Компрессор КТ-6. Контроллер машиниста
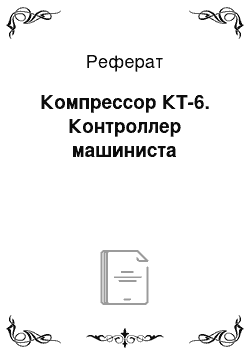
Рама; 8 — вал кулачковый Для предотвращения ошибочных действий при работе все три рукоятки механически сблокированы между собой так, что: при установке реверсивной рукоятки на позицию М главная рукоятка может быть установлена на любую позицию; при установке главной рукоятки на 16, 27 и 37-ю позиции тормозная рукоятка может быть установлена в положение ослабления поля ОП-1, ОП-2, ОП-3, ОП-4, при… Читать ещё >
Компрессор КТ-6. Контроллер машиниста (реферат, курсовая, диплом, контрольная)
компрессор электровоз контроллер машинист
В начале XX в. был разработан ряд оригинальных проектов тепловозов. В 1924 г. бывший Путиловский завод по проекту, разработанному под руководством проф. Я. М. Гаккеля, построил первый в мире магистральный тепловоз серии ТЭ-1 мощностью 1000 л. с. (736 кВт) с электрической передачей. В дальнейшем тепловозы серии ТЭ2, ТЭ3 строились на Коломенском тепловозостроительном заводе им. Куйбышева. Начиная с 1946 г., Харьковский завод транспортного машиностроения им. Малышева серийно выпускал тепловозы ТЭ1 (до 1948 г.), ТЭ2 (до 1955 г.) и ТЭЗ (до 1965 г.). Постройку тепловозов ТЭЗ мощностью 4000 л. с. (2941 кВт) вели также Ворошиловградский и Коломенский тепловозостроительные заводы.
На смену тепловозам ТЭЗ пришли более мощные и совершенные локомотивы 2ТЭ10Л, 2ТЭ10 В, ТЭП60 мощностью 3000 л. с. (2200 кВт) в секими, ТЭП70 мощностью 4000 л. с. (2941 кВт) и ТЭП75—6000 л. с. (4415 кВт).
Новые мощные тепловозы имеют ряд преимуществ по сравнению с тепловозом ТЭЗ: уменьшен удельный вес примерно в 1,5 раза и увеличена мощность двигателя в 1,5—3 раза; уменьшен удельный расход топлива на 5— 25 г/(э. л. с. ч); усовершенствована электрическая передача, система регулирования повысила надежность и экономическую эффективность передачи.
Более надежная и эффективная система охлаждения применена на тепловозах ТЭП60, ТЭП70 и 2ТЭ10 В. Для охлаждения масла использованы водо-масляный теплообменник и устройства для автоматического регулирования температур воды и масла при помощи гидростатического привода (ТЭП60) и гидромуфты переменного наполнения (2ТЭ10В).
Улучшена механическая часть за счет применения бесчелюстных тележек, более надежных несущих кузовов (цельносварных с рамой), усовершенствования рессорного подвешивания, оборудования кабин машиниста звукоизоляцией. Цельносварные кузова дают возможность снизить расход металла на этот узел на 15—20%.
Построены новые тепловозы ТЭ109, 2ТЭ116, ТЭП70, 2ТЭ121 и опытный тепловоз ТЭП75 мощностью 6000 л. с. (4415 кВт).
Тепловозы 2ТЭ116 мощностью 2×3000л. с. (2×2200 кВт) водной секции имеют дизель 5Д49; вместо него может быть установлен также дизель типа 2Д70 такой же экономичности. На этом тепловозе применена электрическая передача переменно-постоянного тока. Такая передача более надежна, экономична и компактна по сравнению с передачами постоянного тока. Холодильник тепловоза имеет смешанную систему с применением водомасляного теплообменника и вентиляторов с встроенными в них электродвигателями. На базе тепловоза ТЭ109 Ворошиловградским заводом строятся экспортные тепловозы мощностью 2600—3000 л. с. (1910—2200 кВт), поставляемые в социалистические и развивающиеся страны.
Применение передач переменно-постоянного и переменного токов обусловлено необходимостью сокращения габаритов электрических машин и повышения надежности работы.
РАЗДЕЛ 1 КОМПРЕССОР ЭЛЕКТРОВОЗА КТ6
1.1 Назначение, устройство, принцип работы компрессора КТ6
Компрессоры КТ-6 (Рис. 1.1.1), КТ-7 и КТ-6 Эл широко применяются на тепловозах и электровозах. Компрессоры КТ-6 и КТ-7 приводятся в действие либо от коленчатого вала дизеля, либо от электродвигателя, как например, на тепловозах 2ТЭ116. Компрессоры КТ-6 Эл приводятся в действие от электродвигателя.
Компрессор КТ-6 — двухступенчатый, трехцилиндровый. поршневой с Wобразным расположением цилиндров. Компрессор КТ-6 состоит из корпуса (картера)13, двух цилиндров 29 низкого давления (ЦНД), имеющих угол развала 120°. одного цилиндра 6 высокого давления (ЦВД) и холодильника 8 радиаторного типа с предохранительным клапаном 10, узла шатунов 7 и поршней 2, 5.
