Комплексное исследование влияния вакуумирования на размерно-геометрическую точность и физико-механические свойства моделей и оболочковых форм с целью получения качественных точных отливок в литье по выплавляемым моделям
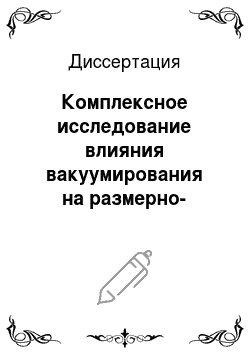
Диссертация
Ввиду специфичности стоматологических, ювелирных и др. видов мелких высокоточных изделий устранение брака отливок очень проблематично. Конструктивные элементы такого типа отливок имеют крайне ограниченные размеры, тонкие стенки и сложную конфигурацию, но они должны выдерживать определенную функциональную нагрузку. Поэтому, иногда даже малозаметный дефект в отливке делает все цельнолитое изделие… Читать ещё >
Список литературы
- Литье по выплавляемым моделям. / Под ред. Я. И. Шкленника и В. А. Озерова. М.: Машиностроение, 1984. — 408 с.
- Богословский С.Д. Литье мелких стальных деталей по выплавляемым моделям. М.: Машиностроение, 1982. — 72 с.
- Специальные способы литья. Справочник / В. А. Ефимов, Г. А. Анисович, В. Н. Бабич и др. Под общ.ред. В. А. Ефимова. М.: Машиностроение, 1991. -436 с.
- Лакеев A.C. и др. Прогрессивные способы изготовления точных отливок. К.: Техника, 1984. — 160 с.
- Высокочастотное литье в зубопротезной технике. М.: Медицина, 1977.—142 с.
- Степанов Ю.А., Баландин Г. Ф., Рыбкин В. А. Технология литейного производства: Специальные виды литья. Учебник для вузов. М.: Машиностроение, 1983. — 251 с.
- Евстигнеев А.И., Тимофеев Г. И., Сапченко И. Г. и др. Совершенствование технологических процессов формообразования керамических форм. Хабаровск, 1989. — 48 с.
- Лакеев A.C. Формообразование в точном литье. Киев: Наукова думка, 1986.-256 с.
- Дошкарж И., Габриэль А., Гоушть М. и др. Производство точных отливок. -М.: Машиностроение, 1980. 296 с.
- Гаранин В.Ф., Климкин Ю. И. Теплофизические характеристики воскоподобных модельных материалов // Вопросы теории и технологии литейных процессов. Комсомольск-на-Амуре, 1985. — С. 92−95.
- Хориути Н., У гота К., Мюрита Я. Точное литье крупногабаритных отливок// Имоно, 1984. -С. 110−115.
- Евстигнеев А.И. Управление деформационной устойчивостью оболочковых форм по выплавляемым моделям. // Автореф. дис. доктора техн. наук. Владивосток. — 1996. — 45 с.
- Куренков В.И. Управление структурой и свойствами оболочковых форм по выплавляемым моделям // Автореф. дис. канд. техн. наук. -Комсомольск-на-Амуре. 1996. — 24 с.
- Жилин С.Г. Управление структурой и свойствами пористых комбинированных удаляемых моделей // Автореф. дис. канд. техн. наук. -Комсомольск-на-Амуре. 2002. — 19 с.
- Шуляк В.С., Рыбаков С. А., Григорян К. А. Производство отливок по газифицируемым моделям / Под ред. проф., д.т.н. В. С. Шуляка М.: МГИУ, 2001.-330 с.
- Писарев И.Е. Одна оценка шероховатости поверхности оболочковых форм по выплавляемым моделям // Изв. вузов. Машиностроение. 1985. № 5. -С.110−116.
- Писарев И.Е., Писарев О. И. О размерной точности оболочковых форм по выплавляемым моделям // Изв.вузов. Машиностроение. 1985. № 7. — С.97−101.
- Писарев И.Е., Писарев О. И. О шероховатости поверхности оболочковых форм и керамичесих стержней // Рукоп. деп. в ВНИИТЭМР2806.88. № 233 -мш.88.
- Писарев И.Е., Писарев О. И. Еще раз о шероховатости поверхности оболочковых форм и керамичесих стержней // Рукоп. деп. в ВНИИТЭМР0604.89. № 136-мш.89.
