Основные элементы прессового оборудования
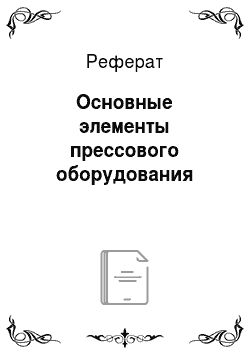
При необходимости в прессах используются ступенчатые цилиндры (рис. 4.49, д). В этих цилиндрах реализуется несколько скоростей за счет комбинации дифференциальных поршней с плунжерами. Ускоренное движение происходит при подаче под давлением рабочей жидкости через отверстие I в полость штока 12 поршня 10. Эта полость работает как подвижный гидроцилиндр, в котором размещен неподвижный плунжер 9… Читать ещё >
Основные элементы прессового оборудования (реферат, курсовая, диплом, контрольная)
Цилиндры гидравлических прессов
Цилиндры являются одними из основных и наиболее ответственных деталей прессов. Гидроцилиндры работают в сложных условиях нагружения, которые зависят не только от условий работы и конструкции самих цилиндров, но и от конструкции сопряженных с ними деталей. Конструкция цилиндра выбирается в зависимости от величины требуемого усилия, условий работы, вида рабочей жидкости и гидравлического давления, с которым она подается в гидроцилиндр. Влияют на конструкцию и технологические возможности предприятия — изготовителя пресса.
Цилиндры бывают поршневые, плунжерные, простые и дифференциальные.
Конструкция поршневых цилиндров (рис. 4.49, а) обеспечивает как создание необходимого усилия и рабочее движение поршня 2 с соединенным с ним штоком 3, так и возвратный ход поршня со штоком. Поршень разделяет цилиндр 1 на две полости: поршневую и штоковую. При поступлении рабочей жидкости под давлением р через отверстие I в поршневой полости создается давление. Одновременно штоковая полость II соединяется со сливом. На поршень начинает действовать сила.

где D — диаметр поршня.

Рис. 4.49. Схемы цилиндров гидравлических прессов.
Сила F обеспечивает рабочее движение поршня со штоком. Возвратный ход поршня и штока происходит после подачи давления рабочей жидкости в штоковую полость через отверстие II и соединения поршневой полости со сливом. Усилие на поршне при возвратном ходе существенно меньше, чем при рабочем, и составляет:

