Диагностирование зоны резания методами бесконтактного контроля при сверлении углеродсодержащих сплавов
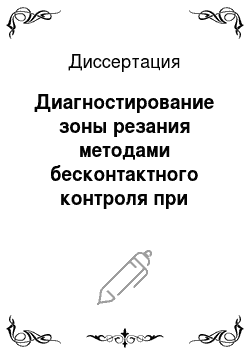
Необходимость применения метода газового анализа к диагностированию процесса сверления вызвана рядом причин. Во-первых, постоянный контроль зоны резания позволяет выработать полностью ресурс осевого режущего инструмента, что существенно снижает экономические затраты на РИ. Стойкость инструмента является случайной переменной величиной, которая может принимать для одного и того же типа инструмента… Читать ещё >
Диагностирование зоны резания методами бесконтактного контроля при сверлении углеродсодержащих сплавов (реферат, курсовая, диплом, контрольная)
Содержание
- Принятые обозначения
- ГЛАВА 1. АНАЛИЗ СОВРЕМЕННЫХ МЕТОДОВ ДИАГНОСТИРОВАНИЯ ЗОНЫ РЕЗАНИЯ. ЦЕЛЬ И ЗАДАЧИ ДИССЕРТАЦИОННОГО ИССЛЕДОВАНИЯ
- 1. 1. Подходы, используемые учёными, при описании явлений в механической обработке
- 1. 2. Обзор методов диагностирования зоны резания при сверлении
- 1. 2. 1. Акустические и виброакутические методы контроля
- 1. 2. 2. Методы теплового контроля
- 1. 2. 3. Силовые и геометрические методы контроля
- 1. 3. Применение метода газового анализа для диагностирования зоны резания
- 1. 4. Анализ работ, посвященных изучению влияния режимов резания на процессы газообразования в зоне резания
- 1. 5. Выводы по главе 1 и задачи диссертационного исследования
- ГЛАВА 2. МОДЕЛИРОВАНИЕ ПРОЦЕССОВ ГАЗООБРАЗОВАНИЯ В ЗОНЕ РЕЗАНИЯ ПРИ СВЕРЛЕНИИ
- 2. 1. Изучение природы диффузионных процессов и процессов газообразования при сверлении
- 2. 2. Разработка математической модели процесса газообразования в зоне резания при сверлении
- 2. 3. Исследование влияния параметров технологической системы на концентрацию образованных газов при сверлении
- 2. 3. 1. Влияние температуры резания
- 2. 3. 2. Влияние скорости резания
- 2. 3. 3. Влияние осевой подачи и глубины резания
- 2. 3. 4. Влияние обрабатываемого и инструментального материалов
- 2. 3. 5. Влияние износа режущего инструмента
- 2. 3. 6. Влияние геометрических параметров сверла
- 2. 3. 7. Влияние глубины сверления
- 2. 3. 8. Влияние основного технологического времени
- 2. 4. Выводы по главе 2
- ГЛАВА 3. ЭКСПЕРИМЕНТАЛЬНЫЕ ИССЛЕДОВАНИЯ ПРОЦЕССА СВЕРЛЕНИЯ С ИСПОЛЬЗОВАНИЕМ МЕТОДА ГАЗОВОГО АНАЛИЗА И ВИБРОАКУСТИЧЕСКОГО МЕТОДА
- 3. 1. Методика проведения экспериментальных исследований при сверлении с использованием метода газового анализа
- 3. 2. Построение математической модели процесса газообразования в зоне резания при сверлении
- 3. 3. Экспериментальные исследования влияния режимов резания на виброакустический сигнал при сверлении
- 3. 4. Результаты экспериментов по исследованию влияния режимов резания на виброакустический сигнал при сверлении
- 3. 5. Исследование влияния режимов резания на качество (шероховатость) поверхности при сверлении
- 3. 6. Выводы по главе 3
- ГЛАВА 4. АНАЛИЗ РЕЗУЛЬТАТОВ ТЕОРЕТИЧЕСКИХ И ЭКСПЕРИМЕНТАЛЬНЫХ ИССЛЕДОВАНИЙ
- 4. 1. Оптимизация режимов резания при сверлении
- 4. 1. 1, Расчёт оптимальных режимов резания при сверлении
- 4. 1. 2. Применение оптимальных режимов резания
- 4. 2. Сравнительная оценка результатов исследований ВА диагностики и метода газового анализа при сверлении
- 4. 3. Практическое использование результатов исследований
- 4. 3. 1. Область применения метода газового анализа
- 4. 3. 2. Методика бесконтактного определения температуры в зоне резания при механической обработке
- 4. 3. 3. Оценка производительности сверления при использовании метода газового анализа
- 4. 3. 4. Оценка экономической эффективности от использования метода газового анализа
- 4. 4. Выводы по главе 4
Актуальность темы
исследования.