Рис. 1.1.1 Компрессор КТ6
1,4 — клапанные коробки, 2, 3, 5 -поршни; 6, 29 — цилиндр; 7 — шатун; 8 — холодильник; 9, 10 — предохранительный клапан; 11, 12, 13, 18 — корпус; 19 — коленчатый вал; 20 — масляный насос; 21 — редукционный клапан; 15, 16, 17, 22 — балансиры; 23 — винты; 25 — сетчатый масляный фильтр Корпус 18 имеет три привалочных фланца для установки цилиндров и два люка для доступа к деталям, находящимся внутри. Сбоку к корпусу прикреплен масляный насос 20 с редукционным клапаном 21, а в нижней части корпуса помещен сетчатый масляный фильтр 25. Передняя часть корпуса (со стороны привода) закрыта съемной крышкой, в которой расположен один из двух шарикоподшипников коленчатого вала 19. Второй шарикоподшипник расположен в корпусе со стороны масляного насоса. Все три цилиндра имеют ребра: ЦВД выполнен с горизонтальным оребрением для лучшей теплоотдачи, а ЦНД имеют вертикальные ребра для придания цилиндрам большей жесткости. В верхней части цилиндров расположены клапанные коробки 1 и 4.
Коленчатый вал 19 компрессора — стальной, штампованный с двумя противовесами, имеет две коренные шейки и одну шатунную. Для уменьшения амплитуды собственных колебаний к противовесам винтами 23 прикреплены дополнительные балансиры 22.
Для подвода масла к шатунным подшипникам коленчатый вал снабжен системой каналов, показанных на рис. 1.1.2. пунктиром.
Узел шатунов состоит из главного 1 и двух прицепных 5 шатунов, соединенных пальцами 14, застопоренными винтами 13.
Главный шатун выполнен из двух частей — собственно шатуна 1 и разъемной головки 4, жестко соединенных между собой пальцем 2 со штифтом 3 и пальцем 14. В верхние головки шатунов запрессованы бронзовые втулки 6. Съемная крышка 15 прикреплена к головке 4 четырьмя шпильками 7, гайки который стопорятся замковой шайбой 8. В расточке головки 4 главного шатуна установлены два стальных вкладыша 11 и 12, залитые баббитом.
Вкладыши удерживаются в головке за счет натяга и стопорения штифтом 10. Зазор между шейкой вала и подшипником шатуна регулируется прокладками 16.
Каналы 9 служат для подачи смазки к верхним головкам шатенов и к поршневым пальцам.
Рис 1.1.2 Узел шатунов компрессора КТ6
1- главный шатун, 2, 14 -пальцы, 3, 10 — штифты, 4- головка, 5- прицепные шатуны, 6- бронзовая втулка, 7- шпилька, 8- замковая шайба, 9- каналы для подачи смазки, 11, 12-вкладыши, 13- стопорный винт, 15- съемная крышка, 16- прокладка
Основным преимуществом данной системы шатенов является значительное уменьшение износа вкладышей и шатунной шейки коленчатого вала, которое обеспечивается передачей усилий от поршней через головку сразу на всю поверхность шейки.
Поршни 2 и 5 — литые чугунные. Они присоединяются к верхним головкам шатунов поршневыми пальцами 30 плавающего типа.
Для предотвращения осевого перемещения пальцев поршни снабжены стопорными кольцами. Поршневые пальцы ЦНД — стальные, пустотелые, поршневые пальцы ЦВД сплошные. На каждом поршне установлены по четыре поршневых кольца: два верхних — компрессионные (уплотнительные), два нижних — маслосъемные. Кольца имеют радиальные пазы для прохода масла, снятого с зеркала цилиндра.
Рис. 1.1.3 Клапанная коробка компрессора КТ-6
1- контргайка, 2- винт, 3, 15- крышки, 4- нагнетательный клапан, 5, 9 -упоры, 6- корпус, 7, 18 -прокладки, 8- всасывающий клапан, 10, 12- пружины, 11- стержень, 13- поршень, 14- резиновая диафрагма, 16- стакан, 17- асбестовый шнур Бвсасывающая полость, Ннагнетательная полость Клапанные коробки внутренней перегородкой разделены на две полости: всасывающую (В) и нагнетательную (Н).В клапанной коробке ЦНД со стороны всасывающей полости прикреплен всасывающий воздушный фильтр 9 а со стороны нагнетательной полости — холодильник 8. Корпус 6 клапанной коробки снаружи имеет оребрение и закрыт крышками 3 и 15. В нагнетательной полости помещен нагнетательный клапан 4, который прижат к гнезду в корпусе с помощью упора 5 и винта 2 с контргайкой 1.
Во всасывающей полости расположен всасывающий клапан 8 и разгрузочное устройство, необходимое для переключения компрессора в режим холостого хода при вращающемся коленчатом вале. Разгрузочное устройство включает в себя упор 9 с тремя пальцами, стержень 11, поршень 13 с резиновой диафрагмой 14 и две пружины 10 и 12.
Крышка 3 и седла клапанов уплотнены прокладками 18 и 7, а фланец стакана 16 — асбестовым шнуром 17.
