Плазменная сварка.
Технология сварочных работ
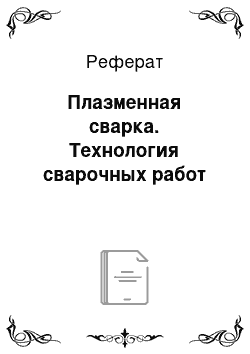
Если плазмообразуюшим газом является водород, то почти все его атомы теряют электронную оболочку, и плазма представляет собой смесь положительно заряженных ядер и не связанных с ними отрицательно заряженных электронов. Если в образовании плазмы участвуют атомы с большей, чем у водорода, массой (имеющие большее число электронных оболочек), например аргона, то атомы теряют электроны с внешних… Читать ещё >
Плазменная сварка. Технология сварочных работ (реферат, курсовая, диплом, контрольная)
Плазменная сварка представляет собой сварку плавлением, при выполнении которой нагрев производится сжатой дугой.
Источником теплоты при плазменной сварке является плазменная струя — направленный поток ионизированных частиц газа с температурой, достигающей 20 000 К. Плазменная дуга, будучи концентрированным источником теплоты, обладает большой проплавляющей способностью.
Плазменной дугой можно сваривать заготовки толщиной до 10 мм без разделки кромок. Обладая высокой стабильностью, она позволяет выполнять микроплазме иную сварку заготовок толщиной 0,025…0,8 мм. Если увеличить расход плазмообразующего газа, то можно значительно повысить тепловую мощность, скорость истечения и давление плазмы. Такая дуга обеспечивает сквозное проплавление и выдувает расплавленный металл, т. е. позволяет осуществлять его резку. Плазменную дугу используют для сварки металлов (высоколегированная сталь, сплавы титана, никеля, молибдена и вольфрама) и неметаллов, резки любых материалов, наплавки, напыления и т. д.
Различают два вида плазмы: изотермическую (возникает при нагреве газа до температур, достаточных для его термической ионизации) и газоразрядную (образуется при электрическом разряде в газе).
Получение изотермической плазмы требует предварительного нагрева газов до температур 3 000… 5 000 К. При этих температурах кинетическая энергия атомов достигает значений, при которых в результате взаимных столкновений разрушаются их внешние электронные оболочки, и нейтральные атомы превращаются в положительно заряженные ионы. Освободившиеся электроны выбивают новые электроны из оболочек других атомов, и процесс наращивания числа электронов и ионов приобретает лавинообразный характер. Газ переходит в состояние плазмы.
Если плазмообразуюшим газом является водород, то почти все его атомы теряют электронную оболочку, и плазма представляет собой смесь положительно заряженных ядер и не связанных с ними отрицательно заряженных электронов. Если в образовании плазмы участвуют атомы с большей, чем у водорода, массой (имеющие большее число электронных оболочек), например аргона, то атомы теряют электроны с внешних оболочек. При температурах 10 000…20 000 К ионизация не заканчивается. Плазма состоит из свободных электронов и ионов, которые представляют собой атомы, сохранившие электроны на своих внутренних оболочках. Следовательно, проникающая (проплавляющая) способность такой плазмы выше, чем у водородной, однако для ее получения необходим дополнительный нагрев (введение дополнительной энергии).
Получение газоразрядной плазмы осуществляется с помощью дугового разряда, который возбуждается между катодом и анодом при соответствующей разности потенциалов, температуре и плотности тока. При атмосферном давлении температура столба электрической дуги составляет 5 000… 6 000 К. Если электрический дуговой разряд обдувать потоком плазмообразующего газа, то возможно возбуждение плазменной дуги.
Строение плазменной дуги показано на рис. 2.29. Подлине дуги можно выделить три области: анодную, катодную и столб дуги. В анодной области скапливается отрицательный объемный заряд, обусловливающий падение напряжения U.d(Ua= 1 …5 В, плотность тока /а = 1… 100 А/мм2).
В катодной области скапливается положительный объемный заряд, вызывающий падение напряжения UK(UK = 5… 10 В, плотность тока /к = 10… 1 000 А/мм2). Протяженность обеих переходных областей — анодной и катодной — соизмерима с длиной свободного пробега электрона.
Между переходными областями располагается цилиндрический канал, заполненный квази нейтральной плазмой — столб дуги. Под квазинейтральностью плазмы понимают равенство нулю алгебраической суммы зарядов в довольно большом объеме (отсутствие избытка электронов или ионов).
Плазменные горелки. В корпусе / горелки (рис. 2.30, а) размещены два основных элемента — газовая камера 2 и электрод 3. Через формирующее сопло 4 газовой камеры пропускают плазмообразующий газ.
