Другие работы
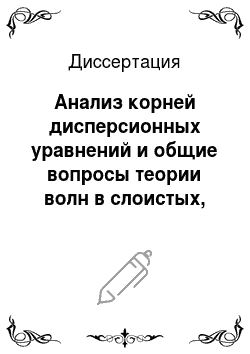
Сессия научного совета АН по пробл. «Физическая и технич. акустика» посвященная памяти И. А. Викторова // Акуст. ж. -1992; № 6 — С. 1121.52. Смешанные задачи механики деформируемого тела /Всесоюзная науч. конф.: Тезисы д-дов. 4.1. Ростов — н/Д, 1977. Спиновые (магнитостатич.) волны: Новые среды носители и нелинейные процессы. Устройства и приборы СВЧ на МС колебаниях и волнах / «Ферритовые СВЧ…
Диссертация 
Теорема Нетер, доказанная ею во время участия в работе целой группы по проблемам общей теории относительности как бы побочно, стала важнейшим инструментом теоретической физики, утвердившей особую роль принципов симметрии при построении физической теории. Можно сказать, что теоретико-инвариантный подход, эрлангенский принцип проник в физику и определил целесообразность формулирования физических…
Реферат 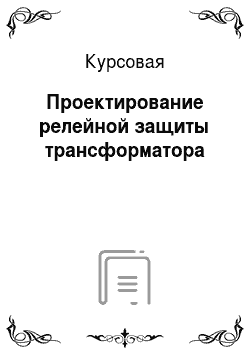
В данном курсовом проекте рассчитаны продольная дифференциальная защиты от к.з. в обмотках и на наружных выводах трансформатора, максимальные токовые защиты (МТЗ) — от внешних к.з., максимальная токовая направленная защита — для устранения подпитки к.з. на ЛЭП системы внешнего электроснабжения со стороны тяговой или районной обмотки трансформатора, максимальные токовые защиты для защиты…
Курсовая 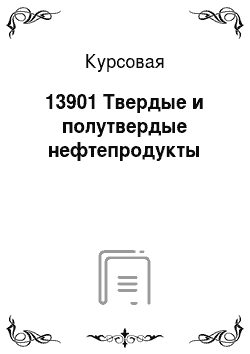
В нормативной документации на каждый вид битума указаны стандарты, по которым необходимо проводить экспертизу битумов для определения соответствия физико-химических характеристик товара нормативным требованиям. К числу стандартных характеристик относятся пенетрация (глубина проникновения иглы при 250С), температура размягчения, растяжимость, растворимость, изменение массы после прогрева…
Курсовая 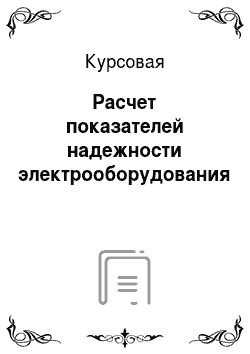
Безотказность электрооборудование надежность Важную роль в проектировании электрических систем играет проблема обеспечения надежности эксплуатации электрооборудования. С ростом конкуренции в данной отрасли возрастает экономическая ответственность компаний за нарушение нормального режима работы выпускаемой ими продукции. Поэтому производственные компании заинтересованы в обеспечении надежности…
Курсовая 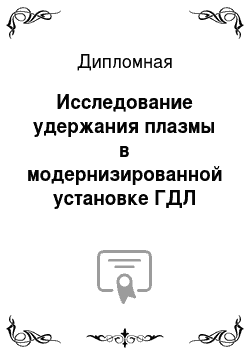
В общем случае осесимметричная магнитная ловушка не обладает конфигурацией благоприятной для обеспечения МГД устойчивого удержания плазмы. В описываемых экспериментах для подавления поперечных потерь, связанных с развитием неустойчивых МГД мод в аксиально-симметричном пробкотроне без использования дополнительных стабилизирующих магнитных ячеек, был применен метод вихревого удержания. Этот метод…
Дипломная 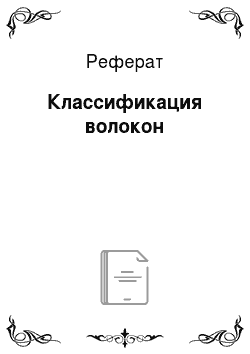
В настоящее время существуют несколько стандартных методов определения жесткости. Согласно ГОСТ 10 550−93 жесткость материалов определяется по методу консоли. Для определения показателей свойств при изгибе применяют различные способы испытаний: метод консоли, метод кольца, продольного изгиба, балки, лежащей на двух опорах. Это связано с тем, что материалы, применяемые для изделий легкой…
Реферат 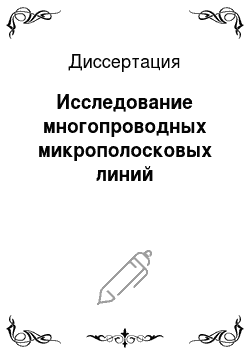
