Привод ленточного конвейера
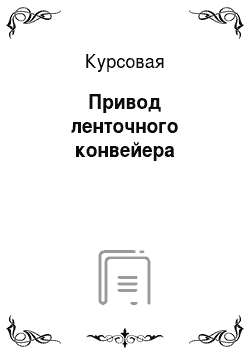
Для стандартизованных элементов привода машин требования к устойчивости при внешних воздействиях установлены в соответствующей нормативно-технической документации (ГОСТах). При проведении расчетов условия эксплуатации учитываются путем использования рекомендованных значений различных коэффициентов, численные значения которых принимаются из справочной литературы. Существенно повысить ресурс вновь… Читать ещё >
Привод ленточного конвейера (реферат, курсовая, диплом, контрольная)
Министерство сельского хозяйства Российской Федерации Казанский Государственный Аграрный Университет ПОЯСНИТЕЛЬНАЯ ЗАПИСКА к курсовому проекту по деталям машин и конструированию на тему: Привод ленточного конвейера ПЛК.062.00.00 ПЗ Казань
Содержание ВВЕДЕНИЕ ТЕХНИЧЕСКОЕ ЗАДАНИЕ
1. КЛАССИФИКАЦИЯ ПРИВОДОВ МАШИН
2. условия эксплуатации, ресурс приводного устройства
3. КИНЕМАТИЧЕСКИЙ РАСЧЕТ ПРИВОДА
3.1 Выбор электродвигателя
3.2 Передаточное отношение и разбивка его по ступеням
3.3 Расчёт числа оборотов валов
3.4 Расчёт вращающих моментов на валах
4. ПРОЕКТНЫЙ РАСЧЁТ ЗАКРЫТОЙ ЗУБЧАТОЙ ПЕРЕДАЧИ
4.1 Определение межосевого расстояния
4.2 Определение количества зубьев
4.3 Определение нормального модуля
4.4 Определение диаметров колёс
5. ПРЕДВАРИТЕЛЬНЫЙ РАСЧЕТ ВАЛОВ
6. НАГРУЗКИ ВАЛОВ РЕДУКТОРА
7. РАСЧЕТНАЯ СХЕМА ВАЛОВ РЕДУКТОРА
7.1 Предварительный выбор подшипников
7.2 Исходные данные для построения эпюр
7.3 Построение эпюр изгибающих и крутящих моментов тихоходного вала
7.4 Построение эпюр изгибающих и крутящих моментов быстроходного вала
8. РАСЧЕТ И ПОДБОР ПОДШИПНИКОВ
9. проверочный расчет шпонок
10. УТОЧНЕННЫЙ РАСЧЕТ ВАЛОВ
11. ВЫБОР ПОСАДОК
12. СМАЗКА РЕДУКТОРА
13. ТЕХНОЛОГИЯ СБОРКИ РЕДУКТОРА СПИСОК ИСПОЛЬЗОВАННОЙ ЛИТЕРАТУРЫ
Значительная часть потребностей человека связана с техникой. Этим объясняется необходимость грамотного обращения при оказании услуг с механизмами, приборами, аппаратами и сооружениями, являющимися составной частью систем сервиса.
Большинство этих устройств входит в состав машин, которые преобразуют энергию, материал и информацию с целью облегчения физического и умственного труда человека. Поэтому, изучение элементов этих машин, их взаимодействия в рамках курсовой работы по дисциплине «Механика» позволяет охватить существующий спектр вопросов, возникающих на практике при использовании современной техники.
Курсовая работа оформлена в виде расчетно-пояснительной записки общим объемом 31 страниц машинописного текста, выполненной на листах формата А4, в соответствии с ЕСКД и графической части (лист формата А4×4), которая является Приложением, А к расчетно-пояснительной записке.
Курсовая работа выполнялась по индивидуальному заданию по рекомендациям, изложенным в учебно-методическом пособии [1], в соответствии с планом курсовой работы, который приведен в Приложении Б.
