Инструментальные материалы.
Резание материалов.
Режущий инструмент
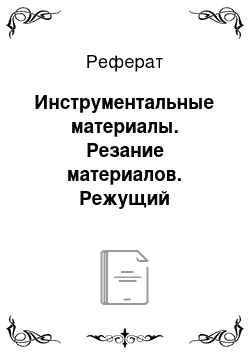
А — по скорости резания и подаче: 1 — быстрорежущие стали; 2 — твердые сплавы; 3 — твердые сплавы с покрытиями; 4 — нитридная керамика; 5 — черная керамика (керметы); 6 — оксидная (белая) керамика; 7 — кубический нитрид бора; б — по служебному назначению: 1 — для обработки конструкционных материалов с аь< 900 МПа (Р6М5, Р12, Р18); 2 — для обработки конструкционных материалов на повышенных… Читать ещё >
Инструментальные материалы. Резание материалов. Режущий инструмент (реферат, курсовая, диплом, контрольная)
В результате изучения данной главы студент должен:
знать
- • требования, предъявляемые к рабочей части инструмента;
- • виды и основные механические и физико-химические свойства инструментальных сталей, твердых сплавов, керамических сверхтвердых материалов, абразивных материалов;
- • физическую сущность явлений, происходящих в материалах при их производстве и эксплуатации изделий из них под воздействием различных эксплуатационных факторов;
уметь
- • выбирать инструментальные материалы;
- • оценивать и прогнозировать поведение инструментальных материалов;
- • устанавливать причины отказов режущей части инструмента под воздействием на них различных эксплуатационных факторов;
владеть
- • навыками выбора инструментальных материалов и назначения их обработки;
- • методиками оценки и прогнозирования поведения инструментальных материалов;
- • навыками анализа причин отказов режущей части инструмента при их эксплуатации.
Инструментальные стали
Материал режущей части инструмента находится во взаимодействии с обрабатываемым материалом и оказывает влияние на процесс резания и производительность обработки.
В этой связи к материалу режущей части инструмента предъявляются следующие требования:
- • высокая изностостойкость, т. е. способность сопротивляться износу (высокая твердость; высокая прочность; высокая теплостойкость, характеризующаяся наивысшей температурой, при которой инструментальный материал сохраняет свою твердость);
- • малочувствителыюсть к циклическим колебаниям температуры (при прерывистом резании);
- • стойкость к появлению усталостных трещин;
- • высокая теплопроводность, т. е. способность отводить теплоту из зоны резания, что снижает температуру режущей кромки;
- • хорошая технологичность (шлифуемость, закаливаемость, прокаливаемость, устойчивость против перегрева, окисления, отсутствие склонности к образованию трещин, обрабатываемость);
- • экономическая целесообразность (некоторые материалы имеют высокую стоимость и являются высокодефицитными, что ограничивает их применение).
Перечисленные требования взаимно противоречивы: если повышается твердость, то снижается прочность, высокая прочность приводит к ухудшению обрабатываемости и других технологических свойств.
В табл. 2.1 приведены основные физико-механические свойства некоторых инструментальных материалов и их компонентов [1 ].
Таблица 2.1
Основные физико-мсханичсскис свойства некоторых инструментальных материалов и их компонентов.
Инструментальный материал. | Микротвердость HV, МПа. | Твердость. 11RA. | Предельная прочность, МПа. | Теплостойкость (красностойкость), °С. | Коэффициент теплопроводности X | |
при изгибе. | при сжатии. | |||||
Быстрорежущая сталь. | —. | До 80. | До 4000. | До 4000. | До 700. | 16,75−25,12. |
Твердые сплавы. | 17 000- 4000. | 87−92. | 800−1000. | 16,75−87,92. | ||
Минсралоксра; мика: оксидные керметы. | 30 000- 19 000. | До 94. | 950−980. |
| 2000;1400. | 4,2−21,0. |
кубический нитрид бора. | 60 000— 80 000. | Свыше. 95,3. | 25,12−83,70. | |||
Алмазы искусственные. | 100 000. | —. | 138−146,5. |
В настоящее время при изготовлении режущего инструмента для обработки металлов резанием применяются четыре основные группы инструментальных материалов:
- • инструментальные стали;
- • твердые сплавы (ТС);
- • режущая керамика;
- • сверхтвердые материалы.
