Очистка газовых выбросов в черной металлургии
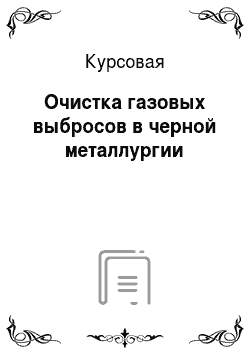
Способ очистки отходящих газов от диоксида серы, включающий его абсорбцию N-алкилпирролидоном с добавкой воды с последующей отгонкой диоксида серы в регенераторе абсорбента, характеризующийся тем, что процесс абсорбции N-метилили N-этилпирролидоном с содержанием воды от 0 до 15 мас.% проводят в интервале температур от -20 до 18 °C, с добавкой 2-пирролидона от 0 до 30 мас.%, с последующей отгонкой… Читать ещё >
Очистка газовых выбросов в черной металлургии (реферат, курсовая, диплом, контрольная)
Курсовая работа Очистка газовых выбросов в черной металлургии
1. Литературный обзор
1.1 Описание производства в черной металлургии
1.1.1 Производство чугуна с использованием доменных процессов
1.1.2 Производства железа в губчатых печах
1.1.3 Производство стали с помощью мартеновского процесса
1.1.4 Производство стали в конверторах
1.2 Источники и выбросы черной металлургии
1.3 Воздействие на окружающую среду и здоровье человека
2. Методы очистки
2.1 Абсорбция
2.1.1 Очистка газов от диоксида серы N-этилпирролидоном
2.1.2 Очистка от SO2 алюмо-сульфатным способом
2.1.3 Поглощение оксида углерода медно-аммиачным раствором
2.1.4 Очистка газов от диоксида серы известковой суспензией
2.1.5 Очистка газов от оксидов серы и азота
2.2 Адсорбция
2.2.1 Способ очистки газов от диоксида серы марганцевым концентратом
2.3 Термокаталитическая очистка газовых выбросов
2.3.1 Метод очистки газов от NO с использованием продуктов термического разложения твердого карбамида
2.3.2 Катализатор окисления оксида углерода
2.3.3 Катализатор для очистки газа от оксидов азота и углерода
3. Расчетная часть
3.1 Технологическая схема
3.2 Подбор и расчет оборудования ЗАКЛЮЧЕНИЕ
Металлы относятся к числу наиболее распространенных материалов, которые человек использует для обеспечения жизненных потребностей. В наши дни трудно найти такую область производства, научно-технической деятельности человека или просто его быта, где металлы не играли бы главенствующей роли, как конструкционного материала.
Однако интенсивное загрязнение атмосферы предприятиями металлургического комплекса значительно сказывается не только на человеке, но и на гидросфере, почвенно-растительном покрове, геологической среде. Поэтому охрана атмосферного воздуха является наиболее приоритетной проблемой охраны окружающей среды в черной металлургии.
На современном этапе для большинства промышленных предприятий очистка вентиляционных выбросов от вредных веществ является одним из основных мероприятий по защите воздушного бассейна. Благодаря очистке выбросов перед их поступлением в атмосферу предотвращается загрязнение атмосферного воздуха.
Для эффективного процесса очистки воздуха необходимо проанализировать воздействие предприятия, как единицы определенной отрасли. Изучение газового состава выбросов, влияние на человека и окружающую среду позволяет подобрать оптимальное оборудование и составить схему локальных газоочистных сооружений на предприятии.
абсорбция термокаталитическая очистка газы сталь
1. Литературный обзор
1.1 Описание производства в черной металлургии
Методы производства железа и стали сводятся к следующей классификации процессов в черной металлургии:
1) Производство чугуна — доменный процесс, процесс в низкошахтной печи.
2)Производство губчатого железа — процессы в шахтной печи, в печах кипящего слоя, во вращающихся трубчатых печах.
3) Производство стали (периодические процессы) — мартеновский процесс, конверторный процесс.
4) Производство стали (непрерывные процессы) — методы: каскадный, окислительная плавка в желобковой печи.
1.1.1 Производство чугуна с использованием доменных процессов
Чугун — сплав железа и углерода с сопутствующими элементами (содержание углерода более 2,14%). Для выплавки чугуна в доменных печах используют железные руды, топливо, флюсы. Подготовка руд к доменной плавке осуществляется для повышения производительности доменной печи, снижения расхода кокса и улучшения качества чугуна. Метод подготовки зависит от качества руды.
Дробление и сортировка руд по крупности служат для получения кусков оптимальной величины, осуществляются с помощью дробилок и классификаторов.
Обогащение руды основано на различии физических свойств минералов, входящих в ее состав:
а) промывка — отделение плотных составляющих от пустой рыхлой породы;
б) гравитация (отсадка) — отделение руды от пустой породы при пропускании струи воды через дно вибрирующего сита: пустая порода вытесняется в верхний слой и уносится водой, а рудные минералы опускаются;
в) магнитная сепарация — измельчённую руду подвергают действию магнита, притягивающего железосодержащие минералы и отделяющего их от пустой породы.
Окусковывание производят для переработки концентратов в кусковые материалы необходимых размеров. Применяют два способа окусковывания: агломерацию и окатывание.
Чугун выплавляют в печах шахтного типа — доменных печах.
