Применение керамики
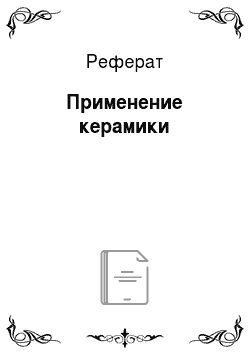
Предел прочности при сжатии пенокерамических изделий средней плотностью 400−700 кг/м3 и размером 250?120?65 мм по данной технологии составляет 2,5−7,5 МПа, теплопроводность — 0,11−0,16 Вт/м°С, морозостойкость — не менее 50 циклов. Следует отметить, что предел прочности при сжатии кладки из пенокерамических изделий составляет 80−92% от предела прочности самих изделий, что позволяет эффективно… Читать ещё >
Применение керамики (реферат, курсовая, диплом, контрольная)
РЕФЕРАТ НА ТЕМУ:
Применение керамики
г. Севастополь, 2010
План
1. Историческая справка.
2. Способы получения.
3. Применение в строительстве и других отраслях.
1. Историческая справка
Керамика — материалы и изделия из глин и их смесей с неорганическими соединениями, полученные путем обжига при высоких температурах. Основными технологические видами керамики являются гончарные изделия, терракота, майолика, фаянс, каменная масса и фарфор.
Термин «керамика» происходит от греческого слова «керамос», что означает глина. Керамическими называют изделия, изготовленные из глины с различными добавками и обожженные до камнеподобного состояния. В результате термической обработки керамика приобретает огнеупорность, химическую стойкость и ряд других свойств, определяющих широкое использование ее в самых различных отраслях народного хозяйства. Керамическое производство относится к числу наиболее древних на земле. Наличие легкодоступного материала — глины — обусловило раннее и практически повсеместное развитие керамического ремесла. Археологические раскопки, проводимые на территории многих стран Европы, Азии, Африки, Америки, дают обширный материал для изучения этой интереснейшей области творческой деятельности человека. Керамическое мастерство зародилось на самой заре человеческой истории, в период первобытно-общинного строя. Появившись, как свидетельствуют археологические данные, еще в эпоху мезолита (среднекаменного века) 15—12 тыс. лет тому назад, оно уже в эпоху неолита (нового каменного века) получило развитой характер. Первоначально основным видом керамических изделий были толстостенные сосуды с пористым черепком, круглым или коническим дном (придававшим устойчивость при установке в землю). Лепились они от руки путем наращивания отдельных жгутов глины (способом налепа). В глину, чтобы она не трескалась при обжиге, добавлялись толченые раковины и измельченный гранит. Крупные сосуды использовались для приготовления пищи, более мелкие служили очевидно для еды. Изделия каменного века обжигались сначала на кострах (вероятная температура обжига 800…900°С), позднее появились специальные обжигательные печи. По многочисленным отпечаткам пальцев было установлено, что древнейшие керамические сосуды изготовлялись женщинами.
В период позднего неолита и энеолита (медного века)—4…2 тыс. до н.э. — формы сосудов (кувшинов, мисок, чаш) становятся более разнообразными; появляются небольшие, условно решенные скульптуры людей и животных. Большая часть сосудов имеет уже плоское дно, что указывает на распространение плоского стола и плоского печного пода, т. е. на преобладание оседлого образа жизни. Тогда же керамические изделия начинают украшать орнаментом. Можно проследить развитие орнамента от простейших, выдавленных штампиком и острием узоров так называемого ямочно-гребенчатого типа, покрывавших в различных комбинациях всю наружную поверхность сосудов, до гораздо более разнообразных и художественно выразительных росписей, состоявших из ритмически чередовавшихся спиралевидных завитков, концентрических кругов, волнообразных линий, сетчатых и шахматных рисунков и т. д. Узоры часто были многоцветными, использовались сочетания красных, белых, черных и других красок.
2. Способы получения Одним из направлений повышения эффективности производства и применения стеновой керамики является уменьшение плотности за счет создания пористой структуры материала, что позволяет снизить материалоемкость производства и увеличить теплозащиту стеновых ограждений.
Известны шесть основных способов поризации структуры строительных материалов:
· вспучивание,
· удаление порообразователя,
· неплотная упаковка,
· контактное омоноличивание,
· объемное омоноличивание,
· создание комбинированных структур.
При разработке технологии поризованной стеновой керамики в той или иной мере находят применение все названные способы. Однако на практике для поризации структуры керамических изделий используют способ удаления порообразователя.