ТЕХНИЧЕСКОЕ ЗАДАНИЕ
Спроектировать привод ленточного конвейера с одноступенчатым горизонтальным цилиндрическим прямозубым редуктором.
Полезная сила, передаваемая лентой конвейера:
F=5,6кН.
D=0,16 м.
Скорость ленты: н=0.2 м/с
Долговечность привода 10 000ч.
Материал зубчатых колес 30ХГС.
Схема привода приведены на рисунке 1.
Рисунок 1-Схема привода
Необходимо разработать:
1. Сборочный чертеж редуктора.
2. Чертеж общего вида привода.
3. Рабочие чертежи:
· вала выходного;
· колеса зубчатого.
1. Классификация приводов машин
Классификация приводов машин производится по виду энергии, используемой для создания рабочего усилия или момента. В зависимости от типа, назначения и характера работы машины механизмы ее могут иметь в основном два вида привода: машинный и ручной. Машинный привод имеет следующие разновидности: электрический, от двигателя внутреннего сгорания, гидравлический, пневматический и, в настоящее время — реже, паровой. Кроме того, в ряде машин находит применение комбинированный привод, как, например, дизель электрический, электрогидравлический и электропневматический.
В современных машинах в основном применяется электрический привод, который имеет ряд преимуществ:
1) постоянная готовность к действию;
2) возможность установки самостоятельного электропривода к каждому механизму, что упрощает конструкцию и управление механизмами;
3) высокая экономичность;
4) легкость регулирования скорости в значительных пределах;
5) надежность работы предохранительных устройств;
6) возможность работы со значительными кратковременными перегрузками.
Определение рациональности применения различных типов приводов следует производить на основе анализа экономических и конструктивно-эксплуатационных показателей, из которых основными являются себестоимость транспортирования, энергетические показатели, надежность работы и независимость от действия условий окружающей среды, удобство управления, технологичность конструкции.
2. Условия эксплуатации, ресурс приводного устройства
Выбор элементов привода, материалов для их изготовления, значений различных коэффициентов при проведении расчетов и многое другое обуславливается условиями эксплуатации и предполагаемым сроком службы привода.
К условиям эксплуатации относятся различные производственные и климатические параметры, такие как: состав и концентрация пыли, влажность и температура воздуха в течение года, насыщение парами различных химических веществ, пожарои взрывобезопасность, характер действующих нагрузок (статических и динамических), вибрация, продолжительность безостановочной работы и сменность, частота включений, особенности монтажа и смазки элементов привода и многое другое.
Для стандартизованных элементов привода машин требования к устойчивости при внешних воздействиях установлены в соответствующей нормативно-технической документации (ГОСТах). При проведении расчетов условия эксплуатации учитываются путем использования рекомендованных значений различных коэффициентов, численные значения которых принимаются из справочной литературы.
Ресурс приводного устройства ограничивается ресурсом его наиболее слабого элемента. В связи с этим, при проведении расчетов необходимо определять срок службы проектируемой передачи или другого элемента привода.
Существенно повысить ресурс вновь разрабатываемого привода можно, используя принцип унификации и блочности, который заключается в применении стандартизованных (имеющих высокие технико-экономические показатели) узлов, соединенных между собой посредством легкоразъемных элементов.
3. Кинематический расчет привода
3.1Выбор электродвигателя
Определение мощности на рабочем органе
(3.1)
где Fполезная сила, передаваемое лентой конвейера, Н;
V — скорость ленты конвейера, м/с.
Определение мощности электродвигателя
(3.2)
где
— общий к.п.д. привода;
(3.3)
где змуфта — потери в муфте; принимаем зм = 0,99;
зопора1,опора2,опора3 — потери в подшипниках качения;
ззацепление — к.п.д. зубчатой цилиндрической передачи; принимаем
ззацепление = 0,97;
зцепная — к.п.д. цепной передачи; принимаем зцепная =0,915.
