Эффективные способы переработки сероводорода на нефтеперерабатывающих заводах (производство серной кислоты, элементной серы и др.)
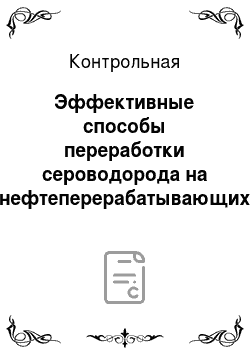
Крупнейшим потребителем серной кислоты является производство минеральных удобрений: суперфосфата, сульфата аммония и др. многие кислоты (например, фосфорная, уксусная, соляная) и соли производятся в значительной части при помощи серной кислоты. Серная кислота широко применяется в производстве цветных и редких металлов. В металлообрабатывающей промышленности серную кислоту или ее соли применяют… Читать ещё >
Эффективные способы переработки сероводорода на нефтеперерабатывающих заводах (производство серной кислоты, элементной серы и др.) (реферат, курсовая, диплом, контрольная)
МИНИСТЕРСТВО ОБРАЗОВАНИЯ РЕСПУБЛИКИ БЕЛАРУСЬ УЧРЕЖДЕНИЕ ОБРАЗОВАНИЯ
" ПОЛОЦКИЙ ГОСУДАРСТВЕННЫЙ УНИВЕРСИТЕТ"
Кафедра химии и ТПНГ Контрольная работа По дисциплине «Промышленная экология»
Эффективные способы переработки сероводорода на НПЗ (производство серной кислоты, элементной серы и др.)
Новополоцк
- 1. Свойства серной кислоты
- 2. Применение серной кислоты
- 3. Сырьевая база производства серной кислоты
- 4. Способы производства серной кислоты
- 5. Функциональная схема производства серной кислоты
- 5.1 Обжиг серосодержащего сырья
- 5.2 Промывка газа после обжига
- 5.3 Окисление диоксида серы
- 5.4 Абсорбция триоксида серы
- 5.5 Система двойного контактирования и двойной абсорбции (ДК/ДА)
- 6. Технология получения серной кислоты из влажного газа WSA и SNOX™ — контроль за выбросами оксидов серы и азота
- 6.1 Фундаментальные исследования
- 6.2 Разработка и оптимизация технологии
- 6.3 Технология SNOX™
- 7.Производство серы методом Клауса
серный кислота выброс оксид
1. Свойства серной кислоты
Безводная серная кислота (моногидрат) представляет собой тяжелую маслянистую жидкость, которая смешивается с водой во всех соотношениях с выделением большого количества тепла. Плотность при 0 °C равна 1,85 г/см3. Она кипит при 296 °C и замерзает при — 10 °C. Серной кислотой называют не только моногидрат, но и водные растворы его (), а также растворы трехокиси серы в моногидрате (), называемые олеумом. Олеум на воздухе «дымит» вследствие десорбции из него. Чистая серная кислота бесцветна, техническая окрашена примесями в темный цвет.
Физические свойства серной кислоты, такие, как плотность, температура кристаллизации, температура кипения, зависят от ее состава. На рис. 1 представлена диаграмма кристаллизации системы. Максимумы в ней отвечают составу соединений или, наличие минимумов объясняется тем, что температура кристаллизации смесей двух веществ ниже температуры кристаллизации каждого из них.
Рис. 1 Температура кристаллизации серной кислоты
Безводная 100%-ная серная кислота имеет сравнительно высокую температуру кристаллизации 10,7 °С. Чтобы уменьшить возможность замерзания товарного продукта при перевозке и хранении, концентрацию технической серной кислоты выбирают такой, чтобы она имела достаточно низкую температуру кристаллизации. Промышленность выпускает три вида товарной серной кислоты.