где d — диаметр штока.
Отличаются не только усилия при прямом и возвратном ходах, но и скорости передвижения поршня со штоком. Это объясняется тем, что при одной и той же производительности насоса, подающего рабочую жидкость, объемы поршневой и штоковой полостей отличаются друг от друга.
Конструкция поршневого цилиндра предусматривает наличие двух видов уплотнений: неподвижного 4 в месте сопряжения цилиндра с подвижным штоком и подвижного 5 в месте сопряжения поршня с цилиндром.
Цилиндры поршневого типа можно подразделить на простые (рис. 4.49, б) и дифференциальные (см. рис. 4.49, а). В простых цилиндрах поршень имеет одинаковые скорости прямого и обратного ходов и снабжен двухсторонним штоком. В дифференциальных цилиндрах, как было показано выше, поршень развивает различные усилия и скорости при прямом и обратном ходах.
Плунжерные цилиндры (рис. 4.49, в) имеют более простую конструкцию. В них давление рабочей жидкости, поступающей через отверстие I, воспринимается плунжером 6, имеющим меньший диаметр, чем внутренний диаметр гидроцилиндра 1. Такая конструкция позволяет существенно упростить обработку внутренней поверхности цилиндра и иметь вместо двух видов уплотнений только один — неподвижное уплотнение 4 в месте сопряжения цилиндра с подвижным плунжером. Существенным недостатком плунжерных цилиндров является отсутствие обратного хода. Для осуществления обратного хода при использовании плунжерных цилиндров приходится устанавливать так называемые возвратные цилиндры (рис. 4.49, г). Основное усилие и ход подвижной плиты 13 осуществляется плунжерным цилиндром 8. Возвратный ход обеспечивается двумя возвратными цилиндрами 7, расположенными симметрично относительно рабочего цилиндра 8. Полость цилиндра 8 соединяется со сливом, а в полости цилиндров 7 под давлением подается рабочая жидкость. Возвратные цилиндры должны преодолевать только силы тяжести и трения, возникающие при движении вверх, поэтому диаметры их плунжеров значительно меньше, чем диаметр плунжера рабочего цилиндра, и, следовательно, при той же самой производительности насоса скорость обратного хода всегда выше, чем рабочего. На прессах разной конструкции устанавливается различное число возвратных цилиндров.
Возвратные цилиндры могут вообще отсутствовать. Так, в прессах нижнего давления с массивными подвижными частями и небольшим возвратным ходом обратное перемещение осуществляется за счет сил тяжести после соединения полости рабочего плунжерного цилиндра со сливом.
При необходимости в прессах используются ступенчатые цилиндры (рис. 4.49, д). В этих цилиндрах реализуется несколько скоростей за счет комбинации дифференциальных поршней с плунжерами. Ускоренное движение происходит при подаче под давлением рабочей жидкости через отверстие I в полость штока 12 поршня 10. Эта полость работает как подвижный гидроцилиндр, в котором размещен неподвижный плунжер 9. при создании в его полости давления он начинает движение вправо. Благодаря небольшому внутреннему диаметру полости реализуется высокая скорость перемещения штока 12 при сравнительно небольшом усилии. По мере продвижения поршня 10 через отверстие II происходит заполнение поршневой полости цилиндра 11. На конечной стадии передвижения штока 12 необходимо снизить скорость его движения и создать большое усилие. Для этого в поршневой полости гидроцилиндра 11 создается давление рабочей жидкости, скорость движения поршня со штоком снижается, а рабочее усилие возрастает. Для возврата поршня со штоком в первоначальное положение рабочая жидкость под давлением подается через отверстие III в штоковую полость цилиндра 11, а его поршневая полость соединяется со сливом.
Конструкцию гидроцилиндра плунжерного типа рассмотрим на примере главного рабочего цилиндра, установленного на рамном прессе верхнего давления с верхним расположением гидробака (рис. 4.50). Обычно цилиндр изготавливается кольцевым сверлением из стальной поковки. В связи с отсутствием подвижных уплотнений, находящихся в контакте с внутренней стенкой цилиндра, отпадает необходимость в шлифовке и упрочнении его внутренней поверхности. Цилиндр 2 крепится в верхней неподвижной поперечине (архитраве) при помощи промежуточной втулки 5 и гайки 1. Контакт плунжера с цилиндром достигается при помощи направляющей втулки 4. Уплотнение плунжера 3 осуществляется манжетой 14. Манжета и направляющая втулка удерживаются втулкой 6 и фланцем 7. Во втулке 6 установлены упругие резиновые кольца 11, 13 для предотвращения утечек рабочей жидкости по плунжеру.

