Системы контроля за состоянием запасов
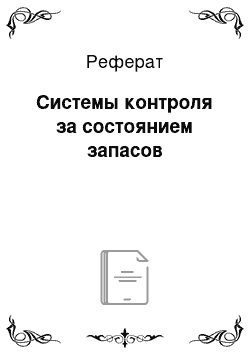
Минимум—максимум", как и система с установленной периодичностью пополнения запасов до постоянного уровня, включает элементы других основных систем. Она ориентирована на ситуацию, когда затраты на учет запасов и издержки на оформление заказа настолько значительны, что становятся соизмеримы с потерями от дефицита запасов. Поэтому в данной системе заказы производятся не через каждый заданный… Читать ещё >
Системы контроля за состоянием запасов (реферат, курсовая, диплом, контрольная)
Управление запасами предусматривает организацию контроля за их фактическим состоянием. Необходимость организации службы такого контроля обусловлена повышением издержек в случае выхода фактического размера запаса за рамки, предусмотренные нормами запаса.
Контроль за состоянием запасов и формирование заказа может осуществляться периодически, по одной из представленных систем:
- • системе оперативного управления — через определенный промежуток времени принимается оперативное решение: «заказывать» или «не заказывать», если заказывать, то какое количество единиц товара;
- • системе равномерной поставки — через равные промежутки времени заказывается постоянное количество единиц товара;
- • системе пополнения запаса до максимального уровня — через равные промежутки времени заказывается партия, объем которой, т. е. число единиц товара, равен разности установленного максимального уровня запасов и фактического уровня запасов на момент проверки. Размер заказа увеличивается на величину запаса, который будет реализован за период выполнения заказа.
Для ситуации, когда отсутствуют отклонения от запланированных показателей и запасы потребляются равномерно, теорией управления запасами предлагаются две основные системы:
- 1) система контроля за состоянием запасов с фиксированным размером заказа;
- 2) система контроля за состоянием запасов с фиксированным интервалом времени между заказами.
Основополагающий параметр системы с фиксированным размером заказа — размер заказа. Он строго зафиксирован и не меняется при изменении условий работы системы. Определение размера заказа — первая задача, которая решается при работе с данной системой управления запасами, причем заказ должен быть оптимальным, т. е. самым лучшим. Критерием оптимизации в данном случае служит минимум совокупных затрат на хранение запасов и повторение заказа.
Функционирование системы контроля за состояние запасов с фиксированным размером заказа приведено на рис. 10.5, а.
В системе с фиксированным интервалом времени заказы делаются в строго определенные моменты времени, отстоящие друг от друга на равные интервалы, которые корректируются на основе экспертных оценок.
Работа системы с фиксированным интервалом времени между заказами приведена на рис. 10.5, б.
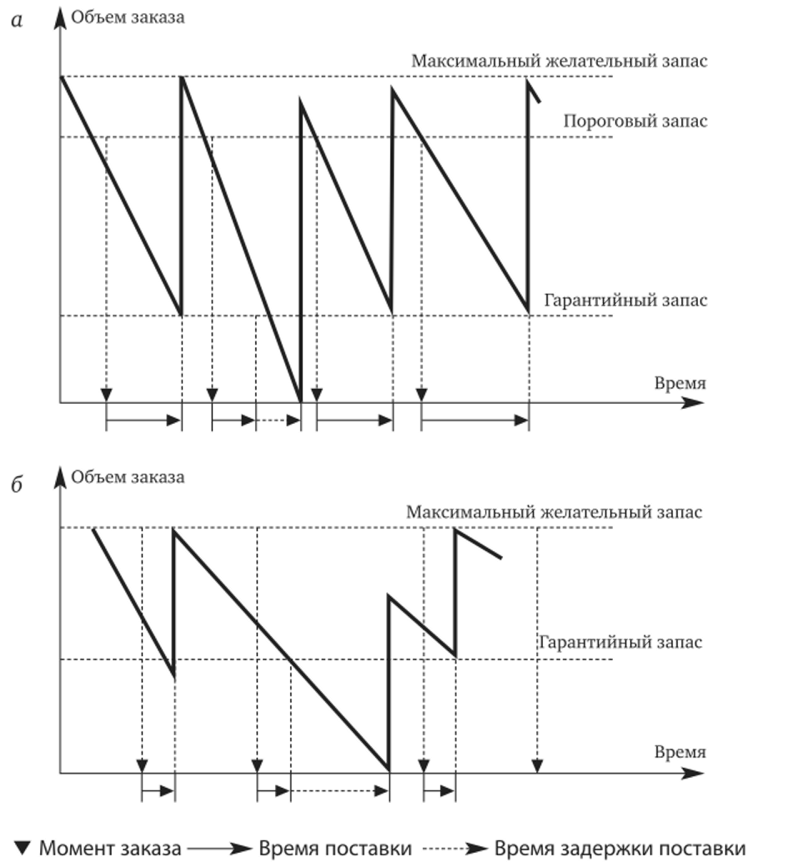
? Момент заказа-Время поставки… Время задержки поставки.