Применение в промышленности строительной керамики способа выжигания порообразователя, вводимого в состав исходной керамической массы, позволило частично решить как выше обозначенные проблемы, так и проблемы, связанные с экономией топлива и утилизацией топливосодержащих отходов. Данная технология позволяет получать изделия средней плотностью 600−1000 кг/м3 в зависимости от глинистого сырья, состава шихты и пустотности изделий. Наиболее эффективными выгорающими добавками для уменьшения плотности изделий являются отходы целлюлозно-бумажного производства, опилки, пенополистирол и др.
В 80-е годы прошлого века за рубежом получила распространение технология изготовления пористо-пустотелых изделий «Poroton», разработанная в Германии и Швеции. Патент на изготовление этих изделий был приобретен 32 странами мира. Так например, изделия «Poroton» получают методом пластического формования, используя в качестве выгорающей добавки вспененный полистирол. В результате выгорания полистирола формируется закрытая ячеистая структура, что благоприятно сказывается на физико-механических показателях изделий. Недостатком этой технологии является значительный выброс продуктов сгорания полистирола в окружающую атмосферу. В связи с этим использование пенополистирола возможно только при условии отжига и очистки отходящих газов.
В настоящее время технология производства пористо-пустотелых изделий успешно применяется на ЗАО «Победа ЛСР». В качестве выгорающей добавки используются тонкоизмельченные опилки. Средняя плотность изделий составляет 650−1000 кг/м3, пустотность — 45−54%, коэффициент теплопроводности — 0,154−0,26 Вт/(м°С), водопоглощение — 9−17%. Изделия выпускаются с маркой по прочности М35, М50, М75, М100, М125 и М150 в зависимости от средней плотности. Марка по морозостойкости составляет не менее F35. Укрупненные пористо-пустотелые керамические изделия средней плотностью 800−1000 кг/м3 выпускают также ЗАО «Норский керамический завод», ЗАО «Петрокерамика» и др. Ведется строительство новых заводов во Владимирской области и республике Татарстан. Некоторые заводы используют в качестве выгорающих добавок уголь, углеотходы и золы. Их вводят в количестве, соответствующем 60−80% расхода топлива. Реализованы в производстве технологии пористо-пустотелых изделий на основе 100% углеотходов. Но высокая продолжительность обжига таких изделий, неравномерность выгорания угля требуют все же введения корректирующих добавок. Необходимо отметить, что при получении пористо-пустотелых изделий средней плотностью менее 800 кг/м3 в технологии возникают следующие проблемы:
· ухудшение формовочных свойств керамических масс;
· необходимость использования среднепластичного или еще лучше высокопластичного глинистого сырья;
· подготовка тонкой фракции выгорающей добавки;
· высокое содержание выгорающей добавки, которое достигает 50—55% по объему вещества;
· снижение прочности изделий.
К тому же далеко не все глинистые породы пригодны для производства пористо-пустотелых изделий средней плотностью 800−1000 кг/м3. По результатам проведенных исследований содержание глинистых минералов в породе должно составлять не менее 30−35%. Применение крупноформатных пористо-пустотелых изделий в кладке в комбинации с лицевым кирпичом позволяет создавать ограждающие стеновые конструкции толщиной 510−640 мм, которые удовлетворяют современным требованиям по теплозащите зданий. Однако предел прочности при сжатии кладки из пористо-пустотелых изделий, выполненной даже на весьма прочном растворе, составляет лишь 30−50% и менее от предела прочности изделий. Основная причина такого снижения прочности заключается в высокой пустотности изделий, размерах и форме пор, а также в расклинивающем действии кладочного раствора, частично затекающего в пустоты и вызывающего растягивающие напряжения в изделиях. Среди других причин снижения прочности кладки из высокопустотных керамических изделий можно назвать следующие:
· неравномерное распределение давления по поверхности кирпича, вызывающее в нем кроме сжатия напряжения изгиба и среза;
· трещины, возникающие в плоскости вертикальных швов, могут проходить по сечениям кладки, ослабленным пустотами и т. д.
Решить данную проблему можно частично путем подшлифовки оснований изделий, применением современных кладочных клеевых растворов, а также использованием специальных сеток, исключающих попадание раствора в пустоты изделий. Однако в России указанные технологические приемы, несмотря на рекомендации производителей, пока не применяются.
