Совершенствование технологии изготовления керамических форм для литья по выплавляемым моделям
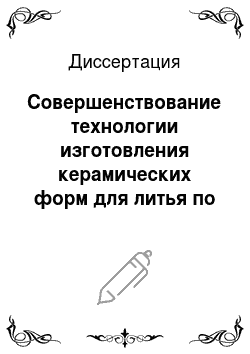
Диссертация
Установлено, что более характерный отрыв по второму слою (рис. 5.2-по линии «б») связан с его недостаточной просушенностью. По оценкам изломов керамики, выполненным с помощью отсчетного микроскопа (применяется при оценках твердости по Бринелю), толщина второго слоя составляла обычно 1,0−1,5 мм. Удаление большей части растворителя из слоя суспензии исследуемого состава толщиной 1,0 мм требует… Читать ещё >
Список литературы
- Шкленник Я.И., Озеров В. А. Литье по выплавляемым моделям:3-е изд., перераб. и доп. -М. Машиностроение, 1984, с. 407.
- Шкленник Я.И., Озеров В. А. Литье по выплавляемым моделям :Инженерная монография: 2-е изд., перераб. и доп.
- М. Машиностроение, 1971, с. 436.
- Чулкова А.Д. и др. Опыт внедрения в производство низкокремнистого этилсиликатного водного связующего «ЗИЛ-ЭФ» // Литейное производство, 1977, № 4,20−22.
- Иванова Т.В. и др. Интенсификация отверждения этилсиликатного связующего без органических растворителей // Литейное производство, 1988, № 12,26−27
- Кириллова Т.М. и др. Повышение качества поверхности отливок по выплавляемым моделям при использовании бесспиртового этилсиликатного связующего // Литейное производство, 1984, № 1,
- Полывъяный В.П. и др. Отечественное готовое связующее для изготовления форм по выплавляемым моделям // Литейное производство, 1990, № 8,13−14
- Повышение производительности конвейерных линий за счет увеличения скорости сушки слоев / отчет Харьковского филиала ВНИИЛИТМАШ, 1988, № гос. регистр. 2 880 006 865
- Попов А, Д. Поверхостные и подкорковые газовые раковины в стальных отливках/Литейное производство, 1975, № 7,стр.24−26.
- Перевозчиков Э.П., Баженова Н. Е. Совершенствование процесса прокаливания форм литья по выплавляемым моделям // Литейное производство, 1978. № 10, с. 29.
- Мамлеев Р.Ф.ДНпиндлер С.С., Неуструев A.A. Исследование заполнения жаропрочным сплавом оболочковых форм по выплавляемым моделям./УИзвестия вузов. Черная металлургия., 1986. -№ 9. -с. 103−107.
- Совершенствование технологии получения титанового и стального литья по выплавляемым моделям, с целью повышения выхода годного. :отчет по НИР ВФ 1−85, № гос. регистрации 01.850 004 400, Воткинск, 1988.
- Сазонов В.А., Александров JI.B. Анализ информации в области технологии изготовления литейных форм ваакумно -пленочной формовкой. // Литейное производство, 1988, № 8,стр.27.
- A.c. 759 204 (СССР) Способ изготовления керамической формы по выплавляемым моделям./ Руденко A.A., Рыбкин В. А., опубликовано в Б.И., 1980,№ 32.
- Руденко A.A., Рыбкин В. А. Применение пористых материаллов в оболочковых формах получаемых по выплавляемым моделям. // Литейное поизводство, 1979, № 2, стр. 18.
- A.c. 1 011 326 (СССР) Способ прокаливания оболочковых форм по выплавляемым моделям./ Ферштатер И. Б., Тишков В. Н., Патракеев Н. И., опубл в Б.И., 1984, № 14
- Патент 56−56 756 (Япония) Способ изготовления форм по выплавляемым моделям. / Тиба Нобуюки и др., опубликовано 18.05.81.
- Патент 57−11 748 (Япония) Способ изготовления форм по выплавляемым моделям. / Тиба Синка и др., опубликовано 21.01.82.
- Изготовление форм по выплавляемым моделям. Shell moulds Adam Dunlop. Англ. патент. В 29 С 1/02, опубл. 23.09.70
- Совершенствование технологии получения титанового и вольфрамового литья с целью улучшения его качества и повышения выхода годного/Отчет по НИФ ВФ 1−80,руководитель Малыгин Ю. Д., г. Воткинск, 1984 г.
- A.c. 1 183 283 (СССР) Способ изготовления оболочковых форм по выплавляемым моделям /Малыгин Ю.Д., Тарасов В.Г.ДПиробоков В.М., другие. 1985.Б.И. № 37.