Рис. 4.50. Гидроцилиндр плунжерного типа.
Масло, просочившееся через уплотнение 14, отводится через отверстие 12. Это отверстие, связанное трубкой со сливным баком, служит также предохранительным устройством. В случае, если не сработает конечный выключатель, фиксирующий крайнее нижнее положение плиты и плунжера, то плунжер, опустившись ниже манжеты 14, откроет путь маслу из рабочего цилиндра на слив.
Уплотнение 15 обеспечивает герметичность соединения верхнего гидробака с внешней поверхностью цилиндра.
Крепление рабочей плиты (ползуна) к плунжеру достигается при помощи винта 8 и шайбы 9.
При транспортировке и ремонте пресса плунжер можно фиксировать в цилиндре в верхнем положении при помощи винта 10. При работе пресса хвостовик винта 10 не должен выступать из фланца 7 и касаться плунжера.
На верхнем торце цилиндра закреплены шпильками корпус клапана наполнения и (с помощью разрезных колец) бак наполнения.
В качестве примера конструкции гидроцилиндра поршневого типа рассмотрим цилиндр выталкивания рамного пресса верхнего давления (рис. 4.51). Он представляет собой сквозной цилиндр 4 с крышкой 1, уплотняемой манжетой 13. В цилиндре расположен составной дифференциальный поршень, состоящий из штока 3, на котором при помощи гайки 12 закреплен поршень 2. Уплотнение обеспечивается резиновым упругим кольцом 11 и манжетами 9. Направляющая втулка 6 крепится гайкой 7 и уплотняется резиновым кольцом 10.
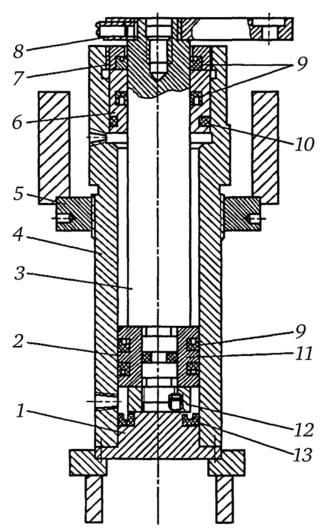
Рис. 4.51. Гидроцилиндр поршневого типа.
Шайба 8 служит для закрепления штанги механизма конечных выключателей. Выталкивающий цилиндр крепится в станине гайкой 5.
Рабочие жидкости, применяемые для привода гидравлических цилиндров, должны хорошо работать в широком диапазоне давлений, скоростей и температур. Жидкость не должна вызывать коррозии, содержать или поглощать значительное количество воздуха, а также образовывать пары или пену. Она должна обладать хорошей смазывающей способностью и оптимальной для данных условий работы вязкостью, с тем чтобы избежать утечек или чрезмерных потерь на трение.
В качестве рабочей жидкости обычно применяются очищенные минеральные масла. Масло не должно содержать примесей, выделяющих омыляемые жиры, кислоты и асфальтены. При нагреве масла до рабочей температуры оно не должно коксоваться. Минеральные масла начинают заметно испаряться при температуре, которая на 80 градусов ниже температуры их вспышки, поэтому во избежание парообразования следует применять масло, имеющее температуру вспышки на 80—100 °С выше рабочей температуры.
Как уже говорилось, в некоторых типах современных прессов верхнего давления, в которых давление жидкости в наполнительной системе равно атмосферному, гидробак располагается непосредственно над рабочим цилиндром, а между баком и цилиндром устанавливается клапан наполнения. Этот клапан при холостом и возвратном ходах подвижной плиты соединяет рабочий цилиндр с наполнительным баком. При холостом ходе жидкость поступает из наполнительного бака в рабочий цилиндр, а при возвратном — наоборот.
Клапан наполнения, показанный на рис. 4.52, устанавливается в наполнительном баке вертикально и крепится шпильками к рабочему цилиндру пресса. Открытие клапана 6 осуществляется за счет давления жидкости на поршень 2. Для подвода жидкости используется отверстие 4. Разгрузочный клапан 3 обеспечивает плавную разгрузку рабочего цилиндра от высокого давления после совершения рабочего хода. Через отверстие 5 происходит слив жидкости в момент снижения давления в рабочем цилиндре. Закрывается наполнительный клапан с помощью пружины 1.
