Проектирование высокоэффективных технологических процессов автоматизированного машиностроения и прогрессивных высокопроизводительных средств автоматизации
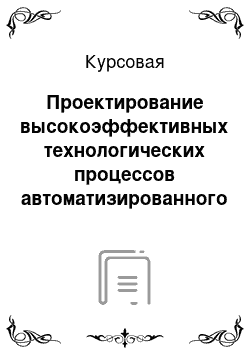
Изобразим циклограмму автоматической линии для вала. Все механизмы на позициях работают независимо и только подают сигналы об окончания зажима. После получения последнего сигнала дается команда на пуск станков. Каждый станок имеет автономную систему управления, которая переключает ее с быстрого подвода на рабочую подачу, а затем и на быстрый отвод. Как только будет сигнал об окончании обработки… Читать ещё >
Проектирование высокоэффективных технологических процессов автоматизированного машиностроения и прогрессивных высокопроизводительных средств автоматизации (реферат, курсовая, диплом, контрольная)
Министерство образования Республики Беларусь
Учреждение образования
«Брестский государственный технический университет»
Кафедра автоматизации технологических процессов и производств
КУРСОВАЯ РАБОТА
по дисциплине:"Автоматизация технологических процессов в машиностроении"
Тема: «Проектирование высокоэффективных технологических процессов автоматизированного машиностроения и прогрессивных высокопроизводительных средств автоматизации»
Выполнил:
студент группы Т-72
IVкурса МСФ Чапко А. Ф.
Проверил:
Иванов В.В.
Брест 2011
- Введение
- 1 Разработка технологического процесса изготовления детали
- 1.1 Анализ конструкции детали
- 1.2 Выбор метода получения заготовки
- 1.3 Разработка технологического процесса
- 1.4 Расчет режимов резания и норм времени
- 2 Проектирование автоматической линии
- 2.1 Разработка структурной схемы автоматической линии
- 2.2 Выбор оптимального варианта структурной схемы автоматической линии
- 2.3 Выбор и компановка технологического оборудования
- 2.4 Выбор и компановка транспортных средств
- 2.5 Выбор метода и средств контроля
- 2.6Планировка автоматической линии
- 2.7Составление циклограммы автоматической линии
- 2.8Анализ циклограммы и математическое описание действия устройств
- 2.9Синтез принципиальной схемы управления
- 3 Синтез принципиальной схемы бесконтактного логического управляющего устройства промышленной автоматики
- 3.1 Словесное описание действия устройства
- 3.2 Анализ устройства и определение входных и выходных параметров
- 3.3 Синтез циклограммы работы устройства
- 3.4 Анализ циклограммы и математическое описание действия устройств
- 3.5Синтез принципиальной схемы управления
- 3.6Анализ проведённой работы
- Заключение
- Список использованных источников
- Приложение
- Введение
- Работа машиностроительных предприятий в условиях рынка требует постоянного совершенствования технологических процессов, средств автоматизации и технологии управления на всех уровнях производства. Известно, что традиционный подход к интенсификации производства, с возможностью быстрого реагирования на потребность рынка заключается во всемерном повышени ипроизводительности технологического оборудования и технологических процессов. Поэтому главная тенденция и особенность современного этапа интенсификации производства состоит в том, что эту проблему необходимо решать по-новому-за счет исключения исчерпывающего себя физического труда человека и расширения применения более гибких форм производства.
- Автоматизация производства в машиностроении — комплексная конструкторско-технологическая задача создания новых технологий и техники, принципиально отличных от арсенала средств неавтоматизированного производства. Генеральное направление автоматизации производственных процессов в машиностроении состоит в создании таких высокоэффективных технологических процессов и высокопроизводительные средств производства, применение которых было бы невозможно при непосредственном участии человека в управлении ими.
- Цель курсового проектирования по автоматизации производственных процессов в машиностроении — приобретение специальных умений и навыков проектирования высокоэффективных технологических процессов автоматизированного машиностроения и прогрессивных высокопроизводительных средств автоматизации.
- 1 Разработка технологического процесса изготовления детали
- 1.1 Анализ конструкции детали
- Анализ конструкции детали произведём с точки зрения её технологичности при обработке на станках, обеспечении требуемой программы выпуска, экономии материала, энергии, затрат производимых при изготовлении детали.
- Данная деталь имеет простую конструкцию. Имеются поверхности для базирования и закрепления на станках на всех операциях.
- Обрабатываемая деталь — ступенчатый вал, изготавливаемый из стали 40, имеет повышенные требования к качеству поверхностей 20, шероховатость которых Ra 1,25 мкм. Шероховатость Ra 3,2 мкм имеют поверхности 26, 34. Центровое отверстие может быть получено сначала сверлением, а затем зенкерованием. Фаски точатся в последнюю очередь. На поверхности с неуказанной шероховатостью в соответствии с чертежом необходимо обеспечить Ra 6,3 мкм.
- При данной форме и конфигурации детали имеется возможность обработки большинства поверхностей проходным резцом. Диаметральные размеры шеек вала убывают к концам вала, что несколько затрудняет их обработку. Шпоночные канавки отсутствуют, что сокращает число операций. В конструкции детали отсутствуют резкие перепады диаметров.
- Деталь имеет достаточную жесткость для применения высокопроизводительных методов обработки.
- Отношение длины вала к минимальному диаметру не должно превышать 15:
- Таким образом, можно сделать вывод, что деталь технологична.
- Рисунок 1.1 Эскиз вала
- 1.2 Выбор метода получения заготовки
- Материал детали сталь 40 — среднеуглеродистая с содержанием углерода 0,4%. Имеет хорошую пластичность, вязкость, высокое сопротивление появлению трещин. Применяют для большой группы деталей машин работающих не только при статических нагрузках, но и в условиях циклических нагрузок. Относится к недорогому конструкционному материалу.
- Заготовку для производства вала можно получить несколькими способами. Рассмотрим следующие из них: литьё под давлением, поперечно-клиновый прокат и использование в качестве заготовки круглого проката. Оценивать тот или иной способ будем по коэффициенту использования металла, подверженности металла данному методу обработки, а так же по себестоимости получения заготовки.
