Разработка технологического процесса механической обработки детали «Втулка разрезная»
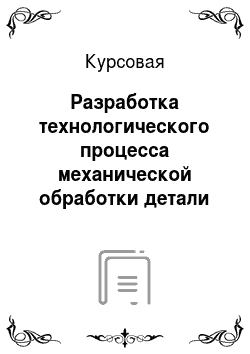
Технологический процесс в машиностроении характеризуется непрерывным совершенствованием конструкции и технологии изготовления машин. Задача машиностроения состоит в том, чтобы основной прирост продукции получать за счет увеличения производительности труда. Очень большое значение для общего технического уровня промышленных предприятий и развития технологии машиностроения является создание… Читать ещё >
Разработка технологического процесса механической обработки детали «Втулка разрезная» (реферат, курсовая, диплом, контрольная)
Разработка технологического процесса механической обработки детали «Втулка разрезная»
Задание Оглавление Введение
1. Подготовка к проектированию технологического процесса механической обработки детали
1.1 Служебное назначение и конструкция детали
1.2 Анализ технологичности конструкции детали
1.3 Определение типа и организационной формы производства
1.4 Выбор метода получения исходной заготовки
2. Проектирование технологических операций механической обработки
2.1 Выбор технологических баз и обоснование выбора технологического процесса
2.2 Выбор оборудования и технологической оснастки
2.3 Расчет и назначение припусков на механическую обработку
2.4 Расчет режимов резания
2.5 Назначение режимов резания
2.6 Техническое нормирование операций технологического процесса
3. Проектирование контрольно-измерительного приспособления
Технология машиностроения — является ведущей отраслью промышленности. В настоящее время основная задача промышленности заключается в расширении и совершенствовании индустриальной базы развития экономики, в повышении технического уровня и эффективности производства, его рентабельности, организации, мобильности, экономии производственных и трудовых ресурсов, улучшении качества продукции.
Технологический процесс в машиностроении характеризуется непрерывным совершенствованием конструкции и технологии изготовления машин. Задача машиностроения состоит в том, чтобы основной прирост продукции получать за счет увеличения производительности труда.
Эффективность производства, его технический прогресс, качество выпускаемой продукции во многом зависят от опережающего развития производства, нового оборудования, машин, станков и аппаратов, от всемирного внедрения методов технико-экономического анализа, обеспечивающие решение технических вопросов и экономическую эффективность технологических и конструкторских разработок.
Очень большое значение для общего технического уровня промышленных предприятий и развития технологии машиностроения является создание систематизированной и упорядоченной технологической документации и повышения качества выпускаемой продукции.
Основным содержанием проекта является разработка нового более прогрессивного технологического процесса механической обработки детали втулка разрезная. В проекте рассматриваются вопросы выбора заготовки, оборудования, расчет и проектирование технологической оснастки, назначения технологических баз, расчёт режимов резания и технического нормирования.
Основная задача заключается в том, чтобы при работе над данным курсовым проектом прослеживать усовершенствование технологического процесса, организации и экономии производства и также технологически незаменимых приспособлений для операций требующих этого. Наряду с этим курсовое проектирование должно научить студента пользоваться справочной литературой, ГОСТами, таблицами, нормативными документами и расценками, умело, сочетая справочные данные с теоретическими знаниями, полученными в процессе изучения курса.
деталь заготовка проектирование измерительный приспособление
1. Подготовка к проектированию технологического процесса механической обработки деталей
1.1 Служебное назначение и конструкция детали
Согласно чертежа, данная деталь — «Втулка разрезная» представляет собой тело вращения типа «фланца». Предназначена для соединения корпуса механизма с подводимым трубопроводом.
Габаритные размеры детали 68Ч116 мм. Деталь имеет два отверстия 2 40Н7 с шероховатостью Ra=0,8, в направлении главной оси детали. Имеются 3 крепёжных отверстия, с выточкой под головку болта: на торце 10 имеются 3 отверстия 4, 14, 17 17Н14, на торце 11 и на торце 19 выточки 3 и 16 28Н14, а также на торце 12 выточка 16 28Н9 с шероховатостью Ra=0,8. На поверхности 1 имеется отверстие 6 21h14, а на поверхности 8 имеется резьба 18 М20 — 7Н, они служат для фиксации втулки с подводимым трубопроводом.
Имеются лыски:
— 5 — служит для угловой ориентации детали в узле;
— 1 и 14 — выполненные от оси симметрии на расстоянии 26 мм, по h14.
Наиболее точными поверхностями являются:
— 56f7 с шероховатостью Ra=0,8, на длине 10 мм от торца детали 10;
— торец 11, так как радиальное биение торца относительно 40Н7 не должно превышать 0,03 мм;
— 28Н9 с шероховатостью Ra = 0,8 — не параллельность с осью отверстия 40Н7 не должно превышать 0,08 мм.
На детали также имеются два несквозных паза шириной 4 и 6 мм.
Втулка изготовлена из Сталь 45 по ГОСТ 1050– — 88. Данная марка стали применяется для изготовления деталей типа: вал — шестерни, коленчатые и распределительные валы, шестерни, шпиндели, бандажи, цилиндры, кулачки и другие нормализованные, улучшаемые и подвергаемые поверхностной термообработке детали, от которых требуется повышенная прочность.
Химические свойства стали Сталь 45 приведены в таблице 1, а физико-механические свойства в таблице 2.
Заменители: Сталь 50, Сталь 50Г2, Сталь 40Х.
Таблица 1.
Химический состав % ГОСТ 1050– — 88.
C | Si | Mn | Cr | Ni | S | P | |
Не более | |||||||
0,40 — 0,50 | 0,17 — 0,37 | 0,50 — 0,80 | 0,30 | 0,30 | 0,045 | 0,045 | |
Таблица 2.
Физико-механические свойства ГОСТ 1050–88.
