Производство рядового шамота
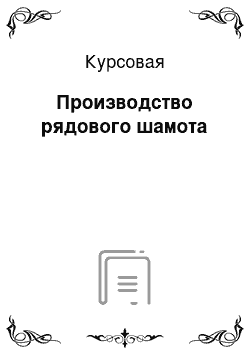
Для выполнения функции и реализации прав, предусмотрено лаборатория охраны окружающей среды. Со всеми подразделениями и техническими подразделениями по вопросам: нормативно-механической документации для организации и проведения контроля производственных факторов, выбросов, эффективности работы аспирационных и вентиляционных систем; документов и материалов необходимых для оформления и получения… Читать ещё >
Производство рядового шамота (реферат, курсовая, диплом, контрольная)
Введение
Наиболее распространенным видом огнеупоров являются алюмосиликатные огнеупоры, содержащие в качестве главных химических компонентов окись алюминия и двуокись кремния в различных состояниях.
К шамотным огнеупорам относят изделия с содержанием А1203 от 28 до 45%. Эти огнеупоры обладают рабочими свойствами, обеспечивающие применение их в ряде тепловых агрегатов общего назначения. Огнеупоры не являются конечной продукцией и обеспечивают только эффективность и экономичность работы тепловых агрегатов.
Огнеупорные изделия должны не только выдерживать высокие температуры, но и обладать комплексом других свойств и прежде всего экономить тепло, то есть быть хорошими теплоизоляторами (а в некоторых случаях, наоборот, проводниками тепла), не разрушаться под действием химического и механического воздействия.
Многообразие условий службы шамотных огнеупоров вызывали необходимость изготовления большого потока производства таких изделий.
Падение производства шамотных огнеупоров привело к закрытию многих цехов огнеупорных предприятий. Снизилось производство нормального кирпича, ковшевых огнеупоров, изделий для воздухонагревателей, коксовых печей для цементной промышленности, а так же теплоизоляционных изделий. Снижение производства закономерно. Вместо шамотных ковшевых изделий стали применять высокоглиноземистые и периклазоуглеродистые изделия и массы.
Не все агрегаты металлургические выводятся из эксплуатации, остаются агрегаты не высокой емкости, которые необходимо футеровать именно шамотными огнеупорами.
Участие огнеупорной промышленности и качество огнеупоров в той или иной стране характеризуют степень её индустриализации. Из более чем 212 самостоятельных и зависимых стран мира развитая огнеупорная промышленность имеется только в 35 странах. Основное количество огнеупоров потребляется черной металлургией, поэтому расход огнеупоров, условно относят, на одну тонну стали. Поэтому без огнеупоров нет другого практически приемленного способа получить и поддерживать длительное время высокие температуры в больших объемах.
Несмотря на более чем 50% падение объемов производства, огнеупорная отрасль сумела выстоять за счет изменения качественной структуры продукции и освоения конкурентоспособных видов огнеупоров.
Промышленность России включает 16 специализированных огнеупорных предприятий. Кроме того, 11 металлургических предприятий имеют собственные огнеупорные производства. Кризис, затронувший практически все отрасли промышленности, потребляющие огнеупоры, не мог не сказаться на производстве огнеупоров.
Поэтому проектируемое производство обеспечит потребности в шамотных огнеупорах на производство технического перевооружения российской металлургии.
Согласно заданию курсового проекта рассматривается производство рядового шамота марки ШР-28 для производства шамотных и многошамотных огнеупорных изделий.
Шамотные огнеупоры нашли широкое применение в металлургической, химической, машиностроительной, коксохимической, огнеупорной и стекольной промышленности, в новой технике, энергетике и других отраслях.
Производство и использование шамотных изделий является потребными, так как шамот обладает термической, механической и химической устойчивостью, высокой термостойкостью и технологичностью, позволяющей изготовлять из шамота разнообразные изделия. Из шамота можно изготовлять мелкие и очень крупные изделия.
1. ФИЗИКО-ХИМИЧЕСКИЕ УСЛОВИЯ ПРОИЗВОДСТВА
1.1 Оценка качества брикета для рядового шамота. Исходное сырьё
Производство шамота ведут обжигом кусковых глин после предварительного брикетирования с последующим обжигом. Брикет должен быть размером 120×80 мм, массой около 2 кг, размер заусенцев не более 10 мм. Влажность брикета 17−23%. Эллипсообразная форма брикета обеспечивает равномерное прохождение дымовых газов по всему объему шахтной печи.
К брикету предъявляют следующие требования:
достаточная высокая механическая прочность, чтобы избежать раскола брикета при транспортировке и загрузке в печь;
небольшая кромка, так как она в результате сушки и обжига осыпается и способствует образованию «козлов» (сваров), не прохождению газов к выходу недожженного шамота;
оптимальная влажность, чтобы облегчить формование на пресс-вальцах.
При брикетировании глины могут возникать следующие виды брака:
— смещение полусферических поверхностей брикета, вызываемое неполным совпадением осей ячеек бандажей.
— образование заусенцев свыше допустимых 5 мм, обусловленное неплотным прилеганием бандажей друг к другу или неполным совпадением осей ячеек бандажей.
— недостаточная прочность брикета — как следствие низкой влажности глины, очень тощей глины или недостаточного питания пресс-вальцов глиной.
— не выпадение брикета из ячеек, вызванное высокой влажностью глины или плохо отшлифованной поверхностью ячеек. 1]
Химический состав брикета, применяемого для изготовления шамота марки ШГР-28, представлен в таблице 1.
