Проектирование станка для резки полосовых заготовок
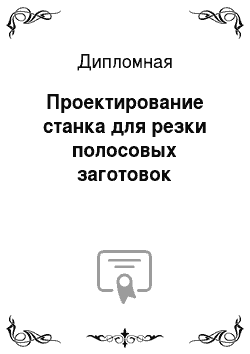
Рисунок 3 — Размеры рабочей поверхности стола Для точного выставления торцевого зазора необходимо ослабить стопорный винт на защитном кольце (рисунок 4 вид А) верхнего ножа, затем переместить кольцо влево открыв доступ к месту размещения прокладок. Затем необходимо ослабить круглую гайку, расположенную слева от верхнего ножа, освободив прокладки. Для уменьшения торцевого зазора необходимо… Читать ещё >
Проектирование станка для резки полосовых заготовок (реферат, курсовая, диплом, контрольная)
Реферат СТАНОК, НОЖ РОЛИКОВЫЙ, ПРИВОД, СТОЛ, МОТОР-РЕДУКТОР, ВАЛ, ПОДШИПНИК, ЦЕПНАЯ ПЕРЕДАЧА, УПОР ПЕРЕДВИЖНОЙ.
Объектом разработки является станок для резки полос из углеродистой и коррозионно-стойкой стали толщиной до 3 мм, поставляемой в рулонах.
Цель работы — разработка конструкции несущей системы и привода вращения роликовых ножей, обеспечивающей высокую производительность в сочетании с точными размерами по ширине листа и комфортными условиями эксплуатации.
В процессе работы проводился анализ технологии разделительных операций применительно к листовому материалу на ОАО «РузХиммаш» и потребность в повышении производительности технологических процессов, возможность использования специализированных средств, альтернативных гильотинным ножницам. Производился синтез кинематической схемы, прорабатывалась конструкция приводов и узлов несущей системы станка для резки полос, выполнялись проектировочные и проверочные расчеты его механизмов.
В результате проведенной работы разработаны чертежи конструкции станка для резки полос шириной до 700 мм. Технические характеристики вновь спроектированного станка позволяют применять его как для резки углеродистых и низколегированных, так и для коррозионно-стойких сталей.
Основные конструктивные и технико-экономические характеристики: возможность эффективного использования рулонной стали для изготовления вагонных конструкций за счет уменьшения количества сварных швов.
Степень внедрения — станок может быть использован на заготовительных участках ОАО «РузХиммаш». Станок может также использоваться для резки неметаллических листовых материалов (резины, паронита).
Содержание Введение
1. Конструирование и расчет станка для отрезки полос
1.1 Требования к проектируемому станку
1.2 Разработка компоновочной схемы станка
1.3 Выбор основных характеристик привода
1.4 Расчет привода при обработке углеродистой стали
1.5 Расчет привода при обработке коррозионно-стойкой стали
1.6 Проверка тягового усилия на ножах
2. Определение себестоимости станка
2.1 Определение стоимости основных материалов
2.2 Определение стоимости покупных изделий и полуфабрикатов
2.3 Определение стоимости возвратных отходов
2.4 Расчёт заработной платы производственных рабочих
2.5 Расчёт цеховых и общезаводских расходов
2.6 Определение полной себестоимости
3. Безопасность жизнедеятельности
3.1 Состояние организации службы охраны труда на предприятии
3.2 Рациональная организация рабочего места
3.3 Техника безопасности на участке
3.4 Состояние травматизма на производственном объекте
3.5 Противопожарные мероприятия
3.5 Мероприятия по экологической безопасности Заключение Список использованных источников
Введение
В современном вагоностроительном производстве (особенно при изготовлении кузовов) значительный объем деталей представляют собой пластины и оболочки, выполненные из листового материала толщиной 0,8…3 мм. Металлургические предприятия поставляют стальной прокат по ГОСТ 19 903–74 в виде листов мерной ширины и длины, а также рулонную сталь по ГОСТ 19 904–90 и ГОСТ 19 903–74.
Применение рулонной стали имеет ряд преимуществ, в частности, при изготовлении габаритных элементов обшивки имеется возможность использовать длинномерные детали, выполненные на всю длину без поперечных стыковых сварных швов. Тем самым увеличивается производительность заготовительных операций за счет уменьшения объема сварочных работ.
Другим существенным преимуществом рулонной стали является компактность рулона по сравнению с листом мерных размеров, возможность использования универсальных грузозахватных крановых приспособлений при разгрузке, лучшая сохранность материала при длительном хранении.
Кроме того, иногда имеется возможность совмещения разделительных и формоизменяющих операций, например, резка полосовой заготовки и одновременное продавливание на ней гофр.
К разделительным операциям относятся операции, в результате которых происходит полное или частичное отделение одной части материала от другой по замкнутому или незамкнутому контуру. Примеры разделительных операций: отрезка, вырезка, врубка, пробивка, надрезка, обрезка, зачистка.
Отрезка — отделение одной части материала от другой по незамкнутому контуру производится на ножницах или в штампах. Отрезку в штампах используют, как правило, для малогабаритных деталей высокой точности, а отрезку на ножницах — в качестве начальных разделительных операций, предшествующих гибке, формовке, вытяжке и другим формоизменяющим операциям.
Ножницы для отрезки листового материала бывают параллельные, гильотинные, роликовые и вибрационные. На рисунке 1 приведены схема работы гильотинных и роликовых ножниц.
Рисунок 1 — Схема работы ножниц станок полоса отрезка Гильотинные ножницы получили наибольшее распространение. С помощью гильотинных ножниц можно отрезать заготовки от мерных листов по ширине, длине или под углом, а также производить резку рулонной стали поперек полотна. Это оборудование отличается простотой настройки и высокой надежностью.
К недостаткам гильотинных ножниц относятся значительный шум при их работе, динамические нагрузки от ударов подвижного ножа о разрезаемый лист, а также ограниченность габаритов заготовки длиной ножа.
Этих недостатков лишены роликовые ножницы, отличающиеся непрерывной работой без дополнительных динамических нагрузок и шума. Длина отрезаемой заготовки ограничена только емкостью рулона.
Одним из факторов, сдерживающих широкое применение рулонной стали в вагоностроении, является отсутствие на машиностроительных предприятиях оборудования, подобного роликовым ножницам. Серийно выпускаемые модели таких ножниц отличаются высокой стоимостью, а примитивные образцы изготовленные кустарным способом — низкой надежностью и точностью.
Таким образом, существует потребность во внедрении станка для резки полосовых заготовок большой длины, работающего по принципу роликовых ножниц и предназначенного для работы с рулонной сталью. Вместе с тем, такой станок может использоваться также для отрезки полос из мерных листов, хотя и менее эффективно, чем гильотинные ножницы.
1 Конструирование и расчет станка для отрезки полос
1.1 Требования к проектируемому станку Создание технологического оборудования, отвечающих современным народного, должно предусматривать их наибольший экономический эффект и высокие технико-экономические и эксплуатационные показатели.
Основные требования, предъявляемые к создаваемой машине: высокая производительность, надежность, технологичность, ремонтопригодность, минимальные габариты и масса, удобство эксплуатации, экономичность.
Необходимо разработать конструкцию станка для резки полос, предназначенных для работы с рулонной сталью шириной до 1250 мм, причем ширина отрезаемой полосы в пределах от 70 до 700 мм.
