Проектирование автоматизированной системы центрального пункта сбора нефти
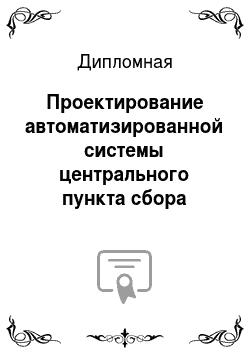
Система не позволяет производить дистанционный запуск оборудования и аварийное опорожнение аппаратов ввиду отсутствия электрифицированной запорно-регулирующей арматуры на линиях аварийного опорожнения аппаратов. Существующее оборудование КИПиА печей ПТБ-10 не удовлетворяет современным требованиям по автоматизации производственных процессов (оборудование морально и технически устарело… Читать ещё >
Проектирование автоматизированной системы центрального пункта сбора нефти (реферат, курсовая, диплом, контрольная)
Нефтедобывающие предприятия представляют собой сложные комплексы технологических объектов, рассредоточенных на больших площадях, размеры которых достигают десятков и сотен квадратных километров. Технологические объекты (скважины, центральные пункты сбора нефти, нефтеперекачивающие станции, установки комплексной подготовки нефти и газа, резервуарные парки) представляют собой в целом единую систему, у которой успешное функционирование во многом зависит от каждого его звена. В связи с чем, современные методы управления производственным процессом на основе компьютерных технологий получают в настоящее время всё более широкое распространение на большинстве промышленных предприятий нефтегазодобывающей отрасли.
Современный уровень технического развития позволяет решать задачи информационной обеспеченности предприятия, непосредственного автоматизированного управления процессом на рассредоточенных технологических объектах. Тщательно спроектированные системы способствуют улучшению эффективности работы предприятия, а также способствует увеличению прибыли.
Одним из основных показателей эффективности работы предприятия является его продуктивность и низкая (минимальная) себестоимость выпускаемой продукции, которая обеспечивается качеством, количеством и скоростью обработки информации получаемой с технологических объектов, в виде электронных таблиц и баз данных. Производственный цикл организации, реализован таким образом, что он может включать перекомпоновку информации, объединять данную информацию с другой, накапливать информацию.
Успешный процесс переработки и перекачки нефти и газа зависит от строгого контроля и поддержания на заданном уровне технологических параметров, а также от контроля качества выходного продукта. Поддержание с заданной точностью на заданном уровне параметров быстротекущих процессов при ручном управлении оказывается очень трудоемким, а порой и не возможным. Таким образом, современный этап развития добычи и переработки нефти и газа немыслим без применения контрольно-измерительных приборов и микропроцессорной технологии, для повышения эффективности работы нефтегазодобывающего предприятия.
В данном дипломном проекте разрабатывается система автоматизированного управления печами ПТБ-10 УППН ЦПС «Дружное», которая предназначена для контроля, управления, регулирования и сигнализации событий, происходящих на данном технологическом объекте.
Автоматизированная система — это совокупность управляемого объекта и автоматизированных управляющих устройств, в которой часть функций управления выполняет человек. Автоматизированная система получает информацию от объекта управления, передаёт, преобразует и обрабатывает её, формирует управляющие сигналы и выполняет их на управляемом объекте.
1. Характеристика УППН ЦПС «Дружное»
1.1 Назначение и состав УППН ЦПС «Дружное»
УПН ЦПС предназначена для приема и подготовки обводненной нефти с месторождений Дружного, Кустового, Восточно-Придорожного. Для аварийного хранения подготовленной и обводненной нефти в резервуарах, очистки пластовых и сточных вод с последующей подачей их на КНС, для закачки в систему поддержания пластового давления. Подготовленная нефть, без балластных примесей, подается в магистральный нефтепровод «ЦПС-ЛПДС „Апрельская“».
В состав установки входят:
два единых технологических блока — ЕТБ-1 и ЕТБ-2 — открытого типа;
насосный блок перекачки и подачи деэмульгатора;
блок приготовления и дозирования ингибитора коррозии;
узел печей;
насосная внешней перекачки;
концевая сепарационная установка (КСУ);
узлы сбора аварийных, дренажных, промдождевых стоков, утечек, уловленной нефти и шлама;
очистные сооружения пластовой и сточных вод;
насосная подачи очистных стоков на КНС-1,3 месторождения «Дружное»;
резервуарный парк товарной нефти;
узел учета нефти;
противопожарная насосная станция с узлом приготовления и хранения пенораствора;
блоки управления;
факельная система низкого и высокого давления;
операторная;
административно — бытовой корпус — АБК;
насосная внешней перекачки на НПЗ;
резервуарный парк подтоварной воды;
блоки управления задвижками.
Проектная производительность УПН ЦПС — 60 млн. т./год товарной нефти.
Сырьем установки подготовки нефти является смесь обводненных нефтей Дружного, Кустового и Восточно-Придорожного нефтяного месторождения.
Физико-химические свойства сырой нефти на входе в ЦПС приведены в таблице 1. Качество товарной нефти должно соответствовать значениям, которые приведенны в таблице 2.
Таблица 1 — Физико-химические свойства сырой нефти
№ | Наименование параметра | М/р «Дружное» | М/р «Кустовое» | М/р «Восточно-Придорожное» | |
Содержание газа, м3/т. | |||||
Плотность, кг/м3 | |||||
Вязкость, сСт при 20 0С при 50 0С | 12,51 6,55 | 12,51 6,55 | 12,51 6,55 | ||
Плотность газа, кг/м3 | 0,853 | 0,853 | 0,853 | ||
Содержание в нефти, % масс. серы парафинов смол асфальтенов | 0,58 2,16 12,30 3,80 | 0,58 2,16 12,30 3,80 | 0,58 2,16 12,30 3,80 | ||
Объемное содержание, % масс, до 100 0С до200 0С до 300 0С | 5,50 26,00 46,00 | 5,50 26,00 46,00 | 5,50 26,00 46,00 | ||
Содержание хлористых солей, мг/дм3 | |||||
Компонентный состав газа, % масс азот двуокись углерода метан этан пропан изобутан н-бутан изопентан н-пентан | 1,17 0,14 81,42 4,23 7,63 1,61 2,41 0,53 0,35 | 1,17 0,14 81,42 4,23 7,63 1,61 2,41 0,53 0,35 | 1,17 0,14 81,42 4,23 7,63 1,61 2,41 0,53 0,35 | ||
Таблица 2 — Показатели качества товарной нефти по ГОСТ 9965–76
№ | наименование показателя | числовое значение | |
Содержание воды, не более, % | 0,5 | ||
Содержание хлористых солей, не более, мг/л | |||
Содержание механических примесей, не более, % | 0,05 | ||
Давление насыщенных паров при температуре нефти в пункте сдачи, не боле, Па (мм рт. ст.) | 66650(5000) | ||
1.2 Описание технологического процесса подготовки нефти
Обводненная нефть поступает по трубопроводу с ДНС-1 м/р «Дружное», «Восточно-придорожное», «Кустовое», с кустов № 7, 10, 17, 38, 26, 28, 39, 76, принадлежащих ЦДНГ-3, в общий коллектор. Из коллектора с температурой 15−350С и давлением 0,6−0,9 МПа и максимальной обводненностью до 80% поступает на УПН (Установка Подготовки Нефти) производства ГДР, где двумя параллельными потоками сырая нефть поступает на единый технологический блок ЕТБ-1,2.
