Организационно-экономическая характеристика ОАО «ГЛЗ «Центролит»
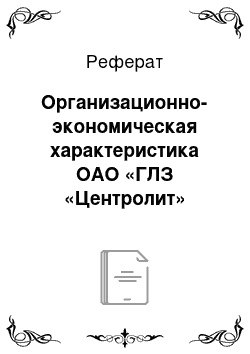
Расчетная производственная мощность завода в настоящее время 32 тыс. тн. литья в год. Завод оснащен широкой гаммой плавильного, формовочного и стержневого оборудования, позволяющего производить отливки весом от 15 т до нескольких грамм любой сложности. Соответственно используется спектр современных технологий, формовочных и стержневых смесей и способов литья. Для производства крупного литья… Читать ещё >
Организационно-экономическая характеристика ОАО «ГЛЗ «Центролит» (реферат, курсовая, диплом, контрольная)
Открытое Акционерное Общество «ГОМЕЛЬСКИЙ ЛИТЕЙНЫЙ ЗАВОД «ЦЕНТРОЛИТ» — крупнейшее предприятие Беларуси, специализирующееся на производстве литых изделий из серого и высокопрочного чугуна (ГОСТ 1412−85 и ГОСТ 7293–85).
Завод сертифицирован в системе менеджмента качества международного стандарта СТБ ISO 2001: 2009; получены экологический сертификат соответствия требованиям СТБ ИСО 14 001−2005, позволяющий не нарушать экологическое равновесие окружающей среды, сертификат на систему управления охраной труда СТБ 18 001−2009. На протяжении более 40 лет завод является известным поставщиком литых изделий не только в Беларуси, но и за рубежа. Его возможности позволяют обеспечить потребность в чугунном литье практически любое предприятие машиностроения, автомобилестроения, станкостроения, а также транспорта, связи.
Завод освоил производство художественного литья, которое используется для городского дизайна. В 2002 году Комитетом по архитектуре и градостроительству Москвы предприятие рекомендовано в качестве изготовителя элементов благоустройства столицы Российской Федерации и внесено в электронный каталог малых архитектурных форм.
Расчетная производственная мощность завода в настоящее время 32 тыс. тн. литья в год. Завод оснащен широкой гаммой плавильного, формовочного и стержневого оборудования, позволяющего производить отливки весом от 15 т до нескольких грамм любой сложности. Соответственно используется спектр современных технологий, формовочных и стержневых смесей и способов литья. Для производства крупного литья развесом от 15 т до 0,5 т применяются песчано-глинистые формовочные смеси, жидкоподвижные самотвердеющие (ЖСС) и пластичные смеси (ПСС). Для изготовления форм установлена автоматическая линия АЛИФ с размером опок 1,9×3,0 м, поточно-механизированная линия включающая установку непрерывного приготовления ЖСС мод. 19 415 для изготовления форм и смесеприготовительная установка непрерывного приготовления смесей ПСС мод. 19 657 для изготовления стержней. Для поверхностной подсушки используются переносные горелки. Для выбивки форм установлена инерционная выбивная решетка.
Среднее литье (0,12−1,5тн) изготавливается на поточно-механизированной линии с использованием формовочных машин 234 и 235 с установками поверхностной подсушки форм газовыми горелками.
Имеется также участок литья в постоянные формы — кокиль.
Крупное и среднее литье производится в цехе № 1.
Мелкое литье (цех № 3) производится на автоматических линиях: без опочной формовки «HUNTER», воздушно-прессовой «ФДК», линии АЛИФ с суммарной мощностью всех электродвигателей 160 кВт, участке оболочкового литья. Формовочная линия «ФДК» предназначена для изготовления отливок в опоках 800×750 мм из единой смеси, приготавливаемой на встроенной смесеприготовительной установке. Формовочная линия «ФДК» имеет производительность 100 форм/час и суммарную мощность всех электродвигателей 500 кВт. Стержни изготавливаются на стержневых автоматах, использующих смеси горячего и холодного твердения.