Концентрация | Температура кристаллизации, °С | ||
Башенная кислота | 75% | — 29,5 | |
Контактная кислота | 92,5% | — 22,0 | |
Олеум | 20% своб. | + 2,0 | |
Серная кислота весьма активна. Она растворяет окислы металлов и большинство чистых металлов;вытесняет при повышенной температуре все другие кислоты из солей. Особенно жадно серная кислота соединяется с водой благодаря способности давать гидраты. Она отнимает воду от других кислот, от кристаллогидратов солей и даже кислородных производных углеводородов, которые содержат не воду таковую, а водород и кислород в сочетании Н: О = 2. дерево и другие растительные и животные ткани, содержащие целлюлозу, крахмал и сахар, разрушаются в концентрированной серной кислоте; вода связывается с кислотой и от ткани остается лишь мелкодисперсный углерод. В разбавленной кислоте целлюлоза и крахмал распадаются с образованием сахаров. При попадании на кожу человека концентрированная серная кислота вызывает ожоги.
2. Применение серной кислоты
Высокая активность серной кислоты в сочетании со сравнительно небольшой стоимостью производства предопределили громадные масштабы и чрезвычайное разнообразие ее применения (рис. 2). Трудно найти такую отрасль, в которой не потреблялась в тех или иных количествах серная кислота или произведенные из нее продукты.
Рис. 2 Применение серной кислоты
Крупнейшим потребителем серной кислоты является производство минеральных удобрений: суперфосфата, сульфата аммония и др. многие кислоты (например, фосфорная, уксусная, соляная) и соли производятся в значительной части при помощи серной кислоты. Серная кислота широко применяется в производстве цветных и редких металлов. В металлообрабатывающей промышленности серную кислоту или ее соли применяют для травления стальных изделий перед их окраской, лужением, никелированием, хромированием и т. п. значительные количества серной кислоты затрачиваются на очистку нефтепродуктов. Получение ряда красителей (для тканей), лаков и красок (для зданий и машин), лекарственных веществ и некоторых пластических масс также связано с применением серной кислоты. При помощи серной кислоты производятся этиловый и другие спирты, некоторые эфиры, синтетические моющие средства, ряд ядохимикатов для борьбы с вредителями сельского хозяйства и сорными травами. Разбавленные растворы серн6ой кислоты и ее солей применяют в производстве искусственного шелка, в текстильной промышленности для обработки волокна или тканей перед их крашением, а также в других отраслях легкой промышленности. В пищевой промышленности серная кислота применяется при получении крахмала, патоки и ряда других продуктов. Транспорт использует свинцовые сернокислотные аккумуляторы. Серную кислоту используют для осушки газов и при концентрировании кислот. Наконец, серную кислоту применяют в процессах нитрования и при производстве большей части взрывчатых веществ.
Рис. 3 Температура кипения серной кислоты при атмосферном давлении | При нитровании, а также в производстве этилового спирта из этилена, при концентрировании азотной кислоты и в ряде других процессов применяют кислоту концентрацией от 92 до 98%, а выводят из процесса разбавленную 50 — 80%-ную кислоту. Такую кислоту концентрируют выпариванием воды, при этом используют диаграмму, приведенную на рис. 15.3. | |
3. Сырьевая база производства серной кислоты
Сырьевая база производства серной кислоты — серосодержащие соединения, из которых можно получить диоксид серы. В промышленности около 80% серной кислоты получают из природной серы и железного (серного) колчедана. Серный колчедан состоит из минерала пирита и примесей. Чистый пирит () содержит 53,5% серы и 46,5% железа. Содержание серы в серном колчедане может колебаться от 35 до 50%. Значительное место занимают отходящие газы цветной металлургии, получаемые при обжиге сульфидов цветных металлов и содержащие диоксид серы. Некоторые производства используют как сырье сероводород, образующийся при очистке нефтепродуктов от серы.
