Вращающаяся печь для обжига портландцемента по мокрому способу
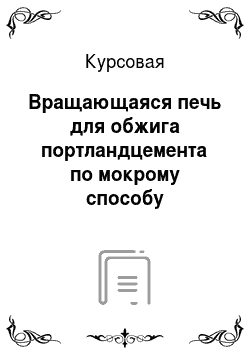
Вспомогательный привод включается в работу при ремонтах печи, в период розжига и остановки, когда печь должна вращаться медленно. Сырьевая мука подается в питательную трубу 7 при помощи ковшовых или объемных дозаторов, находящихся у холодного конца печи. Со стороны головки 8 в печь подается топливо и воздух; в результате сгорания топлива получаются горячие газы, поток которых направлен… Читать ещё >
Вращающаяся печь для обжига портландцемента по мокрому способу (реферат, курсовая, диплом, контрольная)
Пояснительная записка к курсовому проекту
Вращающаяся печь для обжига портландцемента по мокрому способу.
В силикатной промышленности, охватывающей цементное, керамическое, стекольное и другие виды производств, основными технологическими процессами являются обжиг, сушка или плавление шихтовых материалов. Промышленные печи относятся к очень важному производственному оборудованию, отличающемуся сложностью тепловых, аэродинамических и химических процессов, происходящих в них.
В современных условиях значительно возросла мощность заводов силикатной промышленности, а вместе с этим мощность, размеры и производительность печей, оснащенных средствами автоматизации. Значительно усовершенствовались конструкции печей и сушил за счет применения новых теплообменных, топливосжигающих и других устройств и печных элементов. Более сложной стала и эксплуатация таких печей, требующих точного регулирования тепловых процессов, высококвалифицированного обслуживания.
В печах и сушилах силикатной промышленности осуществляются весьма сложные технологические процессы, связанные с сушкой и обжигом материалов и изделий, а также с расплавлением шихтовых материалов, например для получения цементного клинкера.
Промышленная печь как тепловой аппарат отличается тем, что в ней получают тепловую энергию за счет сжигания топлива (или за счет электрической энергии электропечей) и передают ее материалам или изделиям, подвергаемым тепловой обработке. Основными теплотехническими процессами являются процессы сжигания топлива и теплопередачи, происходящие часто одновременно в рабочем пространстве печи. При этом большую роль играет создание необходимых условий для движения газов (аэродинамика).
Основным принципом проектирования современных печей служит непрерывность производственных процессов тепловой обработки материалов или изделий и высокая производительность.
При проектировании печей необходимо учитывать, что к ним предъявляются определенные теплотехнические и технологические требования:
— достаточно высокая тепловая мощность, обеспечивающая данную производительность;
— в рабочем пространстве печи должны быть достигнуты необходимые температуры, соответствующие технологическому режиму производства;
— наиболее эффективное сжигание подаваемого в печь топлива, высокий коэффициент использования топлива, минимальный удельный расход тепла на обжиг или другой тепловой процесс;
— высокая удельная производительность, высокое качество выпускаемой продукции при заданной производительности;
— наибольшая экономичность в эксплуатации, легкость и простота в обслуживании;
— наибольшая продолжительность работы без ремонтов, т. е. высокая стойкость огнеупорной кладки при воздействии высоких температур;
— печь должна быть автоматизированным тепловым агрегатом.
При проектировании всегда стремятся к тому, чтобы печь наиболее полно удовлетворяла этим требованиям. Однако существующие типы печей почти всегда имеют какие-либо конструктивные и эксплуатационные недостатки. Поэтому непрерывно происходит совершенствование существующих типов печей и разработка принципиально новых конструкций на базе научных исследований и практики работы действующих печных установок.
В производствах спекаемых материалов — цементного клинкера, шамота, металлургических магнезита и доломита — ведущую роль играют вращающиеся печи. В цементной промышленности наиболее распространены вращающиеся печи с внутренними теплообменными устройствами для мокрого способа производства. Современные вращающиеся печи имеют колосниковые холодильники для охлаждения обожженного продукта.
1. Вращающаяся печь: особенности строения, принцип работы
вращающийся печь топливо тепловой Вращающиеся печи, используемые для получения цементного клинкера, работают по принципу противотока. При мокром способе производства шлам подаётся в печь со стороны её верхнего (холодного) конца, а топливно-воздушная смесь, сгорающая на протяжении 20 — 30 м длины печи, вдувается со стороны нижнего (горячего) конца. Горячие газы движутся навстречу материалу, нагревая его до требуемой температуры.
Вращающаяся печь (трубчатая печь, барабанная печь), промышленная печь цилиндрической формы с вращательным движением вокруг продольной оси, предназначенная для нагрева сыпучих материалов с целью их физико-химической обработки. Вращающиеся печи различают: по принципу теплообмена — с противотоком и с параллельным током газов и материала; по способу передачи энергии — с прямым, косвенным (через стенку муфеля) и комбинированным нагревом обрабатываемого материала. По назначению различают вращающиеся печи для спекания шихт в производстве глинозёма, получения цементного клинкера, окислительного, восстановительного, хлорирующего обжига, прокалки гидроокиси алюминия, кокса, карбонатов, сульфатов и др., обезвоживания материалов, извлечения цинка и свинца (вельц-печи), получения железа или сплавов цветных металлов их прямым восстановлением из руд в твёрдой фазе (кричные печи), обжига огнеупорного сырья и др.