Технология подготовки нефти подразделяется на ступень обессоливания, перед которыми расположены ступени сепарации. Необходимая рабочая температура ступеней обессоливания составляет примерно 25єС.
Если технологические параметры сырой нефти на входе УПН ЦПС удовлетворяют требованиям нормального протекания технологического процесса, то сырая нефть может быть направлена на концевую сепарационную установку (КСУ) и далее в товарный парк, минуя печи подогрева нефти ПТБ-10/1−4 и единый технологический блок ЕТБ-1,2.
При поступлении нефти с температурой менее 30єС, часть сырой нефти подается на предварительный подогрев в печи П-1/1−4. В печи, нефть подогревается до температуры 40−450С и подается двумя потоками на ЕТБ-1 и ЕТБ-2, где подогретые и холодные части потока сырой нефти объединяются до подачи в сепараторы нефти С-1/1,2.
Регулирование температуры на выходе из печей производится изменением количества топливного газа, подаваемого на горелки печей.
Для защиты печей ПТБ-10 от высокого давления нефти установлены предохранительные клапаны на трубопроводах выхода нефти из печей.
Контроль температуры сырой нефти производится перед сепараторами С-1/1,2, для компенсации незначительных колебаний температуры. В поступающих потоках сырой нефти внутри ЕТБ-1,2 имеется возможность подачи теплой пластовой воды со ступеней обессоливания. Тем самым одновременно улучшается процесс коагуляции эмульсии сырой нефти.
Сепараторы С-1/1,2 оборудованы местными индикаторами температуры и давления, регуляторами давления с клапанами, установленными на линии выхода попутного газа после центробежных сепараторов Ц-1/1,2, регуляторами уровня с клапанами, сигнализаторами предельного уровня и предохранительными клапанами. Уровень в сепараторе нефти С-1/1,2 регулируется таким образом, чтобы емкости заполнялись нефтью до половины. Этим самым достигается максимальная поверхность дегазации.
Из сепаратора С-1/1,2 нефть поступает в один из шести отстойников О-1/1−6. Для достижения необходимой степени обезвоживания соответственно 3 отстойника включаются параллельно, в них содержание пластовой воды уменьшается от предельного 80% до 10% веса. Отстойники О-1/1−6 оборудованы местными индикаторами давления, температуры и приборами сигнализации уровня.
С отстойников нефть по общему коллектору поступает в электродегидраторы ЭГ-1/1−4.
Пластовая вода с отстойников О-1/1−6 и электродегидраторов ЭГ-1/1−4, через общий коллектор поступает в очистные сооружения РВС-5000 № 11, также в этот резервуар с помощью насоса Н-9/3 поступает подтоварная вода с РВС-10 000 6/1−4.
Очистка пластовой воды производится в последовательно работающих резервуарах РВС-5000 № 11−14. Объем каждого резервуара составляет 5000 м³. При нормальных режимах работы подтоварная вода поступает в РВС-5000 № 11 и по трубопроводу перетекает в РВС-5000 № 12. Далее она поступает в РВС-5000 № 13 и РВС-5000 № 14.
С РВС-5000 № 14 подтоварная вода поступает на прием насосов Н-19/1−6, которые подают пластовую воду на прием насосов КНС-1 и КНС-3 м/р «Дружное».
Для откачки нефтяной пленки, образовывающейся при отстое в резервуарах, предусмотрена возможность откачки с высоты 7 и 9,5 м через открытие задвижек на прием насосов Н-17/2 или самотеком в Е-17, откуда отстоявшаяся нефть погружным насосом Н-17/1 откачивается в трубопровод, по которому транспортируется товарная нефть от ЕТБ-1,2 до КСУ.
Окончательное обезвоживание и обессоливание нефти осуществляется в соответствующих параллельно включенных электродегидраторах ЭГ-1/1,2 или ЭГ-1/3,4. В результате обезвоживания и обессоливания содержание пластовой воды в нефти после электродегидраторов снижается до 1,5% веса, а содержание солей до 250 мг/л.
Пластовая вода из электродегидраторов поступает в РВС-5000 № 11−14.
В верхней части электродегидраторов и отстойников предусмотрена возможность периодичного отвода попутного газа в линию некондиции или на свечу.
При достижении в электродегидраторах требуемого качества, нефть поступает на КСУ, которая состоит из четырёх газовых сепараторов С-2/1−4. В сепараторах С-2/1−4 производится дегазация нефти при давлении не более 0,005 МПа.
Нефть после КСУ по трубопроводу диаметром 800 мм поступает на приём насосов внешней перекачки, по трубопроводу диаметром 1000 мм подается в РВС-10 000 № 6/3.
Из резервуара РВС-10 000 № 6/1 через соответствующие задвижки из заборного трубопровода с высоты 4 м и 7 м перетекает в РВС-10 000 № 6/2 и подается на прием насосов внешней перекачки.
Нефть с РВС-10 000 № 6/3 через соответствующие задвижки из заборного трубопровода, установленного на высоте 4 м и 7 м перетекает в РВС-10 000 № 6/4. Далее при открывании соответствующих задвижек на выходе соединяется с потоком товарной нефти из РВС-10 000 № 6/2, и поступает на НВП.
Образующаяся в резервуарах подтоварная вода поступает на прием насосов Н-9/1−4.
Также предусмотрена система размыва осадка в резервуарах РВС-10 000 № 6/1−4 и их опорожнение в систему канализации через погружные емкости Е-½−4.
Для эффективного опорожнения осадков и подтоварной воды была предусмотрена перемычка с Е-½−4 на насосы Н-9/1−4, осадки с РВС-10 000 № 6/1−4 поступают в резервуарный парк пластовой воды.
