Другие работы

Исходным фактором процесса шлифования является подлежащая обработке заготовка: исходя из ее материала и его состояния, формы, размеров, геометрической точности заготовки определяют условия шлифования и, в частности, выбирают средства технологического оснащения. Исследованиям эффективности процессов шлифования заготовок из различных материалов посвящено большое количество работ, в которых…
Диссертация 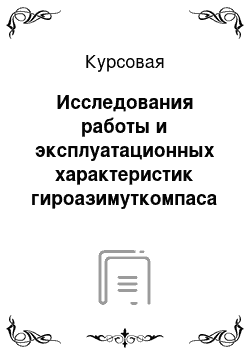
Отметить момент времени, когда погаснет табло «Пуск» (примерно через 3−5 мин. после срабатывания термореле 1ВК3). В этот момент автоматически подается питание на стабилизирующие двигатели, что сопровождается характерным «рывком» шкалы прибора ВГ-1А. Если этот рывок не наблюдается или шкала не начнет вращаться с большей частотой, гироазимуткомпас следует выключить. Если через 40 мин. после…
Курсовая 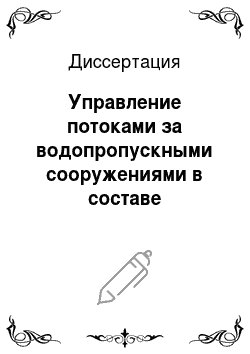
В основу разрабатываемой в рамках данной работы концепции проектирования креплений нижнего бьефа автором была положена идея создания условий для рассосредоточенного характера управления течениями в нижнем бьефе, путём более активного использования элементов крепления дна — рисбермы и концевого устройства — для гашения избыточной энергии потока, т. е. использования их в качестве активных участков…
Диссертация 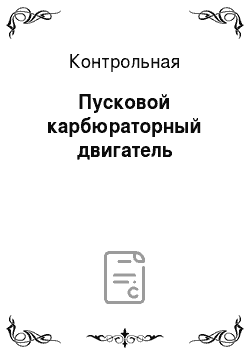
Если угол не соответствует норме, то вывертывают болт и, не меняя положения валика, снимают ры-чаг со шлицев и устанавливают вновь в требуемом поло-жении, после чего завертывают болт. Убеждаются, что пусковая шестерня (бендикс) находится в выключен-ном положении. Для этого поворачивают рычаг про-тив часовой стрелки. Он не должен перемещаться (при перемещении ощущается жесткий удар). При помощи…
Контрольная 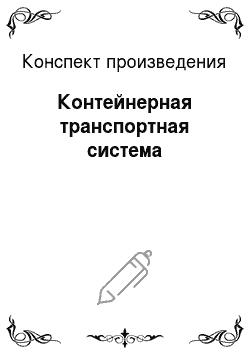
Серийно изготовляемые специализированные платформы отличаются от переоборудованных большей длиной и конструкцией упоров. Размещение упоров на платформах обоих типов дает возможность перевозить на них контейнеры разных типоразмеров. На переоборудованных платформах каждый из промежуточных упоров в отдельности может быть установлен в рабочее или нерабочее положение. На современных длиннобазных…
Конспект произведения 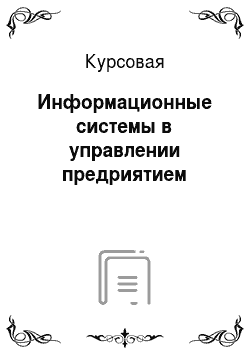
В современных условиях эффективное управление представляет собой ценный ресурс организации, наряду с финансовыми, материальными, человеческими и другими ресурсами. Следовательно, повышение эффективности управленческой деятельности становится одним из направлений совершенствования деятельности предприятия в целом. Наиболее очевидным способом повышения эффективности протекания трудового процесса…
Курсовая 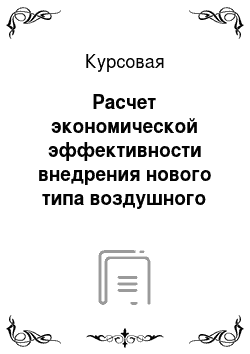
Проведенный нами сравнительный анализ на основании технических и эксплуатационных данных двух воздушных судов: ИЛ-62М и Ту-214, привел к, на первый взгляд, достаточно очевидному решению. Мы получили, что себестоимость авиаперевозок ИЛ-62М составила 20 409 602 рубля, в то время как себестоимость авиаперевозок Ту-214 по тому же маршруту оказалась значительно меньше и составила лишь 11 159 493…
Курсовая 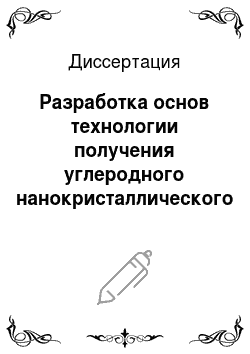