Необходимо предусмотреть возможность работы как с углеродистыми и низколегированными конструкционными сталями (Ст 3, 09Г2С), так и с аустенитными коррозионно-стойкими сталями типа 12Х18Н10Т.
Производительность вновь проектируемого станка должна быть не менее трех погонных метров полосы в минуту.
Номинальная потребляемая мощность станка не должна превышать 2 кВт. Конструкция режущего узла должна обеспечивать возможность регулировки захода и торцевого зазора роликов без разборки всего узла.
Станок предназначен для совместного использования с устройством размотки и подачи рулонного материала.
1.2 Разработка компоновочной схемы станка На рисунке 2 представлена компоновка предлагаемого станка.
Рисунок 1 — Компоновка станка для резки полосовых заготовок Станок состоит из стола, установленного на металлоконструкции и привод. На рабочей поверхности стола установлен режущий узел, передвижные упоры и рольганг. Привод устанавливается на нижней обвязке и включает в себя мотор-редуктор и коробку передач, обеспечивающую две частоты вращения роликовых ножей.
Схема рабочего пространства станка приведена на рисунке 2. Разрезаемый лист разматывается с рулона и подается на поверхность стола. В середине стола расположен режущий узел, состоящий из двух валов с роликовыми ножами. Валы связанны между собой зубчатой передачей с передаточным отношением i = 1, вследствие чего верхний и нижний ролики вращаются с одинаковыми частотами вращения, но в противоположные стороны.
При подаче листа в зону захода роликов происходит надрез кромки, после чего полотно увлекается вращающимися роликами, обеспечивающими непрерывную резку полосы. Чтобы отрезаемая полоса своей кромкой не терлась о стол, его поверхность, расположенная под полосой имеет занижение на 6 мм относительно остальной поверхности стола.
Рисунок 2 — Схема рабочего пространства Настройка станка на требуемую ширину листа осуществляется перестановкой упоров. Упоры имеют возможность перемещаться вдоль пазов, расположенных вдоль коротких сторон стола, при с помощью левого упора устанавливается требуемая ширина полосы, а правый упор выставляется на ширину рулона.
Для исключения трения полосы о поверхность стола также предусмотрен рольганг, ролики которого выдвинуты над поверхностью стола на 3 мм.
При проектировании станка рассчитывались размеры рабочей поверхности стола (рисунок 3).
Ширина стола B = 1555 мм и минимальные расстояния от кромок стола до поверхностей упоров 150 мм обеспечивают возможность разрезания рулонной стали шириной? 1255 мм, которая на 5 мм превышает ширину, указанную в техническом задании. Расстояние от поверхности левого упора до режущей кромки ножей 703 мм соответствует предельной ширине отрезаемой полосы.
Длина стола L = 4000 мм обеспечивают возможность использования станка для резки листов мерной длины, а его высота H = 1550 мм согласована с паспортной высотой устройства для размотки и подачи рулона.
На рисунке 4 показана конструкция режущего узла, позволяющая производить регулировку торцевого зазора ножей без разборки всего узла.
Для обеспечения хорошего качества кромки отрезаемой полосы между рабочими торцами роликовых ножей точного должен быть выдержан зазор 0,05 … 0,008 мм.
Изготовление и сборка режущего узла, обеспечивающие требуемый зазор без подгонки и регулировки невозможно, поэтому в конструкции предусмотрены регулировочные прокладки.
Рисунок 3 — Размеры рабочей поверхности стола Для точного выставления торцевого зазора необходимо ослабить стопорный винт на защитном кольце (рисунок 4 вид А) верхнего ножа, затем переместить кольцо влево открыв доступ к месту размещения прокладок. Затем необходимо ослабить круглую гайку, расположенную слева от верхнего ножа, освободив прокладки. Для уменьшения торцевого зазора необходимо уменьшить толщину комплекта прокладок путем удаления лишних прокладок или их подшлифовкой. Выполнив корректировку толщины прокладок необходимо затянуть круглую гайку и проверить работу режущего узла. Если на кромках отрезаемой полосы отсутствуют дефекты (замятия, заусенцы), значит зазор выставлен правильно. После этого необходимо установить кольцо защитное на прежнее место и застопорить его винтом.
Рисунок 4 — Режущий узел Конструкция прокладок приведена на рисунке 5.
Рисунок 5 — Разрезная регулировочная прокладка Каждая прокладка представляет собой два полукольца, которые устанавливаются по отдельности. Таким образом, имеется возможность быстрой регулировки зазора без разборки режущего узла.
Так как техническим заданием предусмотрено использование станка для резки различных материалов, то для получения оптимальных технологических режимов оборудование целесообразно оснастить коробкой передач, регулирующей частоту вращения роликовых ножей.
Далее приведен расчет привода вращения ножей.
1.3 Выбор основных характеристик привода В качестве источника движения выбираем мотор-редуктор планетарный зубчатый двухступенчатый типа 1МПз2 с радиусом расположения осей сателлитов 80 мм, частотой вращения выходного вала 17,7 об/мин. Конструктивное исполнение по способу монтажа — на лапах, с горизонтальным расположением выходного вала (схема 111 по ГОСТ 30 164). Электродвигатель асинхронный 4AX90LB8 на номинальное напряжение сети переменного тока 380 В, номинальной мощностью NН = 1,5 кВт с частотой вращения ротора n = 700 об/мин. Обозначение выбранного мотор-редуктора: «Мотор-редуктор МПз2−50−18−111−1-380»
КПД мотор-редуктора зР с учетом потерь в опорах зД = 0,96 и в зацеплениях зЗ = 0,7
зР = зД · зЗ = 0,96 · 0,7 = 0,672
Тогда фактическая мощность на выходном вал
N = NН · зР = 1,5 · 0,672 = 1,0 кВт Для получения требуемой частоты вращения ножа частоту вращения выходного вала мотор-редуктора необходимо понизить до n1 = 7 об/мин (для резки аустенитной коррозионно-стойкой стали) и n2 = 10 об/мин (для резки углеродистой и низколегированной стали). Понижение осуществляем при помощи двухступенчатой коробки передач с числом зубьев парных колес 20/40 и 25/35 и цепной передачи с числами зубьев 20/24.
Вычислим ряд частот вращения ножа
n1 = n · 20/40 · 20/24 = 17,7 · 0,5 · 0,83 = 7,4 об/мин
n2 = n · 25/35 · 20/24 = 17,7 · 0,71 · 0,83 = 10,5 об/мин Определяем крутящий момент на выходе редуктора
1.4 Расчет привода при обработке углеродистой стали Выполним расчет привода при включении передачи 25/35 (n2 = 10,5 об/мин).
В соответствии с расчётной цепочкой определяем крутящие моменты на валах привода.
На первичном валу коробки передач MI = M = 539 500 Н· мм;
На выходном валу коробки передач На валу роликового ножа где З = 0,98 [1, с. 24] - коэффициент полезного действия цилиндрической прямозубой передачи;
Р = 0,96 [1, с. 24] - коэффициент полезного действия цепной передачи, П = 0,99 [1, с. 25] - коэффициент полезного действия пары подшипников качения.
Выполним проектировочный расчет зубчатой передачи 25/35.
Выбираем материал колёс — сталь 40Х, термообработка — закалка токами высокой частоты (т.в.ч.) до твёрдости на поверхности не менее HRCЭ60 [1, с. 82].