Таким образом, технология с использованием выгорающих добавок не требует разработки принципиально нового оборудования и реализуема в условиях действующих заводов по выпуску обыкновенного кирпича. Однако следует признать, что при получении изделий со средней плотностью ниже 800 кг/м3 возникает множество проблем (необходимость использования среднеили высокопластичного глинистого сырья, тонкого измельчения выгорающей добавки, увеличения продолжительности обжига, снижение прочности и т. д.).
Существенным недостатком способа неплотной упаковки является весьма низкая прочность изделий при соответственно высокой средней плотности. Так, предел прочности при сжатии обожженных изделий средней плотностью 1000−1100 кг/м3 на основе глинистого сырья составляет всего 4−5 МПа.
Способ объемного омоноличивания в технологии стеновой керамики применяется весьма ограниченно. Причина этого заключается в том, что для существенного снижения плотности необходимо использовать заполнитель с высокой пористостью. Как правило, низкая прочность высокопористого заполнителя не позволяет осуществлять интенсивную массопереработку и формование изделий методами пластического формования или полусухого прессования. Недостатком этого способа является также двойной обжиг заполнителя (вспучивание, затем обжиг в кирпиче), а высокая средняя плотность и низкая прочность полученного материала не позволяет ему конкурировать с керамическими материалами, получаемыми традиционным методом пластического формования с применением различных выгорающих добавок.
Способ вспучивания включает следующие модификации: высокои низкотемпературное газообразование, пенообразование, аэрирование, сухая минерализация пены. Материалы, полученные по этому способу, имеют ячеистое строение, которое формируется при высоких (высокотемпературное газообразование) и низких (низкотемпературное газообразование, пенообразование и др.) температурах. Величина пористости зависит от состава исходной шихты и режимов обработки и определяет плотность изделий. С изменением плотности в широких пределах изменяются и другие свойства пористых керамических материалов.
Наиболее важное преимущество способа вспучивания по сравнению с приведенными выше, заключается в возможности значительного снижения плотности керамических стеновых изделий (вплоть до 250−300 кг/м3). Данный способ позволяет отказаться от прессового и другого энергоемкого оборудования, работающего с большими усилиями, имеющего большую мощность и подвергающегося износу. Наиболее существенный недостаток способа — необходимость разработки и изготовления специального промышленного оборудования, что требует привлечения дополнительных инвестиций.
К недостаткам метода высокотемпературного газообразования следует отнести следующие:
· необходимость использования вспучивающихся глин, которые распространены не повсеместно, или приготовление сложной сырьевой шихты определенного состава;
· строгие требования к полуфабрикату по гранулометрическому составу;
· высокотемпературный обжиг, который чаще всего осуществляется в две стадии в отдельных тепловых агрегатах, что приводит к повышенному расходу топлива;
· обжиг в специальных формах требует применения дефицитных жаростойких материалов и использования обмазки.
Однако при всех ее недостатках данная технология может быть реализована на заводах по производству керамзита (при условии разработки специального оборудования). Следует отметить также, что метод высокотемпературного газообразования позволяет исключить процесс сушки изделий. Необходима лишь сушка гранул или сырьевых компонентов, которая осуществляется в сушильном барабане.
Важным переделом технологий пористокерамических изделий методами низкотемпературного газообразования, пенообразования и аэрирования является довольно сложная и на первый взгляд энергетически затратная шликерная подготовка сырья. Однако и она имеет весьма значительные преимущества:
· способствует полному разрушению природной структуры и усреднению керамической массы, что позволяет использовать потенциальные возможности глинистого сырья для образования пористой структуры изделий. При этом исключается энергоемкий сухой помол компонентов (метод сухой минерализации пены);
· позволяет практически полностью удалить каменистые включения, присутствующие почти во всех глинах;
· позволяет вводить и равномерно распределять как твердые, так и жидкие корректирующие добавки, даже в небольшом количестве.
Существенным недостатком шликерного способа подготовки сырья часто и в большей степени не обоснованно считают повышенное водозатворение керамических масс, и как следствие, высокие затраты энергии на ее удаление при сушке. Однако этот факт является справедливым только при получении плотных керамических изделий.
