Расчет рассеивания примесей в атмосферном воздухе
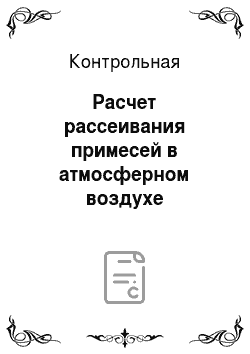
В мире используют различные схемы очистки доменного газа. Так, например, в США, система очистки доменного газа обычно включает циклон, скруббер и мокрые электрофильтры или двухступенчатый скруббер. Использование мокрых электрофильтров обеспечивает безопасность работы при очистке взрывоопасных газов, но их использование сопряжено с рядом трудностей и одновременно увеличивает эксплуатационные… Читать ещё >
Расчет рассеивания примесей в атмосферном воздухе (реферат, курсовая, диплом, контрольная)
Расчетная часть
выброс чугун приземный атмосфера
Задание 1
Определить максимальное значение приземной концентрации вредных веществ при выбросе нагретой газовоздушной смеси из одиночного источника с круглым устьем при неблагоприятных метеорологических условиях на расстоянии ХМ от источника выброса. Построить диаграмму рассеивания. Исходные данные:
— высота трубы Н = 19 м
— диаметр устья D = 0,8 м
— средняя скорость выхода газовоздушной смеси W0 = 13 м/с
— температура газовоздушной смеси ТГ = 30°С
— температура атмосферного воздуха ТВ = 27,3°С
— вредное вещество — H2SO4;
— ПДК = 0,3 мг/м3;
— мощность выброса в атмосферу вредного вещества М = 1 г/с;
— скорость ветра U (м/с): В — 6; СВ — 5; С — 4; СЗ — 5; ЮЗ — 4; Ю — 2;
ЮВ — 4; З — 3.
Расчет Определяем коэффициент А, зависящий от температуры стратификации, определяющий условия рассеивания вредных веществ в атмосферном воздухе. Из справочных данных: А = 200.
Определяем разность температур газовоздушной смеси и атмосферного воздуха T по формуле (1)
Определяем объем выбрасываемой газовоздушной смеси по формуле (2):
Определяем дополнительный параметр по формуле (3):
==138,71
Безразмерный коэффициент F, учитывающий скорость оседания вредных веществ в атмосферном воздухе, учитывая заданное условием вредное вещество, принимаем:
Определяем коэффициент, учитывающий условия выхода газовоздушной смеси из устья источника выброса по формуле (4):
Определяем дополнительный параметр по формуле (5):
Определяем коэффициент, учитывающий условия выхода газовоздушной смеси из устья источника выброса по условию (6):
если, то
Поскольку данные о рельефе местности в условии задачи отсутствуют, безразмерный коэффициент, учитывающий влияние рельефа местности на рассеивание примесей, принимаем:
Определяем максимальную приземную концентрацию вредных веществ по формуле (7):
Определяем значение опасной скорости ветра на уровне флюгера, при которой имеет место наибольшее значение приземной концентрации вредных веществ в атмосферном воздухе, по условию (8):
т. к., то
Определяем соотношение
Определяем поправку по условию (9). Поскольку для каждого из направлении
Определяем поправку по условию (10). Поскольку для каждого из направлений
Определяем максимальное значение приземной концентрации вредного вещества для каждого направления ветра по формуле (11):
Определяем коэффициент по формулам (12, 13) и условию (14):
Т. к., то
Определяем расстояние от источника выброса в направлении среднего ветра, на котором наблюдается величина приземной концентрации вредных веществ по формуле (15):
(15)
Определяем расстояние от источника выброса, на котором, при скорости ветра по направлениям, приземная концентрация вредных веществ достигает максимального значения, по формуле (16):
(16)
По результатам расчета строим диаграмму зависимости расстояния, на котором приземная концентрация вредных веществ достигает максимального значения от скорости ветра для каждого румба в соответствии с рисунком 1.
Рисунок 1 — Диаграмма зависимости от
По результатам расчета можно сделать вывод о том, что наибольшая степень загрязнения (протяженность участка с максимальным значением концентрации вредных веществ) отмечается в восточном направлении.
Задание 2
Рассчитать:
а) максимальную приземную концентрацию при неблагоприятных метеорологических условиях на расстоянии ХМ (м) от источника;
б) величину приземной концентрации вредных веществ в атмосфере по оси факела.