Основными являются вращающиеся печи, в которых сжигается пылевидное, твёрдое, жидкое или газообразное топливо непосредственно в рабочем пространстве печи и греющие газы движутся навстречу обрабатываемому материалу. Металлический барабан, футерованный огнеупорным кирпичом, устанавливают под небольшим углом к горизонту на опорные ролики. В ряде случаев диаметр барабана делают переменным по длине. Барабан приводят во вращение (1−2 об/мин) электродвигателем через редуктор и открытую зубчатую передачу. Шихту загружают со стороны головки. Сухую шихту подают механическими питателями, а шихту в виде пульпы — наливом или через форсунки. Топливо (10−30% от массы шихты) вводят через горелки (форсунки), помещённые в горячей головке. Здесь же выгружают готовый продукт, направляемый в холодильник. Газы из вращающиеся печи очищают от пыли (возгонов) в системе. Для улучшения условий теплопередачи во вращающиеся печи встраивают различные теплообменные устройства — перегребающие лопасти, полки, цепные завесы, насадки и т. д. С этой же целью в ряде случаев футеровку печей выполняют сложной формы, например ячейковой. Основные размеры вращающиеся печи варьируются в значительных пределах: длина от 50 до 230 м, а диаметр от 3 до 7,5 м. Производительность вращающейся печи достигает 150 т/ч (готового продукта). Наблюдается тенденция к соединению вращающиеся печи с различными теплообменными аппаратами, что позволяет при повышении технико-экономических показателей работы печей уменьшать их размеры.
Рисунок 1 — Схема вращающейся печи Вращающаяся печь (рис. 1), состоит из цилиндрического корпуса 1, опирающегося через бандажи 2 на опорные ролики 3. Корпус имеет уклон 3,5−4% и вращается со скоростью 0,5−1,2 об/мин. Привод печи двойной и состоит из двух электродвигателей 4, двух редукторов 5, двух подвенцовых шестерен и одного венцового колеса 6.
В середине печи, на одной из ее опор, устанавливается пара роликов (горизонтально) для контроля за смещением печи вдоль оси (вниз или вверх).
Вспомогательный привод включается в работу при ремонтах печи, в период розжига и остановки, когда печь должна вращаться медленно. Сырьевая мука подается в питательную трубу 7 при помощи ковшовых или объемных дозаторов, находящихся у холодного конца печи. Со стороны головки 8 в печь подается топливо и воздух; в результате сгорания топлива получаются горячие газы, поток которых направлен от горячего конца печи к холодному — навстречу движущемуся материалу. Для улучшения теплопередачи и обеспыливания газов внутри печи в холодном ее конце размещается цепной фильтр-подогреватель 9. Пыль, уловленная за печью в результате газоочистки, возвращается обратно в печь. Она транспортируется пневмонасосом в бункер, а из него при помощи периферийного загружателя 10 направляется в полую часть печи, со стороны горячего конца. Клинкер охлаждается в колосниково-переталкивающем холодильнике 11. На печах корпус оборудован центральной системой смазки 12.
Таблица 1 — Техническая характеристика вращающейся печи
Наименование | Показатели | |
Длина печи, м | ||
Диаметр печи, м | 3,6 | |
Скорость вращения печи, об/мин | 1,2 | |
Производительность, т/ч | 9,5−11 | |
Предлагаемая вращающаяся печь с рекуператорным холодильником предназначена для получения цементного клинкера по «мокрому» способу производства.
В печи применены опоры на подшипниках качения, что снижает расход электроэнергии, предусмотрены эффективные цепная завеса и ячейковый теплообменник, позволяющие снизить расход тепла на обжиг материала.
Плавное регулирование частоты вращения печи обеспечивает оптимальный для технологического процесса режим обжига, в результате увеличивается срок службы футеровок и снижается расход топлива.
1.1 Технология мокрого способа производства
На цементных заводах, работающих по мокрому способу, в качестве сырьевых материалов для производства портландцементного клинкера обычно используют мягкий глинистый и твердый известняковый компоненты. В этом случае технологическая схема производства цемента выглядит следующим образом:
Рисунок 2 — Технологическая схема мокрого способа производства Начальной технологической операцией получения клинкера является измельчение сырьевых материалов. Необходимость тонкого измельчения сырьевых материалов определяется тем, что однородный по составу клинкер можно получить лишь из хорошо перемешанной сырьевой смеси, состоящей из мельчайших частичек ее компонентов.
Куски исходных сырьевых материалов нередко имеют размеры до 1200 мм. Получить из таких кусков материал в виде мельчайших зерен можно только за несколько приемов. Вначале куски подвергаются грубому измельчению, дроблению, а затем тонкому помолу. Для грубого измельчения материалов применяют различные дробилки, а тонкое измельчение в зависимости от свойств исходных материалов производят в мельницах или в болтушках в присутствии большого количества воды.
При использовании в качестве известкового компонента мела, его измельчают в болтушках. Если применяют твердый глинистый компонент, то после дробления его направляют в мельницу.
Из болтушки глиняный шлам перекачивают в мельницу, где измельчается известняк. Совместное измельчение двух компонентов позволяет получать более однородный по составу сырьевой шлам.
В сырьевую мельницу известняк и глиняный шлам подают в определенном соотношении, соответствующем требуемому химическому составу клинкера. Однако даже при самой тщательной дозировке исходных материалов не удается получить из мельницы шлам необходимого химического состава из-за колебаний химического состава сырья одного и того же месторождения. Чтобы получить шлам заданного химического состава, его корректируют в бассейнах.
Для этого в одной или нескольких мельницах приготовляют шлам с заведомо низким или высоким содержанием CаCO3 (называемым титром) и этот шлам в определенной пропорции добавляют в корректирующий шламовый бассейн.
Приготовленный таким образом шлам, представляющий собой сметанообразную массу с содержанием воды до 35−45%, насосами подают в расходный бачок, откуда равномерно сливают в печь.
Для обжига клинкера при мокром способе производства используют вращающиеся печи. Они представляют собой стальной барабан длиной до 150−230 м и диаметром до 7 м, футерованный внутри огнеупорным кирпичом; производительность таких печей достигает 1000−3000 т клинкера в сутки.