Определяем допускаемые контактные напряжения где Hlimb — предел контактной выносливости для легированных сталей высокой твёрдости
Hlimb = 17HRC + 70 = 1760 + 70 = 1090 МПа КHL = 1 [2, с. 33] - коэффициент долговечности;
[SH] = 1,1 [2, стр. 33] - коэффициент безопасности.
Определяем предварительное межосевое расстояние исходя из условия обеспечения достаточной контактной выносливости активных поверхностей зубьев где Ка = 49,5 [2, с. 32] - коэффициент, учитывающий угол наклона зуба для прямозубых колёс;
КН = 1,35 [2, с. 32] - коэффициент, учитывающий неравномерность распределения нагрузки по ширине зуба при несимметричном расположении колёс относительно опор валов;
ba = 0,3 [1, с. 103] - коэффициент ширины венца относительно межосевого расстояния.
По предварительному межосевому расстоянию определяем модуль зацепления По ГОСТ 9563–60* принимаем модуль зацепления m = 5 мм [2, с. 36].
Определяем делительные диаметры колёс z1 и z2
d1 = mz1 = 525 = 125 мм
d2 = mz2 = 535 = 175 мм Уточняем межосевое расстояние
Определяем требуемую ширину колес
[b] = aw · шba = 150 · 0,3 = 45 мм Назначаем седьмую степень точности передачи [2, с. 32].
При модуле m = 5 мм и ширине венца b = 45 мм определяем контактные напряжения на активных поверхностях зубьев где КН — уточнённый коэффициент, учитывающий неравномерность распределения нагрузки по ширине зуба КН = КН КН = 1,35 1,05 = 1,42
КН = 1,08 [2, с. 32] - при несимметричном расположении колёс относительно опор валов;
КН = 1,1 [2, с. 40] - при окружной скорости передачи 5 м/с и коэффициенте ширины венца ba = 0,3.
Из расчёта видно, что контактные напряжения на активных поверхностях зубьев не превышает предельно допустимых для выбранного материала и термообработки Н = 834 МПа < [Н] = 991 МПа
Следовательно, колёса удовлетворяют требованиям контактной выносливости.
Определяем окружную силу, действующую в зацеплении Определяем радиальную силу, действующую в зацеплении
Fr = Ft tg = 8632 tg20 = 3142 Н где = 20 — угол зацепления.
Проверяем зубчатые зацепления на изгибную прочность.
Определяем допускаемые напряжения изгиба где — предел усталостной прочности при изгибе для стали 40Х закаленной при отнулевом цикле изменения напряжений изгиба
= 13,5 · HRC = 13,5 · 60 = 810 МПа
[SF]' = 1,8 [2, с. 44] - коэффициент безопасности для легированных сталей;
[SF]" = 1 [2, с. 45] - коэффициент, учитывающий непостоянство механических свойств материала безопасности для легированных сталей и зависящий от метода получения заготовки для штампованных заготовок.
При работе цилиндрической прямозубой передачи при одинаковых материалах и ширинах зубчатых венцов наибольшие изгибные напряжения возникают у зубчатых колёс имеющих меньшее число зубьев, поэтому проверочный расчёт на прочность при изгибе будем проводить для колеса z1.
Определяем действующие изгибные напряжения для колеса z1.
где KF = 1,26 [2, с. 43] - коэффициент, учитывающий неравномерность распределения напряжений по ширине зуба,
YF = 3,9 [2, стр. 42] - коэффициент формы зуба.
Из расчёта видно, что изгибные напряжения не превышает предельно допустимых для выбранного материала и термообработки
F = 189 МПа < [F]= 386 МПа Следовательно, рассчитанная передача удовлетворяет требованиям изгибной прочности.
Выполним проектировочный расчет цепной передачи. Исходные данные для расчёта цепной передачи:
— вращающий момент на ведущей звёздочке Т1 = МII = 732 792 Нмм;
— вращающий момент на ведомой звёздочке Т2 = МIII = 835 735 Нмм;
— число зубьев ведущей звёздочки z1 = 20;
— число зубьев ведомой звёздочки z2 = 24.
— передаточное число цепной передачи
u = z2 / z1 = 24/20 = 1,2;
— частота вращения ведущей звездочки
n = n2 · u = 10,5 · 1,2 = 12,6 об/мин;
Определяем коэффициент условий эксплуатации КЭ = kД · kА · kН · kР · kС · kП = 1 · 1 · 1 · 1,25 · 1,5 · 1 = 1,875
где kД = 1 -коэффициент динамически при спокойной нагрузке;
kА = 1 — коэффициент при межосевом расстоянии в пределах А=(20…50)t;
kН = 1 — коэффициент при наклоне линии центров к горизонту не более 60є;
kР = 1,25 — коэффициент при периодическом регулировании натяжения цепи;
kС = 1,5 — коэффициент при периодической смазке;
kП = 1 — коэффициент при односменной работе.
Определяем предварительное значение допускаемого давления в шарнирах цепи
[p] = [p'] · [1 + 0,01(z1 — 17)] = 42,8 · [1 + 0,01(20 — 17)] = 44 МПа где [p'] = 42,8 МПа — допускаемое давление при числе зубьев меньшей звездочки z1 = 17
Определяем ориентировочное значение шага однорядной цепи Принимаем цепь приводную однорядную роликовую типа ПР по ГОСТ 13 568–97 с параметрами [2, с. 147, таблица 7.16]:
— шаг t = 38,1 мм;
— разрушающая нагрузка Q = 12 700 Н;
— масса одного метра цепи q = 5,5 кг/м;
— проекция опорной поверхности шарнира АОП? 0,28 · t2 = 0,28 · 38,12 = 406,5 мм².
Определяем скорость цепи Определяем диаметр делительной окружности ведущей звёздочки Определяем диаметр наружной окружности ведущей звёздочки где d1 = 22,12 мм [2, таблица 7.15, с. 147].
Определяем окружную силу в передаче
Ftц = 2Т1 / dД1 = 2 · 732 792 / 243,55 = 6018 Н Проверяем давление в шарнире цепи
МПа Из расчёта видно, что расчётное давление в шарнире цепи меньше допускаемого: р < [р] = 44 МПа, следовательно, выбранная цепь может быть использована.
Определяем ориентировочное межосевое расстояние передачи ац? 20 t = 20 38,1? 762 мм = 0, 762 м Определяем силы, действующие на цепь:
— окружная Ftц = 6018 Н;
— от центробежных сил F = q 2 = 5,5 0,162? 0 Н;
— от провисания цепи Ff = 9,81 kf q aЦ = 9,8135,50,762 = 123 Н.
где kf = 3 [2, с. 151] - коэффициент при наклоне линии центров передачи 60є.
Определяем расчётную нагрузку на валы
FB = Ftц + 2Ff = 6018 + 2123 = 6264 Н.
Определяем коэффициент запаса прочности цепи на растяжение
> 1
где Q = 12 700 Н — разрушающая нагрузка [2, с. 147, таблица 7.16];
kД = 1 — коэффициент динамичности нагрузки [2, с. 149].
Расчётный коэффициент запаса прочности цепи на растяжение s = 2 больше единицы, следовательно, условие прочности цепи выполнено.
Далее произведен расчет валов коробки передач.
