Дизельный двигатель ЗМЗ-617 жидкостного охлаждения с разработкой системы топливоподачи
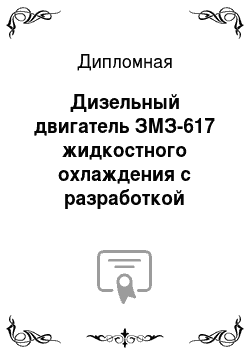
По результатам расчета (прил.2) строим следующие графические зависимости: Рг (), Рj (), РСУМ (), N (), S (), T (), K () и M (), а также полярную диаграмму нагрузок и диаграмму предполагаемого износа шатунной шейки (см. лист графической части ДП). Расчет полярной диаграммы нагрузок и диаграммы предполагаемого износа производим при помощи пакета программ разработанного преподавателями кафедры ДВС… Читать ещё >
Дизельный двигатель ЗМЗ-617 жидкостного охлаждения с разработкой системы топливоподачи (реферат, курсовая, диплом, контрольная)
Федеральное агентство по образованию
Государственное образовательное учреждение высшего профессионального образования
Владимирский государственный университет
Факультет: Автотранспортный Специальность: «Двигатели внутреннего сгорания»
ДИПЛОМНЫЙ ПРОЕКТ
Тема:
Автомобильный дизельный двигатель жидкостного охлаждения номинальной мощностью 95 кВт при частоте вращения коленчатого вала 4200 мин-1 с разработкой системы топливоподачи Студента: Демиденко С.А.
Руководитель проекта:
Драгомиров С.Г.
АННОТАЦИЯ
В дипломном проекте в соответствии с техническим заданием разработан дизель, с улучшенной системой подачи топлива и турбонаддувом.
Проведен тепловой, динамический и прочностной расчеты.
В исследовательском разделе была применена улучшенная система топливоподачи, с применением насос-форсунок.
Рассмотрены методы борьбы с шумом в дизеле при сгорании.
Выполнен расчет экономической эффективности и доказана конкурентоспособность проектируемого двигателя.
Стр. — 128, рис. — 22, таб — 7, прил. — 4.
Im Diplomprojekt entsprechend der technischen Aufgabe ist der Dieselmotor, mit dem verbesserten System die Abgaben des Brennstoffes und die Turboaufladung entwickelt.
Ist thermisch, dynamisch und прочностной die Rechnungen geleitet.
In der Forschungsabteilung war das verbesserte System die Abgaben des Brennstoffes, mit der Anwendung der Pumpen — Dьsen verwendet.
Es sind die Methoden des Kampfes mit dem Lдrm im Dieselmotor bei der Verbrennung untersucht.
Es ist die Rechnung der цkonomischen Effektivitдt erfьllt und es ist die Konkurrenzfдhigkeit des entworfenen Motors bewiesen.
АННОТАЦИЯ
1. ТЕХНИЧЕСКОЕ ЗАДАНИЕ НА ПРОЕКТИРОВАНИЕ
1.1 Цель разработки и область применения
1.2 Технические требования
2. КОНСТРУКЦИЯ ПРОЕКТИРУЕМОГО ДВИГАТЕЛЯ
3. ТЕПЛОВОЙ РАСЧЕТ РАБОЧЕГО ЦИКЛА
3.1 Выбор и обоснование исходных данных
3.2 Анализ результатов расчета
4. ДИНАМИЧЕСКИЙ РАСЧЕТ
4.1 Выбор и обоснования исходных данных
4.2 Силы и моменты, действующие в КШМ
4.3 Алгоритм динамического расчета ДВС
4.4 Анализ результатов динамического расчета
4.5 Уравновешивание двигателя
4.6 Силы, действующие на шатунную шейку
4.7 Силы, действующие на колено вала
4.8 Силы, действующие на коренную шейку
5. РАСЧЕТ ОСНОВНЫХ ДЕТАЛЕЙ ДВИГАТЕЛЯ
5.1 Поршневая группа
5.2 Шатунная группа
5.3 Расчет коленчатого вала
6. РАСЧЕТ СИСТЕМ ДВИГАТЕЛЯ
6.1 Расчет системы смазки
6.2 Расчет системы охлаждения
7. ИССЛЕДОВАТЕЛЬСКИЙ РАЗДЕЛ
7.1 Обзор систем впрыска
7.2 Оценка топливной аппаратуры различных типов с точки зрения организации управления процессом топливоподачи
7.3 Принцип действия и конструкция системы насос — форсунок
7.4 Схема системы насос — форсунок для легковых автомобилей
8. ОЦЕНКА ТЕХНИЧЕСКОГО УРОВНЯ ПРОЕКТИРУЕМОГО ДВИГАТЕЛЯ
8.1 Обзор и выбор критериев оценки
8.2 Обработка выбранного массива двигателей аналогов
9. ТЕХНОЛОГИЧЕСКИЙ РАЗДЕЛ
9.1 Способ обработки распределительного вала
9.2 Общая часть
9.3 Технология обработки
9.4 Расчет режимов резания
9.5 Расчет норм времени для обработки детали
10. БЕЗОПАСНОСТЬ ЖИЗНЕДЕЯТЕЛЬНОСТИ И ЭКОЛОГИЯ
10.1 Безопасность жизнедеятельности
10.2 Экология
11. ОРГАНИЗАЦИОННО-ЭКОНОМИЧЕСКИЙ РАЗДЕЛ
11.1 Понятие конкурентоспособности продукции в маркетинге
11.2 Определения конкурентоспособности продукции методом расчета единичных и групповых показателей
ЗАКЛЮЧЕНИЕ
СПИСОК ИСПОЛЬЗУЕМОЙ ЛИТЕРАТУРЫ
ПРИЛОЖЕНИЯ
Одним из основных показателей уровня развития государства является наличие собственной автомобильной промышленности. На сегодняшний день двигатели внутреннего сгорания (ДВС) являются основными источниками энергии для наземного транспорта. Идея преобразования теплоты от сгорания топлива в цилиндрах в механическую работу возникла еще в начале 19 века и своей актуальности не потеряла в наши дни благодаря сравнительно простому способу ее воплощения и наличия больших запасов нефти.
С момента своего создания двигатели внутреннего сгорания шли по пути увеличения литровой мощности, эффективного к.п.д., снижения удельного эффективного расхода топлива и металлоемкости. Развитие двигателестроения во многом зависит от развития смежных отраслей и благодаря открытиям в области химии, металлургии, автоматики, электроники и фундаментальных наук показатели ДВС улучшились во много раз.
По мере развития цивилизации к наземным транспортным средствам, и конечно же к их силовым агрегатам предъявлялись и дополнительные требования, связанные прежде всего с их эксплуатационными качествами (надежность, простота обслуживания и снижение материальных затрат при эксплуатации, улучшение динамики и т. д.).