Существенную роль в обеспечении технической и экономической эффективности систем радиосвязи, радиолокации и радионавигации играют микроэлектронные устройства сверхвысоких частот (СВЧ). Использование в технике СВЧ приборов и аппаратуры, основанных на применении микроэлектронных устройств, имеющих малые габариты и массу, повышает надежность в условиях воздействия различных дестабилизирующих…
Диссертация 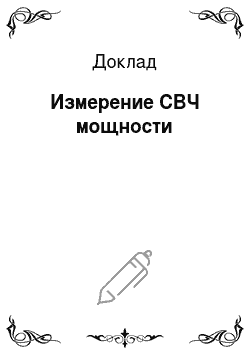
Мощность в общем виде есть физическая величина, которая определяется работой, производимой в единицу времени. Единица мощности ватт (Вт) соответствует мощности, при которой за одну секунду выполняется работа в один джоуль (Дж). На постоянном токе и переменном токе низкой частоты непосредственное измерение мощности зачастую заменяется измерением действующего значения электрического напряжения…
Доклад 
Математически задача исследования квантово-полевых эффектов в искривленном пространстве-времени представляет собой некоторое приближение к пока не созданной квантовой теории гравитации, при котором гравитационное поле рассматривается как классическая фоновая метрика пространства-времени, а материальные поля представляют собой стандартные квантованные объекты (однопетлевое приближение). Исходя…
Диссертация 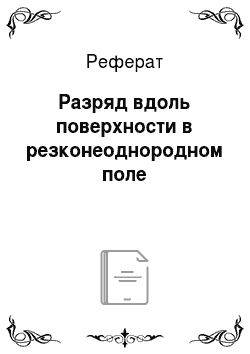
К внутренней изоляции относится изоляция обмоток трансформаторов и электрических машин, изоляция кабелей, конденсаторов, герметизированная изоляция вводов, изоляция между контактами выключателя в отключенном состоянии, т. е. изоляция герметически изолированная от воздействия окружающей среды корпусом, оболочкой, баком и т. д. Внутренняя изоляция как правило представляет собой комбинацию различных…
Реферат 
В течение 50 лет, прошедших с момента появления первого лазера, наблюдается устойчивый рост средних и пиковых мощностей лазерного излучения. Эта тенденция обусловливает ужесточение требований к материалам, используемым в лазерах. Высокие тепловые нагрузки в активных элементах твердотельных лазеров требуют тщательной оптимизации параметров резонатора и активного элемента и знания его реальной…
Диссертация 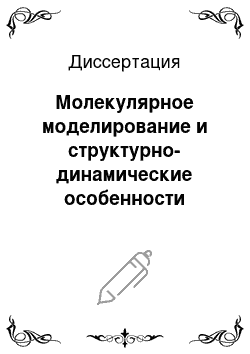
Структурное и функциональное разнообразие ионных каналов, а также их участие в работе жизненно важных систем организма обуславливает повышенный интерес к их исследованию. На сегодняшний день клонировано более 500 генов, кодирующих субъединицы ионных каналов как эукариотического происхождения, так и их бактериальных аналогов (Jegla et al., 2009). Однако сложная молекулярная архитектура…
Диссертация 
Учитывая абсолютные размеры наночастиц, с определенными допущениями можно считать, что наночастица представляет собой вещество, близкое по свойствам к межфазной границе. Например, нанотрубки имеют высокую удельную плотность поверхности, поскольку вся масса сосредоточена в поверхностном слое. Кроме того, расстояние между графитовыми слоями в многослойных системах (0,335 нм) оказывается…
Курсовая 
Отличительной особенностью нулевой схемы выпрямителя является то, что в ней необходим трансформатор, так как двигатель включается между общей точкой трансформатора и общей точкой катодов (VT1…VT3) и анодов (VT4…VT6). Ток проводит тиристор, который имеет наиболее высокий потенциал анода по отношению к катоду. В этой схеме точки естественного от крывания вентилей сдвинуты на угол 30. Каждый…
Курсовая