4. Способы производства серной кислоты
В настоящее время серная кислота производится двумя способами: нитрозным, существующим более 20 лет, и контактным, освоенным в промышленности в конце XIX и начале XX в. Контактный способ вытесняет нитрозный (башенный). Первой стадией сернокислотного производства по любому методу является получение двуокиси серы при сжигании сернистого сырья. После очистки двуокиси серы (особенно в контактном методе) ее окисляют до трехокиси серы, которая соединяется с водой с получением серной кислоты. Окисление в в обычных условиях протекает крайне медленно. Для ускорения процесса применяют катализаторы.
В контактном методе производства серной кислоты окисление двуокиси серы в трехокись осуществляется на твердых контактных массах. Благодаря усовершенствованию контактного способа производства себестоимость более чистой и высококонцентрированной контактной серной кислоты лишь незначительно выше, чем башенной. Поэтому строятся лишь контактные цехи. В настоящее время свыше 80% всей кислоты производится контактным способом.
В нитрозном способе катализатором служат окислы азота. Окисление происходит в основном в жидкой фазе и осуществляется в башнях с насадкой. Поэтому нитрозный способ по аппаратурному признаку называют башенным. Сущность башенного способа заключается в том, что полученная при сжигании сернистого сырья двуокись серы, содержащая примерно 9% и 9−10%, очищается от частиц колчеданного огарка и поступает в башенную систему, состоящую из нескольких (четырех — семи) башен с насадкой. Башни с насадкой работают по принципу идеального вытеснения при политермическом режиме. Температура газа на входе в первую башню около 350 °C. В башнях протекает ряд абсорбционно-десорбционных процессов, осложненных химическими превращениями. В первх двух — трех башнях насадка орошается нитрозой, в которой растворенные окислы азота химически связаны в виде нитрозилсерной кислоты. При высокой температуре нитрозилсерная кислота гидролизуется по уравнению:
. | (1) | |
Двуокись серы абсорбируется водой и образует сернистую кислоту
(2) | ||
последняя реагирует с окислами азота в жидкой фазе:
. | (3) | |
Частично может окисляться в газовой фазе:
(4) | ||
абсорбируясь водой, также дает серную кислоту:
. | (5) | |
Окись азота десорбируется в газовую фазу и окисляется до двуокиси азота кислородом воздуха:
. | (6) | |
Окислы азота поглощается серной кислотой в последующих трех — четырех башнях по реакции, обратной уравнению 15.1. Для этого в башни подают охлажденную серную кислоту с малым содержанием нитрозы, вытекающую из первых башен. При абсорбции окислов получается нитрозилсерная кислота, участвующая в процессе. Таким образом, окислы азота совершают кругооборот и теоретически не должны расходоваться. На практике же из-за неполноты абсорбции имеются потери окислов азота. расход окислов азота в пересчете на составляет 12−20 кг на тонну моногидрата. Нитрозным способом получают загрязненную примесями и разбавленную 75−77%-ную серную кислоту, которая используется в основном для производства минеральных удобрений.
5. Функциональная схема производства серной кислоты
Химическая схема включает в себя реакции:
1) обжиг серного колчедана | ||
горение серы | ||
горение сероводорода | ; | |
2) окисление диоксида серы | ; | |
3) абсорбция триоксида серы | . | |
Если исходные вещества (сырье) содержат примеси, то функциональная схема (рис. 15.4) включает в себя стадию очистки газа после обжига. Первая стадия — обжиг (горение) — специфична для каждого вида сырья, и далее она будет рассмотрена для колчедана и серы как наиболее распространенных исходных веществ. Стадии окисления и абсорбции в основном одинаковы в разных способах получения серной кислоты. Последовательное рассмотрение указанных стадий (подсистем ХТС производства серной кислоты) проведем с позиций принципиальных технологических, аппаратурных и режимных их решений.