В конце 20-го столетия ДВС получили столь широкое распространение, что вступили в прямое противоречие с экологическими и социальными условиями существования человека. Ухудшение экологической обстановки заставило человека вплотную заняться снижением токсичных выбросов двигателей внутреннего сгорания. В высоко развитых странах были введены соответствующие нормы и правила, что послужило толчком к развитию принципиально новых систем двигателей (системы питания с впрыском топлива, системы нейтрализации отработавших газов, системы, совершенствующие рабочий процесс ДВС в целом).
Двигатель внутреннего сгорания стал своеобразным объектом компромиссов. К сохраняющимся мощностным, тягово-динамическим требованиям добавились требования к экономичности, безопасности и экологичности.
При разработке новых ДВС перечисленные требования должны быть выполнены и от того насколько успешно это будет сделано, зависит будущее человечества, материальное благополучие производителя. Именно поэтому крупнейшие фирмы идут по пути все большего использования электроники в управлении рабочим процессом двигателя.
Использование принципов бионики и искусственного интеллекта дает возможность практического решения сложных многомерных задач управления силовой установкой автомобиля. Развитие электроники продолжается все нарастающими темпами. Появившиеся в 1971 г. микропроцессоры содержали 2300 транзисторов, а современные — более 500 000 активных элементов при быстродействии до долей наносекунды.
Двигатель внутреннего сгорания далек от идеального силового агрегата для наземных транспортных средств по многим параметрам и в настоящее время ведутся поиски альтернативы ему, однако пока достойная замена не будет найдена, необходимо повышать уровень отечественного двигателестроения, для удовлетворения имеющихся на сегодняшний день потребностей и успешного конкурирования с иностранными производителями. В конечном итоге это обусловит благосостояние и престиж страны.
1.Техническое задание на проектирование
Дизель размерностью D/S = 87/94, мощностью не менее 95 кВт с номинальной частотой вращения коленчатого вала 4200 мин -1.
1.1 Цель разработки и область применения
1.1.1 Дизель предназначен для установки на легковые автомобили.
1.1.2 Двигатель должен обеспечивать эксплуатацию при температурах окружающего воздуха от — 40оС до + 40оС в соответствии с ГОСТ 15 150– — 69 в условиях умеренного климата.
1.2 Технические требования
1.2.1 Основные параметры:
— тип двигателя — дизель с непосредственным впрыскиванием топлива;
— число тактов — 4;
— число цилиндров — 4;
— расположение цилиндров — вертикально;
— направление вращения коленчатого вала — правое (смотреть со стороны привода топливного насоса);
— степень сжатия — 19,5;
— номинальная мощность — не менее 95 кВт;
— частота вращения соответствующая номинальной мощности — 4200 мин -1;
— минимальная частота вращения холостого хода — 1000 мин -1;
— удельный эффективный расход топлива, минимальный по внешней скоростной характеристике, не более 221 г/(кВт . ч);
— расход масла не более 0,25% от расхода топлива без учета смены;
— пусковые качества дизеля должны соответствовать ОСТ 37.001.052 — 75;
— выделение вредных веществ дизелем должно быть не более норм, установленных ОСТ 37.001.234 — 81 «Охрана природы. Атмосфера. Выбросы вредных веществ с отработавшими газами. Нормы и методы измерений» и ГОСТ 17.2.2.01 — 84 «Дымность отработавших газов»;
1.2.2 Надежность:
— ресурс двигателя при установке его на МТС, используемое в условиях эксплуатации при соблюдении всех правил эксплуатации и ухода, указанных в руководстве по эксплуатации МТС, должен быть не менее 4000 моточасов;
— периодичность технического обслуживания двигателя должна соответствовать срокам проведения технического обслуживания мототранспортного средства;
— конструкция проектируемого двигателя должна обеспечивать свободный доступ ко всем частям, требующим регулировки, периодической замены, подтяжки креплений и замены эксплуатационных материалов.
1.2.3Уровень унификации и стандартизации:
— максимально возможное количество деталей разрабатываемого двигателя должно быть унифицировано с двигателем — прототипом ЗМЗ — 514;
1.2.4 Патентная чистота и конкурентоспособность:
— на двигатель должен быть оформлен патентный формуляр с указанием наличия патентной чистоты по США, Японии, Германии, Франции, Великобритании и Италии.
— показатели двигателя по развиваемой мощности, топливной экономичности, уровню шума, токсичности и дымности отработавших газов и внешнему виду должны быть у на уровне зарубежных аналогов, что позволит обеспечить конкурентоспособность на мировом рынке.
1.2.5 Составные части двигателя, материалы:
— картер состоит из одной части, материал — серый чугун;
— цилиндр материал — серый чугун, уплотнение газового стыка — медная прокладка;
— головка цилиндра съемная, материал — алюминиевый сплав, в теле головки предусмотрены каналы для охлаждающей жидкости;
— поршень из алюминиевого сплава, в головке поршня расположена камера сгорания;
— поршневые кольца: первое компрессионное кольцо из легированного чугуна с покрытием пористым хромом, второе компрессионное кольцо из легированного чугуна без покрытия, маслосъемное кольцо скребкового типа с тангенциальным расширителем, материал — легированный чугун;
— палец поршневой плавающего типа, стальной, полый;
— шатун стальной, кованый, с разъемной кривошипной головкой и стержнем двутаврового поперечного сечения;
— подшипник поршневой головки шатуна — бронзовая втулка;
— подшипник кривошипной головки шатуна — тонкостенные биметаллические вкладыши со стальной основой и антифрикционным слоем из высокооловянистого сплава;
— коленчатый вал стальной, литой, с противовесами, изготовленными как одно целое с продолжениями щек вала;
— подшипники коренные — толстостенные неразъемные бронзовые втулки;
— маховик — чугунный, литой, с напрессованным стальным зубчатым венцом;
— привод клапанов — от распределительного вала;
— клапаны верхнего расположения, четыре на цилиндр, материал — жаропрочная сталь;
— седла клапанов из специального легированного чугуна;
— направляющие втулки клапанов металлокерамические;
— газопроводы впускной и выпускной — стальные тонкостенные трубы с фланцами для крепления;
— система питания двигателя — система насос-форсунок с впрыскиванием топлива непосредственно в цилиндр и электронным управлением клапана регулировки давления в форсунке;
— топливоподкачивающий насос поршневого типа;
— очистка топлива — фильтр грубой и тонкой очистки, со сменным фильтрующим элементом;
— воздухоочиститель со сменным картонным фильтрующим элементом;
— система смазки комбинированная, под давлением смазываются коренные и шатунный подшипники коленчатого вала;
— насос масляный шестеренчатый, односекционный
— фильтр масляный полнопоточный, сменный;
— вентиляция картера закрытая, принудительная;
— система охлаждения жидкостная;
— система пуска — электростартер;
— топливо дизельное летнее для эксплуатации при температурах окружающей среды больше 0оС, зимнее при температурах от — 20оС до 0оС и арктическое при температурах ниже — 20оС в соответствии с ГОСТ 305– — 82.