С РВС-10 000 № 6/1−4 товарная нефть поступает на прием насосов внешней перекачки НВП 1−4.
Товарная нефть на прием насосов внешней перекачки также может поступить из сепараторов С-2/1−4 КСУ, в том случае, если нефть удовлетворяет требованиям предъявляемым к товарной нефти.
Нефть после насосов НВП поступает на коммерческий узел учета нефти (УУН).
Коммерческий узел учета нефти предназначен для контроля параметров перекачиваемой товарной нефти и состоит из пяти рабочих и одной контрольной линии, блока качества и турбопоршневой установки.
Нефть поступает на контрольные линии, проходит через фильтры, струевыпрямители, турбинные преобразователи расхода типа «Smit-150» и регуляторы расхода, после чего товарная нефть поступает в магистральный нефтепровод ЦПС м/р «Дружное» ЛПДС «Апрельская».
Товарная нефть через пятислойный или щелевой пробоотборник поступает в блок качества нефти, на котором установлены вискозиметр, влагомер, термометры, приборы отбора проб, манометры, регулятор расхода.
Нефть из блока качества поступает на прием насосов внешней перекачки.
Товарная нефть также через регулятор расхода, поступает на турбопоршневую установку, которая служит поверочной. Для поверки турбопоршневой установки предусмотрены линии с запорной арматурой.
Все данные о расходе, давлении, температуре, качестве нефти выведены на монитор ЭВМ и приборный блок вторичных приборов.
На трубопроводе, после измерительных линий, установлен прибор показывающий давление, сигнализирующий о минимальном и максимальном давлении и подающий команду на остановку насосов НВП-1−4 при аварийных показателях.
На выкидном трубопроводе с насосов НВП перед задвижкой на выходе врезаны задвижки, предназначеные для подачи товарной нефти на нефтеперерабатывающий завод и УПТН-2 и для отпуска нефти через нефтеналив.
Схема отвода и возврата в технологический процесс некондиционной нефти В случае создания на установке подготовки нефти (ЕТБ-1,2, печи ПТБ-10/1−4) ситуации, когда ведение нормального технологического процесса становится невозможным, сырая нефть направляется минуя УПН на КСУ и далее в один из резервуаров РВС-6/1−4. Такая схема подачи сырой нефти может продолжаться до тех пор, пока уровень в РВС-10 000 не достигнет максимально допустимого значения.
Схема отвода газа и факельная система Выделяющийся в сепараторах С-2/1−4 на ЕТБ-1,2 попутный газ поступает в каплеотбойники Z-1,2, (кроме этого предусмотрена байпасная линия помимо каплеотбойников). Далее газ направляется на установку подготовки газа (УПГ). Давление в линии газа и сепараторах контролируется с помощью манометров и должно составлять не более 0,005 МПа.
При неполадках на УПГ или увеличении давления на КСУ, предусмотрена возможность перевода газа на факел низкого давления.
Поступающий в факельную систему газ сжигается на свече высотой 30 м (200мм). Для отделения конденсата на факеле высокого и низкого давления (700мм) предусмотрен расширитель — 1200 мм и длиной 20 м. Снизу расширителя газовый конденсат факела низкого давления сливается самотеком в емкость Е-10/5, откуда погружным насосом Н-10/5 откачивается в трубопровод нефти на КСУ. Аналогичным образом в этот же трубопровод откачивается и газовый конденсат из факельной системы высокого давления и УПГ насосом Н-10/6 из Е-10/6.
В трубопроводы факельной системы газа высокого давления поступает газ от предохранительных клапанов, расположенных на выкидных линиях газа из аппаратов С-1/1,2, С-2/1−4, С-10, БУ-6, а также газ, отделившийся при дыхании дренажных емкостей УПН и УПГ.
Ёмкости Е-10/5 и Е-10/6 оборудованы змеевиком подогрева конденсата в зимнее время оснащены приборами контроля и сигнализации уровня. На выкидном трубопроводе насосов Н-10/5,6 имеются электроконтактные манометры.
Схема подачи топливного газа и воздуха на горелки печей ПТБ-10/1−4
В качестве топлива в печах ПТБ-10/1−4 применяется осушенный компримированный газ с УПГ.
Для осушки от конденсата сепараторы С-9 и С-10 оснащены местными приборами измерения температуры, давления, уровня, а также для защиты от повышения давления предохранительным клапаном, сбрасывающим давление в трубопровод факела высокого давления (Ф.В.Д.).
Отделившийся в сепараторе С-10 конденсат сливается в дренажные емкости. Газ из С-10 поступает в блок управления (БУ-6), потом через регулирующие клапан двумя потоками поступает в газорегулирующие пункты (ГРП) печей ПТБ-10/1−4 через электрозадвижки (поз. 5).
Регулирование давления топливного газа осуществляется комплексом приборов (поз. 81, 86, 87) и с помощью регулирующих клапанов (поз. 85, 88), установленных на параллельных потоках топливного газа из сепаратора С-10 и из ГРУ, чем обеспечивается равномерное давление топливного газа — 2кг*с/см2 (0,2 МПа) для печей. На входе газа в печь измеряется его давление (поз. 30) и температура (поз. 14). В узле регулирования газа ГРП, топливный газ проходит фильтры очистки от технических примесей, контролируется расход топливного газа (поз. 13). При помощи клапана (поз. 34) происходит регулирование подачи топливного газа к горелкам печей ПТБ-10/1−4.
Соотношение топливного газа и воздуха, подаваемого на сгорание двумя потоками по линии основного газа и по линии запального газа, поступает к четырем горелкам каждой печи. Воздух к горелкам подается от воздуходувок установленных в каждой печи.
Количество подаваемого воздуха автоматически регулируется в зависимости от заданного соотношения «топливный газ-воздух» и составляет от 1:8 до 1:13. На трубопроводах основного и запального газа установлены быстрозакрывающиеся клапана-отсекатели (поз. 27, 28, 29, 35, 36, 37), перекрывающие подачу газа к печам при срабатывании блокировок. В зависимости от температуры нефти на выходе из печи регулируется количество топливного газа, подаваемого в камеру сгорания.
Печи ПТБ-10/1−4 защищены следующими блокировками:
при снижении расхода нефти через змеевик печи ниже допустимого (поз. 18);
при повышении температуры нефти на выходе из печи выше допустимого (поз. 19);
при снижении давления топливного газа перед ГРУ ниже допустимого (поз. 25);
при повышении давления топливного газа к горелкам печи выше допустимого (поз. 40);
при повышении давления запального газа к горелкам печи выше допустимого (поз. 43);
при повышении температуры дымовых газов выше допустимого (поз. 51, 52);
при снижении давления воздуха ниже допустимого (поз. 21);
при погашении пламени горелки (поз. 50, 54, 58, 61);
при снижении расхода воздуха ниже допустимого (поз. 22).