Рис. 4 Функциональные схемы производства серной кислоты из серы (а) и серного колчедана (б) 1 — обжиг серосодержащего сырья; 2 — очистка и промывка обжигового газа; 3 — окисление; 4 — абсорбция
5.1 Обжиг серосодержащего сырья
Обжиг колчедана (пирита) является сложным физико-химическим процессом и включает в себя ряд последовательно или одновременно протекающих реакций:
термическая диссоциация | ; | |
газофазное горение серы | ; | |
горение пирротина | . | |
Суммарная реакция:
, | (7) | |
При небольшом избытке или недостатке кислорода образуется смешанный оксид железа:
.
Химические реакции практически необратимы и сильно экзотермичны.
Если в качестве сырья используется (нефтепереработка), то газофазное горение имеет вид химической реакции:
т.е. практически необратима, экзотермична и идет с уменьшением объема.
Термическое разложение пирита начинается уже при температуре около 200 °C и одновременно воспламеняется сера. При температурах выше 680 °C интенсивно протекают все три реакции. В промышленности обжиг ведут при 850−900 °С. Лимитирующей стадией процесса становится массоперенос продуктов разложения в газовую фазу и окислителя к месту реакции. При этих же температурах твердый компонент размягчается, что способствует слипанию частиц. Эти факторы определяют способ проведения процесса и тип реактора.
Первоначально использовали полочный реактор (камерная печь) (рис. 5, а). Колчедан непрерывно поступает сверху на полки, а воздух снизу проходит через неподвижные слои. Естественно, колчедан — кусковой (тонко измельченный создавал бы значительное гидравлическое сопротивление и мог легко слипаться, что создавало бы неоднородное горение). Обжиг — непрерывный процесс, твердый материал передвигается специальными гребками, вращающимися на валу, расположенном по оси аппарата. Лопатки гребков перемещают куски колчедана по тарелкам сверху вниз поочередно от оси аппарата к его стенкам и обратно, как показано на рисунке стрелками. Такое перемешивание предотвращает слипание частиц. Огарок непрерывно выводится с низа реактора. Реактор обеспечивает интенсивность процесса, измеряемую количеством колчедана, проходящего через единицу сечения реактора, — не более 200 кг/(м2· ч). В таком реакторе движущиеся скребки в высокотемпературной зоне усложняют его конструкцию, создается неодинаковый температурный режим по полкам, трудно организовать отвод тепла из зоны реакции. Трудности теплосъема не позволяют получить обжиговый газ с концентрацией более 8−9%. Основное ограничение — невозможность использования мелких частиц, в то время как для гетерогенного процесса основной способ ускорения скорости превращения — дробление частиц.
Рис. 5 Реакторы обжига колчедана
аполочный (1 — корпус, 2 — полки для колчедана, 3 — вращающиеся скребки, 4 — ось привода скребков); б — печь кипящего слоя (1 — корпус, 2 — теплообменник). Стрелки внутри аппаратов — движение твердого колчедана в реакторах.
Мелкие частицы можно перерабатывать в кипящем (псевдоожиженном) слое, что реализовано в печах КС — кипящего слоя (рис. 15.5, б). Пылевидный колчедан подается через питатель в реактор. Окислитель (воздух) подается снизу через распределительную решетку со скоростью, достаточной для взвешивания твердых частиц. Их витание в слое предотвращает слипание и способствует хорошему контакту их с газом, выравнивает температурное поле по всему слою, обеспечивает подвижность твердого материала и его переток в выходной патрубок для вывода продукта из реактора. В таком слое подвижных частиц можно расположить теплообменные элементы. коэффициент теплоотдачи от псевдоожиженного слоя сравним с коэффициентом теплоотдачи от кипящей жидкости, и тем самым обеспечены эффективные теплоотвод из зоны реакции, управление его температурным режимом и использование тепла реакции. Интенсивность процесса повышается до 1000 кг/(м2· ч), а концентрация в обжиговом газе — до 13−15%. Основной недостаток печей КС — повышенная запыленность обжигового газа из-за механической эрозии подвижных твердых частиц. Это требует более тщательной очистки газа от пыли — в циклоне и электрофильтре. Подсистема обжига колчедана представлена технологической схемой, показанной на рис. 6.