Барабан печи устанавливают с уклоном 3−40 гр. шлам подают с поднятой стороны печи холодного конца, а топливо в виде газа, угольный пыли или мазута вдувают в печь с противоположной стороны (горячего конца). В результате вращения наклонного барабана находящиеся в нем материалы продвигаются по печи в сторону ее горячего конца. В области горения топлива развивается наиболее высокая температура: материала — до 15 000 С, газов — до 17 000 С, и завершаются химические реакции, приводящие к образованию клинкера.
Дымовые газы движутся вдоль барабана печи навстречу обжигаемому материалу. Встречая на пути холодные материалы, дымовые газы подогревают их, асами охлаждаются. В результате, начиная от зоны обжига, температура газа вдоль печи снижается с 1700 до 150−2000 С. Из печи клинкер поступает в холодильник, где охлаждается движущимся навстречу ему холодным воздухом. Охлажденный клинкер отправляют на склад. В ряде случаев клинкер из холодильника направляют непосредственно на помол в цементные мельницы.
Перед помолом клинкер дробят до зерен размером 8−10 мм, чтобы облегчить работу мельниц. Измельчение клинкера производится совместно с гипсом, гидравлическими и другими добавками. Совместный помол обеспечивает тщательное перемешивание всех материалов, а высокая однородность цемента является одной из важных гарантий его качества.
Гидравлические добавки, будучи материалами сильно пористыми, имеют, как правило, высокую влажность (до 20−30% и более). Поэтому перед помолом их высушивают до влажности примерно 1%, предварительно раздробив до зерен крупностью 8−10 мм. Гипс только дробят, так как его вводят в незначительном количестве и содержащаяся в нем влага легко испаряется за счет тепла, выделяющегося в мельнице в результате соударений и истирания мелющих тел друг с другом и с размалываемым материалом.
Из мельницы цемент транспортируют на склад силосного типа, оборудованный механическим (элеваторы, винтовые конвейеры), пневматическим (пневматические насосы, аэрожелоба) или пневмомеханическим транспортом.
Отгружают цемент потребителю либо в таре — в многослойных бумажных мешках по 50 кг, либо навалом в контейнерах, автомобильных или железнодорожных цементовозах, в специально оборудованных судах. Каждая партия цемента снабжается паспортом.
1.2 Физико-химические процессы, протекающие при тепловой обработке портландцемента
Образованию портландцементного клинкера предшествует ряд физико-химических процессов, протекающих в определенных температурных границах — технологических зонах печного агрегата — вращающейся печи. При мокром способе производства цемента по ходу движения обжигаемого материала условно выделяют следующие зоны: I — испарения, II — подогрева и дегидратации, III — декарбонизации, IV — экзотермических реакций, V — спекания, VI — охлаждения. Рассмотрим эти процессы начиная с поступления сырьевой смеси в печь, т. е. по направлению с верхнего ее конца (холодного) к нижнему (горячему).
В зоне испарения при постепенном повышении температуры с 70 до 200 °C испаряется влага; сырьевая смесь подсушивается., Подсушенный материал комкуется. Перемещаясь, комья распадаются на более мелкие гранулы. В печах сухого способа зона испарения отсутствует.
В зоне подогрева при постепенном нагревании сырья с 200 до 700 °C выгорают органические примеси, из глиняных минералов удаляется кристаллохимическая вода (при 450…500°С) и образуется безводный каолинит Al203-2Si02. Зоны испарения и подогрева при мокром способе занимают 50…60% длины печи. В зоне декарбонизации температура обжигаемого материала повышается с 700 до 1100 °C; происходит диссоциация карбонатов кальция и магния с образованием свободных СаО и MgO. Одновременно продолжается распад глинистых минералов на оксиды SiO2, Аl2O3, Fe2O3, которые вступают в химическое взаимодействие с СаО. В результате этих реакций, происходящих в твердом состоянии, образуются минералы ЗСаО-Fe2О3, СаО-А12O3 и частично 2CaO-SiO2.
В зоне экзотермических реакций при температуре 1200… 1300 °C завершается процесс твердофазового спекания материала, образуются ЗСаО-Fe2О3, 4СаО-А12O3-Fе2O3 и белит, резко уменьшается количество свободной извести, но достаточное для насыщения двухкальциевого силиката до трехкальциевого.
В зоне спекания при температурах 1300…1450…1300°С происходит частичное плавление материала (20…30% обжигаемой смеси). В расплав переходят все клинкерные минералы, кроме 2CaO-SiO2, все легкоплавкие примеси сырьевой смеси. Алит кристаллизуется из расплава в результате растворения в нем оксида кальция и двухкальциевого силиката. Это соединение плохо растворимо в расплаве, вследствие чего выделяется в виде мелких кристаллов, которые в дальнейшем растут. Понижение температуры с 1450 до 1300 °C вызывает кристаллизацию из расплава ЗСаО-А1203, 4СаО — Аl2О3-Fе2О3 и MgO (в виде периклаза), которая заканчивается в зоне охлаждения.
В зоне охлаждения температура клинкера понижается с 1300 до 1000 °C, здесь полностью формируются его структура и состав, включающий алит C3S, белит C2S, C3A, C4AF, MgO (периклаз), стекловидную фазу и второстепенные составляющие. Границы зон во вращающейся печи достаточно условны и не являются стабильными. Меняя режим работы печи, можно смещать зоны и регулировать тем самым процесс обжига.
Образовавшийся таким образом раскаленный клинкер поступает в холодильник, где резко охлаждается движущимся навстречу ему холодным воздухом. Клинкер, выходящий из холодильника вращающихся печей с температурой около 100 °C и более, поступает на склад для окончательного охлаждения и вылеживания (магазинирования), где он находится до 15 дней. Если известь содержится в клинкере в свободном виде, то в течение вылеживания она гасится влагой воздуха. На высокомеханизированных заводах с четко организованным технологическим процессом качество клинкера оказывается настолько высоким, что отпадает необходимость его вылеживания.
