Расширение Пунгинской ПХГ (подземного хранилища газа)
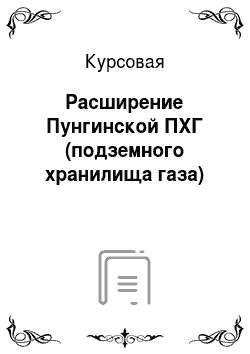
Выполненный расчет ступеней по среднему диаметру определяет требования к геометрии лопаток только в одном сечении — среднем. У корня и на периферии условия обтекания будут отличаться. Поэтому производим расчет ступени с учетом закрутки. Лопаточные аппараты профилируются так, чтобы обеспечить радиальное равновесие потока в межвенцовых зазорах. За счет безударного обтекания рабочих лопаток… Читать ещё >
Расширение Пунгинской ПХГ (подземного хранилища газа) (реферат, курсовая, диплом, контрольная)
- Реферат
- Введение
- 1. Исходные данные теплового расчета
- 1.1 Уточненный расчет тепловой схемы на номинальный режим
- 1.2 Моделирование компрессора
- 2. Газодинамический расчет турбины
- 2.1 Предварительный расчет
- 2.2 Газодинамический расчет ступеней по среднему диаметру
- 2.3 Выбор и расчет закона закрутки для каждой из ступеней
- 3. Профилирование лопаток ТВД и ТНД
- 3.1 Расчет потерь энергии, КПД и мощности турбины
- 4. Расчет на прочность диска ТВД
- 5. Спецтема: Расширение Пунгинского ПХГ (подземного хранилища газа)
- 5.1. Схема работы ПХГ
- 5.2. Расчёт количества эксплуатационных скважин для вывода ПХГ на режим циклической эксплуатации с активным объемом газа 3,5 млрд. м3 и производительностью 35 млн. м3/сут.
- Заключение
- Библиографический список
Реферат
В настоящей работе представлен проект газотурбинной установки мощностью N=10 МВт, предназначенной для привода нагнетателя природного газа на компрессорных станциях магистральных газопроводов.
Проект газотурбинной установки выполнен по регенеративному циклу, то есть с использованием тепла отходящих газов для подогрева атмосферного воздуха, поступающего в камеру сгорания после осевого компрессора.
Выполнены и представлены:
расчёт тепловой схемы ГТУ с выбором оптимальной степени
сжатия компрессора;
газодинамический расчёт турбины;
моделирование компрессора;
расчет на прочность диска ТВД;
по специальной теме: обоснование и схема расширения Пунгинского ПХГ;
мероприятия по безопасности и экологичности проекта;
графические документы.
Перспективы развития газопроводного транспорта огромны. В последние годы выпуск газотурбинных установок (ГТУ) для компрессорных станций (КС) уменьшается. На КС поступали ГТУ большой мощности и производительности, вынужденная остановка которых или длительный простой в ремонте снижает технико-экономические показатели не только КС, но и системы газопроводов в целом.
Сооружение многопоточных газопроводов большой протяженности, в том числе и экспортных, сопровождается постановкой новых задач по проектированию мобильных ГПА при сооружении газотранспортных сетей, по охране окружающей среды, а также по эффективной эксплуатации всего оборудования.
Одной из главных проблем сегодняшнего времени является охрана окружающей среды. Главным источником загрязнения атмосферы в газопроводной транспортной промышленности являются ГТУ, в том числе и установка ГТК-10−4, поставленная на серийное производство еще в 1968 году. Установка ГТК-10−4 была совершенной для своего времени, за исключением некоторых недоработок. В конце 90-х годов началась модернизация топливной системы этих установок и систем управления.
Особенности работы газотурбинного привода в наилучшей степени отвечают требованиям эксплуатации газотранспортных систем: высокая единичная мощность, небольшая относительная масса, высокий уровень автоматизации и надежности, автономность привода и работа его на перекачиваемом газе. Именно поэтому этот вид привода получил наибольшее распространение на газопроводах.
Модернизация газоперекачивающих агрегатов на компрессорных станциях магистрального газопровода с улучшением их технико-экономических показателей позволяет снизить себестоимость транспорта газа, обеспечивать безопасные условия эксплуатации основного и вспомогательного оборудования в компрессорном цехе, решать задачи по охране окружающей среды, повышать культуру производства.
Нормативные ссылки В настоящем курсовом проекте использованы ссылки на следующие стандарты:
ГОСТ 12.1 004−91 ССБТ. Пожарная безопасность. Общие требования.
ГОСТ 12.2 003−91 ССБТ. Оборудование производственное. Общие требования безопасности.
ГОСТ 12.4 011−89 ССБТ. Средства защиты работающих. Общие требования и классификация.
ГОСТ 17.1.3.13−86 Охрана природы. Гидросфера. Общие требования к охране поверхностных вод от загрязнений.
ГОСТ 380–94 Сталь углеродистая обыкновенного качества. Марки.
ГОСТ 3342–79 Соединения сварные. Методы контроля качества.
ГОСТ 6996–66 Сварные соединения. Методы определения механических свойств.
ГОСТ 14 192–96 Маркировка грузов.
ГОСТ 14 637–89 Прокат толстолистовой из углеродистой стали обыкновенного качества. Технические условия.
ГОСТ 19 903–74 Прокат листовой горячекатаный. Сортамент.
ГОСТ 19 904–90 Прокат листовой холоднокатаный. Сортамент.
ГОСТ 23 118–99 Конструкции металлические строительные. Общие технические условия.
СНиП II-23−81Стальные конструкции.
НПБ III-98 Автозаправочные станции. Требования пожарной безопасности.
ГОСТ 2.004−88 ЕСКД. Общие требования к выполнению конструкторских и технологических документов на печатающих и графических устройствах ЭВМ.
ГОСТ 2.102−68 ЕСКД. Виды и комплектность конструкторских документов.
ГОСТ 2.104−68 ЕСКД. Основные надписи.
ГОСТ 2.113−75 ЕСКД. Групповые и базовые конструкторские документы.
ГОСТ 2.124−85 ЕСКД. Порядок применения покупных изделий.
ГОСТ 2.301 — 68 ЕСКД. Форматы.
ГОСТ 2.601 — 95 ЕСКД. Эксплуатационные документы.
ГОСТ 2.602 — 95 ЕСКД. Ремонтные документы.
ГОСТ 2.120 — 73 ЕСКД. Технический проект
ГОСТ 2.301 — 68 ЕСКД. Форматы
ГОСТ 2.302 — 68 ЕСКД. Масштабы
ГОСТ 2.303 — 68 ЕСКД. Линии
ГОСТ 2.304 — 81 ЕСКД. Шрифты чертежные
ГОСТ 2.305 — 68 ЕСКД. Изображениевиды, размеры, сечения
ГОСТ 3.1201 — 85 ЕСТД. Система обозначения технической документации.
ГОСТ 3.1105 — 84 ЕСТД. Формы и правила оформления документов общего назначения.
ГОСТ 3.1127 — 93 ЕСТД. Общие правила выполнения текстовых технологических документов.
ГОСТ 3.1128 — 93 ЕСТД. Общие правила выполнения графических технологических документов.
ГОСТ 3.1201 — 85 ЕСТД. Система обозначения технологической документации.
ГОСТ 8.417−2002 ГСИ. Единицы величин.
ГОСТ 19.104−78 ЕСПД. Основные надписи.
ГОСТ 19.202−78 ЕСПД. Спецификация. Требования к содержанию и оформлению.
ГОСТ 19.404−79 ЕСПД. Пояснительная записка. Требования к содержанию и оформлению.
ГОСТ 19.502−78 ЕСТД. Описание применения. Требования к содержанию и оформлениям.
ГОСТ 7.1 — 84 Библиографическое описание документа. Общие требования и правила составления.
ГОСТ 21.101−97 СПДС. Основные требования к проектной и рабочей документации.
ГОСТ 21.110−95 СПДС. Правила выполнения спецификаций оборудования, изделий и материалов.
ГОСТ 21.205−93 СПДС. Технология производства. Основные требования к рабочим чертежам.
ОК (МК (ИСО/ИНФКО МКС) 001−96) 001−2000 Общероссийский классификатор стандартов.
ОК 005−93 Общероссийский классификатор продукции.
ОК 012−93 Общероссийский классификатор изделий и конструкторских документов.
ОК 015−94 Общероссийский классификатор единиц измерения.
1. Исходные данные теплового расчета
Таблица 1.1
Название | Обозначение | Значение | Единица измерения | |
Температура перед ТВД | Тг | К | ||
Температура среднегодовая перед компрессором | Тв | К | ||
Потери по тракту | тр | 0,1 | —; | |
Относительный расход охлаждаемого воздуха | qохл | 0,035 | —; | |
Степень регенерации | r | 0,7 | —; | |
Относительный расход топлива | qтопл | 0,015 | —; | |
На основании опыта УЗТМ и научно-исследовательских организаций по созданию ГТУ задаёмся необходимыми теплофизическими коэффициентами (табл.1.2).
Таблица 1.2. Необходимые теплофизические коэффициенты
Название | Обозначение | Значение | Единица измерения | |
КПД турбины | Т | 0,88 | —; | |
КПД компрессора | К | 0,86 | —; | |
КПД камеры сгорания | КС | 0,99 | —; | |
КПД механический | мех | 0,98 | —; | |
Теплоемкость воздуха на входе в компрессор | Cp К | 1,008 | кДж/ (кт*К) | |
Теплоемкость газовоздушной смеси в камере сгорания | Cp КС | 1,08 | кДж/ (кт*К) | |
Теплоемкость воздуха в камере сгорания | Cp В | 1,03 | кДж/ (кт*К) | |
Теплоемкость продуктов сгорания в турбине | Cp Т | 1,16 | кДж/ (кт*К) | |
В качестве расчетной величины принимаем значение, оптимальное, как по КПД, так и по эффективной мощности. Результаты расчета представлены в табл.1.3
Таблица 1.3. Данные предварительного расчета тепловой схемы
Обозначение | Значение | Обозначение | Значение | |
4,400 | 3,982 | |||
0,527 | 0,290 | |||
177,9 | 315,2 | |||
285,0 | 791,5 | |||
464,5 | 693,4 | |||
1.1 Уточненный расчет тепловой схемы на номинальный режим
Номинальное значение .
КПД турбомашины принимаем в соответствии с заданием: ,
Из предварительного расчета:
Для воздуха:
Для газа:
Подвод тепла в КС при:
составит:
;
Из уравнения баланса мощностей:
Удельная полезная работа:
Расход воздуха при 10 МВт составит
1.2 Моделирование компрессора
Осевой компрессор проектируемого ГПА при нормальных атмосферных условиях (Ро=0,1013Мпа; То=285К) должен обеспечивать следующие характеристики работы в расчетном режиме:
массовый расход воздуха;
степень повышения давления;
КПД компрессора.
Воздушный осевой компрессор должен работать в диапазоне применяемого приведенного расхода 0,8 … 1,09 от расчетного значения.
Для создания проточной части воздушного осевого компрессора в качестве модели используем проточную часть воздушного осевого компрессора газотурбинной установки ГТК-10−4, выпускаемой НЗЛ.
Моделирование осевого компрессора проектируемой установки можно провести двумя способами:
В качестве точки моделирования на характеристике осевого компрессора выбрать прежнюю расчетную точку, ввести коэффициент моделирования m и уменьшить частоту вращения ротора на этот коэффициент.
Расчетную точку на характеристике компрессора сместить по частоте вращения ротора; при этом размеры компрессора остаются прежними.
Наиболее оправданным является выбор первого варианта, так как он не приводит к снижению КПД, в то время как второй вариант ведет к снижению КПД на 1−1,5%.
Определим коэффициент моделирования
где:
G проект = 83,72 кг/с — расход воздуха через проектный компрессор;
G модель = 86,20 кг/с — расход воздуха через модельный компрессор;
ТВ проект = 288 К — температура воздуха на входе в проектный компрессор;
ТВ модель = 288 К — температура воздуха на входе в модельный компрессор;
Р1 проект = 101,3 кПа — давление воздуха на входе в проектный компрессор;
Р1 модель= 101,3 кПа — давление воздуха на входе в модельный компрессор;
Частоту вращения проектного воздушного осевого компрессора определим используя следующее соотношение:
2. Газодинамический расчет турбины
2.1 Предварительный расчет
Чтобы распределить теплоперепад между ступенями, необходимо определить степень понижения давления, расход газа, работу расширения газа в турбине, полезную работу и полезную мощность этой турбины. Часть данных известна из задания и теплового расчета. Результаты предварительного расчета сведены в табл.2.1
Давление газа перед турбиной
Данные предварительного расчета
Наименование величины | Формула | Обозн | Разм. | Величина | |
Температура газа перед турбиной | задано | Т0* | К | ||
Давление газа перед турбиной | найдено | Р0* | МПа | 0,4236 | |
Полная мощность турбины | задано | N | МВт | ||
Частота вращения ротора ТВД | задано | nТВД | об/мин | ||
Частота вращения ротора ТНД | задано | nТНД | об/мин | ||
Атмосферное давление | задано | Ра* | Па | ||
Расход газа через турбину | из расчета | кг/с | 82,83 | ||
Степень расширения | из расчета | ?Т | ; | 3,982 | |
Адиабатический теплоперепад в турбине | Hад* | кДж/кг | 358,1 | ||
Полная температура газа за турбиной | ТZ* | K | 791,5 | ||
Давление за выходным трактом | Р0*/?Т | РТ* | МПа | 0,106 | |
Удельный объем газа за турбиной | RТZ* /РТ* | ?Т | м3/кг | 2,143 | |
Скорость перед диффузором | задано | СZ | м/с | ||
Скорость в выходном патрубке | задано | СВЫХ | м/с | ||
КПД выходного диффузорного патрубка | задано | ?Д | ; | 0,5 | |
Потеря полного давления в диффузоре | ?РД | Па | |||
Полное давление за ступенью | РZ* | Па | |||
Давление за последней ступенью | РZ | МПа | 0,100 | ||
Адиабатический теплоперепад в турбине по параметрам торможения | Hад1-z | кДж/кг | 370,5 | ||
Распределим теплоперепад по турбинам, исходя из теплового расчета ГТУ, из которого известен теплоперепад на ТНД.
НТНД = 125,75 кДж/кг;
HТВД = HТ — НТНД = 315,15−125,75=189,40 кДж/кг.
Кинематические параметры, принимаемые перед газодинамическим расчётом, сводим в табл.2.2
Таблица 2.2. Кинематические параметры
Наименование | Обозначение | Разм. | ТВД | ТНД | |
Угол выхода потока из сопел | ?1 | град. | 17,40 | 22,44 | |
Степень реактивности ступени | ; | 0,350 | 0,485 | ||
Скорость выхода потока из РК | С2а | м/с | 183,6 | 171,0 | |
Для стационарных ГТУ КПД турбины возрастает при понижении выходной скорости. Величина этой скорости при заданном расходе и параметрах газа на выходе определяется торцевой площадью последней ступени, которая в свою очередь связана с прочностью рабочих лопаток.
Определим корневой диаметр ступени ТВД:
= n/30 = 542,4
= *5280/30 = 552,9 рад/с;
Определим корневой диаметр ступени ТНД:
= n/30;
= *4800/30 = 502,7 рад/с;
2.2 Газодинамический расчет ступеней по среднему диаметру
Распределив теплоперепад и задав кинематические параметры, можно произвести газодинамический расчет по среднему диаметру, результаты которого сведены в табл.2.3
Таблица 2.3. Результаты газодинамического расчета по среднему диаметру
Наименование величины | Формула | Обозн | Разм. | ступень ТВД | ступень ТHД | |
Адиабатический теплоперепад ступени | найден | hстад | кДж/кг | 189,4 | 125,8 | |
Полная температура за ступенью | Т2* | К | 919,4 | 819,7 | ||
Полное давление за ступенью | Р2* | Па | ||||
Осевая составляющая скорости за РЛ | задаемся | С2а | м/с | 183,6 | 171,0 | |
Статическая температура за РЛ | Т2 | К | 904,9 | 807,1 | ||
Статическое давление за РЛ | Р2 | Па | ||||
Удельный объем РЛ | V2 | м3/кг | 1,286 | 1,887 | ||
Ометаемая площадь на выходе из РЛ | F2а | м2 | 0,574 | 0,914 | ||
Высота РЛ | lр | м | 0,153 | 0,244 | ||
Веерность ступени | Dl | ; | 7,794 | 4,897 | ||
Окружная скорость на среднем диаметре РЛ | U2 | м/с | 329,8 | 300,0 | ||
Адиабатический теплоперепад в соплах | hсад | кДж/кг | 123,1 | 64,8 | ||
Степень реактивности на среднем диаметре | принимаем | ?cp | ; | 0,350 | 0,485 | |
Скорость газа на выходе из сопел | С1 | м/с | 486,3 | 352,7 | ||
Угол выхода потока из сопел | Принимаем | ?1 | град | 17,40 | 22,44 | |
Осевая составляющая скорости за СА | C1а | м/с | 145,4 | 134,6 | ||
Статическая температура за СА | Т1 | К | 961,1 | 865,8 | ||
Статическое давление за СА | Р1 | Па | ||||
Удельный объем за СА | V1 | м3/кг | 0,997 | 1,472 | ||
Ометаемая площадь на выходе из СА | F1а | м2 | 0,554 | 0,906 | ||
Высота сопловой лопатки | lc | м | 0,148 | 0,242 | ||
Окружная скорость на среднем диаметре СА | U1 | м/с | 328,5 | 299,6 | ||
Коэффициент расхода для СА | C1а- | ; | 0,443 | 0,449 | ||
Окружная проекция абсолютной скорости | С1u | м/с | 464,0 | 326,0 | ||
Окружная проекция относительной скорости | W1u | м/с | 135,5 | 26,4 | ||
Угол входа потока на РЛ | ?1 | град | 47,02 | 78,89 | ||
Скорость выхода потока на РЛ | W1 | м/с | 198,8 | 137,2 | ||
Скорость выхода потока из РЛ | W2 | м/с | 394,1 | 356,5 | ||
Угол выхода потока из РЛ | ?2 | град | 27,77 | 28,67 | ||
Окружная проекция относительной скорости | W2U | м/с | 348,7 | 312,8 | ||
Окружная проекция абсолютной скорости | C2U | м/с | 18,86 | 12,76 | ||
Угол выхода потока за РЛ | ?2 | град | 84,1 | 85,7 | ||
Скорость выхода потока | C2 | м/с | 184,6 | 171,5 | ||
Скорость звука в потоке за РЛ | a2 | м/с | 588,7 | 556,0 | ||
Число Маха за РЛ | MС2 | ; | 0,314 | 0,308 | ||
Скорость звука на выходе из СА | a1 | м/с | 606,8 | 575,9 | ||
Число Маха на выходе из СА | MС1 | ; | 0,801 | 0,612 | ||
Температура заторможенного потока на РЛ | T1W* | К | 978,2 | 873,9 | ||
Ширина РЛ на среднем диаметре | Bpcp | м | 0,046 | 0,073 | ||
Передний осевой зазор | S1 | м | 0,016 | 0,026 | ||
Ширина сопел на среднем диаметре | BCcp | м | 0,051 | 0,080 | ||
Задний осевой зазор | S2 | м | 0,024 | 0,038 | ||
2.3 Выбор и расчет закона закрутки для каждой из ступеней
Выполненный расчет ступеней по среднему диаметру определяет требования к геометрии лопаток только в одном сечении — среднем. У корня и на периферии условия обтекания будут отличаться. Поэтому производим расчет ступени с учетом закрутки. Лопаточные аппараты профилируются так, чтобы обеспечить радиальное равновесие потока в межвенцовых зазорах. За счет безударного обтекания рабочих лопаток и предупреждения побочных течений газа в ступени экономичность ступени повышается. Закрутка приводит к увеличению степени реактивности ступени от корневого сечения к периферии.
Для обеих ступеней принимаем закон постоянства осевой составляющей скорости выхода газа из сопел, то есть C1a ® = const. Результаты расчетов закрутки в трех сечениях для ступени ТВД сведены в табл.2.4
Изменение основных параметров потока по высоте лопатки ступени ТВД и ТНД представлены на рис. 2.1., 2.2., 2.3., 2.4., 2.5., 2.6 .
Таблица 2.4. Результаты расчета закрутки лопаток ТВД
Наименование величины | Формула | Обозн | Разм. | Сечение | |||
корн. | средн. | периф. | |||||
Относительный радиус | r | ; | 0,872 | 1,000 | 1,128 | ||
Угол выхода потока из сопел | ?1 | град | 15,28 | 17,40 | 19,47 | ||
Осевая составляющая скорости за СА | C1а | м/с | 145,4 | 145,4 | 145,4 | ||
Окружная проекция абсолютной скорости | C1U | м/с | 532,3 | 464,0 | 411,3 | ||
Скорость газа на выходе из сопел | C1 | м/с | 551,8 | 486,3 | 436,2 | ||
Осевая составляющая скорости за РЛ | C2а | м/с | 183,6 | 183,6 | 183,6 | ||
Окружная скорость | U1 | м/с | 286,4 | 328,5 | 370,7 | ||
Адиабатический теплоперепад на соплах | hcад | кДж/кг | 158,5 | 123,1 | 99,1 | ||
Термодинамическая степень реактивности | ?т | ; | 0,163 | 0,350 | 0,477 | ||
Угол входа потока на РЛ | ?1 | град | 30,59 | 47,02 | 74,41 | ||
Скорость входа потока на РЛ | W1 | м/с | 285,7 | 198,8 | 151,0 | ||
Скорость выхода потока из РЛ | W2 | м/с | 359,7 | 394,1 | 428,5 | ||
Угол выхода потока из РЛ | ?2 | град | 30,70 | 27,77 | 25,37 | ||
Окружная проекция относительной скорости | W2U | м/с | 309,3 | 348,7 | 387,2 | ||
Окружная проекция абсолютной скорости | C2U | м/с | — 20,54 | 18,86 | 57,35 | ||
Угол выхода потока за РЛ | ?2 | град | 96,38 | 84,13 | 72,66 | ||
Кинематическая степень реактивности | ?кин | ; | 0,035 | 0,323 | 0,523 | ||
Удельная работа на ободе | hU | кДж/кг | 146,6 | 158,7 | 173,7 | ||
Скорость выхода потока (абсолютная) | C2 | м/с | 184,8 | 184,6 | 192,4 | ||
Статическая температура за СА | T1 | К | 931,8 | 961,1 | 981,0 | ||
Статическое давление за СА | P1 | МПа | |||||
Температура заторможенного потока на РЛ | T1W* | К | 967,0 | 978,2 | 990,8 | ||
Скорость звука на выходе из СА | м/с | 597,4 | 606,8 | 613,0 | |||
Число Маха на выходе из СА | ; | 0,924 | 0,801 | 0,712 | |||
Скорость звука на входе в РЛ | м/с | 597,4 | 606,8 | 613,0 | |||
Число Маха на входе в РЛ | ; | 0,478 | 0,328 | 0,246 | |||
Результаты расчетов закрутки в трех сечениях для ступени ТНД сведены в таблицу 2.5.
Таблица 2.5. Результаты расчета закрутки лопаток ТНД
Наименование величины | Формула | Обозн | Разм. | Сечение | |||
корн. | средн. | периф. | |||||
Относительный радиус | r | ; | 0,796 | 1,000 | 1, 204 | ||
Угол выхода потока из сопел | ?1 | град | 18,2 | 22,4 | 26,4 | ||
Осевая составляющая скорости за СА | C1а | м/с | 134,6 | 134,6 | 134,6 | ||
Окружная проекция абсолютной скорости | C1U | м/с | 409,6 | 326,0 | 270,7 | ||
Скорость газа на выходе из сопел | C1 | м/с | 431,2 | 352,7 | 302,3 | ||
Осевая составляющая скорости за РЛ | C2а | м/с | 171,0 | 171,0 | 171,0 | ||
Окружная скорость | U1 | м/с | 238,4 | 299,6 | 360,7 | ||
Адиабатический теплоперепад на соплах | hcад | кДж/кг | 96,8 | 64,8 | 47,6 | ||
Термодинамическая степень реактивности | ?т | ; | 0,230 | 0,485 | 0,622 | ||
Угол входа потока на РЛ | ?1 | град | 38,17 | 78,89 | 123,76 | ||
Скорость входа потока на РЛ | W1 | м/с | 217,8 | 137,2 | 161,9 | ||
Скорость выхода потока из РЛ | W2 | м/с | 308,4 | 356,5 | 405,9 | ||
Угол выхода потока из РЛ | ?2 | град | 33,68 | 28,67 | 24,92 | ||
Окружная проекция относительной скорости | W2U | м/с | 256,6 | 312,8 | 368,1 | ||
Окружная проекция абсолютной скорости | C2U | м/с | — 43,41 | 12,76 | 68,10 | ||
Угол выхода потока за РЛ | ?2 | град | 104,2 | 85,7 | 68,3 | ||
Кинематическая степень реактивности | ?кин | ; | 0,050 | 0,477 | 0,719 | ||
Удельная работа на ободе | hU | кДж/кг | 87,3 | 101,5 | 122,2 | ||
Скорость выхода потока (абсолютная) | C2 | м/с | 176,4 | 171,5 | 184,1 | ||
Статическая температура за СА | T1 | К | 839,3 | 865,8 | 880,0 | ||
Статическое давление за СА | P1 | МПа | |||||
Температура заторможенного потока на РЛ | T1W* | К | 859,8 | 873,9 | 891,3 | ||
Скорость звука на выходе из СА | м/с | 567,0 | 575,9 | 580,6 | |||
Число Маха на выходе из СА | ; | 0,760 | 0,612 | 0,521 | |||
Скорость звука на входе в РЛ | м/с | 567,0 | 575,9 | 580,6 | |||
Число Маха на входе в РЛ | ; | 0,384 | 0,238 | 0,279 | |||
3. Профилирование лопаток ТВД и ТНД
В основе расчета лежит методика, разработанная специалистами авиапромышленности и основанная на результатах статического анализа геометрических параметров профилей большого числа реально выполненных, тщательно отработанных и испытанных ступеней.
Исходными данными для расчета геометрических параметров профилей являются результаты газодинамического расчета ступени по сечениям.
Расчет производим на ЭВМ. Результаты расчета профилей лопаток ТВД и ТНД сводим в табл.3.1 и 3.2 .
Таблица 3.1. Геометрические параметры профилей рабочих лопаток ступени ТВД
Наименование величины | Формула | Обозн | Разм. | Сечение | |||
корн. | средн. | периф. | |||||
Скорость входа потока в решетку | C1a/sin?1 | W1 | м/с | 285,7 | 198,8 | 151,0 | |
Скорость выхода потока из решетки | ??w12 + 2?т hcтад????? | W2 | м/с | 359,7 | 394,1 | 428,5 | |
Входной угол потока | arctg (c1a/ (c1u — u1)) | ?? | град | 30,6 | 47,0 | 74,4 | |
Выходной угол потока | arcsin (c2a/w2) | ?2 | град | 30,7 | 27,8 | 25,4 | |
Число Маха | w2/a2 | Mw2 | ; | 0,602 | 0,650 | 0,699 | |
Ширина решетки | из расчета по среднему диаметру | B | м | 0,054 | 0,046 | 0,038 | |
Угол установки профиля | 0,85arctg [ (w1sin?1 + +w2sin?2) / (w2cos?2 ; w1sin?1)] | ?y | град | 80,1 | 62,2 | 49,8 | |
Хорда профиля | B [1/ sin?у + 0,054* * (1−1/sin?у)] | b | м | 0,0543 | 0,0516 | 0,0495 | |
Относительная максимальная толщина профиля | Принимаем | Cmax | ; | 0,250 | 0,125 | 0,045 | |
Оптимальный относительный шаг решетки | 0,6{ [180 (sin?1/sin?2) / / (180-?1-?2)] 1/3* * [1-cmax] } | tопт | ; | 0,516 | 0,730 | 0,983 | |
Диаметр рассчитанного сечения | DСР*rОТН | D2 | м | 1,040 | 1, 193 | 1,346 | |
Число лопаток в решетке | ?D2/ (tоптb) | Zл | шт | ||||
Шаг решетки | ?D2/zл | t | м | 0,028 | 0,032 | 0,036 | |
Фактический относительный шаг | t/b | t | ; | 0,518 | 0,626 | 0,737 | |
Входной геометрический угол профиля | ?1/ [a1?12+ +b1?1+c1+ (a2?12+ +b2?1+c2) ??2] | ?1л | град | 30,8 | 54,2 | 75,8 | |
Эффективный выходной угол решетки | ?2 — 2?5 | ?2э | град | 27,7 | 24,8 | 22,4 | |
Затылочный угол профиля | Принимаем | град | 10,5 | 9,8 | 9,1 | ||
Выходной геометрический угол профиля | ?2э + 26,66cmax — 0,276???4,29t + 4,13 | ?2л | град | 33,4 | 26,8 | 22,0 | |
Относительный радиус выходной кромки | Принимаем | R2 | ; | 0,01 | 0,01 | 0,01 | |
Относительный радиус входной кромки | 0,0527sin?1л+0,007* *sin?2л+0,236cmax+ +0,18R2-0,053 | R1 | ; | 0,039 | 0,024 | 0,013 | |
Относительное положение максимальной толщины | 0,1092+1,008?10-3* *?1л+3,335?10-3* *?2л-0,1525t+0,2188* * Сmax+4,697Ч10−3g | Xc | ; | 0,276 | 0,231 | 0, 199 | |
Относительная длина средней линии профиля | 1,32−2,182?10-3?1л — 3,072?10-3* *?2л+0,367cmax | L | ; | 1,242 | 1,165 | 1,103 | |
Угол заострения входной кромки | 3,51arctg [ (cmax/2; R1) / ((1-xc) L-R1)] | ?? | град | 55,5 | 31,1 | 9,1 | |
Угол заострения выходной кромки | 3,51arctg [ (cmax/2; R2) / ((1-xc) L-R2)] | ?2 | град | 15,9 | 7,3 | 1,8 | |
Горло межлопаточного канала | tsin?2 | ?2 | м | 0,0131 | 0,0135 | 0,0139 | |
Радиус входной кромки | bR1 | R1 | м | 0,0021 | 0,0013 | 0,0007 | |
Радиус выходной кромки | bR2 | R2 | м | 0,0005 | 0,0005 | 0,0005 | |
Максимальная толщина профиля | b cmax | Cmax | м | 0,0136 | 0,0064 | 0,0022 | |
Положение макс. толщины профиля | b xc | Xc | м | 0,0150 | 0,0119 | 0,0099 | |
Табчлица 3.2. Геометрические параметры профилей рабочих лопаток ступени ТНД
Наименование величины | Формула | Обозн | Разм. | Сечение | |||
корн. | средн. | периф. | |||||
Скорость входа потока в решетку | C1a/sin?1 | W1 | м/с | 217,8 | 137,2 | 161,9 | |
Скорость выхода потока из решетки | ??w12 + 2?т hcтад????? | W2 | м/с | 308,4 | 356,5 | 405,9 | |
Входной угол потока | arctg (c1a/ (c1u — u1)) | ?? | град | 38,2 | 78,9 | 123,8 | |
Выходной угол потока | arcsin (c2a/w2) | ?2 | град | 33,7 | 28,7 | 24,9 | |
Число Маха | w2/a2 | Mw2 | ; | 0,544 | 0,619 | 0,699 | |
Ширина решетки | из расчета по среднему диаметру | B | м | 0,085 | 0,073 | 0,061 | |
Угол установки профиля | 0,85?arctg? [ (w1sin?1 + +w2sin?2) / (w2cos?2 ; w1sin?1)] | ?y | град | 63,0 | 39,0 | 28,1 | |
Хорда профиля | B [1/ sin?у + 0,054* * (1−1/sin?у)] | b | м | 0,0952 | 0,1138 | 0,1256 | |
Относительная максимальная толщина профиля | принимается | Cmax | ; | 0,250 | 0,125 | 0,045 | |
Оптимальный относительный шаг решетки | 0,6{ [180 (sin?1/sin?2) / / (180-?1-?2)] 1/3х х [1-cmax] } | tопт | ; | 0,553 | 0,903 | 1,287 | |
Диаметр рассчитанного сечения | DСР*rОТН | D2 | М | 0,950 | 1, 194 | 1,438 | |
Число лопаток в решетке | ?D2/ (tоптb) | Zл | шт | ||||
Шаг решетки | ?D2/zл | t | м | 0,052 | 0,066 | 0,079 | |
Фактический относительный шаг | t/b | t | ; | 0,550 | 0,578 | 0,631 | |
Входной геометрический угол профиля | ?1/ [a1?12+ +b1?1+c1+ (a2?12+ b2?1+c2) ??2] | ?1л | град | 40,0 | 80,4 | 115,2 | |
Эффективный выходной угол решетки | ?2 — 2?5 | ?2э | град | 30,7 | 25,7 | 21,9 | |
Затылочный угол профиля | принимаем | град | 11,3 | 10,2 | 9,1 | ||
Выходной геометрический угол профиля | ?2э + 26,66cmax ; 0,276???4,29t + 4,13 | ?2л | град | 36,0 | 27,8 | 22,0 | |
Относительный радиус выходной кромки | принимаем | R2 | ; | 0,01 | 0,01 | 0,01 | |
Относительный радиус входной кромки | 0,0527sin?1л+0,007* *sin?2л+0,236cmax+ +0,18R2-0,053 | R1 | ; | 0,046 | 0,034 | 0,010 | |
Относительное положение максимальной толщины | 0,1092+1,008?10-3* *?1л+3,335?10-3* *?2л-0,1525t+0,2188* * Сmax+4,697Ч10−3g | Xc | ; | 0,293 | 0,270 | 0,255 | |
Относительная длина средней линии профиля | 1,32−2,182?10-3?1л — 3,072?10-3* *?2л+0,367cmax | L | ; | 1,214 | 1,105 | 1,018 | |
Угол заострения входной кромки | 3,51arctg [ (cmax/2; R1) / ((1-xc) L-R1)] | ?? | град | 50,2 | 21,9 | 10,2 | |
Угол заострения выходной кромки | 3,51arctg [ (cmax/2; R2) / ((1-xc) L-R2)] | ?? | град | 16,7 | 8,1 | 2,1 | |
Горло межлопаточного канала | tsin?2 | ?2 | м | 0,0267 | 0,0285 | 0,0296 | |
Радиус входной кромки | bR1 | R1 | м | 0,0044 | 0,0038 | 0,0012 | |
Радиус выходной кромки | bR2 | R2 | м | 0,0010 | 0,0011 | 0,0013 | |
Максимальная толщина профиля | b cmax | Cmax | м | 0,0238 | 0,0142 | 0,0057 | |
Положение макс. толщины профиля | b xc | Xc | м | 0,0279 | 0,0308 | 0,0321 | |
3.1 Расчет потерь энергии, КПД и мощности турбины
Расчет приведен в табл. 3.3
Таблица 3.3
Наименование | Формула | Обозначение | Размерность | ТВД | ТНД | |
Профильные потери для СА | ?hс. п | 4,88 | 2,56 | |||
Профильные потери для венцов РК | ?hр. п | 8,39 | 6,86 | |||
Концевые потери СА | ?hс. к | 1,03 | 0,68 | |||
Концевые потери в рабочих венцах | ?hр. к | 2,00 | 1,90 | |||
Радиальный зазор в СА | принимаем | ?с | мм | 2,0 | 2,0 | |
Радиальный зазор в РА | принимаем | ?р | мм | 2,0 | 2,0 | |
Потери от перетеканий в радиальном зазоре СА | ?hс. з | 1,659 | 0,535 | |||
Потери от перетеканий в радиальном зазоре РЛ | ?hр. з | 0,866 | 0,500 | |||
Использованный в ступени перепад | hu | 170,6 | 112,7 | |||
Внутренний КПД ступени | ?u | 0,901 | 0,896 | |||
Суммарный использованный теплоперепад в турбине:
КПД турбины без учета потерь на трение дисков:
Этот КПД определен с учетом полного использования выходной скорости всех ступеней, за исключением последней.
Оценивая потери на трение дисков с помощью ?тр~0,99, получаем внутренний КПД турбины
hТ—=—huТ—*—hтр;
hТ =0,899 *0,99=0,890
а общую мощность турбины:
= 82,83*283,3*0,890=23 231 кВт.
При вычете мощности, потребляемой компрессором, расположенном на этом же валу, с учетом механических потерь, получаем полезную (эффективную) мощность:
=83,72*177,9*0,86=12 809 кВт;
Ne = (NT — NK) *???мех;
Ne = (23 231 — 12 809) *0,96 = 10 010 кВт.
4. Расчет на прочность диска ТВД
Разрушение дисков является одной из наиболее тяжелых аварий, поскольку оно, как правило, влечет за собой полное разрушение турбины, а также наносит серьезный урон соседнему оборудованию.
Диски роторов являются одними из самых напряженных элементов турбомашин. Основные напряжения в дисках возникают вследствие центробежных сил инерции, обусловленных вращением ротора (динамические напряжения), и неравномерного распределения температуры по объему диска (температурные напряжения). Прочностные расчеты дисков турбомашин обязательны при их проектировании, так как они позволяют достичь необходимого запаса прочности и тем самым обеспечить достаточную надежность и долговечность эксплуатации турбомашин.
Динамические силы и напряжения, связанные с колебаниями и определяющие длительную усталостную прочность деталей в рамках данного дипломного проекта не рассматриваются. Расчет произведен для рабочего колеса ступени турбины высокого давления.
Основными величинами, влияющими на прочность диска, являются температура, воздействующая на него при работе и напряжения от действия центробежных сил.
В расчете используются следующие величины:
N — число разбиений диска на участки;
— плотность материала диска, ;
n — частота вращения диска, ;
— радиусы участков диска, м;
— ширины участков дисков, м;
— значения температур участков диска, ;
— значения коэффициентов линейного расширения, ;
— значения модуля упругости материала диска по участкам, МПа;
— значение динамических радиальных напряжений, МПа;
— значение динамических тангенциальных напряжений, МПа;
— значение температурных радиальных напряжений, МПа;
— значение температурных тангенциальных напряжений, МПа.
Свойства материала: предел текучести, модуль упругости, коэффициент Пуассона и коэффициент линейного расширения — принимаем в соответствии с температурой диска.
Таблица 4.1. Параметры, необходимые для расчёта диска ТВД
Материал диска | МПа | МПа | r0 | r1 | rа | rоб | у0 | у1 | уа | уоб | t0,0С | t, 0С | |
20Х12ВНМФШ | |||||||||||||
Таблица 4.2. Характеристики материала диска
Характеристика материала | Температура 0С | |||||||
Модуль упругости, ??????МПа | 2,14 | 2,12 | 2,09 | 2,03 | 1,95 | 1,87 | 1,71 | |
Коэффициент линейного расширения, ?t.10-6, 1/ 0C | 10,4 | ; | 10,5 | 10,7 | 11,0 | 11,4 | 12,0 | |
Коэффициент Пуассона, ? | 0,3, | 0,3 | 0,3 | 0,3 | 0,3 | 0,3 | 0,3 | |
Плотность, ?, кг/м3 | ||||||||
Предел текучести, ?0.2, МПа | ||||||||
Для расчета разобьем диск на 10 частей. На каждом участке реальный профиль заменяется профилем постоянной ширины. Температурный режим диска задается исходя из условий эксплуатации. Распределение температуры диска по радиусу задано в виде функции Распределение температуры диска по радиусу отображено в табл.4.1
Таблица 4.3. Распределение температуры по радиусу диска
№ участка | Внутренний радиус участка, rср, м | Температура участка, t, 0C | |
0,025 | |||
0,045 | |||
0,110 | |||
0,150 | |||
0,250 | |||
0,350 | |||
0,410 | |||
0,450 | |||
0,485 | |||
0,520 | |||
Расчет напряжений производится с применением ЭВМ (программа DISK22), исходные данные и результаты этого расчета приведены в прил.1.
— суммарные тангенциальные напряжения в точке диска,
— суммарные радиальные напряжения в точке диска.
Изменение температуры по радиусу диска отображено на рис. 4.1
Эпюры распределения напряжений отображены на рис. 4.2
=
== 254,1 МПа.
Запас прочности определяет коэффициент запаса прочности (). Для выбранного материала диска (сплав 20Х12ВНМФШ) при t = 436 С предел текучести =478 МПа.
Коэффициент запаса прочности: kзап =/?max =1,88.
Так как значение коэффициента запаса прочности вошло в необходимый диапазон (1,5 < kзап < 2,0), можно считать, что диск выдержит оказываемую на него нагрузку.
5. Спецтема: Расширение Пунгинского ПХГ (подземного хранилища газа)
" В условиях, когда потребление газа неравномерно в течение года, надежность поставок газа по разным направлениям призваны обеспечить подземные хранилища газа (ПХГ). Начавшийся процесс формирования газового рынка в России требует повышения гибкости поставок газа и увеличения активной емкости ПХГ. Поэтому сегодня «Газпром» работает над повышением суточной производительности ПХГ. Такие характеристики ПХГ позволят обеспечить еще большую надежность поставок российского газа внутренним и зарубежным потребителям" (член правления «Газпрома» Богдан Будзуляк).
Мировое потребление газа растёт и, по прогнозам XXII Мирового газового конгресса в Токио, к 2018 году может увеличиться вдвое. При этом повышаются требования к снижению удельных затрат на его транспортировку, к увеличению надёжности газопотребления.
Из-за неравномерности потребления (рис. 5.1., 5.2., 5.3) режимы работы магистральных газопроводов и компрессорных станций отклоняются от проектных, что приводит к увеличению удельных затрат на транспортировку газа. Для уменьшения неравномерности транспорта и создания резервов газа на случаи аварийных ситуаций на МГ используются подземные хранилища газа (ПХГ).
Пунгинское месторождение было введено в разработку в 1965 году с пластовым давлением 18,46 МПа и начальными запасами 60 млрд. м3 газа.
Пунгинское ПХГ создано на базе истощенного, но герметичного газового месторождения. Первая закачка газа в Пунгинское подземное хранилище газа была начата в августе 1985 года в соответствии с «Технологической схемой создания и эксплуатации комплекса Пунга-Шухтунгорд», разработанной ВНИИГАЗом в 1983 году и утвержденной в Мингазпроме в 1985 году.
Положительным моментом, повлиявшим на выбор Пунгинской структуры в качестве объекта для создания ПХГ явилось её выгодное расположение на трассе магистральных газопроводов от месторождений СРТО в центр Европейской части России.
В 1992 г. по заданию ГГК «Газпром» была разработана технологическая схема расширения Пунгинского ПХГ до активного объема 6,5 млрд. м3. Для ускорения сроков создания газахранилища была предусмотрена этапность его развития.
На первом этапе, используя существующие мощности, предполагалось вывести Пунгинское ПХГ на режим циклической эксплуатации с активным объемом газа 1,2 млрд. м3, что позволило бы на 63−65% отрегулировать сезонную неравномерность газопотребления и одновременно получить дополнительную информацию о пласте, необходимую для корректировки технологической схемы.
На втором этапе создания Пунгинского ПХГ предусматривалось подключить газохранилище к системе МГ с рабочим давлением 75 кгс/см2 (для повышения давления нагнетания), пробурить дополнительно 75 эксплуатационных скважин и вывести ПХГ на режим циклической эксплуатации с активным объемом газа 3,5 млрд. м3, максимальной суточной производительностью на отбор — 35 млн. м3/сут. (II очередь).
По третьему этапу (полное развитие газохранилища) проводилось только экспертная оценка возможных технологических показателей циклической эксплуатации, технологическая схема не разрабатывалась.
Основной задачей настоящей работы является разработка названной технологической схемы и определение основных показателей циклической эксплуатации III очереди создания Пунгинского ПХГ.
Показатели первого этапа создания и циклической эксплуатации на Пунгинском ПХГ достигнуты. Проведено, также подключение газохранилища к системе МГ с рабочим давлением 75 кг/см2. Следовательно, в настоящее время, Пунгинское ПХГ находится на втором этапе создания, хотя бурение эксплуатационных скважин начато, но приостановлено из-за отсутствия финансирования.
В перспективе рассматривается увеличение максимальной суточной производительности до 40 млн. м3.
Геометрический объём хранилища оценивается примерно в 311,5 млн. м3.
За восемнадцать лет эксплуатации Пунгинского ПХГ в пласт закачано 32,8 млрд. м3 и отобрано 24,8 млрд. м3 газа (Рис. 6.1). Максимальный отбор газа из хранилища составил 2,4 млрд. м3 в сезоне 1999;2000 г. г. Максимальное давление в пласте возросло с 4,18 до 6,86 МПа. Разница в 8 млрд. м3 вызвала повышение давления на 2,68 МПа. В соответствии с ростом пластового давления увеличилась производительность хранилища на отбор, превысившая 16 млн. м3/сут.
Отсутствие собственной компрессорной станции влияет на режим эксплуатации хранилища, который характеризуется нестабильностью, связанной с колебаниями давления в магистральном газопроводе. В период отбора нередко происходит переключение на закачку и обратно. Значительным колебаниям подтверждены как величины отборов по месяцам, так и общий объем отбора. Объемы закачки также характеризуются большой переменчивостью.
На балансе Пунгинского ПХГ 37 скважин, в том числе 31 эксплуатационная, 1 в капитальном ремонте и 5 наблюдательных и пьезометрических. Эксплуатационные скважины пробурены в период разработки месторождения и к настоящему времени отработали почти 40 лет. Практически по всем скважинам проводится комплекс исследований, включающих геофизические исследования, замеры давлений, дебитов, отборы проб воды. Существующая технология подготовки газа (двухступенчатая сепарация), морально и физически устаревшее технологическое оборудование не обеспечивают выполнение требований нормативных документов по качеству подготовки газа, подаваемого в магистральные газопроводы.
Актуальность расширения связана с отсутствием благоприятных геологических условий для создания подземных хранилищ вблизи крупных потребителей Урала и вдоль трассы магистральных газопроводов. Кроме этого, стратегические запасы газа в Пунгинском ПХГ позволяют обеспечить подачу газа в транспортную систему при вынужденных отключениях магистральных газопроводов, расположенных по ходу газа до Пунгинского ПХГ и, в общем, повышают надёжность подачи газа и позволяют оптимизировать режим эксплуатации системы газопроводов ООО «Тюментрансгаз» .
5.1. Схема работы ПХГ
При режиме закачки газ из магистральных газопроводов поступает в замерный пункт. После замера газ подаётся в компрессорный цех, компримируется до давления 80−87 кг/см2 и, после охлаждения в АВО, подаётся на блок входных ниток для распределения по газопроводам-шлейфам и скважинам и закачивается в подземное хранилище.
При режиме отбора газ от скважин ПХГ по шлейфам поступает на блок входных ниток, где на установках сепарации улавливается капельная влага и мехпримеси. Отсепарированный газ подаётся на установку осушки газа. Осушка осуществляется высококонцентрированным раствором ТЭГа (98,5−99,3%). После осушки газ замеряется на замерном пункте и, скомпримированный в компрессорном цехе, после охлаждения в АВО, подаётся в систему магистральных газопроводов. В начале сезона отбора, при высоких пластовых давлениях, газ в магистральные газопроводы может подаваться, минуя компрессорный цех.
Отсепарированная жидкость поступает на установку дегазации пластовой воды, где отделяется от углеводородного конденсата, растворённого газа и метанола. Затем жидкость направляется на установку очистки стоков.
Регенерированные метанол и конденсат от установки регенерации возвращается на склад реагентов и масел.
Для обеспечения безаварийной работы основных технологических установок на промплощадке ПХГ предусматриваются вспомогательные установки и сооружения:
система сброса газа высокого и низкого давлений;
установка подготовки топливного, пускового и импульсного газов;
установка подогрева теплоносителя для технологических нужд;
компрессорная воздуха КИП;
установка получения инертного газа;
склад реагентов и масел;
установка приготовления моющего раствора для ГПА и регенерации фильтров;
маслохозяйство компрессорного цеха.
5.2. Расчёт количества эксплуатационных скважин для вывода ПХГ на режим циклической эксплуатации с активным объемом газа 3,5 млрд. м3 и производительностью 35 млн. м3/сут.
На старой промплощадке в настоящее время работает 31 скважина.
Средняя длина одного шлейфа от скважины до существующего ПХГ 3, 464 км;
Диаметр проходного сечения шлейфаD = 150 мм;
Среднее давление на устье скважины рн = 40,4 кг/см2;
Среднее давление на входе в блок сепарации рк = 36,2 кг/см2;
Средняя температура грунтаtгр = - 3,5 оС;
Средняя температура газа на устье скважиныtн = 7,7 оС;
Средняя температура газа на входе в блок сепарацииtк = 4,9 оС;
Средний суточный расход одного шлейфаQ = 0,542 935 млн. м3/сут.
Для расчётов температуры и давления газа необходимо перевести в абсолютные величины:
Т = (t + 273,15) К; Р = (р+ 1) кг/см2.
Расчёт коэффициента гидравлической эффективности (Е)
шлейфа Ду150 мм
;
кг/см2;
;
;
К;
;
Коэффициент сжимаемости газа
где: ;
= 0,2344;
тогда: =0,9144;
Коэффициент гидравлического сопротивления теоретический () шлейфа Ду150 мм
=0,0147;
Коэффициент гидравлического сопротивления фактический () шлейфа Ду150 мм
где:
=0,3142;
тогда: =0,0179;
Коэффициент гидравлической эффективности шлейфа Ду150 мм
= 0,9056.
Расчёт коэффициентов гидравлического сопротивления и гидравлической эффективности «среднего» шлейфа выполнен для одного фактического режима работы шлейфов. В динамике все величины непрерывно меняются. Кроме того, расход газа по шлейфам напрямую зависит от перепада между давлением пласта и создавшимся давлением на замерном узле (в зависимости от режима работы газотранспортной системы). Причём эти зависимости при отборе и закачке разные (рис. 5.4. и 5.5)
На новой промплощадке ПХГ проектируем шлейфы Ду300 мм. Исходя из того, что газ из ПХГ идёт с влагой, и возможны гидратообразования, принимаем для новых шлейфов такую же эффективность. Давление газа на устье скважин для расхода 35 млн. м3/сут рн = 37,9 кг/см2 (при неизменном давлении газа на входе в блок сепарации). Для упрощения расчётов, температуры газа (начальную и конечную) и грунта для шлейфа Ду300 мм принимаем такие же, как и в расчёте шлейфа Ду150 мм.
Расчёт необходимого количества шлейфов и скважин Ду300 мм
Коэффициент гидравлического сопротивления теоретический () шлейфа Ду300 мм
=0,0128;
Коэффициент гидравлического сопротивления фактический () шлейфа Ду300 мм
=0,0156;
=11,52;
Суточный расход одного шлейфа Ду300 мм
=2,058 млн. м3/сут;
Необходимое количество шлейфов для суточного расхода 35 млн. м3
=17.
Так как для статических замеров один раз в декаду шлейфы поочерёдно выключаются из работы, для стабильного расхода газа из ПХГ необходимо 17+1=18 шлейфов и 18 скважин.
Семнадцать новых шлейфов Ду300 мм смогут заменить 32 старых шлейфа Ду150 мм по производительности на тех же режимах работы.
Применение дожимного компрессорного цеха позволит увеличить давление пласта в конце сезона закачки до 80 кг/см2, что, в свою очередь, даст возможность увеличить подачу газа в газотранспортную систему в сезон отбора. В результате: 7 млрд. м3 газа (3,5 млрд. м3 при отборе и 3,5 млрд. м3 при закачке), на которые летом уже затрачена работа, на половине пути по ГТС ООО «Тюментрансгаз» будут заложены на хранение, а зимой, с середины пути, с минимальными затратами, поданы в ГТС.
Заключение
При дипломном проектировании рассчитана ГТУ для привода нагнетателя природного газа мощностью 10 МВт со следующими техническими данными:
Эффективная мощность кВт 10 010;
Эффективный КПД%28,1;
Расход воздуха в компрессоре кг/с83,72;
Степень сжатия в компрессоре 4,4;
Температура газов перед турбиной К1063;
Давление газа перед турбиной МПа0,4236;
Температура газа за ТНД К791,5;
Давление газа за ТНД МПа0,106;
Частота вращения ротора ТВД об/мин5280;
Частота вращения ротора ТНД об/мин4800.
По спецтеме: в результате расширения Пунгинского ПХГ будут решены следующие задачи:
увеличена суточная производительность с 17 до 35 млн. м3/сут;
выведен из эксплуатации существующий технологический комплекс с морально и физически устаревшим оборудованием, не обеспечивающим качественной подготовки газа;
вынесены из пределов водоохраной зоны реки Пунга основные объекты технологического и вспомогательного назначения.
Технико-экономические показатели по этапам расширения ПХГ, приведенные в табл.6.1, свидетельствуют о том, что эффективность капвложений возрастает по мере наращивания активного объема газа в хранилище с 3,5 до 10 млрд. м3. В этой связи рекомендуется строительство объектов расширения ПХГ вести непрерывно с поэтапным вводом в эксплуатацию производственных мощностей по закачке и отбору газа из/в хранилища — 3,5; 6,5; 10 млрд. м3, соответственно.
Для повышения эффективности капвложений представляется целесообразным рассмотрение варианта по закачке газа в хранилище с давлением на стороне нагнетания ГПА до 10 МПа уже на 3-ем этапе (очереди) расширения ПХГ, что позволит увеличить активный объем газа в хранилище без дополнительных капвложений с 6,5 млрд. м3 до 8 млрд. м3.
Кроме того, необходимо уже в настоящее время, т. е. до окончания строительства 2-й очереди сделать заявку на разработку и изготовление отдельных видов арматуры, соединительных деталей трубопроводов и аппаратов воздушного охлаждения (АВО) на давление 12 МПа. Это позволит в последующем (на 4-ом этапе расширения ПХГ) избежать необходимости выполнения трудоемких строительно-монтажных работ по замене отдельных видов арматуры, соединительных деталей трубопроводов и АВО на расчетное давление 12 МПа, а также без увеличения капвложений увеличить активный объем газа в хранилище с 10 млрд. м3 до 13−14 млрд. м3 за счет увеличения, при закачке газа в хранилище, давления на стороне нагнетания ГПА до 12 МПа.
Библиографический список
Газотурбинные установки. Конструкции и расчет. / Справочное пособие под общ. ред. Л. В. Арсеньева и В. Г. Тырышкина. Л.: Машиностроение, Ленинградское отделение, 1978, 232с.
Газодинамический расчет многоступенчатой газовой турбины: Методические указания к курсовому проектированию по курсу «Турбомашины» / Б. С. Ревзин, В. Г. Шамрук. Екатеринбург: УГТУ-УПИ, 1994, 31с.
Расчет на прочность диска сложного профиля с применением ЭВМ: Методические указания к курсовому и дипломному проектированию/ П. Н. Плотников. Свердловск: УПИ, 1989, 27с.
Тепловой расчёт схем приводных газотурбинных установок на номинальный и переменный режимы работы. Б. С. Ревзин, А. В. Тарасов, В. М. Марковский, 2001.
Фондовые материалы: ВНИИГАЗа, РАО «Газпром», ТГНГУ.
Справочник работника газовой промышленности. М. М. Волков, А. Л. Михеев, К. А. Конев М «Недра» — 2-е изд., перераб. и доп. — М Недра, 1989. — 286 с.
Методика определения запаса газа газотранспортных предприятий.
Технико-экономический анализ производства: Б. В. Прыкин М.: ЮНИТИ-ДАНА, 2000. — 399 с.
Экономический анализ предприятия Л. В. Прыкина М.: ЮНИТИ-ДАНА, 2002. — 360 с.
Экономика предприятия: В. П. Грузинов, В. Д. Грибов М.: Финансы и статистика, 2001 г. 208 стр.