Другие работы
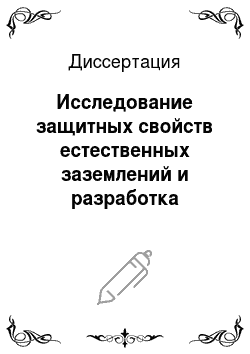
Из табл.1.2. следует, что основное количество нарушений изоляции кабеля (около 80%) связано с электрическим пробоем. До 20% нарушений изоляции происходит за счет механического повреждения и, следовательно, непосредственного соприкосновения механизма с токо-ведущими частями, что равносильно замыканию фазы на корпус. В последние годы наблюдается тенденция к увеличению количества механических…
Диссертация 
Первое — произведение максимального статического усилия в канате на коэффициент использования каната (коэффициент запаса прочности), не должно превышать разрывного усилия каната в целом, указанного в таблице ГОСТа, т. е. F0? Zp· Smax, где F0 — разрывное усилие каната в целом, Н, Zp — коэффициент использования канатов. Канат выбираем по маркировочной группе по временному сопротивлению разрыва 1764…
Курсовая 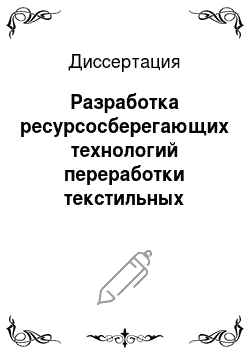
Основные методы исследования. В диссертационной работе использован комплекс теоретических и экспериментальных исследований. В теоретическом анализе применялись дифференциальное, интегральное и векторное исчисление, теория рядов, а также численные методы решения дифференциальных уравнений, компьютерное имитационное моделирование и анализ динамических моделей, средства инженерных и научных…
Диссертация 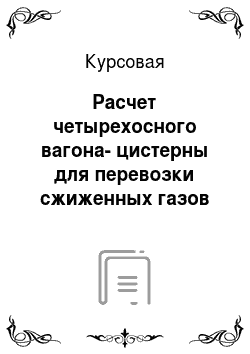
В ходовых частях четырехосных цистерн используются двухосные тележки типа ЦНИИ-ХЗ моделей 18−100 (на подшипниках качения) и 18−109 (на подшипниках скольжения). Все вагоны постройки после 1978 г. оборудованы тележками на подшипниках качения. Все серийные четырехосные цистерны имеют рамную конструкцию и типовую схему крепления котла к раме. На раме смонтировано автотормозное и автосцепное…
Курсовая 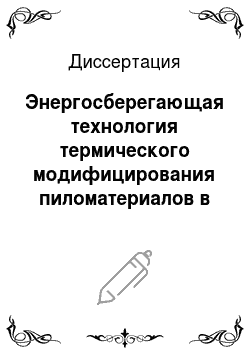
Апробация и реализация результатов диссертации. Основные положения диссертации докладывались на научных сессиях по технологическим процессам ФГБОУ ВПО «КНИТУ» (Казань, 2009;12 г), на Молодежной научной конференции по естественным и техническим дисциплинам «Научному прогрессу — творчество молодых» (Йошкар-Ола, 2010 г), на 1У-ой Международной научно-практической конференции «Современные…
Диссертация 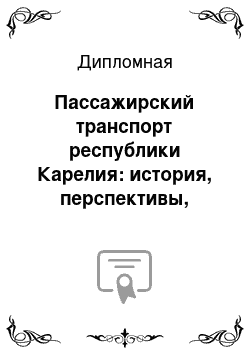
Железнодорожный транспорт Республики представлен участком Октябрьской железной дороги, состоящего из главного пролета (от станции Ревсельга на юге до южной оконечности станции Пояконда на севере), Западно-Карельского участка (ст. Суоярви — ст. Костомукша — ст. Кивиярви с ответвлениями на Лендеры и Юшкозеро), дороги Петрозаводск — Сортавала — Санкт-Петербург (на участке до ст. Куликово и о. п…
Дипломная 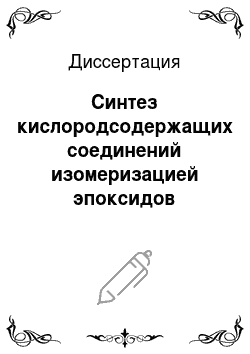
Ненасыщенные спирты применяются в синтезе фармацевтических /1/ и парфюмерных препаратов /12 — 14/, вкусовых добавок. На основе ненасыщенных спиртов получают полимерные материалы, обладающие рядом ценных свойств и вследствие этого находящих применение в различных областях техники /15 — 17/. Так аллиловые смолы отличаются высокой термои хемостойкостью, твердостью, прозрачностью, устойчивостью…
Диссертация 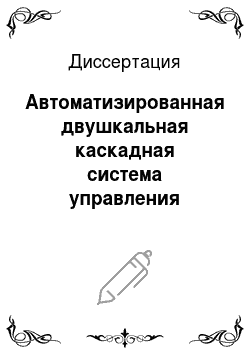