— моторные масла: допускается применение моторных масел отечественного и зарубежного производства класса вязкости SAE 40 — летом, SAE 15W — зимой и SAE — 15W/40 — круглогодично. Категория эксплуатационных свойств масел по классификации API должна быть не ниже CD.
1.2.6 Транспортирование, хранение и консервация:
— двигатель должен быть упакован в тару, обеспечивающую его транспортирование и хранение высокопроизводительными методами (в том числе по железной дороге и автомобильным транспортом) в течение трех лет со дня консервации на заводе — изготовителе
2. КОНСТРУКЦИЯ ПРОЕКТИРУЕМОГО ДВИГАТЕЛЯ
Дизель предназначен для установки на транспортные средства малой грузоподъемности, минитракторы, малогабаритную технику коммунального хозяйства, дорожные и строительные машины, а также могут использоваться для привода мобильных электростанций, генераторных установок, насосных агрегатов. Возможно их применение в качестве двигателей малотоннажных судов.
Таблица 2.1
Технические параметры дизеля
Диаметр цилиндра D, мм | ||
Ход поршня S, мм | ||
Рабочий объём Vh, л | 2,24 | |
Степень сжатия | 19,5 | |
Мощность номинальная по ГОСТ 18 509–86 Nе, кВт | ||
Частота вращения коленчатого вала при номинальной мощности n, мин -1 | ||
Минимальный расход топлива ge, г/кВтч | ||
Минимальная частота вращения коленчатого вала в режиме холостого хода nХХ, мин-1 | ||
Максимальная частота вращения коленчатого вала в режиме холостого хода nmax, мин -1 | ||
Рис. 2.1 Поперечный и продольный разрезы двигателя
Двигатель (Рис. 2.1) состоит из следующих деталей, узлов и систем: картер, цилиндр, головка цилиндра, кривошипно-шатунный механизм, механизм газораспределения, всережимный регулятор частоты вращения, топливная система, система охлаждения, система смазки, система пуска, электрооборудование.
Цилиндр дизеля выполнен из специального износостойкого чугунного сплава.
Головка цилиндров отлита из алюминиевого сплава, имеет запрессованные чугунные седла и направляющие втулки клапанов. В головке выполнены гнездо для установки форсунки. Между головкой цилиндра и крышкой головки устанавливается прокладка.
Основными деталями кривошипно-шатунного механизма (КШМ) являются коленчатый вал, поршень, шатун, поршневые кольца, поршневой палец, шатунный подшипник (вкладыши) и коренные втулки.
Коленчатый вал полноопорный, чугунный, со сверлениями для подачи смазки к коренным и шатунным подшипникам. На носке вала устанавливается шестерня ременного привода вала насоса высокого давления.
Поршень выполнен из алюминиевого сплава с высоким содержанием кремния. В головке поршня расположена камера сгорания. В головке поршня имеются три канавки для установки колец: двух компрессионных и маслосъемного. В канавке маслосъемного кольца сделаны отверстия для отвода масла.
Поршни по наружному диаметру юбки сортируются на три группы — 0, 1, 2, которые при сборке должны совпадать с группой цилиндра. Разбивка на группы осуществляется по диаметру на расстоянии 25 мм от нижней кромки в направлении, перпендикулярном оси пальца. Это связано с тем, что для обеспечения температурного расширения, недопущения в процессе работы прорыва газов в картер и уменьшения стуков на перекладке юбки поршня имеет бочкообразный профиль в вертикальном направлении и сложный эллипсообразный профиль в горизонтальном.
Кроме того, поршни делятся по диаметру отверстия под палец на четыре группы, маркирующиеся различным цветом.
Поршневой палец изготовлен из специальной стали, обладающей большим запасом усталостной прочности. Поршневой палец запрессован в поршне. Поршневые пальцы по внешнему диаметру сортируются на четыре группы, которые при сборке должны соответствовать группам отверстия поршня.
Шатун — стальной, штампованный. Нижняя головка шатуна — разъемная и имеет расточку для вкладышей. Вкладыши шатунного подшипника изготовлены из сталеалюминиевой ленты. В верхнюю головку шатуна запрессована бронзовая втулка. Для смазки поршневого пальца в нижней головке шатуна имеется специальное отверстие.
Поршневые кольца изготовлены из специального чугуна. Верхнее компрессионное кольцо и нижнее маслосъемное кольцо — хромированы по наружной цилиндрической поверхности. Нижнее компрессионное кольцо, скребкового типа, устанавливается в канавку острой кромкой вниз с целью обеспечения съема масла со стенки цилиндра.
Механизм газораспределения — с одним распределительным валом приводимый во вращение от коленчатого вала. Клапаны совершают поступательное движение в направляющих втулках, запрессованных в головку цилиндра, и возвращаются в исходное положение под действием пружины.
Дизель имеет комбинированную систему смазки. Под давлением смазываются коренные и шатунные подшипники коленчатого вала; разбрызгиванием — стенки цилиндров, поршни с поршневыми кольцами, поршневые пальцы, втулка верхней головки шатуна.
Смазка осуществляется следующим образом: масляный насос через сетчатый фильтр маслозаборника подает масло из картера по трубопроводу для очистки в масляный фильтр, на выходе из которого установлен датчик давления, после очистки масло через каналы в картере поступает к коренному подшипнику правой половины картера. После чего через каналы, выполненные в коленчатом валу, масло подается к шатунному подшипнику, далее — к коренному подшипнику левой половины и стекает в полость картера.
Для поддержания постоянного давления в системе смазки имеется редукционный клапан, расположенный в корпусе масляного насоса и отрегулированный на давление срабатывания 0, 6 МПа на холодном двигателе и 0,2…0,35 МПа — на горячем.
Контроль за давлением масла осуществляется с помощью датчика давления, который при снижении давления ниже 0,08 МПа срабатывает и дает сигнал для аварийной остановки двигателя.
Имеется также датчик предельно допустимой температуры масла, которая не должна превышать 110−115°С.
Масло в картер заливается через горловину, расположенную со стороны стартера и закрываемую крышкой. Для проверки уровня масла имеется щуп, расположенный со стороны подкачивающегося насоса. Уровень масла должен быть не ниже и не выше верхней риски щупа, что соответствует 3,5л.
Для смазки дизеля применяются следующие моторные масла:
— летом — класса вязкости SAE 40
— зимой — SAE 15W
— круглогодично — SAE — 15W/40
Допускается использование масел иностранного производства, указанных в табл. 2.2, при этом следует убедиться, что они удовлетворяют требованиям государственных или фирменных спецификаций на смазочные масла, предназначенные для указанных дизелей.