Оба цеха расположены в литейном корпусе. В этом корпусе находятся также плавильные печи (цех № 5); вагранка коксовая, производительностью 2,5−3,0 т/ч; ч; электрические индукционные тигельные печи промышленной частоты ИЧТ-10 с потребляемой мощностью 2495 кВт, емкостью 10 т — 3шт.; такие же ИЧТМ-6, емкостью 6 т — 3шт.
В цехе имеется линия непрерывного литья А-126 производительностью 3−10 тн/сутки в зависимости от профиля заготовки. Для поддержания температуры металла в металлоприемниках установлена газовая горелка с расходом — 25 м3/ч. Установка работает в непрерывном режиме.
Для изготовления формовочных смесей в литейном корпусе имеется смесеприготовительный участок с соответствующим оборудованием: смешивающие бегуны мод. 114, производительностью 10 т/ч; установка приготовления облицовочной смеси; комплект оборудования подготовки оборотной смеси для повторного использования, в том числе: полигональное сито, магнитные сепараторы, система конвейеров и бункеров.
Литейный корпус оснащен внутрицеховым транспортом, а также связан транспортным оборудованием с корпусом, в котором расположены склады формовочных и шихтовых материалов и сухого песка, а также корпусом очистки и обрубки литья. В последнем находятся: гидрокамера ЛН-407 (установочная мощность 170 кВт), две гидрокамеры ЛН-408 (установочная мощность 90 кВт), насосная станция высокого давления 13 Гр-1 (установочная мощность 180 кВт), дробеметная камера 374С (установочная мощность 80 кВт), дробеметная камера 372 (установочная мощность 34,2кВт), дробеметная камера 42 612, дробеметная камера ДК-10, печи термические — 3 шт., камера охладительная, наждачные станки подвесные 3374К, печь термическая с выкатным подом ГЧ113. В обрубочно-очистном корпусе отливки, поступающие из литейного корпуса, отделяются от литников, очищаются от остатков формовочных и стержневых смесей, а также в случае необходимости проводится термообработка (отжиг). Последняя проводится в газовых камерных печах с площадью пода 18,9 м². Продолжительность цикла отжига 6−18 ч, расход природного газа 4137,6 м3/цикл. В этом же корпусе организован склад готовой продукции.
Отделение подготовки и складирования шихтовых и формовочных материалов расположено в отдельном корпусе. Корпус оснащен транспортным, грузоподъемным и весодозирующим оборудованием.
Сушка песка производится в пневмопотоке. Установка для сушки песка производительностью 15 т/ч (фактически 17,5 т/ч) оснащена газовой горелкой с расходом 150−300 м3/ч.
Для сушки глины и бентонита периодически применяется барабанное сушило.
В корпусе блока вспомогательных цехов расположен цех цветного литья, где производят отливки методами литья под давлением, в кокиль, а также непрерывного литья намораживанием. Для литья под давлением используются машины мод. А711А07М и А711А08М.
Плавка цветных сплавов ведется в электрических печах сопротивления САТ-0,15 — 7 шт., газовых тигельных (пламенных) печах «Калеман» — 2шт. Для плавки стали используются также тигельные высокочастотные печи ИСТ-1 — 2 шт.
В этом же цехе установлены термопластоавтоматы мод. ДВ 3127 и ДЕ 3127, на которых производится изготовление деталей (изделий) из полиэтилена, полистирола и др., объемом до 60 см³.
В корпусе расположено также производство моделей из дерева и металла, а также мебели, оснащенное деревообрабатывающими станками, сушилами, окрасочными камерами.
Помимо основных производственных корпусов на предприятии имеются вспомогательные участки: скрапоразделочный цех, имеющий копер для разделки чугунного лома и возврата (литья) собственного производства; цех жидкого стекла; склады.
Для обеспечения тепловой энергией и горячего водоснабжения завод «Центролит» имеет энергоцех, в состав которого входят котельная и компрессорные станции высокого и низкого давления.
Для получения кислорода из воздуха на заводе имеется кислородная станция.
Производственный процесс получения литых заготовок состоит из следующих основных операций (переделов). Исходные материалы, для чугунного литья это доменные чугуны, покупной чугунный и стальной лом, возврат собственного производства и ферросплавы, поступают, разделываются, сортируются и хранятся на складе шихтовых материалов. Сюда же поступают кокс и флюсы (известняк). В настоящее время часть шихтовых материалов хранится в литейном корпусе.