Рис. 1.1.4 Всасывающий (а) и нагнетательный (б) клапаны компрессора КТ-6: 1- седла, 2- большие клапанные пластины, 3- малые клапанные пластины, 4- конические ленточные пружины, 5- обоймы (упоры), 6- корончатые гайки, 7- шпильки Всасывающие и нагнетательные клапаны состоят из седла 1, обоймы (упора) 5, большой клапанной пластины 2, малой клапанной пластины 3, конических ленточных пружин 4, шпильки 7 и корончатой гайки 6. Седла 1 по окружности имеют по два ряда окон для прохода воздуха. Нормальный ход клапанных пластин 1,5 — 2,7 мм. [1]
Разгрузочные устройства компрессора КТ-6 работают следующим образом: как только давление в ГР достигнет 8,5 кгс/см2 регулятор давления открывает доступ воздуха из резервуара в полость над диафрагмой 14 разгрузочных устройств клапанных коробок ЦНД и ЦВД. При этом поршень 13 переместится вниз. Вместе с ним после сжатия пружины 10 опустится вниз и упор 9, который своими пальцами отожмет малую и большую клапанные пластины от седла всасывающего клапана. Компрессор перейдет в режим холостого хода, при котором ЦВД будет всасывать и сжимать воздух, находящийся в холодильнике, а ЦНД будут засасывать воздух из атмосферы и выталкивать его обратно через воздушный фильтр. Это будет продолжаться до тех пор. пока в ГР не установится давление 7,5 кгс/см2, на которое отрегулирован регулятор. При этом регулятор давления сообщит полость над диафрагмой 14 с атмосферой, пружина 10 поднимет упор 9 вверх и клапанные пластины прижмутся к седлу своими коническими пружинами. Компрессор перейдет в рабочий режим. Компрессор КТ-6 Эл при достижении в ГР определенного давления в режим холостого хода не переводится, а отключается регулятором давления.
В процессе работы компрессора воздух между ступенями сжатия охлаждается в холодильнике радиаторного типа.
Холодильник состоит из верхнего и двух нижних коллекторов и двух радиаторных секций. Верхний коллектор перегородками разделен на три отсека. Секции радиаторов крепятся к верхнему коллектору на прокладках. Каждая секция состоит из 22 медных трубок, развальцованных вместе с латунными втулками в двух фланцах. На трубках навиты и припаяны латунные ленты, образующие ребра для увеличения поверхности теплоотдачи. [1]
Для ограничения величины давления в холодильнике на верхнем коллекторе установлен предохранительный клапан, отрегулированный на давление 4,5 кгс/см2. Фланцами патрубковхолодильник прикреплен к клапанным коробкам первой ступени сжатия, а фланцем — к клапанной коробке второй ступени. Нижние коллекторы снабжены спускными краниками для продувки радиаторных секций и нижних коллекторов и удаления скапливающихся в них масла и влага.
Воздух, нагретый при сжатии в ЦНД, поступает через нагнетательные клапаны в патрубки холодильника, а оттуда — в крайние отсеки верхнего коллектора. Воздух из крайних отсеков по 12 трубкам каждой радиаторной секции поступает в нижние коллекторы, откуда по трубкам каждой секции перетекает в средний отсек верхнего коллектора, из которого через всасывающий клапан проходит в ЦВД. Проходя по трубкам, воздух охлаждается, отдавая свое тепло через стенки трубок наружному воздуху. В то время как в одном ЦНД происходит всасывание воздуха из атмосферы, во втором ЦНД идет предварительное сжатие воздуха и нагнетание его в холодильник.
В это же время в ЦВД заканчивается процесс нагнетания воздуха в ГР. Холодильник и цилиндры обдуваются вентилятором, который установлен на кронштейне и приводится во вращение клиновым ремнем от шкива, установленного на муфте привода компрессора. Натяжка ремня осуществляется болтом.
Сообщение внутренней полости корпуса компрессора с атмосферой осуществляется через сапун 3, который предназначен для ликвидации избыточного давления воздуха в картере во время работы компрессора.
Рис. 1.1.6: 1- корпус, 2- решетка, 3- распорная пружина, 4- прокладка, 5,6- шайбы, 7- втулка, 8- упорная шайба, 9- пружина, 10- шпилька, 11- шплинт.
Сапун состоит из корпуса 1 и двух решеток 2, между которыми установлена распорная пружина 3 и помещена набивка из конского волоса или капроновых нитей. Над верхней решеткой помещена фетровая прокладка 4 с шайбами 5, 6 и втулкой 7. На шпильке 10 шплинтом 11 закреплена упорная шайба 8 пружины 9. При повышении давления в картере компрессора, например, за счет пропуска воздуха компрессионными кольцами, воздух проходит через слой набивки сапуна и перемещает вверх фетровую прокладку 4 с шайбами 5 и 6 и втулкой 7. Пружина 9 при этом оказывается сжатой. Сжатый воздух из картера компрессора выходит в атмосферу. [1]
При появлении в картере разрежения пружина 9 обеспечивает перемещение вниз прокладки 4, не допуская попадания в картер воздуха из атмосферу.
Смазка компрессора — комбинированная. Под давлением, создаваемым масляным насосом 20, смазываются шатунная шейка коленчатого вала, пальцы прицепных шатунов и поршневые пальцы.