Система впуска служит для подвода свежего воздуха и организации его вихревого движения в цилиндре требуемой интенсивности с целью обеспечения необходимых условий образования рабочей смеси при впрыскивании и распыливание топлива в камере сгорания. Состоит из воздухоочистителя и впускного патрубка.
Система выпуска предназначена для отвода из цилиндра отработавших газов. Состоит из выпускного патрубка и глушителя шума выпуска.
Воздухоочиститель — с двумя бумажными фильтрующими элементами и резонаторной камерой, снижающей уровень шума впуска.
Таблица 2.2
Фирма | Масло | ||
летом | зимой | ||
British Petroleum | Energol Diesel S. 1 SAE 30 | Energol Diesel S. 2 SAE 20W | |
Caltex Companies | RPM DELO Supercharged 1 SAE 30 | RPM DELO Supercharged 1 SAE 20W | |
E 330 lube Petroleum Co. Ltd/ | E 330 lube HDX 30 TSD 385 | E 330 lube HDX 10 | |
Shell | Rotella «Т2» 30 | Rotella «Т"20/20W | |
Vacuum Co. Ltd. | Delvac Oil S. 130 | Delvac Oil S. 110 | |
Глушитель шума выпуска коробчатого типа имеет двойной корпус с внутренними перегородками, проходя вдоль которых выпускные газы теряют свою энергию, что обеспечивает снижение шума выпуска.
Система подачи топлива состоит из следующих узлов: топливного бака, топливного фильтра, подкачивающего насоса, трубопроводов низкого давления, системы насос-форсунок.
Фильтр тонкой очистки топлива имеет специальный фильтрующий элемент, проходя через который топлива очищается от механических примесей. С целью предотвращения загустевания топливо при эксплуатации двигателя в условиях отрицательных температур в фильтре предусмотрен встроенный электрический подогреватель.
Топливоподкачивающий насос — мембранного типа, крепится к картеру через пластмассовую проставку. У топливоподкачивающего насоса имеется система ручной подкачки для подачи топлива к насос-форсункам перед запуском дизеля. Смазка подкачивающего насоса осуществляется из картера за счет возвратно — поступательного движения штока.
Форсунка служит для создания высокого давления и впрыскивания топлива под высоким давлением в камеру сгорания.
Топливопровод низкого давления — резиновый, армированный кордом шланг, выполненный из маслобензостойкой резины.
Система пуска дизеля включает в себя следующие узлы: электростартер, зубчатый венец, закрепленный на маховике, аккумуляторную батарею, электропроводку.
На дизеле устанавливается генератор переменного тока на постоянных магнитах, встроенных в маховик, мощностью 1500 -2000 Вт. Дизель комплектуется выпрямителем — стабилизатором, который обеспечивает стабильное постоянное напряжение 12 В в бортовой сети машины.
3. ТЕПЛОВОЙ РАСЧЁТ РАБОЧЕГО ЦИКЛА
3.1 Выбор и обоснование исходных данных
Цель теплового расчета: определение основных параметров двигателя S и D при заданной мощности. При выборе конструктивных параметров дизеля руководствуемся следующим. Двигатель должен по технико — экономическим параметрам находиться на уровне лучших, что обусловливает необходимость применения передовых конструктивных решений, выявленных в результате анализа более 20 двигателей указанного класса ведущих мировых производителей (приложение.1). Кроме этого при проектировании необходимо обеспечить максимально возможную унификацию дизеля с двигателем — прототипом — дизелем ЗМЗ-5148. Исходя из вышесказанного, выбираем следующие параметры дизеля.
Номинальная частота вращения дизеля мин-1. Частота вращения коленчатого вала характеризует тип двигателя и его динамические качества.
Отношение хода поршня S к диаметру цилиндра D (S/D) — один из основных конструктивных параметров ДВС. Величину S/D определяем по заданной размерности двигателя: S = 87 мм, D = 94 мм. Значение хода поршня и диаметра цилиндра такие же, как и у прототипа. Таким образом .
Отношение радиуса кривошипа r к длине шатуна l также принадлежит к основным конструктивным параметрам ДВС. Двигатели с большими значениями имеют меньшие габариты и массу, но увеличение значения ведет к возрастанию боковой силы, прижимающей поршень к зеркалу цилиндра, что обусловливает снижение механического КПД и увеличение износа цилиндро-поршневой группы (ЦПГ) двигателя. Кроме этого, при увеличении также возрастают силы инерции второго порядка в кривошипно-шатунном механизме (КШМ) ДВС, что тоже нежелательно. Современные материалы и технология изготовления деталей ДВС позволяют достичь приемлемого соотношения габаритов и массы двигателя с его механическим КПД при относительно высоких значениях. Исходя из этого, принимаем:
Cтепень сжатия
называют отношение полного объёма цилиндра к объёму камеры сгорания,
где Vа — объем надпоршневого пространства при положении поршня в НМТ,
VС — тот же объем при положении поршня в ВМТ.
— параметр, характеризующий особенности конструкции и рабочего процесса двигателя.
Величина определяет термический КПД термодинамического цикла ДВС, а следовательно и его эффективные показатели: среднее давление ре, мощность Ne и экономичность. Увеличение до определенного предела сопровождается улучшением эффективных показателей, а также и пусковых свойств дизеля. При дальнейшем повышении они начинают ухудшаться. Целесообразность увеличения в дизелях ограничивается началом существенного снижения механического КПД и ростом теплонапряженности деталей двигателя. Для обеспечения надежного самовоспламенения топливовоздушной смеси необходимо завышать степень сжатия на 1 — 2 единицы, так как относительно большие утечки рабочего тела через кольцевые уплотнения и более высокие относительные потери тепла в систему охлаждения приводят к снижению температуры заряда в конце сжатия. Учитывая вышесказанное, выбираем степень сжатия = 19,5.
Коэффициент избытка воздуха
где GВ, кг — количество воздуха, действительно находящегося в цилиндре,
GВО, кг — теоретически необходимое для полного сгорания цикловой подачи топлива, количество воздуха.
Так для дизельного топлива, состоящего по массе из 87% углерода, 12.5% водорода и 4% кислорода, величина GВО = 14.5 кг воздуха/кг топлива. Теоретически наибольшую литровую мощность при хорошей экономичности двигателя можно получить при = 1. На практике не удается организовать полное сгорание топлива в цилиндре дизеля при = 1 из-за невысокого качества смесеобразования, не позволяющего получать однородную гомогенную топливовоздушную смесь. Это приводит к тому, что сгорает смесь, обогащенная топливом, тогда как среднее значение по объему цилиндра значительно больше единицы, то есть большая часть воздуха (30 — 60%) в сгорании не участвует. Это обусловливает сравнительно низкую литровую мощность дизелей. Современные достижения в области совершенствования РП дизелей с НВТ позволяют осуществлять качественное сгорание при
= 1,4 1,7. Для номинального режима выбираем =1,4.