Из быстрорежущей стали изготавливают около 55—70% инструмента, из твердых сплавов — 25—40%, из остальных групп — 5%.
Инструментальные стали по своему химическому составу, степени легированное™ подразделяют на инструментальные углеродистые, инструментальные легированные и быстрорежущие (БРС).
Инструментальные углеродистые стали обозначают буквой У, за ней следует цифра, характеризующая содержание углерода в стали, умноженное на 10. Так, в стати марки У10 содержание углерода составляет 1%. Буква Л в конце соответствует высококачественным сталям с пониженным содержанием примесей.
Углеродистую инструментальную сталь (У7А—У13А) мало используют для изготовления режущего инструмента ввиду ее недостаточной теплостойкости. Ее применяют в единичном и мелкосерийном производстве для изготовления инструмента небольших размеров, работающего при скорого сти 10—15 м/мин: это дисковые пилы, сверла небольшого диаметра, развертки, метчики, протяжки, круглые плашки, зенкеры, долбяки, гребенки.
Характерной особенностью углеродистой стали является ее неглубокая прокаливаемость. Это свойство ценно для инструментов, работающих на удар. После закалки и отпуска инструменты из этой стали хорошо шлифуются и доводятся, что обеспечивает высокую остроту режущей кромки (РК), и поэтому их применяют там, где требуется получить высокое качество обработанной поверхности при малых скоростях резания.
Инструментальные легированные стали обозначают цифрой, которая характеризует содержание углерода в десятых долях процента (если цифра отсутствует, то углерода содержится приблизительно 1%), за которой следуют буквы, соответствующие легирующим элементам (Г — марганец, X — хром, С — кремний, В — вольфрам, Ф — ванадий, М — молибден, Т — титан), и цифры, обозначающие содержание элемента в процентах. Инструментальные легированные стали глубокой прокаливаемости марок 9ХС, ХВСГ, XI2М, ХВГ отличаются малыми деформациями при термической обработке.
По применению инструментальные легированные стали подразделяют на две группы:
- • для режущего и мерительного инструмента;
- • для штамнового инструмента.
Наибольшее распространение для изготовления режущего инструмента получили стали 9ХС, Х12М, ХВГ, основное применение которых — изготовление осевых РИ, таких как протяжки, сверла, метчики.
Разупрочнение мартенсита при нагреве во время резания закаленных углеродистых сталей происходит при температуре 200 °C. В легированных и быстрорежущих сталях разупрочнение мартенсита сдерживается наличием легирующих элементов, которые имеют большее, чем железо, сродство с углеродом и образуют более теплостойкие карбиды, которые легко растворяются в а-железе.
В инструментальных легированных сталях массовое содержание этих элементов недостаточно, чтобы связать углерод в карбиды, поэтому теплостойкость сталей этой группы лишь на 50— 100 °C превышает теплостойкость инструментальных углеродистых сталей. В инструментальной БРС теплостойкость повышается до 560—720°С, что достигается путем соединения большей части углерода в карбиды легирующих элементов (вольфрам, молибден, хром, ванадий), при этом исключается образование карбидов железа.
Инструментальные быстрорежущие стали. В начале марки БРС указывается буква Р (индекс данной группы сталей), затем число, показывающее содержание вольфрама (основной легирующий элемент), и обозначения других легирующих элементов с цифрами, показывающими среднее содержание элемента в процентах. Содержание хрома в БРС составляет примерно 4% (табл. 2.2) 11J.
Углерод должен находиться в определенном соотношении с карбидообразующими элементами. В последние годы наблюдается тенденция к увеличению содержания углерода, что повышает твердость, красностойкость, но снижает прочность, ухудшает технологические свойства. Вольфрам придает БРС теплостойкость, хром обеспечивает хорошую прокаливаемость и коррозионную стойкость; ванадий увеличивает теплостойкость, но при этом ухудшается шлифуемость; молибден повышает теплопроводность стаТаблица 2.2
Примерное содержание легирующих элементов в быстрорежущей стали.