- При литье сталь имеет высокую усадку, низкую жидкотекучесть, склонность к образованию горячих трещин. Припуски на последующую механическую обработку получаются в пределах 4…6 мм, что приводит к уменьшению коэффициента использования металла — много металла уходит в стружку, что приводит к увеличению времени на механическую обработку и удорожанию обработки.
- При использовании круглого проката припуски получаются автоматически, и будут на отдельных частях детали очень большими. Коэффициент использования металла 0,6…0,7. В связи с этим также увеличивается время на обработку, повышается износ инструмента, а значит, возрастает себестоимость готовой детали.
- Наиболее оптимальный способ получения заготовки — это поперечно-клиновой прокат, который позволяет назначить припуски в пределах 1,5…2,5 мм в зависимости от размеров поверхности. При прокате повышаются механические свойства металла. Метод имеет высокую производительность, что удешевляет заготовку. Коэффициент использования металла 0,9.
- 1.3 Разработка технологического процесса
- Операции будут строиться из малого числа простых технологических переходов, то есть технологический процесс разрабатываем по принципу дифференциации операций. Это связано в первую очередь с возможностью отделения сложной и точной чистовой обработки, требующей высокоточных станков, от предварительной черновой обработки, которая может производиться высокопроизводительными способами. Дифференциация в условиях средне — серийного производства является экономически целесообразным построением технологического процесса.
- Минимально возможным числом операций может быть пять, это связано с особенностями и методами обработки отдельных поверхностей вала, а также осуществлением чистовой и черновой обработки на отдельных станках.
- Рисунок 1.2 Эскиз обрабатываемых поверхностей
- Заполним таблицу 1.1.Знак «+» в таблице ставим, если указанный переход необходим при обработке данной поверхности и знак «- «если такой переход не нужен.
- Таблица 1.1 Состав переходов при обработке поверхностей детали
- Обработка валов. Согласно типовому техпроцессу обработки вала и учитывая наличие необходимого оборудования для изготовления данной детали и программу выпуска N = 415 шт/см. Целесообразно изготавливать вал на различных токарных автоматах, полуавтоматах, токарно-револьверных станках. Обработку будем проводить твердосплавным инструментом марок Т15К6, Т5К10, со скоростью 100 — 120 м/мин методом врезания.
- Шлифование целесообразно проводить на кругло-шлифовальных станках с базированием по центровым отверстиям методом врезания.
- Для выхода шлифовального круга нам так же необходимо иметь канавки проточенные на поверхностях для шлифования, такую обработку целесообразно проводить на токарных автоматах, полуавтоматах, токарно-револьверных станках оборудованных вертикальным подрезным суппортом.
- Операции будут строиться из малого числа простых технологических переходов, то есть технологический процесс разрабатываем по принципу дифференциации операций. Это связано в первую очередь с возможностью отделения сложной и точной чистовой обработки, требующей высокоточных станков, от предварительной черновой обработки, которая может производиться высокопроизводительными способами. Дифференциация в условиях средне — серийного производства является экономически целесообразным построением технологического процесса.
- Операция фрезерная: на фрезерном автомате производится фрезерование шпоночного паза.
- Операция фрезерно-центровальная: на фрезерно-центровальном автомате за один установ можно произвести фрезерование торцов вала и их зацентровку.
- Операция токарная: на токарном автомате производится черновое наружное точение шеек вала проходным резцом.
- Операция токарная: на токарном автомате чистовая обработка шеек вала с выдерживанием диаметральных и линейных размеров согласно требованиям чертежа.
- Операция токарная: снятие фаски фасочным резцом.
- 1.4 Расчёт режимов резания и норм времени
- В соответствии с требуемой точностью обработки и шероховатостью поверхностей следует назначать режимы резания: скорость вращения шпинделя, глубину резания, подачу.
- Общий припуск под всю механическую обработку 2,5 мм на сторону. Припуск под черновую токарную обработку — 2 мм, под чистовую — 0,5 мм.
- При фрезеровании торцов принимаем подачу S=0,3 мм/об, частоту вращения инструмента (фрезы) n=700 мин-1, глубину равную припуску на торце t=2,5 мм.
- Длину рабочего хода:
- ,
- где dТ — наибольший диаметр фрезеруемого торца, мм.
- Расчётное время обработки:
- При черновом точении принимаем следующие режимы: глубина резания t=2 мм, подача S=0,5 мм/об., частота вращения заготовки n=650мин-1. Длину рабочего хода принимаем равной длине шейки вала. Расчётное время обработки:
- Остальные режимы резания и время на обработку приведём в технологической карте (таблица 1.2).
- Таблица 1.2 — Маршрут технологического процесса
- 26
- 0,12
- Черновое точение
- шеек
- 49
- 9
- 44
- 10
- 43
- 0,3
- 0,055
- 0,27
- 0,06
- 0,26
- Чистовое точение шеек
- 49
- 9
- 44
- 10
- 0,08
- 0,015
- 0,07
- 0,016
- Нам необходимо сравнить основное технологическое время наиболее продолжительного перехода с располагаемым временем.
- где Ф — номинальный годовой фонд времени АЛ (при двухсменной работе и продолжительности рабочей недели 41 ч., Ф = 3725ч.);
- Q — заданная годовая программа выпуска деталей;
- — коэффициент технического использования АЛ (предварительно может быть принят в пределах 0,7 -0,8 и зависит от числа станков АЛ);
- tв — вспомогательное время, может быть принято 0,15 — 0,40 мин;
- Tа — расчетный такт выпуска.
- Так как у нас время затраченное на самый длительный переход не превышает располагаемого времени, то режимы резания и нормы времени оставляем без изменений.
- 2. Проектирование автоматической линии
- 2.1 Разработка структурной схемы автоматической линии
- В массовом и серийном производстве широко используются автоматические линии.
- Автоматическая линия представляет собой группу станков, расположенных по ходу технологического процесса, связанных между собой транспортной системой и имеющих единую систему управления. Система управления обеспечивает работу всей линии без непосредственного участия человека. Таким образом, АЛ состоит из трех элементов (узлов): станков-автоматов, автоматических транспортных устройств, устройств для автоматического управления и контроля. АЛ обладают высокой производительностью, обеспечивают высокое качество продукции, полностью устраняют тяжелый физический труд.