Таблица 1 — Химический состав глиняного брикета, %
Наимено-вание | Содержание оксидов | Сумма | ||||||||||
Si02 | А1203 | Fe203 | ТiО2 | MgO | СаО | Na20 | К20 | SO3 | п.п.п. | |||
брикет | 56,91 | 25,50 | 2,5 | 1,60 | 0,23 | 0,41 | 0,19 | 0,33 | 0,06 | 12,27 | ||
В качестве исходного сырья, для производства рядового шамота марки ШГР-28, будет использована огнеупорная глина Латненского месторождения марки ЛТ-3 по ТУ 14−8-152−75, которые залегают в Воронежской области. Добыча глины ведется открытым способом.
Огнеупорными глинами называют землистые обломочные горные породы осадочного происхождения, которые состоят в основном из высокодисперсных гидроалюмосиликатов, дают с водой пластичное тесто, сохраняющее при высыхании форму, и приобретают после обжига прочность камня. Кроме пластичных огнеупорных глин, в природе встречаются камневидные или сухарные глины, не образующие с водой пластичного теста. Такие глины называют сухарями, кремневками, флинтами и т. п. [2]
Главнейшие первичные породы, из которых образовались огнеупорные глины и каолины — граниты и гнейсы. При выветривании сначала происходит их распад на составляющие минералы — кварц, слюду и полевые шпаты, затем под действием водных растворов углекислоты более глубокое разложение, двух последних материалов. Полевой шпат, например, разлагается по следующей схеме:
К20 А1203 6Si02 (полевой шпат)+2Н20+С02
Al2032Si02 2Н20 (каолинит)+ K2C03+4Si02
К2С03 как растворимое соединение вымывается; остальные продукты реакции образуют горную породу, называемую каолином.
Огнеупорные глины отличаются от вторичных каолинов большей загрязненностью и более высокой дисперсностью. Содержание соединений железа в огнеупорных глинах доходит до 3−5%; содержание К20, Na20, CaO, MgO и др. составляет 3−4%.
Глины относят к полидисперсным материалам. Они не однородны по составу и свойствам. Фракция глин 0,01−0,005 мм имеет обломочный характер; минералогический (и химический) состав этой фракции определяется составом пород, при выветривании которых образовались данные глины. В их состав входят кварц, полевые шпаты, слюды и тяжелые минералы: гранат, магнетит, пирит, марказит, циркон и др. Фракция размером 0,005−0,001 мм является промежуточной, в ней содержится обломочный материал и продукты химического разложения первичных горных пород. В материалах фракции мельче 0,001 мм первичные продукты механического выветривания горных пород обычно не содержатся. Фракция мельче 0,001 мм состоит из продуктов химического выветривания-каолинита, монотермита и других алюмосиликатов, ее называют глинистой субстанцией. [3]
Зерновой состав глин (одного и того же типа) характеризуется большими отклонениями. Глины с содержанием фракции мельче 0,001 мм в количестве 50−60% относят к тонкодисперсным.
Основные примеси в огнеупорных глинах: свободные кремнезем и глинозем, коллоидный кремнезем, щелочные и щелочноземельные оксиды, соединения железа, титана и других металлов, органические примеси в виде углистых включений, гумусовых кислот и др. Содержание Si02 в огнеупорных глинах доходит до 70% и более.
Щелочи встречаются в глинах чаще всего в виде слюды, реже в виде полевых шпатов, а в глинах некоторых месторождений входят в состав основного минерала, например монотермита. Щелочи в глинах содержатся в количестве 0,5−3,5%.
Довольно распространенной примесью в огнеупорных глинах является ТiO2, чаще всего присутствующая в виде минерала рутила.
Содержание ТiO2 составляет 0,5 — 2,0%. Обычными примесями в глинах служит СаО и MgO. Их суммарное содержание составляет 0,1 -1,05%. Из органических примесей в глинах присутствуют каменный уголь, торф и др.; при содержании их до 10 — 15% глины называют углистыми.
Химический состав глины Латненского месторождения марки ЛТ-3 представлен в таблице 2.
Таблица 2 — Химический состав глины марки ЛТ-3, %
Наименование | Содержание оксидов | Сумма | ||||||||||
А12Оз | Si02 | Fe203 | Ti02 | CaO | MgO | K20 | Na20 | п.п.п. | SO2 | |||
Глина ЛТ-3 | 25,52 | 56,96 | 2,5 | 1,6 | 0,41 | 0,23 | 0,33 | 0,19 | 12,28 | 0,06 | 100,08 | |
Цвет огнеупорных глин преимущественно серый разных оттенков. Некоторые глины имеют белый цвет. Плотность глин 2,5−2,8 г/см3. Огнеупорность глин 1580 — 1770 °C и зависит от их химического состава.
Спекаемость глин зависит не только от химико-минералогического состава и дисперсности, но также и от плотности и характера структуры сырца. [1]
Характеристика огнеупорной глины марки ЛТ — 3 представлена в таблице 3.
Таблица 3 — Характеристика огнеупорной глины марки ЛТ-3 по ТУ 14−8-152−75
Наименование показателей | Норма | |
Массовая доля А1203, не менее, % Fe203, не менее, % Огнеупорность, °С, не менее Изменение массы при прокаливании, %, не более | 2,5 | |
1.2 Техническая характеристика рядового шамота Шамот — это обожженная глина до прекращения усадки. На шамот выбирают глины с высоким содержанием А120з, глины хорошо спекающиеся, желательно при невысоких температурах.