Остальные детали смазываются разбрызгиванием масла противовесами и дополнительными балансирами коленчатого вала. Резервуаром для масла служит картер компрессора. Масло заливают в картер через пробку 27, а его уровень измеряют маслоуказателем (щупом) 26.
Уровень масла должен быть между рисками маслоуказателя. Для очистки масла, поступающего к масляному насосу, в картере предусмотрен масляный фильтр 25.
Рис. 1.1.7 Масляный насос
1- крышка, 2- корпус насоса, 3- фланец, 4- валик, 5,9- пружины,
6- лопасть, 7- корпус редукционного клапана, 8- собственно клапан шарового типа, 10- регулировочный винт, 11-штифт, 12- шпилька Масляный насос приводится в действие от коленчатого вала, в торце которого выштамповано квадратное отверстие для запрессовки втулки и установки в нее хвостовика валика 4. Масляный насос состоит из крышки 1, корпуса 2 и фланца 3, которые соединены между собой четырьмя шпильками 12 и центрируются двумя штифтами 11. Валик 4 имеет диск с двумя пазами, в которые вставлены две лопасти 6 с пружиной 5. Благодаря небольшому эксцентриситету, между корпусом насоса и диском валика образуется серповидная полость.
При вращении коленчатого вала лопасти 6 прижимаются к стенкам корпуса пружиной 5 за счет центробежной силы. Масло всасывается из картера через штуцер «А» и поступает в корте насоса, где подхватывается лопастями. Сжатие масла происходит за счет уменьшения серповидной полости в процессе вращения лопастей. Сжатое масло по каналу «С» нагнетается к подшипникам компрессора. [1]
К штуцеру «В» присоединена трубка от манометра. Для сглаживания колебаний стрелки манометра 16 вследствие пульсирующей подачи масла в трубопроводе между насосом и манометром помещен штуцер с отверстием диаметром 0,5 мм, установлены резервуар 17 объемом 0,25 л и разобщительный кран для отключения манометра. Редукционный клапан (рис. З.8.), ввернутый в крышку 1, служит для регулировки подачи масла к шатунному механизму компрессора в зависимости от частоты вращения коленчатого вала, а также для слива избытка масла в картере.
Редукционный клапан состоит из корпуса 7, в котором размещены собственно клапан 8 шарового типа, пружина 9 и регулировочный винт 10 с контргайкой и предохранительным колпачком. По мере повышения частоты вращения коленчатого вала растет усилие, с которым клапан прижимается к седлу под действием центробежных сил. и. следовательно, для открытия клапана 8 требуется большее давление масла. При частоте вращения коленчатого вала 400 об/мин давление масла должно быть не менее 1,5 кгс/см2.
Компрессор КТ-7 получает левое вращение коленчатого вала (если смотреть со стороны привода) вместо правого на компрессоре КТ-6. Это обстоятельство вызвало изменение конструкции вентилятора для сохранения
прежнего направления потока охлаждающего воздуха, а также масляного насоса.
В клапанных коробках компрессора КТ-6 Эл отсутствуют разгрузочные устройства, поскольку этот компрессор не переводится в режим холостого хода, а останавливается. На этом компрессоре не нужен и резервуар для гашения пульсаций стрелки масляного манометра, так как относительно низкая частота вращения коленчатого вала компрессора и валика масляного насоса не дают заметной пульсации стрелки, а вибрация компрессора при такой частоте вращения вала практически отсутствует.
1.2 Ремонт компрессора Компрессоры КТ 6 устанавливаются на электровозах и тепловозах Кт6 или привод от коленвала дизеля через муфту.
Коленвал КТ 6 по часовой стрелке вращается (если смотреть со стороны привода) КТ6 Электровоза имеет электрический двигатель, вал которого связан свалом компрессора и редуктор всасующий клапан не имеет разграничительных устройств, т.к. подача сжатого воздуха или её прекращение обеспечивается включением или отключением двигателя. В картере устанавливается электродвигатель, предотвращающий замерзание смазки зимой. На дизельном подвижном составе производят замену масла на анализ в лабораторию и при хорошем состоянии доливают масло в картер до нормали.
В случае замены масла картер промывают керосином, протирают, осматривают и очищают сетку фильтра и его корпус, а также узлы шатунов.
Проверяют состояние клапанов. При необходимости клапаны разбирают и очищают от нагара. Особое внимание обращают на состояние клапанах пластин и пружин. Изломанные или трещины пластины и пружины, а также пружины высотой меньше 10 мм заменяют.
Подлежат замене клапанные пластины при нарушении их герметичности. В кранах машиниста и вспомогательного тормоза проверяют действия крана контролера электропневматического тормоза и производят смазку деталей в случае неисправности кран заменяют отремонтированным.
Снятые с подвижного состава краны машиниста разбирают, проверяют состояние деталей, неисправности устраняют.
Блокировочное устройство сжатого воздуха испытывают на проходимость сжатого воздуха и проверяют крепление электрических зажимов, пайку и изоляцию проводов.
