Прогрессивные конструкции абразивных инструментов
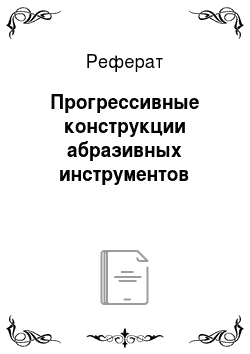
Пропитку абразивных инструментов применяют как средство регулирования их прочностных свойств и твердости и как способ применения смазки. В первом случае, например, для повышения твердости абразивных инструментов на керамической связке производят пропитку инструмента в бакелитовом растворе, а для снижения твердости этих же инструментов их кипятят в водном растворе каустической соды. Во втором… Читать ещё >
Прогрессивные конструкции абразивных инструментов (реферат, курсовая, диплом, контрольная)
Прерывистые шлифовальные круги (рис. 16.12) изготавливают путем прорезания, накатывания или прессования пазов на рабочих поверхностях обычных абразивных кругов. Для изготовления таких кругов рекомендуется использовать круги с повышенной на 1—2 степени твердостью и меньшей зернистостью по сравнению с обычными кругами.
Наличие впадин на рабочей поверхности круга обеспечивает лучшие условия охлаждения шлифуемой поверхности путем подвода СОТС непосредственно в зону контакта круга с заготовкой. В зависимости от протяженности впадин (2—45 мм) силы и температура шлифования снижаются на 10—40%. Благодаря этому при работе на повышенных режимах резания и при обработке высокопрочных материалов уменьшается вероятность появления поверхностных дефектов — ирижогов и микротрещин.
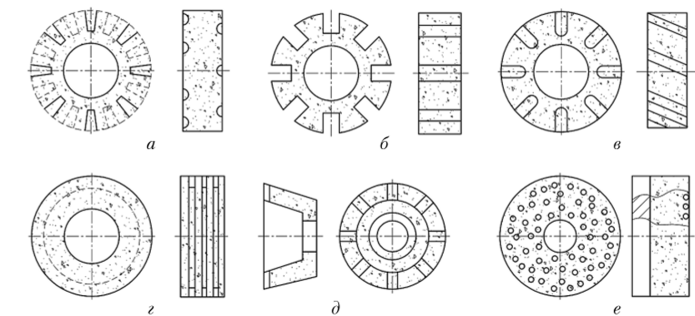
Рис. 16.12. Прерывистые абразивные круги:
а — с выточками; б — с пазами; в — с прорезями; г — с канавками; д — с насечками;
е — с отверстиями Абразивные высокопористые круги благодаря порам обладают лучшим проникновением СОТС в зону обработки, хорошей самозатачиваемостью и меньшей засаливаемостью. Применение таких кругов уменьшает число зерен на рабочей поверхности круга и силу резания, приходящуюся на одно зерно, облегчает правку и повышает эффективность использования СОТС. Однако прочность пористых кругов несколько меньше прочности обычных кругов.
Схема устройства для подачи СОТС через поры круга показана на рис. 16.13. Здесь СОТС через осевое отверстие в шпинделе станка 3, радиальные отверстия 2 подводится к шлифовальному кругу 1, а затем иод действием центробежных сил проходит через поры круга на его рабочую поверхность (периферию круга). При этом СОТС одновременно с охлаждением зоны обработки обеспечивает очистку рабочей поверхности круга от затупившихся зерен.
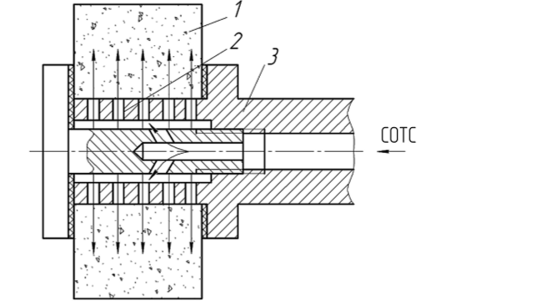
Рис. 16.13. Подача СОТС через поры шлифовального круга:
1 — шлифовальный круг; 2 — радиальные отверстия; 3 — шпиндель станка Пористые круги изготавливают на керамической связке. Причем высокопористое строение круга создается либо из-за газообразования при химической реакции, протекающей в круге во время его изготовления, либо путем введения выгорающих добавок в состав круга. Чаще всего в качестве порообразователей используют порошки синтетических смол, искусственных и природных материалов (нафталин, полистирол, кокс, торф, опилки, перлит и др.).