- АЛ имеют различную структуру и конструктивное выполнение в зависимости от их назначения и конкретных условий работы. Они классифицируются по типу встроенных станков, технологическим признакам, по виду транспортных устройств и способов передачи изделий, по расположению оборудования, по связи между станками и т. д.
- По типу встроенных станков различают автоматические линии из универсальных, специальных и агрегатных автоматов.
- По виду передачи изделий от станка к станку АЛ бывают:
- — со сквозным транспортированием через рабочую зону (преимущество — удобство компоновки, однако обслуживание оборудования усложняется);
- — с верхним транспортированием (облегчается обслуживание станков АЛ, но усложняется транспортная система);
- — с боковым (фронтальным) транспортированием, (но требуется дополнительное устройство для поперечной загрузки заготовок в рабочую зону и съем изделия);
- — с комбинированным транспортированием.
- По расположению оборудования различают замкнутые и незамкнутые АЛ. В замкнутых АЛ автооператор загружает заготовки и снимает с нее готовые изделия на одном месте. Это является преимуществом таких линий, недостаток — затруднительный доступ к оборудованию.
- Большинство АЛ имеют незамкнутое расположение оборудования (прямолинейное, Ш-образное, Г-образное, П-образное и т. д.).
- По виду связи между станками АЛ бывают с жесткой и гибкой связью.
- АЛ с жесткой связью состоят из отдельных станков-автоматов, связанных между собой жесткими транспортными устройствами, которые передают детали в процессе обработки с одного станка на другой. Такие линии называют синхронными, т.к. все станки в них работают в одном такте (время, в течение которого обрабатываются детали на станке). При остановке какого-либо станка останавливается вся линия.
- АЛ с жесткой связью используются для обработки сложных корпусных деталей, а также деталей, требующих для своего перемещения приспособлений-спутников. Транспортная система АЛ проходит через все рабочие позиции; во время обработки деталь, как правило, не снимается с транспортера, фиксируется и зажимается на базовых поверхностях.
- АЛ с гибкой связью называют несинхронными. Они состоят из независимо работающих по времени станков с гибкой транспортной связью. Такие линии снабжаются бункерами-накопителями для хранения определенного запаса деталей, откуда эти детали поступают на станки-автоматы для обработки. При остановке какого-либо станка АЛ продолжает работать, питаясь запасом деталей из бункера-накопителя.
- АЛ с гибкой связью используются преимущественно для обработки изделий типа коротких тел вращения (кольца подшипников, шестерни, втулки, клапаны и т. д.). Их особенностью является перемещение под действием силы собственной тяжести, что находит широкое применение при межстаночном транспортировании, накоплении заделов и т. п.
- Исходным материалом служат как непрерывные (труба, пруток), так и штучные заготовки, получаемые прокаткой, ковкой, штамповкой, литьем и т. д. Наиболее типовые операции в таких линиях — токарные и шлифовальные, что позволяет для данных типов изделий создавать типовые технологические процессы как стабильную основу для создания автоматических систем.
- В курсовой работе применяем автоматическую линию с гибкой связью. Она состоит из независимо работающих по времени станков с гибкой транспортной связью. Такие линии снабжаются бункерами — накопителями для хранения определенного запаса заготовок, откуда эти заготовки поступают на станки автоматы для обработки. При остановке какого-либо станка автоматическая линия с гибкой связью продолжает работать, питаясь запасом из бункера — накопителя.
- 2.2 Выбор оптимального варианта структурной схемы автоматической линии
- На основе определённого времени на обработку составим типовой технологический маршрут.
- Таблица 2.1 — Типовой технологический маршрут
- Фрезерование торцов
- 0,22
- Черновая токарная обработка шеек вала
- № 2
- № 3
- № 4
- № 5
- 0,3
- 0,055
- 0,27
- 0,06
- Чистовая токарная обработка шеек вала
- № 3
- № 4
- № 5
- 0,13
- 0,76
- 0,15
- Фрезерование шпоночного
- Минимальная компоновка автоматической линии будет состоять из шести позиций: одного фрезерно-центровального автомата, трех токарных автоматов, копировально-фрезерный и одного кругло-шлифовального станка. Лимитирующей позицией является чистовая обработка всех шеек вала — 1,78 мин.
- Дифференцируя общий объём обработки вала на число позиций (станков), можно сократить длительность рабочих ходов цикла. Переходы, основное время которых превышает 0,55 мин, необходимо расчленить на более мелкие. Максимальное число позиций 8 ограничивается невозможностью дробления чистовой обработки шейки 1 на два станка.
- Таким образом, для обработки вала даже при простейшем построении однопоточной обработки и жёсткой межагрегатной связью автоматическую линию можно построить по 4 вариантам q=6…9.
- Следующий вариант дифференциации получается делением чистовой обработки на две позиции.
- Приведём технологическую схему обработки при восьми позиционном варианте (q=9):
- I поз. — 0,34 мин: фрезерование и центрование торцов;
- II поз. -0,355 мин: черновая токарная обработка с одной стороны;
- III поз. — 0,59 мин: черновая токарная обработка с другой стороны;
- IV поз. -0,76 мин: чистовое точение поверхности 4;
- V поз. -0,74 мин: чистовое точение поверхности 6;
- VI поз. -0,28 мин: чистовое точение остальных шеек вала;
- VII поз. — 0,08 мин: снятие фаски;
- VIII поз. -0,26 мин фрезерование шпоночного паза;
- IX поз. — 0,25 мин: шлифование;
- Для выбора варианта структуры автоматической линии необходимо рассчитать производительность автоматической линии по формуле:
- , шт/смену
- где Р=1 — количество параллельных линий,
- ТОmax — время наиболее длительной операции,
- tX=0,2 мин — время холостых ходов рабочего цикла,
- ?Сi=0,12 мин/шт-ожидаемые внецикловые потери одного комплекта инструментов
- te=0,02 мин/штожидаемые простои и внецикловые потери из-за отказов устройств и механизмов,
- ny=1,2,3,4 — число участков,
- w — коэффициент возрастания внецикловых потерь при различных вариантах количества участков.
- Определим QАЛ для варианта q=6, ny=1, ТОmax=1,78:
- шт/см.
- Значения производительностей для других структурных вариантов сведём в таблицу 2.2.