При срабатывании одной из блокировок прекращается подача топливного газа путём закрытия клапанов-отсекателей на трубопроводе топливного и запального газа.
Схема опорожнения продуктовой системы печей ПТБ-10
В целях быстрого опорожнения трубной системы печи в аварийных случаях, а также при проведении ремонтных работ предусмотрено опорожнение продуктов системы печи через аварийный трубопровод продукта в аварийную емкость Е-5. Процесс опорожнения, в случае аварии, происходит от аварийной кнопки через электрозадвижку (поз. 6).
При этом:
закрываются электрозадвижки установленные на трубопроводах подачи нефти в печь (поз. 3, 4);
открывается электрозадвижка установленная на трубопроводе сброса сырой нефти в аварийную емкость Е-5 (поз. 6);
открываются электрозадвижки установленные на трубопроводе подачи пара в продуктовую систему печи П-1/1−4 (поз. 7, 31).
Продукт аварийного сброса подается в подземную емкость Е-5 и оттуда погружным насосом Н-6 направляется в резервуарный парк.
Система пароснабжения ЦПС Для тушения возможных возгораний в камерах сгорания и в случае прогара змеевика, предусмотрена возможность подачи пара в блоки печей. Пар также может быть использован для пропарки змеевика печей в случае необходимости остановки печи и опорожнения змеевика.
Пар поступает на ЦПС по трубопроводу диаметром 100 мм от котельной. Далее по трубопроводу диаметром 80 мм пар подаётся к площадке печей ПТБ-10/1−4, откуда двумя параллельными потоками может быть направлен к змеевикам и в камеры сгорания печей через электрозадвижки (поз. 7, 8) соответственно.
Имеется также возможности подачи пара к любой из печей независимо от других при помощи вентилей.
В случае прекращения подачи пара на ЦПС должны быть открыты спускники на трубопроводе пара для опорожнения.
1.3 Обзор существующей системы автоматизации и её недостатки
Существующая система автоматизации технологического процесса УПН ЦПС «Дружное» представляет собой совокупность первичных и вторичных приборов различного назначения и конструкции. Эти приборы предназначены для контроля, сигнализации и регулирования технологических параметров.
Сигналы с первичных и вторичных приборов поступают на существующую систему автоматизации, реализованную на 12 контроллерах MRS.
Первичные приборы — это полевое оборудование, находящееся непосредственно на технологических объектах и трубопроводах. Оно предназначено для преобразования таких параметров, как давление, уровень, расход, температура в стандартные электрические сигналы для последующей их передачи на вторичные приборы в операторную.
Вторичные приборы — это устройства, которые преобразуют электрические сигналы от первичных датчиков в визуальную информацию, необходимую оператору ЦПС для ведения технологического режима.
На вторичные приборы выводятся: количественное значение технологических параметров с последующей их регистрацией, сигнализация превышения параметра норм режима технологического процесса, состояние насосного и других видов оборудования.
Для решения задач регулирования технологическими параметрами применяются микропроцессорные регуляторы RLS в комплексе с запорно — регулирующей арматурой.
В качестве первичных и вторичных преобразователей используются: для температуры ТСМ, ТСМУ, УМС, для давления ДРГМ, Метран, для загазованности СТМ-10, для уровня ДУУ2, УГР-1М, СУ215, для расхода «Взлёт» и др., а в качестве дополнительных средств управления огромное количество БСУ, граничных сигнализаторов и графопостроительных приборов.
Система управления MRS-8, совместно с блоком управления BDE, предназначена для логической обработки поступающих от MRS 3,4,5,6 в кодированном виде групповых сигналов (аварийные и предупредительные аварийные сигналы) и их декодирование.
Каждая из MRS 1,2 отнесена к двум печам. С одной стороны они выполняют прямую связь с четырьмя системами управления площадки печей (печными MRS) и обработки сигналов для коммуникации процесса из операторной (управление, сигнализация), а с другой стороны — управление задвижками продукта и топливного газа, отнесенными к площадке печей, а также пожарными задвижками.
Задания управления самой площадкой печей, включая управление и сигнализацию по месту выполняются одним MRS, установленным в каждом блок — боксе печи.
Существующее оборудование КИПиА ЦПС в малой степени удовлетворяет требованиям по автоматизации производственных процессов и позволяет осуществлять контроль и управление процессом подготовки и транспортировки нефти лишь частично. Из-за большого объема информации, фиксируемого на различных приборах и табло в течение всей смены, от оператора требуется большая сосредоточенность при контроле технологического процесса, при этом велика вероятность упущения какого либо параметра. Ход технологического процесса фиксируется в вахтовых журналах вручную. При этом не исключена возможность ошибок и преднамеренного искажения информации (человеческий фактор). Обмен информацией с комплексной информационной системой невозможен, передача сводок производится по телефону радиостанции. Такая система не имеет возможности гибкого перенастраивания, и при изменении технологического режима или замене оборудования требует много времени на переналадку.
Система не позволяет производить дистанционный запуск оборудования и аварийное опорожнение аппаратов ввиду отсутствия электрифицированной запорно-регулирующей арматуры на линиях аварийного опорожнения аппаратов. Существующее оборудование КИПиА печей ПТБ-10 не удовлетворяет современным требованиям по автоматизации производственных процессов (оборудование морально и технически устарело) и не позволяет осуществлять автоматическое управление процессом подогрева нефтяной эмульсии. В процессе подготовки и перекачки нефти могут возникнуть непредсказуемые (аварийные) ситуации, когда сконцентрированность и оперативность обслуживающего персонала играет важную роль в стабилизации ситуации. Практически все операции при внештатной ситуации производятся вручную. Это требует времени и трудозатрат, что в конечном итоге влияет на масштабность последствий.
Описание контроллера MRS
Контроллер MRS был разработан в 1978 году в Германии. Его основа — центральный арифметический узел, который является подобием процессора, собранного на дискретных элементах И, ИЛИ, НЕ, регистрах, дешифраторах и т. д. Программа храниться в узле памяти и сервиса (EPROM). По средствам плат ввода/вывода контроллер опрашивает различные сигнализаторы и выдаёт команды управления. Структура MRS 702/703 представлена на рисунке 1.