Сущность процесса получения чугуна в доменных печах заключается в восстановлении оксидов железа, входящих в состав руды оксидом углерода, водородом и твердым углеродом, выделяющимся при сгорании топлива.
При выплавке чугуна решаются задачи:
1) Восстановление железа из окислов руды, науглероживание его и удаление в виде жидкого чугуна определённого химического состава.
2) Оплавление пустой породы руды, образование шлака, растворение в нём золы кокса и удаление его из печи.
Восстановление железа происходит по мере продвижения шихты вниз по шахте и повышения температуры от высшего оксида к низшему, в несколько стадий:
Восстановителями окcидов железа являются твердый углерод, оксид углерода и водород.
При температуре 1000…1100 0C восстановленное из руды твёрдое железо, взаимодействуя с оксидом углерода, коксом и сажистым углеродом, интенсивно растворяет углерод. При насыщении углеродом температура плавления понижается и на уровне распара и заплечиков железо расплавляется (при температуре около 1300 0С).
Капли железоуглеродистого сплава, протекая по кускам кокса, дополнительно насыщаются углеродом (до 4%), марганцем, кремнием, фосфором, которые при температуре 1200 0C восстанавливаются из руды, и серой, содержащейся в коксе.
В нижней части доменной печи образуется шлак в результате сплавления окислов пустой породы руды, флюсов и золы топлива.
Шлак образуется постепенно, его состав меняется по мере стекания в горн, где он скапливается на поверхности жидкого чугуна, благодаря меньшей плотности. Состав шлака зависит от состава применяемых шихтовых материалов и выплавляемого чугуна.
Чугун выпускают из печи каждые 3−4 часа через чугунную летку, а шлак — каждые 1−1,5 часа через шлаковую летку.
Летку открывают бурильной машиной, затем закрывают огнеупорной массой. Сливают чугун и шлак в чугуновозные ковши и шлаковозные чаши.
Чугун поступает в кислородно-конвертерные или мартеновские цехи, или разливается в изложницы разливочной машиной, где он затвердевает в виде чушек-слитков массой 45 кг.
1.1.2 Производства железа в губчатых печах
Губчатым железом называют продукт, который получают в результате восстановления железорудного материала без его плавления при температуре менее 1000—12000С. В зависимости от вида исходного сырья губчатое железо представляет собой пористые куски восстановленной руды (редко агломерата) или окатыши, а в некоторых случаях — металлический порошок. Поскольку при восстановлении объемные изменения материала сравнительно невелики, плотность губчатого железа меньше плотности сырья, а пористость велика. Обычно кажущаяся плотность кускового губчатого железа 2—4 г/см3, а пористость 50—80%.
Химический состав губчатого железа определяется в основном составом сырья. По сравнению с ломом оно значительно чище по содержанию примесей цветных металлов. Содержание пустой породы в нем выше, чем в исходной руде, пропорционально степени восстановления. Обычно сырьем служат богатые руды или концентраты, поэтому губчатое железо не подвергают дополнительной очистке, и оно содержит все примеси пустой породы сырья. При получении губчатого железа из бедного сырья его подвергают обогащению магнитной сепарацией.
Губчатое железо используют для плавки стали (главным образом в электропечах), цементации меди (осаждения ее из сернокислых растворов) и получения железного порошка.
При получении губчатого железа добытую руду обогащают и получают окатыши. Окатыши из бункера по грохоту поступают в короб шихтозавалочной машины и оттуда в шахтную печь, работающую по принципу противотока. Просыпь от окатышей попадает в бункер с брикетировочным прессом и в виде окатышей вновь поступает на грохот . Для восстановления железа из окатышей в печь по трубопроводу подают смесь природного и доменного газов, подвергнутую в установке конверсии, в результате которой смесь разлагается на водород H2 и оксид углерода CO. В восстановительной зоне печи создается температура 1000−1100 0C, при которой H2 и CO восстанавливают железную руду в окатышах до твёрдого губчатого железа. Содержание железа в окатышах достигает 90−95%. Для охлаждения железных окатышей по трубопроводу в зону охлаждения печи подают воздух. Охлаждённые окатыши выдаются на конвейер и поступают на выплавку стали в электропечах.
1.1.3 Производство стали с помощью мартеновского процесса
Сущность мартеновского процесса заключается в ведении плавки на поду отражательной печи, оборудованной регенераторами для предварительного подогрева воздуха и газообразного топлива.
В мартеновскую печь загружают шихту, состоящую из чугуна, скрапа, металлического лома и др. Шихта нагревается под действием тепла от сжигаемого топлива и постепенно плавится. После заливки чугуна плавление твердой металлической части шихты резко ускоряется. Одновременно с прогревом шихты начинается окисление примесей. К концу расплавления шихты почти полностью окисляется кремний, более половины марганца, почти третья часть фосфора и частично углерод. Окисление примесей происходит по тем же реакциям, что и при конверторном процессе. Известняк переводит в шлак фосфор и серу.
После расплавления шихты начинается доводка стали до необходимого химического состава. Готовность плавки определяют взятием пробы и ее экспресс-анализом. После этого проводится раскисление и выпуск стали в ковши, из которых ее разливают в слитки.
Продолжительность плавки стали в мартеновской печи составляет 8…16 ч. Печь работает непрерывно. Длительность функционирования печи в основном зависит от стойкости ее свода. Средняя стойкость динасового свода 200…350 плавок, магнезитового — 300−1000 плавок. Расход металлошихты на 1 т годных слитков составляет 1100−1200 кг.