- Сокол И.Б. Обжиг и заливка оболочковых форм, изготовленных по выплавляемым моделям. // Взаимодействие литейной формы и отливки: Сборник. М.: АН СССР, 1962. — С.326−332.
- Иванов В.Н., Чулкова А. Д. и др. Снижение времени прокаливания формы из кристаллического кварца. // Повышение качества и эффективности литья по выплавляемым моделям. М.: МДНТП, 1981. — С. 64−72.
- Тимофеев Г. И., Евстигнеев А. И. и др. О термостойкости армированных форм в литье по выплавляемым моделям. // Повышение качества отливок и слитков. Горький, 1981. — С.86−91.
- Брайнин М.И., Маценко А. П., Юдин В. В. Увеличение термостойкости оболочковых форм в литье по выплавляемым моделям // Литейное производство. 1982. № 7. — С.37−38.
- Руденко А. А., Рыбкин В. А. Применение пористых огнеупорных материалов в оболочковых формах, полученных по выплавляемым моделям // Литейное производство. 1979. — № 2. — С. 18−20.
- Голеников Ю.В., Рыбкин В. А. Оценка деформаций оболочковых форм при заливке // Литейное производство. 1989.- № 7.- С.17−18.
- Добродеев В.В., Воздвиженский В. М., Кудрявцева Е. Е. Повышение качества отливок при литье по выплавляемым моделям. // Новые высокопроизводительные технологические процессы. Киев, 1986. — С. 110 111.
- Добродеев В.В., Воздвиженский В. М., Кудрявцева Е. Е. Повышение точности графитовых форм по выплавляемым моделям. // Эконом, мет. при констр. И про-ве отливок. Вып.1. Пенза, 1986. — С.17−20.
- Евстигнеев А.И., Латухин А. Ю. К вопросу напряженно-деформированного состояния ОФ по выплавляемым моделям // Совершенствование технологических процессов и оборудование в литейном производстве. Хабаровск, 1989. — С. 107−114.
- Лозингер В.А. Повышение термостойкости оболочек для литья по выплавляемым моделям. // Автореф. дис. канд.техн.наук. Киев. — 1985.-18 с.
- A.c. 458 390 СССР. В 22 С 9/12. Выплавляющий водный раствор для удаления легкоплавких моделей из керамической формы. / Ю. С. Ислантьев, Н. П. Фролов. Опубл. 1975. Бюлл. № 4.
- Иванов В.Н., Чулкова А. Д. Разделение выплавляющей среды и модельной композиции. // Литейное производство. 1974. — № 4. — С. 37−38.
- Заявка 57−17 156. Япония. МКИ В 22 С 9/04 / Морита Ясухору. -Опубл. 12.02.81.
- Заявка 57−17 158. Япония. МКИ В 22 С 9/04 / Морита Ясухору. -Опубл. 12.02.81.
- Волокнистые композиционные материалы. / Под ред. С. З. Бокштейна. -М.: Мир, 1967.-284 с.
- Будников Н.П., Ливинский Ю. Е. Новые керамические материалы. -М.: Знание. 1968.-48 с.
- A.c. 1 139 560 СССР. В 22 С 9/04. Способ изготовления оболочковых форм, полученных по выплавляемым моделям. / И. Е. Писарев, В. М. Рогожин, О. И. Писарев. № 3 607 964/22 — 02- Заявл. 17.06.83- Опубл. 1985. Бюлл. № 6.
- Евстигнеев А.И., Тимофеев Г. И., Сапченко И. Г. Барботажная технология и установки приготовления связующих растворов и суспензий для ЛВМ. Владивосток: ИМиМ ДВО РАН, 1997. С.234−246.
- Евстигнеев А.И., Тимофеев Г. И., Сапченко И. Г. Проектирование и расчет пневмоустановок для приготовления связующих и суспензий. // Литейное производство. 1985. — № 9. — С.22−23.
- Евстигнеев А.И., Чернышов Е. А., Сапченко И. Г. Некоторые направления и предпосылки проектирования барботажных перемешивающих аппаратов. // Повышение качества и эффективности литья по выплавляемым моделям. М.: МДНТП, 1986. — С.99−106.
- A.c. 1 196 100 СССР. В22 С9/04. Способ приготовления суспензии и установка для его осуществления. / В. И. Уваров, Е. А. Чернышов и др. Опубл. 1985. Бюлл. № 45.
