Деформационные процессы в полимерах при механопневмоформовании осесимметричных изделий
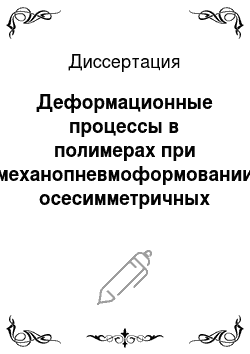
Диссертация
Вместе с тем, следует отметить, что наряду с отмеченными преимуществами комбинированные технологии термоформования полых полимерных изделий имеют и свои недостатки, приводящие к возникновению вполне определенных практических проблем. Эти проблемы связаны, во-первых, с проявлением с той или иной частотой специфического дефекта в виде разрушения полимерной заготовки (разрыв заготовки) в процессе… Читать ещё >
Список литературы
- Бартенев Г. М., Зеленев Ю. В. Курс физики полимеров. Л.: Химия, 1976. -288 с.
- Бердышев Б.В. Основы теории формования полых изделий из полимеров, методы расчета формующих элементов перерабатывающего оборудования. Дисс.. докт. техн. наук. М.:МГУИЭ, 1999. — 335 с.
- Бердышев Б.В., Скопинцов И. В. Термоформование изделий из плоских полимерных заготовок. -М.: МГУИЭ, 2001. 28 с.
- Бердышев Б.В., Басов Н. И., Кий К.И. Описания процесса формования экс-трузионных заготовок в полые изделия. «Машины и технология переработки каучуков, полимеров и резиновых смесей». -Ярославль: ЯПИ, 1980. с. 105 109.
- Бердышев Б.В., Скуратов В. К. К расчёту распределения толщин цилиндрических изделий в процессе их раздувного формования. «Машины и технология переработки каучуков, полимеров и резиновых смесей». -Ярославль: ЯПИ, 1983. с. 82−83.
- Бердышев Б.В. Теоретические основы процессов пневмо-и механоформо-вания полых изделий из полимерных материалов. «Пластические массы», 1991, № 3, с. 47−50.
- Бердышев Б.В. Методы производства тары и упаковки. «Полимерные материалы». 2001, № 5 (24), с. 2−5.
- Бердышев Б.В. Методы производства тары и упаковки. «Полимерные материалы». 2001, № 6 (25), с. 2−3.
- Бердышев Б.В., Смышляев А. Р. Оборудование для раздувного формования. Статья в энциклопедии машиностроения, том IV-12: Машины и аппараты химических и нефтехимических производств. М.: Машиностроение, 2004. с. 702−710.
- Бердышев Б.В. Термоформование: основные технологические методы и оборудование. «Пластике». 2005, № 6 (28), с. 28−31.
- Бердышев Б.В., Борисов А. А., Герасимчук И. А. Термодинамика и механика деформирования «сшитых» эластомеров. «Химическое и нефтегазовое машиностроение». 2005, № 6, с. 3−5.
- Борисов А.А., Герасимчук И. А., Кузьмин М. С., Михайлов А. Н. Термодинамика и механика деформирования сшитых эластомеров. Тезисы интернетг конференции творчество молодых в науке и образовании. Часть II. -М.:1. МГУИЭ, 2003, с. 20−24.
- Брагинский В. А. Термоформование это просто? «Пластике». 2005, № 6 (28), с. 24−27.
- Бражевская Т., Мошкина А. Исследование рынка родниковой бутилиро-ванной воды в отдельных регионах России. «Food. Производство продуктов питания». 1995, № 1, с. 56−57.
- Веселов В.А. Оборудования для переработки пластических масс в изделия. Тепловые расчёты. -М.: Машгиз, 1961. 212 с.
- Вульф М.А., Московский C.JL, Никитин Ю. В., Бухгалтер В. И. Расчёт разнотолщинности конических вакуум пневмоформованных изделий. «Пластические массы». 1978, № 7, с. 50−51.
- Вульф М.А., Московский C.JL, Никитин Ю. В., Бухгалтер В. И. Расчёт разнотолщинности цилиндрических вакуум пневмоформованных изделий. «Пластические массы». 1976, № 5, с. 34−36.
- Вульф М.А., Московский С. Д., Никитин Ю. В., Бухгалтер В. И. Уточнение расчёта разнотолщинности конических вакуум пневмоформованных изделий. «Производство и переработка пластмасс и синтетических смол». -М.: НИИПМ, 1977, Вып.2, с. 18−20.
- Годовский Ю.К. Теплофизика полимеров. -М.: Химия, 1982. -280 с.
- Грин А., Адкинс Дж. Большие упругие деформации и нелинейная механика сплошной среды. -М.: Мир, 1965. 445 с.
- Гуль В.Е. Перспективы развития технологии переработки пластмасс. «Проблемы эффективного применения пластмасс в народном хозяйство». Тез. докл. Всесоюзн. научн. -техн. конф. М., 1978. с. 93−96.