Исходными данными для расчета являются нагрузки, действующие на валы со стороны механических передач (эти нагрузки были определены при расчете соответствующих передач), а также осевые размеры валов. При расчете валов не учитываем весовые нагрузки в виду их незначительности по сравнению с усилиями в передачах.
Ориентировочные размеры валов получим из предварительной эскизной компоновки редуктора с учетом расположения цилиндрических зубчатых колес. Расчетная схема для силового расчета коробки передач представлена на рисунке 5.
Произведем расчет вала I.
По посадочным диаметрам валов под опоры подбираем стандартные подшипники: подшипник 210 ГОСТ 8338–75 (внутренний диаметр 50 мм).
Расчетная схема вала, эпюры моментов представлены на рисунке 6.
Для определения реакции опоры RY1 составляем уравнение моментов относительно опоры «2»
где FY1 = 8632 Н — вертикальная сила в зацеплении колес 25/35, равная окружной;
?1 = 62,5 мм; ?2 = 229,5 мм — осевые размеры вала (рисунок 6).
Рисунок 5 — Схема нагружения валов Рисунок 6 — К расчету вала I
Для определения реакции опоры RY2 составляем уравнение моментов относительно опоры «1»
Проверяем правильность определения опорных реакций, составив уравнение проекций сил на вертикальную ось Для определения реакции опоры RX1 составляем уравнение моментов относительно опоры «2»
Для определения реакции опоры RX2 составляем уравнение моментов относительно опоры «1»
Проверяем правильность определения опорных реакций, составив уравнение проекций сил на горизонтальную ось Определяем суммарные радиальные реакции опор Рассмотрим наиболее нагруженный подшипник.
Эквивалентная нагрузка РЭ2 = R2 · V · Кб · КТ = 7219 · 1 · 1,2 · 1 = 8662,8 Н где V = 1 [3, с. 212] - коэффициент от вращения внутреннего кольца;
Кб = 1,2 [3, с. 214, таблица 9.19] - коэффициент от условий работы;
КТ = 1 [3, с. 214, таблица 9.19] - коэффициент от температуры.
Для более нагруженного подшипника вычисляем расчетный ресурс где а1 = 1 [3, 132] - коэффициент, учитывающий вероятность отказов подшипника;
а2 = 0,7 [3, 132] - коэффициент, учитывающий условия работы;
C = 35 100 [3, с. 233, таблица 136] - динамическая грузоподъемность.
Рекомендуемое значение расчетного ресурса для заданных условий работы 10 000 ч [4, с. 129, таблица 71]. Так как расчетный ресурс подшипников больше требуемого, то делаем вывод о достаточной надежности подшипников вала I.
Уточненный расчет вала состоит в определении коэффициентов запаса прочности для опасных сечений и сравнения их с допускаемыми значениями [S] = 2,5 [3, с. 162].
Определим коэффициенты запаса прочности для опасного сечения ведущего вала, принимая, что нормальные напряжения изменяются по симметричному циклу, а касательные — по отнулевому (пульсирующему).
Назначаем материал вала — сталь 45, имеющую механические свойства:
— временное сопротивление на разрыв в =598 МПа;
— предел выносливости по нормальным напряжениям -1 =309 МПа;
— предел выносливости по касательным напряжениям -1 =179 МПа.
Определяем результирующие изгибающие моменты в середине посадочного места колеса где MY — изгибающий момент в опасном сечении в плоскости y0z
MY = RY1 · ?2 = 1848 · 229,5 = 424 116 Н· мм
MX — изгибающий момент в опасном сечении в плоскости y0z
MX = RX1 · ?2 = 673 · 229,5 = 154 453,3 Н· мм В качестве концентратора напряжений в середине колеса выступают шлицы. Предварительно намечаем шлицы легкой серии (наружный диаметр 58 мм, внутренний диаметр 52 мм, ширина шлица 10 мм, число шлицев 8).
Проверяем вал на усталостную прочность в опасном сечении при одновременном действии изгибающего и крутящего моментов. Для этого определяем коэффициент запаса усталостной прочности где S — коэффициент запаса усталостной прочности при изгибе
— 1 = 309 МПа [3, с. 200] - предел выносливости стали 45 при изгибе;
kу / (еу?в) = 2,17 [5, с. 554] - эффективный коэффициент концентрации напряжений изгиба;
— поправочный коэффициент, учитывающий качество обработки и состояние поверхности вала (для термообработанных валов с последующим шлифованием);
— масштабный фактор, учитывающий влияние размеров сечения вала на усталостную прочность;
V — амплитуда цикла изгибных напряжений при симметричном цикле
W — момент сопротивления изгибу шлицевого сечения вала
d = 52 мм — диаметр впадин шлицев;
о = 1,13 — коэффициент, учитывающий усиление вала выступами шлицев
S — коэффициент запаса усталостной прочности при кручении
— 1 = 179 МПа [3, с. 200] - предел выносливости при кручении;
kф / (еф?в) = 3,84 [5, с. 554] - эффективный коэффициент концентрации напряжений кручения;
— поправочный коэффициент, учитывающий качество обработки и состояние поверхности вала (для термообработанных валов с последующим шлифованием);
— масштабный фактор, учитывающий влияние размеров сечения вала на усталостную прочность;
V — амплитуда цикла напряжений при кручения
WКР — момент сопротивления кручению сечения вала шф = 0,1 — коэффициент чувствительности материала вала к постоянной составляющей отнулевого цикла касательных напряжений;
М = V = 8,6 МПа — постоянная составляющая отнулевого цикла касательных напряжений Из расчета видно, что фактический коэффициент запаса усталостной прочности для опасного сечения вала S = 3,5 больше предельно допустимого коэффициент запаса [S] = 2,5, следовательно, рассчитанный вал обладает достаточной усталостной прочностью.
Проверяем на прочность шпоночное соединение выходного конца быстроходного вала с полумуфтой по допускаемым напряжениям смятия [СМ]=100 МПа [3, с. 170]
где d = 58 мм — диаметр вала,
lP — длина рабочей грани шпонки
lP = l — b = 100 — 16 = 84 мм
l = 40 мм — общая длина шпонки,
h = 5 мм — высота шпонки,
t1 = 3 мм — глубина шпоночного паза на валу;
b = 5 мм — ширина шпонки.
Проверяем на прочность шлицевое соединение блока шестерен с валом по допускаемым напряжениям смятия [СМ] = 100 МПа [3, с. 175]
где z = 8 — число шлицев, АСМ — расчетная площадь смятия,
RCP — средний радиус соединения
RCP = 0,25(D+d) = 0,25(58+52) = 27,5 мм
D = 58 мм — диаметр вершин шлицев,
d = 52 мм — диаметр впадин шлицев,
f = 0,5 мм — фаска при вершине шлица.
Из расчета видно, что напряжение смятия в шлицевом соединении не превышает предельно допустимого, т. е. СМ = 14 МПа < [СМ] = 100 МПа.
Произведем расчет вала II.
Расчетная схема вала, эпюры моментов представлены на рисунке 7.
Рисунок 7 — К расчету вала II
Определяем предварительные значения диаметра вала из расчета на чистое кручение по пониженным касательным напряжениям где [ф] = 16 МПа [3, с. 161] - допускаемое напряжение при кручении.
