Схемы реакций, метод синтеза
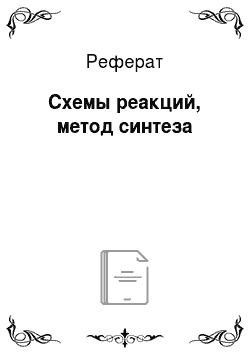
Плотность ПЭ 960 кг/м3, добавка на стадии полимеризации 2% бутена-1 в смеси с этиленом уменьшает плотность продукта до 941 кг/м*. добавка 8% бутена-1 позволяет получать продукт с плотностью 930 кг/м. Показатель текучести расплава ПЭ составляет 1−10 г/10 мин (при нагрузке 21,2 Н). Выход с 1 г твердого катализатора меняется от 5 до 10 кг за время контакта 2—4 ч, что соответствует зольности 0,02—U… Читать ещё >
Схемы реакций, метод синтеза (реферат, курсовая, диплом, контрольная)
Полимеризация этилена на окиснохромовых катализаторах может протекать как в среде углеводородного инертного растворителя, так и в газовой фазе: в зависимости от температуры процесс может осуществляться в суспензии (при температуре ниже температуры растворения ПЭ в используемом растворителе) или в растворе (при температуре выше 120°С). Для суспензионного процесса применяется более легко-кипящий растворитель.
Применение растворителя способствует лучшему осуществлению теплосъема, более равномерному распределению катализатора в реакционном объеме и защищает катализатор от ядов полимеризации. Ядами полимеризации являются ацетилен, кислород, вода, окись и двуокись углерода, сернистые соединения. Для удаления ацетилена из этилена применяют как метод селективного гидрирования, так и извлечение органическими соединениями при низких температурах; сернистые соединения и углекислый газ удаляют щелочной очисткой, метан, окись углерода — тонкой ректификацией, кислород— пропусканием этилена через слой горячей металлической меди, а воду—адсорбционными методами (осушкой на активированной окиси алюминия, силикагеле или цеолитах).
Хотя в настоящее время созданы суспензионные процессы получения ПЭ без стадии выделения катализатора, часть заводов работает по старой схеме (рис. 1.27).
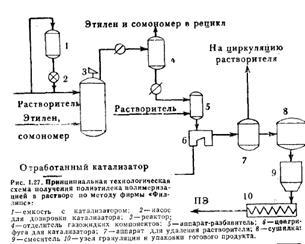
Разбавленная суспензия катализатора в углеводородном растворителе дозируется в реактор с помощью насоса, включенного в катализаторный контур, или очень концентрированная суспензия подается в реактор с помощью специального дозирующего приспособления. Растворитель (парафины, циклопарафины или их смесь) вводится в реактор вместе с этиленом и (если требуется) с другим сомономером. Реактор представляет собой автоклав с мешалкой, в котором обеспечены хорошее перемешивание и быстрый отвод тепла. Возможны различные типы реакторов и регулирующих систем. Время пребывания реакционной смеси в реакторе (до 4 ч) регулируется подачей растворителя, концентрация полимера в реакторе — подачей катализатора. Посредством регулирования скорости потока этилена, поступающего в реактор, поддерживается необходимая концентрация мономера в растворителе. Давление в реакторе (3—3,4 МПа) определяет максимальную концентрацию этилена в реакторе; температура в реакторе 125—160°С. Расход катализатора зависит от времени контакта, давления и степени чистоты используемого сырья. Нормальный расход катализатора 0,5—1 кг на 1 т ПЭ.
Раствор полимера, растворенный этилен (и сомоно-мер) и суспендированный катализатор непрерывно через теплообменник выводятся из реактора. Этилен испаряется при снижении давления и вновь возвращается в цикл. Раствор полимеризата освобождается от катализатора центрифугированием или фильтрованием. Свободный от катализатора раствор полимера подвергается обработке водяным паром. Порошок ПЭ далее сушат и гранулируют. Во время экструзии гранулята вводят стабилиза: торы, красители и другие необходимые добавки.
Работы по усовершенствованию методов очистки сырья и подготовки катализаторов позволили осуществить процесс получения ПЭ на окиснохромовых катализаторах без стадии выделения катализатора. Например, Далиным и другими создана простая технология растворной полимеризации этилена, отличающаяся высокими технико-экономическими показателями. В этом процессе достигнут выход ПЭ 150 кг/г Сг, а концентрация полимера в реакционной массе на выходе из иоли-меризационного блока составляет 25—30%, это примерно равно концентрации ПЭ в суспензионных процессах. Технологическая схема этого процесса представлена на рис. 1.28.