Рис. 6 Технологическая схема обжига колчедана
1 — тарельчатый питатель; 2 — печь (реактор) кипящего слоя; 3 — котел-утилизатор; 4 — циклон; 5 — электрофильтр
Как указывалось ранее, в качестве сырья может использоваться сера (самородная сераказывалось ранее в качестве сырья может использоваться сера ()й на рис. 15.6. тдачи от кипящей жидкости, и тем самым обеспече). Сера — легкоплавкое вещество: температура плавления 113 °C. Перед сжиганием ее расплавляют, используя пар, получаемый при утилизации теплоты ее горения. Расплавленная сера отстаивается и фильтруется для удаления имеющихся в природном сырье примесей и насосом подается в печь сжигания. Сера горит в основном в парофазном состоянии. Чтобы обеспечить ее быстрое испарение, необходимо ее диспергировать в потоке воздуха. Для этого используют форсуночные и циклонные печи.
Рис. 7 Зависимость адиабатической температуры горения серы Т от концентрации образующегося | Горение протекает адиабатически, и температура зависит от концентрации образующегося (рис. 15.7). Теплота горения серы 11 325 кДж/кг, и температура в печи — более 1000 °C. Этих условий достаточно для испарения жидкой серы (теплота испарения 288 кДж/кг, температура кипения 445 °С). Печь сжигания работает в комплексе со вспомогательным оборудованием для плавления и фильтрования серы и котлом-утилизатором для использования тепла реакции (рис. 8). | |
Рис. 8 Технологическая схема сжигания серы
1 — фильтр серы; 2 — сборник жидкой серы; 3 — печь сжигания; 4 — котел-утилизатор
При горении серы по реакции часть кислорода эквимолярно переходит в диоксид серы, и потому суммарная концентрация и постоянна и равна концентрации кислорода в исходном газе (), так что при сжигании серы в воздухе .
Газ от сжигания серы богаче кислородом, чем от сжигания колчедана.
5.2 Промывка газа после обжига
Газы обжига колчедана содержат в виде примесей соединения фтора, селена, теллура, мышьяка и некоторые другие, образующиеся из примесей в сырье. Естественная влага сырья также переходит в газ. При горении образуется некоторое количество и, возможно, оксиды азота. Эти примеси приводят или к коррозии аппаратуры, или к отравлению катализатора, а также сказываются на качестве продукта — серной кислоте. Их удаляют в промывном отделении, упрощенная схема которого приведена на рис. 9.
Рис. 9 Схема промывного отделения производства серной кислоты
1, 2 — промывные башни; 3 — мокрый фильтр; 4 — сушильная башня
5.3 Окисление диоксида серы
Реакция
(8) | ||
является обратимой, экзотермической, протекает на катализаторе с уменьшением объема. Тепловой эффект реакции при температуре 500 °C кДж/моль. Константа равновесия [атм-0,5] зависит от температуры и в интервале 400−700 °С равна
. | (9) | |
Согласно закону действующих масс, при равновесии
(10) | ||
где, , — парциальные давления соответствующих компонентов в состоянии равновесия, атм.
Равновесную степень превращения диоксида серы получим из стехиометрического уравнения (8) и условия равновесия (10):
. | (11) | |
Выражение показывает относительное изменение (уменьшение) объема реакционной смеси. Уравнение 15.11 определяет в неявном виде и решается подбором. Необходимые степени превращения (около 99%) достигаются при температурах 400−420 °С. Давление не сильно влияет на, поэтому в промышленности процесс проводят при давлении, близком к атмосферному.
Катализаторы окисления готовят на основе оксида ванадия () с добавкой щелочных металлов, нанесенных на оксид кремния. Скорость реакции описывается уравнением Борескова-Иванова:
(12) | ||
где — константа скорости реакции;
=0,8 — константа;
, — парциальные давления соответствующих компонентов, атм.