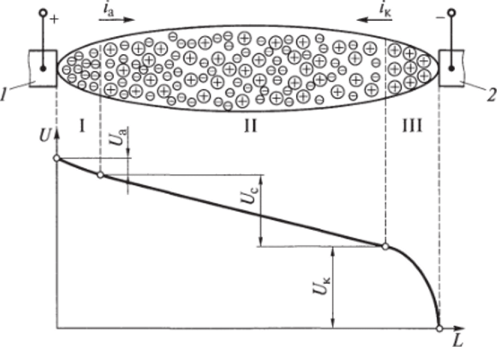
Рис. 2.29. Строение плазменной дуги и распределение падения напряжения вдоль ее оси:
/ — анод; 2 — катод; I — анодная область; II — столб дуги; III — катодная область; /а — плотность анодного тока; /к — плотность катодного тока; U — падение напряжения; L — длина дуги; Ua, ?/с, UK — падения напряжения соответственно в областях I, II и III.
Плазменная дуга появляется при обжатии электрической дуги струей газа, приводящем к уменьшению площади поперечного сечения дуги и существенному повышению ее температуры.
В установившейся плазменной дуге можно различить несколько однородных участков разряда (см. рис. 2.29). На поверхности электрода располагается катодная область. Между катодной областью и верхним срезом цилиндрической части формирующего сопла (см. рис. 2.30, а) находится закрытый участок дуги длиной /5 с относительно холодным потоком газа. Между входным и выходным срезами цилиндрической части сопла расположен участок дуги длиной /4, подвергаемый сжатию холодными стенками канала. Далее следует открытый участок длиной /3, стабилизированный соосными потоками плазмы и оболочкой более холодного газа, а также рабочий участок длиной /2. В зоне сварки располагается факел длиной /,.
Сжатие дуги и уменьшение ее поперечного сечения происходят в конусной части сопла. В результате сжатия температура центральной части дуги повышается до 10 000…50 000 К. Внутренняя часть дуги нагревается до температуры 10 000… 20 000 К, а наружная часть, соприкасающаяся со стенкой сопла, остается относительно холодной. Наружный слой играет роль электрической и тепловой изоляции. Он препятствует отклонению столба дуги от заданного направления и его замыканию на стенки сопла.
Различают плазменную дугу прямого и косвенного действия. В горелке с плазменной дугой прямого действия (см. рис. 2.30, а),.

Рис. 2.30. Схемы плазменных горелок (а, б) у стабилизации дуги (в, г):
/ — корпус горелки; 2 — газовая камера; 3 — электрод; 4 — формирующее сопло; 5 — плазма; 6 — преграда (свариваемые заготовки), 7 — ванна жидкого металла; 8 — охлаждающая камера; 9— радиальный поток газа; Ю — тангенциальный (вихревой) поток газа; /| — /5 — значения длины (/( — факела плазмы; /2 — рабочего участка; /3 — открытого участка; /4 — сжатого участка, /5 — закрытого участка) анодом являются свариваемые заготовки. При этом тепловая энергия поступает в зону сварки от всего столба дуги (КПД дуги составляет 60…70%). Однако такая дуга неприменима для обработки заготовок из диэлектрических материалов.
Дуга косвенного действия (рис. 2.30, б) горит между электродом и корпусом горелки (свариваемые заготовки не включены в электрическую цепь). Анодом является корпус горелки, а анодное пятно расположено внутри цилиндрического отверстия сопла. Поэтому температура и скорость течения плазмы на выходе из сопла резко уменьшаются, что приводит к снижению КПД дуги до 30…40% и стойкости сопла. Однако такая дуга позволяет обрабатывать диэлектрические и тонколистовые материалы.
Стабилизация дуги осуществляется двумя методами — осевым и вихревым. При осевой стабилизации (рис. 2.30, в) плазмообразующий газ подается вдоль оси электрода (траектория 9). Газ охлаждает электрод. Проходя через конусный канал сопла, газ обжимает столб дуги и стабилизирует се. Этот способ стабилизации предъявляет высокие требования к соосности электрода и каналов сопла.
При вихревой стабилизации (рис. 2.30, г) газ поступает по касательной к окружности поперечного сечения сопла и в камере 2 движется по спирали, охватывая столб дуги вихревым потоком, что обеспечивает автоматическую и точную фокусировку дуги по оси канала. Благодаря равномерной толщине газовой оболочки возрастает стойкость сопла.
Плазмообразующие газы (среды). Плазмообразующая среда должна обеспечить наибольшую удельную тепловую мощность дуги при заданном расходе газа и затраченной электрической энергии, а также возможность концентрации полученной энергии в тонком плазменном шнуре. Выбор среды определяется технологическими особенностями способа сварки, надежностью плазменной горелки, характеристиками имеющегося сварочного оборудования и экономическими показателями.