Расчёт мощности электродвигателя:
Исходя из данных расчёта мощности выбираем три электродвигателя [1]:
Таблица 3.1- Параметры электродвигателей привода
Марка электродвигателя | N. кВт | n, мин-1 | |
АИР 80А4 | 1.1 | ||
АИР 80В6 | 1.1 | ||
АИР 90LВ8 | 1.1 | ||
Определение частоты вращения рабочего органа
(3.4)
где Vскорость ленты, м/c;
Dдиаметр звездочки, м.
Диаметр звездочки определится:
Определение минимального и максимального передаточного числа заданного привода
(3.5)
(1.6)
Определение передаточного отношения от выбранных двигателей
(3.7)
где — частота вращения первого выбранного двигателя,;
— частота вращения рабочего органа, ;
(3.8)
где — частота вращения второго выбранного двигателя,;
(3.9)
где — частота вращения третьего выбранного двигателя,;
Из полученных расчётов принимаем трёхфазный асинхронный электродвигатель АИР 90LВ8, для которого: Nд=1,1 кВт, nд=695 об/мин
3.2 Передаточное отношение и разбивка его по ступеням
Общее передаточное отношение
(3.10)
— передаточное отношение цепной передачи.
Таблица 3.2 — Рекомендуемые передаточные числа
Тип передачи | Рекомендуемое передаточное число | ||
среднее | наибольшее | ||
Закрытая зубчатая передача | 3…6 | ||
Зубчатая открытая передача | 3…7 | ||
3.3 Расчёт числа оборотов валов
nд= n1=695 () — число оборотов входного (быстроходного) вала;
где nэл.двиг- частота вращения эл. двигателя, ;
n1 -частота вращения первого вала, ;
n2= n1/ U1, (3.11)
где n2 -частота вращения на втором валу, ;
n2=695/9,09=76,5 ().
n3= n2/ U2, (1.12)
где n3 -частота вращения на третьем валу, ;
n3=76,5/10=7,65 ().
3.4 Расчёт вращающих моментов на валах
(3.13)
где Fполезная сила, передаваемое лентой конвейера, Н;
— диаметр приводной звездочки, м;
— вращающий момент на рабочем органе, Нм;
Определение вращающего момента на третьем валу
(3.14)
Определение вращающего момента на втором валу
(3.15)
Определение вращающего момента на первом валу
(3.16)
— потери в зацеплении;
Таблица 3.3 — Результаты расчетов
Вал | n, мин-1 | M, Нм | М, Н мм | |
12,8 | ||||
76,5 | 110,5 | |||
7,65 | 984,8 | |||
4. Проектный расчёт закрытой зубчатой передачи
4.1 Определение межосевого расстояния
Межосевое расстояние определяем по формуле:
(4.1)
где КН =f (НВ) — коэффициент нагрузки, зависит от термообработки;
= коэффициент относительной ширины колеса к межосевому расстоянию;
— вращающий момент на втором валу, Нм;
U-передаточное отношение в зацеплении;
— предельное контактное напряжение, зависит от термообработки;
(4.2)
Sн — коэффициент безопасности для редукторов, зависит от термообработки;
(4.3)
Для проектирования не коррегированной передачи принимаем межосевое расстояние из нормального ряда a=200мм.
4.2 Определение количества зубьев
Определение суммарного числа зубьев
ZУ =2 а w / m; (4.4)
Подставляя значения в формулу получаем
ZУ = 2 *200 / 2 = 200.
Определение числа зубьев шестерни
Z1 = ZУ / (u +1); (4.5)
Подставляя суммарное число зубьев ZУ = 100 и передаточное число u = 5 получим
Z1 = 200/ (9,09 +1) = 19,82.
Назначаем Z1 = 20.
Определение числа зубьев колеса
Z2 = ZУ — Z1; (4.6)
Подставляя значения, получим
Z2 = 200−20 =180.