Температурные границы и значение в них для разных катализаторов могут различаться. Для катализаторов ИК-1−6 и СВД кДж/моль при К. это — низкотемпературные катализаторы. Активность промышленных катализаторов при температуре ниже 680 К весьма мала, а выше 880 К происходит их термическая дезактивация. Поэтому рабочий интервал температур эксплуатации большинства катализаторов — 580−880 К, а степень превращения в реакторе, определяемая нижней границей этого интервала, составляет 98%.
Рис. 11 Схема реактора окисления
1 — слой катализатора; 2 — промежуточные теплообменники; 3 — смеситель; 4 — внешний теплообменник; Хг — ввод холодного газа
Начальная концентрация перерабатываемого газа выбирается так, чтобы режим процесса находился в пределах рабочих температур катализатора. Большое значение при К приводит к резкому уменьшению скорости реакции с понижением температуры. Чтобы адиабатический процесс в первом слое мог интенсивно развиваться, начальная температура должна быть не ниже 713 К. Ее называют «температурой зажигания» (для низкотемпературных катализаторов она ниже). На диаграмме «» адиабатический процесс представлен прямой линией. Наклон ее определен величиной адиабатического разогрева. Для окисления приближенно град на 1%. Чем больше (или начальная концентрация —), тем больше разогрев. Процесс может развиваться до равновесия, и максимальная (равновесная) температура не должна превышать допустимую. На рис. 10 это соответствует начальной концентрации 7−8%. Низкотемпературный катализатор позволяет поднять концентрацию до 9−10%. Температуры в остальных слоях определяют из оптимизации режима реактора.
5.4 Абсорбция триоксида серы
Абсорбция триоксида серы — последняя стадия процесса, в которой образуется серная кислота. Взаимодействие с
протекает достаточно интенсивно как в жидкой, так и газообразной (паровой) фазах. Кроме того, может растворять в себе, образуя олеум. Этот продукт удобен для транспортировки, поскольку он не вызывает коррозии даже обычных сталей. Растворы серной кислоты чрезвычайно агрессивны. Олеум является основным продуктом сернокислотного производства.
Равновесие «газ — жидкость» для системы «» представлено на рис. 3. Особенностью этой системы является то, что в широком интервале концентраций раствора в паровой фазе присутствуют почти чистые пары воды (левая часть графика), а над олеумом (раствор в) в газовой фазе преобладает (правая часть графика). одинаковый состав жидкой и паровой фаз (азеотропная точка) будет при концентрации серной кислоты 98,3%. Если поглощать раствором с меньшей концентрацией, то реакция 5 будет протекать и в паровой фазе — будет образовываться туман серной кислоты, который уйдет из абсорбера с газовой фазой. А это — и потери продукта, и коррозия аппаратуры, и выбросы в атмосферу. Если абсорбировать олеумом, то поглощение будет неполным.
Из этих свойств следует двухстадийная (двухбашенная) схема абсорбции (рис.12). Газ, содержащий, после реактора проходит последовательно олеумный 1 и моногидратный 2 абсорберы. Другой компонент реакции () подается противотоком в моногидратный абсорбер. За счет интенсивности циркуляции жидкости (абсорбента) в ней можно поддерживать близкую к оптимальной концентрацию — 98,3% (увеличение концентрации за проход жидкости не более 1−1,5%). Техническое название такой кислоты — моногидрат, откуда и название абсорбера. Концентрационные условия абсорбции обеспечивают полное поглощение и минимальное образование сернокислотн6ого тумана. Кислота из моногидратного абсорбера поступает в олеумный. В нем циркулирует 20% раствор в, который частично отбирается как конечный продукт — олеум. Кислота из предыдущего абсорбера — моногидрат — также может быть продуктом.