Тормозной цилиндр проверяют на плотность. В случае пониженной плотности цилиндр вскрывают, вынимают поршень, очищают и смазывают манжету и внутреннюю поверхность цилиндра. Поврежденную манжету заменяют, не реже чем 8 месяцев при плановом ремонте. [2]
Тормозную рычажную передачу осматривают: шарнирные соединения не должны иметь износа с однополюсным зазором между валиками и отверстием более 3 мм. Тормозной винт, гайку, шестерни, передаточные секторы ручного тормоза очищают и промывают керосином, шарнирные соединения и валики и валики смазывают маслом. Регулируют тяговую передачу с обеспечением установленных нормативом выхода штока тормозного цилиндра. В воздухопроводе проверяют плотность соединения, прочность крепления труб, соединение рукавов, фильтров, маслоотделителей. Устраняют утечки сжатого воздуха и другие неисправности. Производится исследование на прочность.
1.3 Охрана труда при ремонте компрессора тепловоза Работники производственных участков обязаны:
Выполнять только ту работу, которая поручена мастером и при условии, что безопасные приемы ее выполнения хорошо известны. В сомнительном случае обратиться к мастеру. Быть внимательным, не отвлекаться на посторонние дела и разговоры, не отвлекать других работающих.
Работать только исправным инструментом. Инструмент хранить в переносном инструментальном ящике или сумке.
При групповой работе каждый работающий должен принимать положение, безопасное для себя и не угрожающее безопасности другого.
При транспортировке узлов и деталей пользоваться только специальными грузозахватными приспособлениями. Запрещается пользоваться поврежденными или немаркированными грузозахватными приспособлениями и тарой. Во всех случаях перед подъемом груза убедиться в том, что груз надежно закреплен. Для этого поднять груз на 200−300 мм от поверхности, проверить правильность крепления и натяжения строп. При обнаружении неправильной и ненадежной зацепки груза опустить его и произвести строповку вновь. Помнить, что удерживать стропы, соскальзывающие с груза при его подъемке или транспортировке, а также направлять их ударами молотка или лома запрещается.
При перемещении груза в горизонтальном направлении, он должен быть поднят не менее чём на 0,5 м выше встречающихся препятствий. Необходимо следить за тем, чтобы в зоне транспортировки не было людей, сопровождать груз сзади, находясь в безопасной зоне.
С воздушными, сварочными и водопроводными шлангами, с электрическими проводами обращаться аккуратно, не допускать их перегибов, запутывания, пересечения с тросами, другими шлангами. Размещать их так, чтобы была исключена возможность наезда на него транспорта и прохода по нему рабочих.
Соблюдать меры личной гигиены:
— Нельзя курить и принимать пищу на рабочем месте;
— Перед едой тщательно помыть руки водой с мылом;
— Для питья следует применять только остуженную кипяченую воду.
Напильники, шаберы и отвертки должны быть прочно закреплены в деревянных рукоятках, не имеющих сколов и трещин, снабженных металлическими кольцами. При обработке деталей напильником, шабером скопившуюся стружку убирать щеткой.
Не разрешается производить работу на уровне лица. К работе с электроинструментом слесарь должен приступить только после оформления наряда-допуска. Получая на руки электроинструмент, он должен осмотреть его и проверить на холостом ходу. Корпус электроинструмента, работающего от сети напряжением выше 42 В или не имеющего двойной изоляции, должен быть заземлен. При необходимости следует использовать диэлектрические перчатки.
Электроинструмент следует присоединять к электрической цепи при помощи вилки. При работе кабель должен быть защищен от случайного повреждения (например, подвешен).
Запрещается непосредственное соприкосновение кабеля с горячими, влажными и загрязненными нефтепродуктами поверхностями, а также его перекручивание и натягивание.
При работе с электроинструментом на высоте необходимо пользоваться площадками, снабженными перилами, работать, стоя на лестнице, запрещается.
При переноске пневматического инструмента необходимо держать его за рукоятку корпуса, а воздушный шланг — свернутым в кольцо.
Запрещается работа в рукавицах со сверлильными и другими вращающимися инструментами.
Требования к содержанию рабочих мест.
Рабочие места и проходы к ним следует содержать в чистоте, не допуская загромождения их запасными частями, снятыми деталями с вагона и посторонними предметами. Обтирочный материал необходимо складывать в металлические ящики с плотно закрывающимися крышками.
Детали и инструмент размещать так, чтобы работа с ними не вызывала лишних движений. Детали, запчасти и материалы укладывать на стеллажи, расположенные на междупутьях, в отделениях и производственных участках, обеспечивая свободные проходы и исключая возможность их раскатывания и падения. Запрещается сдувать мусор с рабочего места и оборудования или очищать одежду сжатым воздухом.
ВВЕДЕНИЕ
По темпам электрификации, протяженности линий, объему перевозок и грузообороту наша страна оставила далеко позади все страны мира. Интенсивная электрификация железных дорог вызвана ее большими технико-экономическими преимуществами. По сравнению с паровозом или тепловозом электровоз при том же весе и габаритах может иметь значительно большую мощность, так как он не имеет первичного двигателя (паровой машины или дизеля). Поэтому электровоз обеспечивает работу с поездами с значительно большими скоростями и, следовательно, повышает пропускную и провозную способность железных дорог.
Использование управления несколькими электровозами с одного поста (система многих единиц) позволяет увеличить эти показатели в еще большей степени. Более высокие скорости движения обеспечивают ускорение доставки грузов и пассажиров к месту назначения и приносят дополнительный экономический эффект для народного хозяйства.