4.3 Определение нормального модуля
(4.5)
где амежосевое расстояние, мм;
По ГОСТ 9563–80 принимаем =2мм
4.4 Определение диаметров колёс
(4.6)
гдеуточнённый модуль зацепления;
— количество зубьев на первом колесе;
— угол наклона зубьев,;
(4.7)
проверка: (4.8)
гдеделительный диаметр первого колеса, мм;
— делительный диаметр второго колеса;
Таблица 4.1 — Геометрические размеры колес
Параметр | Геометрические зависимости | Числовые значения | |
Диаметры вершин зубьев dа1, dа2 | dа1 = d1 + 2 m dа2 = d2 + 2 m | dа1 = 40+4=44 мм dа2 = 360+4=364 мм | |
Диаметры впадин зубьев df1, df2 | df1, =d1-2,5m df2= d2 -2,5m | df1 =40−5=35мм df2=360−5=355мм | |
Ширина колеса b2 | b2 = ца * аw | b2=0,315*200=63мм. | |
Ширина шестерни b1 | b1 = b2 +5 мм | b1 = 67 мм | |
4.5 Расчет передачи на контактную прочность
Окружная скорость колеса:
(4.13)
гдеуточнённый делительный диаметр второго колеса, мм;
— частота оборотов на втором валу, ;
При данной скорости назначаем 8-ю степень точности.
При данной скорости выбираем
Коэффициент нагрузки для проверки контактных напряжений:
(4.14)
где — коэффициент, учитывающий неравномерность распределения нагрузки по ширине венца;
— динамический коэффициент, зависящий от окружной скорости колес и точности их изготовления;
— коэффициент, учитывающий неравномерность распределения нагрузки между зубьями;
Проверяем контактные напряжения:
(4.15)
гдеуточнённое межосевое расстояние, мм;
— уточнённое передаточное отношение;
— коэффициент нагрузки для проверки контактных напряжений;
— крутящий момент на втором валу, об/мин;
Определяем отклонение:
(4.14)
Т.к. расчётное напряжение ун меньше допускаемого [у]H в пределах 15%, то ранее принятые параметры передачи принимаем за окончательные.
5. ПРЕДВАРИТЕЛЬНЫЙ РАСЧЕТ ВАЛОВ
Ведущий вал: находим диаметр выходного конца при допускаемом напряжении по формуле:
(5.1)
где к — допустимые касательные напряжения при кручении
(к=20 — 25МПа);
Полученный диаметр согласуем с диаметром вала электродвигателя и со стандартной муфтой. Назначаем =28мм.
Рисунок 5.1 — Схема быстроходного вала с размерами Примем диаметр вала под подшипниками 35 мм. Шестерню выполняем за одно целое с валом.
Ведомый вал: Диаметр выходного конца при допускаемом напряжении по формуле:
(5.2)
где М2кр-крутящий момент на втором валу, Нм;
Принимаем диаметр вала под шестерню 42 мм.
Примем диаметр вала под подшипниками 55 мм.
Диаметр вала под зубчатым колесом: 60 мм.
Размеры ступиц колес:
(5.3)
Рисунок 5.2 — Схема тихоходного вала с размерами Толщина стенки редуктора:
Толщину стенки редуктора принимаем 6 мм.
Расстояние от боковых поверхностей элементов, вращающихся вместе с валом, до неподвижных наружных частей редуктора
6. НАГРУЗКИ ВАЛОВ РЕДУКТОРА
Консольные силы в зацепление цилиндрической закрытой передачи.
Окружные силы в зацеплении шестерни и колеса:
(6.1)
где М1в — крутящий момент на первом валу, Нм;
d1 — делительный диаметр первого колеса, мм.
Радиальные силы в зацеплении шестерни и колеса:
(6.2)
где — угол зацепления в цилиндрической косозубой закрытой передаче принят, в градусах (,);
— действительная величина угла наклона зубьев для косозубых передач, в градусах (в=0).
Консольные силы в шестерне открытой передачи на тихоходном валу, Н:
Окружное усилие Радиальное усилие Консольные силы в муфте на быстроходном валу, Н:
(6.4)
где — вращающий момент на валу быстроходной передачи, Нм;
7. РАСЧЕТНАЯ СХЕМА ВАЛОВ РЕДУКТОРА
7.1 Предварительный выбор подшипников
Выбираем подшипник для вала-шестерни:
Тип подшипника: радиальный шариковый однорядный легкой серии 207.