Механический КПД, характеризующий долю (Ne) индикаторной мощности (Ni), развиваемой газами в цилиндре, отдаваемую двигателем потребителю:
где NМ — потери индикаторной мощности в ДВС.
Доля NМ индикаторной мощности в дизеле расходуется на:
— газообмен: очистку цилиндра от отработавших газов (ОГ) и наполнение его свежим зарядом (мощность насосных ходов);
— на трение в парах «поршень — цилиндр», «поршневые кольца — цилиндр», в шатунных и коренных подшипниках (мощность трения);
— на привод агрегатов (мощность агрегатов): механизма газораспределения, топливного насоса высокого давления (ТНВД), топливоподкачивающего насоса, масляного насоса системы смазки, генератора.
Оценить величины вышеуказанных потерь на стадии проектирования можно лишь ориентировочно, опираясь на статистические данные по двигателям такого класса. Для расчета принимаем значение м=0.86 на режиме номинальной мощности. Высокое значение м при значительной средней скорости поршня
Сm = Sn/30 = 0,094 . 4200/30 = 13,16 м/с
обусловливается относительно невысокими потерями на привод агрегатов (отсутствие распределительного вала).
Максимальное давление цикла рz принимаем равным 11 МПа на основании того, что дизель будет оборудован системой управления периодом задержки воспламенения, способствующей снижению жесткости рабочего процесса (скорости нарастания давления в цилиндре).
Нижеперечисленные параметры дизеля также трудно поддаются оценке на стадии проектирования, поэтому их величинами задаемся ориентировочно на основе статистических данных.
Для быстроходного четырехтактного выбираем следующие значения параметров:
— температура остаточных газов
Тr = 850 К;
— приращение температуры свежего заряда при наполнении
Т = 15К;
— коэффициент сопротивления впускной системы, включающей в себя винтовой впускной канал, обеспечивающий вращение воздушного заряда в цилиндре,
ВП = ра/рК = 0,90;
— коэффициент сопротивления выпускной системы
ВЫП = рГ/рТ = 1,05;
— коэффициент дозарядки на номинальном режиме ДОЗ = 1,12, так как фазы газораспределения изменяемы таким образом, чтобы обеспечивать максимальное наполнение цилиндра на всех режимах;
— коэффициент использования тепла в точке «z» Z = 0,85 — характеризует долю тепла от его количества, выделяющегося в результате сгорания цикловой подачи топлива, которая подводится к рабочему телу на участке быстрого сгорания (от момента отклонения кривой давления при сгорании от кривой давления при сжатии до момента достижения рZ) и расходуется на увеличение его внутренней энергии и совершение работы;
— коэффициент использования тепла в точке «b» В = 0,90. Физический смысл в аналогичен Z, но B характеризует участок рабочего процесса от начала сгорания до момента открытия выпускного клапана;
— коэффициент полноты индикаторной диаграммы принимаем равным 0,97. Он учитывает уменьшение площади теоретической индикаторной диаграммы при скруглении ее в точках «с», «z» и «b» целью приближения к действительной зависимости давления в цилиндре от объема цилиндра или угла поворота коленчатого вала (ПКВ) дизеля.
Алгоритм теплового расчета четырехтактного дизеля численно реализован группой авторов кафедры ДВС ВлГУ на языке программирования Фортран 77 для ПЭВМ IBM PC и совместимых с ними. Пакет программ для теплового расчета включает в себя 3 файла:
— dizdn. dat — файл содержащий исходные данные для теплового расчета;
— dizdn. exe — исполняемый файл в котором реализован алгоритм теплового расчета дизеля;
— dizdn. rez — файл, в который помещаются исходные данные и результаты теплового расчета после выполнения командной строки операционной системы MS DOS:
C:DVS>dizdn.exe dizdn. rez .
Алгоритм теплового расчета позволяет проводить как проектный (задаются мощность и частота вращения, а вычисляется размерность SxD), так и проверочный (задаются частота вращения, S и D, а мощность вычисляется) расчеты.
3.2 Анализ результатов расчета
Коэффициент остаточных газов
это отношение количества остаточных газов МГ к количеству свежего заряда М1, поступающего в цилиндр двигателя в процессе впуска. Значение Г = 0,021 свидетельствует о высоком качестве очистки цилиндра от ОГ.
Коэффициент наполнения
;
— это отношение действительного количества свежего заряда, поступившего в цилиндр, к тому количеству свежего заряда, которое могло бы заполнить рабочий объём цилиндра при условиях на впуске. Значение V = 0,897 — характерная величина для дизеля с винтовым впускным каналом на номинальном режиме. Рассчитанное значение V позволяет предполагать удовлетворительное протекание процессов газообмена у реального ДВС.
Давление и температура в конце сжатия рС = 8,28МПа, ТС = 1100 К обеспечивают надежное самовоспламенение топливовоздушной смеси. Определяются из уравнения политропы с постоянным показателем n1,, .Значения рС и ТС у реального двигателя могут превышать расчетные, так как использованный алгоритм расчета не учитывает способ охлаждения двигателя.
Средний показатель политропы сжатия n1 зависит от частоты вращения, степени сжатия, размеров цилиндра, материалов ЦПГ, системы охлаждения и других факторов. По данным для дизелей без наддува с неохлаждаемыми поршнями n1 = 1,35…1,42. Рассчитанное значение n1 = 1,36.
Максимальная температура цикла (температура сгорания) характеризует тепловую напряженность двигателя. Значение ТZ = 2354К, что приемлемо для дизеля с НВТ. Преимущество поршневого ДВС перед другими тепловыми двигателями состоит в том, что цикличность его работы позволяет реализовать большой мгновенный перепад температур при относительно низкой средней температуре цикла.
Давление и температура в конце расширения Рb и Tb определяются по формулам политропного процесса:
Полученные значения Pb = 0,555 МПа, Tb = 953 К.
Средний показатель политропы расширения как и показатель политропы сжатия, характеризует степень теплообмена. Значение n2 = 1,212 указывает на то, что в процессе расширения тепловой поток направлен от рабочего тела к стенкам, что объясняется высоким перепадом температур газов и омываемых ими поверхностей, площадь которых во время расширения постоянно увеличивается.
Среднее индикаторное давление рi = 1,42 МПа, полученное с учетом скругления индикаторной диаграммы в точках «c», «z» и «b» позволяет отнести дизель к высокофорсированным по рi ДВС.