По технологическим картам набирается необходимый состав шихты и загружается в электропечи ИЧТ-10, где расплавляется и доводится до нужного химического состава и температуры. Затем металл передается на заливку в литейные формы, а в случае необходимости переливается в печи ИЧТМ-6 для хранения и раздачи на литейные линии и установки непрерывного литья, кокильный участок и др.
Для изготовления литейных форм и стержней используются песок, глины, специальные добавки, отработанные формовочные смеси. Последние составляют до 90 % песчано-глинистых формовочных смесей. За исключением смесей ЖСС, ПСС, остальные получают в смесеприготовительном отделении, откуда транспортируются к формовочным машинам.
Стержневые смеси готовят из свежего песка с различными связующими в зависимости от типа смеси. Смесители установлены непосредственно в стержневом отделении, часть смесей готовится в стержневых машинах.
Формы для крупных и средних отливок подсушиваются переносными горелками или в сушилах, в частности после формовочных машин 234, 235. На участке крупного литья также установлены зонты.
Полуформы и стержни подаются к месту сборки, после чего собранные формы поступают на заливку.
Заливка форм производится ковшами. После кристаллизации и охлаждения отливок формы выбивают, отливки отделяют от смеси.
Далее отливки поступают на установки выбивки (удаления) стержней, отделения литниковой системы и финишную обработку в обрубочно-очистной корпус.
Производство непрерывно литых заготовок различного профиля диаметром 40−220 мм осуществляется на специальных установках, состоящих из раздаточной емкости (тигля) и тянущей клети. Металл кристаллизуется в охлаждаемом графитовом кристаллизаторе, отливка-пруток непрерывно вытягивается из кристаллизатора, охлаждается, а затем разрезается на мерные прутки длиной 3−5 м.
При литье в кокиль на машинах литья под давлением не используются формовочные смеси, отливки имеют более высокую точность и качество поверхности. Большая часть их не требует механической обработки перед использованием. Высокую точность и качество поверхности отливок обеспечивает способ оболочкового (коркового) литья, а также литья в постоянные формы (кокиль).
Сменность работы завода — непрерывный цикл (литейное производство).
Среднесписочная численность работающих на предприятии составила 1768 человек.
Загрузка оборудования — в течение года неравномерная.
На исследуемой организации функционирует линейно-функциональная структура управления. Под подчинением генерального директора находятся руководители структурных подразделений, которые руководят процессом производства и реализации. Перед всеми отделами устанавливаются планы выполняемых показателей, которые должны выполняться для обеспечения бесперебойного процесса производства. Выполнение планов проверяется еженедельно на планерках, исходя из устных отчетов руководителей структурных подразделений.
ОАО «Гомельский литейный завод «Центролит» является организацией государственной формы собственности, ориентированной на выпуск металлопроката, чугунных отливок и товаров народного потребления.
Предприятие находится в подчинении Министерства промышленности Республики Беларусь и является специализированным предприятием по производству чугунного литья. Предприятие производит продукцию для станко-, машино-, автомобилестроения, градостроительства и дорожную арматуру.
Первые производственные мощности были введены в эксплуатацию в мае 1966 года на базе блока вспомогательных цехов: ремонтно-механический, деревомодельный цех и участок цветного литья. Первые производственные мощности по производству чугунного литья были введены в октябре 1968 года — цех крупного литья.
Объем производства чугунного литья в 2011 г. составил 24 550 тонн, в 2012 г. — 26 707 тонн, в 2013 г.- 30 200 тонн и до 2014 года прогнозируется увеличение выпуска до 35 700 тонн.
Номенклатура на предприятии продукции, выпускаемой и планируемой к поставке имеет следующие направления:
- 1) корпусное литье: для станкостроения; для машиностроения; для автомобилестроения, дорожной техники; для метростроя; для нефтегазовой промышленности; для сельского хозяйства; непрерывнолитые заготовки из серого и высокопрочного чугуна Ш 30−230 мм, профили сечений длиной до 2500 мм.