Шамот применяют в качестве отощителя при производстве шамотных и многошамотных огнеупорных изделий.
Введение
большого количества шамота позволяет повысить механическую прочность изделий, термостойкость, шлакоустойчивость, температуру начала размягчения и обеспечить точность размеров и формы.
Фазовый состав шамота — это муллит и стеклофаза.
По внешнему виду шамот представляет собой продукт сферической формы от светло-желтого до коричневого цвета.
Критерием качества шамота служит водопоглощение.
Водопоглощение — это отношение массы поглощаемой материалом воды при кипячении к весу абсолютно сухой навески.
Зерновой состав оказывает влияние на формирование важнейших свойств готовых изделий. Оптимально подобранный зерновой состав обеспечивает хорошую термостойкость изделий, формирует механическую прочность и плотность.
При подборе зернового состава шамота преследуется цель достижения наиболее плотной укладки зерен шамота при прессовании массы.
Зерновой состав шамота с максимально плотной укладкой при двух — трех исходных фракциях характеризуется соотношением этих фракций: крупной 55 — 65%, средней 10 — 30% и мелкой 15 — 30%. [4]
Качественные показатели рядового шамота марки ШГР-28 по ТУ 1518−020−188 162−97 представлены в таблице 4.
Таблица 4 — Характеристика рядового шамота марки ШГР-28 по ТУ 1518−020−188 162−97
Наименование показателя | Норма | |
Массовая доля, %: Al2O3, не менее Fe203, не более Огнеупорность, °С, не ниже Водопоглощение, %, не более Массовая доля влаги при отгрузки, %, не более | 5,5 12,0 | |
1.3 Технология изготовления брикета для рядового шамота. Контроль производства В курсовом проекте предлагается технологическая схема производства рядового шамота методом предварительного брикетирования. Этот метод обеспечивает уменьшение пылеуноса при обжиге в шахтных печах и равномерный обжиг, что исключает пережог шамота.
Глина складируется на складе полузакрытого типа.
Склад оборудован приемными бункерами, отсеками и глинорезной машиной. Таким образом, глина из отсеков отбирается краном и подается
Технологическая схема производства рядового шамота марки ШР-28
Склад глины
Мостовой грейферный кран
Стругач Ленточный конвейер с магнитным сепаратором
Сушильный барабан (в зимний период)
Ленточный конвейер
Двухвальный смеситель
возврат
Пресс-вальцы крошки
Ленточный конвейер
Элеватор
Бункер брикета
Шахтная печь
Ленточный конвейер
Склад шамота (бункера) в приемные бункера, откуда поступает на дробление в стругач. Влажность глины на складе 18−23%, размер кусков 10−300 мм.
Глина дробится в стругаче до кусков размером не более 60 мм. Дробленая глина ленточным конвейером подается в смеситель, а затем в пресс-вальцы минуя сушильный барабан.
В зимнее время мерзлая глина предварительно размораживается в сушильном барабане. Массовая доля влаги после сушильного барабана должна быть не менее 17%.
Дробленая глина подвергается магнитной сепарации.
В смесителе при необходимости глина увлажняется горячей водой и подается для прессования брикета в пресс-вальцы. Из пресс-вальцов брикет должен выходить овальной формы, хорошо спрессованный, с толщиной заусенец не более 10 мм. Массовая доля влаги в брикете должна быть 17−23%.
Брикет из пресс-вальцов ленточным конвейером поступает на виброрешетки, где осуществляется осыпь заусенец с целью уменьшения пылеобразования в печах, и элеватором подается в бункера, установленные над каждой печью, а затем в печи на обжиг.
Обжиг шамота производится в шахтных печах, работающих на природном газе. Питание печи осуществляется автоматическими объемными питателями барабанного типа. Температура обжига 1380 °C. Загрузка печи производится при достижении температуры отходящих дымовых газов не менее 120 °C. Замер температуры отходящих газов проводится термометром сопротивления с передачей на автоматический самопишущий мост или термопарами с передачей на самопишущий потенциометр.
Обожженный шамот в области холодильника печи охлаждается водой, затем выгружается из печи при помощи механической выгрузки. Она должна работать на протяжении всей смены с использованием реле времени установленному по заданной программе.
Готовый шамот выгружается в расходные бункера.
Для поддержания качественных параметров на участке производства сортового шамота работает технический контроль.
Качество шамота определятся, как качеством используемых материальных элементов, так и соблюдением регламентирующих положений технологии на всех стадиях комплексного прогресса.
Для этого применяют следующие виды контроля: входной контроль сырья и материалов; текущий контроль технологического процесса; контроль качества готовой продукции (выходной контроль).
Текущий контроль обеспечивает поддержание точности технологического процесса на предприятии и составляет неотъемлемую часть технологии.
В задачу текущего контроля входят: соблюдение технологического процесса; предупреждение причин, приводящих к браку; накопление и обработка статических материалов по контролю производства.
Текущий контроль осуществляют на протяжении всего процесса производства, и контрольные функции распределяются следующим образом:
цеховой технический персонал проверяет качество готовой продукции и следит за соблюдением технологической дисциплины;
заводская лаборатория контролирует качество сырьевых материалов и готовой продукции;
отдел технического контроля (ОТК) проверяет качество готовой продукции, принимает ее, периодически проверяет соответствие технологии производства технологическим правилам и режимам по отдельным операциям.