В настоящее время обработка металлов резанием в большинстве отраслей промышленности составляет около 80−90% от всех выполняемых операций по обработке поверхностей деталей машин и, следовательно, оказывает решающее значение на темпы развития машиностроения.
Механическая обработка имеет ряд преимуществ по сравнению с другими методами обработки: достаточно высокая производительность при малых энергозатратах, возможность получения деталей любой формы и конфигурации с достижением требуемого качества поверхности.
Решающую роль в обеспечении этих преимуществ играет применение производительных и экономически обоснованных режимов резания. В частности, сейчас при сверлении выбор режимов резания определяется исключительно опытом и квалификацией рабочих. Машиностроительные нормативы 1990 года содержат усреднённые значения режимов резания. Появление новых инструментальных материалов для свёрл и комбинированных методов обработки вызывает необходимость разработки современных технологических рекомендаций по назначению режимов резания для сверления.
В то же время существует множество факторов, которые сдерживают назначение форсированных режимов резания при сверлении: температура резания, стойкость осевого режущего инструмента, вибрации и колебания, возникающие в ТС, кинематические характеристики станка и многие другие. Контроль этих факторов в процессе резания в допустимых диапазонах численных значений даёт эффективную механическую обработку на форсированных режимах резания.
В технологической системе инструмент является наиболее слабым звеном, а среди инструментов — сверло. Оно обладает малой жесткостью, в зону резания сложно подвести СОТС, стружка может многократно попадать на режущие кромки, её отвод затруднен. Сверление является процессом с ограниченной стабильностью, особенно при глубоком сверлении, когда физико-механические характеристики материала могут изменяться в широких пределах. Кроме того, партии поступающих на предприятие сверл не одинаковы по своим режущим способностям даже при закупках у одного и того же поставщика. Бывают случаи, когда целая партия новых свёрл не обладает заявленными параметрами и не может быть запущена в производство. И, наоборот, свёрла «хорошей» партии стараются использовать по максимуму, многократно их перетачивая, и вновь запуская в процесс обработки. В этом случае должна применяться комплексная диагностика зоны резания вследствие внезапного отказа или преждевременного износа сверла. Целесообразно использовать устройства бесконтактного контроля, которые могут быть оперативно установлены и настроены на станке. В связи с этим, комплексное исследование влияния параметров технологической системы на параметры диагностирования при сверлении является актуальной задачей.
На рис. 1.1 представлена структурная схема процесса резания, на которой обозначены параметры, определяющие ход процесса резания, а также параметры, обеспечивающие изготовление детали с заданными свойствами и геометрическими характеристиками.
Работа СД основана на контроле процессов, происходящих в зоне резания. Совокупность методов, устройств и средств диагностирования составляют систему диагностирования. Разработка составляющих СД и их внедрение в ТС, а также учёт большинства ограничивающих факторов процесса резания позволяют избежать катастрофического износа отдельных элементов ТС, отказов РИ, распространения высоких температур в зоне резания и во всей ТС, снижения надёжности работы оборудования в целом.
Необоснованное назначение сверхвысоких скоростей резания может привести к снижению стойкости РИ, возникновению колебаний в ТС, появлению вибраций, что будет способствовать снижению качества обрабатываемой поверхности, выкрашиванию режущей части сверла и, как следствие, преждевременному выходу инструмента из строя.
Рис. 1.1. Структурная схема процесса резания.
Наиболее эффективное решение указанной проблемы обеспечивается управлением механической обработкой с использованием ЭВМ, а также контролем состояния осевого режущего инструмента и его автоматической заменой при достижении заданной степени износа, при сколе или поломке или достижению заданного численного значения диагностируемого параметра.
Учёными разработаны устройства диагностирования, предназначенные для использования в составе систем контроля станков с ЧПУ и управления мехатронными системами [64, 74]. Эти устройства позволяют решать поставленные задачи в условиях неполной информации о внешней среде и внешнем воздействии, а также ограниченного использования обслуживающего персонала.