- Таблица 2.2 — Производительности автоматической линии
- Из задания требуемая производительность автоматической линии QАЛ (min)=415 шт/см, с увеличением до Qmax=530 шт/см. В данный диапазон попадает 3 структурных варианта.
- Из этих вариантов выбор оптимального произведём путём сопоставления
- стоимостных характеристик.
- Определим приведённые затраты для каждого варианта
- ,
- где Кi — стоимость оборудования для i-го варианта, у.е.,
- Сi — годовые эксплуатационные затраты для i-го варианта, у.е.,
- ЕН=0,17 — нормативный коэффициент эффективности капиталовложений
- ,
- где САВТ=29 500 у.е. — стоимость одного станка-автомата,
- СНАК=5230 у.е. — стоимость одного накопителя
- СЗУ=3850 у.е. — стоимость одного загрузочного устройства,
- у.е. — стоимость транспортной системы,
- Вариант 1: QАЛ=513 шт/см; ny=1; q=9
- у.е.
- у.е.
- ,
- где А-амортизационные отчисления, принимаем 13% от стоимости оборудования;
- ЗР-затраты на текущий ремонт и межремонтное обслуживание, принимаем 8% от стоимости оборудования;
- ЗПЛ-годовой фонд заработной платы обслуживающих рабочих при двухсменной работе;
- СИН=9650 у.е. — стоимость инструмента и электроэнергии.
- у.е.
- Тогда приведённые затраты:
- у.е.
- При сравнении все полученные значения приведённых затрат должны быть скорректированы на одинаковый выпуск продукции CПi*цi.
- у.е.
- Вариант 2: QАЛ=434 шт/см; ny=2; q=9.
- у.е.
- у.е.
- у.е.,
- Тогда приведённые затраты:
- у.е.
- При сравнении все полученные значения приведённых затрат должны быть скорректированы на одинаковый выпуск продукции CПi*цi.
- у.е.
- Вариант 3: QАЛ=444 шт/см; ny=3; q=9
- у.е.
- у.е.
- у.е.
- Тогда приведённые затраты:
- у.е.
- При сравнении все полученные значения приведённых затрат должны быть скорректированы на одинаковый выпуск продукции CПi*цi.
- у.е.
- 2.3 Выбор и компоновка технологического оборудования
- Выбор и компоновку технологического оборудования обосновываем на базе разработанного технологического процесса. Для обеспечения различных операций техпроцесса в автоматической линии используем оборудование как специально созданное для работы в автоматических линиях, так и приспособленное либо модернизированное для этих целей. При массовом производстве используем специально оснащенные автоматы. Для размещения примем последовательную схему расположения оборудования см. лист 1, на котором изображена схема расположения станков, транспортных потоков заготовок, деталей, уборки стружки. Отображено вспомогательное оборудование и габаритные размеры станков, необходимые для оптимального варианта монтажа автоматической линии.
- Выбор технологического оборудования производим по справочной литературе.
- 1. Двухсторонний фрезерно-центровальный полуавтомат 6C230, исполнение с автоматической сменой деталей.
- Технические характеристики:
- Наибольший диаметр вала, мм… до 100
- Наибольшая длина вала, мм…200
- Частота вращения шпинделя, мин-1…215- 1000
- Общая мощность электродвигателей, кВт…4,2
- Габаритные размеры (ДхШхВ), мм…2850−2055;2100
- Масса, кг…3500
- 2.Токарный многорезцовый копировальный автомат с цикловым программным управлением 1716Ц (класс точности Н), поставляют с автоматическим манипулятором для загрузки-выгрузки деталей.
- Технические характеристики:
- Диаметр обрабатываемой детали, мм… до 200
- Наибольшая длина вала, мм…500(1000)
- Частота вращения шпинделя, мин-1…100 — 2000
- Общая мощность электродвигателей, кВт…22
- Габаритные размеры (ДхШхВ), мм…2465−1215−1900
- Масса, кг…4500
- 3. Одношпиндельный токарно-револьверный автомат модели МЕ226С0:
- Технические характеристики:
- Диаметр обрабатываемой детали, мм … 120
- Наибольшая длина вала, мм…500
- Частота вращения шпинделя, мин-1…1250
- Мощность электродвигателя, кВт…5,5
- Габаритные размеры (ДхШхВ), м… …3915−1670−2430
- Масса, кг…2800
- 4. Фрезерный гидрокопировальный автомат 641(класс точности Н).
- Технические характеристики:
- Размеры рабочей поверхности стола… 250?400 мм;
- Частота вращения шпинделя …800−10 000 мин-1
- Общая мощность электродвигателей …1 кВт;
- Габаритные размеры …1720×1520×1740 мм;
- Масса… 1250 кг.
- 5. Круглошлифовальный автомат 6С232 (класс точности-В)
- Технические характеристики:
- Диаметр, мм: обрабатываемой детали…20−87
- шлифуемой поверхности…17−80
- Частота вращения шлифовального круга, мин-1…3000−10 000
- Диаметр шлифовального круга, мм…100−200
- Скорость обработки, м/с…60
- Мощность электродвигателя привода шлифовального круга, кВт.3−7,5
- Наибольшая суммарная мощность электродвигателей, кВт…10
- Габаритные размеры (ДхШхВ), мм…2200−1180−2280
- Масса, кг…5100
- 2.4 Выбор и компоновка транспортных средств.
- Транспортная система — это комплект транспортных средств и загрузочных устройств, обеспечивающий межстаночное и межлинейное транспортирование объекта автоматического производства.
- В зависимости от программы выпуска, количества оборудования устанавливаемого для выполнения каждой операции, особенностей детали, технологического процесса, экономических показателей, характеризующих процесс изготовления детали, применяем структурную схему автоматической линии с последовательно работающим оборудованием. Компоновку транспортных средств смотри на листе 1. В нашем случае принимаем транспортную систему, обеспечивающую возможность работы агрегатов без синхронизации циклов обработки. В зависимости от формы, размеров детали и выполняемых операций применяем гравитационный способ перемещения детали.
- Автооператоры производящие загрузку, выгрузку деталей на станки используем стандартизованные, встроенные в металлорежущие станки.