Исходные данные:
— длина аэрационных фонарей ;
— ширина аэрационных фонарей ;
— средняя скорость выхода газовоздушной смеси ;
— мощность выброса в атмосферу вредного вещества ;
— высота от уровня земли до верхней кромки фонаря ;
— расстояние по горизонтали от центра фонаря до расчетной точки ;
— скорость ветра ;
— температура газовоздушной смеси ;
— температура атмосферного воздуха ;
— вредное вещество — CS2;
— ПДК = 0,0001 мг/м3
Расчет Определяем объем выбрасываемой газовоздушной смеси по формуле (17):
(17)
Определяем дополнительный параметр по формуле (18):
(18)
Определяем коэффициент по условию (19):
Т. к., то
Определяем эффективный диаметр устья фонаря по формуле (20):
Определяем дополнительный параметр по формуле (21):
(21)
Определяем коэффициент по формуле (22):
(22)
Значения и? принимаем равными еди единице и определяем максимальную приземную концентрацию вредных веществ по формуле (7):
(7)
Определяем значение опасной скорости ветра по условию (8):
т. к., то (8)
Тогда Определяем поправку r по условию (23).
Т.к. то
Определяем максимальное значение приземной концентрации вредного вещества по формуле (11):
(11)
Определяем коэффициент d по формулам (12, 13) и условию (14):
Т. к., то
(12)
Определяем расстояние по формуле (15):
(15)
Определяем безразмерную величину по формуле (24):
(24)
Определяем наибольшую концентрацию вредной примеси по формуле (25):
(25)
Определим отношение
Определяем коэффициент по условия (26):
Т.к., то (26)
Определяем величину приземной концентрации вредных веществ в атмосфере по оси факела по формуле (27):
(27)
Задание 3
Определить массовые и валовые выбросы древесины в атмосферу при механической обработке древесины на участке деревообработки.
Исходные данные:
На деревообрабатывающем участке расположены станки, подключенные к системе аспирации (первый источник загрязнения атмосферы — ИЗА-1), данные о которых приведены в таблице 1.
Таблица 1 — Станки, подключенные к системе аспирации
Номер источника выделения | Наименование станка | Время работы, мин. | Время работы Т, ч/год | |
ИВ-1 | Станок для раскроя плит с программным управлением ЦТМФ | |||
ИВ-2 | Станок сверлильно-присадочный многошпиндельный горизонтально-вертикальный СГВП — 1А | |||
ИВ-3 | Станок полировальный однобарабанный П1 — Б | |||
ИВ-4 | Линия лакирования нитроцеллюлозными лаками МЛН — 1 | |||
ИВ-5 | Станок для промежуточного шлифования лаковой пленки Шл2В | |||
Эффективность местных отсосов равна 95%. Перед выбросом в атмосферу воздух очищается от пыли в циклоне типа УЦ со степенью очистки 99,9%. Неуловленная местными отсосами часть пыли удаляется через общеобменную вытяжную систему вентиляции — крышный вентилятор — ИЗА-2. Одновременно могут работать три станка — либо ИВ-1, -2, -3, либо ИВ-3, -4, -5.
Расчет ИЗА — 1
По справочным данным определяем удельные выделения древесной пыли от каждого станка:
ИВ-1: У = 17,225 кг/ч;
ИВ-2: У = 1,814 кг/ч;
ИВ-3: У = 0,829 кг/ч;
ИВ-4: У = 0,100 кг/ч;
ИВ-5: У = 1,000 кг/ч Определяем массовые выделения пыли от каждого источника выделения по формуле (28):
(28)
ИВ-1:
ИВ-2:
ИВ-3:
ИВ-5:
Определяем массовые выделения пыли с учетом одновременности работы станков:
ИВ-1, -2, -3: ;
ИВ-3, -4, -5:
Массовые выделения по ИЗА-1 принимаем как максимальные из двух вариантов:
Определяем массовые выбросы древесной пыли в атмосферу с учетом очистки в циклоне по формуле (29):
(29)
Определяем валовые выделения пыли от каждого ИВ по формуле (30):
(30)
ИВ-1:
ИВ-2:
ИВ-3:
ИВ-4:
ИВ-5:
Определяем валовые выделения пыли в целом по ИЗА-1 от ИВ-1−5:
Определяем валовые выбросы через ИЗА-1 по формуле (31):
(31)
Расчет ИЗА-2
Определяем массовые выделения пыли в воздух помещения с учетом одновременности работы оборудования с помощью коэффициента пересчета:
ИЗА-1:
ИЗА-2:
Коэффициент пересчета = 0,0526
Тогда Определяем массовые выбросы пыли в атмосферу с учетом оседания пыли в помещении:
Определяем валовые выделения пыли в воздух помещения от всех ИВ с помощью коэффициента пересчета:
Определяем валовые выбросы пыли в атмосферу с учетом коэффициента оседания пыли в помещении:
Результаты расчетов заносим в таблицу 2.