Рис. 10.5. Движение запасов в системе контроля за состоянием запасов с фиксированными размером заказа (а) и интервалом времени между заказами (б)
Так как в рассматриваемой системе «момент» заказа заранее определен и не меняется ни при каких обстоятельствах, постоянно пересчитываемым показателем является именно «размер» заказа. Его вычисление основывается на прогнозируемом уровне потребления до момента поступления заказа на склад предприятия. Расчет размера заказа в системе контроля за запасами с фиксированным интервалом времени между заказами проводится по формуле:

где РЗ — размер заказа, шт.; МЖЗ — максимальный желательный заказ, шт.; ТЗ — текущий заказ, шт.; ОП — ожидаемое потребление за время поставки, шт.
Согласно расчету размер заказа определяется таким образом, чтобы поставка пополняла запас на складе до желаемого уровня.
Обе рассмотренные системы имеют как преимущества, так и недостатки (табл. 10.6).
Таблица 10.6. Сравнение основных систем контроля за запасами.
Система. | Преимущество. | Недостаток. |
С фиксированным размером заказа. |
| Ведение постоянного контроля наличия запасов на складе. |
С фиксированным интервалом времени между заказами. | Отсутствие постоянного контроля наличия запасов на складе. |
|
В практической деятельности организаций и служб маркетинга используются и другие принципиальные системы регулирования запасов, учитывающие тот факт, что разные виды запасов имеют различный удельный вес в общей структуре расходов компании и применение точных методов расчета для всего объема запасов не всегда оправдано.
В экономике широко известно так называемое правило Парето (20/80), согласно которому множество управляемых объектов делится на две неравные части: лишь пятая часть (20%) всего количества объектов, с которыми приходится иметь дело, дает примерно 80% результатов. Вклад остальных 80% объектов составляет только 20% общего результата[1].
Например, в торговле 20% наименований товаров дает, как правило, 80% прибыли предприятия, остальные 80% наименований товара — лишь необходимое дополнение, обязательный ассортимент.
В целях контроля запасов используется вариация правила Парето, известная как метод АВС, предлагающий деление запасов на три группы в соответствии с их долей в материальных затратах. Метод АВС позволяет классифицировать запасы по определенному показателю значимости, обычно по годовому использованию конкретного товара в денежном выражении.
Категория А включает ограниченное количество наиболее ценных ресурсов, которые требуют постоянного и скрупулезного учета и контроля, возможно даже ежедневного (существенный вес — 20% номенклатуры, 80% затрат). Для таких ресурсов обязателен расчет оптимального размера заказа. Категория В составлена из запасов, которые в меньшей степени важны для предприятия и оцениваются при ежемесячной инвентаризации (30% номенклатуры, до 15% затрат). Для запасов этой категории, как и категории А, приемлемы методики определения оптимального размера заказа. Возможно применение концепции «красного света» — уровень возобновления устанавливается без расчета оптимальной партии, исходя из такого критерия, как время поставки.
Категория С включает широкий ассортимент оставшихся малоценных видов запасов, закупаемых обычно в большом количестве. Предметы категории С могут составлять до 50% по объему и всего лишь около 5—10% по цене. Уровень контроля также должен соответствовать этим соотношениям — концепция «двух ящиков» (заказ производится тогда, когда заканчивается первый ящик). Имеется в виду, что текущая величина запаса столь незначительна, что умещается в двух ящиках.