Текущий контроль осуществляют по графикам контроля, в которых регламентировано наименование контролируемого параметра, место и частота отбора проб, персонал, осуществляющий отбор и определение. Все определения идут в строгом соответствии с требованиями ГОСТ, ТУ и других нормативно-технических документов. По результатам текущего контроля за месяц работники отдела технического составляют отчет по качеству продукции, который обсуждается на совещании по качеству. [5]
Контроль качества технологического процесса производства шамота представлен в таблице 5.
Таблица 5 — Контроль качества производства шамота
Наименование операции технологического процесса | Контролируемые параметры | Место отбора проб | Частота определений | Исполнитель | ||
По отбору проб | По испытанию | |||||
Дробление глины | Массовая доля влаги | Ленточный конвейер перед сушильным барабаном | 1 опр/см | Контролер ЦЗЛ | Контролер ЦЗЛ | |
Размораживание и подсушка | Массовая доля влаги | Ленточный конвейер после сушильного барабана | 1 опр/см | — II; | II | |
Прессование брикета | Массовая доля влаги | Ленточный конвейер после пресс-вальцев | 1 опр/см | — II; | II | |
Изменение массы при прокаливании | — II; | — II; | Контролер ЦЗЛ | Лаборант-аналитик ЦЗЛ | ||
Запесоченность глины | — II; | — II; | Контролер ЦЗЛ | Контролер ЦЗЛ | ||
Размер заусенцев | — II; | — II; | — II; | — II; | ||
Массовая доля А1203, Fe203. | — II; | — II; | Контролер ЦЗЛ | Лаборант-аналитик ЦЗЛ | ||
1.4 Применение шамота в производстве шамотных огнеупоров огнеупорный глина шамот брикет Шамот — это обожженная глина до прекращения усадки. На шамот выбирают глины с высоким содержанием А120з, глины хорошо спекающиеся, желательно при невысоких температурах.
Шамот применяют в качестве отощителя при производстве шамотных и многошамотных огнеупорных изделий.
Введение
большого количества шамота позволяет повысить механическую прочность изделий, термостойкость, шлакоустойчивость, температуру начала размягчения и обеспечить точность размеров и формы.
Характеристика рядового шамота марки ШГР-28 представлена в таблице 6.
Таблица 6 — Характеристика рядового шамота марки ШГР-28
Наименование показателя | Норма | |
Массовая доля, %: Al2O3, не менее Fe203, не более Огнеупорность, °С, не ниже Водопоглощение, %, не более Массовая доля влаги, %, не более Фазовый состав: — муллит — стеклофаза Цвет | 5,5 12,0 3Al2032Si02 Si02 желтый | |
Критерием качества сортового шамота служит водопоглощение.
Водопоглощение — это отношение массы поглощаемой материалом воды при кипячении к весу абсолютно сухой навески.
Качественная функция отощителя определяется степенью его зернистости. Поэтому для эффективной оценки степени обработки отощителя служит зерновой состав, который в разрабатываемой технологии устанавливается опытным путем.
Зерновой состав оказывает влияние на формирование важнейших свойств готовых изделий. Оптимально подобранный зерновой состав обеспечивает хорошую термостойкость изделий, формирует механическую прочность и плотность.
При подборе зернового состава шамота преследуется цель достижения наиболее плотной укладки зерен шамота при прессовании массы. [4]
Шамот марки ШГР-28 применяют для изготовления шамотных изделий общего назначения марки ША по ГОСТ 390–96.
Физико-химические показатели огнеупорных изделий марки ША представлены в таблице 7.
Таблица 7 — Физико-химические показатели огнеупорных изделий марки ША по ГОСТ 390–96
Наименование показателя | Норма | |
Массовая доля Al2O3, %, не менее Огнеупорность, 0С, не ниже Усадка линейная дополнительная или рост, %, не более при температуре, 0С Пористость открытая, %, не более Предел прочности при сжатии, МПа, не менее Температура начала размягчения при удельной нагрузке, 0,2 МПа, 0С, не ниже Термостойкость, водяных теплосмен, не менее | 0,7 | |
Шамотными называются огнеупорные изделия с содержанием 80% шамота и 20% глины, с массовой долей А1203 от 28 до 45%, огнеупорностью 1600 — 1750 °C.
Огнеупорные изделия должны обладать определенными свойствами для их дальнейшей эксплуатации: огнеупорность, высокая механическая прочность, высокая температура деформации под нагрузкой, термостойкость, химическая стойкость.
Огнеупорность шамотных изделий зависит от исходного сырья, его чистоты и фазового состава изделия.
Механическая прочность зависит от плотности изделия, его пористости. Строительная прочность зависит от фазового состава материала и формируется при подборе зернового состава.
Химическая стойкость зависит от природы материала, его фазового состава.
Термостойкость шамотных изделий зависит от зернового состава шихты и от химико — минералогического состава.
Теплопроводность зависит от структуры, механического теплопереноса, от фазового состава пористости.
Форма и геометрические размеры (рис.1) огнеупорных изделий марки ША соответствуют ГОСТ 8691–73 или выполняются по чертежам:
Рисунок 1 — Огнеупорные изделия марки ША, а — изделия № 1−10 Кирпич прямой; б — изделия № 11−15 Кирпич прямой полуторный; в — изделия № 16 — 19 Кирпич прямой трехчетвертной; г — изделия № 20 — 32 Клин торцовый (двусторонний и односторонний); д — изделия № 33 — 41 Клин торцовый полуторный (двусторонний и односторонний); е — изделия № 42 — 48 Клин ребровый (двусторонний и односторонний).