Удельный индикаторный расход топлива gi — это расход топлива, приходящийся на единицу развиваемой двигателем индикаторной мощности. Значения gi = 182 г/(кВт . ч) и индикаторный КПД i = 0,464 являются показателями качественного протекания рабочего процесса. Среднестатистические значения для четырехтактных дизелей находятся в пределах gi = 170…220 г/(кВт.ч) и i = 0.39…0.49.
Среднее эффективное давление — отношение полезной работы, получаемой на валу двигателя к единице рабочего объёма цилиндра. Значение ре =1,23 МПа также как и рi характеризует уровень форсирования по среднему давлению цикла как высокий.
Удельный эффективный расход топлива
— отношение часового расхода топлива к эффективной мощности. Значения gе = 183 г/(кВт.ч) и эффективный КПД е = 0,40 для дизеля являются хорошими показателями экономичности.
Эффективный КПД
отношение количества теплоты Le, эквивалентной полезной работе на валу двигателя, к общему количеству теплоты, внесенному в двигатель с топливом.
Крутящий момент МКР — одна из важнейших характеристик двигателя, от которой зависят динамические и тяговые качества автомобиля. По результатам расчета МКР =218 Нм.
Часовой расход топлива
- количество топлива, потребляемое двигателем на заданном режиме за 1 час. Расчетное значение GT = 20,37 кг/ч.
Рабочий объём двигателя
По результатам расчета для заданных S и D Vh = 2,24 дм3.
4. ДИНАМИЧЕСКИЙ РАСЧЕТ
4.1 Выбор и обоснование исходных данных
Основная цель динамического расчета — построение зависимости индикаторного крутящего момента двигателя от угла поворота коленчатого вала и определение его средней величины. Кроме этого необходимо рассчитать зависимости сил, действующих в КШМ, которые требуются для прочностных расчетов деталей двигателя, и найти максимальное и среднее удельные давления на шатунную шейку коленчатого вала, которые определяют применимость конкретного материала шатунных вкладышей и их работоспособность. Расчет проводится на режиме максимальной мощности.
Исходные данные для динамического расчета:
mШ = 0,9 кг — масса шатуна;
lШ = 26 мм — длина рабочей части шатунного подшипника;
dШ = 56 мм — диаметр шатунной шейки коленчатого вала;
r = 43,5 мм — радиус противовеса для удобства вычислений выбираем равным радиусу кривошипа;
2 — число противовесов на одном кривошипе.
Для приближенного определения масс можно использовать конструктивные массы:
Масса поршневого комплекта и части шатуна отнесенная к оси поршневого пальца:
кг, где mПК = 0,6 кгмасса поршневого комплекта; mШ.П = 0,2 кг — масса части шатуна, отнесенной к оси поршневого пальца;
mШК = 0,70 кг — масса части шатуна, отнесенной к оси шатунной шейки коленчатого вала;
mК = 1,5 кг — масса неуравновешенной части кривошипа приведенная к его радиусу определяется приближенно по чертежу коленчатого вала.
Масса шатуна:
.
Для упрощения расчетов кривошипно-шатунный механизм двигателя заменяют его двухмассовой моделью и определяют силы инерции возвратно — поступательно движущихся масс по приближенным формулам, что несущественно снижает точность расчетов, но значительно уменьшает их объем. Двухмассовая модель и схема действия сил в КШМ приведены на листе графической части ДП.
Массы совершающие вращательные движения:
.
Массы совершающие вращательно-поступательное движение:
.
Рис. 4.1 Схема действия сил в кривошипно-шатунном механизме
4.2 Силы и моменты, действующие в КШМ
Сила давления расширяющегося рабочего тела на поверхность поршня для упрощения динамического расчета, заменяют равнодействующей, направленной вдоль оси цилиндра и приложенной к оси поршневого пальца. Ее значение вычисляется как
где рГ — давление газов в цилиндре для данного угла п.к.в.; р0 — давление газов в картере двигателя принятое равным атмосферному давлению.
Силы инерции, действующие в КШМ, в соответствии с характером движения приведенных масс подразделяются на силы инерции поступательно движущихся масс Pj и центробежные силы вращающихся масс Кr.
Силы инерции поступательно движущихся масс вычисляют в зависимости от угла п.к.в. по формуле:
.
Силу Рj принято представлять как сумму сил инерции 1-го и 2-го порядков:
где c-1 — угловая скорость кривошипа; n, мин-1 — частота вращения коленчатого вала, о — угол поворота кривошипа.
Центробежная сила инерции вращающихся масс:
.
Суммарная сила:
.
Нормальная сила, действующая на стенки цилиндра:
где — угол отклонения шатуна;
Сила, действующая вдоль оси шатуна:
.
Сила, направленная по радиусу кривошипа:
.
Тангенциальная сила, направленная по касательной к окружности радиуса кривошипа:
По величине Т определяют крутящий момент цилиндра:
МР (МОПР) — реактивный момент, стремиться опрокинуть двигатель, равен по величине крутящему моменту и противоположен ему по направлению МР = -МКР.
Сила, нагружающая шатунный подшипник:
.
Радиальная сила:
Суммарная радиальная сила, действующая вдоль радиуса кривошипа:
Результирующая сила, нагружающая коренные опоры коленчатого вала:
.
Горизонтальная составляющая силы, передающейся на опоры двигателя:
.
Вертикальная составляющая силы, передающейся на опоры двигателя:
.
Момент, передающийся на опоры двигателя:
Формулы сил и момента на опорах дизеля выведены без учета механизма уравновешивания.
4.3 Алгоритм динамического расчета ДВС
Алгоритм динамического расчета как таковой не сложен, но требует наличия данных о давлении газов в цилиндре при каждом угле поворота коленчатого вала, поэтому целесообразно совместить тепловой и динамический расчеты двигателя. Алгоритм такого расчета реализован группой авторов кафедры ДВС ВлГУ на языке программирования Фортран 77 для ПЭВМ IBM PC и совместимых с ними. Пакет программ для теплового и динамического расчета четырехтактного дизеля включает в себя 3 файла: dindis. dat, dindis. exe и dindis.rez. Организация и способ проведения расчета у этого пакета программ аналогичны описанному в п. 4.1. пакету для теплового расчета.
Динамический расчет дизеля целесообразно осуществить для двух режимов работы: номинального и режима максимального крутящего момента. Для номинального режима динамический расчет проводим по исходным данным п.п. 4.1 и 5.1. Распечатка результатов динамического расчета приведена в прил.2.
Для того, чтобы определить мощность двигателя NM и частоту вращения nM на режиме максимального крутящего момента воспользуемся математической моделью внешней скоростной характеристики двигателя, которая позволяет построить характеристику проектируемого двигателя по значениям его номинальной мощности и частоты вращения на основе характеристики прототипа. Номинальная мощность дизеля полученная в результате теплового расчета составляет 95 кВт при частоте вращения 4200 мин-1. По расчетным данным режим максимального крутящего момента проектируемого двигателя характеризуется следующими величинами: nM = 2400 мин-1, NM = 59 кВт, Мmax = 235,3 Н.м. По скорректированным данным п.п.3.1 и 4.1 проводим динамический расчет дизеля на режиме максимального крутящего момента. Распечатка результатов расчета приведена в прил.2.