По посадочным диаметрам валов под опоры подбираем стандартные подшипники: подшипник 113 ГОСТ 8338–75 (внутренний диаметр 65 мм).
Для определения реакции опоры RY1 составляем уравнение моментов относительно опоры «2»
где FY1 = 8632 Н — вертикальная сила в зацеплении колес 25/35, равная окружной;
FY2 — вертикальная составляющая силы в цепной передаче
FY2 = FB · cos 60є = 6264 · cos 60є = 5423 Н
?1 = 62,5 мм; ?2 = 229,5 мм; ?3 = 107,5 мм — расстояние от места приложения нагрузки до середин опор вала.
Для определения реакции опоры RY2 составляем уравнение моментов относительно опоры «1»
Проверяем правильность определения опорных реакций, составив уравнение проекций сил на вертикальную ось
Для определения реакции опоры RX1 составляем уравнение моментов относительно опоры «2»
где FX1 = 3124 Н — горизонтальная сила в зацеплении колес 25/35, равная радиальной;
FX2 — горизонтальная составляющая силы в цепной передаче
FX2 = FB · sin 60є = 6264 · sin 60є = 3132 Н Для определения реакции опоры RX2 составляем уравнение моментов относительно опоры «1»
Проверяем правильность определения опорных реакций, составив уравнение проекций сил на горизонтальную ось Определяем суммарные радиальные реакции опор
Рассмотрим наиболее нагруженный подшипник.
Эквивалентная нагрузка РЭ2 = R2 · V · Кб · КТ = 8877 · 1 · 1,2 · 1 = 10 652,4 Н где V = 1 [3, с. 212] - коэффициент от вращения внутреннего кольца;
Кб = 1,2 [3, с. 214, таблица 9.19] - коэффициент от условий работы;
КТ = 1 [3, с. 214, таблица 9.19] - коэффициент от температуры.
Для более нагруженного подшипника вычисляем расчетный ресурс где а1 = 1 [3, 132] - коэффициент, учитывающий вероятность отказов подшипника;
а2 = 0,7 [3, 132] - коэффициент, учитывающий условия работы;
C = 30 700 [3, с. 233, таблица 136] - динамическая грузоподъемность.
Рекомендуемое значение расчетного ресурса для заданных условий работы 10 000 ч [4, с. 129, таблица 71]. Так как расчетный ресурс подшипников больше требуемого, то делаем вывод о достаточной надежности подшипников вала II.
Определим коэффициенты запаса прочности для предположительно опасных сечений ведомого вала.
Определяем результирующие изгибающие моменты в середине посадочного места подшипника «1»
где MY1 — изгибающий момент в опасном сечении в плоскости y0z
MY1 = FY2 · ?3 = 5423 · 107,5 = 582 972,5 Н· мм
MX1 — изгибающий момент в опасном сечении в плоскости y0z
MX1 = FX · ?1 = 3132 · 107,5 = 336 690 Н· мм Определяем результирующие изгибающие моменты в середине посадочного места зубчатого колеса где MY2 — изгибающий момент в опасном сечении в плоскости y0z
MY2 = RY2 · ?1 = 8781 · 62,5 = 548 812,5 Н· мм
MX2 — изгибающий момент в опасном сечении в плоскости y0z
MX2 = RX2 · ?1 = 1302 · 62,5 = 81 375 Н· мм Из эпюр изгибающих моментов положение опасного сечения очевидно — это сечение в середине посадочного места подшипника «1». В качестве концентратора напряжений выступает переходная посадка с возможным натягом.
Проверяем вал на усталостную прочность в опасном сечении при одновременном действии изгибающего и крутящего моментов. Для этого определяем коэффициент запаса усталостной прочности
где S — коэффициент запаса усталостной прочности при изгибе
— 1 = 309 МПа [3, с. 200] - предел выносливости стали 45 при изгибе;
kу / (еу?в) = 3,52 [5, с. 554] - эффективный коэффициент концентрации напряжений изгиба;
— поправочный коэффициент, учитывающий качество обработки и состояние поверхности вала (для термообработанных валов с последующим шлифованием);
— масштабный фактор, учитывающий влияние размеров сечения вала на усталостную прочность;
V — амплитуда цикла изгибных напряжений при симметричном цикле
W — момент сопротивления изгибу круглого сечения вала
d = 65 мм — диаметр вала в опасном сечении;
S — коэффициент запаса усталостной прочности при кручении
— 1 = 179 МПа [3, с. 200] - предел выносливости при кручении;
kф / (еф?в) = 3,79 [5, с. 554] - эффективный коэффициент концентрации напряжений кручения;
— масштабный фактор, учитывающий влияние размеров сечения вала на усталостную прочность;
V — амплитуда цикла напряжений при кручения
WКР — момент сопротивления кручению сечения вала шф = 0,1 — коэффициент чувствительности материала вала к постоянной составляющей отнулевого цикла касательных напряжений;
М = V = 6,7 МПа — постоянная составляющая отнулевого цикла касательных напряжений Из расчета видно, что фактический коэффициент запаса усталостной прочности для опасного сечения вала S = 3,1 больше предельно допустимого коэффициент запаса [S] = 2,5, следовательно, рассчитанный вал обладает достаточной усталостной прочностью.
Проверяем на прочность шпоночное соединение вала с зубчатым колесом z = 35 по допускаемым напряжениям смятия [СМ] = 100 МПа [3, с. 170]
где d = 75 мм — диаметр вала в шпоночном соединении,
lP — длина рабочей грани шпонки
lP = l — b = 100 — 20 = 80 мм
l = 100 мм — общая длина шпонки,
h = 12 мм — высота шпонки,
t1 = 7,5 мм — глубина шпоночного паза на валу;
b = 20 мм — ширина шпонки.
1.5 Расчет привода при обработке коррозионно-стойкой стали Выполним расчет привода при включении передачи 20/40 (n2 = 7,4 об/мин).
В соответствии с расчётной цепочкой определяем крутящие моменты на валах привода.
На первичном валу коробки передач
MI = M = 539 500 Н· мм;
На выходном валу коробки передач На валу роликового ножа где З = 0,98 [1, с. 24] - коэффициент полезного действия цилиндрической прямозубой передачи;
Р = 0,96 [1, с. 24] - коэффициент полезного действия цепной передачи, П = 0,99 [1, с. 25] - коэффициент полезного действия пары подшипников качения.
Выполним проектировочный расчет зубчатой передачи 20/40.
Материалы передачи и требования к термообработке для передачи 20/40 аналогичны передаче 25/35. Основные расчетные характеристики (согласно 1.4):
— модуль зацепления m = 5 мм;
— ширина венца b = 45 мм;
— межосевое расстояние aW = 150 мм;
— передаточное число u = 2;
— допускаемые контактные напряжения [уH] = 991 МПа;
— уточнённый коэффициент контактных напряжений КН = 1,42;
— допускаемые изгибные напряжения [уF] = 463 МПа;
Определяем контактные напряжения на активных поверхностях зубьев Из расчёта видно, что контактные напряжения на активных поверхностях зубьев не превышает предельно допустимых для выбранного материала и термообработки Н = 976 МПа < [Н] = 991 МПа Следовательно, колёса удовлетворяют требованиям контактной выносливости.
Определяем окружную силу, действующую в зацеплении Определяем радиальную силу, действующую в зацеплении
Fr = Ft tg = 107 902 tg20 = 3927 Н где = 20 — угол зацепления.
