Другие работы
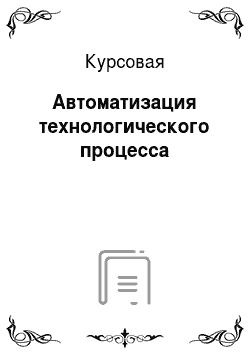
Механизмы МЭО (механизмы электрические однооборотные) в комплекте с запорно-регулирующей арматурой используются для контроля и регулирования трубопроводными потоками различных жидких и газообразных сред. Управление работой механизмов МЭО осуществляется в автоматическом режиме по командному сигналу в соответствии с заданным законом регулирования регулирующего устройства в системах автоматического…
Курсовая 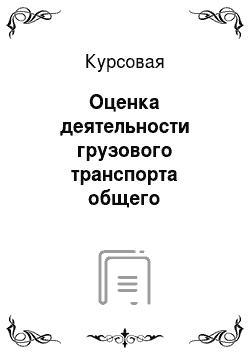
За изучаемый период с 2006 по 2010 год в Российской Федерации наибольший удельный вес по перевозкам груза в общем занимает автомобильный транспорт. В среднем за пять лет доля автомобильного транспорта по грузоперевозкам составила 73% от общего количества и число его грузоперевозок возрастает от года к году. Просматривается положительная динамика. Наименьший удельный вес отводится воздушному…
Курсовая 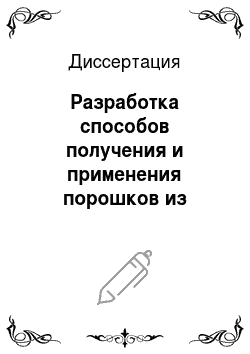
На территории Таджикистана расположены большие массивы дикорастущего шиповника, а ежегодный объем заготовок плодов составляет около 2−4 тыс. т. Плоды шиповника являются богатейшим источником природных антиоксидантов (витаминов С, Е, каротиноидов, биофлавоноидов), пищевых волокон и минорных биологически активных веществ, повышающих устойчивость организма к загрязнению среды, радиации, стрессовым…
Диссертация 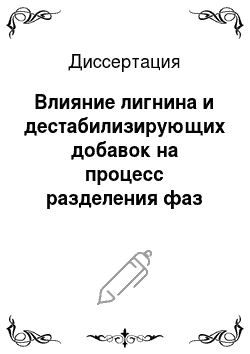
В современных условиях особое внимание уделяется вопросам рационального природопользования, экологии, влиянию промышленности на состояние окружающей природной среды. Для бассейна Северной Двины наиболее значимы проблемы, связанные с процессами получения целлюлозы, т.к. он отличается высокой концентрацией целлюлозно-бумажных предприятий. Целлюлозное производство является наиболее крупным…
Диссертация 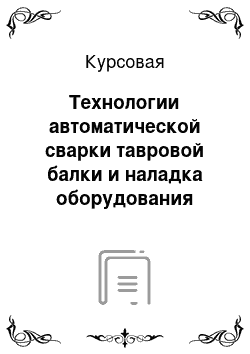
Режим ТОМОГРАФОбеспечивает работу прибора с АР и формирование томограмм в реальном масштабе времени. При работе в томографическом режиме на экран выводится не только томограмма (В-Скан), но и служебная информация, включая стробы, курсоры, цифровые индикаторы и т. д. После обнаружения дефектов обеспечивается возможность оценки их реальных или эквивалентных размеров следующими методами: классическим…
Курсовая 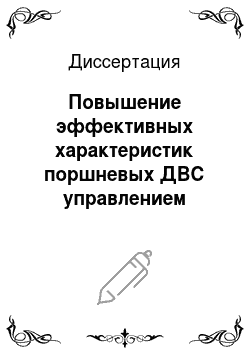
Считается, в настоящее время двигатели внутреннего сгорания практически исчерпали резервы улучшения показателей работы, таких как экономические, экологические, эффективные. Одно из направлений развития ДВС связано с улучшением рабочего процесса, путем организации работы двигателя на предельно обедненной топливо-воздушной смеси (TBC). Работа на таких режимах связана с большими величинами…
Диссертация 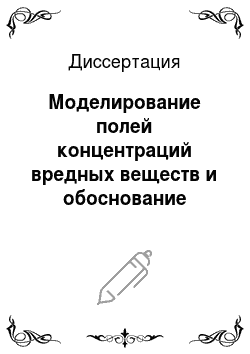
Публикации. По материалам диссертационной работы опубликовано 5 научных работ, общим объемом 17 стр. Личный вклад автора составляет 11 стр. Основные результаты по разработке математической модели распространения вредных веществ в производственных помещениях опубликованы в Научном вестнике Воронежского государственного архитектурно-строительного университета и в Вестнике Воронежского…
Диссертация 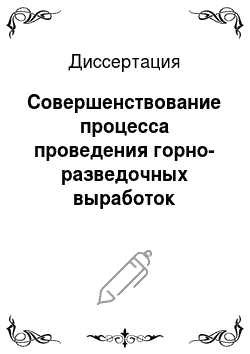