1.1.4 Производство стали в конверторах
Кислородно-конвертерный процесс — выплавка стали из жидкого чугуна в конвертере с основной футеровкой и продувкой кислородом через водоохлаждаемую фурму.
Перед плавкой конвертер наклоняют, с помощью завалочных машин загружают скрап, заливают чугун при температуре 1250−1400 0C. По окончании заливки чугуна подают дутье и конвертер устанавливают в вертикальное положение. Начинается процесс окисления примесей чугуна. В течение периода шлакообразования интенсивно окисляются примеси, имеющие наибольшее химическое сродство к кислороду: Si, Mn и в какой-то мере Fe. Образующийся шлак содержит SiO2, MnO, FeO. Вследствие относительно низких температур первого периода углерод почти не окисляется. Поскольку общая масса жидкого металла в результате окисления Si, Mn и Fe уменьшается, относительное содержание углерода в ванне может немного увеличиться.
При окислении Mn, Fe, и особенно Si, температура ванны резко возрастает (до 1600−1650 °С) и начинается период кипения, во время которого окисляется углерод. Начало второго периода может быть достаточно точно зафиксировано визуально: как только начинает окисляться углерод, из ванны выделяется большое количество образующегося СО.
При высокой температуре металла и шлака процесс окисления углерода протекает очень интенсивно: углерод окисляется не только кислородом дутья, но частично и кислородом, содержащимся в оксидах железа шлака.
Подачу кислорода заканчивают, когда содержание углерода в металле соответствует заданному. После этого конвертер поворачивают и выпускают сталь в ковш, где раскисляют осаждающим методом ферромарганцем, ферросилицием и алюминием, затем сливают шлак.
В кислородных конвертерах выплавляют стали с различным содержанием углерода, кипящие и спокойные, а также низколегированные стали. Легирующие элементы в расплавленном виде вводят в ковш перед выпуском в него стали. Плавка в конвертерах вместимостью 130−300 т заканчивается через 25−30 минут.
1.2 Источники и выбросы черной металлургии
Все известные технологические процессы, производства чугуна, стали и их последующего передела сопровождаются образованием больших количество отходов в виде вредных газов и пыли, шлаков, шламов, сточных вод, содержащих различные химические компоненты, скрапа, окалины, боя огнеупоров, мусора и других выбросов, которые загрязняют атмосферу, воду и поверхность земли. Все металлургические переделы являются источниками загрязнения пылью, оксидами углерода и серы (таблица 1).
Таблица 1 Газовые выбросы (до очистки) металлургического производства
Составляющие выбросов | Агломерационное производство, кг/т агломерата | Доменное производство, кг/т чугуна | Сталеплавильное производство, кг/т стали | Прокатное производство | |
Пыль | 20−25 | 100−106 | 13−32 | 0,1−0,2 кг/т проката | |
Оксид углерода | 20−50 | 600−605 | 0,4−0,6 | 0,7 т/м поверхности металла | |
Оксиды серы | 3−25 | 0,2−0,3 | 0,4−35 | 0,4 т/м поверхности металла | |
Оксиды азота | 0,3−3,0 | 0,5 т/м поверхности металла | |||
Сероводород | 10−60 | ||||
Аэрозоли травильных растворов | в травильных отделениях | ||||
Пары эмульсии | при металлообработке | ||||
Современное металлургическое предприятие является сложным производственным комплексом, включающим самые разнообразные цехи, а иногда отдельные заводы, которые в значительной степени ухудшают состояние ОС. Основными источниками загрязнения атмосферы выбросами металлургических предприятий являются коксохимическое, агломерационное, доменное, ферросплавное и сталеплавильное производства. Коксохимическое производство загрязняет атмосферу окислами углерода и серы. На 1 т перерабатываемого угля выделяется около 0,75 кг SO2 и по 0,03 кг различных углеводородов и аммиака. Кроме газов, коксохимическое производство выделяет в атмосферу большое количество пыли. Имеются данные, что при производстве кокса на 1 т перерабатываемого угля выделяется около 3 кг угольной пыли. Также большое количество пыли выделяется при разгрузке и перегрузке угля, в среднем 0,005% от массы угля.
На аглофабриках источниками загрязнения воздуха являются аглоленты, барабанные и чашевые охладители агломерата, обжиговые печи, узлы пересыпки и сортировки агломерата и других компонентов шихты. Количество агломерационных газов 2,5−4,0 тыс. м3/т полученного агломерата с содержанием в них пыли от 5 до 10 г/м3 В состав газов входят оксиды серы и углерода, а пыль содержит железо и его оксиды, оксиды марганца, магния,
фосфора, кремния, кальция, иногда частицы титана, меди, свинца.
Доменное производство характеризуется образованием большого количества доменного газа (? 2−4 тыс. м3/т чугуна). Этот газ содержит оксиды углерода и серы, водород, азот, некоторые другие газы и большое количество колошниковой пыли (до 150 кг/т чугуна). Пыль содержит окислы железа, кремния, марганца, кальция, магния, частицы шихтовых материалов.