Определяем действующие изгибные напряжения для колеса z1.
где KF = 1,204 [2, с. 43] - коэффициент, учитывающий неравномерность распределения напряжений по ширине зуба,
YF = 4,09 [2, стр. 42] - коэффициент формы зуба.
Из расчёта видно, что изгибные напряжения не превышает предельно допустимых для выбранного материала и термообработки
F = 254 МПа < [F]= 386 МПа Следовательно, рассчитанная передача удовлетворяет требованиям изгибной прочности.
Выполним проектировочный расчет цепной передачи 20/24. Исходные данные для расчёта цепной передачи:
— вращающий момент на ведущей звёздочке Т1=МII=1 046 846 Нмм;
— вращающий момент на ведомой звёздочке Т2=МIII=1 193 907 Нмм;
— передаточное число цепной передачи u = 1,2;
— частота вращения ведущей звездочки
n = n1 · u = 7,4 · 1,2 = 8,9 об/мин;
— коэффициент условий эксплуатации КЭ = 1,875
— допускаемое давление в шарнирах цепи [p] = 44 МПа
— шаг цепи t = 38,1 мм;
— разрушающая нагрузка Q = 12 700 Н;
— масса одного метра цепи q = 5,5 кг/м;
— проекция опорной поверхности шарнира АОП = 406,5 мм².
— диаметр делительной окружности ведущей звездочки dД1 = 243,55 мм;
— диаметр наружной окружности ведущей звёздочки DД1 = 260,59 мм;
— межосевое расстояние передачи ац = 762 мм = 0, 762 м Определяем скорость цепи Определяем окружную силу в передаче
Ftц = 2Т1 / dД1 = 2 · 1 046 846 / 243,55 = 8597 Н Проверяем давление в шарнире цепи
МПа Из расчёта видно, что расчётное давление в шарнире цепи меньше допускаемого: р < [р] = 44 МПа, следовательно, выбранная цепь может быть использована.
Определяем силы, действующие на цепь:
— окружная Ftц = 8597 Н;
— от центробежных сил F = 0 Н (см. 1.4);
— от провисания цепи Ff = 123 Н (см. 1.4).
Определяем расчётную нагрузку на валы
FB = Ftц + 2Ff = 8597 + 2123 = 8843 Н.
Определяем коэффициент запаса прочности цепи на растяжение
> 1
Расчётный коэффициент запаса прочности цепи на растяжение s=1,5 больше единицы, следовательно, условие прочности цепи выполнено.
Далее произведен расчет валов коробки передач.
Расчетная схема для силового расчета коробки передач в режиме резки коррозионно-стойкой стали представлена на рисунке 8.
Произведем расчет вала I.
Расчетная схема вала, эпюры моментов представлены на рисунке 9.
Для определения реакции опоры RY1 составляем уравнение моментов относительно опоры «2»
где FY1 = 10 790 Н — вертикальная сила в зацеплении колес 20/40, равная окружной;
?1 = 229,5 мм; ?2 = 62,5 мм — расстояние от места приложения нагрузки до середин опор вала (рисунок 9).
Рисунок 8 — Схема нагружения валов Для определения реакции опоры RY2 составляем уравнение моментов относительно опоры «1»
тогда Проверяем правильность определения опорных реакций, составив уравнение проекций сил на вертикальную ось Рисунок 9 — К расчету вала I
Для определения реакции опоры RX1 составляем уравнение моментов относительно опоры «2»
Для определения реакции опоры RX2 составляем уравнение моментов относительно опоры «1»
Проверяем правильность определения опорных реакций, составив уравнение проекций сил на горизонтальную ось Определяем суммарные радиальные реакции опор Рассмотрим наиболее нагруженный подшипник.
Эквивалентная нагрузка РЭ1 = R1 · V · Кб · КТ = 9024 · 1 · 1,2 · 1 = 10 828,8 Н где V = 1 [3, с. 212] - коэффициент от вращения внутреннего кольца;
Кб = 1,2 [3, с. 214, таблица 9.19] - коэффициент от условий работы;
КТ = 1 [3, с. 214, таблица 9.19] - коэффициент от температуры.
Для более нагруженного подшипника вычисляем расчетный ресурс где а1 = 1 [3, 132] - коэффициент, учитывающий вероятность отказов подшипника;
а2 = 0,7 [3, 132] - коэффициент, учитывающий условия работы;
C = 35 100 [3, с. 233, таблица 136] - динамическая грузоподъемность.
Рекомендуемое значение расчетного ресурса для заданных условий работы 10 000 ч [4, с. 129, таблица 71]. Так как расчетный ресурс подшипников больше требуемого, то делаем вывод о достаточной надежности подшипников вала I.
Определим коэффициенты запаса прочности для опасного сечения ведущего вала.
Определяем результирующие изгибающие моменты в середине посадочного места колеса где MY — изгибающий момент в опасном сечении в плоскости y0z
MY = RY1 · ?2 = 8480 · 62,5 = 530 000 Н· мм
MX — изгибающий момент в опасном сечении в плоскости y0z
MX = RX1 · ?2 = 3086 · 62,5 = 192 875 Н· мм Проверяем вал на усталостную прочность в опасном сечении (в середине колеса z = 25), ослабленного шлицами. Для этого определяем коэффициент запаса усталостной прочности где S — коэффициент запаса усталостной прочности при изгибе
— 1 = 309 МПа [3, с. 200] - предел выносливости стали 45 при изгибе;
kу / (еу?в) = 2,17 [5, с. 554] - эффективный коэффициент концентрации напряжений изгиба;
— поправочный коэффициент, учитывающий качество обработки и состояние поверхности вала;
— масштабный фактор, учитывающий влияние размеров сечения вала на усталостную прочность;
V — амплитуда цикла изгибных напряжений при симметричном цикле
W = 15 598 мм3 — момент сопротивления изгибу шлицевого сечения вала (см. 1.4);
S = 5,3 — коэффициент запаса усталостной прочности при кручении (см. 1.4).
Из расчета видно, что фактический коэффициент запаса усталостной прочности для опасного сечения вала S = 3,1 больше предельно допустимого коэффициент запаса [S] = 2,5, следовательно, рассчитанный вал обладает достаточной усталостной прочностью.
Проверяем на смятие соединения быстроходного вала: шпоночное соединение с полумуфтой и шлицевое соединение с блоком шестерен по допускаемым напряжениям [уСМ] = 100 МПа.
Так как крутящий момент на входе коробки передач для обоих режимов одинаков, то напряжения смятия на рабочих гранях шпонки и шлицев равны 55 и 14 МПа соответственно (см. 1.4). Следовательно, шлицевое и шпоночное соединения удовлетворяют требованиям прочности при смятии.
Произведем расчет вала II.
Расчетная схема вала, эпюры моментов представлены на рисунке 10.
Для определения реакции опоры RY1 составляем уравнение моментов относительно опоры «2»
где FY1 = 10 790 Н — вертикальная сила в зацеплении колес 20/40, равная окружной;
?1 = 229,5 мм; ?2 = 62,5 мм; ?3 = 107,5 мм — расстояние от места приложения нагрузки до середин опор вала.