т | в | ан, Дж/см2 | НВ, не более | ||||
МПа | % | горячее-катанной | отожжен-ной | ||||
не менее | |||||||
1.2 Анализ технологичности конструкции детали
Основные задачи, решаемые при анализе технологичности конструкции детали, сводятся к возможному уменьшению трудоемкости и металлоемкости, возможности обработки детали высокопроизводительными методами. Таким образом, улучшение технологичности конструкции детали позволяет снизить себестоимость ее изготовления без ущерба для служебного назначения.
Деталь — «Втулка разрезная», изготавливается из Стали 45 по ГОСТ 1050–88.
Форма детали вызовет не значительные трудности при получении заготовки.
Мало технологичными в данной конструкции являются:
— наружная поверхность, диаметром ш56f7. Эта поверхность должны быть выполнены в пределах указанных отклонений, а также торцевое радиальное биение не должно превышать 0,03 мм относительно внутреннего диаметра;
— отверстие, диаметром ш40H7 и Ra0.8. Эту поверхность, с заданной точностью и шероховатостью, невозможно получить на станках токарной группы, необходимо вводить в технологический процесс дополнительной операции — шлифовальной;
— отверстие диаметром ш28H9. Это отверстие должно быть выполнено в пределах допуска на размер и допуска на не параллельность с внутренним диаметром не превышающего 0,08 мм;
— пазы, шириной 4 и 6 мм отличаются большой глубиной и не имеют сквозного выхода к противоположной поверхности детали.
Вывод: деталь мало технологична.
1.3 Определение типа и организационной формы производства
Тип производства на данном этапе проектирования определяется ориентировочно в зависимости от массы детали и годовой программы выпуска, используя таблицу 4.
При массе детали 2,02 кг и годовой программе выпуска 4800 шт/год тип производства является серийным.
Скорректируем выбранный тип производства определив коэффициент серийности.
где: tв — величина такта выпуска, мин/шт.
где: Fд — действительный годовой фонд времени работы оборудования.
Fд = 4029 ч.
N — годовая программа выпуска деталей, шт.
N=4800 шт.
Тшт.ср. — среднее штучное время.
Так как коэффициент серийности Кс < 20, то производство — серийное.
Расчет количества деталей в партии
Количество деталей в партии запуска n рассчитывается по формуле:
g=(Na)/F
где N — годовая программа выпуска 4800 шт.;
а — периодичность выпуска в днях;
F — число рабочих дней, в году 254 дня.
Рекомендуемое значение а- 3;6;12;24 [6 cтр.23], принимаем а=12.
g = (4 800 227 шт.
1.4 Выбор метода получения заготовки
Разбиваем заготовку на простые фигуры и определяем объём и массу:
Таблица 3
Прокат | Штамповка | |
m3 = 6,2 кг mq = 2,02 кг | m3 = 3,4кг mq = 2,02 кг | |
По стоимости:
Для проката
где: М — затраты на материал исходной заготовки,
Q — масса заготовки, кг;
S — цена 1 кг материала заготовки, руб;
q — масса готовой детали, кг;
Sотх — цена 1 т отходов, руб.
Для штамповки
руб.,
где Ci — базовая стоимость 1 т заготовок, в рублях;
Кт, Кс, Кв, Км, Кп — коэффициенты, зависимые от класса точности, группы сложности, массы, марки материала и объёма производства;
Q — масса заготовки, кг;
q — масса готовой детали, кг;
Sотх — цена 1 т отходов, руб.
Кт = 1 — нормальной точности;
Км = 1 — Сталь 45;
Кс = 0,84 — 2-я группа сложности;
Кв = 1 — масса штамповки до 4 кг;
Кп = 1 — от объёма производства.
Схема для определения дополнительных переходов для получения заготовки Для точения:
= 1,151 мин
Для сверления:
мин Для рассверливания:
= 2,396 мин Для фрезерования лыски:
мин Для фрезерования:
мин Вывод: выбираем заготовку, обеспечивающую меньшую себестоимость — штамповка.
2. Проектирование технологического процесса механической обработки
2.1 Выбор технологических баз и обоснование варианта маршрутного технологического процесса
2.2 Выбор оборудования и технологической оснастки
При выборе оборудования принимают во внимание конструктивные особенности и размеры детали, технические требования, определяющие точность обрабатываемых заготовок, технологические возможности, производительность и эксплуатационные свойства оборудования, экономическую целесообразность его применения.
При выборе технологической оснастки следует отдавать предпочтение быстродействующим, автоматизированным многоместным приспособлениям, допускающим совмещение переходов, перекрытие основного и вспомогательного времени.
005 Токарно-револьверная
Токарно-револьверный станок модели 1П365
Мощность электродвигателя, кВт …13
На данной операции заготовка устанавливается в трёхкулачковый самоцентрирующийся патрон и базируется по боковым поверхностям и верхнему торцу.
Подрезные отогнутые резцы 2112−0084 ц=90? с пластинами из твёрдого сплава Т15К6 ГОСТ 18 880–73.
Расточной резец 2141−0057 ц=90? с пластинами из твёрдого сплава Т15К6 ГОСТ 18 883–73.
Зенкер специальный диаметром 39,03 мм из быстрорежущей стали Р6М5.
Развёртка специальная диаметром 39,61 мм из быстрорежущей стали Р6М5.
Вспомогательные инструменты:
Державка ГОСТ 18 074–72;
Втулка конус Морзе ГОСТ 17 178–71.
010 Токарно-винторезная
Токарно-винторезный станок модели 16К20
Мощность электродвигателя, кВт …10
На данной операции заготовка устанавливается в трёхкулачковый самоцентрирующийся патрон и базируется по боковым поверхностям и верхнему торцу.
Подрезной отогнутый резцы 2112−0084 ц=90? с пластинами из твёрдого сплава Т15К6 ГОСТ 18 880–73.
Расточной резец 2142−0087 ц=90? с пластинами из твёрдого сплава Т15К6 ГОСТ 9795–84.
015 Горизонтально-фрезерная
Горизонтально — фрезерный станок модели 6Р83
Мощность электродвигателя, кВт …11
На данной операции заготовка устанавливается на специальное приспособление и базируется по плоскости и специальном приспособлении (палец) на отверстии 40H17, и по боковому торцу.