Таблица 2 — Результаты расчетов
Номер источника загрязнения атмосферы | г/с | г/с | т/год | т/год | |
ИЗА — 1 | 5,08 | 0,508 | 8,22 | 0,822 | |
ИЗА — 2 | 0,267 | 0,0534 | 0,432 | 0,0864 | |
Реферативная часть
Предприятия черной металлургии относятся к числу наиболее крупных народнохозяйственных объектов, в значительной степени определяющих уровень экономического развития России. Одновременно они являются одним из основных источников загрязнения окружающей среды. На их долю приходится 15−20% промышленных выбросов России в атмосферу (1,6 млн. т/год твердых дисперсных материалов; 7,3 млн. т/год газообразных веществ, в том числе оксидов азота, серы, углерода) и в водоемы (около 4 млрд. т/год).
Доменное производство оказывает существенное влияние на загрязнение окружающей среды, так как при производстве чугуна образуется большое количество газовых выбросов и отходов. Особую ценность имеет доменный газ (ДГ), учитывая это целесообразным и актуальным является его дальнейшее использование, в результате чего происходит улучшение экологической обстановки на предприятиях. Но для того чтобы дальнейшее использование доменного газа стало возможным необходимо отделить от него колошниковую пыль, которая также имеет высокую сырьевую ценность и может использоваться в производстве.
Действующие схемы очистки доменного газа мокрым способом снижают эффективность использования доменного газа в качестве вторичного энергетического ресурса, также из-за насыщения ДГ водяными парами снижается его теплота сгорания, а физическое тепло полностью теряется с водяным паром. Также является проблематичным использование газовой утилизационной бескомпрессорной турбины (ГУБТ) из-за наличия водяного пара. Таким образом, актуальным является перевод доменных печей с мокрой газоочистки на сухую.
В мире используют различные схемы очистки доменного газа. Так, например, в США, система очистки доменного газа обычно включает циклон, скруббер и мокрые электрофильтры или двухступенчатый скруббер. Использование мокрых электрофильтров обеспечивает безопасность работы при очистке взрывоопасных газов, но их использование сопряжено с рядом трудностей и одновременно увеличивает эксплуатационные расходы почти вдвое. Кроме того, с точки зрения рационального природопользования более прогрессивными являются способы сухой очистки доменного газа, потому что это снижает общее загрязнение водных и земельных ресурсов при устранении шламового хозяйства, и позволяет исключить из системы оборотного водоснабжения условно грязную воду.
Исходя из вышесказанного, следует отметить, что в мире разработан ряд аппаратов сухой очистки доменного газа, с их помощью газ очищают до остаточного содержания пыли менее 10 мг/мі при 200−300єC. При такой температуре доменный газ может быть использован непосредственно потребителями или в ГУБТ для получения электроэнергии [2,3].
Технологический процесс производства чугуна
Агрегатом для осуществления доменного процесса служит печь шахтного типа. Рабочее пространство доменной печи в горизонтальных сечениях имеет круглую форму, а в вертикальном разрезе — своеобразное очертание, называемое профилем.
Важнейшим условием осуществления доменного процесса в рабочем пространстве печи является непрерывное встречное движение и взаимодействие опускающихся шихтовых материалов, загружаемых в печь через колошник, и восходящего потока газов, образующегося в горне при горении углерода кокса в нагретом до 1000 — 1200° С воздухе (дутье), который нагнетается в верхнюю часть горна через расположенные по его окружности фурмы. К дутью может добавляться технический кислород, природный газ, водяной пар.