Для определения реакции опоры RY2 составляем уравнение моментов относительно опоры «1»
Рисунок 10 — К расчету вала II
Проверяем правильность определения опорных реакций, составив уравнение проекций сил на вертикальную ось
Для определения реакции опоры RX1 составляем уравнение моментов относительно опоры «2»
где FX1 = 3927 Н — горизонтальная сила в зацеплении колес 20/405, равная радиальной;
FX2 — горизонтальная составляющая силы в цепной передаче
FX2 = FB · sin 60є = 8843 · sin 60є = 3829 Н Для определения реакции опоры RX2 составляем уравнение моментов относительно опоры «1»
Проверяем правильность определения опорных реакций, составив уравнение проекций сил на горизонтальную ось Определяем суммарные радиальные реакции опор
Рассмотрим наиболее нагруженный подшипник.
Эквивалентная нагрузка РЭ1 = R1 · V · Кб · КТ = 8561 · 1 · 1,2 · 1 = 10 273,2 Н где V = 1 [3, с. 212] - коэффициент от вращения внутреннего кольца;
Кб = 1,2 [3, с. 214, таблица 9.19] - коэффициент от условий работы;
КТ = 1 [3, с. 214, таблица 9.19] - коэффициент от температуры.
Для более нагруженного подшипника вычисляем расчетный ресурс где а1 = 1 [3, 132] - коэффициент, учитывающий вероятность отказов подшипника;
а2 = 0,7 [3, 132] - коэффициент, учитывающий условия работы;
C = 30 700 [3, с. 233, таблица 136] - динамическая грузоподъемность.
Рекомендуемое значение расчетного ресурса для заданных условий работы 10 000 ч [4, с. 129, таблица 71]. Так как расчетный ресурс подшипников больше требуемого, то делаем вывод о достаточной надежности подшипников вала II.
Определим коэффициенты запаса прочности для предположительно опасных сечений ведомого вала.
Определяем результирующие изгибающие моменты в середине посадочного места подшипника «1»
где MY1 — изгибающий момент в опасном сечении в плоскости y0z
MY1 = FY2 · ?3 = 7658 · 107,5 = 823 235 Н· мм
MX1 — изгибающий момент в опасном сечении в плоскости y0z
MX1 = FX · ?1 = 3132 · 107,5 = 336 690 Н· мм Определяем результирующие изгибающие моменты в середине посадочного места зубчатого колеса где MY2 — изгибающий момент в опасном сечении в плоскости y0z
MY2 = RY2 · ?1 = 5129 · 229,5 = 1 177 105,5 Н· мм
MX2 — изгибающий момент в опасном сечении в плоскости y0z
MX2 = RX2 · ?1 = 569 · 229,5 = 130 585,5 Н· мм Из эпюр изгибающих моментов положение опасного сечения очевидно — это сечение в середине посадочного места колеса z = 40. В качестве концентратора напряжений выступает шпоночный паз глубиной 7,5 мм и шириной 20 мм.
Проверяем вал на усталостную прочность в опасном сечении при одновременном действии изгибающего и крутящего моментов. Для этого определяем коэффициент запаса усталостной прочности
где S — коэффициент запаса усталостной прочности при изгибе
— 1 = 309 МПа [3, с. 200] - предел выносливости стали 45 при изгибе;
kу / (еу?в) = 2,37 [5, с. 554] - эффективный коэффициент концентрации напряжений изгиба;
— поправочный коэффициент, учитывающий качество обработки и состояние поверхности вала;
— масштабный фактор, учитывающий влияние размеров сечения вала на усталостную прочность;
V — амплитуда цикла изгибных напряжений при симметричном цикле
W — момент сопротивления изгибу круглого сечения вала
d = 75 мм — диаметр вала в месте посадки колеса z = 40;
t1 = 7,5 мм — глубина шпоночного паза на валу;
b = 20 мм — ширина шпоночного паза;
S — коэффициент запаса усталостной прочности при кручении
— 1 = 179 МПа [3, с. 200] - предел выносливости при кручении;
kф / (еф?в) = 2,61 [5, с. 554] - эффективный коэффициент концентрации напряжений кручения;
— масштабный фактор, учитывающий влияние размеров сечения вала на усталостную прочность;
V — амплитуда цикла напряжений при кручения
WКР — момент сопротивления кручению сечения вала шф = 0,1 — коэффициент чувствительности материала вала к постоянной составляющей отнулевого цикла касательных напряжений;
М = V = 6,6 МПа — постоянная составляющая отнулевого цикла касательных напряжений Из расчета видно, что фактический коэффициент запаса усталостной прочности для опасного сечения вала S = 3,7 больше предельно допустимого коэффициент запаса [S] = 2,5, следовательно, рассчитанный вал обладает достаточной усталостной прочностью.
Проверяем на прочность шпоночное соединение вала с зубчатым колесом z = 40 по допускаемым напряжениям смятия [СМ] = 100 МПа [3, с. 170]
где d = 75 мм — диаметр вала в шпоночном соединении,
lP =80 мм — длина рабочей грани шпонки (см. 1.4);
h = 12 мм — высота шпонки,
t1 = 7,5 мм — глубина шпоночного паза на валу;
b = 20 мм — ширина шпонки.
1.6 Проверка тягового усилия на ножах Построим схему относительного расположения ножей и листовой заготовки на момент начала резания (рисунок 11).
Определяем радиальную силу на ноже [1, с. 65]
где S = 3 мм — расчетная толщина листа;
уВ = 445 МПа — временное сопротивление на разрыв материала листа;
б = 25,78є - угол захвата ножей при расчетной толщине листа;
Определяем суммарную силу на ноже [1, с. 65]
P = 1,3 · PR = 1,3 · 1106 = 1438 Н Окружную силу на ноже определим решив векторное уравнение Для решения этого уравнения построим план сил на момент начала резания (рисунок 1). Проводим вектор длиной? R = 60 мм (длина вектора принимается произвольно). Далее из начала вектора проводим дугу окружности радиусом r
Рисунок 11 — Схема сил на роликах
r =? 1,3 = 60 · 1,3 = 78 мм Опустив перпендикуляр из конца вектора на дугу r = 78 мм, найдем конечную точку векторов и .
Фактическое значение окружной силы найдем из соотношения где? Т? 50 мм — длина вектора на плане сил.
Тогда Определяем крутящий момент на ролике М = R · PT = 75 · 922 = 69 150 Н· мм где R = 75 мм — радиус режущей кромки ролика.
Проектировочные расчеты привода производились исходя из заданной в техническом задании потребляемой мощности 1,5 кВт. При этом крутящий момент на роликовых ножах M = 83 574 Н· мм — для углеродистой и низколегированной стали и M = 1 193 991 Н· мм — для коррозионно-стойкой стали. Очевидно, что спроектированный станок обладает достаточной прочностью и пригоден для обработки широкой номенклатуры рулонных материалов.
2. Определение себестоимости станка Определение себестоимости будем проводить по следующим статьям:
Сырьё и основные материалы;
Покупные изделия и полуфабрикаты;
Транспортно-заготовительные расходы;
Возвратные отходы;
Основная заработная плата производственных рабочих;
Дополнительная заработная плата производственных рабочих;
Начисления на заработную плату;
Цеховые расходы;
Общезаводские расходы;
Внепроизводственные расходы.