Сравним количество испаряемой воды с плотных и пористых изделий одинакового объема. Массу испаряемой воды можно определить из формулы:
mв = Wабс mс,
керамика глина обжиг строительство где Wабс — абсолютная формовочная влажность, кг/кг; mс — масса абсолютно сухого изделия, кг. Примем во внимание тот факт, что абсолютная формовочная влажность пористокерамических изделий (50−70%) в среднем в 3 раза выше влажности изделий пластического формования (17−23%). А плотность абсолютно сухих изделий в среднем составляет: 600 кг/м3 — для газои пенокерамического кирпича и 1800 кг/м3 — для полнотелого кирпича пластического формования. Таким образом, при сушке изделий одинакового объема масса абсолютно сухого пористокерамического кирпича в 3 раза меньше массы абсолютно сухого кирпича пластического формования; следовательно, в данном случае, количество испаряемой воды с единицы изделия будет одинаково.
Необходимо отметить, что отличительной особенностью процесса обжига газои пенокерамики по сравнению с керамическими материалами пластического формования или полусухого прессования является возможность его интенсификации в связи с высокопористой структурой, поры которой препятствуют развитию трещин.
К недостаткам методов низкотемпературного газообразования, пенообразования, аэрирования и сухой минерализации пены следует отнести многокомпонентный состав сырьевых материалов; высокую воздушную усадку сырца, которая достигает 15−20%; большой парк форм; использование обмазки и промывки форм.
До настоящего времени основной проблемой технологии газои пенокерамических изделий являлась стабилизация поризованной массы в формах, которая осуществляется добавкой строительного гипса (от 10 до 20% по массе сухого вещества). Использование гипса с экологической точки зрения не приемлемо, так как в этом случае при обжиге воздушная среда интенсивно загрязняется сернистыми газами. В противном случае, получение устойчивой и прочной сырцовой структуры материала становится проблематичным из-за значительной осадки пеномассы и, как следствие, разрушения структуры сырца. При этом прочность при сжатии обожженных изделий обычно не превышает 2 МПа для средней плотности 800 кг/м3.
В институте ВНИИстром им. П. П. Будникова разработана технология производства пенокерамических стеновых и теплоизоляционных изделий средней плотностью 400−700 кг/м3 на основе легкоплавких глин методом пенообразования.
Отличительной особенностью разработанной технологии является формирование устойчивой сырцовой структуры за счет регулирования процессов коагуляции глинистой составляющей в поризованной керамической массе, что позволяет:
· отказаться от применения гипса в качестве стабилизатора пеномассы;
· повысить структурную прочность сырца в начальный период сушки;
· осуществить распалубку изделий через 2−3 часа после формования и интенсифицировать процесс сушки;
· повысить трещиностойкость изделий;
· снизить воздушную усадку до 6−10%, в зависимости от глинистого сырья и состава пенокерамических масс.
Предел прочности при сжатии пенокерамических изделий средней плотностью 400−700 кг/м3 и размером 250?120?65 мм по данной технологии составляет 2,5−7,5 МПа, теплопроводность — 0,11−0,16 Вт/м°С, морозостойкость — не менее 50 циклов. Следует отметить, что предел прочности при сжатии кладки из пенокерамических изделий составляет 80−92% от предела прочности самих изделий, что позволяет эффективно применять пенокерамические материалы в стеновых конструкциях. Что касается разработки специального оборудования, то авторами предложен ряд технических решений способствующих этому. Разработано новое устройство для приготовления пены, основные преимущества которого заключаются в том, что кратность получаемой пены составляет 50−150, устойчивость пены увеличивается в 2−4 раза; расход пенообразователя снижается в 2−3 раза, влажность шликерной массы после вспенивания уменьшается на 4−7% в зависимости от заданной средней плотности изделий. Предложен способ и устройство для распалубки, промывки и опесочивания форм, позволяющее автоматизировать данную операцию и тем самым сократить многочисленный парк форм.
Таким образом, на основании объективного анализа основных преимуществ и недостатков различных технологий производства поризованных керамических изделий можно сделать вывод, что наиболее эффективными являются методы высокотемпературного газообазования и пенообразования. Однако в современной действительности наиболее востребованной и развивающейся останется технология пористо-пустотелых изделий. Технологии производства высокопористых стеновых изделий способом вспучивания глинистого сырья не реализуются до тех пор, пока не будет разработано и изготовлено промышленное оборудование.