Кокс поступает в горн нагретым до 1400 — 1500° С. В зонах горения углерод кокса взаимодействует с кислородом дутья. Образующийся в зонах горения диоксид углерода при высокой температуре и избытке углерода неустойчив и превращается в оксид углерода. Таким образом, за пределами зон горения горновой газ состоит только из оксида углерода, азота и небольшого количества водорода, образовавшегося при разложении водяных паров или природного газа. Смесь этих газов, нагретая до 1800 — 2000° С, поднимается вверх и передает тепло материалам, постепенно опускающимся в горн вследствие выгорания кокса, образования чугуна и шлака и периодического выпуска их из доменной печи. При этом газы охлаждаются до 200 — 450° С, а оксид углерода, отнимая кислород из оксидов железа, превращается частично в диоксид углерода, содержание которого в доменном газе на выходе из печи достигает 14 — 20%.
Шихтовые материалы загружают в доменную печь при помощи засыпного аппарата отдельными порциями — подачами. Они располагаются на колошнике чередующимися слоями кокса, руды или агломерата и флюса при работе на не полностью офлюсованном агломерате. Загрузку подач производят через 5 — 8 мин. по мере освобождения пространства на колошнике в результате опускания материалов.
В процессе нагревания опускающихся материалов происходит удаление из них влаги и летучих веществ кокса и разложение карбонатов. Оксиды железа под действием восстановительных газов постепенно переходят от высших степеней окисления к низшим, а затем — в металлическое железо.
Свежевосстановленное железо заметно науглераживается еще в твердом состоянии. По мере науглераживания температура плавления его понижается. При температуре 1000 — 1100° С восстановление железа почти заканчивается и начинают восстанавливаться более трудновосстановимые элементы — кремний, марганец и фосфор. Науглероженное железо, содержащее около 4% углерода и некоторое количество кремния, марганца и фосфора, плавится при температуре 1130 — 1150° С и стекает в виде капель чугуна в горн. В нижней половине шахты начинается образование жидкого шлака из составных частей пустой породы руды и флюса. Понижению температуры плавления шлака способствуют невосстановленные оксиды железа и марганца. В стекающем вниз шлаке под действием возрастающей температуры постепенно расплавляется вся пустая порода и флюс, а после сгорания кокса и зола.
При взаимодействии жидких продуктов плавки с раскаленным коксом в заплечиках и горне происходит усиленное восстановление кремния, марганца и фосфора из их оксидов, растворенных в шлаке. Здесь же поглощенная металлом в ходе плавки сера переходит в шлак. Железо и фосфор печи полностью восстанавливаются и переходят в чугун, а степень восстановления кремния и марганца и полотна удаления из чугуна серы в большой мере зависят от температурных условий, химического состава шлака и его количества.
Жидкие чугун и шлак разделяются в горне благодаря различным удельным массам. По мере скопления их в горне чугун выпускают через чугунную летку, а шлак — через шлаковые летки (верхний шлак) и чугунную летку во время выпуска чугуна (нижний шлак).
Все перечисленные процессы протекают в доменной печи одновременно, оказывая взаимное влияние в соответствии с рисунком 2[4].
1 — защитные сегменты колошника; 2 — большой конус; 3 — приёмная воронка; 4 — малый конус; 5 — распределитель шихты; 6 — воронка большого конуса; 7 — наклонный мост; 8 — скип; 9 — воздушная фурма; 10 — чугунная лётка; 11 — шлаковая лётка.
Рисунок 2 — Доменная печь
Типы загрязнений
Основным продуктом доменной плавки является чугун, а побочными — шлак и доменный (колошниковый) газ. В среднем при сгорании 1 т сухого кокса образуется 3400 м3 доменного газа со средней теплотой сгорания 3,96 МДж/м3. Пыль и газообразные выбросы из доменных печей образуются в результате сложных физических и химических процессов в соответствии с рисунком 3.
Рисунок 3 — Продукты доменной плавки Масса пыли, вносимой доменными газами, составляет 20−100 кг/т чугуна. Средняя запыленность доменных газов равна 9−55 г/м3, а при неполадках или мелкой шихте может достигать 200 г/м3. Количество образующегося доменного газа составляет 3880 м3/т влажного кокса, или 4000 м3/т сухого кокса, или 2000;2500 м3 на 1 т чугуна. Удельные технологические выбросы с колошниковыми газами при выплавке передельного чугуна составляют, кг на 1 т чугуна:
— пыли-100;
— СО-640;
— О2 — 0,08−0,45.
Состав колошникового газа приведен в таблице 3.
Температура доменного газа на выходе из печи составляет обычно 300−3500 С.
Химический состав пыли изменяется в широких пределах. Например, при выплавке передельного чугуна и работе с повышенным давлением на колошнике печи пыль имеет состав в соответствии с таблицей 4.