Помол клинкера совместно с добавками производят в трубных многокамерных мельницах.
Тонкое измельчение клинкера с гипсом и активными минеральными добавками в тонкий порошок производится преимущественно в сепараторных установках, работающих по открытому или замкнутому циклу.
Эффективная работа трубной мельницы обеспечивается охлаждением мельничного пространства путем его аспирации (вентилирования). Благодаря аспирации производительность мельниц растет на 20…25%, уменьшается пылевыделение, улучшаются условия труда. Для интенсификации помола вводят добавку — сульфитно-дрожжевую бражку (СДБ), при этом производительность мельниц увеличивается на 20…30%.
На современных цементных заводах помол портландцемента в открытом цикле проходит по следующей технологической схеме. Клинкер, гипс и активные минеральные добавки со склада подаются в бункера и дозируются тарельчатыми питателями. После измельчения цемент поступает через цапфу мельницы в аспирационную шахту, а из нее в бункер цемента и далее на склад. Мельничное пространство аспирируется, запыленный воздух частично очищается в аспирационной шахте, а затем в циклонах и электрофильтре, далее собирается шнеком и направляется в расходный бункер цемента. Недостатком помола в открытом цикле является трудность получения цемента с высокой удельной поверхностью (до 400…500 м2/кг).
Мельницы, работающие в замкнутом цикле, дают более однородный по размеру зерен продукт большей удельной поверхности (4000…5000 см2/г); замкнутый цикл помола включает помольный агрегат и центробежный сепаратор, определяющий крупные зерна, возвращаемые на домол в первую камеру, а тонкая фракция домалывается в третьей камере, из которой выгружается готовый цемент. В полностью замкнутом цикле материал проходит через сепаратор дважды.
В последнее время получает распространение короткая трубная мельница, обычно двухкамерная, работающая в замкнутом цикле с сепаратором.
Готовый портландцемент (с температурой 100 °C и более) пневматическим транспортом направляется в силосы для охлаждения. После этого его расфасовывают по 50 кг в многослойные бумажные мешки или загружают в специально оборудованный автомобильный, железнодорожный или водный транспорт.
2. Теплотехнические расчеты вращающейся печи
2.1 Расчет горения топлива
Основным топливом служит природный газ из групп северных месторождений Западной Сибири. Транспортируется он по газопроводу. Резервным топливо служит мазут. Для его использования имеется циркуляционный магистральный мазутопровод от мазутного хозяйства комбината до цеха, а также разводка его до каждой печи. В таблице 9 показан состав сухого газа.
Таблица 2 — Состав сухого газа
СН4, % | С2Н6, % | С3Н8, % | С4Н8, % | N2, % | СО2, % | Сумма, % | |
98,16 | 0,7 | 0,22 | 0,05 | 0,82 | 0,05 | ||
Топливо считается с коэффициентом расхода воздуха б = 1,14. Воздух, идущий на горение, нагревается до температуры 700 °C.
Принимаем содержание влаги в воздухе 1,0%. Пересчитаем состав сухого газа на влажный рабочий газ:
= СН4•(100-Н2О/100) = 98,16•(100−1/100) = 97,18
Составляющие сводим в таблицу 3.
Таблица 3 — Состав влажного газа
СН4, % | С2Н6, % | С3Н8, % | С4Н10, % | N2, % | CO2, % | H2O, % | Сумма, % | |
97,18 | 0,69 | 0,22 | 0,05 | 0,81 | 1,0 | 0,05 | ||
Определим теплоту сгорания газа по следующей формуле:
(1)
Находим теоретически необходимое количество сухого воздуха:
Lтеор=0,264/100• +?L. (2)
Находим теоретически необходимое количество воздуха с учетом его влажности по формуле:
Lґтеор=1,016•Lтеор. (3)
Lґтеор=1,016•9,4 = 9,55 мі/мі
Действительное количество воздуха при коэффициенте расхода б = 1,14:
сухого: Lб= 1,14•9,4 = 10,716 мі/мі;
атмосферного: Lґб = 1,14•9,55 = 10,887 мі/мі
Определим количество и состав продуктов горения при б = 1,14 по формулам:
VС02 = 0,01 •(СО2+СН4+2С2Н6+3С3Н8+4С4Н10). (4)
VС02=0,01•(0,05+97,18+2•0,69+3+0,22+4•0,05) = 0,995 мі/мі
VН2О=0,01•(Н20+2•СН4+3•С2Н6+4•С3Н8+5•С4Н10+0,16•d•Lб), (5)
где d — влагосодержание атмосферного воздуха, d=10г/кгс. в.
VН2О=0,01•(1+2•97,18+3•0,69+4•0,22+5•0,05+0,16•10•10,72)=2,166 мі/мі
VN2=0,79•Lб+0,01•N2. (6)
VN2 = 0,79 • 10,72 + 0,01 • 0,81 =8,48 мі/мі
VO2 = 0,21 • (б — 1) • Lтеор. (7)
VO2 = 0,21 • (1,14 — 1) • 9,4 = 0,276 мі/мі
Общее количество продуктов горения составляет:
Vб = 0,995 + 2,166 + 8,48 +0,276 = 11,917 мі/мі
Находим процентный состав продуктов горения по формулам:
СО2 = (100 • VСO2)/ Vб. (8)
СО2 = (100 • 0,955)/ 11,917 = 8,3%;
Н2О = (100 • VН2О)/ Vб. (9)
Н2О = (100 • 2,166)/11,917 = 18,2%;
N2 = (100 • VN2)/ Vб. (10)
N2 = (100 • 8,48)/ 11,917 = 71,2%
О2 = 100•VО2)/ Vб• L. (11)
О2 = (100 • 0,276)/ 11,917 = 2,3%
Всего: 100%
Составляем материальный баланс процесса горения (таблица 4). Он необходим для определения количества воздуха, пошедшего на горение, и продуктов сгорания в результате горения.