4.4 Анализ результатов динамического расчета
По результатам расчета (прил.2) строим следующие графические зависимости: Рг(), Рj(), РСУМ(), N (), S (), T (), K () и M (), а также полярную диаграмму нагрузок и диаграмму предполагаемого износа шатунной шейки (см. лист графической части ДП). Расчет полярной диаграммы нагрузок и диаграммы предполагаемого износа производим при помощи пакета программ разработанного преподавателями кафедры ДВС. Указанный пакет программ, реализованный на языке программирования Fortran 77, включает в себя файл rr1. c, предназначенный для исходных данных, и файл Din286. exe, предназначенный для расчета и построения полярной диаграммы нагрузок. На диаграмме предполагаемого износа выделяем наиболее нагруженный участок шейки — Б и наименее нагруженный — А для того, чтобы определить наиболее выгодное положение оси масляного отверстия с точки зрения работы шатунного подшипника скольжения. Ось масляного отверстия ОМ является биссектрисой угла между лучами, ограничивающими наименее нагруженный участок, А поверхности шатунной шейки. Угол м, определяющий расположение выхода масляного отверстия на поверхность шейки равен 70о. Учитывая то, что технологически существенно проще сверлить отверстие для подвода масла к шатунному подшипнику под углом 90о к плоскости кривошипа, чем под углом 70о, ось масляного отверстия оставляем перпендикулярной плоскости кривошипа, но смещаем ее вдоль радиуса кривошипа таким образом, чтобы выход масляного отверстия располагался в пределах наименее нагруженного участка, А поверхности шатунной шейки. Величина угла М при этом остается допустимой.
4.5 Уравновешивание двигателя
У данного двигателя кривошипы расположены под углом 180, промежутки между вспышками равны 180. Порядок работы цилиндров двигателя: 1−3-4−2.
Центробежные силы инерции проектируемого двигателя Рис. 4.2. Схема сил действующих на КВ и их моменты полностью уравновешены с помощью противовесов, расположенных на продолжениях всех щек коленчатого вала:
.
Силы инерции первого порядка и их моменты также уравновешены:
.
Силы инерции второго порядка для всех цилиндров направлены в одну сторону (рис. 5.5.1):
.
Уравновешивание этих сил в проектируемом двигателе нецелесообразно, т.к. применение двухвальной системы с противовесами значительно усложнит конструкцию двигателя. Моменты от этих сил в связи с симметричностью вала полностью уравновешены.
Рис. 4.3 Силы, действующие на шатунную шейку
4.6 Силы, действующие на шатунную шейку
Результирующая сила, действующая на шатунную шейку (рис. 4.4.):
.
Сила, действующая на шатунную шейку по кривошипу, Н:
.
Направление результирующей силы RШШ для различных положений коленчатого вала определяется углом, заключенным между вектором RШШ и осью кривошипа. Угол находится из соотношения. Графическое построение силы RШШ в зависимости от угла поворота кривошипа осуществляется в виде полярной диаграммы.
Рис. 4.4 Силы, действующие на колено вала
4.7 Силы, действующие на колено вала
Результирующая сила, действующая на колено вала (рис. 4.5):
.
Сила, действующая на колено вала по кривошипу, Н:
.
Центробежная сила инерции вращающихся масс кривошипа:
.
4.8 Силы, действующие на коренные шейки
Результирующая сила RШШ, действующая на коренную шейку (рис. 4.6.), определяется геометрическими сложениями сил, равных на противоположных по направлению силами, передающимися от двух смежных колен:
где
и
— соответственно усилия, передаваемые от i — го и (i+1) — го колен на коренную шейку, заключенную между ними;
l1 и l2 — расстояния по оси вала между центрами коренной и шатунной шеек;
L — расстояние между центрами соседних коренных шеек.
При проведении динамических расчетов двигателей целесообразно пользоваться не полными, а удельными силами, отнесенными к единице площади поршня.
Таблица 4.1
Значения RШШ для лучей, МПа
п.к.в. | Услов. обозн. | |||||||||||||
1,24 | 1,24 | 1,24 | ; | ; | ; | ; | ; | ; | ; | 1,24 | 1,24 | |||
; | ; | ; | ; | ; | ; | ; | ; | |||||||
0,58 | 0,58 | 0,58 | 0,58 | ; | ; | ; | ; | ; | ; | ; | 0,58 | |||
0,32 | 0,32 | ; | ; | ; | ; | ; | ; | ; | 0,32 | 0,32 | 0,32 | |||
0,66 | ; | ; | ; | ; | ; | ; | ; | 0,66 | 0,66 | 0,66 | 0,66 | |||
0,8 | 0,8 | ; | ; | ; | ; | ; | ; | ; | 0,8 | 0,8 | 0,8 | |||
0,8 | 0,8 | ; | ; | ; | ; | ; | ; | ; | ; | 0,8 | 0,8 | |||
0,8 | 0,8 | 0,8 | ; | ; | ; | ; | ; | ; | ; | 0,8 | 0,8 | |||
0,74 | 0,74 | 0,74 | 0,74 | ; | ; | ; | ; | ; | ; | ; | 0,74 | |||
0,52 | 0,52 | 0,52 | 0,52 | ; | ; | ; | ; | ; | ; | ; | 0,52 | |||
0,32 | 0,32 | ; | ; | ; | ; | ; | ; | ; | 0,32 | 0,32 | 0,32 | |||
0,2 | 0,2 | 0,2 | 0,2 | ; | ; | ; | ; | ; | ; | ; | 0,2 | |||
; | ; | ; | ; | 2,74 | 2,74 | 2,74 | 2,74 | ; | ; | ; | ; | |||
; | ; | ; | ; | ; | 1,8 | 1,8 | 1,8 | 1,8 | 1,8 | ; | ; | |||
