Другие работы
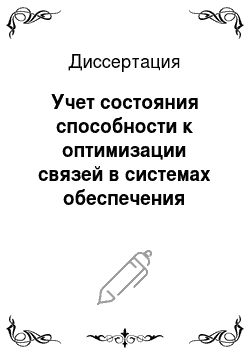
Прогресс в области разработки и эксплуатации сложных технических систем связан с заметными успехами в области их надежного функционирования. Этому способствует появление исследований, в которых оценивается влияние технических систем на органы человека, которые формируют целые направления как в области проектирования технических устройств под человека-оператора, так и в области разработки…
Диссертация 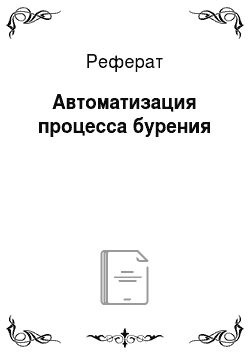
В системе присутствуют следующие датчики:. Датчик веса на крюке устанавливается на неподвижной ветви талевого каната. В качестве первичного преобразователя в датчике используется тензометрический силоизмерительный элемент. Датчик контроля момента на роторе (тензометрический) устанавливается на редукторе привода ротора вместо фиксирующей серьги-стяжки или фиксирующей опоры. Контролируется…
Реферат 
Черепетской и Приднепровской ГТЭС, хотя по установленной мощности блоки СКД определяют лицо ЕЭС, тем ни менее количество и станций с барабанными котлами, и таких котлов в общем парке — абсолютно превалирует. А в последнее время, в связи с появлением относительно новой для России парогазовой технологии доля барабанных котлов будет увеличиваться. Более того, можно предположить, что повышение…
Диссертация 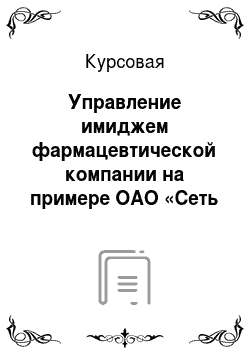
Имидж организации — целостное восприятие компании различными группами общественности, которое формируюется как результат хранения в их памяти информации о различных сторонах ее деятельности. Он формируется в процессе основной деятельности организации, а также как результат информационной работы, которая ориентируется на общественные целевые группы. Процесс создания имиджа происходит с учетом…
Курсовая 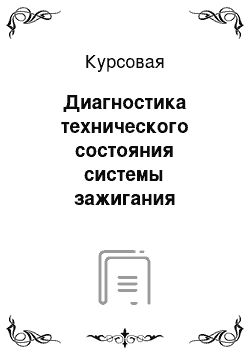
Сердечник катушки набран из листов электротехнической стали. Вторичная обмотка, намотанная на изоляционную втулку, располагается на сердечнике. Число витков этой обмотки лежит в пределах 16−40 тыс., диаметр провода 0,06−0,09 мм. Поверх вторичной обмотки через изоляционную прокладку располагается первичная обмотка. Такое расположение способствует лучшему ее охлаждению. Обмотка имеет 260 — 330…
Курсовая 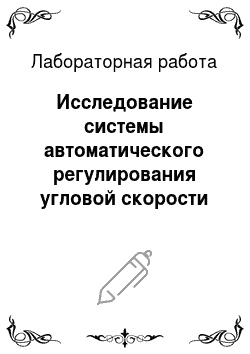
В установившемся режиме определенному моменту нагрузке МН на валу дизеля соответствует некоторая подача топлива, зависящая от положения рейки топливного насоса, которую перемещает сервомотор СМ. Если нагрузка по какой-либо причине уменьшится, тогда угловая скорость дизеля возрастет, грузы ЦБМ разойдутся и переместят муфту, а вместе с нею и золотник ГУ. Рабочая жидкость поступит в СМ и он начнет…
Лабораторная работа 
Изотропная электротехническая сталь является магнитомягким материалом, применяемым для изготовления магнитопроводов электрической аппаратуры, работающих во вращающемся переменном магнитном поле (статоры и роторы электродвигателей, электрогенераторов и др.). Основной характеристикой оценки качества этой стали являются магнитные свойства — потери энергии на процесс перемагничивания, магнитная…
Диссертация 
Одним из важных агротехнических требований, предъявляемых к зерносушильным агрегатам, является необходимость в доведении семенного материала до кондиционной влажности за короткий промежуток времени при минимальных удельных энергозатратах и исключения снижения урожайных качеств. Эта технологическая операция в настоящее время осуществляется на стационарных и передвижных агрегатах в основном…