В последние годы для создания нанокомпозитов и УНМ привлекают процессы самоорганизации на основе методов неравновесной термодинамики. К таким методам относится термообработка, а также воздействие различных видов излучения. В случае полимера представляются актуальными процессы, происходящие при взаимодействии РЖ-излучения с веществом, из-за активного поглощения полимером излучения в этой области…
Диссертация 
Для подъема автомобиля по возможности пользуйтесь ромбическими или гидравлическими домкратами взамен штатного — они более устойчивы и надежны. Поднимая или опуская автомобиль (на домкрате или подъемнике), никогда не находитесь под ним. Предварительно убедитесь, что соответствующие силовые элементы кузова (усилители пола, пороги) достаточны прочны. Используйте для подъема автомобиля только…
Курсовая 
Из основных элементов очистного механизированного комплекса наиболее важную роль играет механизированная крепь. В течение выемочного цикла, при любой схеме добычи угля, оператор крепи выполняет в среднем от 184 до 370 рабочих операций, в зависимости от конструкции крепи, длины лавы, степени автоматизации систем управления, сложности горногеологических условий. Машинист комбайна, при тех же…
Диссертация 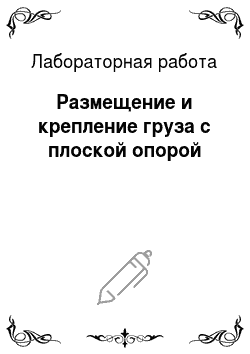
Продольные упорные бруски с одной стороны груза выглядят так: груз опирается на поперечно направленный брусок длиной, равной ширине пола вагона (2770 мм), в который можно забить максимум 28 гвоздей (в данной работе 20), и несколько продольно направленных брусков (в данной работе 4), которые подпирают поперечно направленный брусок. Зная ус и хс, по «Инструкции по перевозке негабаритных…
Лабораторная работа 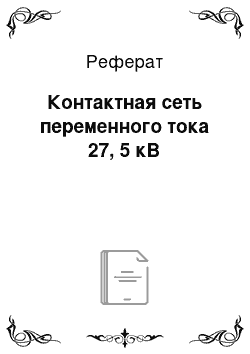
Наименование операции. |Содержание операций и технологические требования. — | |Не допускается эксплуатация проводов электрических| — |соединителей имеющих цвета побежалости, — | |свидетельствующие о нагреве проводов выше — |Проверка электрических |допустимого. Соединенные зажимы должны — |соединителей. |соответствовать сечениям соединяемых поводов. — | |Зажимы, имеющие цвета побежалости…
Реферат 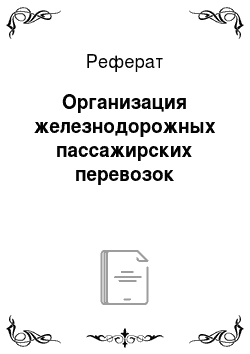
Для обеспечения правильного использования средств ж/д транспорта и соблюдения правил перевозок пассажиров и багажа управления дорог организуют контроль. Контролирующие лица проверяют: наличие у пассажиров проездных документов, обеспечение со стороны поездной бригады надлежащего содержания вагонов и качество обслуживания пассажиров, соблюдение пассажирами общественного порядка в поездах…
Реферат 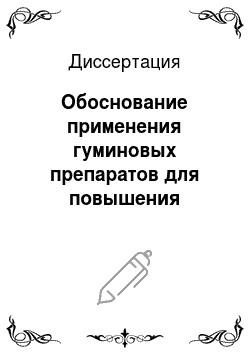
Гуминовые кислоты представляют собой особый класс биоорганических полимерных соединений, образующихся в окружающей среде в результате трансформации органических остатков. Благодаря исключительному многообразию составляющих фрагментов и функциональных группировок, они обладают широким, спектром свойств, что позволяет применять их в самых различных технологических сферах, в частности, для создания…
Диссертация 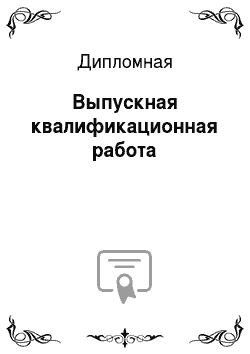
П/п Статьи расходов Сумма расходов, руб. 1 Материальные расходы 304 861 1.1 Основные и вспомогательные материалы 144 900 1.2 Запасные части для ремонта технологического оборудования и транспортных средств 1682 1.3 Малоценные и быстроизнашивающиеся предметы 900 1.4 Топливо, вода и энергия всех видов 143 688 1.5 Работы и услуги производственного характера, выполняемые сторонними организациями 500…
Дипломная