В состав плазмообразующей среды могут входить одно-, двухили многокомпонентные газы (аргон, азот, гелий, воздух, смесь аргона и азота с водородом, аммиак, вода).
Аргон — инертный одноатомный газ с низкой теплопроводностью. Он хорошо защищает вольфрамовый электрод и сопло от перегрева и разрушения. Вследствие низкой напряженности электрического поля в аргоне не требуется высокого напряжения для возбуждения дуги и обеспечивается надежный устойчивый процесс ее горения. Однако аргоноплазменная сварка приводит к появлению литой структуры сварного шва и зоны термического влияния.
Гелий — инертный одноатомный газ, обладающий большей теплопроводностью, чем ар’гон. Гелий обеспечивает в 4 раза более высокие значения напряженности электрического поля в столбе дуги и КПД преобразования электрической энергии в тепловую. Для ионизации гелия требуется больше энергии, поэтому чаще всего он используется в смеси с аргоном.
Гелий хорошо защищает вольфрамовый электрод от разрушения. При рабочих температурах (около 10 000 К) его теплопроводность существенно меньше, чем у меди, поэтому он обеспечивает более надежную тепловую защиту медного сопла.
Азот — двухатомный газ, хорошо стабилизирующий плазменную дугу. Поскольку в воздухе содержится 78% азота, вместо чистого азота можно применять воздух. При рабочих температурах энтальпия азота в 5 раз больше, чем у аргона. По сравнению с аргоном азот активнее взаимодействует с вольфрамом с образованием его нитридов, что снижает стойкость вольфрамовых электродов.
Наличие в техническом азоте примесей (до 1% кислорода) обусловливает формирование оксидов вольфрама. Поэтому желательно применять циркониевые или гафниевые электроды. Плазменная сварка в атмосфере азота сопровождается выделением оксидов азота, что требует наличия вытяжной вентиляции и использования индивидуальных средств зашиты дыхательных путей сварщика.
Воздух является сильным окислителем металлов из-за наличия в нем кислорода. Поэтому необходимо применять только циркониевые или гафниевые электроды. Напряженность электрического поля дуги в кислородной атмосфере ниже, чем в азотной, поэтому преобразование энергии менее эффективно. При взаимодействии кислородной плазмы с черными металлами интенсивно протекающие термохимические процессы обеспечивают более глубокое проплавление заготовок. Кислород активно окисляет металл заготовок, электрод и сопло.
Водород — двухатомный газ, обеспечивающий значительно более высокую напряженность электрического поля в столбе дуги, чем аргон, что предопределяет более эффективное преобразование электрической энергии в тепловую. Диссоциация и ионизация водорода происходят при более низких температурах, чем у гелия и аргона. Поэтому энтальпия водородной плазмы примерно в 4 раза больше, чем у аргоновой. Так как водород обладает высокой теплопроводностью, сопло быстро нагревается (перегревается) и разрушается.
Водород редко применяется как самостоятельный плазмообразующий газ. Чаще всего его используют в качестве добавки к аргону или азоту, в пропорции 2:1. Применение аргоноводородной смеси (содержащей до 35% водорода) обеспечивает получение чистых ровных кромок при резке алюминиевых сплавов.
Вода может использоваться как самостоятельная плазмообразующая среда или добавка к рабочему газу. При повышении температуры до 5 000 К вода полностью разлагается на водород и кислород. При этой температуре происходит диссоциация молекул водорода, сопровождающаяся поглощением теплоты, что приводит к интенсивному охлаждению периферийных слоев дуги и концентрации тепловой энергии по оси дуги. Возрастает температура ядра дуги и повышается ее проплавляющая способность. Одновременно контакт дуги с относительно холодной заготовкой вызывает взаимодействие водорода и кислорода с выделением дополнительного количества теплоты.
Техника безопасности. Наибольшую опасность для оператора при плазменной обработке представляют высокочастотный шум, интенсивное ультрафиолетовое излучение, высокое напряжение источников питания, брызги расплавленного металла, выделение аэрозолей сложного химического состава и токсичных газов.
При плазменной обработке генерируется шум в дйапазоне частот 50…40 000 Гц; его уровень на расстоянии 0,5 м от плазмотрона достигает 132 дБ, А (на 52 дБ, А больше нормы). Поэтому для защиты оператора необходимо устанавливать шумопоглощающие стеновые и потолочные панели в кабине сварщика и применять индивидуальные средства защиты органов слуха.
Эксплуатировать плазменную аппаратуру необходимо с соблюдением общих правил техники безопасности и производственной санитарии при электросварочных работах. В соответствии с ГОСТ.
1222—63* напряжение холостого хода источников питания для ручных работ не должно превышать 180 В при наличии автоматических устройств отключения источника в случае обрыва дуги и 90 В при отсутствии таких устройств.