3. Применение в строительстве и других отраслях Изучение применения керамических изделий в прошлом особенно поучительно, так как одни из них почти в неприкосновенности сохранили свое извечное предназначение, другие же претерпели столь существенные изменения, что их с полным правом можно назвать новыми, эффективными. Однако надо не забывать, что в архитектуре не все новое современно и не все древнее устарело. Только сопоставление «классических» приемов применения керамики с требованиями нашего времени поможет архитектору творчески подойти к использованию ее в современном строительстве.
Керамика в саду Сейчас керамика переживает небывалую популярность, архитекторы и дизайнеры охотно используют ее как в интерьере, так и в экстерьере. И дело здесь, видимо, не только в пластических возможностях керамики, относительно невысокой стоимости самого материала и его долговечности. Рожденная землей и огнем, керамика органично сочетается как с живой природой, так и с большинством строительных материалов.
Керамика из раствора Изготовление керамики — одно из древнейших производств, ему не меньше 12 тысяч лет. Но лишь в последние десятилетия технология керамики стала базироваться на научных основах, строгих закономерностях физической химии. Это связано и с чрезвычайно возросшими требованиями к керамике, и с удивительным разнообразием керамических изделий, в которых нуждается человечество сегодня.
Керамика как конструкционный материал Рассмотрение не только конструкционных материалов из глины, но вообще строительной керамики обычно начинают с кирпича, традиционного стенового материала, которым еще в древние времена человек заменял природный камень для кладки стен и который поэтому Андреа Палладио включил в главу, названную «О камне». Он писал: «…Искусственный камень называется кирпичом и имеет форму прямоугольника». Витрувий в том же духе трактует кирпич и предпосылает это рассуждение всем остальным — «ибо здание в конечном итоге разлагается на кирпичи, которые первыми кладутся при постройке, как элементы здания».
Керамика в облицовке зданий Применение облицовочных керамических материалов с давних пор развивалось по двум направлениям. Одно возникло вынужденно из-за того, что стены из бута или сырцового кирпича неизбежно требовали атмосферостойкой защиты, роль которой выполняла примитивная глиняная обмазка. После получения обожженных керамических изделий их стали использовать в виде декоративных плиток, защищающих и украшающих наружные стены.
Полы из керамики Кирпичи, покрытые глазурью (по размерам близкие к нашим плиточным изделиям), уже в начале I тыс. до н.э. применялись для настилки полов во дворцах Древнего Египта. Притом изделия различных оттенков, получавшиеся при обжиге глазури, подбирались таким образом, чтобы на поверхности пола создавались плавные Цветные переходы. Еще более широко использовались керамические изделия для устройства водостойких полов террас и полузакрытых Дворов в Вавилоне.
Кровля из керамики Черепица — кровельное штучное изделие из обожженной глины— является одним из старейших видов покрытий зданий. Появилась она тогда, когда стали возводить скатные кровли, так как плоские крыши жилищ в Древнем Египте или Вавилоне вряд ли нуждались в специальных покрытиях из довольно дорогой керамики.
Санитарно-технические изделия из керамики Создание древних городов в долинах рек Нила и Инда, Тигра и Евфрата уже в IV тыс. до н. э. выдвинуло проблему водоснабжения и канализации жилищ. Скопление большого числа жителей при отсутствии самых простейших элементов благоустройства приводило к распространению опустошительных эпидемий. В борьбе с их последствиями возникли и стали развиваться основы гигиены, которые вначале выливались в форму обязательных религиозных ритуалов. Недаром во всех древних религиях есть предписания о чистоте тела, об омовениях и купаниях в священных водах.
Декоративно-художественная керамика Во многих выдающихся музейных собраниях мира имеются декоративные керамические изделия, поражающие совершенством фордо и богатством росписи. Это вазы и светильники, барельефы и скульптура, изразцы и мозаика, выполненные мастерами древности. Некоторые из них были специально предназначены для применения в строительстве. Наиболее ранние свидетельства о применении декоративных плит из керамики, покрытых глазурями или эмалями, в отделке зданий мы находим в Древнем Египте.
Лепка из глины
Лепка — это простая техника, которая демонстрирует непосредственный результат. Наметьте толщину стенок около 13 мм. С опытом вы сможете формовать более тонкие стенки сосудов, но сначала достаточно будет толстых глиняных стенок, которые вы потом сможете обжать немного тоньше.
Классификация Как показал краткий обзор применения глиняных изделий в архитектуре, огромную роль керамики нельзя переоценить. Притом история строительной керамики продолжается. Расширяется и сырьевая база для изготовления керамики.
www.belemont.ru
www.akeram.ru
www.library.by