Решениями ХХУ1 съезда КПСС и XI пятилетним планом развития народного хозяйства СССР предусматривается дальнейшее расширение минерально-сырьевой базы. В комплексе геологоразведочных работ важное место занимает проходка подземных разведочных выработок. По прогнозным данным разведка месторождений подземными горными выработками в системе Мингео СССР сохранит свое преимущественное значение…
Диссертация 
По результатам выполненных исследований, на основании анализа процессов полного растворения хромихроматов, их деоксоляции, деолифика-ции и двухстадийного восстановления разработан технологический регламент получения сухого хромового дубителя с улучшенными кожевенно-технологическими свойствами. Указанный регламент апробирован с положительными результатами на Актюбинском заводе хромовых соединений…
Диссертация 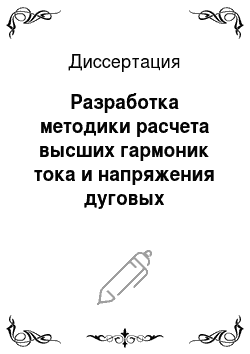
Апробация работы. Основные положения диссертационной работы докладывались на кафедре «Электроснабжение и электротехника» Тольят-тинского государственного университета, а также обсуждались на V Всероссийской научно-технической конференции «Современные промышленные технологии» (г. Нижний Новгород, 2006 г.), Международной научно-технической конференции, посвященной 50-летию ЛГТУ «Энергетика…
Диссертация 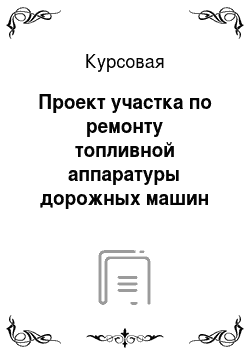
К настоящему времени сформировались различные системы технического обслуживания (ТО) и текущего ремонта (Р), среди которых можно выделить две основные: планово-предупредительную (ППР) и систему ТО и Р по потребности. Эти системы основаны на использовании технического диагностирования, с помощью которого определяют состояние машины в данный момент и дают рекомендации по объёму и времени…
Курсовая 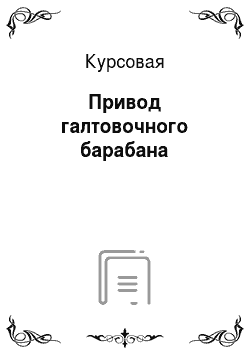
Смазывание подшипников осуществляем пластичными материалами. Полость подшипника закрываем с внутренней стороны мазеудерживающими шайбами. Смазочный материал набивают в подшипник вручную при снятой крышке подшипникового узла на несколько лет. Смену смазочного материала производят при ремонте. Для предотвращения вытекания смазочного материала из подшипниковых узлов, а также для защиты…
Курсовая 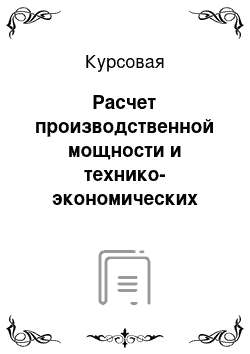
Р -количество вспомогательных рабочих;Kдоп- коэффициент, учитывающий доплаты по районному коэффициенту, доплаты за условия интенсивность труда (Kдоп=1,2÷1,4);Kпрем — коэффициент, учитывающий доплаты по премиальным системам оплаты труда (Kпрем =1,15÷1,3);Kдзп — коэффициент, учитывающий дополнительную заработную плату (Kдзп=1,15);Звсп = 42,98*14*1760*1,3*1,2*1,15 = 1900 тыс. руб. Отчисления…
Курсовая 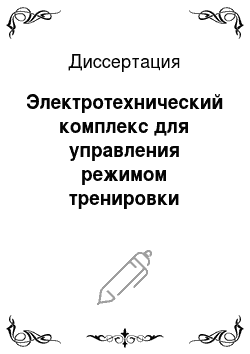
Вопросам повышения эффективности тренировочного процесса с введением строго дозированных по интенсивности и времени выполнения физических нагрузок в последнее время посвящено много работ применительно к конкретным видам спорта. Получили достаточно широкое распространение радиоэлектронные автоматизированные средства контроля и управления характером, интенсивностью и продолжительностью упражнений…
Диссертация 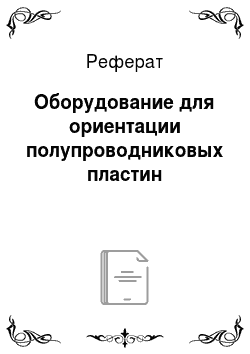
Для ориентации рентгеновским способом используют установки УРС-50И, УРС- 60, УРС-70К1. Универсальная установка УРС-50И с приставкой ЖК 78.04 предназначена для определения ориентации в кристаллографической плоскости (111). Максимальный угол отклонения кристаллографической плоскости (111) от торца слитка Si, который можно определить на данной установке, составляет 14°, а для слитков Ge — 13…
Реферат