Практическая значимость работы. Разработана двушкальная каскадная автоматизированная система управления, позволяющая уменьшить погрешность продольного профиля нежестких валов при токарной обработке с начального значения ео = 0,1±0,03 мм до ±0,02 мм. Система также позволяет в реальном времени обработки деталей построить модель систематической погрешности обработки и настроить прямой канал…
Диссертация 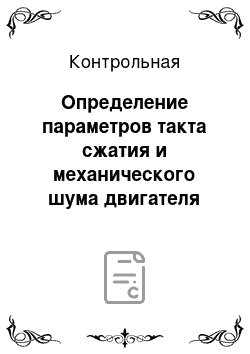
Применение алюминиевых поршней и головок блока цилиндра увеличивает отвод теплоты и n1 имеет более низкие значения из-за повышенной теплопроводности алюминия по сравнению с чугуном. Для уменьшения отвода теплоты и получения более высоких значений n1 необходимо, чтобы отношение Fпов/Vh было по возможности меньше. Его значение зависит от рабочего объема Vh (при большом Vh отношение Fпов/Vh=const/D…
Контрольная 
В настоящее время в России ведется крупномасштабная работа по экономии всех видов энергоресурсов. Усиливающиеся товарно-денежные отношения, постоянный рост цен на энергоносители заставляет производителей и потребителей энергии все чаще задумываться о ее стоимости и путях экономии. Еще 10−15 лет назад производство и потребление таких видов энергоресурсов, как горячая и холодная вода, пар, чаще…
Диссертация 
С целью повышения эффективности перевозочного процесса на железнодорожном транспорте и его конкурентоспособности, в настоящее время ведется интенсивная работа по созданию новых и модернизации существующих конструкций вагонов. В обеспечении безопасности движения и комфорта основополагающую роль играет разработка ходовых частей. Одним из основных направлений улучшения динамических качеств вагона…
Диссертация 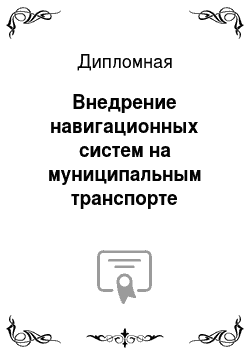
Использование спутниковых навигационных систем в России С точки зрения действующего законодательства Российской Федерации порядок ввоза на территорию России, приобретения и эксплуатации спутниковых навигационных приемников в России носит разрешительный характер. Причиной этому является то, что на основании Федерального Закона РФ «О связи» № 15ФЗ от 16.02.95 в ред. от 17.07.99 Правительство…
Дипломная 
Современный опыт сертификации показывает, что качество ее результатов в основном зависит от эффективности сертификационных испытаний, обеспечивающих подтверждение соответствия сертифицируемого технического объекта установленным требованиям. Поэтому не менее остро стоит проблема совершенствования технологии и повышения эффективности лабораторностендовых сертификационных испытаний изделий…
Диссертация 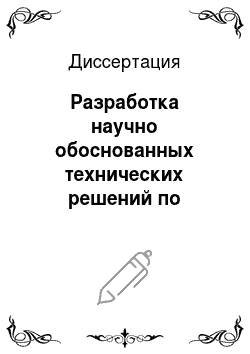
Достоверность основных научных положений, выводов и рекомендаций обоснована соответствующими теоретическими доказательствами, базирующимися на фундаментальных физических законах и основах механики, результатах вычислительных экспериментов на математических моделях динамических моделей тяжелых КГШП, адекватность которых и обоснованность принятых допущений подтверждена экспериментальными…
Диссертация 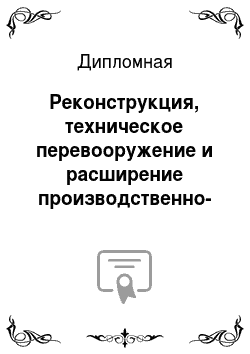
Таблица 5.7 — Состав отработанных газов двигателя внутреннего сгорания Компоненты выхлопного газа Содержание по объему, % Примечание бензиновые дизели Азот 74,0 — 77,0 76,0 — 78,0 нетоксичен Кислород 0,3 — 8,0 2,0 — 18,0 нетоксичен Пары воды 3,0 — 5,5 0,5 — 4,0 нетоксичны Диоксид углерода 5,0 — 12,0 1,0 — 10,0 нетоксичен Оксид углерода 0,1 — 10,0 0,01 — 5,0 токсичен Углеводороды неканцерогенные…
Дипломная