Таблица 4 — Материальный баланс процесса горения
Приход | кг | Расход | кг | |
природный газ: СН4 = 97,18 • 0,717 С2Н6 = 0,69 •1,356 С3Н8 = 0,22 • 2,020 С4Н10 = 0,05 • 2,840 СО2 = 0,05 • 1,977 Н2О = 1,0 • 0,804 Воздух: О2 =9,43 • 21 •1,14 •1,429 | 69,678 0,936 0,444 0,142 0,099 0,804 322,603 | продукт горения: СО2 = 0,995 • 100• •1,977 Н2О = 2,166 • 100• •0,804 N2 = 8,48 •100 •1.251 O2 = 0,276 •100 •1,429 Невязка: | 196,711 174,146 1060,848 39,440 — 0,191 | |
N2 = 198.03 • 1,14 •3,762• •1,251 Н2О = 0,16 • 10•10,72 •0,804 | 1062,458 13,790 | |||
Итого: | 1470,954 | Итого: | 1470,954 | |
Невязка баланса составляет: (100•0,191):1470,954 = 0,013%
Определим теоретическую температуру горения. Для этого находим теплосодержание продуктов горения с учетом подогрева воздуха до температуры 700 °C при б = 1,14.
По i-t-диаграмме находим теплоту нагрева атмосферного воздуха, iвозд = 960 кДж/мі.
Тогда iобщ = Qн/ Vб+Lб•iвозд/Vб = 35 509,84/11,917 + 10,887*960/11,917 = 3856,79 кДж/мі
По i-t-диаграмме при, а = 1,14 теоретическая температура горения 1 теор = 2120 °C, а калориметрическая температура горения tк = 2308 °C.
Определим калометрическую температуру горения с помощью таблиц энтальпий, для этого задаемся температурами t1 = 2200 °C и t2 = 2300 °C. Теплота продуктов горения для температур t1 и t2 определяется с помощью приложения.
При T1 = 2200°С: При T2 = 2300°С:
СО2 = 0,080•5387,0 = 430,96; СО2 = 0,080•5658,7 = 452,70;
Н2О = 0,172•4402,2 = 757,18; Н2О = 0,172•4643,8 — 798,73;
N2 = 0,716•3289,3 = 2355,14; N2 = 0,716•3452,6 = 2472,06;
О2 = 0,032•3482,7 = 111,45; О2 = 0,032•3656,5 = 117,01;
il = 3654,73 кДж/м3. i2 = 3840,5 кДж/м3.
Следовательно, 3840,5> iобщ <3654,73
3856,79−3654,73 = 200,54
?t = 200,54•100/186 = 108, следовательно, tК = 2200+108 = 2308 °C Определим действительную температуру горения при коэффициенте з=0,8:
iдейст = iобщ•з = 3856,79•0,8 = 3084,2 кДж/мі
Действительная температура горения по i-t-диаграмме при б = 1,14 с учетом диссоциации равна 1810 °C.
2.2 Материальный баланс по сырью
1. Выход продукции из вращающейся печи с учетом безвозвратных потерь при транспортировке:
Q1 = Qгод ·, (12)
где q1 — процент безвозвратных потерь при транспортировке;
Qгод — годовой объем выпуска продукции, т/год.
Q1 = 50 000· = 50 100 т/год Масса безвозвратных потерь при транспортировке:
q'1 = Q1 — Qгод. (13)
q'1 = 50 000 — 50 100 = 100 т/год
Q2 =, (14)
где Дmпрк — потери при прокаливании, %.
2. Подача сырья в печь с учетом потерь при прокаливании:
Q2 = = 51 649 т/год Масса потерь при прокаливании:
q'2 = Q2 — Q1. (15)
q'2 = 51 649 — 50 100 = 1549 т/год
3. Подача сырья в печь с учетом пылеуноса:
Q3 = Q2 ·, (16)
где q3 — процент всей уносимой пыли.
Q3 = 51 649 · = 68 865 т/год Масса уносимой пыли:
q'3 = Q3 — Q2. (17)
q'3 = 68 865 — 51 649= 17 216 т/год Масса уловленной пыли:
q''3 = q'3 ·, (18)
где k — коэффициент полезного действия пылеулавливающего устройства.
q''3 = 17 216 · = 16 872 т/год Масса безвозвратно уносимой пыли:
q'''3 = q'3 — q" 3. (19)
q" '3 = 17 216 — 16 872= 344 т/год
4. Подача сырья в печь с учетом возврата пыли:
Q4 = Q3 — q''3. (20)
Q4 = 68 865 — 16 872 = 51 993 т/год
5. Подача сырья в печь с учетом влажности:
Q5 = Q4 ·, где (21)
где q5 — влажность сырья, %.
Q5 = 51 993 · = 86 655 т/год Масса воды, испаряемой в печах:
q'5 = Q5 — Q4. (22)
q'5 = 86 655 — 51 993 = 34 662 т/год Обобщенные данные сведем в таблицу 5.
Таблица 5 — Материальный баланс сырья
Приход | т/год | Расход | т/год | |
Q5 | Qгод | |||
q'1 | ||||
q'2 | ||||
q'''3 | ||||
q'5 | ||||
Итого: | Итого: | |||
Невязка баланса составляет: (100•0):86 665 = 0%
2.3 Расчет теплового баланса вращающейся печи
ПРИХОД ТЕПЛА:
1. Тепло от горения топлива:
Qг = · B, (23)
где — тепло сгорания топлива, кДж/мі;
В-расход топлива, мі/с.
Qг = 35 509,84· B кВт
2. Тепло, вносимое подогретым воздухом:
Qвозд = Lб · iвозд · B, (24)
где Lб — действительное количество воздуха, подаваемое для горения топлива, мі /мі;
iвозд — теплосодержание воздуха, кДж/мі.