Основные источники загрязнения воздуха при производстве ферросплавов — электродуговые печи. Выбросы этих печей состоят из нетоксичной и токсичной пыли (окислы железа, меди, цинка, свинца, хрома, кремния, газы). В зависимости от вида выплавляемого сплава и мощности печей суммарное количество пыли, образующейся в результате технологических процессов, может составлять сотни тонн в сутки. При этом Cr+6 и пыль обнаруживают на расстоянии до 3 км от источника загрязнения. Заводы, выплавляющие ферросилиций, загрязняют атмосферный воздух в радиусе 2−3 км мельчайшими частицами SiO2, наибольшее содержание которых наблюдается на расстоянии около 0,5 км от предприятия.
1.3 Воздействие на окружающую среду и здоровье человека
Наиболее угрожающие последствия загрязнение атмосферы вызванные деятельностью металлургических предприятий, являются оксид углерода, диоксид серы, оксиды азота, пыль. Отрицательные последствия эмиссии соединений серы и азота выражается в первую очередь в возникновении таких негативных явлений как смог и кислотные осадки.
Смог представляет собой смесь тумана и дыма, наполненного опасными для живых организмов веществами. Смог может полностью обволакивать город на несколько дней. Различают влажный, фотохимический и ледяной смоги.
Смог в виде густого ядовитого тумана, который образуется в осенне-зимнее время, называют смогом лондонского типа. Его основой является сернистый ангидрит, содержание SO2 в котором в несколько раз превышает ПДК [9,10].
Другой вид смога — фотохимический туман. Основные компоненты — фотооксиданты, оксиды азота, угарный и углекислый газы, альдегиды, кетоны, фенолы, метанол и т. п. Он образуется в теплое время года в воздухе, сильно загрязненном промышленными газами, в результате из разолжения под действием солнечного излучения.
Смог ледяной — это состояние газообразных загрязнителей, пылевых частиц и кристалликов льда, возникающих при замерзании тумана.
Кислотные осадки — это осадки, выпадающие в виде дождя и снега со значением pH 5,5−5,6.Это связано с присутствием в атмосфере диоксидов углерода, серы и азота, поступающих из антропогенных источников.
Диоксид серы в большом количестве образуется при сжигании органического топлива в металлургической промышленности. Среднее время жизни SO2 составляет четверо суток, а затем происходит окисление в SO3. Соединяясь с парами воды, присутствующими в воздухе триоксид серы образует серную кислоту. Таким же образом происходит образование азотной кислоты.
Кислотные осадки ускоряют процессы коррозии в городах, разрушают памятники и сооружения из мрамора и известняка. При действии на почвы кислотные осадки вызывают закисление и нарушают естественные круговороты веществ, а также биологическое равновесие. Кроме того они выщелачивают из почвы тяжелые металлы, превращая их в растворимые формы, хорошо усваиваемые растениями. Далее по трофическим цепям они поступают в организм человека и накапливаются, разрушая различные органы и нарушая метаболические реакции в организме.
Кислотные осадки представляют для человека серьезную опасность, так как могут вызывать раздражение слизистых оболочек дыхательных путей, глаз, а при больших концентрациях — удушье и смерть. Особенно опасен диоксид серы, когда он осаждается на пылинках и в этом виде проникает глубоко в дыхательные пути.
Пыль, содержащая диоксид кремния (SiO2), вызывает тяжелое заболевание легких — силикоз. Оксиды азота раздражают, а в тяжелых случаях и разъедают слизистые оболочки, например, глаз, легких, участвуют в образовании ядовитых туманов и т. д. Особенно опасны они, если содержатся в загрязненном воздухе совместно с диоксидом серы и другими токсичными соединениями. В этих случаях даже при малых концентрациях загрязняющих веществ возникает эффект синергизма, т. е. усиление токсичности всей газообразной смеси.
Широко известно действие на человеческий организм оксида углерода (угарного газа). При остром отравлении появляются общая слабость, головокружение, тошнота, сонливость, потеря сознания, возможен летальный исход (даже спустя 3—7 дней). Однако из-за низкой концентрации СО в атмосферном воздухе он, как правило, не вызывает массовых отравлений, хотя и очень опасен для лиц, страдающих анемией и сердечно-сосудистыми заболеваниями.
Среди взвешенных твердых частиц наиболее опасны частицы размером менее 5 мкм, которые способны проникать в лимфатические узлы, задерживаться в альвеолах легких, засорять слизистые оболочки.
2. Методы очистки
2.1 Абсорбция
Абсорбция — поглощение газов или паров из газовых или парогазовых смесей жидкими поглотителями, называемыми абсорбентами. Возможность осуществления процесса абсорбции основывается на растворимости газов в жидкостях. Поглощение газа может происходить либо за счет его растворения в абсорбенте, либо в результате его химического взаимодействия с абсорбентом. В первом случае процесс называют физической абсорбцией, а во втором случае — хемосорбцией. Абсорбентами служат индивидуальные жидкости или растворы активного компонента в жидком растворителе. Во всех случаях к абсорбентам предъявляют ряд требований, среди которых наиболее существенными являются: высокая абсорбционная способность, селективность, низкое давление пара, химическая инертность по отношению к распространенным конструкционным материалам (при физической абсорбциитакже к компонентам газовой смеси), не токсичность, огнеи взрывобезопасность, доступность и не высокая стоимость.
Абсорбенты, применяемые для очистки отходящих газов, приведены в таблице 2.