- Гуль В.Е. Полимеры сохраняют продукты. -М.: Знание, 1985. -127 с.
- Гуль В.Е., Беляцкая О. Н. Плёночные полимерные материалы для упаковки пищевых продуктов. -М.: Пищевая промышленность. 1968. 278 с.
- Ермаков Д.Б., Бердышев Б. В., Скуратов В. К. Математическое моделирование процесса механотермоформования полых изделий из плоских полимерных материалов. «Химическое и нефтегазовое машиностроение». 1998, № 5, с. 3−5.
- Казачок А.А. К расчёту пневматического формования цилиндрического стакана из пластического материала. «Химическое машиностроение». Рес-публ. межведомств, научн. -тех. сб. -К.: Техника. 1968. Вып.8, с. 110−113.
- Казачок А.А. К вопросу расчёта утонения стенки при пневматическом формовании конического стакана из пластичного листового материала. «Химическое машиностроение». Республ. межведомств, научн. -тех. сб. -К.: Техника, 1969. Вып.9, с. 39−43.
- Калинчев Э.Л., Саковцева М. Б. Выбор пластмасс для изготовления и эксплуатации изделий. Справочное пособие. Л.: Химия, 1987. — 416 с.
- Ким B.C. Теория и практика экструзии полимеров. М.: Химия, КолосС, 2005. — 568 с.
- Леонов А.И. Об описании реологического поведения упруговязких сред при больших упругих деформациях. -М.: Изд-во АН СССР, 1973. 63 с.
- Мак-Келви Д. М. Переработка полимеров. М.: Химия, 1965. — 444 с.
- Малков Г. А., Шерышев М. А., Трелль Н. Р. Критерий разнотолщинности при механопневматическом формовании листовых термопластов. «САПР оборудования для переработки полимерных материалов». Сборн. Нучн. Тр. -Ярославль:ЯПИ, 1989. с. 93−98.
- Муравин Я.Г., Толмачева М. Н., Додонов A.M. Применение полимерных и комбинированных материалов для упаковки пищевых продуктов. -М.: Аг-ропромиздат, 1985. -205 с.
- Оборудование для переработки пластмасс. Справочное пособие. Под. Ред. Завгороднего. В.К. -М.: Машиностроение, 1977. 407 с. г 38. Определение индекса расплава термопластов. Методические указания клабораторной работе. Москва, 1974. 16 с.
- Основы технологии переработки пластмасс. Под ред. В. Н. Кулезнева и В. К. Гусева. М.: Химия, 2004. — 600 с.
- Переработка пластмасс: Справочное пособие. Под редакции В. А. Брагинского -Д.: Химия, 1985. 296 с.
- Попова И.Н., Файнберг Е. Д., Лившиц Ю. Т. Экономика производства и применения полимеризационных пластмасс. JL: Химия, 1977. — 200 с.
- Реутов С.В., Скуратов В. К., Нагорнов А. И. Технико-экономические аспекты производства полых изделий из пластмасс. Сопоставительные обзорыпо отдельным производствам химической промышленности. -М.: НИИТЭ-ХИМ, 1970. Вып.16. 74 с.
- Салазкин К.А., Шерышев М. А. Машины для формования изделий из листовых термопластов. -М.: Машиностроение, 1977. 160 с.
- Скуратов В.К., Бердышев Б. В., Орлова JI.A. Исследование закономерностей раздувного полых осесимметричных изделий. «Теория механической переработки полимерных материалов». 3-й Всесоюзн. Симпоз. Тез. Докл. -Пермь, 1985. с. 169.
- Скуратов В.К., Бердышев Б. В., Филимонова О. Н., Волков Ф. А. Определение констант эластичности полимерных материалов. «Механика в химической технологии». :Сборник научных трудов. -М.: МХТИ, 1991. с. 49−55.
- Соломенко М.Г., Шредер B.JL, Кривошей В. Н. Тара из полимерных материалов. -М.: Химия, 1990. 300 с.
- Стрельцов К.Н. Переработка термопластов методом механопневмофор-мования. -Д.: Химия, 1981.-231 с.
- Стрельцов К.Н. Пневматическая переработка термопластов. —JL: ГХИ, 1963.- 176 с.
- Султанов Ф.М., Ярин A.JI. О Рэлей-тейлоровской неустойчивости раздуваемых полимерных плёнок. «ПМТФ», 1988. № 3, с. 104−110.
- Тагер А.А. Физико-химия полимеров-М.: Химия, 1968. 536 с.
- Торнер Р.В. Основные процессы переработки полимеров (теория и методы расчета). М.: Химия, 1972. — 456 с.
- Успехи реология полимеров. Под. Ред. Виноградова. Г. В. -М.: Химия, 1970.-293 с.
- Холм-Уолкер В. А. Переработка полимерных материалов. -М.: Химия, 1979.-304 с.
- Чернов М.Е. Упаковка макаронных изделий. -М.: Издательский комплекс МГУПП, 1997. 130 с.