Фреза 3-х сторонняя 200×40 со вставными ножами Р6М5 ГОСТ 1669–78.
020 Вертикально-фрезерная
Вертикально — фрезерный станок модели 6Р13
Мощность электродвигателя, кВт …11
На данной операции заготовка устанавливается в специальном приспособлении, базируется по плоскости, отфрезерованному торцу и по наружнему диаметру 116.
Фреза концевая 1−32 32 Р6М5 по ГОСТ 50 572–93.
025 Вертикально-сверлильная
Вертикально-сверлильный станок модели 2Н135
Мощность электродвигателя, кВт …4,0
На данной операции заготовка устанавливается на специальное приспособление, сверление осуществляется по кондуктору, базируется на отверстии 40H7, и по боковому торцу.
Сверло спиральное 2301−1706 17 мм Р6М5 по ГОСТ 22 736–77.
Зенкер 2323−0542 28 мм Р6М5 по ГОСТ 12 489–71.
Развёртка 2363−3481 28 мм Р6М5 по ГОСТ 1672–80.
030 Горизонтально-фрезерная
Горизонтально — фрезерный станок модели 6Р83
Мощность электродвигателя, кВт …11
На данной операции заготовка устанавливается на специальное приспособление, базируется по плоскости, фрезерованному торцу и по верхнему торцу 116.
Фреза прорезная 2254−1072 Р6М5 по ГОСТ 2679–93.
035 Горизонтально-фрезерная
Горизонтально — фрезерный станок модели 6Р83
Мощность электродвигателя, кВт …11
На данной операции заготовка устанавливается на специальное приспособление, базируется по плоскости, фрезерованному торцу и по нижнему торцу 116.
Фреза прорезная 2254−0986 ГОСТ 2679–93.
040 Вертикально — сверлильная
Вертикально-сверлильный станок модели 2Н135
Мощность электродвигателя, кВт …4,0
На данной операции заготовка устанавливается на специальное приспособление, сверление осуществляется по кондуктору, базирование осуществляется по плоскости, отверстии 40H7, и по торцу.
Сверло спиральное 2301-3257 17,5 мм Р6М5 по ГОСТ 12 121–77.
Метчик М20 2621- 1719 Р6М5 по ГОСТ 3266–81.
Сверло спиральное 2301−3275 21 мм Р6М5 по ГОСТ 12 121–77.
045 Внутришлифовальная
Внутришлифовальный станок 3К227В
Мощность электродвигателя, кВт …4,0
На данной операции заготовка устанавливается в трёхкулачковый самоцентрирующийся патрон и базируется по плоской поверхности.
Шлифовальный круг 25А16С27К, D=32мм, H=40мм.
050 Торцекруглошлифовальная
Круглошлифовальный станок 3У131 М
Мощность электродвигателя, кВт …5,5
На данной операции заготовка устанавливается на две гидропластовые оправки и базируется в торец.
Шлифовальный круг 25А40С15К, D=350мм, H=40мм.
2.3 Расчет и назначение операционных припусков на механическую обработку
Исходная заготовка — штамповка на ГКМ. Масса исходной заготовки 3,4 кг.
Расчёт припусков на механическую обработку будем вести для отверстия Ш40. Технологический маршрут обработки поверхности Ш40. состоит из следующих переходов:
1. Зенкерование (IT12, Rz40)
2. Развёртывание (IT9, Rz20)
3. Термообработка — закалка ТВЧ
4. Шлифование (IT7, Rz5)
Таблица 4
Технологический переход | Элементы припуска, мкм | 2Zmin мкм | Расчётн. миним. размер dmax, мм | Допуск на изгот. Тd, мкм | Предельные размеры на переход, мм | Предельный припуски с учётом округл., мм | ||||||
Rz | h | ДУ | dmax | dmin | 2Zmаx | 2Zmin | ||||||
Исходная заготовка | ; | ; | 35,355 | 35,35 | 33,15 | ; | ; | |||||
Зенкерова-ние | 93,6 | 2· 1965 | 39,285 | 39,28 | 39,03 | 5,88 | 3,93 | |||||
Развертыва-ние | 62,4 | 2· 194 | 39,673 | 39,67 | 39,61 | 0,58 | 0,39 | |||||
Термообра-ботка | ; | ; | 75,1 | ; | ; | ; | ; | ; | ; | ; | ; | |
Шлифова-ние | ; | ; | ; | 2· 176 | 40,025 | 40,025 | 40,00 | 0,39 | 0,35 | |||
ИТОГО | 6,85 | 4,67 | ||||||||||
Для поковки имеем пространственные отклонения, возникающие при штамповке, будут равны:
ДУиз=
где — величина смещения штампов пресса
— величина эксцентриситета прошиваемого отверстия по отношению к наружному диаметру.
Определение промежуточных значений припусков на механическую обработку:
Дзенкер. = ДУиз · ky = 1560 · 0,06 = 93,6 мкм
Kу = 0,06 — коэффициент уточнения формы Дразвёрт. = Диз · ky = 1560 · 0,04 = 62,4 мкм
Kу = 0,04 — коэффициент уточнения формы ДТО= мкм Погрешность установки, возникающая при выполнении операций принимаем равной: .
На основании записанных в таблице данных проводим расчёт минимальных значений межоперационных припусков, по формуле:
Минимальный припуск :
под зенкерование
под развёртывание
под шлифование
Схема графического расположения припусков и допусков на обработку поверхности Ш40 Н7.
Расчет припусков на механическую обработку будем вести для линейного размера 68. Данный размер получается вследствие последовательной подрезки двух торцов на первой и второй токарно-револьверной операции.