- Евстигнеев А.И., Чернышов Е. А. Установки приготовления связующих растворов и суспензий для керамических оболочковых форм. // Литейное производство. 1984. — № 5. — С.20.
- Евстигнеев А.И., Сапченко И. Г. Основные процессы и аппараты приготовления связующих растворов и суспензий в точном литье по постоянным моделям. // Повышение эффективности литейных процессов и качества отливок. Хабаровск: КнАПИ, 1986. — С.115−130.
- Евстигнеев А.И., Васин В. В., Черномас В. В. и др. Модель технологического процесса и установок приготовления связующих растворов и суспензий. // Управление строением отливок и слитков. Горький, 1989. -С.95−101.
- Сапченко И.Г., Петров В. В., Евстигнеев А. И. Тепловые процессы управления пористостью структур ОФ в ЛВМ. // Прикладные задачи механики деформируемого твердого тела: Сб. науч. трудов. Владивосток: ИМиМ ДВО РАН, 1997. -С.234−246.
- A.c. 1 135 528 СССР. МКИ В 22 С 9/04, 9/12. Способ изготовления литейных форм по выплавляемым моделям. / Пиевский И. М., Шпильский А. Б. -Опубл. 1985. Бюлл. № 3.
- Магницкий О.Н., Пирайнен В. Ю. Художественное литье: Учебник для >— технических вузов и художественно-реставрационных училищ. СПб.:1. Политехника, 1996.-231 с.
- Точное литье. GIFA 84: Fein und Genaugie? verfahren. Buchen Wolfgang. // «Giesserei», 1984, 71 № 21, 832−837,2.
- Л.Г. Знаменский. Вакуумно-ультразвуковая дегазация гипсовых смесей в точном литье. // Литейное производство. 2002. — № 10. — С.26−27.
- Применение процессов заливки форм с использованием вакуума. Reynolds Y. A. «Ghh World Conf. Investment Cast., Washington, D.C., Oct. 10−13, 1984» S.Y., s.a., V. 3/01 3/07.
- Пат. 4 791 977 США. МКИ 4 В22 Д18/06. Способ изготовления отливок. Chondley George D.- Metal Casting Technology. № 47 907- Опубл. 20.12.88- НКИ 164/63.
- A.c. 1 214 313 СССР. МКИ В22 С9/12. Способ сушки форм, получаемых по выплавляемым моделям./ Бутцева JI.H., Бутцев А. Н. Опубл./ 1986. Бюлл. № 8.
- Шагеев З.А. Современные скоростные способы точного литья по выплавляемым моделям. М.: МАИ. — 1970. — 107 с.
- Курепин В.И. Трещинообразование в ОФ при выплавлении модельного состава. // Литейное производство. 1983. -№ 11.- С.21−22.
- Евстигнеев А.И. Управление деформационной устойчивостью ОФ по выплавляемым моделям. // Автореферат дис.д.т.н. Владивосток. — 1996. — 45 с.
- Васин В.В. Исследование процессов формообразования оболочки повыплавляемым моделям и их влияние на свойства форм. // Авторефератдис.к.т.н. Комсомольск-на-Амуре. — 1996. — 20 с.
- Ферштатер И.Б. Низкотемпературное прокаливание ОФ. // Литейное производство. 1985. — № 10. — С.20−21.
- Заявка 6 328 044 Япония. МКИ В22 С9/04 / Минами Йоити-ро. Опубл. 06.02.87.
- Reynolds Y.A. The scrata replicact process advances in shell-moulding techniques // Six world conf. Investment cast. Washington. — 1984. — P. 10−13.
- A.c. 1 197 767 СССР. МКИ B22 C9/04, B22 Д18/06. Способ получения отливок в оболочковой форме и литейная форма для его осуществления. / Ефремов С. А., Пушкарев A.A., Ткаченко В. Н. Опубл. 1985. Бюлл. № 46.
- Cost effective investment costing of thin Sections the CLA — process. Recaldin A.Y. «Des. Eng» (Gr. Brit.), 1985, Oct., 149,153,157 (англ.)
- Литье по выплавляемым моделям в вакууме. Prazision aus dem
- Vakuum: Aluminiumfeingussniit hoher Oberflachengute und Massgenauigkeit. Lorch D., «Aluminium», 1988, 64 № 5, 500−501 (нем.)
- Применение CLA процесса. Some developments in investment castings. Recaidin A.J. «Stainless Steel Ind.,» 1984,12. — № 69, 12−15 (англ.)