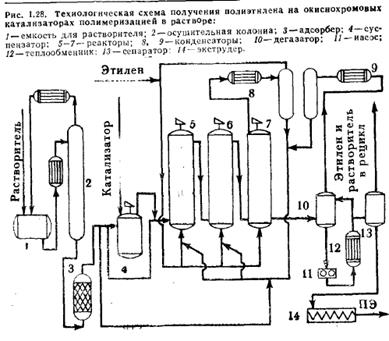
Полимеризация проводится в трех последовательно соединенных реакторах 5, б и 7, в первый из которых подается весь катализатор из емкости-суспеизатора 4, поэтому в нем реакция протекает наиболее интенсивно и образуется около 60% всего ПЭ. Скорость реакции во втором реакторе падает в соответствии с кривой зависимости скорости от времени контакта. Во втором реакторе образуется 30% общего количества полимера, а в третьем реакторе —всего 10% полимера, т. е., с одной стороны, концентрация ПЭ от реактора к реактору увеличивается, условия теплосъема как бы ухудшаются, но, с другой стороны, уменьшается количество снимаемой теплоты, которая используется для испарения на рециркуляцию растворителя в третьем реакторе. Отвод теплоты реакции осуществляется путем подачи в реакторный блок смеси этилен — растворитель с температурой ниже температуры реакции полимеризации.
Раствор полимера подвергается дегазации в дегазаторе 10, где концентрация раствора увеличивается до 40—45% (масс.) при постоянной температуре за счет циркуляции раствора по циклу дегазатор — насос — подогреватель— дегазатор. Далее освобожденный от этилена раствор полимера нагревается до 180—200 °С и поступает в сепаратор 13, где его концентрация доводится до 70—75% (масс). Здесь же происходит усреднение продукта. Окончательное удаление летучих и грануляция ПЭ с введением стабилизатора и других добавок осуществляются в двухчервячной машине «СН».
По этой схеме выпускаются продукты с показателем текучести расплава от 0,2 до 12 г/10 мин (при нагрузке 49 Н). Полидисперсность ПЭ регулируется температурой полимеризации и концентрацией полимера в реакционной массе. При синтезе СЭБ по данной технологии в реактор вводится сомономер, либо полимеризация этилена осуществляется на бифункциональном хромоникелевом катализаторе.
Существенное упрощение технологической схемы производства ПЭНД на окисиохромовых катализаторах было достигнуто фирмой «Филлипс» при переходе к суспензионному процессу с применением петлевого реактора, где теплосъем осуществляется за счет циркуляции воды в рубашке реактора. Схема процесса представлена на рис.
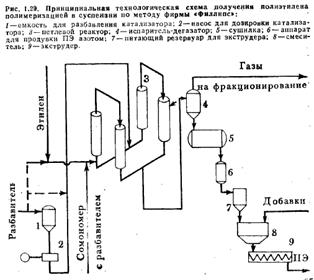
Очень высокие требования в этом процессе предъявляются к чистоте сырья: допускается суммарное содержание примесей не более 1.0 млн. Так как основным средством регулирования молекулярной массы является температура полимеризации, то очень важно, чтобы растворяющая способность (в отношении ПЭ) используемого растворителя была минимальной. Этим требованиям удовлетворяют низкомолекулярные парафины и циклопарафины (в частности, изобутан). Применение низкокипящего растворителя упрощает также технологическую схему производства.
Реактор работает при давлении 2—3 МПа и температуре 65—110 °С. Турбоциркуляционное перемешивающее устройство позволяет равномерно распределять катализатор в трубчатом реакторе, выравнивать температуру по всему реактору и отводить тепло к стенкам реактора.
Из полимеризатора полимер, растворитель и непрореагировавший мономер выводятся в испаритель-дегазатор 4, работающий при нормальном давлении. Здесь удаляется мономер и испаряется почти весь растворитель. После холодильника конденсат растворителя попадает в циркуляционный контур и снова в реактор.
Полимер образуется в виде частиц размером порядка 800 мкм и имеет насыпную плотность около 400 кг/м3.
Он упаковывается в виде порошка после сушки или поступает на грануляцию.
Плотность ПЭ 960 кг/м3, добавка на стадии полимеризации 2% бутена-1 в смеси с этиленом уменьшает плотность продукта до 941 кг/м*. добавка 8% бутена-1 позволяет получать продукт с плотностью 930 кг/м. Показатель текучести расплава ПЭ составляет 1−10 г/10 мин (при нагрузке 21,2 Н). Выход с 1 г твердого катализатора меняется от 5 до 10 кг за время контакта 2—4 ч, что соответствует зольности 0,02—U, 0l ftнастоящее время полимеризацией в суспензии по методу фирмы «Филлипс» выпускается 1750 тыс. т/год ПЭ и только 250 тыс. т/год ПЭ производится полимеризацией в растворе.