- A.c.856 647 (СССР) Способ прокалки литейных керамических форм получаемых по выплавляемым моделям/ Перевощиков Э. П., Баженова И. Е., опубл. в Б.И., 1882 ,№ 31
- Танкелевич Б.Ш., Демидова A.A., Абадаев A.B. Газовыделение при прокаливании форм с этилсиликатным связующим // Литейное производство, 1979, № 12,21−22
- Евстигнеев А.И., Дмитревскй И. П., Васин В. В. Расчет времени выплавления моделей. //Известия вузов. Черная металлургия. -1992. -№ 10. -с.28−32.
- Евстигнеев А.И., Дмитревскй И. П. Влияние многослойности оболочковых форм на кинетику выплавления моделей.//Совершенствование процессов формообразования в литейном производстве. -Комсомольск-на-Амуре.-1994. -С.-110−114.
- Баркова Л. С. Дуренин В.И., Перевозкин Ю. Л. Расчет температурных режимов для выплавления модельного состава при точном литье. // Литейное производство,!981, — № 3. -с.20−21.
- Патент 49−9014 (Япония) Способ удаления моделей из форм. / Ямамото Ясунобу и др., МКИ В 22 С 7/00,опубликовано 1.03.74.
- A.c. 977 099 (СССР) Способ удаления модельного состава из оболочковых форм. /Озеров В.А., Гаранин В. Ф., Шприц Б. Б. и др.,, опубликовано в Б.И.,№ 44,1982.
- Педымов А.Н., Грижицкий М. В. Исследование поцесса вытопки модельных составов в поле токов высокой частоты. //Электротехника. -1982. -№ 8. -с.29−31.
- Литье по ледяным выплавляемым моделям. Casting with ise Patterns. / Heine J. //Fonndy Manag. andTechnol. -1992. -№ 11. -cl7.
- A.c. 1 311 838 (СССР) Способ приготовления водного раствора для выплавления легкоплавких моделей из оболочек форм / Чулкова А. Д., Яковлева Г. В., Касаткин А. Н., опубл в Б.И., 1987, № 19.
- A.c. 1 088 863 (СССР) Способ удаления модельного состава из оболочковых форм. /Киреевский Б.А., Чихаев В. В., Приступа А. И. и др., опубликовано в Б.И., 1984,№ 16.
- Гузман В.М., Василевский Ю. И. Интенсификация газовоздушного выплавления моделей из керамических форм. // Литейное производство,-1986. -№ 9. -с.29−30.
- Кулаков Б.А., Дубровин В. К., Кулаков А. Б. Пути снижения дефектности отливок из никелевых сплавов при литье по выплавляемым моделям. // Литейное производство, 1995, № 10, с.24−25
- АТэн Э. Б. Повышение качества отливок по выплавляемым моделям, фильтрованием //Материалы семинаров: Повышение качества и эффективности литья по выпловляемым моделям.-М.:0-во «Знание» РСФСР, 1989.-С119−125.
- Сургучев А.Н., Пушкаренко А. В., Свшценко A.A. и др.Применение фильтрования в литье по выплавляемым моделям ./Днепрозержинский индустриальный институт Днепрозержинск, 1989.-5с.,-ДЕП. в УкрНИИИНТИ, 25.08.89, № 2091-Ук 89.
- A.c. 1 400 764 (СССР) Устройство для обработки воздухом нагретых форм, для литья по выплавляемым моделям. /Серебряков С.П., Пирашвили Ш. А., Новиков H.H. и др., опубликовано в Б.И., 1988,№ 21.
- Серебряков С.П., Чеканов A.B. Активное инжектирование форм, прокаливаемых в опорном наполнителе. // Повышение качества и эффективности литья по выплавляемым моделям. М.: Знание, 1986. -с.111−116.
- Шипулин И.В. Предотвращение засоров в отливках по выплавляемым моделям. //Литейное производство, 1969.-№ 5.-с.40−41.
- Иванова Т. В, Танкелевич Б. Ш., Абадаев A.B. и др. Повышение прочности этилсиликатных керамических форм // Литейное производство, 1984, № 3, с.20−21.
- A.c. 1 238 880 (СССР) Суспензии для изготовления оболочковых литейных форм по выпловляемым моделям. /Александров В.М., Кулаков Б. А., Солодянкин A.A. и др., опубликовано в Б.И., 1986.-№ 23.
- Нечитайлов Г. И., Васильева Н. Ф., Власова М. С. Повышение качества комбинированных оболочковых форм //Литейное производство, 1989,№ 4,-с.34
- Лакеев A.C. Формообразование в точном литье. Киев.: Наукова думка, 1986, — 256с.