Рис. 1 — Структура контроллера MRS-702/703
Основные недостатки контроллера MRS-702/703:
ограниченное число входов/выходов (максимум 120);
только дискретные входы/выходы, т. е. отсутствие аналоговых и импульсных входов/выходов;
программаторы вышли из строя;
платы ввода вывода содержат релейные элементы, которые нуждаются в замене;
свой язык программирования;
скорость обработки 26 мс 1 КБайт инструкций;
взаимодействие между собой: с выхода платы одного контроллера на входы другого;
очень ненадёжные источники питания, изменение питания на 0,2 В приводит к остановке контроллера (питание контроллера 24В);
отсутствие стандартных протоколов связи (RS-232, RS-485);
большое потребление энергии (5А каждый);
постоянный перегрев, вследствие чего останов контроллера;
высокая чувствительность к внешним наводкам;
не ремонто-пригоден, выход каких-либо элементов на платах приводит к замене всей платы целиком;
громоздкость;
отсутствие поддержки завода-изготовителя (завод больше не существует);
Средством управления является диспетчерский пульт, оборудованный рядом вторичных и регистрирующих приборов, множеством выключателей и ручными регуляторами.
Основным видом управления является релейно-гидравлическое управление. Использование пневматических и гидравлических устройств для регулирования, сигнализации и измерения обуславливает в холодное время года выход из строя ряда устройств.
Необходимо отметить, что на установке уже применяются современные системы автоматизации. Одна из таких систем установлена на коммерческом узле учёта нефти. Там используется система на базе контроллера QFLO. В диспетчерском пункте узла учёта нефти установлен компьютер, отображающий данные датчиков расхода, давления и температуры.
2. Разработка системы автоматизированного управления печами ПТБ-10 УППН ЦПС «Дружное»
2.1 Назначение и цель создания системы
Основанием для разработки данной системы является необходимость в замене устаревшей системы автоматизации печей ПТБ-10 УППН ЦПС «Дружное» на современные системы управления, повышение надёжности управления, удобства и качества управления. Разрабатываемая система автоматизированного контроля и управления печей ПТБ-10 УППН ЦПС «Дружное» предназначена:
для контроля за состоянием основного и вспомогательного технологического оборудования печей;
для управления в автоматическом режиме технологическими процессами подогрева нефти;
для снижения потребности в использовании вторичной аппаратуры;
для создания информационной сети с выводом информации о состоянии технологических объектов управления УППН на уровень ЦИТС и НГДУ;
для снижения трудозатрат на техническое обслуживание основного и вспомогательного технологического оборудования печей ПТБ-10.
Конечной целью разработки системы является:
достижение более высокого уровня автоматизации технологических объектов УППН;
обеспечение оперативного контроля над технологическими параметрами процессов подогрева нефти и достоверности контроля количественных и качественных параметров за отчётный период;
выдача, при необходимости, регулирующих и управляющих воздействий;
минимизация простоев основного и вспомогательного технологического оборудования;
документирование основных контролируемых технологических параметров;
обеспечение защиты информации от несанкционированного доступа.
В функции системы управления входит:
организация интерфейса операторов;
управление подогревом нефти;
функциональный контроль;
обеспечение сопряжения с другими системами;
выдача отчетов;
Поэтому система управления должна обеспечивать:
автоматическое управление технологическим процессом;
получение достоверной информацию с технологических объектов;
повышение оперативности управления процессом;
внедрение математических методов контроля и управления процессами;
вести автоматическое архивирование всех технологических параметров;
отображать графически технологическую информацию;
значительно снизить влияние «человеческого» фактора в управлении процессом;
повысить безопасность производства.
Выполнение большинства операций контролируется из операторной. АСУ поддерживает интерфейс «Человек — машина» в любой момент времени, когда оператор получает указания, вводит данные или подтверждает получение инструкций на выполнение операций, которые координируются АСУ [4,5].
2.2 Общая структура системы
Структурная схема системы автоматизированного контроля и управления представлена на рисунке 2.
Рис. 2 — Структурная схема системы автоматизированного контроля и управления Из структурной схемы автоматизированного контроля и управления, представленной на рис. 2, видно, что в проекте используется 2 контроллера. Первый из которых отнесён к первой и второй печи ПТБ-10, а второй контроллер к третьей и четвертой печи. За счёт чего происходит увеличение надёжности системы, т.к. неисправности, связанные с выходом из строя одного контроллера, не влечёт за собой полного нарушения технологического процесса на УПН ЦПС «Дружное».
В измерительном помещении печей устанавливается промышленный компьютер [6], предназначенный для отображения информации о текущем состоянии агрегата по месту и для управления соответствующей печью, что необходимо для обслуживающего персонала. Также компьютер устанавливается в помещении операторов ЦПС, он предназначен для отображения полной информации о ходе технологического процесса подогрева нефти и его управления.
2.3 Уровень контрольно-измерительных приборов и автоматики
Основные требования к КИП и исполнительным механизмам Качество работы проектируемой системы управления во многом зависит от применяемых контрольно-измерительных приборов (КИПиА) и исполнительных механизмов. Именно эти устройства находятся непосредственно на объектах и подвергаются воздействию, как со стороны технологических факторов, так и со стороны атмосферных явлений. В связи с этим к контрольно-измерительным приборам и исполнительным механизмам предъявляется ряд требований:
устойчивость к технологическим параметрам (температура, давление, вибрации);
взрывобезопасность;
работа при низких температурах (до -50оС);
высокая надёжность работы;
точность показаний.
Все эти факторы учитывались при выборе контрольно-измерительных приборов и исполнительных механизмов. Необходимо отметить, что все приборы КИПиА были выбраны с участием представителей цеха автоматизации производства НГДУ «Дружбанефть». В приложении Д перечислены все измеряемые и управляющие сигналы УППН ЦПС «Дружное», пределы изменения этих параметров, соответствующие измерительные приборы с измеряемыми диапазонами.
Комплекс технических средств уровня КИПиА Приборы для измерения температуры Для измерения температуры нефти на входе и выходе печи, в трубах змеевика, температуры газа на входе в печь, температуры в технологических помещениях, применяются термопреобразователи с унифицированными токовыми выходами ТСМУ/1−288 Ех с различными длинами чувствительных элементов.
Для измерения температуры выхлопных газов применяется термопреобразователь с унифицированными токовым выходом ТХАУ/1−205 Ех.