Таблица 3
Компоненты | СО2 | СО | СН4 | Н2 | О2+N2 | |
Объемная доля, % 1 при работе без повышения давления и комбинированного дутья 2 при работе с повышением давления и комбинированным дутьем | 11,2 11,3 | 31,2 29,0 | 0,21 0,20 | 2,99 4,30 | 55,1 55,2 | |
Таблица 4 — Состав пыли на колошнике печи
Компонент | SiO2 | MgO | Al2O3 | CaO | S | MnO | FexOy | |
Содержание,% | 14.6 | 4.35 | 4.35 | 11.85 | 0.74 | 3.75 | 60.36 | |
Дисперсный состав пыли также зависит от многих факторов и может колебаться в широких пределах, приведен в таблице 5.
Таблица 5 — Дисперсный состав пыли
Размер частицы, мкм | 200−100 | 100−60 | 60−20 | 20−10 | Менее 10 | ||
Содержание, % | 34,5 | 12,3 | 19,0 | 7,5 | 1,7 | ||
Кроме колошникового устройства доменной печи, источником загрязнения атмосферы доменного цеха являются рудный и литейный дворы.
На рудном дворе пыль выделяется при разгрузке вагонов, перегрузке руды, подаче руды на бункерную эстакаду и т. п. Удельное выделение пыли на рудном дворе ориентировочно принимают равным 50 кг на 1 т чугуна, а на бункерной эстакаде — 20 кг на 1 т чугуна. Концентрация пыли на рудном дворе и бункерной эстакаде колеблется от 17 до 1000 мг/м3.
В доменных цехах существует две системы подачи сырых материалов на колошник доменной печи: скиповая, применявшаяся в старых печах, и конвейерная, применяемая в новых печах, значительно снижающая пылевыделение.
Наибольшее количество пыли выделяется в подбункерном помещении, где происходит выгрузка сырых материалов в вагон-весы. Концентрация пыли в воздухе подбункерных помещений достигает 500 мг/м3, в связи с чем на многих заводах кабину машиниста вагон-весов приходится герметизировать. В подбункерных помещениях, оборудованных конвейерами, аспирационной системой отсасывается около 2,5 кг пыли на каждую тонну чугуна. После очистки в атмосферу выбрасывается в среднем около 90 г пыли на 1 т чугуна.
На литейном дворе пыль и газы выделяются в основном от леток чугуна и шлака, желобов участков слива и ковшей. Удельные выходы вредных веществ на 1 т чугуна составляют: 400−700 г пыли, 0,7−1,15 кг СО, 120−170 г SO2. Максимальное количество пыли и газов выбрасывается во время выпуска чугуна и шлака. Пыль и газы удаляются частично через фонари литейного двора (около 160 г пыли на 1 т чугуна), частично с помощью аспирационных систем с очисткой пыли перед выбросом в атмосферу преимущественно в групповых циклонах.
Средняя концентрация пыли в период выпуска составляет 150−1500 мг/м3; максимальная концентрация наблюдается над главным желобом и ковшом для чугуна.
Содержание СО на рабочих местах в период выпуска чугуна составляет 125−250 мг/м3. Наибольшая концентрация наблюдается в момент выпуска чугуна и шлака у леток и поворотных желобов.
При выпуске горячего шлака из домны сера реагирует с кислородом воздуха с образованием SO2. Этот газ выделяется от шлаковых леток, желобов и шлаководов; средняя концентрация SО2 на этих участках в период выпуска шлака достигает 30 мг/м3.
Выпущенные из печи продукты плавки направляются на дальнейшую переработку: чугун — на разливку в чушки на разливочной машине, шлак — на грануляцию, доменный газ — на очистку.
В последнее время все газовые выбросы литейного двора крупных печей стремятся объединять и направлять их на очистку в электрофильтры. Общее количество отсасываемого газа у крупных печей достигает 1 млн. м3/ч. Чтобы уменьшить его, все системы отсоса газа от источников пылегазовыделений снабжают дроссельными клапанами, позволяющими по мере надобности дистанционно включать необходимое в данный момент укрытие (зонт).
Сухая очистка доменного газа
Для очистки доменного газа до концентраций пыли не выше 10 мг/мі на отечественных металлургических заводах применяют многоступенчатые комбинированные схемы.