- 2) литье для градостроительства.
- 3) дорожная арматура.
- 4) изделия по разовым заказам сторонним организациям и др.
Профилирующей продукцией организации являются чугунные отливки из серого чугуна марки СЧ 20−25 и высокопрочного чугуна марки ВЧ 40−50 по весовым группам от 1 кг до 15 000 кг. Их производство осуществляется в литейных цехах: мелкочугунного литья; крупночугунного литья; плавки; шихтовых и формовочных материалов; обрубки и очистки отливок и др.
Предприятие также осуществляет услуги по грунтовке, мехобработке, термообработке чугунных отливок; изготавливает металлическую и деревянную оснастку.
Организационная структура управления общества представлена в Приложении 1.
Руководство текущей деятельностью осуществляет дирекция и генеральный директор. Они подотчетны в своей деятельности наблюдательному совету и собранию акционеров. В состав дирекции входят: генеральный директор, его заместители, главный бухгалтер, технический отдел. Еженедельно, дирекцией предприятия проводятся планерки — встречи с руководителями и специалистами структурных подразделений, на которых обсуждаются вопросы различного характера: доводятся планы, ставятся задачи и подводятся итоги.
На исследуемой организации функционирует линейно-функциональная структура управления. Под подчинением директора находятся руководители структурных подразделений, которые руководят процессом производства и реализации. Перед всеми отделами устанавливаются планы выполняемых показателей, которые должны выполняться для обеспечения бесперебойного процесса производства. Выполнение планов проверяется еженедельно на планерках, исходя из устных отчетов руководителей структурных подразделений.
Результаты хозяйственной деятельности ОАО ГЛЗ «Центролит» за 2011;2013 гг. рассмотрим при помощи сводной таблицы 1.1.
Таблица 1.1 — Динамика производства и реализации продукции ОАО ГЛЗ «Центролит» за 2010 — 2012 гг.
Показатели. | Годы. | Темп роста, % или отклонение (+,-). | ||||
2012 к 2011. | 2013 к 2012. | 2013 к 2011. | ||||
1. Объем производства продукции, млн р.: | 195,6. | 108,6. | 215,6. | |||
2. Выручка от реализации продукции, работ, услуг, млн р. | 167,3. | 113,6. | 190,1. |
Примечание — Источник: собственная разработка на основании данных, взятых из документации предприятия Из данных таблицы 1.1 видно, что выпуск продукции ОАО «Центролит» увеличивается: в 2011 году данный показатель составил 157 855 млн р., в 2011 — 313 413 млн р., в 2012 — 340 377.
В целом, ОАО ГЛЗ «Центролит» является экспортно-ориентированным предприятием, поскольку в 2013 г. на рынках России и дальнего зарубежья было востребовано 60% продукции. Однако в 2013 году уменьшилась доля отгрузки в страны дальнего зарубежья и на российский рынок на 2%, вместе с тем, увеличилась доля внутреннего рынка в отгрузке на 4%. Уменьшение роста отгрузки в страны дальнего зарубежье явилось следствием уменьшения количества предприятий, закупающих нашу продукцию. Так, отсутствие сбыта в Англию объясняется проблемами, связанными с закупочной политикой заказчика (закрытие представительства в России); уменьшение поставок в Прибалтику в целом объясняется неудовлетворением литовских заказчиков по объемам поставок и ценовым факторам.
Выручка от реализации продукции за вычетом налогов и других обязательных платежей в 2011 г. составила 178 344 млн. р., в 2012 году выручка увеличилась на 13,6% и составила 298 329 млн р. В 2013 году данный показатель составил 338 950 млн р.
Рассмотрим показатели изменения объемы производимой продукции.
Таблица 1.2 — Показатели, характеризующие изменение объема продукции по ОАО ГЛЗ «Центролит» за 2012 — 2013 гг.