2.1 Определение стоимости основных материалов Стоимость основных материалов определяем по общей формуле СОМ = ЦОМ КОМ;
где ЦОМ — цена одного килограмма материала, р.;
КОМ — норма расхода материала, кг.
Определяем стоимость проката круглого сечения диаметром 105 мм из стали 20
СОМ = ЦОМ КОМ = 28,2 86,94 = 2451,71 р.
где ЦОМ = 28,2 р. — цена одного килограмма выбранного сортамента;
КОМ = 86,94 кг. — норма расхода выбранного сортамента.
Определяем стоимость проката круглого сечения диаметром 95 мм из стали 20
СОМ = ЦОМ КОМ = 28,2 13,23 = 373,09 р.
где ЦОМ = 28,2 р. — цена одного килограмма выбранного сортамента;
КОМ = 13,23 кг. — норма расхода выбранного сортамента.
Определяем стоимость проката круглого сечения диаметром 70 мм из стали 20
СОМ = ЦОМ КОМ = 28,2 33,08 = 932,86 р.
где ЦОМ = 28,2 р. — цена одного килограмма выбранного сортамента;
КОМ = 33,08 кг. — норма расхода выбранного сортамента.
Определяем стоимость проката круглого сечения диаметром 50 мм из стали 20
СОМ = ЦОМ КОМ = 28,2 13,23 = 373,09 р.
где ЦОМ = 28,2 р. — цена одного килограмма выбранного сортамента;
КОМ = 13,23 кг. — норма расхода выбранного сортамента.
Определяем стоимость листа горячекатаного толщиной 16 мм из стали 10ХСНД СОМ = ЦОМ КОМ = 30,3 97,02 = 2939,71 р.
где ЦОМ = 30,3 р. — цена одного килограмма выбранного сортамента;
КОМ = 97,02 кг. — норма расхода выбранного сортамента.
Определяем стоимость листа горячекатаного толщиной 12 мм из стали 10ХСНДСОМ = ЦОМ КОМ = 30,3 1079,27 = 32 701,88 р.
где ЦОМ = 30,3 р. — цена одного килограмма выбранного сортамента;
КОМ = 1079,27 кг. — норма расхода выбранного сортамента.
Определяем стоимость листа горячекатаного толщиной 10 мм из стали 10ХСНД СОМ = ЦОМ КОМ = 30,3 779,98 = 23 633,39 р.
где ЦОМ = 30,3 р. — цена одного килограмма выбранного сортамента;
КОМ = 779,98 кг. — норма расхода выбранного сортамента.
Определяем стоимость листа горячекатаного толщиной 8 мм из стали 10ХСНД СОМ = ЦОМ КОМ = 30,3 122,47 = 3710,84 р.
где ЦОМ = 30,3 р. — цена одного килограмма выбранного сортамента;
КОМ = 122,47 кг. — норма расхода выбранного сортамента.
Определяем стоимость листа горячекатаного толщиной 6 мм из стали 10ХСНД СОМ = ЦОМ КОМ = 30,3 15,44 = 467,83 р.
где ЦОМ = 30,3 р. — цена одного килограмма выбранного сортамента;
КОМ = 15,44 кг. — норма расхода выбранного сортамента.
Определяем стоимость крепёжных изделий СОМ = ЦОМ КОМ = 35 19,7 = 689,5 р.
где ЦОМ = 35 р. — цена одного килограмма крепежа;
КОМ = 19,7 кг. — чистый вес крепежа.
Определяем стоимость прочих материалов СОМ = 835,14 р.
Определяем стоимость сварочных материалов СОМ = 2053,62 р.
Определяем стоимость лакокрасочных материалов СОМ = 1026,81 р.
Определяем стоимость консервации СОМ = 479,18 р.
Определяем общую стоимость основных материалов СОМ = 2451,71 + 373,09 + 932,86 + 373,09 + 2939,71 + 32 881,86 +
+ 23 633,39 + 3710,84 + 467,83 + 689,5 + 835,14 + 2053,62 +
+ 1026,81 + 479,18 = 72 848,63 р.
2.2 Определение стоимости покупных изделий и полуфабрикатов Стоимость покупных изделий полуфабрикатов определяем по общей формуле СПИ = ЦПИ КПИ;
где ЦПИ — цена одной покупной единицы, р.;
КПИ — необходимое количество покупных единиц, шт.
Результаты расчётов стоимости покупных изделий и полуфабрикатов представлены в таблице 1.
Таблица 1 — Стоимость покупных изделий и полуфабрикатов
Наименование | Количество | Цена за штуку, р. | Стоимость, р. | |
Гидроцилиндр HCJ.140.25.830 — 01 | ||||
Гидроцилиндр HCС.60.25.860 — 01 | ||||
Гидроцилиндр HCJ.30.25.360 — 01 | ||||
Редуктор планетарный | ||||
Электродвигатель асинхронный | ||||
Определяем транспортно-заготовительные расходы. Принимаем транспортно-заготовительные расходы равными 7% от стоимости сырья, основных материалов, покупных и комплектующих изделий. Тогда СОМ = (СОМ + СПИ) 0,07 = (72 848,63 + 49 000) 0,07 = 8529,4 р.
2.3 Определение стоимости возвратных отходов Стоимость возвратных отходов определим по общей формуле СВО = ЦВО (КОМ — МИ);
где ЦВО — цена одного килограмма отходов, р.;
КОМ — норма расхода материала, кг.;
МИ — чистый вес изделия, кг.
Определяем стоимость возвратных отходов проката круглого сечения диаметром 105 мм из стали 20
СВО = ЦВО (КОМ — МИ) = 2,65 (86,94 — 48,3) = 102,4 р.
где ЦВО = 2,65 р. — цена килограмма отходов выбранного сортамента;
КОМ = 86,94 кг. — норма расхода выбранного сортамента;
МИ = 48,3 кг. — чистый вес изделия.
Определяем стоимость возвратных отходов проката круглого сечения диаметром 95 мм из стали 20
СВО = ЦВО (КОМ — МИ) = 2,65 (13,23 — 12,6) = 1,67 р.
где ЦВО = 2,65 р. — цена килограмма отходов выбранного сортамента;
КОМ = 13,23 кг. — норма расхода выбранного сортамента;
МИ = 12,6 кг. — чистый вес изделия.
Определяем стоимость возвратных отходов проката круглого сечения диаметром 70 мм из стали 20
СВО = ЦВО (КОМ — МИ) = 2,65 (33,08 — 31,5) = 4,19 р.
где ЦВО = 2,65 р. — цена килограмма отходов выбранного сортамента;
КОМ = 33,08 кг. — норма расхода выбранного сортамента;
МИ = 31,5 кг. — чистый вес изделия.
Определяем стоимость возвратных отходов проката круглого сечения диаметром 50 мм из стали 20
СВО = ЦВО (КОМ — МИ) = 2,65 (13,23 — 12,6) = 1,67 р.
где ЦВО = 2,65 р. — цена килограмма отходов выбранного сортамента;
КОМ = 13,23 кг. — норма расхода выбранного сортамента;
МИ = 12,6 кг. — чистый вес изделия.
Определяем стоимость возвратных отходов листа горячекатаного толщиной 16 мм из стали 10ХСНД СВО = ЦВО (КОМ — МИ) = 2,65 (97,02 — 92,4) = 12,24 р.
где ЦВО = 2,65 р. — цена килограмма отходов выбранного сортамента;