При высоких скоростях движения жидкости в рабочих органах машины, маленьких выдержках под давлением и надежных уплотнениях целесообразно применять менее вязкие жидкости, так как потери энергии на возмещение утечек будут меньше, чем потери на преодоление сил трения, которые при вязких маслах на больших скоростях резко возрастают.
Необходимо помнить, что масло, применяемое для приводов гидроцилиндров, под влиянием температуры и давления изменяет свою плотность и объем. Упругая деформация (сжимаемость) жидкости для гидравлических систем является отрицательным фактором, так как ввиду практической необратимости энергии, расходуемой на сжатие жидкостей, общий КПД приводов понижается. Сжимаемость жидкости оценивается коэффициентом относительного объемного сжатия (3, который характеризует изменение объема жидкости, приходящееся на единицу изменения давления:
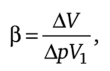
где Vl — начальный объем жидкости при атмосферном давлении; Ар — приращение давления, действующего на жидкость; ДУ — изменение объема жидкости при изменении давления на Ар.
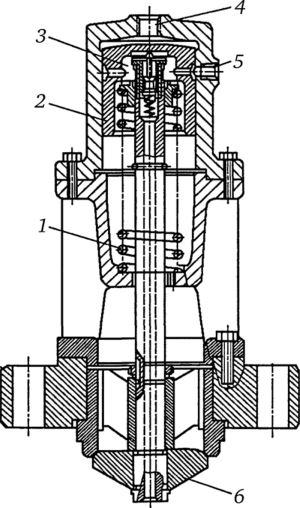
Рис. 4.52. Клапан наполнения.
Величина, обратная (3, называется объемным модулем упругости жидкости при всестороннем сжатии (Е = 1/(3). Объемный модуль упругости Е при 20 °C и атмосферном давлении для минеральных масел, используемых в гидросистемах прессов, составляет 1350—1750 МПа.
Очистка рабочей жидкости служит для продления срока службы уплотнений, цилиндров, а также распределительных устройств прессов. Как правило, очистка производится отстаиванием и фильтрацией. Наибольшее распространение для фильтрации масел получили пластинчатые фильтры. Для очистки от мельчайших примесей ферромагнитных частиц пользуются магнитными фильтрами.
Уплотнения являются необходимой и ответственной частью всех гидравлических прессов. Они должны исключать или сводить к минимуму утечки рабочей жидкости и предотвращать попадание во внутреннюю полость гидравлических систем пыли, абразивное действие которой может привести к преждевременному износу трущихся поверхностей рабочих органов.
Уплотнительные устройства делятся на уплотнения неподвижных деталей и уплотнения подвижных соединений. В свою очередь, устройства для уплотнения подвижных соединений делятся на уплотнения деталей вращения и уплотнения деталей с возвратно-поступательным движением.
По характеру взаимодействия с уплотняемыми деталями все уплотнения делятся на контактные и бесконтактные. Контактные уплотнения осуществляют герметизацию за счет плотного прилегания к поверхностям сопрягаемых деталей. Контактные уплотнения (сальниковые, манжетные, упругими разрезными и неразрезными кольцами и др.) обеспечивают высокую надежность герметизации. Однако при движении в связи с трением происходит износ как уплотнений, так и герметизируемых поверхностей, что ограничивает срок их службы. Кроме того, на преодоление сил трения расходуется значительная энергия.
При работе бесконтактных уплотнений жидкость запирается без непосредственного контакта уплотняющих элементов с перемещающимися деталями.
Для изготовления большинства уплотнений требуются специализированное оборудование и оснастка, которые окупаются только при массовом изготовлении уплотнений. В целях обеспечения взаимозаменяемости все основные типоразмеры и конструктивные параметры уплотнений стандартизованы.
Ниже рассмотрим уплотнения, нашедшие наибольшее применение в прессостроении.
Металлические поршневые кольца являются наиболее простыми и долговечными из применяемых уплотнений между внутренней поверхностью цилиндра и поршнем, совершающем возвратно-поступательное движение (рис. 4.53).