Наибольший эффект метод ЛВС дает в комбинации cXYZ-ана- лизом[2], позволяющим классифицировать запасы в зависимости от масштабов потребления и точности прогнозирования изменений в их потребности. Категория X — это группа, характеризующаяся стабильной величиной потребления и высокой точностью прогноза срока потребления. К категории Y относятся ресурсы, потребность в которых характеризуется известными тенденциями и средними возможностями их прогнозирования. Ресурсы, относимые к категории Z, используются нерегулярно, величину их потребления прогнозировать сложно. Наложение результатов AYZ-анализа на данные метода АВС позволяет разбить запасы на девять блоков, каждый из которых имеет две характеристики: стоимость запасов и точность прогнозирования потребности в них.
Для управления запасами готовой продукции с целью синхронизации производства и реализации, минимизации затрат по обслуживанию используется модификация модели EOQ — модель оптимальной партии заказа готовой продукции (Economic Production Run, EPR):

где V — объем выпуска в анализируемом периоде; С" — издержки по переработке; Сх — стоимость хранения единицы готовой продукции.
Указанная модель может быть использована лишь теми компаниями, которые имеют возможность менять размер выпускаемой партии готовой продукции в различные отчетные периоды.
В практической деятельности компании могут использовать и другие системы регулирования запасов, основанные на различных стратегиях пополнения запасов, т. е. на определенных правилах этого пополнения. Параметрами этих правил являются величина имеющихся на складе запасов, допустимые колебания уровня запасов, размеры заказа на пополнение запасов, его периодичность и др. Системы различаются между собой в зависимости от того, какие из параметров выбраны в качестве регулирующих.
К другим системам контроля за запасами можно отнести: систему с установленной периодичностью пополнения запасов до постоянного уровня, систему «минимум—максимум», систему «точно в срок».
Система с установленной периодичностью пополнения запасов до постоянного уровня, как и система с фиксированным интервалом времени между заказами, имеет входной параметр «период времени между заказами». В отличие от основной системы она ориентирована на работу при значительных колебаниях потребления. Чтобы предотвратить завышение объемов запасов, содержащихся на складе, или их дефицит, заказы производятся не только в установленные моменты времени, но и при достижении запасом порогового уровня.
Таким образом, рассматриваемая система включает элемент системы с фиксированным интервалом времени между заказами и элемент с фиксированным размером заказа.
«Минимум—максимум», как и система с установленной периодичностью пополнения запасов до постоянного уровня, включает элементы других основных систем. Она ориентирована на ситуацию, когда затраты на учет запасов и издержки на оформление заказа настолько значительны, что становятся соизмеримы с потерями от дефицита запасов. Поэтому в данной системе заказы производятся не через каждый заданный интервал времени, а только при условии, что запасы на складе в этот момент оказались равными или меньше установленного минимального уровня.
Перспективным методом сокращения запасов, повышения гибкости и возможности противостояния возрастающей конкуренции считается метод «точно в срок» (Just in Time, JIT), представляющий собой систему синхронного производства и поставки материалов, деталей в требуемом количестве и в нужное время. В противоположность традиционным методам управления, в соответствии с которыми плановая служба выдает производственные задания всем отделам производства, при методе «точно в срок» централизованное планирование касается только последнего звена производственного процесса — склада готовой продукции.
Таким образом, в связи с расширенной номенклатурой товаров и повышением издержек производства построение эффективных систем контроля за движением запасов обеспечивает постоянный мониторинг состояния запасов с использованием сравнительного анализа (сравнение нормативных параметров с фактическими) и создает базу для решения логистами проблемы размещения и движения товаров.
В сферу ответственности финансового менеджера входит определение оптимального уровня затрат, связанных с запасами, анализ движения и остатков запасов на складах и в незавершенном производстве в денежной форме, определение потребности в источниках финансирования поддержания оптимального уровня запасов, а также оценка влияния размеров и движения запасов на уровень ликвидности и рентабельности компании.