Таблица 5
Технологический переход | Элементы припуска, мкм | Zmin мкм | Расчётн. миним. размер lmin, мм | Допуск на изгот. Тl, мкм | Предельные размеры на переход, мм | Предельный припуски с учётом округл., мм | ||||||
Rz | h | ДУ | lmax | lmin | Zmаx | Zmin | ||||||
Исходная заготовка | ; | ; | 70,863 | 75,28 | 73,08 | ; | ; | |||||
Точение черновое торца 1 | 50,4 | 69,615 | 71,83 | 71,09 | 4,19 | 1,25 | ||||||
Точение чистовое торца 1 | 33,6 | 69,464 | 70,94 | 70,20 | 1,63 | 0,15 | ||||||
Таблица 6
Технологический переход | Элементы припуска, мкм | Zmin мкм | Расчётн. миним. размер lmin, мм | Допуск на изгот. Тl, мкм | Предельные размеры на переход, мм | Предельный припуски с учётом округл., мм | ||||||
Rz | h | ДУ | lmax | lmin | Zmаx | Zmin | ||||||
Исходная заготовка | ; | ; | 69,464 | 70,94 | 70,20 | ; | ; | |||||
Точение черновое торца 2 | 67,26 | 68,00 | 67,26 | 3,68 | 2,20 | |||||||
ИТОГО | 9,5 | 3,60 | ||||||||||
для первого торца:
где:
;
ДУ черн. = kу и.з = 0,06 840 = 50,4 мкм ;
ДУ чист. = kу и.з = 0,04 840 = 33,6 мкм.
для второго торца:
где:
;
ДУ черн. = kу и.з = 0,06 1800 = 108 мкм.
Обработка первого торца ведется в самоцентрирующем патроне с упором в торец:
Обработка второго торца ведется в самоцентрирующем патроне с упором в торец:
для первого торца:
для второго торца:
Схема графического расположения припусков и допусков на обработку торца 68.
2.4 Расчет режимов резанья
Расчёт режимов резания на сверление (операция 040 вертикально-сверлильная)
Исходные данные:
Наименование операции сверление 21Н14, нарезание резьбы М20−7Н Деталь … втулка разрезная Обрабатываемый материал … Сталь 45
Характер заготовки… горячая штамповка Вес заготовки …3,4 кг Станок… вертикально-сверлильный 2Н135
Инструмент .сверло спиральное 2301−3257 17,5 мм по ГОСТ 12 121–77
сверло спиральное 2301−3275 21 мм по ГОСТ 12 121–77
метчик М20 2621- 2875 ГОСТ 3266–81
Материал сверла и метчика… Р6М5
1 переход: сверление
1. Скорость резания:
Cv = 9,8
q = 0,4
у = 0,5
m = 0,2
Охлаждение есть.
S = 0,35 мм/об;
T = 45 мин.
Kv = KмvKuvKlv
где Кмv — коэффициент на обрабатываемый материал,
Kмv = ;
Кuv — коэффициент на инструментальный материал (Р6М5),
Кuv = 1;
Klv — коэффициент, учитывающий глубину сверления, Кlv = 1,0 (l < 3D)
КV = 1,2•1•1 = 1,2;
Принимаем: n = 500 об/мин.
2. Крутящий момент и осевая сила:
См = 0,0345
Ср = 68
qm = 2,0
qp = 1,0
уm = 0,8
уp = 0,7
3. Мощность резания:
Мощность станка:
где — КНД станка Определим требуемую мощность резания, учитывая, что должно выполняться условие Nрез < Nст.
3,8 > 2,0 условие выполняется
4. Рассчитаем основное время:
Для сверления основное время зависит от пройденного пути, подачи инструмента на оборот, скорости резания (оборотов инструмента) и определяется по формуле:
То =К L/(n S)
где: К-количество обрабатываемых отверстий То = 60/(5000,35)= 0,35 мин.
2 переход: рассверливание
1. Скорость резания:
Cv = 16,2
q = 0,4
x = 0,2
у = 0,5
m = 0,2
Охлаждение есть.
S = 0,4 мм/об;
T = 50 мин.
t = 0,5 (D — d) = 0,5 (21 — 17,5) = 1,75 мм
Kv = KмvKuvKlv
где Кмv — коэффициент на обрабатываемый материал,
Kмv = ;
Кuv — коэффициент на инструментальный материал (Р6М5),
Кuv = 1;
Klv — коэффициент, учитывающий глубину сверления,
Кlv = 1 (l < 3D)
КV = 1,2•1•1 = 1,2;
Принимаем: n = 700 об/мин.
2. Крутящий момент и осевая сила:
См = 0,09
Ср = 67
qm = 1,0
уm = 0,8
уp = 0,65
x = 0,9
3. Мощность резания:
Мощность станка:
где — КНД станка Определим требуемую мощность резания, учитывая, что должно выполняться условие Nрез < Nст.
3,8 > 0,92 условие выполняется
4. Рассчитаем основное время:
Для сверления основное время зависит от пройденного пути, подачи инструмента на оборот, скорости резания (оборотов инструмента) и определяется по формуле:
То =К L/(n S)
где: К-количество обрабатываемых отверстий То = 30/(7000,4)= 0,1 мин.
3 переход: резьбонарезание
1. Скорость резания:
Cv = 64,8
у = 0,5
q = 1,2
m = 0,9
S = 2,5 мм/об;
T = 90 мин.
Kv = KмvKuvKlv
где Кмv — коэффициент на обрабатываемый материал (Р6М5),
Kмv = ;
Кuv — коэффициент на инструментальный материал, Кuv = 1;
Klv — коэффициент, учитывающий глубину сверления, Кlv = 1 (l < 3D)
КV = 1,2•1•1 = 1,2;
Принимаем: n = 500 об/мин.
2. Крутящий момент:
См = 0,027
q = 1,4
у = 1,5
3. Мощность резания:
Мощность станка:
где — КНД станка Определим требуемую мощность резания, учитывая, что должно выполняться условие Nрез < Nст.
3,8 > 3,6 условие выполняется
4. Рассчитаем основное время:
Для сверления основное время зависит от пройденного пути, подачи инструмента на оборот, скорости резания (оборотов инструмента) и определяется по формуле:
То =К L/(n S)
где: К-количество обрабатываемых отверстий То = 30/(5002,5)= 0,025 мин.