Введение
таких выгорающих добавок приводит к образованию в процессе термообработки инструмента большой объемной пористости (до 70%) и к увеличению размеров отдельных пор. Так, например, при использовании в качестве иорообразующего наполнителя синтетического полистирола марки I ICC и перлита марки 11 объемное содержание пор для кругов зернистостью 40—16 может находиться в пределах 5—25%, а зернистостью 12—6 — в пределах 10—30%.
Применение высокопористых кругов приводит к снижению в 1,5—1,7 раза температуры обрабатываемой поверхности, что позволяет осуществлять бесприжоговое шлифование труднообрабатываемых материалов. При этом уменьшаются энергетические затраты, а производительность процесса шлифования возрастает на 15—70%.
Имнрегнированные шлифовальные круги — это абразивные круги, пропитанные специальными составами — импрегнаторами (графит, дисульфид молибдена, стеарин, парафин, формальдегидные смолы и др.). Заполнение пор абразивных кругов наиболее часто осуществляют путем свободного капиллярного заполнения их жидкими составами.
Пропитку абразивных инструментов применяют как средство регулирования их прочностных свойств и твердости и как способ применения смазки. В первом случае, например, для повышения твердости абразивных инструментов на керамической связке производят пропитку инструмента в бакелитовом растворе, а для снижения твердости этих же инструментов их кипятят в водном растворе каустической соды. Во втором случае пропитку используют для изменения процессов контактного взаимодействия инструмента с заготовкой, благодаря чему на поверхностях абразивных зерен и связки формируется смазочное покрытие, а в порах инструмента создаются микрообъемы смазки, которая находится в твердом или пластическом состоянии. После размягчения смазки теплотой резания она перемещается в зону обработки под действием центробежных сил.
Эффективность импрегнирования значительно выше при сухом шлифовании, чем при работе с СОТС, и при обработке закаленных сталей, чем при обработке сталей незакаленных. В целом импрегнирование позволяет существенно повысить стойкость шлифовальных кругов (в 2—4 раза), снизить их засаливаемость и уменьшить шероховатость обработанной поверхности. В ряде случаев устраняются скрытые тепловые дефекты шлифованной поверхности.
Круги для высокоскоростного шлифования работают на скоростях 80— 120 м/с вместо скоростей 25—35 м/с, имеющих место при обычном шлифовании. Это позволяет увеличить стойкость кругов, повысить производительность обработки, а также точность и качество обработанной поверхности.
При высоких скоростях вращения в шлифовальных кругах возникают большие напряжения, вызываемые центробежной силой. Для повышения прочности таких кругов применяют специальные керамические связки К5 и Кб — для работы со скоростью 60 м/с и К43 и К43Л — для работы со скоростью 80 м/с. Применяют также круги переменного сечения с утолщением центральной части, плавно снижающейся к рабочей части. Иногда центральную часть кругов на керамической связке пропитывают термопластичными составами, например эпоксидной смолой и др.
Точность кругов для высокоскоростной обработки должна быть классов АА и А, неуравновешенность — не ниже класса 2 для кругов с рабочей скоростью до 60 м/с и не ниже класса 1 для кругов, работающих со скоростью 80 м/с.
Круги для глубинного шлифования. Круги для глубинного шлифования чаще всего используют для вышлифовывания за 1—4 рабочих хода стружечных канавок сверл, концевых и шпоночных фрез, разверток, метчиков и других концевых инструментов в закаленных стальных или спеченных твердосплавных заготовках.
Основными достоинствами глубинного шлифования являются высокие производительность (в 1,5—2,0 раза выше, чем при фрезеровании) и точность обработки при низких трудоемкости и стоимости. Этот процесс требует больших энергетических затрат и характеризуется интенсивным тепловыделением. Поэтому вышлифовывание стружечных канавок со снятием полного припуска применяют в основном при изготовлении концевых инструментов диаметром до 15 мм. В инструментах больших размеров канавки предварительно получают методами пластического деформирования (прокатыванием или прессованием), а лишь затем шлифуют.
Для вышлифовывания и шлифования канавок инструментов из БРС абразивными кругами обычно применяют круги из электрокорунда 24А на вулканитовой и бакелитовой связках зернистостью 10—16, твердостью СТ2—СТ1 или эльборовые круги на металлической связке (концентрация зерен эльбора — 200%). Канавки твердосплавных инструментов вышлифовывают алмазными кругами на металлической связке. При использовании алмазных кругов на органической связке чаще применяют многопроходное шлифование.