Таблица 2 Абсорбенты, применяемые для очистки отходящих газов
Поглощаемые компоненты | Абсорбенты | |
Оксиды азота N2O3, NO2, N2O5 | Вода, водные растворы и суспензии: NaOH, Na2CO3, NaHCO3, KОН, K2СО3, КНСО3, Са (ОН)2, СaСО3, Mg (OH)2, MgCO3, Ba (OH)2, ВаСО3, NH4HCO3 | |
Оксид азота NO | Растворы FeCl3, FeSO4, Na2S2O3 NaHCO3, NaHSO3, Na2SO3 | |
Диоксид серы SO2 | Вода, водные растворы: Na2SO3(18—25%-ные), NH4OH (5—15%-ные), Са (ОН)2, Na2CO3(15—20%- ные), NaOH (15—25%-ные), KОН,(NН4)2SО3 (20—25%-ные), ZnSO3, K2СО3; суспензии CaO, MgO, СаСО3, ZnO, золы; ксилидин—вода в соотношении 1: 1, диметиланилин C6H3(CH3)2NH2 | |
Сероводород H2S | Водный раствор Na2CO3 + Na3AsO4; водный раствор Аs2О3(8—10 г/л) + NН3(1,2—1,5 г/л) + (NH4)3AsO3 (3,5—6 г/л); моноэтаноламин (10—15%-ный раствор); растворы K3РO4(40—50%-ные), NH4ОH, K2CO3, Na2CO3, CaCN2, натриевая соль антрахинондисульфокислоты | |
Оксид углерода СО | Жидкий азот; медно-аммиачные растворы [Сu (NН3)]nЧСОСН | |
Диоксид углерода СО2 | Водные растворы Nа2СО3, K2СО3, NaOH, KОН, Са (ОН)2, NH4OH, этаноламины RNH2, R2NH4 | |
До обработки органическим абсорбентом из загрязненных газов необходимо удалить дисперсные примеси. Иначе абсорбент быстро загрязняется и становится отходом, практически не поддающимся очистке.
Органические абсорбенты должны иметь низкое давление насыщенных паров при температуре процесса. Растворители с недостаточно низкой упругостью паров будут интенсивно испаряться, и загрязнять обрабатываемые газы. Кроме того, низкокипящий абсорбент сложно регенерировать, так как извлечь (десорбировать из него) уловленное вещество нагреванием невозможно. На интенсивность перехода загрязнителя из газовой фазы в жидкую большое влияние оказывают температура и давление процесса, а также способ организации контакта фаз. С ростом давления и снижением температуры скорость абсорбции увеличивается.
Газовая смесь, содержащая извлекаемый из нее компонент, поступает в абсорбер, где происходит контакт с абсорбентом, который поглощает данный компонент. Газ, очищенный от компонента, удаляется (очищенный воздух может быть выброшен в атмосферу), а раствор поглотителя, содержащий абсорбированный компонент, поступает в теплообменник, где нагревается. Нагретый раствор насосом подается в десорбер, где из него выделяется (десорбируется) поглощенный компонент путем испарения в результате нагревания поглотителя паром. Поглотитель, освобожденный от компонента, поступает в теплообменник, где отдает теплоту абсорбенту при его противоточном движении в десорбер, а затем направляется в холодильник, пройдя который, снова поступает в абсорбер. Круг замкнулся. По такому циклу работает установка для абсорбционно-десорбционного улавливания определенных паров и газов из газовой смеси.
2.1.1 Очистка газов от диоксида серы N-этилпирролидоном
Способ очистки отходящих газов от диоксида серы, включающий его абсорбцию N-алкилпирролидоном с добавкой воды с последующей отгонкой диоксида серы в регенераторе абсорбента, характеризующийся тем, что процесс абсорбции N-метилили N-этилпирролидоном с содержанием воды от 0 до 15 мас.% проводят в интервале температур от -20 до 18 °C, с добавкой 2-пирролидона от 0 до 30 мас.%, с последующей отгонкой диоксида серы под давлением в интервале 1,2−1,5 атмосферы. Преимуществом данного способа по сравнению с использованием N-метилпирролидона, является уменьшение энергетических затрат при очистке отходящих газов от диоксида серы и увеличение поглотительной способности абсорбента. Применение повышенного давления при отгонке диоксида серы, позволяет совместить десорбцию диоксида серы с его термокомпрессией и транспортировать концентрированный продукт к месту переработки без затрат электроэнергии на его компрессию.
2.1.2 Очистка от SO2 алюмо-сульфатным способом
Процесс, заключается в сорбции диоксида серы раствором основного сульфата алюминия. Растворимость диоксида серы в растворе основного сульфата алюминия, примерно, в 20 раз выше, чем в воде, и увеличивается с повышением концентрации алюминия, основности и понижением температуры. После окисления сульфита алюминия диспергированным сжатым воздухом до сульфата, небольшую часть раствора направляют в реактор на нейтрализацию известняком. В отличие от традиционного процесса десульфуризации (известковый способ) при использовании алюмо-сульфатного способа не происходит отложений гипса в абсорберах и трубопроводах. Другим существенным преимуществом процесса является его нечувствительность к изменениям расхода газа, его температуры и концентрации SO2, объясняющаяся высокой сорбционной способностью основного сульфата алюминия в широком диапазоне изменения основности. Дополнительное преимущество — использование дешевого известняка вместо извести. Эффективность очистки данным способом составляет 92%.