Основное (технологическое) время на операцию:
То = 0,35+0,1+0,025? 0,48мин
Расчёт режимов резания для точения (операция 010 токарно-винторезная)
Исходные данные:
Наименование операции … наружное точение 116 h14, 68 h14
Деталь … втулка разрезная Обрабатываемый материал … Сталь 45
Характер заготовки … горячая штамповка Вес заготовки …3,4 кг Станок… токарно-винторезный 16К20
Инструмент … резец Т15К6 2142−0087 ГОСТ 9795–84
резец Т15К6 2112−0084 ГОСТ 18 880–73
1 переход: наружное точение 116 h14
1. Скорость резания:
Cv = 340
x = 0,15
у = 0,45
m = 0,2
Охлаждения нет
S = 1 мм/об;
T = 60 мин.
t = 1,8 мм
Kv = KмvKuvKlv
где Кмv — коэффициент на обрабатываемый материал,
Kмv = ;
Кпv — коэффициент состояния поверхности, Кпv = 0,8;
Kиv — коэффициент материала инструмента (Т15К6),
Киv = 1
Kv = 1,23•0,8•1 = 0,98;
Принимаем: n = 400 об/мин.
2. Сила резания:
Ср = 300
x = 1,0
y = 0,75
n = -0,15
где:
при = 90
kp(P) = 0,89
при = 10
kp(P) = 1, 0
при = 0
krp(P) = 1,0
Н
3. Мощность резания:
Мощность станка:
где — КНД станка Определим требуемую мощность резания, учитывая, что должно выполняться условие Nрез < Nст.
8,5 > 4,6 условие выполняется
4. Рассчитаем основное время:
Для сверления основное время зависит от пройденного пути, подачи инструмента на оборот, скорости резания (оборотов инструмента) и определяется по формуле:
То = L/(n S)
То = 78/(4001,0)= 0,2 мин.
2 переход: наружное точение торца 68
1. Скорость резания:
Cv = 340
x = 0,15
у = 0,45
m = 0,2
Охлаждения нет
S = 1 мм/об;
T = 60 мин.
t = 1,8 мм
Kv = KмvKuvKlv
где Кмv — коэффициент на обрабатываемый материал,
Kмv = ;
Кпv — коэффициент состояния поверхности, Кпv = 0,8;
Kиv — коэффициент материала инструмента (Т15К6),
Киv = 1
Kv = 1,23•0,8•1 = 0,98;
Принимаем: n = 400 об/мин.
2. Сила резания:
Ср = 300
x = 1,0
y = 0,75
n = -0,15
где:
при = 90
kp(P) = 0,89
при = 10
kp(P) = 1, 0
при = 0
krp(P) = 1,0
Н
3. Мощность резания:
Мощность станка:
где — КНД станка Определим требуемую мощность резания, учитывая, что должно выполняться условие Nрез < Nст.
8,5 > 4,6 условие выполняется
4. Рассчитаем основное время:
Для сверления основное время зависит от пройденного пути, подачи инструмента на оборот, скорости резания (оборотов инструмента) и определяется по формуле:
То = L/(n S)
То = 65/(4001,0)= 0,16 мин.
Основное (технологическое) время на операцию:
То = 0,2+0,16? 0,36мин
Расчёт режимов резания на шлифование (операция 050 торцекруглошлифовальная)
Исходные данные:
Наименование операции… шлифование Ш56f7
Деталь … втулка разрезная Обрабатываемый материал … Сталь 45
Характер заготовки… горячая штамповка Вес заготовки …3,4 кг Станок… круглошлифовальный 3У131М Инструмент… шлифовальный круг 25А40С15К
1. Выбор характеристики шлифовального круга
Шлифовальный круг марки: 25А40С15К (D=350mm, H=40mm).
Окружная скорость круга: 35м/с.
2. Назначение скорости касательного движения подачи
Частота вращения заготовки для закалённой стали имеет вид:
, об/мин
где - диаметр заготовки, мм;
об/мин.
3. Назначение скорости радиального движения подачи, мм/мин
, мм/мин
где: 2П — снимаемый припуск на диаметр, 2П = 0,45 мм;
В — ширина шлифования, В = 10+30=40 мм;
- поправочный коэффициент в зависимости от группы обрабатываемого материала, =1,56;
- поправочный коэффициент в зависимости от диаметра шлифовального круга и скорости шлифования ;
- поправочный коэффициент в зависимости от способа осуществления радиального движения подачи и способа измерения диаметра обрабатываемой поверхности ;
- поправочный коэффициент в зависимости от жёсткости заготовки и формы обрабатываемой поверхности ;
— поправочный коэффициент в зависимости от моделей круглошлифовальных станков и срока их эксплуатации
- поправочный коэффициент в зависимости от твёрдости выбранного шлифовального круга .
мм/мин
4. Учёт ограничений по мощности резания
, кВт,
где: - поправочный коэффициент в зависимости от твёрдости круга и скорости шлифования,
- поправочный коэффициент в зависимости от группы обрабатываемого материала,
кВт
Мощность, затрачиваемая на шлифование, не должна превышать мощности привода главного движения станка.
где: — КПД станка,
кВт
5,2 > 2,1 условие выполняется
5. Проверка на отсутствие прижогов
Предельное значение мощности, затрачиваемое на шлифование, при котором прижоги отсутствуют, вычисляют по формуле:
[N*пр] = 0,039, кВт/мм
где К1 — поправочный коэффициент в зависимости от степени твёрдости шлифовального круга. К1 =0,91
[N*пр] = 0,039 кВт/мм
В дальнейшем сравнивается предельное значение мощности резания для бесприжоговой обработки с мощностью резания, приходящейся на 1 мм ширины шлифовании.
Отсутствие прижога соответствует выполнению условия
[N*пр] N / B.
N / B=2,1/40=0,05 кВт/мм
0,15 > 0,05 — условие выполняется
6. Основное время
мин.
где Кв — коэффициент, учитывающий продолжительность выхаживания (коэффициент выхаживания). Кв=1,2
мин.