Рис. 4.53. Схемы уплотнений с помощью металлических разрезных.
поршневых колец Схема действия такого уплотнения показана на рис. 4.54. Кольцо из положения, представленного на рис. 4.54, а, под действием давления жидкости устанавливается в одно из рабочих положений (см. рис. 4.54, бив). Наружный диаметр кольца всегда несколько больше внутреннего диаметра цилиндра. При монтаже кольцо, в котором обязательно предусматривается разрез (замок), сжимается, а после монтажа за счет своей упругости плотно прижимается к внутренней поверхности цилиндра. К силам упругости прибавляется сила, возникающая при давлении рабочей жидкости на внутреннюю (нижнюю) поверхность кольца. Кроме того, давление рабочей жидкости обеспечивает плотное прижатие кольца к боковой поверхности канавки.

Рис. 4.54. Схема работы металлических разрезных поршневых колец.
Поршневые кольца применяются для уплотнения как поршней, так и штоков, причем в последнем случае они должны за счет упругости плотно охватывать шток (см. рис. 4.53, а).
К недостаткам металлических поршневых колец относится необходимость соблюдения жестких допусков на изготовление сопрягаемых деталей, а также чувствительность к нарушениям качества и точности обработки. Кроме того, эти уплотнения не обеспечивают полной герметизации.
Наиболее широко эти кольца применяются для уплотнения поршней силовых цилиндров. В уплотнительном узле применяется одно (см. рис. 4.53, б) или несколько колец (см. рис. 4.53, в), однако герметизация осуществляется в основном первым кольцом (со стороны действия давления).
Опыт показывает, что второе уплотнительное кольцо со ступенчатым замком снижает утечки примерно на 15%. Однако при применении нескольких колец удлиняется межремонтный срок уплотнительного узла, так как по мере износа первого со стороны давления, а следовательно, более нагруженного кольца в работу вступают последующие кольца.
Поршневые кольца изготавливаются из кованой бронзы, перлитного чугуна с высокими механическими и антифрикционными свойствами и стали. В некоторых случаях применяют графит или фторопласт. Желательно подобрать материал колец так, чтобы он составлял с цилиндром и поршнем антифрикционную пару.
Применяют прямой (рис. 4.55, а), косой (рис. 4.55, б) и ступенчатый (рис. 4.55, в) стыки (замки). Прямой и косой стыки применяют при средних давлениях (прямой — до 5 МПа, косой под углом 60° — от 5 до 20 МПа), а ступенчатый — при более высоких давлениях. Благодаря тому что в ступенчатом замке (см. рис. 4.55, в) стыкующиеся ступенчатые концы кольца перекрывают друг друга, уменьшается стыковой зазор и соответственно повышается герметичность соединения. Часто одну из сопряженных поверхностей в замке выполняют плоской (параллельной торцовой поверхности), а вторую — выпуклой (рис. 4.55, г), поэтому повышается давление в стыке кольца под нагрузкой, что способствует повышению герметичности.
Кольца со ступенчатым замком практически можно применять при диаметрах поршня не менее 35 мм. При меньших диаметрах поршня кольца с этим стыком не используют из-за трудности монтажа.
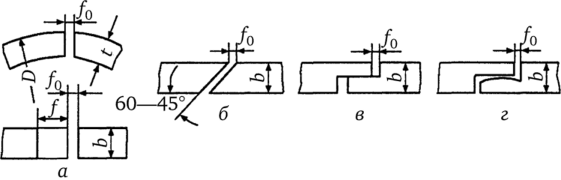
Рис. 4.55. Схемы замков металлических разрезных поршневых колец.
Величина стыкового зазора / + /0 кольца в свободном его состоянии (см. рис. 4.55, а) и величина/, на которую этот зазор уменьшится при монтаже поршня с кольцом в цилиндр, определяют напряжение кольца в сжатом положении и при надевании его на поршень. Для практических расчетов можно пользоваться величиной.

где t — радиальная толщина кольца.
При выборе ширины кольца может быть использована зависимость.

Резиновые уплотнительные кольца нашли в последнее время широкое применение как для уплотнения деталей, имеющих возвратнопоступательное или вращательное движение, так и для уплотнения неподвижных соединений.
На рис. 4.56 показаны основные конструкции уплотнительных колец. Наиболее распространенными являются О-образные кольца (рис. 4.56, а и 4.57, а), которые могут уплотнять в обоих направлениях и устанавливаются в канавки прямоугольной формы. Кольцо при установке подвергается диаметральному сжатию с силой, составляющей примерно 10% от усилия, которое будет действовать на кольцо во время работы (рис. 4.57, б). При движении поршня кольцо, упруго деформируясь под влиянием перепада давлений, обеспечивает уплотнение (рис. 4.57, в). При изменении направления рабочей жидкости происходит перемещение кольца и оно прижимается к другой стенке канавки. Размеры уплотняемых деталей, канавок, зазоров, колец и чистота обработки при уплотнении кольцами круглого сечения регламентируются ГОСТ 9833–73. Эти кольца рекомендуются для давления до 10 МПа, а при применении защитных шайб — до 20 МПа.

Рис. 4.56. Схемы установки упругих резиновых уплотнительных колец.