- Гибкие лотки управления потоками деталей в гравитационных системах транспортирования.
- Материал лотков — пружинистая листовая сталь.
- Наименьший радиус изгиба лотков по внутренней стенке — 300 мм.
- Угол наклона лотков 10° - 15°
- Для уборки стружки предусматриваем скребковый транспортер удаляющий стружку из рабочей зоны станков.
- Для проектируемой автоматической линии с последовательно работающим оборудованием и с поперечным расположением технологического оборудования при сквозном прохождении конвейера необходимы механические подъёмники, которые будут осуществлять загрузку и выгрузку заготовок и деталей, а так же отводящий конвейер для перемещения деталей между позициями.
- Автоматические подъёмники прерывистого действия широко применяются в транспортных системах автоматических линий. В процессе транспортировки в подъёмниках детали могут ориентироваться для загрузки на станок в определённом направлении. Выбираем подъёмник модели КК5А:
- Технические характеристики:
- Диаметр транспортируемых валов, мм … до 80;
- Наибольшая длинна валов, мм … 150;
- Тип привода … пневматический;
- Регулирование скорости… бесступенчатое;
- Скорость движения, м/мин:
- — каретки … 10;
- — кассеты загрузки/выгрузки … 12;
- Габариты, мм …1250×900×1900;
- Масса, кг …800.
- Отводящие конвейеры обеспечивают непрерывное принудительное перемещение заготовок или деталей по фронту автоматической линии с распределением их между параллельно работающими станками и сбором обработанных деталей.
- 2.5 Выбор метода и средств контроля
- Для контроля и сортировки деталей в автоматических линиях используют жесткие калибры, а также электроконтактные, пневмоэлектроконтактные, электронные и пневмоэлектронные измерительные системы.
- Для каждого контролируемого параметра выбор той или иной измерительной системы, а следовательно, и типа преобразователя определяется требуемой точностью, пределами измерения, производительностью и числом групп сортировки.
- Жесткие калибры применяют тогда, когда не требуется высокой точности контроля. Простой в эксплуатации является электроконтактная система автоматического контроля, в состав которой входят амплитудные и электроконтактные датчики.
- Для контрольных автоматов, встраиваемых в автоматические линии, существенное влияние на их компоновку оказывают транспортная система линии, условия связей с другими агрегатами, требования удобства обслуживания, монтажа, периодических осмотров и ремонта.
- Для контроля валов выбираем автомат марки ПБ-250.
- Контролируемые параметры: — радиальное биение шеек под подшипники относительно оси вала.
- Диапазон размеров контролируемых параметров деталей, мм.0 — .250
- Предельно допустимая погрешность измерения, мкм…15
- Тип преобразователя… пневмомеханотронный
- Производительность, шт/ч…720
- Мощность электродвигателя, кВт…0,8
- Габаритные размеры, мм…500−290−330
- 2.6 Планировка автоматической линии
- Планировку автоматической линии выполняем в масштабе 1:125. В качестве исходных данных для планировки автоматической линии используем структурную схему, эскизы станков и транспортных устройств, выполненные с учетом выбранных типов и габаритов. При передаче деталей с одной рабочей позиции на другую предусматриваем промежуточные агрегаты (подъемники, накопители).
- Выполняя планировку автоматической линии учитываем минимально допустимое расстояние между механизмами, которое разработано с учетом обеспечения удобства обслуживания и соблюдения правил техники безопасности.
- Таблица 2.3 Минимально допустимые расстояния между механизмами.
- 2.7 Составление циклограммы автоматической линии.
- Циклограмма автоматической линии составляется с целью — наглядного изображения последовательности и времени работы всех механизмов АЛ. Она должна быть построена таким образом, чтобы обеспечить наиболее рациональное сочетание последовательности движений, т.к. от этого зависит производительность АЛ.
- Все движения, которые должны совершать механизмы АЛ за один цикл, можно условно разделить на лимитирующие и совмещенные. Лимитирующими называет те движения, сумма которых составляет один цикл работы, а совмещенными — движения, происходящие одновременно с лимитирующими.
- Время цикла может быть уменьшено путем сокращения длины хода и увеличения скорости перемещения механизмов. Холостым перемещения следует выбирать минимальными при соблюдении двух условий: 1. чтобы режущий инструмент в исходном положении выходил за контуры детали и не мешал ее перемещению. 2. чтобы быстрый подвод был достаточным для освобождения конечных выключателей, контролирующих исходное положение режущего инструмента.
- Изобразим циклограмму автоматической линии для вала. Все механизмы на позициях работают независимо и только подают сигналы об окончания зажима. После получения последнего сигнала дается команда на пуск станков. Каждый станок имеет автономную систему управления, которая переключает ее с быстрого подвода на рабочую подачу, а затем и на быстрый отвод. Как только будет сигнал об окончании обработки, включаются механизмы разжима и фиксации, которые освобождают обрабатываемые детали. С обработкой синхронизируется и работа остальных механизмов (механизмы для удаления стружки и др.)
- Для разработки циклограммы составим расчетный лист настройки АЛ при обработке изделия.
- 1. Транспортирования изделия транспортером участка.
- ?1 = 1000мм — шаг транспортера; s1 = 8м/мин — скорость транспортирования изделия.
- Время транспортирования изделия
- ?х1 = ?1/ s1 = (1000 · 60)/8000 = 7,5 с.
- 2. Зажим и фиксация. На зажим и фиксацию по паспорту автоматической линии уходит 3 с, т. е. tх2 = 3 с.
- 3. Отвод транспортера в исходное положение tх3 = 6,0 с — по аналогии с первой операцией.
- Фрезерно-центровальная операция
- 4. Быстрый подвод фрезы к изделию
- ?4 = 300 мм — длина быстрого подвода; s4 = 10,0 м/мин — скорость быстрого подвода.
- Время быстрого подвода фрезы
- tх4 = ?4/s4 = (30 · 60)/10 000 =1,5с.
- 5. Обработка фрезой
- tр5 =13,2 с.
- 6. Быстрый отвод фрезы
- ?6 = 385 мм — длина отвода; s6 = 10,0 м/мин — скорость отвода;
- х6 = ?6/ s6 = (385×60)/10 000 = 2,5 с время отвода.
