Высоколегированные стали.
Сварка и пайка в авиационной промышленности
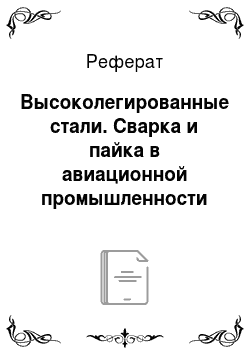
Свариваемость сталей мартенситного класса ограничена главным образом возможностью образования при сварке хрупких структур в шве и околошовной зоне, а также горячих и холодных трещин. При сварке приходится учитывать более высокую теплопроводность этих сталей, что ускоряет теплоотвод от шва и способствует увеличению скорости охлаждения и, следовательно, может привести к образованию холодных трещин… Читать ещё >
Высоколегированные стали. Сварка и пайка в авиационной промышленности (реферат, курсовая, диплом, контрольная)
К ним относятся стали с суммарным содержанием легирующих элементов более 10%. Высоколегированные стали могут быть ферритного, аустенитного и мартенситного классов, а также переходных: аустенитно-ферритных, аустенитно-мартенситных и мартенситно-ферритных. По основному легирующему элементу принято указанные стали делить на высокохромистые, хромоникелевые, хромоникелемарганцевые и др.
Высокохромистые стали в зависимости от содержания углерода и хрома могут быть мартенситного класса (20X13, 14X17Н2 и др.), ферритно-мартенситного (12X13, 14Х12В2МФ и др.), ферритного (12X17, 15Х25Т, 08X17Т и др.).
Свариваемость сталей мартенситного класса ограничена главным образом возможностью образования при сварке хрупких структур в шве и околошовной зоне, а также горячих и холодных трещин. При сварке приходится учитывать более высокую теплопроводность этих сталей, что ускоряет теплоотвод от шва и способствует увеличению скорости охлаждения и, следовательно, может привести к образованию холодных трещин. Этому же способствует мартенситный распад при пониженных температурах, что исключает процесс самоотпуска, делает сварное соединение малопластичным.
Существенным недостатком хромистых сталей мертенситного класса является их разупрочнение под влиянием сварочного нагрева. Восстановить первоначальные свойства указанных сталей можно только трудоемкой двойной термообработкой — нормализацией с отпуском. Для сварки сталей мартенситного класса рекомендуются дуговая, электронно-лучевая, лазерная и контактная сварка. Основным технологическим приемом, направленным на получение высококачественного соединения, является предварительный и сопутствующий подогрев, который исключает отрицательное влияние повышенной теплопроводности этих сталей. Так как холодные трещины в мартенситных сталях могут образовываться немедленно после сварки, то приходится находить способы замедления охлаждения швов при температурах мартенситного превращения 373—423 К в зависимости от конкретной марки стали и толщины металла. Это приводит к образованию менее хрупких структур и уменьшает количество остаточного аустенита. Практически такой тепловой режим можно получить, например, при предварительном и последующем нагреве шва в процессе сварки и с помощью токов высокой частоты. Установленные перед сварочной головкой и после нее индукторы подогревают шов и прилегающую к нему зону до необходимых температур. Подобная технология часто применяется при сварке корпусов твердотопливных реактивных двигателей из высокопрочных сталей.
Склонность к образованию хрупких структур требует особых условий при контактной сварке сталей мартенситного класса. Она производится на машинах, обеспечивающих трехимпульсную подачу тока: подогрев — сварка — отпуск.
Стали с повышенным содержанием хрома при сварке могут окисляться с образованием тугоплавкого оксида хрома, который в ряде случаев препятствует хорошему формированию обратной стороны шва. Этого можно избежать, защищая шов от окисления сваркой на подкладках, плотно прилегающих к шву, с подачей снизу аргона, нанесения специальных флюсов на свариваемые кромки с обратной стороны шва.