Рис. 4.57. Схема установки и работы О-образного упругого резинового уплотнительного кольца.
Х-образное кольцо (рис. 4.56, б) с четырьмя округлыми ребрами может ставиться в обычную канавку под О-образное кольцо; область применения и условия работы те же, что и у О-образных колец, но Х-образные кольца не подвержены спиральному скручиванию, поэтому их целесообразно применять для уплотнения вращающихся деталей.
D-образное кольцо (рис. 4.56, в) может служить для уплотнения штоков при возвратно-поступательном движении. При монтаже необходимы подкладные кольца, которые исключают выдавливание D-образного кольца в зазор при высоких давлениях.
Т-образное кольцо (рис. 4.56, г) не подвержено спиральному скручиванию; эти кольца чаще используются на поршнях и штоках с возвратно-поступательным движением. Для работы Т-образного кольца необходимы подкладные металлические кольца, которые исключают выдавливание его в зазор. Рекомендуются для работы под высоким давлением (до 140 МПа).
А-образное кольцо (рис. 4.56, д) имеет в поперечном сечении форму треугольника. В связи с высоким трением срок службы кольца невелик. Применяются такие кольца относительно редко.
При установке упругих колец предусматривают хорошую входную фаску и закругленные кромки, иначе при сборке кольцо может быть защемлено или подрезано.
Более плотная посадка колец способствует повышению эффективности уплотнения, но увеличивает трение и снижает срок службы колец. Удлинить срок службы уплотнения можно за счет высокой чистоты обработки канавки и рабочих поверхностей, по которым перемещается кольцо.
В целях уменьшения выдавливания упругого кольца в зазор могут быть также использованы подкладные шайбы из металла, пластмассы или кожи.
Манжетные уплотнения являются наиболее распространенными устройствами для уплотнения подвижных частей в гидравлических прессах. В зависимости от конструкции и назначения манжеты делятся на воротниковые (U-образные), полуворотниковые (V-образные или шевронные), манжеты штока и поршневые манжеты.
Манжетные уплотнения могут работать под внутренним давлением, когда манжета прижимается жидкостью к уплотняемой поверхности. В тех случаях, когда уплотнение должно быть двухсторонним (дифференциальный плунжер), ставится не менее двух манжет, обращенных своими основаниями друг к другу.
За счет собственной упругости или расклинивающего действия манжетодержателя борт манжеты предварительно прижимается к уплотняемой поверхности. Герметичность во время работы обеспечивается за счет расклинивающего действия давления рабочей жидкости.
Манжетное уплотнение является самоуплотняющимся с самонастраивающейся силой прижатия, зависящей от рабочего давления.
Манжеты изготавливают из различных сортов резины, прорезиненной ткани, полиамидов, поливинилхлоридных пластиков и других полимерных материалов, а также из кожи. Манжеты из пластмасс и резины изготавливаются горячим прессованием или литьем под давлением.
На рис. 4.58 показана конструкция резиновой воротниковой манжеты; все размеры манжеты лимитируются ГОСТ 14 896–84.

Рис. 4.58. Воротниковая манжета.
Описываемые манжеты имеют плоское основание, что упрощает конструкцию нажимного кольца и пресс-формы для изготовления манжет, а главное — уменьшает возможность разрыва основания манжеты, так как все элементы ее подвергаются в основном деформации сжатия. Борта манжеты имеют треугольную форму, при этом вершины треугольника (усы) разведены в разные стороны. Такая конфигурация обеспечивает хорошее уплотнение даже при низком давлении рабочей жидкости.
Манжеты шевронные многорядные (ГОСТ 22 704—77), конструкция которых изображена на рис. 4.59, изготавливаются из хлопчатобумажной ткани, с двух сторон пропитанной графиторезиновой смесью. Рабочая высота отдельно взятой шевронной манжеты недостаточна для обеспечения герметичности, поэтому манжеты этого типа используются в виде пакета, набранного из нескольких манжет. Манжеты используются совместно с «кольцом в манжету» (опорное кольцо) и «кольцом на манжету» (нажимное кольцо), изготовленными из того же материала, что и манжеты, либо из бронзы или пластмассы. Шевронные манжеты рекомендуется использовать на давление до 50 МПа.
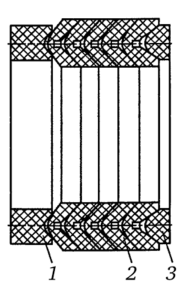
Рис. 4.59. Шевронные манжеты:
1 — опорное кольцо; 2 — шевронное кольцо; 3 — нажимное кольцо В некоторых случаях, например когда есть возможность легко извлечь плунжер из цилиндра, используются закладные однорядные манжеты (рис. 4.60), применяющиеся без нажимных и опорных колец. Для установки такой манжеты в цилиндре выполняют проточку, в которую запрессовывают манжету.
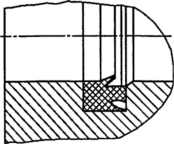
Рис. 4.60. Схема установки закладной манжеты.
Следует иметь в виду, что теплостойкость манжет невелика: кожаные манжеты растительного дубления рекомендуется применять при температуре до 40 °C, хромового дубления — до 70 °C, резиновые — до 80 °C, поливинилхлоридные — до 60 °C.