Данные термопреобразователи предназначены для измерения температуры газов, жидкостей и сыпучих средств и обеспечивают непрерывное преобразование температуры в унифицированный токовый сигнал. Термопреобразователи используются в системах автоматического контроля, регулирования и управления технологическими объектами. Краткие технические характеристики прибора:
диапазон выходного сигнала, мА: 4…20;
длина монтажной части, мм: выбирается из ряда;
предел приведённой погрешности, %: 0.25, 0.5;
напряжение питания, В: 18.36;
устойчивость к воздействию вибраций по ГОСТ 12 997–84: группа № 3 (n=5−80Гц, А=0.075мм, g=9.8м/с2);
потребляемая мощность, Вт: не более 0.8;
вид взрывозащиты: ГОСТ 12.2.020−76 1ЕхdIICT6X.
Термопреобразователь состоит из первичного преобразователя температуры и измерительного преобразователя. В качестве первичных преобразователей используются термопреобразователи сопротивления с НСХ и преобразователи термоэлектрические с НСХ ХА (К). Измерительный преобразователь предназначен для преобразования температуры в токовый сигнал. Данный преобразователь содержит компенсатор нелинейности сигнала первичного преобразователя температуры и компенсатор холодного спая для ТХАУ. Измерительный преобразователь закреплён в головке первичного преобразователя температуры на четырех металлических шпильках, которые служат для подключения линии связи к блоку питания и измерительному прибору или к барьеру искрозащиты. На рисунке 3 представлена схема подключения преобразователя.
Рис. 3 — Подключение термопреобразователя с токовым выходным сигналом Приборы для измерения давления Для измерения давления в трубопроводах нефти и газа в печах ПТБ-10, газовых сепараторах, в данном проекте используются датчики избыточного давления-разряжения МИДА-ДИ-13Ех, рассчитанные на различный диапазон значений измеряемого давления.
Датчики МИДА предназначены для измерения избыточного давления-разряжения жидкости и газов и преобразование давления в унифицированный токовый сигнал. Эти датчики применяются в системах автоматизации технологических объектов. Краткие технические характеристики прибора:
диапазон выходного сигнала, мА: 4…20;
диапазон рабочих температур, оС: −40…+80;
предел приведённой погрешности, %: 0.25, 0.5;
напряжение питания, В: 12.36;
устойчивость по механике: G2;
потребляемая мощность, Вт: не более 1;
вид взрывозащиты: искробезопасная электрическая цепь OExiaIICT4.
Несмотря на то, что по паспорту датчики работают до -40оС, на практике они дают правильные показания и при -50оС.
Конструктивно датчик состоит из двух блоков: первичного преобразователя и электронного блока, соединеные между собой кабельной перемычкой. Датчик подсоединяется к рабочей магистрали с помощью штуцера. Измеряемое давление подводиться через штуцер в рабочую полость первичного преобразователя датчика и воздействует на приёмную мембрану, вызывая её прогиб и изменение сопротивления тензоризисторов, которое преобразуется в сигнал разбаланса мостовой схемы и затем в выходной сигнал датчика.
Схема подключения датчиков МИДА к блоку питания МИДА-БПП102-Ех-2−03 представлена на рисунке 4.
Некоторые датчики МИДА, для индикации значения давления по месту снабжена цифровыми индикаторами МИДА-ИЦ201-Ех.
Рис. 4 — Схема подключения датчиков МИДА к блоку питания МИДА-БПП102-Ех-2−03
Приборы для измерения расхода Для измерения расхода газа, воздуха и нефти используются вихревые расходомеры SWIRL-SR. Конструкция расходомера основана на зависимости расхода от частоты пульсаций давления, возникающих в пристеночной области за счет вращательного движения потока. Вращательное движение возникает из-за вихре образующего элемента, расположенного на входе прибора. Пульсации давления воспринимаются тензодатчиком, выход с которого поступает на преобразователь (конвертер), где преобразуется в масштабированный частотный сигнал. Зависимость частоты пульсации давления от расхода линейна в широком диапазоне расходов. Для измерений расхода газов и водяного пара предусмотрена возможность дополнительных измерений давления и температуры с целью расчета массового расхода. Краткие технические характеристики:
схема подключения 2-х проводная;
длина кабеля между сенсором и конвертором, м: 10;
категория взрывозащиты ЕЕх ib IIC T4;
температура измеряемой среды, оС: −55…+280;
температура окружающей среды, оС: −55…+60;
диапазон выходного сигнала, мА: 4…20;
основная погрешность прибора, %: 0,5;
погрешность воспроизведения, %: 0,2;
напряжение питания для Ех — исполнения, В: 14−28.
Конструктивно датчик состоит из двух блоков: первичного (сенсор) и вторичного преобразователя (конвертера) выполненного в виде отдельного блока, соединеные между собой кабелем. Сенсор снабжен фланцами и вставляется в разрыв трубопровода между его фланцами.
Приборы для сигнализации до взрывных концентраций Сигнализация загазованности в технологических помещениях осуществляется сигнализаторами СТМ-10. Сигнализатор СТМ-10 общетехнического применения, который предназначен для непрерывного контроля до взрывоопасных концентраций в воздухе помещений и открытых пространств горючих газов, паров и их смесей.
Краткие технические характеристики датчика:
диапазон выходного сигнала, мА: 4…20, релейный;
число каналов, шт.: в данном проекте 9;
диапазон рабочих температур, оС: −60…+50;
предел приведённой погрешности, %: 1;
напряжение питания, В: 220, 50 Гц;
ток потребления, ВА: не более 15;
вид взрывозащиты: искробезопасная электрическая цепь 1ЕxdIICT4;
срок службы, лет: 10.
Сигнализатор СТМ 10 является автоматическим стационарным прибором, состоящим из блока сигнализации, блока питания и выносных датчиков.
Принцип действия сигнализатора — термохимический. Он основан на изменении теплового эффекта от окисления горючих газов и паров на каталитически активном элементе датчика, дальнейшее преобразование полученного сигнала в модуле МИП и выдачи сигнала о достижении сигнальной концентрации:
сигнализацию красного цвета о достижении концентрации срабатывания аварийной сигнализации;
сигнализацию красного цвета о достижении концентрации срабатывания предупредительной сигнализации;
сигнализацию желтого цвета прерывистую о наиболее вероятной неисправности сигнализатора.
Электронное реле контроля пламени Электронное реле контроля пламени РЕП-2 предназначено для автоматического контроля пламени в топочных камерах котлов и печей.