Диссертация 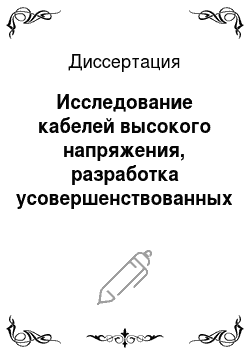
В целом состояние отечественного рынка кабелей высокого напряжения определяется, с одной стороны, затяжным экономическим кризисом, и, с другой, — признаками экономического роста и огромными ресурсами и потенциалом развития России в сфере энергетики и народного хозяйства в целом. Данные факторы в совокупности означают большой неудовлетворенный спрос на новые экономичные, но качественные и надежные…
Диссертация 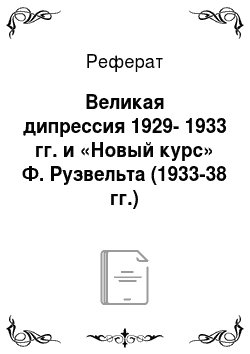
Концентрация производства и капитала в конце 30-х годов харак-теризовалась тем, что на крупных предприятиях (с производством продукции на миллион долларов и более), составлявших 5,2% общего количества американских предприятий, было сосредоточено 55% всех занятых рабочих и производилось 67,5% валовой продукции промышленности. Гигантские концерны, составлявшие не более одной тысячной от общего…
Реферат 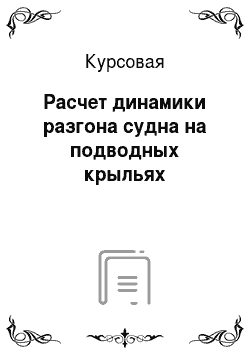
Из курса теоретической механики известно, что в соответствии принципам Даламбера неустановившееся движение тела описывается вторым законом Ньютона. Поскольку в данной задаче рассчитывается движение лишь в направлении одной из осей координат (в данном случае оси «X»), то достаточно записать уравнения движения в проекции на ось «X» и решать его относительно скорости «V» в направлении оси «X…
Курсовая 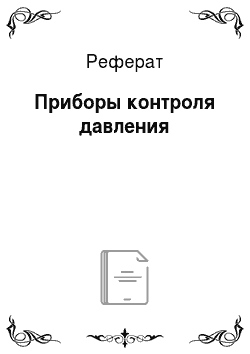
Пьезорезистивный эффект заключается в изменении проводимости при механическом напряжении в кристалле полупроводника, что связано с изменением подвижности носителей электричества в кристаллической решетке. Коэффициент тензочувствительности у кремния достигает значений от 1 до 150. Как правило, пьезорезисторы формируются в кремниевой диафрагме сразу в виде мостовой схемы, совмещенной с электронным…
Реферат 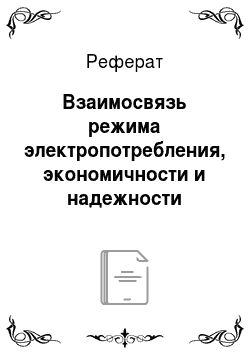
Рост выбросов CO2 на душу населения в секторе пассажирского транспорта оказался удивительно неравномерным в разных странах. В некоторых государствах уровень выбросов остался сравнительно стабильным. Уровень выбросов фактически упал в Финляндии, Германии и Великобритании из-за ограниченного роста уже достаточно большого количества владельцев транспортных средств, ограниченного увеличения…
Реферат 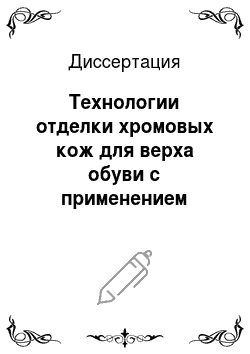
В последнее время все шире применяются электрофизические методы модификации материалов как наиболее эффективные и экономичные. Перспективным методом модификации натуральных высокомолекулярных материалов является такой электрофизический метод обработки, как воздействие потоком плазмы ВЧЕ-разряда пониженного давления на натуральные высокомолекулярные материалы. Преимущество такого метода…
Диссертация 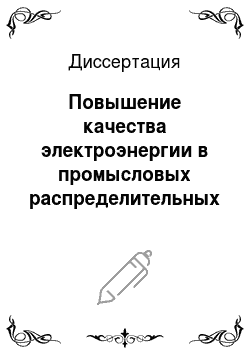
Вопросами компенсации провалов напряжения занимались такие известные ученые как Кучумов Л. А., Каялов Г. М., Абрамович Б. Н., Иванов О. В., Гамазин С. И., и другие. Однако для условий нефтедобывающего комплекса остается нерешенной задача обеспечения непрерывности работы чувствительных к провалам напряжения электроприемников, к которым относятся погружные электродвигатели, установки поддержания…
Диссертация