Шамотные огнеупоры нашли свое применение в сталеплавильном производстве, в основном в неответственных зонах металлургических печей, сталевыпускных желобов, крышек завалочных окон мартеновских печей, котлах, нижних рядах насадки регенераторов, футеровка промышленных печей (туннельные, стекловаренные и др.) и т. д.
Расход шамотного кирпича на сталевыпускные желоба составляет от 2,5 до 6,5 кг/тн стали. Возможность смены крышек создала практику применения в их футеровке изделий низких классов. Износ кирпича в крышках происходит путем оплавления его пламенем.
1.5 Процессы при производстве Для получения брикета из глины проходят следующие технологические процессы: первичное дробление глины, увлажнение и смешение глины, формование брикета.
Измельчение крупных и средних кусков называют дроблением. Глина на склад прибывает в виде кусков разной формы и размеров. Для облегчения последующей обработки его необходимо подробить. Дробление возможно осуществлять несколькими способами: раздавливанием, раскалыванием, истиранием, удар, разрезание и т. д. Выбор способа измельчения определяется структурой материала. Для эффективного измельчения материала применяют сочетание вышеуказанных способов, например: удар и истирание, раскалывание и истирание. Для предварительного измельчения глины, т.к. он является пластичным материалом, в основном применяют способ разрезания. Для осуществления данной технологической операции используют стругач (глинорезку).
Чтобы сформовать из глины брикет, необходимо предварительно затворить её водой, с целью предания пластичности массе. Этот процесс осуществляется в двухвальном лопастном смесителе. Влагу добавляют в глину в виде воды или пара. Нормальной влажностью глины, называют влажность, при которой глина легко мнется в руках, но не прилипает к пальцам. Для этого необходимо, чтобы добавляемая вода впитывалась в глину и она равномерно набухала по всей массе.
Увлажнение водой. Увлажнение может быть однократным или ступенчатым.
Однократное увлажнение глиняной м ассы при ее механической обработке осуществляют в смесителе, подавая распыленную воду. Время пребывания глиняной массы в смесителе при этом составляет всего несколько минут.
Чтобы обеспечить равномерную, влажность массы по всему ее объему, увлажнение следует производить в начале технологической линии. Смеситель устанавливают в начале технологической линии, одновременно производят увлажнение водой и паром. Вода должна быть направлена в первую половину смесителя (считая от загрузки), для того чтобы по всей его длине перемешивалась увлажненная масса.
При ступенчатом увлажнении добавляют некоторое количество воды в процессе переработки глиняной массы на бегунах и во втором смесителе, установленном непосредственно перед формующим агрегатом. Глину следует увлажнять горячей водой.
Паровое увлажнение.
При паровом увлажнении достигается более равномерное, чем при увлажнении водой, распределение влаги в глиняной массе, улучшаются ее формовочные и сушильные свойства. Масса прогревается до 45−500C, что снижает вязкость содержащейся в ней воды и облегчает ее продвижение из центра сырца к периферии.
Вследствие более равномерного увлажнения и набухания глины улучшаются ее пластические свойства, что повышает производительность прессов примерно на 10% и сокращает расход электроэнергии на 15−20%. 6]
Задачей процесса формования является получение брикета сферической формы из глинистой массы влажностью 18−23%. Предварительно процессу формования следует процесс подготовки глиняной массы, что в свою очередь во многом предопределяет качество брикета. При смешении глинистые массы претерпевают глубокие физикохимические превращения в контакте с водой. Вокруг частицы глины образуются водяные оболочки, препятствующие непосредственному сближению частиц. Такую структуру называют коагуляционной, она обуславливает пластичность и ползучесть массы при приложенных малых напряжений сдвига. Коагуляционная структура тиксотропна: она может быть разрушена механическим путем, но в состоянии покоя такая структура возникает вновь.
При уменьшении содержания жидкости в системе глина-вода коагуляционная структура переходит в конденсационную. При прибавлении воды снова образуется коагуляционная структура. Конденсационная структура является жесткой. Глинистые массы в этом состоянии плохо прессуются. Толщина водных оболочек и их свойства определяются коллоидно-химическими свойствами глин. [2]
2. ТЕХНОЛОГИЧЕСКОЕ ОБЕСПЕЧЕНИЕ ПРОИЗВОДСТВА
2.1 Расчет состава глиняного брикета Проектируемое производство специализируется на выпуске брикета для рядового шамота марки ШГР-28, которое будет осуществляться на основе глины Латненского месторождения марки ЛТ-3, химический состав которой представлен в таблице 8.
Таблица 8 — Химический состав глины ЛТ-3, %
Наименование | Содержание оксидов | Сумма | ||||||||||
Si02 | А1203 | Fe203 | ТiО2 | MgO | СаО | Na20 | К20 | SO3 | п.п.п. | |||
Глина ЛТ-3 | 56,96 | 25,52 | 2,5 | 1,6 | 0,23 | 0,41 | 0,19 | 0,33 | 0,06 | 12,28 | 100,08 | |
Произведем пересчет химического состава глины марки ЛТ-3 на 100%. Данные пересчета заносим в таблицу 9.
Химический состав глины соответствует химическому составу брикета рядового шамота.