Считаем, что весь воздух, необходимый для горения поступает в печь из холодильника с температурой 700 °C.
По расчету горения топлива Lб = 10,887 мі/мі, iвозд = 960 кДж/м3, тогда
Qвозд = 10,887· 960·В = 10 451,52· В кВт Физическое тепло холодного природного газа не учитывается.
3. Приход тепла:
Qприх = Qг + Qвоз (25)
Qприх = 35 509,84· B + 10 451,52· В = 45 961,36 · В кВт РАСХОД ТЕПЛА:
1. Тепло, затраченное на нагрев обжигаемого материала:
Qм = P · Сk · tk — Pc· Сн · tн, (26)
где Р — производительность печи по сухому (обожженному) материалу, кг/с;
Рс — расход сухих шихтовых материалов, кг/с;
Ck, tk — энтальпия (теплосодержание) материала в конце нагрева до конечной температуры обжига, кДж/кг;
Cн, tн — теплосодержание материала в начале нагрева при начальной температуре tн кДж/кг.
Рс =· Р, (27)
где ?mпрк — потер массы при прокаливании.
Р == 2,6 кг/с Рс = · 2,6 = 2,7 кг/с
Qм = 2,6 · 1730 · 1,31 — 2,7· 10 · 0,912 = 5867,8 кВт
2. Расход тепла на испарение физической влаги, содержащейся в материале:
Qисп = (2500 — 4,2· tн +)· Wвл, (28)
где Wвл — количество влаги, испаряемой из материала, кг/с;
0,804 — удельная масса водных паров, кг/мі;
2500 — скрытая теплота парообразования, кДж/кг;
tн — температура влажных материалов, поступающих в печь,°С;
iуг — теплосодержание водяных паров при iуг = 600 °C, кДж/мі.
Wвл = Рс · (29)
Wвл = 2,7 · =1,8 кг/с
Qисп = (2500 — 4,2· 10 +)· 1,8 = 4627,2 кВт
3. Расход тепла на химические реакции:
Qхим= qхим · G, (30)
где qхим — теплота, расходуемая на физико-химические процессы 1 кг исходного химического вещества в необожженном продукте, кДж/кг;
G — количество исходного химического вещества в материале, загружаемом в печь.
G = 0,01 · n · Рс, (31)
где n — процентное содержание исходного химического вещества в сухой массе материала, %;
Рс — количество сухого материала, поступающего в печь, кг/с.
G = 0,01 · 2,7 = 0,027
Теплота диссоциации: МgСО3 — 1310 кДж/кг, СаСО3 — 1780 кДж/кг
Qхим = 1310· 50,64·0,027 + 1780· 15,17·0,027 = 2520 кВт
4. Потери с уходящими продуктами разложения:
Qдис = 0,01· Рс· (0,4 · СаО+0,553· МgО) · iСО2, (32)
где МgО и СаО — содержание оксидов в обожженном продукте, %
iСО2 — теплосодержание СO2 при tух = 600 °C, iСО2 = 814,4 кДж/м МgО = 75,0%, СаО = 14,7%.
Qдис = 0,01· 2,7·(0,4·14,7+0,553·75)·814,4= 1041,4 кВт
5. Потери тепла с уносом:
Принимаем общий унос сухого материала 25%, степень теплоты декарбонизации безвозвратного уноса в = 0,3…0,6; принимаем в=0,5.
Общий унос тепла определяется по формуле:
Gун = Рс · · (1 — · в), (33)
где G’ун — количество уносимой из печи сырьевой пыли, (процент от расхода сухого сырья);
в — степень полноты декарбонизации безвозвратного уноса для вращающихся печей.
Gун = 2,7· · (1 — · 0,5) = 0,66 кг/с Определим потери тепла с пылью, уносимой с продуктами горения в атмосферу:
Qун = Gун · Сун · tух, (34)
где Cун — теплоемкость уносимой пыли, Cун = 1,6 кДж/кг•град;
tух — температура уходящих газов,°С.
Qун = 0,66 · 1,6· 600 = 633,6 кВт Расход тепла на декарбонизацию и дегазацию уноса, выбрасываемого в атмосферу, определяется по формуле:
= · (29,64 · СаО + 17,0 · МgО), (35)
где СаО и МgО — содержание оксидов в составе шихты, %;
— количество сухих и сырьевых материалов в безвозвратном уносе, кг/с.
= 0,66· (29,64· 14,7+17,0· 75,0) = 1129,1 кВт Продукты дегазации уноса, уходящие с дымовыми газами определим по формуле:
Qух= 0,1 · 0,5 · Qдис. (36)
Qух = 0,1 · 0,5·1041,4 = 52,07 кВт Общие потери тепла с уносом составляют:
Qун= Qун + Qун + Qух. (37)
Qун= 633,6 + 1129,1 + 52,07 =1814,77 кВт
6. Потери тепла с уходящими продуктами горения:
Qдым = Vдым · iдым · В, (38)
где Vдым — объем продуктов горения, уходящих из рабочего пространства печи с учетом подсосов окружающего воздуха, мі/с.
где iдым — энтальпия продуктов горения при температуре уходящих газов, кДж/мі.