Показатели. | Годы. | Отклонение. | |
1. Объем продукции (работ, услуг) в фактических ценах (V), млн р. | |||
2. Среднесписочная численность персонала основного вида деятельности (Ч), чел. | — 21. | ||
3. Среднегодовая выработка (ГВ), млн р. | 221,9. | 244,7. | 22,8. |
4. Среднегодовая стоимость основных средств основного вида деятельности (ОС), млн р. | |||
5. Фондоотдача (Ф), р. | 3,33. | 2,88. | — 0,45. |
6. Материальные запасы (МЗ), млн р. | |||
7. Материалоотдача (МО), р. | 15,4. | 13,3. | — 2,1. |
Примечание — Источник: собственная разработка на основании данных, взятых из документации предприятия Из таблицы видно, что предприятие функционирует эффективно — среднегодовая выработка в 2012 году составила 221,9 млн р., в 2013 году данный показатель увеличился на 22,8 млн р. и составил 244,7 млн р.
Однако стоит отметить, что по сравнению с 2012 годом, в 2013 году все меньше получается отдачи от использования основных средств и материальных ресурсов.
Проанализируем состояние кадров на ОАО ГЛЗ «Центролит» за 2012;2013 гг. посредством таблицы 1.3.
Таблица 1.3 — Показатели движения кадров по ОАО ГЛЗ «Центролит» за 2012 — 2013 гг.
Показатели. | Годы. | Темп роста, % или отклонение (+,-). | |
2012 к 2011. | |||
1. Принято на работу, чел. | — 96. | ||
2. Уволено работников, всего, чел. | |||
В том числе: по сокращению. | ; | ||
за прогул и другие нарушения трудовой дисциплины, чел. | — 19. | ||
по собственному желанию, чел. | |||
3. Списочная численность работников в среднем за год, чел. | — 138. | ||
4. Показатели оборота: по приему, %. | |||
по увольнению, %. | 26,7. | 32,8. | 6,1. |
текучести кадров, %. | 26,7. | 32,8. | 6,1. |
постоянства кадров, %. | 73,3. | 67,2. | — 6,1. |
Примечание — Источник: собственная разработка на основании данных, взятых из документации предприятия Из таблицы видно, что на предприятии имеется динамика к ухудшению состояния кадров — в 2013 году по сравнению с прошлым годом ухудшились показатели движения кадров. Коэффициенты на увольнению повысились, а постоянства кадров — наоборот — уменьшились.
Структура управления ОАО ГЛЗ «Центролит» относится к категории «вертикальных» иерархических линейно-функциональных структур и является достаточно эффективной в условиях действующего производства, так как:
- — прежде всего, отражает цели и задачи организации, а следовательно, она подчинена производству и его потребностям;
- — предусматривает оптимальное разделение труда между органами управления и отдельными работниками, обеспечивающее творческий характер работы и нормальную нагрузку, а также надлежащую специализацию;
формирование структуры управления связано с определением полномочий и ответственности каждого работника и органа управления, с установлением системы вертикальных и горизонтальных связей между ними;
между функциями и обязанностями, с одной стороны, и полномочиями и ответственностью с другой, поддерживается соответствие, нарушение которого приводит к дисфункции системы управления в целом.
Понятие «внешняя среда» включает экономические условия, потребителей, профсоюзы, законодательство, конкурирующие организации, общественные взгляды, технику и технологию, другие составляющие. Эти взаимосвязанные факторы оказывают влияние на всё, что происходит внутри организации. Различают внешнюю среду прямого и косвенного воздействия.
Среда прямого воздействия включает факторы, которые влияют на деятельность организации. К ним относят поставщиков, акционеров, трудовые ресурсы, законы и учреждения государственного регулирования, профсоюзы, потребителей и конкурентов.
Главными разновидностями входов являются материалы, оборудование, энергия, капитал и рабочая сила. Поставщики обеспечивают ввод этих ресурсов. Получение ресурсов из других стран может быть выгоднее с точки зрения цен, качества или количества, но одновременно опасным усилением таких факторов подвижности среды, как колебания обменных курсов или политическая нестабильность.
На производственных предприятиях особую роль играет эффективное использование основных и оборотных средств. Различия между данными понятиями в том, что основные средства не полностью расходуются за один производственный цикл, а оборотные средства — полностью.
Рассмотрим показатели эффективности использования основных средств (таблица 1.4).