Таблица 9 — Химический состав глиняного брикета
Наимено-вание | Содержание оксидов, % | Сумма | ||||||||||
Si02 | А1203 | Fe203 | ТiО2 | MgO | СаО | Na20 | К20 | SO3 | п.п.п. | |||
брикет | 56,91 | 25,50 | 2,5 | 1,60 | 0,23 | 0,41 | 0,19 | 0,33 | 0,06 | 12,27 | ||
Вывод: Выбранное сырье позволяет получить полуфабрикат для производства рядового шамота марки ШГР-28 в соответствии ТУ 1518−020−188 162−97.
2.2 Расчет производства Материальный баланс производства составляется по всем переделам от склада готовой продукции до склада сырья, с целью определения количества материалов, подлежащих переработке на каждом участке производства. По данным материального баланса определяем общий объем расхода сырьевых материалов на определенных стадиях производства.
Расчет производства ведется в соответствии с технологической схемой производства сортового шамота.
Расходные нормативы производства представлены в таблице 10.
Таблица 10 — Расходные нормативы производства
Расходные статьи | Норма, % | |
1. Влажность кускового шамота 2. Потери при транспортировке в бункера 3. Удаление п.п.п. из брикета при обжиге 4. Удаление влаги при обжиге 5. Потери массы при брикетировании 6. Пылеунос из шахтной печи 7. Потери массы при смешении 8. Доувлажнение массы при смешении 9. Потери глины при дроблении 10. Потери глины при хранении | 0,2 11,18 0,1 3,0 0,2 1,0 0,3 0,3 | |
Расчет расхода сырья для производства 90 000 т/год шамота.
1. Определим годовую производительность цеха с учетом потерь
шамота при транспортировке в расходные бункера:
т/год Потери при транспортировке составят:
90 180 — 90 000 = 180 т/год
2. Определим потребное количество брикета загружаемого в печь
с учетом удаления п.п.п. при обжиге:
т/год Удаление п.п.п. составят:
102 710 — 90 108 = 12 602 т/год
3. Определим количество брикета загружаемого в печь с учетом
удаления влаги:
т/год Удаление влаги составит:
130 012 — 102 710 = 27 302 т/год
4. Определим потребность в брикете на обжиг с учетом пылеуноса из шахтной печи:
т/год Пылеунос составит:
134 033 — 130 012 = 4021 т/год
5. Определим потребность в брикете с учетом потерь массы при
брикетировании:
т/год
Технологическая схема производства рядового шамота
Склад сырья
Транспортировка
Дробление
Транспортировка
Смешение вода
Брикетирование
Транспортировка
Обжиг
Транспортировка
Склад шамота Потери массы при брикетировании составят:
134 167 — 134 033 = 134 т/год
6. Определим потребное количество массы с учетом потерь при смешении:
т/год Потери массы при смешении составят:
134 435 — 134 167 = 268 т/год
7. При смешении глина до увлажняется на 1%. До увлажнение составит:
т/год Количество глины, подаваемой на смешение, составит:
134 435 — 1344 = 133 091 т/год
8. Определим потребность в глине, подаваемой на дробление с
учетом ее потерь при дроблении:
т/год Потери глины при дроблении составят:
133 491 — 133 091 = 400 т/год
9. Определим потребность в кусковой глине с влажностью 20% с
учетом потерь при хранении на складе:
т/год Потери глины при хранении на складе составят:
133 892 -133 491 = 401 т/год
10. Расходный коэффициент кусковой глины на шамот составит:
Составляем материальный баланс производства. Данные материального баланса заносим в таблицу 11.
Таблица 11 — Материальный баланс производства
Приход | т/год | Расход | т/год | |
1. Глина кусковая 2. Техническая вода 4. Возврат брака при брикетировании (70%) 5. Возврат потерь глины при складировании (90%) | 133 892 93,8 360,9 | 1. Кусковой шамот 2. Потери шамота при транспортировке в расходные бункера 3.Удаление влаги из брикета 4.Удаление п.п.п. из брикета 5.Пылеунос из печи 6. Потери при брикетировании (30%) 7. Потери при смешении 8. Потери глины при дроблении 9. Потери глины при складировании (10%) | 90 000 27 302 12 602 4 021 40,2 40,1 | |
Всего: | 135 690,7 | Всего: | 134 853,3 | |
Рассчитаем невязку производства Н, по формуле:
(1)
где П — приход производства, т/год;
Р — расход производства, т/год.
2.3 Подбор оборудования Ритмичная работа проектируемого участка производства сортового шамота обеспечивается на основе установки надежного производственного оборудования, увязанного в едином технологическом потоке. Заданное производство проектируется с учетом современных требований к промышленному оборудованию, обеспечивающему механизацию и автоматизацию технологических процессов.
Подбор оборудования произведен в соответствии с технологической схемой участка смесительно-формовочного отделения.
Ленточный конвейер
Двухвальный смеситель
Пресс-вальцы
Ленточный конвейер Баланс работы оборудования представлен в таблице 12.
Таблица 12- Баланс работы оборудования
Наименование показателей | Значения | |
1. Календарный фонд рабочего времени, дни 2. Капитальный и текущий ремонт, дни 3. Продолжительность работы оборудования, час 4. Продолжительность работы оборудования в сутки, час 5. Продолжительность работы оборудования в год, час | 7,6 22,8 | |
Дробленную глину ленточным конвейером транспортируют в двухвальный лопастной смеситель, где происходит одновременно её смешение и до увлажнение. Перемешанная глина подают в пресс-вальцы, в которых происходи формование брикета. Отформованный брикет должен иметь гладкую, чистую поверхность без заусенцев. После формования ленточным конвейером брикет направляется на элеватор.