- Евстигнеев А.Н. Классификация., анализ и пути снижения брака отливок по засору в литье по выплавляемым моделям.//Вопросы теории и технологии литейного производства-Комсомольск-на-Амуре, 1985-с.86−92.
- Зарецкая Г. М., Иванов В. Н., Яковлева Г. В. и др Антииспарители при литье по выплавляемым моделям // Литейное производство, 1971, № 2, с 34
- Малыгин Ю.Д. и др. Оценка прочности форм по выплавляемым моделям, методом межслойного отрыва. //Авиационная промышленность. -1989.-№ 11.-с.
- A.c. 1 696 099 (СССР) Способ изготовления многослойных форм по удаляемым моделям. /Малыгин Ю.Д."опубликовано в Б.И., 1995,№ 33.
- A.c. 863 141 (СССР) Суспензия для изготовления литейных керамических форм по выплавляемым моделям./Ковалев А.С., Одинец В. С., опублик. в Б.И., 1981.,№ 34.
- A.c. 884 822 (СССР)Суспензия для изготовления литейных керамических форм по выплавляемым моделям/ Осилчик В.С.ДСлинова Л.В., Акутин М. С. и др., опубликовано в Б.И.1981, № 44.
- A.c. 884 221 (СССР) Суспензия для изготовления огнеупорных литейных форм по выплавляемым моделям/ Ежов Т. В., Томолов В .И., Гречко В. Н. и др., опубликовано в Б.И., 1981, № 44.
- A.c. 880 607 (СССР) Суспензия для изготовления литейных керамических форм получаемых по удаляемым моделям/Максилеков В. Н. Романов А.Д., опубликовано в Б, И, 1981, № 42.
- A.c. 637 191.(СССР) Огнеупорная суспензия для изготовления форм по выплавляемым моделям. /Кашуба Н.А., Писаренко Л. З., Горецкая М. Г. и др, опубликовано в Б.И., 1978. № 46.
- A.c. 688 271 (СССР) Суспензия для изготовления огнеупорных керамических форм по выплавляемым моделям./Погребняк Д.А., Сасова С. П., опубликовано в Б.И., 1979 ,№ 36.
- Иванова Т.В., Танкелевич Б. Ш., Абадаев A.B. и др. Повышение прочности этилсиликатных керамических форм. // Литейное производство, 1984,№ 3,с. 20−21.
- A.c. 1 238 880 (СССР) / Суспензии для изготовления оболочковых литейных форм по выплавляемым моделям / Александров В. М., Кулаков Б. А., Солодянкин A.A. и др., опубл Б. И 1986, № 23
- Уваров Б.И., Озеров В. А., Чернышев Е. А. Использование перекиси водорода в процессе приготовления этилсиликатной суспензии / Повышение качества и эффективности литья по выплавляемым моделям, об-во Знание РСФСР, 1989,42−46.
- Клименчук Л.В., Сыч Б.И., Жукова З. Д. и др. Исследование оболочковых форм с алюмохромофосфатным связующим //Литейное производство, 1986 -№ 7.-179.
- A.c. 1 653 888 Способ подготовки этилсиликата / Крылов В. М. и др., опубл. в Б. И, 1991, № 21
- A.c. 33 181 (НРБ) Способ изготовления форм по выплавляемым моделям /Попов Цочо Цветков, Керванбашиев Стою Петков, МКИ В 22 С 9/04,опубликовано 30.12.87.
- A.c. 554 660 (СССР) Обсыпочный материал доя изготовления керамических форм для литья по выплавляемым моделям / Лакеев A.C., Борисов Г. П., Марченко В. Е. и др., опубл в Б.И., 1977, № 4
- Тимофеев Г. И. Сапченко И.Г., Евсеев А. И. Армирование оболочковых форм вспученным перлитом//Литейное производство,!991-№ 6, — 30−31.
- Шипулин Н.В. Упрочненные формы при литье по выплавляемым моделям // Литейное производство, 1969, № 12., с 32−33.
- A.c. 900 478 (СССР) Способ изготовления литейных форм по выплавляемым моделям ./Чирков А. А., Черкасова П.А.ДСонотопов B.C., опубл. вБ.И.-1981.--№ 34.