2.1.3 Поглощение оксида углерода медно-аммиачным раствором
В процессе медно-аммиачной очистки окись углерода поглощается под высоким давлением водным раствором медно-аммиачной соли. В практике используются аммиачные растворы формиата, карбоната или ацетата меди. Степень очистки газа зависит от парциального давления окиси углерода над регенерированным раствором и общего давления газа. Для достижения остаточного содержания окиси углерода в 10 млн-1. промывка должна производиться при давлении 80−300 атмосфер и температуре от 0 до -10°С.?При замене карбонатного медно-аммиачного раствора ацетатным степень очистки увеличивается на и 30% и на 40% снижается объем циркулирующего раствора.
2.1.4 Очистка газов от диоксида серы известковой суспензией
Способ очистки технологического газа от диоксида серы путем абсорбции известковой суспензией, кристаллизации и удаления шлама, отличающийся тем, что перед абсорбцией газ охлаждают в испарительном режиме до точки росы водой, подаваемой в количестве 0,08−0,12 л/м3 газа и с температурой, превышающей температуру точки росы охлаждаемого газа на 10 °C.
Абсорбцию газа осуществляют суспензией в виде капель, подаваемых перпендикулярно потоку газа. Данный метод позволяет снизить солевые отложения сульфатов и сульфитов кальция на стенках абсорбера, повысить степень очистки технологического газа от диоксида серы.
2.1.5 Очистка газов от оксидов серы и азота
Сущность метода заключается в том, что газы, содержащие оксиды серы и азота, охлаждают и подвергают абсорбции примеси последовательным контактированием газов с концентрированной серной кислотой, с жидким триоксидом серы при 17−44oC и с концентрированной серной кислотой. После этого очищенные газы выбрасывают в атмосферу, а абсорбенты с поглощенными оксидами азота и серы перерабатывают в контактно-нитрозном процессе в серную и азотную кислоты с рециркуляцией отходящих газов этого процесса на очистку совместно с исходными газами. Процесс абсорбции проводят под избыточным давлением. Факторами, влияющими на эффективность процессов, протекающих в отделении очистки, является давление, температура, нитрозность серной кислоты. Степень очистки в данном методе по диоксиду серы составляет 99,932%, по оксидам азота 99,756%.
2.2 Адсорбция
Адсорбция позволяет почти полностью извлечь из газовой смеси загрязняющие компоненты, она дает возможность осуществлять глубокую очистку газов. Процесс адсорбции происходит на поверхности твердого пористого тела — адсорбента, где ненасыщенные поверхностные силы вступают во взаимодействие с силовыми полями адсорбируемых молекул. Адсорбенты, используемые в системах очистки отходящих газов, должны удовлетворять следующим требованиям: иметь большую адсорбционную способность при поглощении компонентов при небольших концентрациях их в газовых смесях, обладать высокой селективностью, иметь высокую механическую прочность, обладать способностью к регенерации и иметь низкую стоимость.
2.2.1 Способ очистки газов от диоксида серы марганцевым концентратом
Способ включает адсорбцию влажным свежеосажденным марганцевым концентратом, полученным обработкой раствора сульфата марганца аммиаком и воздухом при pH 8 — 8,5 и температуре 40 — 50oC, при этом влажный свежеосажденный марганцевый концентрат используется в виде пульпы MnO2, которую заливают в реактор, снабженный барбатером для пропускания через нее очищаемых газов, и температуру пульпы поддерживают в пределах 40 — 70oC. В условиях проведении адсорбции при температуре 30oC свежеосажденным марганцевым концентратом за время 60 минут средняя степень очистки составляет 98,6%.
2.3 Термокаталитическая очистка газовых выбросов
Термоокисление газообразных загрязнителей может происходить в газовой фазе (в объеме) или на границе раздела фаз (на поверхности). Газофазный процесс осуществляют непосредственной огневой обработкой (сжиганием в пламени) газовых выбросов при температурах, превышающих температуру воспламенения горючих компонентов выбросов. Для организации процесса окисления на границе раздела фаз используют катализаторы — конденсированные вещества, способные за счет активности поверхностных частиц ускорять процесс окисления того или иного загрязнителя при температурах ниже температуры воспламенения. Каталитические методы очистки газов основаны на гетерогенном катализе и служат для превращения примесей в безвредные или легко удаляемые из газа соединения. Процессы гетерогенного катализа протекают на поверхности твердых тел — катализаторов.
Катализаторы должны обладать определенными свойствами: активностью, пористой структурой, стойкостью к ядам, механической прочностью, селективностью, термостойкостью, низким гидравлическим сопротивлением, иметь небольшую стоимость. Особенность процессов каталитической очистки газов заключается в том, что они протекают при малых концентрациях удаляемых примесей. Основным достоинством метода является то, что он дает высокую степень очистки, а недостатком — образование новых веществ, которые надо удалять из газа адсорбцией или абсорбцией.
2.3.1 Метод очистки газов от NO с использованием продуктов термического разложения твердого карбамида
Сущность метода заключается в процессе использования восстановительной смеси, которая образуется в результате термического разложения карбамида в интервале температур 20 — 600 °C. Восстановительная смесь, полученная в реакторе термического разложения твердого карбамида, направленная в реактор высокотемпературного восстановления NO, происходила очистка газовых выбросов при температуре от 700 до 1100 °C, характерной для условий работы стационарных топливосжигающих установок.