Таблица 1.4 — Показатели эффективности использования основных средств на ОАО ГЛЗ «Центролит» за 2011 — 2013 гг.
Показатели. | Годы. | Темп роста, %. | ||||
2012 к 2011. | 2013 к 2012. | 2013 к 2011. | ||||
1. Объем продукции (работ, услуг) в фактических ценах, млн р. | 195,6. | 108,6. | 215,6. | |||
2. Прибыль от реализации, млн р. | 117,8. | 26,3. | 30,9. | |||
3. Среднегодовая стоимость основных средств, млн р. | 160,0. | 125,5. | 200,8. | |||
4. Среднесписочная численность работников, чел. | 104,2. | 98,5. | 102,6. | |||
5. Фондоотдача основных средств, р. | 2,7. | 3,3. | 2,9. | 122,2. | 87,9. | 107,4. |
6. Фондовооруженность, млн р. | 43,4. | 66,7. | 84,9. | 153,7. | 127,3. | 195,6. |
7. Фондорентабельность, %. | 59,5. | 43,8. | 9,2. | — 15,7. | 21,0. | 15,5. |
Примечание — Источник: собственная разработка на основании данных, взятых из документации предприятия Из таблицы видно, что на предприятии наблюдается улучшение показателей эффективности использования основных средства — все показатели за исследуемый период улучшились. Фондоотдача составила — в 2011 году — 2,7 р., в 2012 г. — 3,3 р., в 2013 г. — незначительное снижение 2,9 р. закупочный логистика автоматизированный склад Фондовооруженность в 2011 году составила 43,4 млн р., в 2012 году — 66,7 млн р., в 2013 году — 84,9 млн р. А вот фондорентабельность имеет тенденцию к снижению — в 2011 году — 59,5%, в 2012 году — 43,8%, в 2013 году — 9,2%.
Далее рассмотрим эффективность использования оборотных средств.
Таблица 1.5 — Показатели эффективности использования оборотных средств на ОАО ГЛЗ «Центролит» за 2011 — 2013 гг.
Показатели. | Годы. | Темп роста, %. | |||
2012 к 2011. | 2013 к 2012. | ||||
1. Выручка от реализации товаров, продукции, работ, услуг, млн р. | 167,3. | 113,6. | |||
2. Среднегодовая стоимость оборотных средств, млн р. | 170,1. | 132,9. | |||
3. Прибыль от реализации, млн р. | 117,8. | 26,3. | |||
| 4,7. | 4,7. | 4,0. | 100,0. | 85,1. |
— продолжительность одного оборота, дней. | 116,7. | ||||
5. Рентабельность оборотных средств, %. | 94,0. | 65,1. | 12,9. | — 28,9. | — 52,2. |
Примечание — Источник: собственная разработка на основании данных, взятых из документации предприятия Из таблицы видно, что предприятие в 2012 году менее эффективно использует оборотные активы — число оборотов за исследуемый период уменьшилось с 4,7 до 4, а продолжительность одного оборота увеличилась с 78 дней до 91, что является «тревожным звонком» для предприятия.
Рассмотрим затраты на один рубль продукции и его изменение за исследуемый период.
Таблица 1.6 — Состав и структура затрат на производство продукции на ОАО ГЛЗ «Центролит» за 2011 — 2013 гг.
Показатели. | Годы. | Темп роста, %. | ||||
2012 к 2011. | 2013 к 2012. | 2013 к 2011. | ||||
1. Объем произведенной продукции (выполненных работ, оказанных услуг), млн р. | 195,6. | 108,6. | 215,6. | |||
2. Затраты на производство продукции (выполнение работ, оказание услуг), млн р. | 194,9. | 199,2. | 388,2. | |||
3. Затраты на 1 р. продукции (работ, услуг) всего, р. | 2,3. | 2,3. | 1,3. | 56,5. | 56,5. |
Примечание — Источник: собственная разработка на основании данных, взятых из документации предприятия Из таблицы видно, что затраты на 1 рубль продукции уменьшились за исследуемый период — в 2011 году данный показатель составил 2,3 рублей, в 2012 году показатель остался без изменений, в 2013 году уменьшился до 1,3.