- 7. Быстрый подвод сверла к изделию
- tх7 = 1,5 с — время быстрого подвода (так же, как у фрезы).
- 8. Обработка сверлом.
- tр8 =7,2 с.
- 9. Быстрый отвод сверла
- ?9 = 304 мм — длина отвода; s9 = 10 м/мин — скорость отвода;
- tх9 = ?9/ s9 = (304×60)/10 000 = 1,8 с время отвода.
- Черновое точение с одной стороны
- 10. Быстрый подвод чернового резца к изделию
- ?10 = 250 мм — длина быстрого подвода; s10 = 10,0 м/мин — скорость быстрого подвода.
- Время быстрого подвода чернового резца
- tх10 = ?10/s10 = (250 · 60)/10 000 = 1,5с.
- 11. Обработка черновым резцом
- tр11 =21,3 с.
- 12. Быстрый отвод чернового резца
- ?12 = 295 мм — длина отвода; s12 = 10 м/мин — скорость отвода;
- tх12 = ?12/ s12 = (295×60)/1000 = 1,77 с время отвода.
- Черновое точение с другой стороны
- 13. Быстрый подвод чернового резца к изделию
- ?13 = 250 мм — длина быстрого подвода; s13 = 10,0 м/мин — скорость быстрого подвода.
- Время быстрого подвода чернового резца
- tх13 = ?4/s13 = (250 · 60)/10 000 = 1,5с.
- 14. Обработка черновым резцом
- tр14=35,4 с.
- 15. Быстрый отвод чернового резца
- ?15 = 295 мм — длина отвода; s15 = 10 м/мин — скорость отвода;
- tх15 = ?15/ s15 = (295×60)/1000 = 1,5 с время отвода.
- Чистовое точение (поверхность 4)
- 16. Быстрый подвод чистового резца к изделию
- ?19 = 250 мм — длина быстрого подвода; s19 = 10,0 м/мин — скорость быстрого подвода.
- Время быстрого подвода чистового резца
- tх19 = ?19/s19 = (250 · 60)/10 000 = 1,5с.
- 17. Обработка чистовым резцом
- tр20 =45,6 с.
- 18. Быстрый отвод чистового резца
- ?21 = 330 мм — длина отвода; s21 = 10 м/мин — скорость отвода;
- tх21 = ?21/ s21 = (330×60)/1000 = 1,98 с время отвода.
- Чистовое точение (поверхность 6)
- 19. Быстрый подвод чистового резца к изделию
- ?16 = 250 мм — длина быстрого подвода; s16 = 10,0 м/мин — скорость быстрого подвода.
- Время быстрого подвода чистового резца
- tх16 = ?16/s16 = (250 · 60)/10 000 = 1,5с.
- 20. Обработка чистовым резцом
- tр17 =44,4 с.
- 21. Быстрый отвод чистового резца
- ?18 = 330 мм — длина отвода; s18 = 10 м/мин — скорость отвода;
- tх18 = ?18/ s18 = (330×60)/1000 = 1,98 с время отвода.
- Чистовое точение остальных поверхностей
- 22. Быстрый подвод чистового резца к изделию
- ?16 = 250 мм — длина быстрого подвода; s16 = 10,0 м/мин — скорость быстрого подвода.
- Время быстрого подвода чистового резца
- tх16 = ?16/s16 = (250 · 60)/10 000 = 1,5с.
- 23. Обработка чистовым резцом
- tр17 =16,8 с.
- 24. Быстрый отвод чистового резца
- ?18 = 330 мм — длина отвода; s18 = 10 м/мин — скорость отвода;
- tх18 = ?18/ s18 = (330×60)/1000 = 1,98 с время отвода.
- Обработка фаски
- 25. Быстрый подвод резца к изделию
- tх22 = 1,5 с — время быстрого подвода (так же, как у фрезы).
- 26. Обработка фасочным резцом
- tр23 =4,8 с.
- 27. Быстрый отвод фасочного резца
- ?24 = 261 мм — длина отвода; s24 = 10 м/мин — скорость отвода;
- tх24 = ?24/ s24 = (261×60)/1000 = 1,57 с время отвода.
- Фрезерование шпоночного паза
- 25. Быстрый подвод фрезы к изделию
- L25 = 300 мм — длина быстрого подвода; s25 = 10 м/мин — скорость быстрого подвода.
- Время быстрого подвода фрезы
- tх25 = l25/s25 = (30 · 60)/10 000 = 1,5с.
- 26. Обработка фрезой
- Tр26=15,6 с.
- 27 Быстрый отвод фрезы
- L27 = 385 мм — длина отвода; s27 = 10 м/мин — скорость отвода;
- Х27 = l27/ s27 = (85•60)/10 000 = 2,5 с время отвода.
- Шлифование шейки вала
- 28. Быстрый подвод шлифовального круга к изделию
- ?28 = 250 мм — длина быстрого подвода; s28 = 10,0 м/мин — скорость быстрого подвода.
- Время быстрого подвода шлифовального круга
- tх28 = ?28/s28 = (250 · 60)/10 000 = 1,5с.
- 29. Обработка шлифовальным кругом.
- tр29 =15 с.
- 30. Быстрый отвод шлифовального круга
- ?30 = 250 мм — длина отвода; s30 = 10 м/мин — скорость отвода;
- tх30 = ?30/ s30 = (250×60)/1000 = 1,5 с время отвода.
- Все эти данные заносятся в расчетный лист настройки в таблицу 2.4
- Таблица 2.4 — Расчетный лист настройки
- n,
- После составления расчетного листа можно составить циклограмму работы станков.
- Рисунок 2.1 — Циклограмма работы автоматической линии
- 2.8 Анализ циклограммы и математическое описание действий устройств
- Проанализируем циклограмму и составим уравнения алгебры логики для схемы на релейно-контактных элементах.
- В начальный момент времени при нажатии кнопки «Пуск» и при наличии сигнала разрешения цикла возникает неопределённость связанная с тем, что суммарный сигнал является коротким и не может управлять линией, в связи с этим вводим логическую переменную, а, которая будет срабатывать от данных сигналов, а сбрасываться сигналом от кнопки «стоп».
- Далее включается привод транспортёра Y10, который останавливается при подаче сигнала от датчика позиции лотка транспортёра X10.
