Другие работы
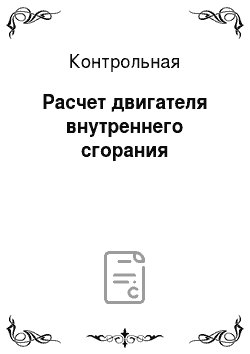
Из точки, А восстанавливаем перпендикуляр вверх равный силам инерции в ВМТ. Из точки В опускаем перпендикуляр вниз равный силам инерции в НМТ. Полученные точки С и D соединяем тонкой линией. Из точки пересечения Е опускаем перпендикуляр вниз равный отрезку ЕF. Соединяем точки CF и FD. Полученные отрезки делим на равное количество частей (6−8) и тонкими линиями соединяем одноименные точки…
Контрольная 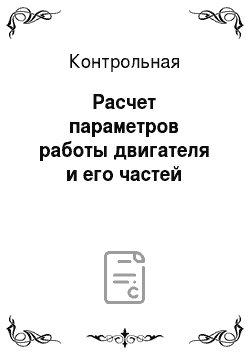
Подобрать прессовую посадку, обеспечивающую соединение зубчатого колеса с валом (шпонку не учитывать). Соединение нагружено вращающим моментом М и осевой силой Fа. Диаметр d и длина l посадочной поверхности, условный наружный диаметр ступицы d2, вал сплошной (d1 = 0). Материал зубчатого колеса и вала — сталь 45. Сборка прессованием. Коэффициент запаса сцепления К = 1,5, коэффициент трения f…
Контрольная 
Рисунок 2.7 — Десятиступенчатая коробка передач David Brawn, тип 557А Если передаточное число пониженной передачи в дополнительной коробке достаточно большое, чтобы увеличить общий диапазон, по крайней мере, вдвое, ее называют «демультипликатор». Если же она почти не увеличивает общий диапазон, а служит для получения «половинок» между передачами основной коробки, ее называют «делителем», имея…
Курсовая 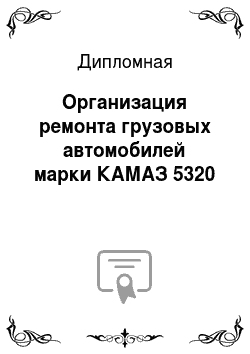
Описание графиков грузовых потоков: машина поступающая на ремонт ТОО «Автоцентр КамАЗ» заезжает в разборо-моечный участок I, где происходит разборка и мойка узлов подлежащих ремонту. Из разборо-моечного участка детали поступают в дефектовачный участок II. Изношенные детали, подлежащие ремонту поступают в слесарно-механический VII. Восстановленные детали поступают на участок комплектовки III куда…
Дипломная 
Экспериментально доказано, что вареные колбасы, изготовленные с заменой 10 и 15% свинины полужирной на гидратированный 1:7 яичный белок, обладают высокой пищевой ценностью: содержат больше белка и меньше жира (на 2−4%) — лучше сбалансированы по аминокислотному составуимеют более высокую степень переваримости белков «in vitro» — обладают улучшенными структурно-механическими показателями…
Диссертация 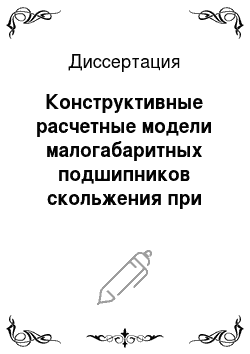
Исходными уравнениями являются уравнения движения Навье-Стокса, уравнение неразрывности и уравнение притока тепла (с учётом диссипативных членов). Рассматриваемая задача здесь решается при следующих граничных условиях: условие прилипания смазки к поверхности вала и вкладыша, равенство скоростей, касательных и нормальных напряжений, температур и тепловых потоков на границе раздела слоевтеплообмен…
Диссертация 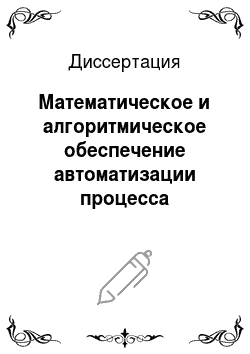
Результаты анализа процесса формования с точки зрения определения параметров, характеризующих качество формования и доступных для регистрации с помощью компьютерных видеотехнологий, и результаты исследования операций формования изделий конфетного производства в различных режимах с одновременным созданием базы видеоданных были переданы ОАО «Кондитерский концерн Бабаевский», что подтверждается…
Диссертация 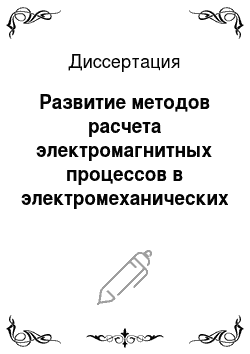