Электрическая тяга имеет более высокий к.п.д. по сравнению с тепловозной и особенно с паровой тягой. Средний эксплуатационный к.п.д. паровой тяги составляет 3—4%, тепловозной — около 21% (при 30-процентном использовании мощности дизеля), а электрической тяги — около 24%.
При питании электровоза от старых тепловых электростанций к. п. д. электрической тяги составляет 16—19% (при к.п.д. самого электровоза порядка 85%). Такой низкий к.п.д. системы при высоком к.п.д. электровоза получается вследствие больших потерь энергии в топках, котлах и турбинах электрических станций, к.п.д. которых составляет 25—26%.
Современные электрические станции с мощными и экономичными агрегатами работают с к.п.д. до 40%, и к.п.д. электрической тяги при получении энергии от них составляет 25—30%.
Наиболее экономична работа электровозов и электропоездов при питании линии от гидростанции. При этом к.п.д. электрической тяги составляет 60—62%.
Нужно отметить, что паровозы и тепловозы работают на дорогом и высококалорийном топливе. Тепловые электрические станции могут работать на более низких сортах топлива — буром угле, торфе, сланцах, а также использовать природный газ. Эффективность электрической тяги возрастает также при питании участков от атомных электрических станций. Электровозы более надежны в эксплуатации, требуют меньших затрат на осмотры и ремонты оборудования и позволяют поднять производительность труда на 16—17% по сравнению с тепловозной тягой.
Только электрическая тяга обладает свойствами перерабатывать запасенную в поезде механическую энергию в электрическую и отдавать ее при рекуперативном торможении в контактную сеть для использования ее другими электровозами или моторными вагонами, работающими в этот период в режиме тяги. При отсутствии потребителей энергию можно передать в энергосистему. За счет рекуперации энергии удается получить большой экономический эффект. Так, в 1976 г. за счет рекуперации было возвращено в сеть около 1,7 млрд. кВт/ч электроэнергии.
Рекуперативное торможение позволяет повысить уровень безопасности движения поездов, уменьшить износ тормозных колодок и бандажей колес.
Все это дает возможность снизить себестоимость перевозок и сделать процесс перевозки грузов более эффективным. За счет технической реконструкции тяги на железнодорожном транспорте сэкономлено примерно 1,7 млрд. топлива, а. эксплуатационные расходы уменьшились на 28 млрд. д.е.
Если предположить, что до сих пор на наших магистралях работали бы паровозы, то, например, в 1974 г. потребовалось бы в их топках израсходовать треть добываемого в стране каменного угля.
Электрификация железных дорог способствует прогрессу народного хозяйства прилегающих районов, так как от тяговых подстанций получают питание промышленные предприятия, колхозы, совхозы и закрываются малоэффективные неэкономичные местные дизельные электростанции.
РАЗДЕЛ 2 КОНТРОЛЛЕР МАШИНИСТА
2.1 Назначение. Устройство. Принцип действия Контроллер машиниста (рис. 2.1.1) служит для дистанционного управления работой тяговых двигателей.
Контроллер машиниста КМЭ-8Г имеет два кулачковых вала: главный и тормозной. Валы приводятся в движение двумя рукоятками: главной и тормозной, которые связаны с соответствующими зубчатыми передачами.
Реверсирование тяговых двигателей и выбор схемы их соединения на тормозном режиме осуществляются двумя кулачковыми барабанами, которые посажены на подшипниках на главном и тормозных валах; оба барабана управляются одной реверсивно-селективной рукояткой. Изоляционные кулачковые шайбы главного и тормозного валов и кулачки барабанов переключают контакторные элементы, смонтированные на двух рейках.
Главный вал имеет 24 кулачковые шайбы и осуществляет 37 позиций (не считая нулевой), из которых 16, 27 и 37-я являются рабочими, а остальные пусковыми. Тормозной вал набран из 22 кулачковых шайб и имеет четыре позиции ослабления поля и 16 позиций торможения. [6]
Фиксация главного и тормозного валов по позициям обеспечивается защелками рукояток, западающими в пазы секторов на крышке контроллера.
Реверсивно-селективная рукоятка имеет девять позиций: нулевую, четыре позиции М (моторный режим), П, СП и С (рекуперативный режим) — в положении рукоятки Вперед и такие же четыре позиции в положении Назад.
Каждый контакторный элемент имеет подвижной и неподвижный контакты, установленные на изоляторе, который крепится к рейке.
Контакты замыкаются под действием пружины, размыкаются при нажатии кулачковой шайбы.