Данные подшипника:
d=35мм.
D=72мм.
В=17мм.
Выбираем подшипник для тихоходного колеса:
Тип подшипника: радиальный шариковый однорядный лёгкой серии 211.
Данные подшипника:
d=55мм.
D=100мм.
В=21мм.
7.2 Исходные данные для построения эпюр
Силовые факторы, Н:
на шестерне:
Делительный диаметр шестерни прямозубой передачи:
Расстояние между точками приложения реакций в опорах подшипников быстроходного вала :
где — ширина подшипника для быстроходного вала, в мм;
На колесе:
Делительный диаметр колеса косозубой передачи:
7.3 Построение эпюр изгибающих и крутящих моментов тихоходного вала
Плоскость YOZ (вертикальная). Учитываем усилие от зубчатой открытой передачи Fr1 =1,22кН.
Определяем реакции в опорах
УМА=0:
Или
Подставляя значения, получим
УМb = 0: или
Подставляя значения, получим кН.
УF (Y) = 0:
Строим эпюру изгибающих моментов Мy.
Участок АC:
Мy = Ya * Z,
Точка А: Z= 0, Мy = 0Нм.
Точка С: Z=a, Мy=Ya*a=0,98*70 =68,6Нм.
Участок DВ:
Мy = Fr1 *Z,
Точка D Z= 0, Мx = 0Нм.
Точка В: Z= c, Мx = 1.22*100 = 122Нм
Участок ВC:
Мy = Fr1 *(c+Z)+ Yb*Z,
очка B Z= 0, Мx = 122Нм.
Точка C: Z= b, Мx = 1,22*(100+70) — 1.98*70=68.6Нм
Плоскость XOZ (горизонтальная).
Учитываем усилие от зубчатой открытой передачи Ft =3,4кН.
Определяем реакции в опорах.
УМА=0:
Или
Подставляя значения, получим
УМb = 0: или
Подставляя значения, получим кН.
УF (Y) = 0:
Строим эпюру изгибающих моментов М x.
Участок АC:
Мx = Xa * Z,
Точка А: Z= 0, Мx = 0Нм.
Точка С: Z= a, Мx = Xa * a =2.75*70=192.5Нм.
Рисунок 3.1 — Расчетная схема и эпюры моментов тихоходного вала
Участок DВ:
Мx = Ft1 *Z,
Точка D Z= 0, Мx = 0Нм.
Точка В: Z= c, Мx = 3.4*100 =340Нм
Участок ВC:
Мx = Ft1 *(c+Z)+ Xb*Z,
очка B Z= 0, Мx = 340Нм.
Точка C: Z= b, Мx = - Ft1 *(c+b)+ Xb*b = 3.4(100+50)-5.5*70=192.5Нм
Строим эпюру крутящего момента Мк.
Определяем суммарные моменты;
7.4 Построение эпюр изгибающих и крутящих моментов быстроходного вала
Плоскость YOZ (вертикальная). Определяем реакции в опорах
Строим эпюру изгибающих моментов Мy.
Участок АC:
Мy = Ya * Z,
Точка А: Z= 0, Мy = 0Нм.
Точка С: Z=a, Мy=Ya*a=0,115*70 =8Нм.
Плоскость XOZ (горизонтальная).
Учитываем усилие от муфты FУ =0,45кН.
Определяем реакции в опорах.
УМА=0:
Или
Подставляя значения, получим
УМb = 0: или
Подставляя значения, получим кН.
УF (Y) = 0:
Строим эпюру изгибающих моментов М x.
Участок АC:
Мx = Xa * Z,
Точка А: Z= 0, Мx = 0Нм.
Точка С: Z= a, Мx = Xa * a =0,64*70=44,8Нм.