- Литье по выплавляемым моделям. Nichigori Toruro. «Umono, J. Japan, Fourdrjmen ¦ s Soc.», 1987, 59, № 1, (9−15) япон.
- Заливка керамических оболочковых форм. Klement Josef. Slevarens tvi, 1986, 34 № 9, 377−381.
- A.c. 1 310 098 СССР. B22 C9/04. Способ изготовления форм по выплавляемым моделям / Ю. П. Васин, Т. М. Евсеева и др.- № 3 915 600/31−02- Опубл. 1987. Бюлл. № 18.
- Заявка 56−148 440 Япония. МКИ В 22 С 7/02 / Кубота Кацуеси // Дайсэру кагаку коге к.к. 1981.
- Заявка 57−165 156 Япония. MICH В 22 С 7/02 /Мураки Минору // Дайсэру кагаку коге к.к. 1982.
- A.c. 1 214 321, СССР. МКИ В 22 Д 18/06. Устройство для заливки под вакуумом литейных форм. / Филимонова В. Н., Ченцов A.C., Петров А. Н., Жданов Г. С. Опубл. 1986. Бюлл. № 8.
- Одиноков В.И. Численное исследование процесса деформации материалов бескоординатным методом. Владивосток: Дальнаука, 1995. 168 с.
- Одиноков В.И. Численное исследование процесса деформации материалов бескоординатным методом. Владивосток: Дальнаука, 1985.- Т.21. -№ 1. -С.97−102.
- Петров В.В., Аласкаров Н. И., Одиноков В. И. Расчет напряжений и деформаций в оболочковой форме при затвердевании отливки. // Литейное производство.- 2000. № 3. — С.53−55.
- Сапченко И.Г., Штерн М. В. Расчет напряжений и деформаций в оболочковой форме при затвердевании отливки // Сборник «XXI Российская школа по проблемам науки и технологий. Краткие сообщения. Екатеринбург: УрО РАН. — 2003. — С.263−265.
- Рыжков Н.Ф., Гини Э. Ч. Литье методом вакуумного всасывания.- М.: Машиностроение, 1982−95 с.
- Сапченко И.Г. Управление пористым строением и свойствами оболочковых форм в литье по выплавляемым моделям // Автореферат дис.канд.техн.наук. Н.Новгород. — 1991. — 24 с.
- Одиноков В.И. Численный метод решения дифференциальных уравнений пластического течения // Прикладная механика. 1973. — Вып.9.№ 12.
- Одиноков В.И. Численное решение некоторых задач о деформации несжимаемого материала // Прикладная механика. 1974. — Вып. 10. — № 1.
- Одиноков В.И., Песков A.B. Методика расчета напряжений и деформаций при упругой и упруго-пластической деформации: Учеб. пособие / Свердл. инж.-пед. ин-т, Свердловск 1989. — 36 с.
- Щур В. А. Современные методы контроля и исследования процессов литья по выплавляемым моделям. — М.: НИИМАШ, 1970.- 72 с.
- Медведев Я.И., Валисовский И. В. Технологические испытания формовочных материалов. М.: Машиностроение, 1973. — 310 с.
- Гуляев В.В., Корнюшкин O.A., Кузин A.B. Формовочные процессы. -JL: Машиностроение: Ленинградское отделение, 1987. 264 с.
- Литье вакуумным всасыванием. Койке Сусуку, Хироеэ Иосиоки: к.к. Кобэ сэйкосе. Япония. Заявл. 13.11.85 № 60−255 786, опубл. 26.05.87 МКИ В 22- ' Д 18/06.
- Способ литья вакуумным всасыванием и устройство для его ^ осуществления. Уодзумо Минору, Масаока Тосино и др. Тоета дзидося к.к.1Г311ПЗаявка62−33 051,Япония. Опубл. 13.02.87. МКИВ22 Д 18/06
- А.с. 39 668 НРБ, МКИ 2 В 22 С 9/ 00/ Кирилов Кирилл Любенов- Висш. Машиино-електротехн. Институт «В.И. Ленин» № 69 698- Заявл. 11.04.85- опубл. 29.08.86. Способ изготовления оболочковых форм.
- Borsan Alex Литье по выплавляемым моделям художественных изделий Metallurgia, 1970,22, № 9, 566−567.-V/