; | ; | ; | ; | ; | ; | ; | 0,64 | 0,64 | 0,64 | 0,64 | 0,64 | |||
0,84 | ; | ; | ; | ; | ; | ; | ; | 0,84 | 0,84 | 0,84 | 0,84 | |||
; | ; | ; | ; | ; | ; | ; | ||||||||
0,96 | 0,96 | ; | ; | ; | ; | ; | ; | ; | 0,96 | 0,96 | 0,96 | |||
0,88 | 0,88 | ; | ; | ; | ; | ; | ; | ; | ; | 0,88 | 0,88 | |||
0,82 | 0,82 | 0,82 | ; | ; | ; | ; | ; | ; | ; | 0,82 | 0,82 | |||
0,76 | 0,76 | 0,76 | 0,76 | ; | ; | ; | ; | ; | ; | ; | 0,76 | |||
0,26 | 0,26 | 0,26 | ; | ; | ; | ; | ; | ; | ; | 0,26 | 0,26 | |||
0,5 | ; | ; | ; | ; | ; | ; | ; | 0,5 | 0,5 | 0,5 | 0,5 | |||
; | ; | ; | ; | ; | ; | ; | ||||||||
RШШ | 6,92 | 3,8 | 2,74 | 4,54 | 4,54 | 5,18 | 6,44 | 8,34 | 11,84 | 14,64 | ||||
Таблица 4.2
Значения RКШ для лучей, коренной шейки, МПа
п.к.в. | Услов. обозн. | |||||||||||||
0,49 | 0,49 | ; | ; | ; | ; | ; | ; | ; | ; | 0,49 | 0,49 | |||
0,4 | 0,4 | 0,4 | 0,4 | ; | ; | ; | ; | ; | ; | ; | 0,4 | |||
0,21 | 0,21 | 0,21 | 0,21 | 0,21 | ; | ; | ; | ; | ; | ; | ; | |||
; | ; | ; | ; | ; | ; | ; | 0,07 | 0,07 | 0,07 | 0,07 | 0,07 | |||
0,25 | ; | ; | ; | ; | ; | ; | ; | 0,25 | 0,25 | 0,25 | 0,25 | |||
0,27 | 0,27 | ; | ; | ; | ; | ; | ; | ; | 0,27 | 0,27 | 0,27 | |||
0,26 | 0,26 | ; | ; | ; | ; | ; | ; | ; | ; | 0,26 | 0,26 | |||
0,27 | 0,27 | 0,27 | ; | ; | ; | ; | ; | ; | ; | 0,27 | 0,27 | |||
0,28 | 0,28 | 0,28 | 0,28 | ; | ; | ; | ; | ; | ; | ; | 0,28 | |||
0,19 | 0,19 | 0,19 | 0,19 | 0,19 | ; | ; | ; | ; | ; | ; | ; | |||
; | ; | ; | ; | ; | ; | ; | ; | 0,06 | 0,06 | 0,06 | 0,06 | |||
; | ; | 0,07 | 0,07 | 0,07 | 0,07 | 0,07 | ; | ; | ; | ; | ; | |||
; | ; | ; | ; | 1,51 | 1,51 | 1,51 | 1,51 | ; | ; | ; | ; | |||
; | ; | ; | ; | ; | 0,97 | 0,97 | 0,97 | 0,97 | 0,97 | ; | ; | |||
; | ; | ; | ; | ; | ; | 0,32 | 0,32 | 0,32 | 0,32 | 0,32 | ; | |||
; | ; | ; | ; | ; | ; | ; | 0,37 | 0,37 | 0,37 | 0,37 | 0,37 | |||
0,41 | ; | ; | ; | ; | ; | ; | ; | 0,41 | 0,41 | 0,41 | 0,41 | |||
0,36 | 0,36 | ; | ; | ; | ; | ; | ; | ; | 0,36 | 0,36 | 0,36 | |||
0,3 | 0,3 | ; | ; | ; | ; | ; | ; | ; | ; | 0,3 | 0,3 | |||
0,29 | 0,29 | 0,29 | ; | ; | ; | ; | ; | ; | ; | ; | 0,29 | |||
0,27 | 0,27 | 0,27 | 0,27 | ; | ; | ; | ; | ; | ; | ; | 0,27 | |||
0,05 | 0,05 | 0,05 | ; | ; | ; | ; | ; | ; | ; | 0,05 | 0,05 | |||
0,18 | 0,18 | ; | ; | ; | ; | ; | ; | ; | 0,18 | 0,18 | 0,18 | |||
0,4 | ; | ; | ; | ; | ; | ; | ; | 0,4 | 0,4 | 0,4 | 0,4 | |||
RКШ | 4,88 | 3,82 | 2,03 | 1,42 | 1,98 | 2,55 | 2,87 | 3,24 | 2,85 | 4,26 | 4,06 | 4,98 | ||
5. РАСЧЁТ ОСНОВНЫХ ДЕТАЛЕЙ ДВИГАТЕЛЯ
5.1 Поршневая группа
Рис. 5.1 Схема поршня
5.1.1 Поршень
Наиболее напряженным элементом поршневой группы является поршень, имеющий ударный характер приложения нагрузки, контакт с горячими газами
(Тz = 2500…2800 C), коррозионный и механический износ.
Поэтому к материалу поршня при его изготовлении предъявляются повышенные требования.
Поршни дизелей имеют более теплонапряженный режим работы из — за: высокой турбулизации и плотности газовой среды; интенсивного теплового излучения из — за горения жидких углеводородов непосредственно в камере сгорания; высокая неравномерность температурных полей (объёмное сгорание + впрыск топлива непосредственно в пламя). Схема поршня представлена на рис. 5.1.
Материал поршня — алюминиевый сплав АК — 25 М² ГОСТ 2685).
Исходные данные для расчета:
D = 87 мм — диаметр поршня;
mпк = 0,5 кг — масса поршневого комплекта;
R = 47 мм — радиус кривошипа;
nxx = 5100 об/мин — максимальная частота вращения холостого хода;
nном = 4200 об/мин — номинальная частота вращения;
=0,318 — отношение радиуса кривошипа к длине шатуна;
Pz =11 МПа — максимальное давление цикла;
Максимальная сила давления газов на поршень:
Расчет верхней кольцевой перемычки.
hП = 5,0 мм — толщина верхней кольцевой перемычки.
Напряжение среза:
;
Напряжение изгиба:
;
Эквивалентное напряжение:
;
Опасное сечение по канавке маслосъёмного кольца.
dK = 77 мм — внутренний диаметр кольца;
d1 = 30 мм — внутренний диаметр поршня;
nM = 6 — число дренажных отверстий;
d0 = 2,0 мм — диаметр дренажных отверстий.
Разрывающая сила инерции в опасном сечении Х — Х:
Сила инерции в опасном сечении при расчете на номинальном режиме работы:
Площадь опасного сечения Х — Х:
Напряжения в опасном сечении:
;
;
Удельная нагрузка на бобышки.
lБ = 18,0 мм — длина опорной поверхности бобышек;
dП = 30 мм — диаметр поршневого пальца.
Удельная нагрузка на юбку поршня от нормальной силы.
hЮ = 56 мм — высота юбки поршня;
Nmax = 3437 Н — максимальная нормальная сила, действующая на поршень.
Динамические зазоры в горячем состоянии.
Зазоры в холодном состоянии:
Г = 0,2 мм — зазор между головкой поршня и цилиндром в холодном состоянии;
Ю = 0,1 мм — зазор между юбкой поршня и цилиндром в холодном состоянии;