Реле РЕП-2 обеспечивает:
преобразование сигнала от датчика пламени (штыревой электрод) в дискретный сигнал (размыкание электронного ключа или контакта реле при отсутствии пламени);
самоблокировку при отсутствии пламени;
снятие самоблокировки при наличии пламени или при включенном тумблере розжиг;
аварийное включение сигнализации при пропадании пламени.
Реле состоит из электронного блока и датчика пламени (штыревой электрод диаметром 5 мм).
Блоки питания датчиков и вторичной аппаратуры Для питания датчиков и вторичных приборов ТСМУ, ТХАУ и МИДА используются блоки питания МИДА-БПП102-Ех-2−03. Эти блоки питания предназначены для питания, защиты и преобразования выходного сигнала датчиков и других приборов. Краткие технические характеристики:
количество каналов: 2;
выходное напряжение канала, В: 24 +/-0,072;
входной сигнал, мА: 4.20;
выходной сигнал, мА: 4.20;
диапазон рабочих температур, оС: −10…+50;
напряжение питания, В: 220, 50 Гц;
основная погрешность, %: 0.1;
потребляемая мощность, ВА: не более 7;
устойчивость к механическим воздействиям: № 3 ГОСТ 12 997–84;
вид взрывозащиты: искробезопасная электрическая цепь 1ExibIIВТ5Х.
Блоки управления электроприводом Управление электроприводом регулирующих клапанов установленных на трубопроводах топливного газа и свежего воздуха к горелкам печи, осуществляется с помощью БУЭП-1. Блок управления электроприводом БУЭП-1, выполненный на основе микроконтроллеров. Он предназначен для регулирования степени открытия технологических клапанов и задвижек, снабженных однофазными и трехфазными исполнительными электроприводными механизмами.
Краткие технические характеристики устройства:
токовый выход, мА: 0…20;
токовый вход, мА: 0…20;
напряжение питания, В: 180…242, 50 Гц;
мощность, ВЧА: не более 18;
вид взрывозащиты: искробезопасная цепь ГОСТ 12.2.007.0.
Состояние исполнительного механизма контролируется с помощью реостатных или индуктивных датчиков положения и путевых выключателей. Кроме того, прибор выполняет контроль за током потребления электропривода. Для трехфазного электропривода прибор обеспечивает измерение текущего значения тока потребления по фазе. Индикация степени открытия, выраженная в процентах, осуществляется на семи сегментном светодиодном индикаторе, имеющем четыре знакоместа. Дополнительно, состояние исполнительного механизма индицируется дискретными светодиодными индикаторами «Закрыто», «Открыто», «Авария», «Ток двигателя» (только для трехфазного электропривода).
Рабочая коммутация силовых цепей выполняется полупроводниковым трехфазным реверсивным реле. При возникновении аварийных ситуаций, а также снятии питания со схемы управления, силовые цепи размыкаются электромагнитным реле, включенным до рабочего полупроводникового реле.
Прибор работает под управлением регуляторов с выходным токовым сигналом 0…5 мА или 0…20 мА (режим работы — «Автомат»). Прибор обеспечивает ручное местное или дистанционное управление электроприводом (режим работы — «Местное» или «Дистанционное»).
Входы прибора, обеспечивающие дистанционное управление, предназначены для работы со схемами, которые состоят из «сухих контактов», и не требуют дополнительных источников питания.
Прибор имеет в своем составе:
три дискретных выхода для организации пользователем схем индикации на светодиодах;
четыре дискретных выхода для индикации положения рабочего органа исполнительного механизма;
токовый выход 0…20 мА для индикации степени открытия клапана (задвижки);
токовый выход 0…20 мА для индикации тока двигателя электропривода.
Исполнительные механизмы В качестве регулирующих клапанов используются затворы поворотные дисковые АМ 7.720.324.ГЕ ДУ с различным диаметром. Данные механизмы представляют собой поворотные дисковые затворы — регулирующие в неразъёмном корпусе с металло-резиновым вкладышем.
Краткие технические характеристики:
тип привода: регулирующий электропривод;
давление рабочей среды, МПа: 2.5;
электрическое питание механизма: трёхфазная сеть 380 В., 50 Гц;
температура рабочей среды, °С: до 110.
Для дистанционного управления потоками жидкости, пара или газа, предусмотрено использование задвижек типа ЗКЛ-…/10-эп-30с964нжХЛ с электроприводом УФ 099.016. Допустимая для использования температура окружающей среды до -60°С. Задвижки литые (ЗКЛ) под электропривод, на различный диаметр. Электропривод с двухсторонней муфтой ограничения крутящего момента (пружинный датчик).
Для дистанционного управления затворами подачи воздуха и топливного газа, в горелку печи ПТБ-10, используются однооборотные механизмы электрические МЭО.
Механизмы МЭО в комплекте с запорно-регулирующей арматурой позволяют создавать автоматизированные объекты управления, контроля и регулирования трубопроводными потоками различных жидких и газообразных сред.
В составе механизма имеется датчик положения выходного органа (токовый, индуктивный или реостатный), что позволяет формировать дискретную информацию о крайних и промежуточных положениях рабочего органа арматуры и аналоговую (цифровую) информацию о динамике его перемещения.
Наличие в составе механизма механических ограничителей полного хода выходного органа позволяет предохранить арматуру от механических повреждений при отказе концевых микропереключателей.
Неподвижность маховика ручного дублера при управлении арматурой от электродвигателя создает безопасные условия эксплуатации арматуры и исключает травмирование персонала при переходе на ручное управление арматурой.
По защищенности от попадания внутрь механизма твердых частиц (пыли) и воды, механизмы имеют степень защиты 1Р 54 по ГОСТ 14 254.
Механизмы выпускаются в общепромышленном, а также во взрывозащищенном исполнении (с видом взрывозащиты «искробезопасная электрическая цепь» — «взрывонепроницаемая оболочка»).
Эти механизмы состоят из редуктора, электродвигателя, датчика положения, блока питания и пускателя.
Барьеры искробезопасности и гальванические развязки Для защиты входных и выходных цепей используемых контроллеров и вторичных приборов от высоких напряжений и токов, появляющихся либо в результате отказа оборудования, либо в результате наводок, попадания молний и т. д. необходимо использовать барьеры искробезопасности и гальванические развязки. В данном проекте используются барьеры искробезопасности с гальванической развязкой серии K-System.
Барьеры искробезопасности серии K-System — это компактные, модульные барьеры, которые используются для обеспечения гальванического цепей, находящихся в потенциально взрывоопасных областях, и цепей находящихся в безопасной зоне. Они соответствуют требованиям ГОСТ 22 782.5−78 «Электрооборудование взрывозащищенное с видом взрывозащиты «искробезопасная электрическая цепь» «(маркировка взрывозащиты ExiaIIС).