Группа. | Марка материала. | Средний химический состав, %. | |||||
С. | W. | Мо. | Сг. | V. | Со. | ||
Базовая. | Р6М5. | 0,86. | 6,0. | 5,0. | 4,1. | 1,9. | До 0,5. |
Р18. | 0,78. | 17,75. | До1. | 1,2. | |||
С увеличенным содержанием хрома и ванадия. | Р6М5ФЗ. | 1,0. | 6,2. | 5,0. | 4,1. | 2,5. | До 0,5. |
Содержащая кобальт. | Р6М5К5. | 0,9. | 6,2. | 5,0. | 4,1. | 1,9. | 5,0. |
Р9М4К8. | 1,05. | 9,0. | 4,0. | 3,3. | 2,5. | 8,0. |
ли; кобальт придает повышенную твердость и теплостойкость, но увеличивает хрупкость стали, появляется склонность к обезуглероживанию.
Все это приводит к тому, что разупрочнение БРС происходит при более высоких температурах (табл. 2.3).
Таблица 2.3
Показатели прочности, твердости и теплостойкости.
Марка материала. | Прочность на изгиб C7″:ir, МПа. | Твердость IIRC. | Теплостойкость, «С, при твердости 59 HRC. |
Р6М5. | 3000−4000. | 63−66. | |
Р18. | 2600−3200. | 62−65. | |
Р6М5ФЗ. | 2000;3200. | 64−66. | |
Р6М5К5. | 2400−3000. | ||
Р9М4К8. | 2000;2700. | 64−67. |
Быстрорежущие стати подразделяют натри группы: БРС нормальной производительности, БРС повышенной производительности и порошковые БРС.
Быстрорежущие стали нормальной производительности (базовая группа) используются для изготовления режущего инструмента, предназначенного в основном для обработки конструкционных сталей, ферритноперлитных чугунов твердостью до 220 НВ и цветных сплавов. Основной маркой этой группы является стать Р6М5, которая предназначена для изготовления большинства режущих инструментов: резцов, фрез, сверл, зенкеров, разверток, протяжек, резьбообрабатывающих инструментов (до 70% инструментов из инструментальных сталей).
Быстрорежущие стали повышенной производительности характеризуются увеличенным содержанием углерода и ванадия. Сталь Р6М5ФЗ обладает износостойкостью на 30—40% больше, чем Р6М5, но уступает ей по шлифуемости. Сталь Р6М5ФЗ применяют с целью повышения стойкости таких инструментов, как резцы, сверла, зенкеры и т. п.
Быстрорежущие стали повышенной производительности, содержащие кобальт, используются для изготовления режущего инструмента, предназначенного для обработки конструкционных сталей и перлитных чугунов твердостью более 280 НВ. Наиболее широко используемой кобальтсодержащей БРС является сталь Р6М5К5, применение которой, по сравнению с Р6М5, обеспечивает рост скорости резания в среднем на 20% и увеличение количества периодов стойкости инструментов в 1,5—3 раза.
Сталь Р9М4К8 обладает повышенной износостойкостью по сравнению с Р6М5К5, но уступает ей по прочности, шлифуемости и является более дорогой. Она применяется, когда режущие свойства стали Р6М5К5 недостаточны. В отдельных случаях обработка деталей высокой твердости осуществляется с применением БРС Р12МЗФ2К8. Эта сталь превосходит по износостойкости Р9М4К8, но уступает ей по прочности и шлифуемости и значительно дороже. Целесообразность применения стали Р12МЗФ2К8 на конкретных операциях определяется предварительным испытанием.
Порошковые быстрорежущие стали. Наиболее эффективные возможности повышения качества БРС, эксплуатационных свойств и создания новых инструментальных материалов появились при использовании порошковой металлургии [5].
Порошковая БРС характеризуется однородной мелкозернистой структурой, равномерным распределением карбидной фазы, пониженной деформируемостью в процессе термической обработки, хорошей шлифуемостыо, более высокими технологическими и механическими свойствами, чем стали аналогичных марок, полученные по традиционной технологии [5].
Существуют два способа получения порошковой БРС: распылением водой и азотом. Изготовление режущего инструмента из БРС, полученной из водно-распыленных порошков, дешевле, однако качество такого металла ниже ввиду большей окисленности порошковых частиц. Поэтому для изготовления высококачественного металла используется порошок, полученный распылением азотом.