Совершенствование машиностроительного производства требует рационального использования технологического оборудования. Наличие «жесткой» управляющей программы, устанавливающей заданные режимы металлообработки и не учитывающей особенности обработки конкретной детали, является характерной особенностью для станков с ЧПУ.
Под эффективностью в настоящей работе понимается комплексный параметр, который обеспечивается достижением следующих показателей:
— повышение производительности сверления за счёт обоснованного применения форсированных режимов резания;
— сокращение основного технологического времени;
— снижение экономических затрат за счёт уменьшения времени отладки ТС, вызванной поломкой РИ.
Обеспечение выполнения этих показателей требует наличия в ТС быстродействующих точных приборов для измерения и поддержания параметров ТС. Принципы работы приборов основаны на различных явлениях и свойствах вещества. Особенностью измерений в этих приборах являются однозначные зависимости результатов измерений от параметров физико-химических процессов.
Одним из наиболее предпочтительных аналитических методов является метод анализа газов (метод газового анализа), образующихся при резании и уносимых из зоны резания вместе со стружкой. Измеряемым и контролируемым параметром, по которому проводится диагностика состояния осевого РИ, является концентрация газа, образованного в зоне резания.
Необходимость применения метода газового анализа к диагностированию процесса сверления вызвана рядом причин. Во-первых, постоянный контроль зоны резания позволяет выработать полностью ресурс осевого режущего инструмента, что существенно снижает экономические затраты на РИ. Стойкость инструмента является случайной переменной величиной, которая может принимать для одного и того же типа инструмента в одинаковых условиях эксплуатации различные значения [29]. Инструмент при эксплуатации на предшествующих условиях работы может приобретать неблагоприятную для последующих условий эксплуатационную наследственность [69]. Во-вторых, метод газового анализа позволяет назначать значения режимов резания выше нормативных значений и контролировать их по допускаемой температуре [5]. В-третьих, применение метода значительно повышает надёжность технологической системы за счёт замены инструмента до момента наступления его отказа, поломки или катастрофического износа. В-четвёртых, на производстве наблюдается тенденция к применению сухого резания как наиболее экологически чистого метода обработки, поэтому газовоздушная среда зоны резания изолирована от попадания в неё различных веществ, искажающих информацию о концентрации газов. По данным профессора Подгоркова, в настоящее время доля обработки без использования СОТС составляет 50%.
Повышение численных значений режимов резания неизбежно приводит к снижению качества обрабатываемой поверхности. При сверлении отверстия имеют 12−13 квалитет точности и шероховатость Ка 3,2-Й2,5 мкм, поэтому требований к высокому качеству отверстия, получаемых сверлением, технологи не предъявляют. Следовательно, форсирование режимов резания не приведёт к значительному ухудшению качества отверстия, из-за чего требовались бы дополнительные технологические операции или переходы. Следовательно, при оптимизации режимов резания качество обрабатываемого отверстия не является фактором, сдерживающим назначение более производительных режимов резания.
Использование метода газового анализа необходимо осуществлять после проверки достоверности и сходимости полученных результатов. Наиболее известным, достоверным и широко распространённым в резании является метод измерения виброакустического сигнала. Измеряемый ВА сигнал эквивалентен по амплитуде и частоте параметрам процесса резания, которые характеризуют НДС металла.
В данной работе предстоит определить степень соответствия данных о концентрации газа и параметров резания, характеризующих НДС технологической системы.
В диссертационной работе впервые представлены экспериментально-теоретические исследования диффузионных процессов и закономерности образования газообразных соединений, таких как СО, СОг в зоне обработки при глубоком сверлении, и связанная с этим методика бесконтактного контроля зоны резания, основанная на регистрации концентрации одного или нескольких газов.
Под глубокими отверстиями понимаются отверстия, длина которых равна пяти и более диаметрам.
В работе рассмотрена взаимосвязь между регистрируемыми в процессе резания ВА сигналом, температурой резания и процессами газообразования, происходящими в зоне резания. Определены основные закономерности, вызванные сменой или изменением ряда параметров ТС.
Работа представляет собой исследование процесса диффузии частиц металла, образования газов и их массопереноса в газовоздушном пространстве зоны обработки, характеризующих изменения состояния процесса резания, в том числе состояние осевого РИ.
Целью работы является повышение эффективности сверления углеродсодержащих сплавов за счёт выбора рациональных (оптимальных) режимов резания с использованием методов регистрации виброакустического сигнала и концентрации образованного в зоне резания газа.