Работа выполнена в соответствии с научным направлением ЮжноРоссийского государственного технического университета (ЮРГТУ) «Интеллектуальные электромеханические устройства, системы и комплексы» от 25.01.1995 г., № 3.15, которое относится к «Приоритетным направлениям развития науки и техники», утвержденным Председателем правительства Российской Федерации 21 июня 1996 г., № 2727п.-118, разделы…
Диссертация 
К недостаткам речного транспорта следует отнести невысокий современные уровень материально-технической базы. Значительное количество технических средств перевозки и перегрузки устарели физически и морально, а обновления их нет. Многие пункты отправления и особенно прибытия грузов не имеют причальных сооружений и перегрузочной техники. Сокращается протяженность водных путей, оборудованных…
Диссертация 
Ухудшает сложившееся положение в отрасли то обстоятельство, что в настоящее время импорт тракторов и зерноуборочных комбайнов в Россию в 1,5 раза превысил объем их отечественного производства. При этом экономически оправданное присутствие зарубежных фирм на российском рынке составляет 10−15% (максимум 15−20%) к объему продаж всех видов техники. Ориентация на массовое применение импортной техники…
Диссертация 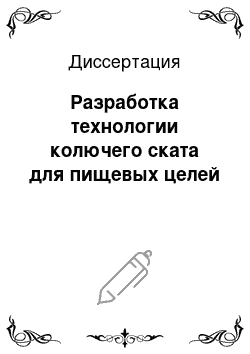
Рыбная промышленность может внести заметный вклад в осуществление продовольственной безопасности России. Рыба и другие морепродукты являются одними из самых важных и необходимых составляющих пищевого рациона человека. Они имеют огромное значение как источники белка, легкоусваиваимых жиров, витаминов, макрои микроэлементов. Однако в пределах исключительной экономической зоны России почти все…
Диссертация 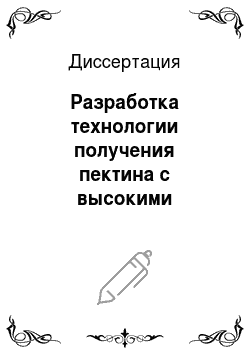
Экономически обоснована целесообразность внедрения в промышленное производство предлагаемой технологии электроосаждения пектина из пектинового экстракта. Ожидаемый экономический эффект от внедрения составляет 1,0 тыс. руб на 1 тонну сухого пектина. Математическое описание процесса электроосаждения пектина г.-гm = m (т, t) m = m (!) m = m (U) пч = Пч (U) Емет = Емет (U) Еам —ам (U…
Диссертация 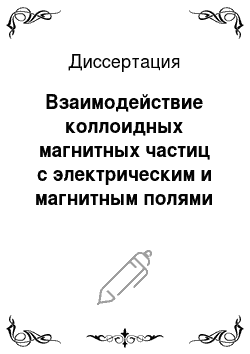
Актуальность работы. Во второй половине прошлого века были синтезированы коллоидные растворы магнитных материалов, которые впоследствии получили название «магнитные жидкости (Magnetic fluids)». Магнитные жидкости (МЖ) — ультрадисперсные (со средним диаметром dcp -10 нм) устойчивые коллоиды ферроили ферримагнитных однодоменных частиц, диспергированных в различных жидкостях и совершающих…
Диссертация 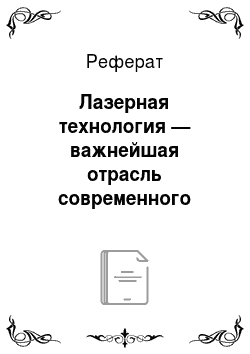
Собственным первоначальным фотоном. Для того чтобы среду с инверсной населенностью можно было использовать для генерации лазерного луча, т. е. направленного луча с высокой монохроматичностью, необходимо «снимать» инверсную населенность с помощью первичных фотонов, уже обладающих одной и той же энергией, совпадающей с энергией данного перехода в атоме. В этом случае мы будем иметь лазерный…
Реферат 
Пильный блок состоит из 8 балансирных пил, расположенных внизу под приемным столом и объединенных в 2 группы по 4 пилы с общим групповым электроприводом. Одновременное надвигание всех пил, участвующих в программе, производится при помощи силовых пневмотических цилиндров 5. Одновременно с включением пил на надвигание в работу включаются пневмоцилиндры прижимов 6 хлыста. Пилы в верхнем положении…
Реферат