Схема автоматизации печей ПТБ-10 приведена в приложении А, схема автоматизации системы подачи газа приведена в приложении Б.
2.4 Микропроцессорный контроллер в системе автоматизации печей ПТБ-10
Обоснование выбора контроллера В настоящее время имеется большое количество программно-технических комплексов, предназначенных для решения задач автоматизации. Одно из лидирующих мест по использованию в системах АСУ ТП в России занимают контроллеры корпорации Rockwell Automation.
Здесь можно выделить несколько групп контроллеров отличающихся друг от друга количеством портов ввода/вывода, объемом памяти, предоставлением различных сетевых протоколов, по размеру и т. д. [15, 16]:
micro logic controllers (микроконтроллеры, например MicroLogix 1000) (количество точек ввода/вывода до 32);
small logic controllers (малые программируемые контроллеры, например SLC500) — количество точек ввода/вывода до 960;
programmable logic controllers (например PLC-5) — количество точек ввода/вывода свыше 1000;
контроллеры Control Logix (количество точек ввода/вывода до 128 000 дискретных или до 3800 аналоговых);
контроллеры Soft Logix5 (количество точек ввода/вывода от 896 до 4096).
Существуют ещё большое количество различных программируемых контроллеров. Почти все контроллеры похожи друг на друга по своим свойствам и качествам. По этому на сегодняшний день выбор контроллеров осуществляется в основном по следующим параметрам:
число поддерживаемых входов/выходов;
поддерживаемые протоколы обмена;
фирма производитель;
стоимость оборудования и возможности поставки;
поддержка фирмы производителя;
предпочтения и пожелания заказчика АСУ ТП.
В данной работе выбран контроллер американской фирмы Allen Bradley Company. Этот выбор сделан по рекомендации технического отдела НГДУ «Дружбанефть», который уже использует контроллеры этой фирмы и уверен в надёжности их работы и простоте обслуживания. На сегодняшний день реализована автоматизированная система управления (АСУ) технологическим процессом на ДНС-1 м/р «Дружное» и на установке предварительного сброса воды (УПСВ) м/р «Восточно — Придорожное».
На основании этих требований и фактов, можно сделать вывод, что программируемым контроллером, решающим задачи автоматизации печей ПТБ-10 на УППН ЦПС «Дружное» будет контроллер SLC-5/05.
Процессоры SLCэто быстродействующие, однослотовые процессоры, которые используются для управления и обработки информации. Все процессоры SLC-5 обладают следующими общими свойствами:
поддержка нескольких языков программирования (структурный текст, последовательные функциональные схемы, релейные диаграммы, функциональные блоки);
мощное программное управление (16 основных управляющих программ, управляемые временем и событиями прерывания процессора, PID-алгоритмы);
встроенные коммуникации (RS-232/422/423, сеть Ethernet, Data Highway Plus, сеть управления Remote I/O, дистанция связи удалённого ввода/вывода 3 м);
возможен модуль дублирования связи;
температура внешней среды при работе контроллера, оС: 0…+60;
относительная влажность воздуха, %: 5…95;
часы и календарь с батарейной поддержкой;
механическая прочность: пиковое ускорение 30 g;
вибрация: 10…500 Гц.
Выбранный контроллер SLC-5/05 является Ethernet-процессором, который предлагает встроенные возможности связи Ethernet TCP/IP, что обеспечивает интеграцию разрабатываемой системы в структуру управления НГДУ «Дружбанефть». Сеть Ethernet — это локальная сеть со скоростью связи 10, 100 Мбит/с. Она разработана для быстрого обмена информацией между компьютерами и связанными устройствами. Используя сеть Ethernet, мы получаем фактически безграничные возможности работы в сети: связь между различным оборудованием, свободный доступ к файлам и серверам и многое другое.
Основные характеристики контроллера SLC-5/05 (1747-L553):
максимальная память программы, КБайт: 64;
максимальное количество дискретных входов/выходов: 960;
набор инстукций: 71;
программирование: APS, RSLogix 500 A.I.;
время выполнения битовой инструкции, мкс: 0,37;
время сканирования программы, время/Кслово: 0,9 мс;
память EEPROM, на батарейке.
К одному микропроцессору можно подключить до 30 модулей вводов/выводов, при этом не более 3-х rack.
Возможности АСУТП на базе контроллера ALLEN — BREDLEY
Основное назначение АСУТП на базе контроллера ALLEN — BREDLEY заключается в автоматизированном контроле и управлении параметрами технологического процесса.
Система обеспечивает:
сбор информации о технологическом процессе подогрева нефти с помощью датчиков, установленных на аппаратах, трубопроводах и технологических агрегатах и последующей ее передачи на верхний уровень;
обработку информации с помощью разработанного алгоритма и программного обеспечения;
визуализацию полученной информации на мониторе компьютера в режиме удобном для восприятия оператором;
хранение информации о технологических параметрах за любые промежутки времени в памяти компьютера;
выдачу текстовых и графических сводок в виде таблиц, графиков и сообщений;
выдачу аварийных звуковых и текстовых сообщений;
автоматическое регулирование технологических параметров (температуру нефти на выходе печей, подачу топливного газа и т. д.);
автоматическое управление агрегатами (воздуходувки, вентиляторы) по команде оператора с верхнего уровня управления или по аварийным сигналам от датчиков;
диагностику работоспособности полевого оборудования (датчиков) и контроллеров.
Главное преимущество предлагаемого контроллера — это возможность передачи технологической информации на верхний уровень системы сбора информации, и тем самым повышается оперативность принятия решений аппаратом управления.
Проектная конфигурация контроллера Структурная схема автоматизации четырех печей ПТБ-10 включает в себя два контроллера. Один из которых отнесён к первой и второй печи. а второй контроллер к третьей и четвертой, соответственно. Каждый из контроллеров, рассчитан на резервное управление системой подачи газа к печам ПТБ-10, в случае выхода из строя одного из контроллеров, что обеспечивает увеличение надёжности системы автоматизированного управления и позволяет не нарушать технологический режим работы УПН ЦПС «Дружное». Таким образом, в проекте используется два контроллера с абсолютно одинаковой конфигурацией и программным обеспечением, и поэтому в дальнейшем будем рассматривать систему автоматизированного контроля и управления для первой и второй печи ПТБ-10, включающую в себя систему автоматизированного контроля и управления подачи газа к печам ПТБ-10.