Достоинствами селективного некаталитического метода по сравнению с каталитическим методом — это высокая избирательность восстановительной смеси, высокая степень очистки, наименьшее значение рано 84%. В данном методе учтена возможность использования карбамида и при низких температура. Эффективность очистки при 131 °C составляет 58%. Недостатком метода, является образование незначительного количества NH3 в результате разложения карбамида при низких температурах.
2.3.2 Катализатор окисления оксида углерода
Сущность каталитического воздействия анодного шлама заключается в том, что при его образовании в электрохимическом процессе анодного окисления составляющих шлама происходят химические и структурные превращения, приводящие к образованию соединений, обладающих эффективным каталитическим действием в процессе окисления оксида углерода.
В качестве катализатора используют анодный шлам, образующийся на свинцовом аноде при электролитическом восстановлении цинка из кислых сульфатных растворов, состава, массовая доля %: диоксид марганца 53,9; диоксид свинца 15; оксид серебра 0,06; примеси — остальное. Степень очистки газа от CO возрастает и при температуре 250 oC достигает 90−97% при скорости газового потока 0,35−0,50 дм3/мин.
2.3.3 Катализатор для очистки газа от оксидов азота и углерода
Катализатор для очистки газа от оксидов азота и оксида углерода (II), содержащий активную массу, нанесенную на подложку на основе хромникелевого пористого материала, отличающийся тем, что в качестве пористого материала он содержит ФНС-5, а активная масса содержит Al, Ni, Cu при следующем соотношении компонентов, вес.%: Пористый материал ФНС-5 (ТУ 14−1-1400−75) представляет собой пластину толщиной 0,14−0,20 мм, обладающую пористостью 32−37%, изготовленную методом прокатки порошка нержавеющей стали марки Х18Н15−2. Активная масса составляет 11−13 вес.%. Степень очистки от оксидов углерода и азота варьируется в зависимости от соотношения Cu/Ni и температуры процесса и может достигать для оксида углерода — 90%, для оксида азота — 99%.
3. Расчетная часть
3.1 Технологическая схема
Разработаны две схемы очистки — мокрая и сухая.
Рис. 1 — Схема обеспыливания доменного газа По мокрой схеме (рис. 1) газ из колошника 2 доменной печи по газоходу 3 отводится в систему газоочистки. В сухом пылеуловителе 4 инерционного или центробежного типа доменный газ очищается от крупной пыли до конечного пылесодержания 5—10 г/м3. Периодически пыль удаляется из бункера пылеуловителя в железнодорожный вагон через устройство, состоящее из отсечного клапана, шнекового транспортера и системы подачи воды или пара для увлажнения пыли. В полом скруббере 5 газ охлаждается и очищается от крупной пыли. Запыленность доменного газа после полого скруббера составляет 2—4 г/м3, а иногда меньше.
Окончательная очистка доменного газа осуществляется в скоростном пылеуловителе с трубами Вентури. В трубе или трубах Вентури 6 (в зависимости от объема доменной печи) происходит укрупнение мелкодисперсной пыли. Наиболее крупная пыль и капли жидкости выводятся из газа в инерционном пыле и брызгоуловителе 7, а окончательная очистка газа от пыли до требуемого конечного пылесодержания осуществляется в центробежном скруббере 9. Очищенный газ отводится в коллектор чистого газа 10, откуда подается потребителям. Для повышения давления газа в доменной печи перед центробежным скруббером установлена дроссельная группа 8. Все аппараты, расположенные между доменной печью и дроссельной группой, работают под повышенным давлением газа, поэтому их конструкцию делают жесткой, способной выдерживать такое давление. Дроссельную группу в зависимости от ее конструкции устанавливают на горизонтальном или вертикальном участках газопровода.
Для схем доменной газоочистки характерны конструктивные особенности, которые зависят от местных условий, числа доменных печей, а также от способа использования энергии доменного газа. В том случае, если для коагуляции пыли вместо труб Вентури используется дроссельная группа, схема газоочистки упрощается.
3.2 Подбор и расчет оборудования
Гидравлическое сопротивление трубы Вентури при подаче в нее орошающей жидкости описывается уравнением:
где — гидравлическое сопротивление трубы Вентури без орошения, Па; - гидравлическое сопротивление трубы Вентури, обусловленное вво-дом орошающей жидкости. Па.
Гидравлическое сопротивление труб Вентури, обусловленное орошающей жидкостью, рассчитывают по формуле:
,
где — коэффициент гидравлического сопротивления, обусловленный вводом жидкости; mудельный расход орошающей жидкости, м3/м3.
Величину коэффициента о ж следует определять по выражению:
,
где — скорость капель жидкости на выходе из горловины трубы Вентури (обычно в 1,5−3 раза меньше, меньшие значения берут для высоких скоростей газа), м/с.