2.5 Назначение режимов резания
005 Токарно-револьверная операция
Станок токарно-револьверный 1П365
1 переход — Подрезка торца черновое
Резец подрезной отогнутый с пластинкой из твердого сплава Т15К6
1. Глубина резания: t = 1,95 мм;
2. Подача: S = 0,8 1,3 мм/об. [5, стр266];
Принимаю S = 1,0 мм/об.
3. Скорость резания: V = 65 м/мин [10, стр45]
n = = 172 об/мин Принимаем n = 188 об/мин
VФ = 71 м/мин
4. Основное время То
То= мин
2 переход — Подрезка торца чистовое
Резец подрезной отогнутый с пластинкой из твердого сплава Т15К6
1. Глубина резания: t = 0,89 мм;
2. Подача: S = 0,8 1,3 мм/об. [5, стр266];
Принимаю S = 1,0 мм/об.
3. Скорость резания: V = 73 м/мин [10, стр45]
n = = 387 об/мин Принимаем n = 385 об/мин
VФ = 72,5 м/мин
4. Основное время То
То= мин
3 переход — наружное черновое обтачивание 58
Резец расточной с пластинкой из твердого сплава Т15К6
1. Глубина резания: t = 1,1 мм;
2. Подача: S = 0,8 1,3 мм/об. [5, стр266];
Принимаю S = 1,0 мм/об.
3. Скорость резания: V = 73 м/мин [10, стр45]
n = = 401 об/мин Принимаем n = 385 об/мин
VФ = 70 м/мин
4. Основное время То
То= мин
4 переход — наружное чистовое обтачивание 56
Резец расточной с пластинкой из твердого сплава Т15К6
1. Глубина резания: t = 0,8 мм;
2. Подача: S = 0,8 1,3 мм/об. [5, стр266];
Принимаю S = 1,0 мм/об.
3. Скорость резания: V = 65 м/мин [10, стр45]
n = = 367 об/мин Принимаем n = 385 об/мин
VФ = 68 м/мин
4. Основное время То
То= мин
5 переход — зенкерование 39,03
Зенкер специальный Р6М5 39,03
1. Глубина резания: t = 2 мм;
2. Подача: S = 0,9 1,2 мм/об. [10, стр81];
Принимаю S = 1,0 мм/об.
3. Скорость резания: V = 13 м/мин [10, стр123]
n = = 106 об/мин Принимаем n = 136 об/мин
VФ = 16 м/мин
4. Основное время То
То= мин
6 переход — развёртывание 39,61
Развёртка специальная Р6М5 39,61
1. Глубина резания: t = 0,3 мм;
2. Подача: S = 1,35 мм/об. [10, стр81];
3. Скорость резания: V = 8,3 м/мин [10, стр125]
n = = 66,7 об/мин Принимаем n = 66 об/мин
VФ = 8,2 м/мин
4. Основное время То
То= мин
015 Горизонтально-фрезерная операция
Станок горизонтально-фрезерный 6Р83
Фреза 3-х сторонняя 200×40 со вставными ножами Р6М5 ГОСТ 1669–78.
1. Глубина резания: t = 38 мм;
2. Подача: S = 0,06 мм/об;
3. Скорость резания: V = 50 м/мин
4. Частота: n = 250 об/мин
5. Основное время То
То= мин
020 Вертикально-фрезерная операция
Станок вертикально-фрезерный 6Р13
Фреза концевая 1−32 32 Р6М5 по ГОСТ 50 572–93
1. Глубина резания: t = 30 мм;
2. Подача: S = 0,03 мм/об;
3. Скорость резания: V = 55 м/мин
4. Частота: n = 250 об/мин
5. Основное время То
То= мин
025 Вертикально-сверлильная операция
Станок вертикально-сверлильный 2Н135
1 переход — сверление 17
Сверло спиральное Р6М5.
1. Подача: S = 0,26 0,32 мм/об. [10, стр103];
Принимаю S = 0,3 мм/об.
2. Скорость резания: V = 24 м/мин [10, стр45]
n = = 450 об/мин Принимаем n = 480 об/мин
VФ = 25 м/мин
3. Основное время То:
То= мин
2 переход — сверление 17
Сверло спиральное Р6М5.
1. Подача: S = 0,26 0,32 мм/об. [10, стр103];
Принимаю S = 0,3 мм/об.
2. Скорость резания: V = 24 м/мин [10, стр45]
n = = 450 об/мин Принимаем n = 480 об/мин
VФ = 25 м/мин
3. Основное время То:
То= мин
3 переход — зенкерование 28
Зенкер 28 Р6М5.
1. Глубина резания: t = 5,5 мм;
2. Подача: S = 0,8 1,0 мм/об. [10, стр122];
Принимаю S = 1,0 мм/об.
3. Скорость резания: V = 12,9 м/мин [10, стр123]
n = = 147 об/мин
Принимаем n = 122 об/мин
VФ = 11 м/мин
4. Основное время То:
То= мин
4 переход — зенкерование 28
Зенкер 28 Р6М5.
1. Глубина резания: t = 5,5 мм;
2. Подача: S = 0,8 1,0 мм/об. [10, стр122];
Принимаю S = 1,0 мм/об.
3. Скорость резания: V = 12,9 м/мин [10, стр123]
n = = 158 об/мин Принимаем n = 122 об/мин
VФ = 10 м/мин
4. Основное время То:
То= мин
5 переход — зенкерование 28
Зенкер 28 Р6М5.
1. Глубина резания: t = 1,2 мм;
2. Подача: S = 0,8 1,0 мм/об. [10, стр122];
Принимаю S = 1,0 мм/об.
3. Скорость резания: V = 12,9 м/мин [10, стр123]
n = = 158 об/мин Принимаем n = 122 об/мин
VФ = 10 м/мин
4. Основное время То:
То= мин
6 переход — развёртывание 28
Развёртка 28 Р6М5.
1. Глубина резания: t = 0,8 мм;
2. Подача: S = 0,8 мм/об. [10, стр125];
3. Скорость резания: V = 9,3 м/мин [10, стр127]
n = = 106 об/мин
Принимаем n = 87 об/мин
VФ = 8 м/мин
4. Основное время То:
То= мин
030 Горизонтально-фрезерная операция
Станок горизонтально-фрезерный 6Р83
Фреза прорезная Р6М5 ГОСТ 2679–93.