- Шерышев М.А. Формования полимерных листов и плёнок. -JL: Химия, 1989.- 120 с. ц 57. Шерышев М. А. Расчет стабильности размеров термоформованных изделий. «Пластические массы», 1991, № 12, с. 43−45.
- Шерышев М.А. Технология формования объемных изделий из листовых и пленочных термопластичных материалов. «Пластике». 2005, № 6 (28), с. 3237.
- Шерышев М.А. Технологическая оснастка для термоформования. «Пластике». 2005, № 6 (28), с. 38−44.
- Шерышев М.А. Формовочные машины листовых и пленочных материалов. Статья в энциклопедии машиностроения, том IV-12: Машины и аппараты химических и нефтехимических производств. М.: Машиностроение, 2004, с. 710−718.
- Шерышев М.А., Ким B.C. Переработка листов из полимерных материалов. -JL: Химия, 1984. 216 с.
- Шерышев М.А., Пылаев Б. А. Пневмо-и вакуумформование. -Л.: Химия, > 1975.-96 с.
- Шерышев М.А. Разработка методов расчёта оборудования и процессов формования листовых термопластов и эластомеров. Дисс. .Докт. Тех. Наук. -М.: МИХМ, 1989.-410 с.
- Юдаев Б.Н. Техническая термодинамика. Теплопередача. -М.: Высшая школа, 1988.-479 с.
- Delorenzi H.G., Nied H.F. Blow molding and thermoforming of plastics. «Computers and Structures», 1987, v.26, N ½, p. 197−206.
- Dutta A., Ryan M.E. Confined parison inflation behavior of highdensity polyethylene. «Polymer Engineering and Science», 1984, v.24, N16, p. 1232−1239.
- Erwin L., Pollok M.A., Gonzales H. Blowing of oriented PET bottles. «Polymer Engineering and Science», 1983, v.23, N15, p.826−829.
- Fukase H., Iwawki A., Kunio T. A method of calculation the wall-thickness distribution in blow-molded articles. «SPE Tech. Papers», 1978, v.24, p. 650.
- Gabriele M.C. Thermoforming technology meets diverse requirements. «Modern plastics international», 1995, v.25, N.3, p.64−69.ш
- Grawford R.G., Lui S.K.L. Prediction of wall-thickness distribution in thermo-formed moulding. «Engineering Polymer Journal», 1982, v. 18, N8. p. 699−705.
- Hunkar D.B. Blow molding. «Modern Plastics International'', 1974, N4, p. 58−61.
- Lai M.O., Holt D.L. The extensional flow of РММЛ and HIPS at thermoform-ing temperatures. «Journal of Applied Polymer Science». 1975, v. 19. p. 1209−1220.
- Laun H. M. Prediction of elastic of polymer melts in shear and elongation. «Journal of rheology 1986, V. 30, N3, p. 459−501.
- Lee J.K., Virkler T.L. Scott C.E. Effects of rheological properties and processing parameters on ABS thermoforming. «Polymer Engineering and Science», 2001, v.41,N2,p. 240−261.
- Meissner J. Development of universal extensional rheomcter for the uniaxial elongation of polymer melts. «Trans. Soc. Rhco.», 1972. N3, p. 405−420.
- Myers J. Technical blow molding developments chart new horizons. «Modern
- Plastics International». 1995. v.25, N6, p. 52−54.
- Nam G.J., Ahn K.H. Lee J.W. Three dimensional simulation of thermoforming process and its comparison with experiments. «Polymer Engineering and Science», 2000, v.40, N10. p. 2232−2240.
- Nied H.F., Taylor С.Л. Delorcnzi H.G. Three dimensional finite element simulation of thermoforming. «Polymer Engineering and Science», 1990, v.30, N.20, p. 1314−1322.
- Poslinski A.J., Tsamopoulos J.A. Nonisothermal parison inflation in blow molding. «AIChE Journal». 1990, v.36, N12, p. 1837−1850.
- Rosenzweig N., Narkis M., Tadmor Z. Wall thickness distribution in thermoforming. «Polymer Engineering and Science», 1979, v. 19, N13. p. 946−951.
- Rush, et al. Methods and apparatus for vacuum/pressure thermoforming. «US Patent 5 641 524», 1997.
- Ryan M.E., Dutta A. The dynamics of free inflation at extrusion blow molding. «Polymer Engineering and Science», 1982, v.22, N9, p. 569−57.
- Throne J.L., Thermoforming. Hanser publishers, Munich, 1987.
- Vinogradov G.V., Mai kin A.I., Volosewitch V.V. Some fundamental problems in viscoelastic behavior of polymers in shear and extension. «Appl. Poly. Symp.», 1975, N27, p. 47−59.
- White J.L. Theoretical considerations of biaxial stretching of viscoelastic fluid sheets with application to plastic sheet forming. «Rheo. Acta». 1975, v. 14, p. 600−611.