Методы исследования: работа выполнена на основе фундаментальных положений теории резания металлов, законов физики и химии с применением методов математической статистики, математического моделирования, вычислительных экспериментов на реальных и модельных данных, математической обработки экспериментальных данных при помощи программ Excel и Maple.
Научная новизна:
— впервые разработаны математические модели, отражающие взаимосвязь концентрации газов, образующихся в зоне резания при сверлении углеродсодержащих сплавов, с параметрами технологического процесса;
— предложен метод расчёта численных значений режимов резания при сверлении с учётом особенностей реального состояния режущего инструмента и обрабатываемых заготовок;
— выявлена и оценена взаимосвязь между режущими характеристиками сверла, физико-механическими характеристиками заготовки, режимами резания и параметрами газообразования, виброакустического сигнала и шероховатости обрабатываемого отверстия;
— разработан оригинальный способ бесконтактного определения температуры в зоне резания при механической обработке, посредством которого можно получить экспресс-информацию о состоянии процессов в зоне резания.
Практическая ценность:
— разработаны алгоритм и программа управления режимами резания при глубоком сверлении углеродсодержащих сплавов на основе математического моделирования процессов газообразования;
— предложены и оценены методы бесконтактного контроля зоны резания по виброакустическому сигналу и концентрации газа;
— разработана методика контроля износа осевого режущего инструмента в процессе глубокого сверления на основе газового анализа.
Достоверность и обоснованность полученных в работе результатов подтверждена адекватностью разработанных моделей реальным физическим процессам, тщательной отработкой методик проведения и анализа результатов экспериментов, сходимостью результатов экспериментов. Результаты работы апробированы на производстве.
Внедрение результатов работы.
Теоретические и практические результаты диссертационной работы использованы на ЗАО «Новгородский машиностроительный завод «Энергия», ООО «ПИ-технология» Великий Новгород, о чём имеются соответствующие акты.
Положения, выносимые на защиту.
1. Алгоритм и программа управления режимами резания при глубоком сверлении углеродсодержащих сплавов на основе математического моделирования процессов газообразования.
2. Методика контроля износа осевого режущего инструмента в процессе глубокого сверления на основе газового анализа.
3. Оригинальный способ измерения температуры резания, позволяющего получить экспресс-информацию из зоны резания на основе метода газового анализа.
Апробация работы.
Основные научные результаты работы докладывались на следующих конференциях и семинарах:
— Дни науки Новгородского государственного университета имени Ярослава Мудрого — 2008, 2009, 2010, Великий Новгород;
— Международная конференция «Молодые учёные — промышленности Северо-западного региона» — 2009, Санкт-Петербург;
— Международная научно-практическая конференция «Новые технологии, автоматизация оборудования и оснастки машиностроительного производства» — 2008, 2009, Великий Новгород.
Публикации.
Основные теоретические положения и результаты исследований опубликованы в 9 научных работах, в т. ч. в 4 журналах, рекомендованных ВАК, 2 статьях в сборниках научных трудов международных конференций, 1 тезисах докладов конференций международного уровня, 1 патенте на изобретение, 1 отчёте (в 2 томах) о выполнении государственного контракта.
Диссертационная работа выполнена на кафедре «технологии машиностроения» Новгородского государственного университета имени Ярослава Мудрого и на кафедре «технологии машиностроения, металлорежущие станки и инструменты» Российского университета дружбы народов. Экспериментальные исследования выполнены в рамках государственного контракта №П2125 по федеральной целевой программе «Научные и научно-педагогические кадры инновационной России» на 20 092 013 годы. По тематике работы автором получен патент «Способ бесконтактного определения температуры в зоне резания при механической обработке».
Структура и объём диссертации.
Диссертация состоит из введения, четырех глав с выводами, заключения, списка литературы из 108 наименований и 2 приложений. Общий объем работы составляет 164 страницы печатного текста, 19 таблиц, 47 рисунков.
ОСНОВНЫЕ ВЫВОДЫ.
В работе решена научно-техническая задача, имеющая большое значение для промышленности и заключающаяся в повышении эффективности безаварийного сверления углеродсодержащих сплавов на основе применения методов бесконтактного контроля, основанных на регистрации виброакустического сигнала и концентрации образованного в зоне резания газа.