- Y10: S=a+(Y12•X11)
- R=X10
- При поступлении заготовки на место загрузки включается привод зажима и фиксации Y11:
- Y11: S=Y9•X9
- R=X11
- Затем включаются приводы механизмов обработки, которые останавливаются при подаче сигнала окончания обработки.
- Y1: S=X10•X12 R=X1
- Y2: S=X10•X12 R=X2
- Y3: S=X10•X12 R=X3
- Y4: S=X10•X12 R=X4
- Y5: S=X10•X12 R=X5
- Y6: S=X10•X12 R=X6
- Y7: S=X10•X12 R=X7
- Y8: S=X10•X12 R=X8
- Y9: S=X10•X12 R=X9
- По окончанию обработки включается привод снятия детали Y12
- Y12: S=X1•X2•X3•X4•X5•X6•X7•X8•X9 R=X11
- Цикл повторяется заново, пока не нажата кнопка «стоп».
- 2.9 Синтез принципиальной схемы управления
- По полученным уравнениям строим логическую часть электросхемы на релейно контактных элементах.
- Рисунок 2.3 — Логическая часть электросхемы
- 3. Синтез принципиальной схемы бесконтактного логического управляющего устройства промышленной автоматики
- 3.1 Анализ заданного устройства
- Произведём автоматизациюработы фасонного отрезного автомата при помощи устройства, принцип работы которого указан ниже.
- Фасонно-отрезные автоматы используются для изготовления из прутка (или бунта) мелких деталей простой формы. Пруток 2 закрепляется во вращающемся шпинделе с помощью цангового патрона 3. Обработка ведется резцами 4 и 7, закрепленными в суппортах 1 и 5, перемещающихся только в поперечном направлении. Заданная длина детали обеспечивается выдвижением прутка до подвижного упора 6.
- Рисунок 3.1 — схема обработки заготовки на фасонно-отрезном автомате:1,5 — суппорты; 2 — заготовка (пруток); 3 — цанговый патрон; 4,7 — резцы; 6 — подвижный упор; Dr — главное движение; Ds — движение подачи.
- 3.2 Анализ устройства и определение входных и выходных параметров
- Проанализировав принцип работы устройства, отметим, что устройство легко поддаётся автоматизации.
- При включении кнопки Пуск начинается движение подвижного упора Y1+, при срабатывании которого выключается датчик исходного положения упора Х1.
- После достижения упором конечного положения, срабатывает датчик конечного положения упора Х2, который выключает движение упора.
- После выдвижения упора включается привод перемещения прутка Y2, пруток выдвигается до тех пор пока не достигает упора. Срабатывает датчик контакта заготовки и упора X3, который выключает перемещение упора.
- При срабатывании датчика контакта заготовки и упора включается привод зажима патрона Y3+, при срабатывании которого выключается датчик исходного положения патрона Х4.
- Привод зажима работает до тех пор пока не включится датчик конечного положения патрона X5.
- Далее происходит перемещение упора от заготовки Y1-, по достижению упором исходного положения срабатывает датчик исходного положения упора X1 и движение прекращается.
- Далее включается привод шпинделя Y4 и начинается движение фасонного резца к заготовке Y5+. Выключается датчик исходного положения фасонного резца X6.
- При включении датчика конечного положения фасонного резца X7 прекращается движение фасонного резца к заготовке и начинается движение фасонного резца обратно.
- При включении датчика исходного положения фасонного резца X6 останавливается отвод фасонного резца и включается обработка отрезным резцом. Выключается датчик исходного положения отрезного резца X8.
- При включении датчика конечного положения отрезного резца X9 прекращается движение отрезного резца к заготовке и начинается движение отрезного резца обратно.
- При включении датчика исходного положения отрезного резца X8 останавливается отвод отрезного резца и выключается привод шпинделя и происходит разжим патрона Y3- Включается датчик исходного положения патрона.
- Рисунок 3.2 -Схема действия устройства, расположения исполнительных элементов
- 3.3 Синтез циклограммы работы устройства
- Составим циклограмму работы, предусмотрим кнопку «Пуск» и «Стоп» (КнП и КнС соответственно).
- Рисунок 3.4 — Цикл работы устройства
- Заметим, что промежуточный сигнал, а выполняет функцию памяти для кнопки «Пуск» и сбрасывается кнопкой «Стоп».
- 3.4 Анализ циклограммы и математическое описание действия устройств
- Проанализируем циклограмму и составим уравнения алгебры логики для элементов И-НЕ.
- Y1, сначала в прямом Y1+, затем в обратном направлении Y1-, нужно убедится, что упор находится в стартовом положении для этого нужен сигнал от датчика X1, также нужно разрешение на выполнение цикла измерения РЦ от датчика Х0, который даёт информацию о наличии заготовки для проведения измерения и собственно сигнал от кнопки «Пуск». Для снятия неопределённостей введен сигнал, а и элементы памяти на основе RS-триггера И-НЕ (для управления используем инверсные сигналы SETи RESET).
- Далее вступает в действие исполнительный элемент Y2, являющийся приводом перемещения прутка. Сброс производится датчиком Х3.
- Далее вступает в действие исполнительный элемент Y3, который включает зажим патрона, сначала зажим Y3+, затем разжим Y3-. Сброс производится датчиками Х4 и Х5.
- Далее вступает в действие исполнительный элемент Y4, являющийся приводом шпинделя. Сброс производится при выключении Y6-.
- Далее вступает в действие исполнительный элемент Y5, который включает привод фасонного резца, сначала к заготовке Y5+, затем от заготовки Y5-. Сброс производится датчиками Х6 и Х7.
- Далее вступает в действие исполнительный элемент Y6, который включает привод отрезного резца, сначала к заготовке Y6+, затем от заготовки Y6-. Сброс производится датчиками Х8 и Х9.
- 3.5 Синтез принципиальной схемы управления
- По полученным уравнениям строим логическую часть электросхемы на универсальных элементах И-НЕ (рис3.5). При этом RS-триггеры базируются также на элементах И-НЕ.
- Рисунок 3.5 -Логическая часть электросхемы
- Полная принципиальная схема управления приведена в приложении.