Участок DВ:
Мx = -FУ *Z,
Точка D Z= 0, Мx = 0Нм.
Точка В: Z= c, Мx = -0,64*100 = -64Нм
Участок ВC:
Мx = - FУ *(c+Z)+ Xb*Z,
Точка B Z= 0, Мx = - FУ *c =-64Нм.
Точка C: Z= b, Мx = - FУ *(c+b)+ Xb*b = - 0,64(100+70)+0,45*70=-77,3Нм
Строим эпюру крутящего момента Мк.
Определяем суммарные моменты;
Рисунок 3.2 — Расчетная схема и эпюры моментов быстроходного вала
8. РАСЧЕТ И ПОДБОР ПОДШИПНИКОВ
Для быстроходного вала подбирается подшипник 207 ГОСТ 8328–75.
Эквивалентная нагрузка определяется по формуле из[4] :
(6.1)
где — максимальная радиальная нагрузка на подшипник, Fr=0,64кН;
— коэффициент вращения,(из[4]);
— коэффициент безопасности, (из[4]);
— температурный коэффициент, (из[4]);
Р=0,64•1•1,3•1 = 0,8кН.
Номинальная долговечность (в миллион оборотов) определяется по формуле из[4]:
(6.2)
где — динамическая грузоподъёмность,(С=12 700Н);
— коэффициент, учитывающий тип подшипника,();
Номинальная долговечность (в часах) определяется по формуле:
(6.3)
где — частота вращения вала,(n=702мин-1).
Долговечность подшипников выше установленного ресурса, который составляет 10 000ч.
Для вала II подбирается подшипник 211 ГОСТ 8328–75.
Максимальная радиальная нагрузка на подшипник Fr=5,5кН
Динамическая грузоподъёмность C=43,6кН;
Р=5,5•1•1,3•1 = 4,6кН.
Номинальная долговечность подшипников рассчитывается по формуле (6.2);
Долговечность подшипников рассчитывается по формуле (6.3);
Частота вращения вала,(n=140,4мин-1)
Долговечность подшипников выше установленного ресурса, который составляет 10 000ч.
9. ПРОВЕРОЧНЫЙ РАСЧЕТ ШПОНОК
Материал шпонок — сталь 45. Проверим шпонки под зубчатыми колесами на срез и смятие. .
Условия прочности:
(9.1)
(9.2)
Шпонка на быстроходном валу:
Шпонки на тихоходном валу:
Все шпонки удовлетворяют условию прочности на срез и смятие
10. УТОЧНЕННЫЙ РАСЧЕТ ВАЛОВ
Материал валов — сталь 45 улучшенная, предел прочности ;
Общий коэффициент запаса прочности по пределу текучести, определяется по формуле из стр.280:
(10.1)
— коэффициент запаса прочности по нормальным напряжениям, определяется по формуле из стр.280:
(10.2)
где — предел выносливости материала при изгибе с симметричным знакопеременном цикле нагружения, определяется по формуле:
(10.3)
.
— эффективный коэффициент концентрации напряжений (из атласа детали машин для всех валов);
— коэффициент поверхностного упрочнения (из атласа детали машин для всех валов);
— коэффициент, учитывающий влияние поперечных размеров вала, из атласа детали машин для быстроходного вала
;
для тихоходного вала
.
— амплитуда цикла нормальных напряжений, определяется по формуле:
(10.4)
где — момент сопротивления сечения изгибу, определяется по формуле:
(10.5)
для быстроходного вала
для тихоходного вала
для быстроходного вала
для тихоходного вала
— коэффициент характеризующий чувствительность материала к асимметрии цикла нагружения, определяется по формуле:
(10.6)
.
— среднее напряжение цикла,().
для быстроходного вала
для тихоходного вала
— коэффициент запаса прочности по касательным напряжениям, определяется по формуле из[1] стр.280:
(10.7)
где — предел выносливости материала при кручении с симметричным знакопеременном цикле нагружения, определяется по формуле:
(10.8)
— эффективный коэффициент концентрации напряжений (из атласа детали машин);
— коэффициент поверхностного упрочнения (из атласа детали машин);
— коэффициент, учитывающий влияние поперечных размеров вала, из атласа детали машин:
для быстроходного вала
;
для тихоходного вала
.