Qдым = 11,917 · В · 866,3 = 10 323,7· В кВт
7. Потери тепла корпусом печи в окружающую среду:
Qкор = 0,15 · · В (39)
Qкор = 0,15 · 35 509,84 · B = 5326,48· B кВт
8. Неучтенные потери тепла вследствие неполноты горения топлива, выбивания газов и излучения через отверстия в головке печи:
Qнеуч = 0,5 · · B (40)
Qнеуч = 0,5· 35 509,84·В = 17 754,92· В кВт Составим уравнение теплового баланса и определим расход топлива:
Qприх = Qг + Qвозд = 35 509,84· В + 10 451,52· B = 45 961,36 · B кВт
Qрасх = Qм + Qисп + Qхим +Qун+Qдис + Qдым + Qкор + Qнеучт (41)
Qрасх = 5867,8+4627,2+2520+1814,77+1041,4+10 323,7· B+5326,48·B +
+ 17 754,92•В = 15 871,17 + 33 405,1· В
Qрасх = Qприх
15 871,17 + 33 405,1· B = 45 961,36· B
Секундный расход топлива:
B = 1,26 мі/с Часовой расход топлива составляет:
В' = 1,26 · 3600 = 4536 мі/ч Удельный расход тепла, внесенное топливом:
q =. (42)
где 29 300 — теплота сгорания топлива, кДж/мі;
Р — секундная производительность печи, кг/с.
q = = 16 955 кДж/кг Таблица 6 — Тепловой баланс вращающейся печи
Наименование статьи | Количество тепла: | ||
кВт | % | ||
Приход тепла: | |||
1. Тепло горения топлива | 44 723,4 | 77,25 | |
2. Физическое тепло воздуха | 13 168,9 | 22,75 | |
Итого: | 57 892,3 | 100,0 | |
Расход тепла: | |||
1. Нагрев материала | 5867,8 | 10,1 | |
2. Испарение и перегрев влаги | 4627,2 | 8,0 | |
3. Теплота химических реакций | 4,3 | ||
4. Потери с уходящими продуктами разложения | 1041,4 | 1,8 | |
5. Потери тепла с уносом | 1814,77 13 007,86 6711,36 22 371,20 | 3,1 22,5 11,6 38,6 | |
6. Потери тепла с уходящими продуктами горения 7. Потери в окружающую среду 8. Неучтенные потери | |||
Невязка: | 69,29 | ||
Итого: | 57 892,3 | 100,0 | |
Невязка баланса составляет: (100•69,29):57 892,3 = 0,12%
3. Контроль соблюдения и регулирования режима работы вращающейся печи
Движение печи вниз осуществляется за счет небольшой смазки бандажей. Для контроля положения печи существуют контрольные ролики, для кратковременного удержания — кратковременные ролики. Для предотвращения падения печи или схода печи с опорных роликов конечные отсекатели, отключение электроэнергии. Кроме основного привода предусмотрен вспомогательный привод для кратковременного поворота печи во время ремонта и непрерывного вращения печи во время охлаждения и разогрева. Горячая печь должна обязательно вращаться, иначе возникает прогиб корпуса между опорами.
Загрузка в печи и горны выгрузка из них деталей должны быть максимально механизированы. Ручная загрузка ил выгрузка деталей должны производиться с помощью специальных клещей и захватов, размеры и форма которых соответствуют величине и форме деталей. Забрасывать детали в печь при загрузке запрещается. Продвижение деталей в печи и горны должно осуществляться при помощи специальных приспособлений и устройств.
Конструкция и содержание газопроводов должны удовлетворять «Правилам устройства эксплуатации газовых сетей городов и населенных пунктов». В цехе должны иметься схемы трубопроводов мазута, газа, пара, воздуха с указанием номеров вентилей задвижек и мест их расположения. Для удобства безопасности обслуживания трубопроводы следует окрашивать в соответствующие цвета.
Запорные устройства трубопроводов (мазута, газа, воздуха, пара) должны располагаться в местах, удобных безопасных для обслуживания. Вентили задвижки необходимо снабжать указателями (стрелками) с надписями: «Открыто» и «Закрыто».
4. Автоматизация вращающейся печи
Вращающаяся печь является сложным объектом автоматизации, но в то же время важным, поскольку правильный режим обеспечивает однородность и высокое качество обожженного магнезита, удлинение срока службы футеровки, увеличение коэффициента использования печи, а также снижение удельного расхода топлива. Назначение системы автоматического регулирования состоит в обеспечении стабилизации качества обжига, снижении расхода топлива и ручного труда.
На стабильность технологического процесса обжига оказывают влияние следующие факторы:
— колебания подачи сырья в печь;
— неравномерность скорости движения материала в печи из-за изменения
гранулометрического состава сырья;
— колебания температуры в зоне подогрева из-за изменения
физико-химических свойств сырья;
— колебания температуры в зоне обжига;
— колебания давления газа, поступающего на горение.
Процесс горения топлива зависит от количества подаваемого в печь воздуха. Обычно во вращающейся печи воздух подается от вентилятора высокого давления и через холодильник за счет разряжения в печи.
Поддержание определенного соотношения между количеством подаваемого воздуха и топлива, необходимого для горения, является непременным условием получения максимальной температуры факела, а следовательно, и повышается экономичность процесса горения. Если количество воздуха подается больше, чем необходимо для горения, то температура факела становится ниже и происходит пережог топлива. При подаче меньшего количества воздуха температура факела уменьшается и происходит неполное сгорание топлива. В обоих случаях из-за нарушения указанного соотношения, для получения оптимальной температуры горения необходимо осуществлять управление технологическим процессом. Необходимое соотношение воздуха и природного газа устанавливается с помощью датчика этих регуляторов расхода. Сигналы передаются на преобразующие измерительные приборы, на исполнительные механизмы, которые управляются регулирующими дросселями. Расход первичного воздуха и газа измеряется сужающимися устройствами и измеряются измерительными приборами.
Автоматическая система регулирования подачи воздуха полностью обеспечивает экономичное горение топлива.
При контроле теоретического коэффициента избытка необходим дополнительный контроль фактического коэффициента избытка воздуха по составу отходящих дымовых газов, по анализу на содержание кислорода.
Не менее важным параметром при обжиге магнезита является температура. Одно из основных условий нормального обжига материала — это поддержание установленных температур в зоне обжига.