Как правило, сначала очистку доменного газа проводят в сухих пылеуловителях диаметром 5−8 м, в которых оседают частицы пыли размером 50 мкм и более. В этих аппаратах улавливается 70−90% пыли, содержащейся в доменном газе, благодаря влиянию сил гравитации и инерционных сил, возникающих при повороте газового потока на 180є. Пыль с пылеуловителя удаляется с помощью винтового конвейера, который смачивается водой. Остаточное содержание пыли в доменном газе после грубой очистки не превышает 3−10 м/мі.
Для второй ступени очистки газа используют системы мокрой очистки. Обычно доменный газ из системы грубого сухой очистки поступает на полутонкую очистку газа, где удаляются частицы размером 20 мкм и более и газ очищается до остаточного содержания пыли на выходе 0,6−1,6 г/мі. Полутонкую очистку осуществляют в аппаратах мокрого типа — форсуночных полых скрубберах и трубах Вентури. Газы в доменных скрубберах имеют скорость 1−2 м/с, удельный расход воды, составляет 3−6 кг/мі газа. Проходя через скруббер доменный газ охлаждается с 250−300єC до 40−50єС и полностью насыщается влагой. Степень очистки газа от пыли в скруббере не превышает 60−70%.
После скруббера газ в большинстве случаев поступает в две-четыре малонапорные трубы Вентури, скорость газов в горловине которых равна 50−80 м/с при удельном расходе 0,2 кг/мі. Здесь завершается полутонкая очистка газа.
Тонкую очистку доменного газа, который содержит до 10 мг/мі пыли, осуществляют в аппаратах 1 класса. В связи с широким внедрением на заводах черной металлургии газорасширительных станций, использующих потенциальную энергию давления доменного газа для выработки электроэнергии в ГУБТ, для тонкой очистки газа обычно применяют аппараты, работающие с малой потерей давления, например мокрый электрофильтр.
Основные недостатки использования мокрой очистки доменного газа:
— снижение эффективности применения ДГ как источники ВЭР, так как теплота сгорания снижается за счет насыщения газа водяными парами;
— полная потеря физического тепла с водяными парами;
— осложнения при применении ГУБТ из-за наличия водяного пара и низкой эффективности очистки газов от пыли;
— осложнения использования ВМР в виде шламов;
— необходимость содержания водно-шламового хозяйства и отвода больших территорий под шламы.
В настоящее время перспективной является система сухой очистки доменного газа с применением рукавного фильтра с импульсной регенерацией, которая используется для очистки от пыли доменного газа, выделяющегося в процессе работы доменных печей металлургических предприятий, с помощью метода сухой фильтрации через фильтрующие элементы.
Принцип работы системы сухой очистки доменного газа основан на прохождении доменного газа через фильтрующие элементы секций рукавного фильтра, под влиянием разности давлений в межконусном пространстве доменной печи (3,0 атм) и в общезаводских коллекторе чистого доменного газа (1,2 атм).
Электрофильтры — наиболее эффективные газоочистные аппараты, потому что эксплуатационные расходы на их содержание, по сравнению с другими пылеи золоуловителями, гораздо ниже. Установка для электрической очистки газов включает в себя электрофильтр и агрегат питания. Запыленный газ поступает в электрофильтр, на электроды которого подается высокое напряжение, между электродами возникает коронный разряд, в результате чего происходит заполнение межэлектродного пространства отрицательно заряженными ионами газа, которые под действием электрического поля движутся от коронирующих электродов к осадительным. Встряхивания электродов происходит ударно-импульсным способом. Схема очистки с применением электрофильтра приведена на рисунке 4.
1 — доменная печь; 2 — сухой инерционный пылеуловитель; 3 — циклон; 4 — задвижка; 5 — дроссельная группа; 6 — коллектор чистого газа; 7 — сухой электрофильтр; 8 — подогреватель газа; 9 — ГУБТ; 10 — электрогенератор.
Рисунок 4 — Схема очистки доменного газа c сухим пылеуловителем и электрофильтром [2]
Сопоставление опыта использования газоочистительного комплекса с электрофильтром с работой тканевого фильтра показало, что:
— электрофильтр имеет полную автоматизацию всех процессов, что позволяет высвободить обслуживающий персонал, своевременно и удаленно проводить диагностику, значительно снизить энергопотребление.