1. Глубина резания: t = 78 мм;
2. Подача: S = 1,0 мм/об;
3. Скорость резания: V = 37,5 м/мин
4. Частота: n = 185 об/мин
5. Основное время То
То= мин
035 Горизонтально-фрезерная операция
Станок горизонтально-фрезерный 6Р83
Фреза прорезная Р6М5 ГОСТ 2679–93.
1. Глубина резания: t = 38 мм;
2. Подача: S = 1,0 мм/об;
3. Скорость резания: V = 34,5 м/мин
4. Частота: n = 84 об/мин
5. Основное время То
То= мин
045 Внутришлифовальная операция
Шлифовать отверстие 40+0,025
Станок кругло-шлифовальный 3К227А
Шлифовальный круг 25А16С27К (D=32мм, Н=40мм).
1. Припуск: 2П = 0,4 мм;
2. Подача: Sдв.ход = 0,005 мм/об;
3. Скорость резания: V = 35 м/с;
4. Скорость вращения заготовки: Vз = 37,1 м/мин;
5. Обороты заготовки: n = 215 об/мин;
6. Скорость радиальной подачи: Vsос= 4550мм/мин
5. Основное время То
мин
Lш=(0,3…0,5)Вк+lд
2.6 Техническое нормирование операций технологического процесса
Расчёт норм времени для 005 токарно-револьверной операции.
1. Определение основного времени на точение:
[3, стр14];
2. Определение вспомогательного времени:
Вспомогательное время на токарно-револьверную операцию определяется по формуле: Тв = tуст + tпер + t изм , [3, стр15];
где: tуст — время на установку и снятие детали со станка, мин
tуст = 0,42 мин [3, стр32, карта 2];
tпер — вспомогательное время, связанное с переходом, мин для первого перехода …0,20
для второго перехода …0,20
для третьего перехода …0,13
для четвертого перехода …0,13 [3, стр86, карта 24];
для пятого перехода … 0,13
для шестого перехода …0,13
tпер = 0,92 мин
tизм — время на измерение, мин Поверхности, обрабатываемые на данной операции, контролируются при помощи штангенциркуля и калибр-пробки.
tизм = 0,19 + 0,12 + 0,12 + 0,12 + 0,11 + 0,11 = 0,75 [3, стр185, карта 86];
Вспомогательное время:
ТВ = 0,42 + 0,92 + 0,75 = 2,09 мин
3. Определение времени на обслуживание рабочего места, отдых и личные надобности:
Tобс = 5,5% Топ [3, стр92, карта 25];
Tотд = 5% Топ [3, стр203, карта 88];
4. Определение оперативного времени:
Топ = То + Тв
Топ = 1,69 + 2,09 = 3,78 мин
5. Определение норм штучного времени:
Тшт = (Т0 + ТВ) [3, стр15];
Тшт = (1,69 + 2,09) = 4,17 мин
6. Подготовительно-заключительное время:
Тпз = 30 мин [3, стр92, карта 25];
7. Определение норм штучно-калькуляционного времени
Тшк = Тшт + Тпз / n
где n — число деталей в партии, n = 4800 шт.
Подставляя числа в формулу получим:
Тшк = 4,17+30/4800 = 4,18 мин
Расчёт норм времени для 010 токарно-винторезной операции.
1. Определение основного времени на точение:
[3, стр14];
2. Определение вспомогательного времени:
Вспомогательное время на токарно-винторезную операцию определяется по формуле:
Тв = tуст + tпер + t изм , [3, стр15];
где: tуст — время на установку и снятие детали со станка, мин
tуст = 0,42 мин [3, стр32, карта 2];
tпер — вспомогательное время, связанное с переходом, мин для первого перехода …0,17
для второго перехода …0,09 [3, стр64, карта 18];
tпер = 0,28 мин
tизм — время на измерение, мин Поверхности, обрабатываемые на данной операции, контролируются при помощи штангенциркуля.
tизм = 0,19 + 0,17 = 0,36 [3, стр185, карта 86];
Вспомогательное время:
ТВ = 0,42 + 0,28 + 0,36 = 1,06 мин
3. Определение времени на обслуживание рабочего места, отдых и личные надобности:
Tобс = 3,5% Топ [3, стр70, карта 19];
Tотд = 5% Топ [3, стр203, карта 88];
4. Определение оперативного времени:
Топ = То + Тв
Топ = 0,36+ 1,06 = 1,42 мин
5. Определение норм штучного времени:
Тшт = (Т0 + ТВ) [3, стр15];
Тшт = (0,36 + 1,06) = 1,54 мин
6. Подготовительно-заключительное время:
Тпз = 14 мин [3, стр70, карта 19];
7. Определение норм штучно-калькуляционного времени
Тшк = Тшт + Тпз / n
где n — число деталей в партии, n = 4800 шт.
Подставляя числа в формулу получим:
Тшк = 1,54 + 14/4800 = 1,55 мин
Расчёт норм времени для 015 горизонтально — фрезерной операции.
1. Определение основного времени на точение:
2. Определение вспомогательного времени:
Вспомогательное время на горизонтально-фрезерную операцию определяется по формуле:
Тв = tуст + tпер + t изм , [3, стр15];
где: tуст — время на установку и снятие детали со станка, мин
tуст = 0,17 мин [3, стр54, карта 16];
tпер — вспомогательное время, связанное с переходом, мин
tпер = 1,4 мин [3, стр112, карта 33];
tизм — время на измерение, мин Поверхности, обрабатываемые на данной операции, контролируются при помощи штангенциркуля.
tизм = 0,19 + 0,16 = 0,35 [3, стр185, карта 86];
Вспомогательное время:
Тв = 0,17 + 1,4 + 0,35 = 1,92 мин
3. Определение времени на обслуживание рабочего места, отдых и личные надобности:
Tобс = 4,5% Топ [3, стр114, карта 34];
Tотд = 4% Топ [3, стр203, карта 88];
4. Определение оперативного времени:
Топ = То + Тв
Топ = 4,5+ 1,92 = 6,42 мин
5. Определение норм штучного времени:
Тшт = (Т0 + ТВ) [3, стр15];
Тшт = (4,5 + 1,92) = 6,96 мин
6. Подготовительно-заключительное время:
Тпз = 27 мин [3, стр114, карта 34];
7. Определение норм штучно-калькуляционного времени
Тшк = Тшт + Тпз / n
где n — число деталей в партии, n = 4800 шт.