Образование серной кислоты и абсорбция триоксида серы — экзотермические процессы. Их тепло снимается в оросительных теплообменниках 3 на линии циркуляции жидкости в абсорберах. При температуре менее 100 °C поглощается практически на 100%. Диоксид серы практически не абсорбируется.
Рис. 12 Схема отделения абсорбции в производстве серной кислоты
1 — олеумный абсорбер; 2 — моногидратный абсорбер; 3 — холодильники; 4 — сборники кислоты; 5 — брызгоотделители
5.5 Система двойного контактирования и двойной абсорбции (ДК/ДА)
Несмотря на довольно большую степень превращения — 98%, мощные сернокислотные системы, производящие до 540 т продукта в сутки, ежечасно выбрасывают в атмосферу более 300 кг диоксида серы. Исходя из данных по равновесию реакции окисления, увеличить степень превращения можно снижением температуры в последних слоях ниже 610 К или повышением давления более 1,2 МПа. Возможность снижения температуры ограничена активностью имеющихся катализаторов, повышение давления усложняет инженерное оформление процесса, и поэтому эти методы пока не получили промышленного применения.
Эффективным способом увеличения степени превращения в обратимой реакции является удаление ее продукта. Технологическая схема такого способа показана на рис. 13. На первой стадии окисления использован трехслойный реактор 1. Концентрация в поступающем газе — 9,5−10,5%. Степень превращения на выходе из реактора 90−95%. Промежуточная абсорбция включает олеумный 2 и моногидратный 3 абсорберы. После них газ содержит только 0,6−1%. Для его нагрева до температуры реакции (690−695 К) используют теплообменник после второго слоя реактора 1. Реакторы первой и второй ступени окисления конструктивно объединены в одном корпусе. Степень превращения оставшегося составляет примерно 95%, общая степень превращения 99,6−99,8%. Сравним: если бы не было промежуточной абсорбции, то степень превращения оставшихся 1−0,6% в присутствии не превысила бы 50%. Небольшое количество образовавшегося полностью поглощается во втором моногидратном абсорбере 3.
Как видим, количество непревращенного (и, следовательно, выбросов в атмосферу) в системе ДК/ДА уменьшается почти в 10 раз по сравнению с системой однократного контактирования. Но для этого приходится поверхность теплообменников увеличивать в 1,5−1,7 раза.
Рис. 13 Технологическая схема стадий контактирования и абсорбции в системе «двойное контактирование — двойная абсорбция»
I, III — первая и вторая ступени окисления; II, IV — первая и вторая системы абсорбции водой; 1 — реактор (первая и вторая ступени окисления, расположенные в одном корпусе, показаны отдельно); 2 — олеумный абсорбер; 3 — моногидратный абсорбер; 4 — выносные теплообменники реактора; 5 — холодильники кислоты
6. Технология получения серной кислоты из влажного газа WSA и SNOX™ — контроль за выбросами оксидов серы и азота
Разработка технологии WSA компании Топсе для удаления соединений серы из дымовых газов с производством серной кислоты началась в конце 70-х гг. Технология WSA создана на основе обширного опыта Топсе в сернокислотной промышленности и неизменной решимости двигаться дальше и дальше в развитии катализаторов и технологических процессов. Основными областями исследований стали окисление SO2 на сернокислотных катализаторах и процесс конденсации кислоты.
6.1 Фундаментальные исследования
Возможность конденсировать пары серной кислоты для получения концентрированной серной кислоты без выброса кислотного тумана является уникальной особенностью технологии WSA, что было достигнуто на основании фундаментальных экспериментальных и теоретических работ, выполненных в компании Топсе.
Во время охлаждения содержащихся в газовой фазе паров серной кислоты самопроизвольное гомогенное формирование центров конденсации, гетерогенная конденсация и конденсация на стенках происходят одновременно. Для разработки и совершенствования конденсатора WSA в лабораториях компании Топсе проводятся фундаментальные исследования в отношении этих принципиально важных механизмов конденсации.