Промышленное производство порошковых БРС в начале 1980;х гг. было направлено на изготовление марок, являющихся аналогами сталей традиционной технологии. Опыт ряда зарубежных фирм (США, Швеция), а также отечественных исследователей показал, что новая технология позволяет существенно изменить схему легирования с целью направленного повышения тех или иных эксплуатационных характеристик, определяющих стойкость режущего инструмента.
Основные принципы разработки новых составов стали [5]:
- • введение в состав стали до 5—7% ванадия (по массе) с целью увеличения объемной доли карбидов типа МС в стали до 15% и повышения износостойкости без ухудшения шлифуемости;
- • повышение содержания углерода (выше стандартного содержания) в БРС, т. е.
введение
углерода с пресыщением} а также замена части углерода азотом, который вводят путем азотирования порошка непосредственно перед операцией компактировапия.
Реализация указанных принципов позволяет использовать относительно низкие массовые доли вольфрама, молибдена и кобальта для получения максимальных значений твердости и теплостойкости. Таким образом были разработаны порошковые быстрорежущие стали ДИ 100 (Р7М2Ф6) и ДИ 106 (Р9М2Ф5К6-М1) по ГОСТ 28 393–89. Инструменты, изготовленные из указанных сталей, показали высокую эффективность при многочисленных промышленных испытаниях [5].
Технология порошковой металлургии также используется для получения карбидосталей, которые по своим свойствам могут быть классифицированы как промежуточные между БРС и твердыми сплавами.
Карбидостали отличаются от обычных БРС высоким содержанием карбидной фазы (в основном карбидов титана), что достигается путем смешивания порошка быстрорежущей стали и мелкодисперсных частиц карбида титана. Содержание карбидной фазы в карбидостали колеблется в пределах 30—70%. Пластическим деформированием, главным образом экструзией, из спрессованного порошка получают заготовки простой формы. В отожженном состоянии твердость карбидостали составляет 40—44 HRC, а после закалки и отпуска — 68—70 HRC.
При использовании в качестве материма РИ карбидосталь обеспечивает повышение стойкости в 1,5—2 раза по сравнению с аналогичными марками обычной технологии производства. В ряде случаев карбидосталь является полноценным заменителем твердых сплавов, особенно при изготовлении формообразующих инструментов.
Выбор БРС для конкретных условий резания определяется большим числом факторов. Этот выбор не является однозначным, так как каждая группа сталей представлена несколькими марками. Определяющим условием являются свойства обрабатываемого материала и режимы резания (рис. 2.1, а)у а для некоторых видов инструмента — и технологические особенности стали (рис. 2.1, б).
Для обработки конструкционных материалов прочностью менее 600— 700 МПа рекомендуются низколегированные БРС (цветные металлы (например, сплавы на алюминиевой основе); отожженные конструкционные стали; серые чугуны и т. д.).
Для обработки конструкционных материалов прочностью до 1000 МПа используются стали умеренной теплостойкости: Р6М5, Р6М5К5, Р6М5ФЗ и др.
Для обработки конструкционных материалов повышенной прочности (свыше 1200 МПа), а также труднообрабатываемых материалов (нержавеющие и жаропрочные стали и сплавы, титановые сплавы, улучшенные стали с повышенной твердостью и др.) рекомендуются стали повышенной теплостойкости [5].
Применение сталей повышенной теплостойкости рекомендуют и для обработки стандартных конструкционных материалов, в тех случаях, когда требуется значительное повышение стойкости режущего инструмента или производительности обработки (скорости резания). В первом случае используют высокованадиевые стали, во втором — кобальтовые [5].
Учитывая эти рекомендации, следует иметь в виду, что в пределах каждой группы большей прочностью обладают стали, легированные молибденом, а более высокой теплостойкостью — вольфрамовые. Например, при использовании кобальтовых сталей для работы в условиях ударных нагрузок рекомендуется БРС типа Р6М5К5 |5|, так как она обладает наибольшей прочностью среди кобальтовых сталей.
В случае когда от режущих инструментов требуются высокая износостойкость и эксплуатационная надежность, наиболее целесообразно для их изготовления применять БРС с повышенным содержанием ванадия, в том числе легированные кобальтом. Это прежде всего относится к режущему инструменту, работающему в условиях автоматизированного производства.