Профиль шлифовального круга для вышлифовывания канавок концевых инструментов очерчивается в основном дугами окружностей и прямыми. Так, например, для вышлифовывания канавок сверл наибольшее применение получили радиусно-угловой и двухрадиусный профиль, причем у радиусно-углового профиля круга коническая сторона расположена под углом Pv = 15-^35°. Для повышения стойкости угловой кромки шлифовального круга диаметром D ее скругляют радиусом (0,1h-0,15)D. Для увеличения ширины круга при вышлифовывании канавок мелкоразмерных сверл (D = 0,2-г-1,5 мм) используют трехрадиусный профиль.
Упрощенный двухугловой профиль применяют при вышлифовывании канавок в условиях мелкосерийного производства, а также при вышлифовке резьбы на метчиках.
Абразивные ленты применяют для ленточного шлифования и полирования сложнофасонных заготовок практически из всех материалов. Суть ленточного шлифования состоит в том, что лентопротяжный механизм ленточно-шлифовального станка, состоящий из двух шкивов, охваченных с некоторым натяжением бесконечной абразивной лентой, передает на последнюю крутящий момент. Этим обеспечивается главное движение резания. В месте контакта с заготовкой лента поджимается опорой, профилирующей ленту по форме обрабатываемой поверхности.
Особенность обработки бесконечными лентами состоит в создании предварительного статического нагружения на абразивные зерна путем прижима ленты к обрабатываемой поверхности и деформирования основания ленты. Это позволяет улучшить условия работы абразивных зерен, повысить их износостойкость, устранить ирижоги и микротрещины, улучшить самозатачиваемость режущих зерен и уменьшить интенсивность засаливания ленты. Упругие опоры позволяют вести обработку маложестких заготовок, что невозможно осуществлять на обычных шлифовальных станках.
Для ленточного шлифования применяют шлифовальные ленты на тканевой и бумажной основах зернистостью М80—М40 из электрокорунда, карбида кремния и эльбора ЛМ10—ЛМ20. Ширина и длина ленты зависят от размеров обрабатываемой заготовки и конструкции станка.
Бесконечность ленты достигается путем склеивания ее концов. Работоспособность ленты зависит от ее размеров, эластичности и жесткости контактной опоры, свойств обрабатываемого материала, размеров заготовки и режима обработки: давления на ленту, скорости ленты и глубины шлифования. Оптимальные скорость ленты и давление заготовок на ленту для разных случаев обработки различны. Так, например, при обработке плоских заготовок из чугуна, бронзы и твердых сталей скорость ленты должна быть в пределах 15—20 м/с, а при цилиндрическом и профильном шлифовании сталей — 25—30 м/с. Давление на ленту при обработке цветных металлов и их сплавов должно быть не более 0,03—0,04 МПа, при обработке сталей и чугунов — 0,05—0,02 МПа.
Ленточное шлифование и полирование экономически более эффективны, чем обработка войлочными и тканевыми полировально-шлифовальными кругами.
Абразивные инструменты, закрепленные в корпусах сложных конструкций. Шлифовальные круги со вставными сегментами применяются в связи с тем, что сплошные круги больших диаметров малоэкономичны, так как материал круга плохо используется ввиду:
- • больших отходов, остающихся после окончательного износа круга;
- • наличия в круге трещин;
- • большой площади контакта круга с заготовкой, вызывающей сильный нагрев обрабатываемой поверхности;
- • затрудненных условий подвода СОТС в зону резания и отвода отходов шлифования.
Сборные круги применяют для плоского шлифования на вертикальных станках с круглым вращающимся столом. В этом случае шлифовальный круг состоит из нескольких сегментов, закрепленных механическим путем или клеем на стальном корпусе. При этом повреждение одного из сегментов не требует изъятия из эксплуатации всего круга, так как поврежденный сегмент легко заменяется новым. Пространство между сегментами облегчает подвод СОТС в зону резания и отвод шлама. Меньшая площадь контакта круга с заготовкой способствует уменьшению нагрева обрабатываемой поверхности, а следовательно, повышению ее качества. Последнее обстоятельство исключает прижоги при работе на повышенных скоростных режимах.
Хонинговальные головки применяют для окончательной обработки отверстий диаметром 1—1500 мм и глубиной до 25 000 мм. При этом точность обработанных отверстий достигает IT5—IT6, а шероховатость Ra 0,32—0,08. Такие высокие результаты объясняются тем, что, в отличие от шлифования, процесс хонингования характеризуется:
- • большой площадью контакта брусков с обрабатываемой поверхностью;
- • малой величиной давления брусков и низкой скоростью резания;
- • значительным числом одновременно работающих зерен;
- • низкой температурой в зоне резания.
При хонинговании головка вращается с окружной скоростью vKf) и совершает возвратно-поступательное перемещение вдоль оси обрабатываемого отверстия со скоростью vBn. При этом осуществляется непрерывный разжим брусков — радиальная подача.