Рис. 4. Технология стеклянных трубок, разработанная Топсе, используется в WSA для конденсации паров серной кислоты
6.2 Разработка и оптимизация технологии
Испытания на уровне пилотных и промышленных установок наряду с детальным моделированием конденсатора WSA используются для изучения влияния конструкции и режима эксплуатации конденсатора на его рабочие показатели с целью определения критериев проектирования и контроля технологического процесса.
Еще одной приоритетной областью наших технических разработок является усовершенствование технологии стеклянных трубок WSA и постоянное повышение качества конструкционных материалов. Последняя задача требует применения нашего опыта в области испытания материалов для сложных условий работы сернокислотных установок.
Для того, чтобы полностью задействовать потенциал технологии WSA, мы используем инновационные методы при создании технологических схем при внедрении собственных расчётных инструментов Топсе для оптимального решения различных промышленных задач. Одним из стимулов такого развития является рост внимания к энергопотреблению и выбросам CO2 во всем мире, что требует максимальной рекуперации тепла.
6.3 Технология SNOX™
Для удаления из дымовых газов оксидов серы и азота компания Топсе разработала технологию SNOX™, объединяющую технологию WSA с удалением оксидов азота по технологии СКВ, что обеспечивает оптимальную интеграцию для электроэнергетики.
7. Производство серы методом Клауса
ООО «Премиум Инжиниринг» может предложить четыре основных способа процесса Клауса для производства элементарной серы из кислых компонентов природного газа и нефтезаводских газов:
· Прямоточный (пламенный)
· Разветвленный
· Разветвленный с подогревом кислого газа и воздуха
· Прямое окисление
1. Прямоточный процесс Клауса (пламенный способ) применяют при объемных долях сероводородав кислых газах выше 50% и углеводородов менее 2%. При этом весь кислый газ подается на сжигание в печь-реактор термической ступени установки Клауса, выполненный в одном корпусе с котлом-утилизатором. В топке печи-реактора температура достигает 1100−1300°С и выход серы до 70%. Дальнейшее превращение сероводорода в серу осуществляется в две-три ступени на катализаторах при температуре 220−260°С. После каждой ступени пары образовавшейся серы конденсируются в поверхностных конденсаторах. Тепло, выделяющееся при горении сероводорода и конденсации паров серы, используется для получения пара высокого и низкого давления. Выход серы в этом процессе достигает 96−97%.
2. При низкой объемной доле сероводорода в кислых газах (30−50%) и объемной долеуглеводородов до 2% применяют разветвленную схему процесса Клауса (треть-две трети). По этой схеме одна треть кислого газа подвергается сжиганию с получением сернистого ангидрида, а две трети потока кислого газа поступают на каталитическкую ступень, миную печь-реактор. Серу получают в каталитических ступенях процесса при взаимодействии сернистого ангидрида с сероводородом, содержащимся в остальной части (2/3) исходного кислого газа. Выход серы составляет 94−95%.
3. При объемной доле сероводорода в кислом газе 15−30%, когда при использовании схемы треть-две трети минимально допустимая температура в топке печи-реактора (930°С) не достигается, используют схему с предварительным подогревом кислого газа или воздуха.
4. При объемной доле сероводорода в кислом газе 10−15% применяют схему прямого окисления, в которой отсутствует высокотемпературная стадия окисления (сжигания) газа. Кислый газ смешивается со стехиометрическим количеством воздуха и подается сразу на каталитическую ступень конверсии. Выход серы достигает 86%.
Для достижения степени извлечения серы 99,0−99,7% используются три группы методов доочистки отходящих газов процесса Клауса:
· Процессы, основанные на продолжении реакции Клауса, т. е. на превращении H2S и SO2 в серу на твердом или жидком катализаторе.
· Процессы, основанные на восстановлении всех сернистых соединений в сероводород с последующим его извлечением.
· Процессы, основанные на окислении всех сернистых соединений до SO2 или до элементарной серы с последующим их извлечением.