Среди технологических свойств, влияющих на выбор БРС, следует выделить обрабатываемость при шлифовании. Это важнейшее свойство определяет не только особенности изготовления инструмента, но и его эффективность.


Рис. 2.1. К классификации инструментальных материалов по назначению и скорости резания и подаче:
а — по скорости резания и подаче: 1 — быстрорежущие стали; 2 — твердые сплавы; 3 — твердые сплавы с покрытиями; 4 — нитридная керамика; 5 — черная керамика (керметы); 6 — оксидная (белая) керамика; 7 — кубический нитрид бора; б — по служебному назначению: 1 — для обработки конструкционных материалов с аь< 900 МПа (Р6М5, Р12, Р18); 2 — для обработки конструкционных материалов на повышенных скоростях резания, чистовой и получистовой обработки коррозионностойких и жаропрочных сталей и сплавов (Р6М5ФЗ, Р12ФЗ, Р14Ф4, Р2М9Ф2КЗ, Р6М5К5, Р9К5, 10Р6М5К5); - для обработки материалов твердостью 45—50 HRC, коррозионностойких и жаропрочных сталей и сплавов, конструкционных сталей на высоких скоростях (Р7М4Ф2К8, Р9М4К8, Р12МЗФ2К8, Р8МЗК6С); 4 — для чистовой и получистовой обработки высокопрочных, жаропрочных и других специальных сталей и сплавов (Р12Ф4К5, Р10Ф5К5, Р12М4ФЗК10, Р12М2Ф4К10); 5 — для чистовой обработки специальных сталей и сплавов (сплавы типа В11М7К23); 2' — порошковые стали и в ряде случаев может оказаться решающим фактором при выборе марки стали для определенных видов инструмента, например для резьбонарезного.
Основным фактором, определяющим обрабатываемость шлифованием, является содержание в стали ванадия, образующего карбиды MevC высокой твердости. Но шлифуемое™ БРС можно подразделить на четыре группы (рис. 2.2, а) [5]:
- • группа 1: содержание ванадия — до 1,3%, относительная шлифуемость — 0,9—1 (за единицу принята обрабатываемость при шлифовании стали Р18, обладающей наилучшей шлифуемостью);
- • группа 2: содержание ванадия — 1,6—2,5%, относительная шлифуемость — 0,4—0,95. В эту группу, в частности, входит сталь Р6М5;
- • группа 3 содержание ванадия — 2,6—3,3%, относительная шлифуемость — 0,2—0,5;
- • группа 4: содержание ванадия — более 4%, относительная шлифуемость — 0,2—0,3.
Порошковые БРС независимо от содержания ванадия относятся к группам 1 и 2.
При низком (группа 1) и высоком (группа 4) содержании ванадия относительная шлифуемость не зависит от содержания вольфрама и молибдена: в первом случае шлифуемость хорошая, в последнем — плохая.
Стали с пониженной шлифуемостью склонны к ирижогам, г. е. к изменению структуры приповерхностных слоев стали после шлифования или затачива;

Рис. 2.2. Изменение твердости стали после шлифования с прижогами (а) и влияние суммарного содержания вольфрама и молибдена на шлифуемость быстрорежущих сталей (б):
К — интервал колебаний шлифуемости; D — содержание W + Мо.

ния, появлению вторичной закатки с большим количеством аустенита, зон вторичного отпуска с пониженной твердостью (см. рис. 2.2, а). Следствием прижогов является значительное снижение стойкости режущего инструмента.
Для сталей групп 2 и 3 лучшая шлифуемость достигается у сталей с соотношением W + 1,5Мо = 12—14%, так как в этом случае растворимость ванадия в них максимальна. Указанное, в свою очередь, означает, что количество карбидов ванадия в таких сталях при прочих равных условиях наименьшее. Вместе с тем для этих сталей относительная шлифуемость в большей степени зависит от содержания вольфрама и молибдена (а также ванадия и углерода), даже в пределах плавочного состава. Таким образом, для таких сталей надежно гарантировать высокую шлифуемость невозможно. На рис. 2.2, 6 указан интервал колебаний шлифуемости К в зависимости от D — содержания W + Мо — в пределах состава для некоторых марок стали [5].