Ленточный конвейер состоит из приводной станции, натяжной станции, металлической рамы, на которой смонтированы опорные ролики и лента, которая выполняет одновременно функции тягового и несущего органов. Угол наклона транспортера, во избежание скатывания или скольжения материала вниз вдоль ленты, рекомендуется принимать до 180.
Техническая характеристика ленточного конвейера представлена в таблице 13.
Процесс перемешивания является одной из основных и ответственных операций производства шамота. Он происходит в двухвальном лопастном смесителе с пароувлажнением марки СМК-18.
Таблица 13- Техническая характеристика ленточного конвейера
Наименование показателей | Величина | |
Ширина ленты, мм Производительность, т/час Скорость ленты, м/с Мощность, кВт | 400−500 0,8 2,7 | |
Двухвальный смеситель крепится на двух стойках — кронштейнах, на которых установлены подшипники, в которых расположены два параллельных горизонтальных вала. На этих валах укреплены расположенные по винтовой линии лопасти. Валы помещены в металлический корпус (корыто), имеющий с одного конца входное отверстие, куда дозирующим питателем подается глина, а с другого конца выходное отверстие для выгрузки готовой массы.
При вращении валов лопасти перелопачивают массу и продвигают её от загрузочного конца к выходному. Процесс перемешивания продолжается обычно 2−3 минуты. Привод одного из валов осуществляется от электродвигателя через редуктор. Второй вал получает вращение от первого через пару шестерен. Пар поступает в смеситель через щели.
Техническая характеристика двухвального лопастного смесителя представлена в таблице 14. 7]
Таблица 14 — Техническая характеристика двухвального лопастного смесителя марки СМК — 18
Наименование показателей | Величина | |
Длина корыта, мм Ширина корыта, мм Угловая скорость лопастных валов, об/мин Производительность, т/ч Мощность электродвигателя, кВт Масса, кг | ||
Рассчитываем необходимое количество двухвальных смесителей.
Потребная производительность двухвальных смесителей составит:
т/ч Количество смесителей составит:
Принимаем к установке 2 двухвальных лопастных смесителя.
Для обжига в шахтных печах глину брикетируют на пресс-вальцах брикетами массой около 2 кг. Значительно меньших размеров брикет готовят из высокоглиноземистых материалов с добавкой низкоспекающихся пластичных глин для обжига во вращающихся печах.
Основной рабочей частью пресс-вальцов, определяющей форму и размер брикета, являются вращающиеся навстречу друг другу валы с бандажами; на поверхности бандажей имеются полусферические углубления, совпадающие при вращении (рисунок 2).
Рисунок 2 — Валы пресс-вальцов для прессования брикетов со сферическими ячейками По течке масса направляется между валами пресс-вальцов, где, попадая в углубления, спрессовывается и выходит в форме сферических брикетов, которые по решетчатой наклонной течке попадают на транспортерную ленту и затем в вагонетку и — к загрузочному аппарату печи.
Благодаря высокой температуре и обдуву, которому подвергается брикет, проходя по решетчатой течке и транспортеру, он быстро подсыхает с поверхности и приобретает достаточную прочность для дальнейшего пути.
Обычно валы пресс-вальцов вращаются со скоростью 3,8—3,9 об/мин и на их бандажах размещается по 36 углублений; для обжига в шахтных печах применяют брикет массой в среднем 2 кг.
При этих условиях производительность вальцов составляет 16,4 т/ч. 4]
Определим необходимое количество пресс-вальцов.
Потребная производительность пресс-вальцов составит:
т/ч Количество шахтных печей составит:
Принимаем к установке 2 пресс-вальцов.
2.4 Двухвальный смеситель. Устройство, работа Лопастные смесители являются смесителями непрерывного действия с принудительным перемешиванием, отличаются простотой конструкции, большой производительностью и легкостью обслуживания.
Недостатки лопастных смесителей: не обеспечивается тщательное смешение компонентов и лопасти смесителя вгоняют воздух в смешиваемую массу, что ухудшает ее пластичность.
Смесители бывают однои двухвальные (более совершенные).
Двухвальные лопастные смесители при меньшей длине лучше смешивают материалы, чем одновальные. Они бывают с одинаковым и разным числом оборотов лопастных валов, прямоточные и противоточные, для перемешивания сухих и увлажненных материалов, с водяным и паровым увлажнением, с протирочной решеткой и без нее, без накопителя и с накопителем.
Советские ученые разработали и внедрили в производство метод увлажнения глиняных масс не водой, как обычно, а насыщенным паром низкого давления, который, конденсируясь, увлажняет и прогревает глину. Как показала практика, при пароувлажнении глиняные массы увлажняются более равномерно, формовочные свойства глины улучшаются, уменьшается свилеобразование, производительность формовочных прессов увеличивается на 10—12%, сокращается расход электроэнергии на формование до 20%.