- A.c. № 801 959 (СССР) Раствор для пропитки форм получаемых по выплавляемым моделям/Табунов С .А., Градополов A.C., Нейфак Е. В., опубл. в Б. И, №
- Шур В. А. Современные методы контроля и исследования процессов литья по выплавляемым моделям. М.: МДНТП, 1970,72с
- А.с. 851 177 (СССР) Образец для определения механических свойств оболочковых форм, материала и покрытия для оболочковых форм / Лакеев А. С., опубл. в Б.И., 1981, № 28
- Озеров В.А. Методы испытания оболочек : Литье по выплавляемым моделям, М.: Машгиз, 1959,25с
- Иванов В.Н., Чулкова А. Д., Булатов Ю. Б. Контроль и методы исследования процесса получения оболочковых форм при литье по выплавляемым моделям // Литейное производство, 1976, № 9, с 25−28
- Контроль качества огнеупорных покрытий для точного литья .-Бошкку ТгаёеЛ, 1975,139 № 3069, с 466−470
- Основы научных исследований: Учеб. для техн. вузов / Кругов В. Н., Грушко И. М., Попов В. В. и др.- под ред. Крутова В. Н, М.: Высш. шк., 1989., 400с
- Новик Ф.С., Арсов Я. Б. Кругов В.Н Оптимизация процессов технологии металлов методами планирования экспериментов. , М.: Машиностроение, 1980,304с.
- Красовский Г. И., Филатов Г. Ф. Планирование эксперимента . Мн.: Изд-воБГУ, 1982,302 с.
- Королев В.М., Степанов В. М. Фасонное литье по выплавляемым моделям. М.: Оборонгиз, 196,159с.
- Стрюченко А.А., Захарченко Э. В. Керамические формы в точном литье по выплавляемым моделям. М. Машиностроение, 1988. 128с.
- Косяну К., Видя М., Литье в керамические формы, М.: Машиностроение, 1980,200с.
- Богданов М.Г. Влияние технологических факторов на прочность оболочки при литье по выплавляемым моделям. / Литейное производство, № 9,1958.
- Шкленник Я.И. Получение прочных оболочковых форм при литье по выплавляемым моделям :сб. Точное литье транспортном и тяжелом машиностроении., М.:Машгиз, 1954
- Шкленник Я.И., Самсонова И. Н., Гелеван М. Н. и др. Подготовка формовочных материалов и прочность оболочек литейных форм при литье по выплавляемым моделям., МДНТП, 1960
- Лукьянов А.Б. Физическая и коллоидная химия.: Учебн. для техникумов. -М.: Химия, 1980,224с.
- Евстратова К.И., Кунина H.A., Малахова Е. Е. Физическая и коллоидная химия: Учебн. для фармацевтических вузов и факультетов / под ред. Евстратовой. -М.: Химия., 1974., 224с.
- Практикум по коллоидной химии и электронной микроскопии. / Под ред. проф. Воюцкого С. С. М.:Химия, 1974,224с.
- Чулкова А.Д., Иванов В. Н., Матвеев H.A. и др. Эмульсионное этилсиликатное связующее / Литейное производство, 1972, № 10,18−10
- Специальные способы литья: Справочник / Ефимов В. А., Анисович Г. А., Бабич В. Н. и др % под общ. ред. Ефимова В. А. М.: Машиностроение., 1991,436с.
- A.c. 123 880 (СССР) Суспензия для изготовления оболочковых литейных форм по выплавляемым моделям./ Александров В. М., Кулаков Б. А., Солодянкин A.A., опубл. в Б.И., 1986, № 23
- Ас 1 011 326 (СССР) Способ прокаливания оболочковых форм по выплавляемым моделям / Ферштатер И. Б., Тимков В. Н., Патракеев Н. И., опубл. в Б.И., 1983, № 14
- А.с 787 137 (СССР) Способ изготовления оболочковых литейных форм по выплавляемым моделям /Бушуев А.Н., Гарбер Н. М., Бушуева Л. Н., опубл. в Б.И., 1980, № 46
- А.с 616 039 (СССР) Способ получения композиции для изготовления керамических литейных форм по выплавляемым моделям / Иванов В. Н., Чулкова А. Д, Шабанова Н. А. и др., опубл. в Б.И., 1978, № 27
- А.с 342 727 (СССР) Суспензия для изготовления огнеупорных форм в производстве литья по выплавляемым моделям / Гольдин Г. С., Авербах К. О., Кондратенко О. Н., опубл. в Б.И., 1972, № 20
- А.с 521 060 (СССР) Способ приготовления суспензии для получения форм по выплавляемым моделям / Семененко А. А., Парыгин В. Г., Пепенко В. Д., опубл. в Б.И., 1976, № 26
- Патент № 475 363 (Австралия) Способ выплавления модельного состава. / Vaughn Charles Draper, Jackson James Dwight Microwave dewaxing TRW Inc., опубл. 2.06.76
- Патент № 995 855 (Канада) Способ изготовления керамических оболочковых форм. / Valenta Joseph Shell formulations Vestshell Inc., опубл. 31.08.76