Температура — это наиболее важный контролируемый параметр для печей. Если температура будет выше установленной, то магнезит будет пережженным. Если температура будет ниже установленной, то магнезит будет содержать недожог. Температура в печи изменяется по ряду причин, которые контролируются приборами. При управлении температурным режимом обжига, должно достигаться изменение температуры по ходу обжига.
Для обеспечения более полного контроля режима работы печи, а также для получения возможности исследования печи, как объекта автоматического регулирования, оказалось необходимым усовершенствовать существующую систему с помощью разработки и введения в эксплуатацию дополнительных узлов автоматического регулирования и контроля.
Измерение температуры во вращающихся печах связано с затруднениями как установки измерительных элементов (термопар), так как они должны вращаться вместе с барабаном печи и обжигаемый материал, продвигаясь по печи, соприкасается с измерительным элементом, так и передачи, показаний от термопары к вторичному прибору, расположенному на щите управления работой печи. Измерение температуры радиационными пирометрами, связано со значительными и непостоянными по величине погрешностями из-за большой запыленности воздуха и продуктов сгорания в печи, через слой которых происходит измерение температуры.
Измерение температуры порядка 500−600°С в зоне подогрева, осуществляется хромель-алюмелевыми термопарами, установленными в барабан вращающейся части печи. Рабочий конец термопары выступает в рабочее пространство печи, соприкасается с обжигаемым материалом, когда термопара внизу, и омываемая продуктами сгорания, когда термопара наверху. Поэтому показания этой термопары имеют среднее значение. Сравнительно низкие температуры и еще небольшая твердость обжигаемого материала в этой зоне создают условия, при которых термопара здесь служит практически неограниченно длительное время.
Для эффективного ведения технологического режима обжига необходимо измерить температуру в зоне обжига, которой в основном определяется качество сырья. Температура в зоне обжига достигает 1500 °C. Для защиты термопары, выходящей в пространство печи, от истирания в футеровке печи выполнены специальные «карманы». На конец термопары, находящейся в «кармане», перемещение материала вдоль печи, изнашивающее термопару, не оказывает воздействия. При вращении барабана печи в «карман» засыпается обжигаемый материал и термопара нагревается до температуры материала.
Подача показаний от термопары к вторичному прибору осуществляется при помощи специальных троллей и токосъемников. Измерение температуры в зоне обжига осуществляется платинородной и специальными термопарами, армированными в фарфоровые и алундовые защитные чехлы.
Главной задачей, которую должна решать комплексная система автоматического регулирования является автоматическое поддержание заданного качества продукции при максимальной производительности установки и при экономичном режиме производства. Для решения этой задачи необходим непрерывный автоматический контроль качества сырья и готовой продукции, температуры в зоне обжига и других. В схеме автоматизации предусмотрена звуковая сигнализация при нарушении давления воздуха в воздухопроводе перед горелками, остановке дымососа и отключении электроэнергии. Во всех случаях происходит отсечка газа предохранительными клапанами.
Показания вторичных приборов тепловых и технологических параметров работы печи объединены в три основные группы и вынесены на три специальных щита:
— щит управления обжигальщика;
— щит машиниста котла-утилизатора;
— щит оператора преобразовательной подстанции отделения «Газоочистка».
На щит обжигальщика вращающейся печи вынесены следующие приборы:
— автоматический самопишущий потенциометр ПСР-1−52 для контроля температуры в пылевой камере;
— автоматический самопишущий потенциометр ПСР-1−0,1 для контроля температуры отходящих газов в газоходе;
— автоматический самопишущий прибор с дифференциально-трансформаторной схемой ДСР-1−14 для контроля разряжения в газоходе;
— автоматический самопишущий прибор с дифференцально-трансформаторной схемой АСД-2564 для контроля расхода газа, подаваемого в печь:
— автоматический прибор с дифференциально-трансформаторной схемой ОБМ-160 для контроля давления газа, поступающего на горение;
— вторичный прибор ВФС-М2Г-РР для контроля за загрузкой материала во вращающуюся печь с помощью ДН-959−63;
— задатчик дистанционный пультовый сдвоенный 2ДЗН-24-У-4 для увеличения или снижения загрузки магнезита во вращающуюся печь;
— вторичный прибор ВФС-4 для контроля производительности вращающейся печи.
Кроме этого имеются следующие приборы для контроля печи:
— пружинный монометр ОБ 14−1 -100 для контроля за давлением газа, мазута в магистрали;
— сигнализатор падения давления газа, мазута СПДН-300.
Для повышения производительности и улучшения условий труда и качества продукции устанавливаю компьютерную систему, где все данные работы печи выводятся на экран. С помощью этого можно более точно регулировать режим работы печи.
Заключение
вращающийся печь топливо тепловой В данном курсовом проекте были выполнены теплотехнические расчеты вращающейся печи 3,6×90 м для обжига цементного клинкера по мокрому способу. В качестве топлива используется природный газ из групп северных месторождений Западной Сибири.
Библиографический список
1. Гинзбург, Д. Б. Печи и сушила силикатной промышленности / Д. Б. Гинзбург, С. Н. Деликишкин, Е. И. Ходоров. — М.: Промстройиздат, 1956. — 456 с.
2. Бутт, Ю. М. Химическая технология вяжущих материалов / Ю. М. Бутт, М. М. Сычев, В. В. Тимашев. — М.: Высшая школа, 1980. — 460 с.
3. Левченко, П. В. Расчеты печей и сушил силикатной промышленности / П. В. Левченко. — М.: Высшая школа, 1968. — 363 с.
4. Воробьёв, Х. С. Теплотехнические расчёты цементных печей и аппаратов / Х. С. Воробьёв, Д. Я. Мазурова. — М.: Высшая шкала, 1962. — 350 с.
5. Левченко, П. В. Расчет печей и сушил силикатной промышленности / П. В. Левченко. — М.: Высшая шкала 1968 г. — 363 с.