Степень очистки газов в скруббере Вентури можно рассчитать по полуэмпирической формуле:
где Stk — критерий Стокса:
m — удельный расход орошающей жидкости, л/м3;
с — коэффициент, учитывающий геометрические соотношения частей трубы Вентури, зависит от длины lэф. Эффективная длина горловины lэф равна сумме длин горловины lг и начального участка диффузора lґ. При угле раскрытия диффузора б= 6° величина l? = 0,476dг.экв (dг.экв — эквивалентный диаметр горловины)[25]. Величину dк (в мкм), характеризующую средний диаметр капель жидкости, можно определить по эмпирической формуле:
ЗАКЛЮЧЕНИЕ
Металлургическая отрасль находится на втором месте среди всех других отраслей промышленности по атмосферным выбросам. Именно загрязнение атмосферы является главной причиной экологических проблем, возникающих в результате деятельности металлургических гигантов. Основными загрязнителями атмосферного воздуха в металлургии являются диоксид серы, оксиды азота, оксид углерода, пыль. Они пагубно отражаются на здоровье человека и окружающей среде, что ставит необходимым задачу по очистке отходящих производственных газов и снижения концентрации вредных веществ, до пределов, не превышающих норм предельно допустимых концентраций. С этой целью в данной курсовой работе были проанализированы основные этапы и циклы металлургического производства для подбора оборудования оптимально подходящего для нужд металлургического комплекса.
1) Бабич В. К. Лукашкин Н.Д. Основы металлургического производства .M: Металлургия, 1982. ст.272
2) Ченцова Л. И. Очистка и переработка промышленных выбросов и отходов: учеб. пособие для вузов — Красноярск: СибГТУ, 2012. — 250 с.
3) Линчевский Б. В. Металлургия черных металлов. М: Металлургия, 1986
4) Циммерман Р. Гюнтер К. Металлургия и материаловедение. Справ. изд. Пер. с нем. М: Металлургия, 1982. 480 с.
5) ТретьяковаН.В.Лекции по дисциплине «Технология конструкционных материалов», Иваново, 2007, ст. 160
6) КнязевВ. Ф, Гиммельфарб А. И., Неменов.А. М. Бескоксовая металлургия железа, Из-во: Металлургия, 1972 г., ст.272
7) Акулич Н. В. Процессы производства черных и цветных металлов и их сплавов, Гомель 2008, ст.270
8) Кудрин В. А. Теория и технология производства стали: Учебник для вузов. — М.: «Мир», ООО «Издательство ACT», 2003, ст. 528
9) Большина Е. П. Экология металлургического производства: Курс лекций. — Новотроицк: НФ НИТУ «МИСиС», 2012. — 155с.
10) Влияние отраслей промышленности на экологию окружающей среды: /Материалы студенческих докладов XLV, XLVI, XVII апрельской научно-практической конференции // Сборник докладов. / Отв. ред. О. В. Карташова, Р. А. Панина. — Горно-Алтайск: РИО ГАГУ, 2012. — 117 с.
11) Вронский В. А. Прикладная экология: Учебное пособие. Ростов н/Д. Изд-во «Феникс» 1996, ст. 512.
12) Тарасова Г. И., Свергузова С. В. Общая экология — Белгород, 2010 г.
13) Коробкин В. И., Передельский Л. В. Экология: учебник для вузов. Ростов н/Д: Феникс, 2007. — ст.602.
14) Ветошкин А. Г. Процессы и аппараты газоочистки. Учебное пособие. — Пенза: Изд-во ПГУ, 2006. — с.: ил., библиогр.
15) Патент 2 011 122 378/05, 02.06.2011, Щелкунов С. А., Малышев О. А., Вьюгина Т. П., Никонова Е. Б. Способ очистки отходящих газов от диоксида серы // Патент России № 2 467 788. 2007. Бюл. № 33.
16) Попов В. М., Бурочкин К. Б., Попов В. А. Очистка металлургических газов от диоксида серы алюмо-сульфатным способом. «Черные металлы» — 2010.
17)Черный И.Р., Черный Ю. И. Тематический обзор серии «Нефтехимия и сланцепереработка» М: ЦНИИТЭнефтихим, 1976 г.
18) Патент 2 005 110 591/15, 11.04.2005, Зелинский К. В. Способ очистки технологического газа от диоксида серы // Патент России № 2 286 836. 2006. Бюл. № 33.
19) Патент 96 115 580/25, 24.07.1996. Кобяков А. А., Кобяков А. И. Способ очистки газов от оксидов серы и азота // Патент России № 2 104 754. 1998. Бюл. № 33.
20) Патент. Теляков Н. М. Федоров И.А. Способ очистки газов от диоксида серы // Патент России № 2 084 271. 1997. Бюл. № 33.
21) Куценко Е. В. Разработка метода очистки газов от оксидов азота с использованием продуктов термического разложения твердого карбамида. Автореф. дис. канд. техн. наук. — Москва, 2004. — 29 с.
22) Патент. Воропанова Л. А. Лисицина О.Г. Катализатор окисления оксида углерода// Патент России № 2 156 164. 2000. Бюл. № 33.
23) Патент 99 108 491/04, 26.04.1999. Кузьмина Р. И., Севостьянов В. П., Молина С. Е., Мухина Л. П. Катализатор для очистки газа от оксидов азота и углерода// Патент России № 2 162 011. 2001. Бюл. № 33.
24) Тимонин А. С. Инженерно-экологический справочник. Т.1. — Калуга: Издательство Н. Бочкаревой — 2003, ст.917
25) Ветошкин А. Г. Процессы и аппараты пылеочистки. Учебное пособие. — Пенза: Изд-во Пенз. гос. ун-та, 2005. - с.: ил., библиогр.