Подставляя числа в формулу получим:
Тшк = 6,96 + 27/4800 = 6,97 мин
Расчёт норм времени для 020 вертикально — фрезерной операции.
1. Определение основного времени на точение:
2. Определение вспомогательного времени:
Вспомогательное время на вертикально-фрезерную операцию определяется по формуле:
Тв = tуст + tпер + t изм ,[3, стр15];
где: tуст — время на установку и снятие детали со станка, мин
tуст = 0,19 мин [3, стр54, карта 16];
tпер — вспомогательное время, связанное с переходом, мин
tпер = 0,90 мин [3, стр112, карта 33];
tизм — время на измерение, мин Поверхности, обрабатываемые на данной операции, контролируются при помощи штангенциркуля.
tизм = 0,12 + 0,13 = 0,25 [3, стр185, карта 86];
Вспомогательное время:
Тв = 0,19 + 0,90 + 0,25 = 1,34 мин
3. Определение времени на обслуживание рабочего места, отдых и личные надобности:
Tобс = 4,0% Топ [3, стр114, карта 34];
Tотд = 4,0% Топ [3, стр203, карта 88];
4. Определение оперативного времени:
Топ = То + Тв
Топ = 1,16+ 1,34 = 2,50 мин
5. Определение норм штучного времени:
Тшт = (Т0 + ТВ) [3, стр15];
Тшт = (1,16 + 1,34) = 2,70 мин
6. Подготовительно-заключительное время:
Тпз = 22 мин [3, стр114, карта 34];
7. Определение норм штучно-калькуляционного времени
Тшк = Тшт + Тпз / n
где n — число деталей в партии, n = 4800 шт.
Подставляя числа в формулу получим:
Тшк = 2,70 + 22/4800 = 2,71 мин
Расчёт норм времени для 025 вертикально — сверлильной операции.
1. Определение основного времени на точение:
2. Определение вспомогательного времени:
Вспомогательное время на вертикально-сверлильную операцию определяется по формуле:
Тв = tуст + tпер + t изм , [3, стр15];
где: tуст — время на установку и снятие детали со станка, мин
tуст = 0,30 мин [3, стр32, карта 2];
tпер — вспомогательное время, связанное с переходом, мин для первого перехода …0,10
для второго перехода …0,05
для третьего перехода …0,10
для четвёртого перехода …0,05 [3, стр95, карта 27];
для пятого перехода …0,05
для шестого перехода …0,05
tпер = 0,40 мин
tизм — время на измерение, мин Отверстия, обрабатываемые сверлением и зенкерованием, контролируются при помощи гладкой двусторонней калибр-пробкой.
tизм = 0,20 + 0,10 + 0,22 + 0,11 + 0,11+ 0,11 = 0,85 [3, стр185, карта 86];
Вспомогательное время:
Тв = 0,30 + 0,40 + 0,85 = 1,55 мин
3. Определение времени на обслуживание рабочего места, отдых и личные надобности:
Tобс = 4,0% Топ [3, стр100, карта 28];
Tотд = 4,0% Топ [3, стр203, карта 88];
4. Определение оперативного времени:
Топ = То + Тв
Топ = 2,58 + 1,55 = 4,13 мин
5. Определение норм штучного времени:
Тшт = (Т0 + ТВ) [3, стр15];
Тшт = (2,58 + 1,55) = 4,46 мин
6. Подготовительно-заключительное время:
Тпз = 15 мин [3, стр101, карта 28];
7. Определение норм штучно-калькуляционного времени
Тшк = Тшт + Тпз / n
где n — число деталей в партии, n = 4800 шт.
Подставляя числа в формулу получим:
Тшк = 4,46 + 15/4800 = 4,47 мин
Расчёт норм времени для 030 горизонтально — фрезерной операции.
1. Определение основного времени на точение:
2. Определение вспомогательного времени:
Вспомогательное время на горизонтально-фрезерную операцию определяется по формуле:
Тв = tуст + tпер + t изм , [3, стр15];
где: tуст — время на установку и снятие детали со станка, мин
tуст = 0,30 мин ;
tпер — вспомогательное время, связанное с переходом, мин
tпер = 0,90 мин;
tизм — время на измерение, мин Поверхности, обрабатываемые на данной операции, контролируются при помощи штангенциркуля.
tизм = 0,13 [3, стр185, карта 86];
Вспомогательное время:
Тв = 0,30 + 0,90 + 0,13 = 1,33 мин
3. Определение времени на обслуживание рабочего места, отдых и личные надобности:
Tобс = 4,5% Топ [3, стр114, карта 28];
Tотд = 4,0% Топ [3, стр203, карта 88];
4. Определение оперативного времени:
Топ = То + Тв
Топ = 0,43 + 1,33 = 1,76 мин
5. Определение норм штучного времени:
Тшт = (Т0 + ТВ) [3, стр15];
Тшт = (0,43+ 1,33) = 1,91 мин
6. Подготовительно-заключительное время:
Тпз = 27 мин [3, стр114, карта 34];
7. Определение норм штучно-калькуляционного времени
Тшк = Тшт + Тпз / n
где n — число деталей в партии, n = 4800 шт.
Подставляя числа в формулу получим:
Тшк = 1,91 + 27/4800 = 1,92 мин
Расчёт норм времени для 035 горизонтально — фрезерной операции.
1. Определение основного времени на точение:
2. Определение вспомогательного времени:
Вспомогательное время на горизонтально-фрезерную операцию определяется по формуле: