Другие работы
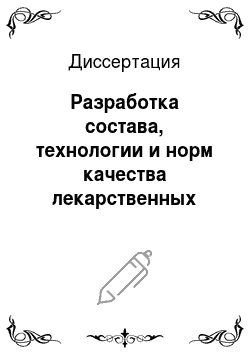
Проведено сравнительное изучение 14 мазевых основ и выбран оптимальный состав мази и пластырной массы эвкалипта листьев экстракта густого. Разработан способ производства мази и диадерматического пластыря, позволяющий получить лекарственные препараты с высокой фармацевтической доступностью и необходимыми технолого-экономическими характеристиками. Экспериментально установлена возможность…
Диссертация 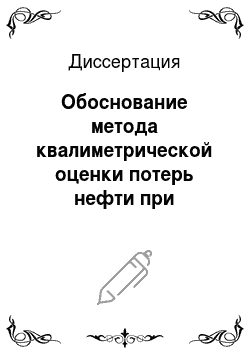
Обобщение опыта разработки нефтяных месторождений позволило выделить возможные варианты недропользования: I — добыча — сбор, учет и транспортирование продукции скважин — подготовка нефтимагистральный трубопровод, хранениеII — добыча — сбор, учет и транспортирование продукции скважин — подготовка нефти — внутрипромысловое хранение — магистральный трубопровод, хранениеIII — добыча — сбор, учет…
Диссертация 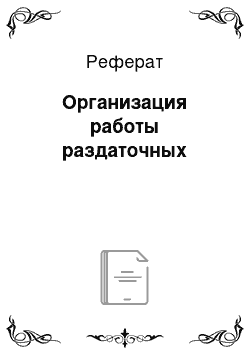
ЗАДАНИЕ: проанализируйте текст и перенесите в тетрадь ниже приведенную таблицу, заполнив в ней IV колонку. |Вид раздачи |Марка |Оборудование |Назначение — |немеханизирован|ЛПС |Прилавок для подносов и приборов; — | |ные, — |охлаждаемый прилавок-витрина для — | |универсальные — |холодных закусок; прилавки-мармиты — | — | |для первых и вторых блюд; прилавок — | — | |для горячих напитков, холодных…
Реферат 
Новые индукционные технологии, разработка которых производится в настоящее время, это зонная плавка полупроводниковых монокристаллов большого диаметра, нагрев слябов в сталепрокатном производстве, стальной ленты в процессе нанесения корозионно стойких покрытий типа цинкования и гальванилинга, пайка высокотемпературными припоями медных выводов мощных электрических машин и трансформаторов, пайка…
Диссертация 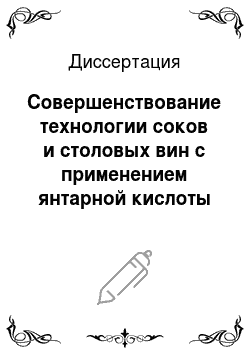
Новая социально-экономическая ситуация, складывающаяся в стране в связи с переходом к рыночным отношениям, приводит к обострению социальных проблем. Проблема качественного питания является многогранной и включает в себя социально-экономический, медико-биологический, научно-технический и производственный аспекты. Разработка экономического и медико-биологического обоснования научных исследований…
Диссертация 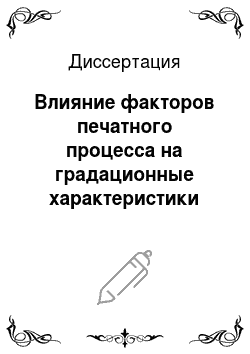
Тенденция к увеличению объёмов производства продукции, изготавливаемой с использованием трафаретного способа печати ставит задачу расширения возможностей и повышения качества воспроизведения полутоновых изображений. Наиболее оптимальным методом полутонового репродугщрования, как и в других способах печати, является растрирование. Воспроизведение растровых изображений на стадии печатного процесса…
Диссертация 
Между тем, как показали проведенные нами эксперименты, перспективным способом МХА катализаторных масс (композиций), в частности, ни-кельмедьалюминиевой каталитической системы, является их обработка в гидромеханической мельнице струями воды высокого давления и мелющими телами. Данная система проявляет высокие каталитические свойства в процессах очистки технологических газов от кислорода, а также…
Диссертация 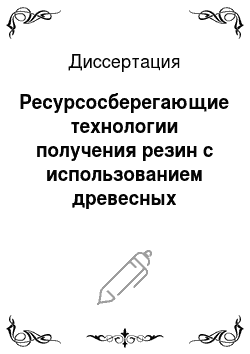
В настоящее время социальные и экономические достижения любой страны во многом определяются развитием производства полимеров. Однако их производство связано с большим количеством энергетических, материальных и трудовых затрат. В тоже время необходимость повышения качества выпускаемых изделий требует создания новых композиционных материалов и усовершенствование существующих. Свойства полимерных…
Диссертация 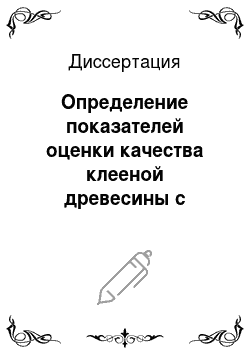
Установлено, что разрушающие напряжения в клееных композициях, содержащих дефекты склеивания, значительно меньше, чем в бездефектных. Если величина дефекта стремится к нулю, значения разрушающих напряжений стремятся: для трещин нормального отрыва к пределу прочности при равномерном отрыведля трещин плоского сдвига — к пределу прочности при скалывании. При увеличении размеров дефектов разрушающие…
Диссертация 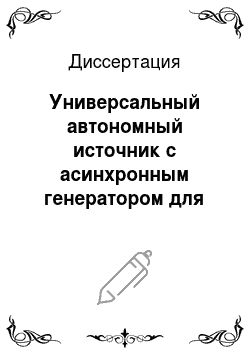
Методика исследования включает аналитические и экспериментальные методы. Аналитические методы исследования базируются на современной теории работы асинхронных машин, численных методах решения систем дифференциальных уравнений, а также методиках определения экономической эффективности результатов научно-исследовательских и опытно-конструкторских работ. Экспериментальные исследования проводились…
Диссертация 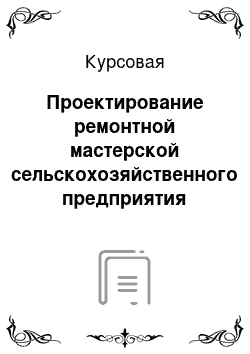
В настоящее время в связи с увеличением численности парка автомобилей и тракторов увеличивается его воздействие на окружающую среду. Основными факторами, влияющими на окружающую среду, животный и растительный мир, в том числе и на человека, являются отработавшие газы автомобиля, которые содержат окиси углерода, а также окислы свинца. Наряду с отработавшими газами вредное действие на окружающую…
Курсовая 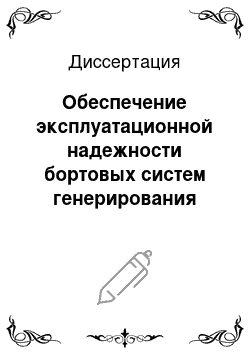
Основы теории надежности в нашей стране разработаны Гнеденко Б. В., Беляевым Ю. К., Соловьевым А. Д. Научные изыскания в области надежности авиационной техники продолжили Барзилович Е. Ю., Северцев H.A. и другие. Большой вклад в развитие теории технической эксплуатации авиационного оборудования внесли Воробьев В. Г., Константинов В. Д. Кузнецов C.B. и другие ученые, подкрепив теоретические…
Диссертация 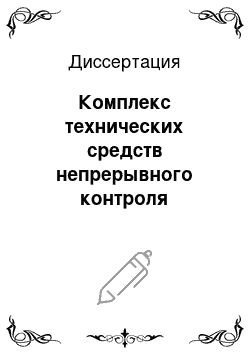
Актуальность работы В настоящее время большое значение имеет надежность электроснабжения потребителей. В то же время, мощность оборудования, отработавшего свой ресурс, в энергосистемах России возросла и в 2000 г. достигла, по оценкам экспертов, 35,3 млн кВт (17,2%), а к 2005 г. составит -55 млн кВт (26,8%). Кроме того, к 2005 г. выработают свой ресурс 21- млн кВт мощностей оборудования…
Диссертация 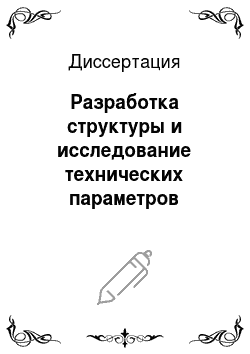
Современные тенденции в приборостроении предполагают использование микропроцессоров, контроллеров, быстродействующих электронных преобразователей измеряемого параметра с высокими метрологическими характеристиками, управляющих ПЭВМ. Новая философия измерений смещается от классической (измерение с помощью датчиков и вольтметров) концепции измерения одной величины специально предназначенным для…
Диссертация 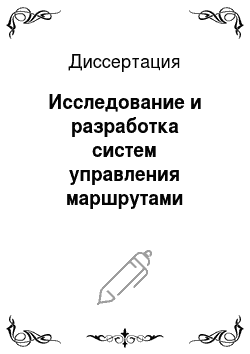
Высокие темпы развития народного хозяйства нашей страны, непрерывный рост выпуска промышленной продукции и значительно возрастающие объемы перевозок энергетического сырья требуют резкого увеличения грузопотока на железнодорожном транспорте. В постановлении / I / «Основные направления экономического и социального развития СССР на I98I-I985 годы и на период до 1990 года», принятом на ХХУ1 съезде…
Диссертация