В процессе теоретического и экспериментального исследований получены следующие результаты и выводы:
1. Использование метода газового анализа увеличило продолжительность безаварийного сверления за счёт подбора рациональных (оптимальных) режимов резания, основанного на входном контроле состояния сверла и обрабатываемой заготовки. Снизилось время наладки станка на 1,5% от годового фонда времени работы станка. Максимально возможные рациональные режимы резания превосходят нормативные значения по производительности сверления для сверл из быстрорежущей стали — на 14%, для твердосплавных свёрл — на 30%. Произошло снижение основного технологического времени на 12% при обработке сталей сверлами Р6М5 и на 35% при обработке сверлами ВК8.
2. Опытным путём установлено однозначное влияние на концентрацию образованных газов в зоне резания таких параметров технологического процесса, как режимы резания, характеристики инструментального и обрабатываемого материала. Во всех графических и аналитических зависимостях наблюдалось повышение численного значения концентрации образованного газа с увеличением варьируемого параметра. Также параметр «концентрация образованного газа» инвариантен к вибрациям в кинематических цепях станка.
3. Впервые получены математические модели концентрации образованного газа от режимов резания при сверлении. Данные модели используются в широком диапазоне применяемых численных значений режимов резания: скорость резания Г=7^-47 м/мин., осевая подача 5=0,06^-0,36 мм/об., глубина резания /=2,55 мм. Расхождение экспериментальных и расчётных значений по математическим моделям не превышает 8%, что подтверждает адекватность полученных математических моделей.
4. Установлены закономерности поведения газообразования в зоне резания при отказах сверла: при сколе и поломке концентрация уменьшается, при износе увеличивается. Изученное в широком диапазоне численных значений режимов резания поведение диагностического параметра даёт возможность проводить обработку свёрлами ненадлежащего качества, в работе которых могут возникать частые отказы. Наличие системы диагностирования на основе метода газового анализа позволяет обнаружить отказ инструмента в 91% всех случаев. Экономический эффект от внедрения метода бесконтактного контроля на вертикально-сверлильном станке с ЧПУ составляет до 300 тыс. руб. при годовой программе выпуска N=7000 шт.
5. Представлены технологические рекомендации по выбору рациональных (оптимальных) режимов сверления, позволяющие максимально использовать ресурс стойкости сверла в режиме безотказной работы.
6. Используемый в работе метод виброакутической диагностики позволил выявить собственные частоты основных элементов станка, существенно влияющих на устойчивость процесса обработки. Это позволяет исключить режимы сверления, соответствующие собственным частотам элементов станка, из списка рекомендуемых, а также обеспечить стабильность процесса обработки.
Опытно-промышленными испытаниями, проведёнными в производственных условиях на ЗАО «Новгородский машиностроительный завод «Энергия» и ООО «ПИ-технология», подтверждена высокая эффективность разработанных рекомендаций по выбору форсированных (оптимальных) режимов резания при обработке стали 45.
Список литературы
- Аблапохин Ю.А. Исследование вибраций при точении и растачивании консольно закреплённых деталей: Автореф. дисс. канд. техн. наук. -Куйбышев, 1973. — 28 с.
- Адлер Ю.П., Маркова Е. В., Грановский Ю. В. Планирование эксперимента при поиске оптимальных условий. М.: Наука, 1976. — С. 93 — 102.
- Алёшин А.К., Гущин В. Г. Метод диагностики состояния инструмента // Вестник научно-технического развития. 2009. — № 2(18). — с. 3 — 6.
- Армарего И. Дж. А., Браун Р. X. Обработка металлов резанием. Пер. с англ. В.А. Пастунова. М.: Машиностроение, 1977. — 325 с.
- Афанасьев К.В. Использование метода газового анализа для активного контроля зоны резания при сверлении стали 45 на форсированных режимах // Журнал «Контроль. Диагностика». 2011. — № 4. — с. 49 — 51.
- Афанасьев К.В., Рогов В. А. Использование метода газового анализа для контроля температуры при сверлении. Журнал «Вестник РУДН», № 4, 2011. с. 35 — 40.
- Афанасьев К.В., Рогов В. А. Метод диагностирования состояния осевого режущего инструмента на основе информации о концентрации образованных газов в зоне резания // Научно-технический журнал СТИН. -М.-2011.-№ 9.-с. 16−20.
- Ахматов A.C. Молекулярная физика граничного трения. М.: Наука, 1963.-472 с. 1 СП13