— амплитуда цикла касательных напряжений, определяется по формуле из[1] стр.280:
(10.9)
для быстроходного вала
для тихоходного вала
— коэффициент, характеризующий чувствительность материала к асимметрии цикла нагружения, определяется по формуле:
(10.10)
.
— среднее напряжение цикла,().
для быстроходного вала
для тихоходного вала
для быстроходного вала
для тихоходного вала
Общий коэффициент запаса прочности выше минимально допустимого. Прочность обеспечена.
11. ВЫБОР ПОСАДОК
Посадки элементов передач на валы — Н7/р6 по ГОСТ 25 347–82.
Посадка звездочки цепной передачи на вал редуктора Н7/h6.
Посадки муфт на валы редуктора — Н8/h8.
Шейки валов под подшипники выполняем с отклонением вала k6.
Остальные посадки назначаем по.
12. СМАЗКА РЕДУКТОРА
В редукторе применена картерная система смазки, то есть масло заливается непосредственно в корпус редуктора. При картерной смазке колёса редуктора смазываются разбрызгиваемым маслом. Так как окружная скорость колёс менее
3 м/с то для смазывания подшипников используется пластичная смазка. Пластичной смазкой на 1/3 заполняется пространство внутри подшипникового узла. Данное пространство отделяется от внутренней полости корпуса мазеудерживающим кольцом.
В качестве жидкой смазки используется индустриальное масло И-30А ГОСТ 20 799–95.
В качестве пластичной смазки используется Литол-24 ГОСТ 21 150–87
Для замены масла в корпусе редуктора предусмотрено специальное отверстие, закрываемое пробкой.
Для контроля уровня масла предусмотрен жезловой маслоуказатель.
13. ТЕХНОЛОГИЯ СБОРКИ РЕДУКТОРА
Перед сборкой внутреннюю полость корпуса редуктора тщательно очищают и покрывают маслостойкой краской. Сборку производят в соответствии с чертежом общего вида редуктора, начиная с узлов валов.
На валы закладывают шпонки и напрессовывают элементы передач редуктора. Маслоудерживающие кольца и подшипники следует насаживать, предварительно нагрев в масле до 80−100 градусов по Цельсию, последовательно с элементами передач. Собранные валы укладывают в основание корпуса редуктора и надевают крышку корпуса, покрывая предварительно поверхности стыка крышки и корпуса спиртовым лаком. Для центровки устанавливают крышку на корпус с помощью двух конических штифтов; затягивают болты, крепящие крышку к корпусу. После этого в подшипниковые камеры закладывают смазку, ставят крышки подшипников с комплектом металлических прокладок, регулируют тепловой зазор. Перед постановкой сквозных крышек в проточки закладывают войлочные уплотнения, пропитанные горячим маслом. Проверяют проворачиванием валов отсутствие заклинивания подшипников (валы должны проворачиваться от руки) и закрепляют крышку винтами. Затем ввертывают пробку маслоспускного отверстия с прокладкой и жезловый маслоуказатель. Заливают в корпус масло, закрепляют крышку болтами. Собранный редуктор обкатывают и подвергают испытанию на стенде по программе, устанавливаемой техническими условиями.
1. Дунаев П. Ф., Леликов О. П. Детали машин. Курсовое проектирование, М.: Издательство Машиностроение, 2002;535c.
2. Иванов М. Н. Детали машин. — М.:Высшая школа, 2002
3. Кудрявцев В. Н. Детали машин. — Л.: Машиностроение, 1980
4. Решетов Д. Н. Детали машин. — М.: Машиностроение, 1989
5. Проектирование механических передач. — М.: Машиностроение, 1984
6. Чернавский С. А., Боков К. Н., Чернин И. М., Ицкович Г. М., Козинцов В.П.