- 3.6 Анализ проведённой работы
- В рамках проведённой работы была разработана принципиальная схема обработки заготовки на фасонно-отрезном автомате. Полученная схема полностью выполняет возложенные на неё функции. Устройство можно применять для обработки любыми фасонными резцами.
- Полученный при реализации схемы практический опыт может служить фундаментом для разработки более сложных схем и позволяет более углубленно вникнуть в процессе автоматизации устройств.
- Список использованных источников
- 1Справочник технолога-машиностроителя в 2-х томах./Под ред. А. Г. Косиловой, Р. К. Мещерякова. М.: Машиностроение 1985.
- 2Автоматические линии в машиностроении. Справочник в 3-х томах./Под ред. Волчкевича Л. И. М.: Машиностроение 1984.
- 3 Корсаков В. С. Автоматизация производственных процессов. М., Высшая школа, 1978 г.
- 4 Камышный Н. И., Автоматизация загрузки станков, М., Машиностроение, 1977 г.
- деталь заготовка автоматическая линия
Наименование перехода | Номера поверхностей | |||||||||
1 Фрезерование | ||||||||||
2 Точение (черновое) | ||||||||||
2 Точение (чистовое) | ||||||||||
4 Шлифование | ||||||||||
Операции | Операционный эскиз | Припуск мм | Длина раб. хода, мм | n, мин-1 | S, | t, мм | tP, мин | |
Фрезерва-ние торцов | 2,5 | 0,3 | 2,5 | 0,1 | ||||
Центрование торцов | 2,5 | 0,1 | 2,5 | 0,12 | ||||
вала | 0,5 | |||||||
0,5 | 0,5 | 0,5 | 0,07 | |||||
Снятие фаски | 0,1 | 2,5 | 0,05 | 0,03 | 0,08 | |||
Фрезерование шпоночного паза | 2,5 | 0,2 | 2,5 | 0,3 | ||||
Шлифование наружной цилиндрической поверхности | 0,05 | 0,075 | 0,05 | 0,238 | ||||
Операции | ТО, мин | |
Зацентровка торцов | 0,12 | |
I позиция — 0,34 | ||
№ 6 | 0,26 | |
II позиция — 0,945 | ||
№ 6 | 0,74 | |
III позиция — 1,78 | ||
Точение фасок | 0,08 | |
IV позиция — 0,08 | ||
паза | 0.26 | |
V позиция — 0,26 | ||
Шлифование | 0,25 | |
VI позиция — 0,25 | ||
q | Tomax, мин | Qал, шт/смену | ||||
nу=1 | nу=2 | nу=3 | nу=4 | |||
1,78 | ; | |||||
1,02 | ||||||
0,945 | ||||||
0,675 | ||||||
Степень подвижности оборудования | Доступ не нужен | Доступ нужен | |||
Проход имеется | Проход отсутствует | Для регулирования | Для постоянной работы | ||
Оба механизма неподвижны | —; | —; | А? 700 мм | А1?1100 мм | |
Один или оба механизма подвижны | Б? 600 мм | Б1? 250 мм | Б2? 800 мм | Б3? 1200 мм | |
Операция | ?, мм | s, мм/мин | мин-1 | tрi, c | tхi, с | Время, с | ||
от | до | |||||||
Транспортирование изделия | ; | ; | 7,5 | 7,5 | ||||
Зажим и фиксация | ; | ; | ; | ; | 7,5 | 10,5 | ||
Отвод транспортера назад | ; | ; | 7,5 | 10,5 | ||||
Быстрый подвод фрезы | ; | ; | 1,5 | 10,5 | ||||
Обработка фрезой | 13,2 | ; | 25,2 | |||||
Быстрый отвод фрезы | ; | ; | 2,5 | 25,2 | 27,7 | |||
Быстрый подвод сверла | ; | ; | 1,5 | 10,5 | ||||
Обработка сверлом | 7,2 | ; | 19,2 | |||||
Быстрый отвод сверла | ; | ; | 1,8 | 19,2 | ||||
Быстрый подвод черн. резца | ; | ; | 1,5 | 10,5 | ||||
Обработка черн. резцом с 1 стороны | 21,3 | ; | 33,3 | |||||
Быстрый отвод черн. резца | ; | ; | 1,77 | 33,3 | 35,07 | |||
Быстрый подвод черн. резца | ; | ; | 1,5 | 10,5 | ||||
Обработка черн. резцом с 2 стороны | 35,4 | ; | 47,4 | |||||
Быстрый отвод черн. резца | ; | ; | 1,5 | 47,4 | 48,9 | |||
Быстрый подвод чист. резца | ; | ; | 1,5 | 10,5 | ||||
Обработка чист. резцом поверхность 4 | 45,6 | ; | 57,6 | |||||
Быстрый отвод чист. резца | ; | ; | 1,98 | 57,6 | 59,58 | |||
Быстрый подвод чист. резца | ; | ; | 1,5 | 10,5 | ||||
Обработка чист. резцом поверхность 6 | 44,4 | ; | 56,4 | |||||
Быстрый отвод чист. резца | ; | ; | 1,98 | 56,4 | 58,38 | |||
Быстрый подвод чист. резца | ; | ; | 1,5 | 10,5 | ||||
Обработка чист. резцом остальные поверхности | 16,8 | ; | 28,8 | |||||
Быстрый отвод чист. резца | ; | ; | 1,98 | 28,8 | 30,78 | |||
Быстрый подвод фасочного резца | ; | ; | 1,5 | 10,5 | ||||
Обработка фасочн. резцом | 4,8 | ; | 16,8 | |||||
Быстрый отвод фасочного резца | ; | ; | 1,57 | 16,8 | 18,37 | |||
Быстрый подвод фрезы | ; | ; | 1,5 | 10,5 | ||||
Фрезерование шпоночного паза | 15,6 | ; | 27,6 | |||||
Быстрый отвод фрезы | ; | ; | 2,5 | 27,6 | 30,1 | |||
Быстрый подвод шлиф. круга | ; | ; | 1,5 | 10,5 | ||||
Обработка шлиф. кругом | 1,5 | ; | ||||||
Быстрый отвод шлиф. круга | ; | ; | 1,5 | 28,5 | ||||
Разжим и снятие | ; | ; | ; | ; | 59,58 | 62,58 | ||