Детали малой толщины из сталей ферритного или ферритномартенситных класса свариваются удовлетворительно, однако при сварке деталей больших толщин наблюдаются значительное увеличение зерен и снижение механических свойств. В таких случаях для восстановления механических свойств металла следует применять предварительный подогрев и термическую обработку после сварки. Однако и предварительный подогрев, и термическая обработка отличаются от подогрева и термообработки сталей мартенситного класса. Прежде всего пониженная теплопроводность сталей ферритного класса позволяет уменьшить температуру подогрева до 423 К. Стремление ограничить увеличение зерен при сварочном нагреве приводит к выбору таких методов сварки, которые обеспечивают минимальное тепловложение: дуговая, контактная, электронно-лучевая и т. п. Термическая обработка в основном направлена на повышение стойкости сварных соединений к межкристаллической коррозии и состоит в длительном отжиге при температурах 1033—1053 К с последующим ускоренным охлаждением. При отсутствии особых требований по стойкости к межкристаллитной коррозии можно термическую обработку ограничить отпуском при 973—1023 К.
Увеличение зерна в шве устраняется введением в проволоку или покрытие электрода титана, ванадия, алюминия.
Хромоникелевые стали — это коррозионно-стойкие жаропрочные стали с высоким содержанием хрома и никеля (стали 08Х18Н10, 12Х18Н10Т, 08Х18Н12, 20Х13Н18 и др.). При их сварке могут образовываться горячие трещины, поэтому для улучшения свариваемости сталей типа Х18Н9 в шов вводят легирующие добавки для измельчения зерен или создания в шве двухфазной аустенитно-ферритной структуры. Последнее не рекомендуется для высокохромистых сталей мартенситного класса, так как снижает их стойкость против образования холодных трещин, и аустенитного класса из-за снижения свойств металла шва по сравнению с основным металлом. Другой особенностью сварки сталей аустенитного класса является ухудшение их антикоррозионных свойств под влиянием сварочного нагрева. Это происходит в интервале температур 723—1123 К, когда резко возрастает скорость диффузии углерода в межкристаллитные прослойки и начинается обеднение границ зерен свободным хромом в результате образования карбидов хрома.
Быстрее всего металл теряет стойкость против межкристаллитной коррозии (рис. 4.15, заштрихованная область) при нагреве металла в интервале температур 1003—1023 К. При работе с такими сталями в агрессивной среде в околошовной зоне наблюдаются случаи межкристаллитной коррозии и растрескивание металла под напряжением. Для предупреждения межкристаллитной коррозии целесообразно добавлять в сталь в небольших количествах титан и особенно ниобий, располагающийся в пограничных слоях аустенитных зерен. Эти элементы химически более активны по отношению к углероду и образуют с ним карбиды, высвобождая тем самым хром (стали 12Х18Н10Т, 08Х18Н12Б). Рекомендуется также снижать количество углерода в стали и сварочной проволоке. Так, высокой стойкостью против межкристаллитной коррозии обладает сталь 00Х18Н10 (С < 0,04%), однако эта и подобные ей стали имеют высокую стоимость.

Рис. 4.15. Зависимость межкристаллитной коррозии от температуры.
и времени Повысить стойкость против межкристаллитной коррозии можно выдержкой после сварки изделия при температуре 1123—1173 К в течение 2—3 ч с ускоренным последующим охлаждением, что приводит к восстановлению содержания хрома в межкристаллитных прослойках, а также подбором соответствующих режимов сварки.
В авиационной промышленности применяются двухфазные хромоникелевые стали переходных классов. По сравнению с однофазными их свариваемость выше, особенно сопротивляемость образованию трещин и межкристаллитной коррозии. Мартенситно-стареющие коррозионно-стойкие стали (08Х15Н5Д2Т и др.) могут в зоне сварного соединения иметь ослабленные участки в отношении величины ударной вязкости и стойкости против коррозии. Антикоррозионные свойства сварных соединений восстанавливаются после полной термической обработки. Рекомендуется для этих же целей отпуск перед сваркой при температуре 873—923 К. Для предотвращения старения металла в зоне сварного соединения в процессе эксплуатации конструкции и последующего снижения его пластических свойств применяют термообработку после сварки (при температуре 873—923 К).
Хромоникелевые стали сваривают практически всеми методами сварки. В авиационной промышленности широко применяются аргонодуговая сварка неплавящимся и плавящимся электродами, в некоторых случаях — в углекислом газе, электронно-лучевая, плазменная. Режимы стремятся подбирать так, чтобы сварка происходила при малых значениях погонной энергии. Успешно сваривают хромоникелевые стали контактной сваркой.