Основные положения работы доложены на международной научно-технической конференции «Прогрессивные технологии, машины и механизмы в машиностроении» (г. Калининград, 2002 г.), Всероссийской научно-технической…
Диссертация 
В 1993. 1995 годах в НИПТИМЭСХ проведены испытания плуга с бороздным колесом вместо полевых досок, работающего по принципу самонастраивающейся механической системы. Проведенные лабораторно-полевые испытания показали, что плуг имеет меньшие удельное тяговое сопротивление на 30±4% и тяговое сопротивление на 21 + 4% по сравнению с серийным плугом ПЛН-3−35. В последующем это позволило установить…
Диссертация 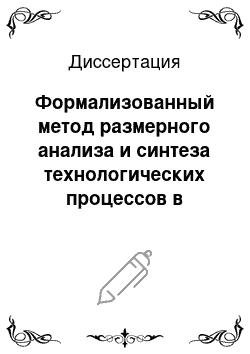
Одним из таких путей явилось намеченное в самое последнее время стремление разработать универсальные математические модели, основа которых одинаково пригодна для заполнения ее количественными связями типа параметрических уравнений, структурно-схемных отношений, или, при их отсутствии, различными справочными и нор"* мативными рекомендациями" При создании такой модели процесс механической обработки…
Диссертация