— электрофильтр имеет эксплуатационную надежность выше чем у рукавного фильтра;
— тканевый фильтр при выходе из строя системы подогрева или компрессорной станции для регенерации рукавов не работоспособен;
— срок службы деталей рукавного фильтра составляет от полугода до трех лет, а их цена достигает 30% от общей стоимости всего аппарата, тогда как срок эксплуатации электродов электрофильтра — около 20 лет;
— высокая степень очистки, больше чем у рукавного фильтра;
— капитальные и эксплуатационные затраты на электрофильтр выше, чем на рукавный фильтр;
— электрофильтр имеет высокую взрывоопасность.
Наиболее эффективным способом улавливания мелкодисперсной пыли из отходящих газов и аспирационных выбросов различных технологических процессов и агрегатов является фильтрация. В ходе осуществления этого процесса газы проходят через фильтрующий материал, в качестве которого используется ткань с различными характеристиками.
Принцип работы системы сухой очистки доменного газа основан на прохождении доменного газа через фильтрующие элементы секций рукавного фильтра.
Из-за высокого давления газа применить имеющиеся схемы регенерации обратной продувкой или импульсом сжатого воздуха не представляется возможным. Поэтому для такой газоочистки нужна установка ГУБТ. В этом случае за счет комбинации с перепадами давления до и после ГУБТ есть возможность проводить регенерацию фильтра очищенным колошниковым газом.
В данной работе предлагается замена действующих мокрых схем очистки доменного газа на сухую, которая была разработана на основе зарубежного опыта на предприятии ОАО «Запорожсталь».
Аналогичная схема, которая используется на одном из Японских заводов, приведена на рисунке 5.
1 — доменная печь; 2 — пылеуловитель; 3 — дроссельная группа; 4 — отсечные клапаны; 5 — рукавный фильтр; 6 — ГУБТ; 7 — регулятор давления.
Рисунок 5 — Технологическая схема обеспыливания колошникових газов сухим методом при помощи рукавного фильтра.
В укрупненном виде тканевый фильтр представляет собой металлический корпус, внутри которого размещаются фильтрующие элементы, состоящие из тканевых рукавов, одетых на металлические проволочные каркасы.
Для регенерации фильтрующих элементов используется импульсная продувка сжатым воздухом через быстродействующие продувочные клапаны. 6].
Заключение
Первые результаты работы газоочисток подтвердили высокую экономическую и экологическую эффективность использования сухого способа очистки ДГ. Сухая очистка позволит:
— получить стабильную и эффективную работу ГУБТ для выработки электроэнергии, потому что концентрация пыли в доменном газе уменьшается до 2−3 мг/мі, что увеличивает срок службы воздухонагревателей, а также повышает производительность ГУБТ на 30% и устойчивость лопаток ГУБТ — до 1 года;[7]
— увеличить использование ВМР в связи с исключением образования шлама;
— исключить из производства использование воды для мокрых газоочисток, в связи с чем исключаются или сокращаются объемы строительства ряда объектов водного хозяйства доменной печи: шламовой перекачивающей станции газоочистки, отстойников и флокулятора шлама, насосной станции перекачки пульпы, циркуляционной насосной станции оборотного цикла газоочистки и др.;
— повысить температуру нагрева доменного дутья и использовать физическое тепло доменного газа, так как температура газа после сухой очистки составляет 100−120єС, что на 50−70єС выше, чем при использовании мокрой газоочистки; влажность газа снижается на 50−60 г/мі, что в совокупности равноценно увеличению калорийности доменного газа на 50−60 ккал/мі;
— улучшить экологическую обстановку на заводе в связи с более качественной очисткой газа от пыли и устранением шламового хозяйства.
Список использованных источников
1 Юсфин Ю. С. Промышленность и окружающая среда — М.: ИКЦ Академкнига, 2002.
2 Юдашкин М. Я. Очистка газов в металлургии. — М.: «Металлургия», 1976.
3. Набока В. И., Крутас Н. В., Волкова Л. А., Бородавко А. А. Улавливание и очистка неорганизованных выбросов доменной печи — Металл и литье Украины 2003.
4. Полтавец В. В. Доменное производство. — М., 1981/
5. Юсфин Ю. С., Товаровский И. Г., Черноусов П. И. Доменная печь — агрегат XXI века. — М.: «Сталь», 1995.
6. http://destal.net/ru — Защита воздушного бассейна от выбросов доменных печей в условиях ОАО «Запорожсталь»
7. Осипенко В. В., Осипенко В. Д., Губанов В. И. Сухая очистка доменного газа — новый этап развития предприятия черной металлургии. — Сталь. — 2010.