Последовательность замыкания контактов определяется профилем кулачковых шайб:
Рис. 2.1.1. Контроллер машиниста
1 — тормозная рукоятка; 2 — главная рукоятка; 3 — крышка;
4 — контактор кулачковый; 5 — кожух; 6 — рейка;
7 — рама; 8 — вал кулачковый Для предотвращения ошибочных действий при работе все три рукоятки механически сблокированы между собой так, что: при установке реверсивной рукоятки на позицию М главная рукоятка может быть установлена на любую позицию; при установке главной рукоятки на 16, 27 и 37-ю позиции тормозная рукоятка может быть установлена в положение ослабления поля ОП-1, ОП-2, ОП-3, ОП-4, при этом перемещение главной рукоятки невозможно до возвращения тормозной рукоятки на позицию 0; при установке реверсивной рукоятки на позиции П, СП и С тормозная рукоятка может быть установлена на позицию 02, что дает возможность установить главную рукоятку на позицию 1, а затем поворачивать тормозную рукоятку до позиции 15; обратный поворот тормозной рукоятки возможен до позиции 1 включительно, а после установки главной рукоятки на позицию 0 тормозную рукоятку можно повернуть на позицию 0; при рабочем положении главной и. тормозной рукояток поворот реверсивно-селективной рукоятки невозможен. [6]
При каждом периодическом ремонте проверяется последовательность замыкания контактов контакторных элементов, взаимодействие механических блокировок, разрыв, провал и давление контактов.
Технические данные Номинальное напряжение… 50 в Номинальный ток контактов… 30 а Вес… 175 кг Технические требования Раствор контактов…4—7 мм Провал … 2,5—4 мм Нажатие … 0,25—0,3 кГ Напряжение переменного тока (частота 50 га,)
для испытания изоляции в течение 1 мин … 1 500 в Максимальный разрываемый ток
при напряжении 50 в и индуктивности
в цепи L=50 мгн … 10 а
2.2 Ремонт контроллера машиниста Износы и повреждения. Контроллеры машиниста как аппараты управления находятся в непрерывной работе, что приводит к активному износу их отдельных элементов, что в свою очередь может привести к появлению других неисправностей.
Так, в результате ослабления посадки на валу кулачковых шайб и малой шестерни, ослабления крепления рукояток, зубчатых секторов, повышенного износа защелки главной рукоятки и деталей контакторных элементов, излома или нарушения профиля кулачковых шайб моменты включения и выключения контакторных элементов могут отклоняться от диаграммы замыкания контактов. Повышенный износ поверхностей упорных рычагов и шайб, ослабление их посадки, излом и повышенная выработка отверстий соединительных тяг, ослабление и выработка осей и подшипников узла блокировочного механизма могут привести к нарушению взаимодействия механических блокировок. В результате разрушения подшипников валов, излома зубьев шестерен и секторов, попадания в места зацепления посторонних предметов может произойти заклинивание рукояток контроллера.
У контроллеров наблюдаются также утечки воздуха в клапане безопасности, заедание роликов контакторных элементов, обрыв шунтов, повышенный износ контактов контакторных элементов, излом пружины и др.
Если обнаруженную неисправность устранить непосредственно невозможно, то аппарат снимают и передают для ремонта в аппаратное отделение.
Ремонт контроллеров и переключателей режимов электровозов. Контроллер или переключатель обдувают в обдувочной камере сжатым воздухом и осматривают. Снимают рукоятки, секторы, верхнюю крышку, контакторные элементы, блокировочный механизм, кулачковые валы. Все детали промывают в бензине и осматривают. Если у кулачкового вала будет обнаружено ослабление посадки на нем подшипников, шестерни, кулачковых шайб или шайбы будут иметь повышенный износ, трещины, отколы или профиль, не соответствующий диаграмме замыкания контактов, то кулачковый вал разбирают.
Вал с биением более 0,5 мм протачивают на токарном станке. Шейки валов под подшипники с повышенным износом и дефектный квадрат реверсивного вала под установку рукоятки наплавляют и обрабатывают.
Подшипники с радиальным зазором более 2 мм, с трещинами или изломами в сепараторе или обойме и с шелушением на роликах или кольцах заменяют. Кулачковые шайбы контроллера КМЭ-8 с износом по окружности более 4 мм и более 6 мм у контроллера электровозов переменного тока, а также шайбы, с нарушенной конфигурацией выступов и впадин, со сколами или трещинами заменяют. Шестерни с ослабшей посадкой на валу заменяют новой, устанавливаемой с натягом 0,02—0,05 мм. Проверяют зубомером профиль и износ зубьев шестерни и зубчатых секторов. При необходимости их наплавляют и обрабатывают. Сегменты барабанных валов толщиной менее 2,5 мм и изодиновые шайбы кулачкового вала со сколами и трещинами заменяют. При необходимости восстанавливают наплавкой изношенные квадраты валов под посадку рукояток и заменяют указательные лимбы.
Рукоятки контроллеров разбирают f и осматривают. Трещины в рукоятке разделывают и заваривают с последующей слесарной обработкой. Разработанные отверстия заваривают и рассверливают до чертежных размеров.
Специальные винты с выработкой более 0,2 мм, пружины с остаточной деформацией и с отогнутыми конечными витками и изношенную накладку защелки заменяют. Упорный зуб и выступ рычага с повышенным износом наваривают и обрабатывают под чертежный размер, а изношенный более чем на 1 мм стержень кнопки наплавляют или заменяют. Отремонтированные корпус, рычаг и кнопку рукоятки хромируют.
Детали блокировочного механизма промывают в бензине и тщательно осматривают. С учетом данных предварительного (до разборки) осмотра контроллера к изношенным упорным рычагам и впадинам шестерен приваривают накладные пластины или их восстанавливают наплавкой, контролируя профили рычагов и шайб шаблонами. [7]
Разработанные отверстия рассверливают под запрессовку бронзовых втулок с соответствующим внутренним диаметром. Пружины, имеющие трещины или не отвечающие характеристикам, заменяют.
Ролик механической блокировки контроллера КМЭ-55 с трещинами или выработкой заменяют. Сработанные выступы на валу механической блокировки наплавляют и обрабатывают.
Контакторные элементы контроллеров и групповых переключателей цепей управления однотипны, а технология их ремонта аналогична описанной ранее технологии ремонта контакторных элементов ПКГ и ЭКГ.
Толщина контактов должна быть у контроллеров: КМЭ-8, КМЭ-10—1,8 мм, КМЭ-55, ТР-60, ТР-103 —0,8— 1,2 мм. Износ контактов контроллера КМЭ-80 более 0,1 мм не допускается. Смещение подвижных контактов относительно неподвижных для всех типов контакторных элементов контроллеров не должно превышать 1,8 мм.
2.3 Охрана труда при ремонте контролера машиниста Все работы по подготовке электровоза к эксплуатации должны производиться специально подготовленным персоналом локомотивных депо с соблюдением Правил техники безопасности.
К управлению электровозом должны допускаться локомотивные бригады, знающие устройство и правила эксплуатации электровоза. Все работы по обслуживанию электровоза должны выполняться при обязательном выполнении требований, изложенных в настоящем разделе.
При работе электровоза под контактным проводом или при подаче на него напряжения извне электрооборудование и машины находятся под напряжением. Прикосновение к токоведущим частям! независимо от значения напряжения может оказаться смертельным!
Защитные меры и средства. Для исключения доступа обслуживающего персонала к токоведущим частям электрооборудования и измерительных приборов пульта машиниста при поднятом токоприёмнике на электровозе осуществлено блокирование входа в ВВК, подъёма токоприёмника, включения БВ и других ответственных аппаратов управления. Также предусмотрено заземление на кузов электровоза корпусов вспомогательных машин.
Средства защиты, которыми укомплектован электровоз, сигнальные принадлежности и инструмент необходимо применять в соответствии с их назначением и хранить в специально выделенных местах. Средства защиты должны иметь клейма с указанием даты очередного испытания и значения, на которое рассчитано данное средство.
Пользование защитными средствами, не имеющими указанных клейм или с просроченным сроком испытания, запрещается! В проходном коридоре каждой секции рядом с входной дверью предусмотрены места для хранения .
Пожарная безопасность на электровозе. Для тушения пожара электровоз снабжён противопожарными средствами. На каждой секции имеются четыре углекислотных огнетушителя ОУ-5 (или порошковых ОП-5 и ОП-10) и вёдра с песком. При возникновении пожара на электровозе локомотивная бригада должна подать сигнал пожарной тревоги, по возможности остановить поезд в удобном для тушения пожара месте, установить штурвал и рукоятки контроллера в нулевые положения, выключить все кнопки, остановить все вспомогательные машины и опустить токоприёмники.
Тушить пожар на электровозе углекислотными, порошковыми огнетушителями или водой можно только после снятия напряжения и заземления контактной сети. Если напряжение снять невозможно, локомотивная бригада, соблюдая особую осторожность, должна приступить к тушению огня углекислотными огнетушителями или сухим песком. Горящие провода и электрические аппараты тушат только углекислотными, порошковыми огнетушителями или сухим песком.
Во избежание возникновения пожара на электровозе все подбивочные, обтирочные и смазочные материалы должны храниться в закрытом металлическом ящике. Для устранения неисправностей в цепях управления запрещается использовать временные перемычки из проводов, сечение которых меньше сечения штатных проводов цепей! В крайнем случае разрешается использовать такие провода, соединённые параллельно в два-три раза.
ЗАКЛЮЧЕНИЕ
Компрессор КТ-6 широко применяются на тепловозах и электровозах. Компрессоры КТ-6 приводятся в действие от электродвигателя, как например, на тепловозах 2ТЭ116.
Контроллеры машиниста служат для дистанционного (косвенного) управления работой тяговых двигателей в тяговом и тормозном режимах; с их помощью подключают к источнику низкого напряжения и отключают в определенной последовательности провода цепи управления, т. е. включают и выключают в определенной последовательности высоковольтные аппараты при пуске, регулировании скорости движения, остановке, изменении направления движения и электрическом торможении электровоза или электропоезда. Контроллер машиниста имеет ряд рукояток, каждая из которых предназначена для определенных операций управления и имеет несколько фиксированных позиций, соответствующих определенным включениям аппаратов силовой цепи.
При конструировании контроллеров должны быть соблюдены требования, обеспечивающие простоту и легкость пользования ими и наиболее простую кинематику блокировочных механизмов; наименьшие массу и габаритные размеры аппарата; надежность работы его переключающих устройств, удобство осмотра и ремонта всех его деталей. Распределение функций управления и расположение отдельных рукояток контроллера выполняют так, чтобы обеспечить простоту и удобство пользования ими и не допускать отвлечения машиниста от наблюдения за сигналами, путем и контактной сетью. Механические блокировки в контроллере создают взаимозависимость между рукоятками, что предотвращает ошибочные действия машиниста.