Пароувлажнение глины осуществляется в лопастном смесителе марки СМК-18. В смесителе пар подается в пространство между основным 2 (рис. 3) и специально вмонтированным в смеситель чешуйчатым днищем 3 и поступает в смеситель через щели между пластинками чешуи. Щели высотой 2—3 мм расположены по всему днищу и боковым стенкам до уровня вала 6. Паровое пространство состоит из семи ячеек, в каждую из которых входят по два отростка 10 и 12 от паропроводящих трубок 11, соединенных с основным паровым коллектором 14. На каждой паропроводящей трубке имеется вентиль 13. Пар поступает в смеситель под давлением 0,04—0,05 МПа.
Рисунок 3 — Двухвальный лопастной смеситель СМК-18 с пароувлажнением Для отвода конденсата и отстоя грязи в нижней части корыта в смесителе СМК-18 установлено шесть конденсационных горшков (грязевиков) 1 с крышками 5 и труба 4. Снизу до уровня вала смеситель изолируют шлаковатой или асбестом, помещаемым в кожух 9. Смеситель закрывают крышкой со смотровым окном. Лопастные валы 6 и 15 приводятся во вращение от электродвигателя 8 через редуктор 7 и пару цилиндрических шестерен.
Кроме того, в приводе установлены две муфты — одна фрикционная и одна уравнительная. На каждом валу установлено по 22 лопасти под углом 65° к оси. В зависимости от свойств массы и технологических особенностей угол установки лопастей можно менять.
Масса смесителя уменьшена с 6,6 до 4,6 т. 7]
2.5 Охрана окружающей среды Технологический процесс получения шамота основан на термической обработке измельченного сырья, которое в значительной мере теряется с отходящими газами и выбросами. Поэтому пылеулавливающие установки являются неотъемлемой частью технологического процесса. К пылеулавливающим аппаратам относятся одиночные циклоны ЦН-15, сухие и мокрые циклоны СИО. Технологическое оборудование относящие современными рукавными фильтрами типа ФА, ФРЦИЭ, ФРКН. Выбросы вредных веществ в атмосферу по сравнению с ранее существующим производством сократились более чем в 10 раз.
Насосная станция технологического водозабора из реки Дон, для предотвращения попадания рыб, оборудовано рыбозащитным устройством — горизонтальной фильтрующей кассетой, запасенной гранитным щебнем ежегодно, специализированными организациями проводится подводное обследования устройства, а при необходимости его ремонта.
Эффективная работа пылеулавливающего оборудования подтверждается инструментальными замерами качества атмосферного воздуха в зоне влияния промышленных выбросов, проводимыми ежемесячно Центром Санэпиднадзора в Семилукском районе. Поданным этих замеров на протяжении последних 5−6 лет превышения ПДК атмосферного воздуха углерода, диоксидов серы и азота, фенола не наблюдалась.
Квалификация и опыт работы персонала обеспечивают проведение измерений в соответствии с областью оценки состояния измерений. Для каждого специалиста: имеются должностная инструкция, устанавливающая функции, права, обязанности и ответственность.
Для выполнения функции и реализации прав, предусмотрено лаборатория охраны окружающей среды. Со всеми подразделениями и техническими подразделениями по вопросам: нормативно-механической документации для организации и проведения контроля производственных факторов, выбросов, эффективности работы аспирационных и вентиляционных систем; документов и материалов необходимых для оформления и получения разрешения на выброс вредных веществ, для проведения инвентаризации источников выбросов вредных веществ в атмосферу; сведения о разработки планов природоохранных мероприятий; сведения о разработки проектов ПДВ, СЗЗ; сведения о проведения аттестации рабочих мест по условиям труда; сведения об образовании, размещении и вывозов отходов на утилизацию.
Сотрудники ЛООС несут ответственность за правильность проведения измерений, объективность, достоверность, полученных результатов, за выполнения установленных сроков проведения контроля, за выполнение соответствующих конкретных функций и обязанностей, регламентируемых должностными инструкциями, а также за выполнения других обязанностей, предусмотренных настоящим положением. [8]
ЗАКЛЮЧЕНИЕ
Курсовой проект на тему: «Проект усовершенствования технологии изготовления брикета для рядового шамота. Р=90 000 т/год» выполнен в соответствии с заданием и содержит все необходимые разделы.
В ходе выполнения курсового проекта было установлено, что приготовление шамота имеет одно из важнейших значений при производстве шамотных огнеупоров. В связи с этим к шамоту предъявляются высокие технические требования.
Анализ службы шамотных изделий показал, что рассматриваемая технология производства позволяет с высокой эффективностью использовать огнеупоры на основе шамота в соответствующих отраслях народного хозяйства.
Для получения качественного шамота необходим подбор соответствующего сырья, в качестве которого была выбрана глина Латненского месторождения марки ЛТ-3. Такой выбор позволяет получить шамот для производства изделий общего назначения марки ША.
В технологической части произведен расчет химического состава брикета, который обеспечивают изготовление шамота марки ШГР-28 по ТУ 1518−020−188 162−97.
Так же был выполнен расчет материального баланса производства, расходный коэффициент сырья составил 1,48, произведен подбор основного технологического оборудования, необходимого для обеспечения высокой производительности участка термической обработки брикета, рассмотрено устройство и принцип работы шахтной печи.
Рассмотрен вопрос об охране окружающей среды на производстве.
СПИСОК ИСПОЛЬЗУЕМОЙ ЛИТЕРАТУРЫ Аристов Г. Г. Шамотное производство. М.: Металлургия, 1975 -280с.
Будников П. П. Химическая технология керамики и огнеупоров. М. Металлургия, 1979 — 547с.
Девисимов В. А. Охрана окружающей среды, М.: Форум-Инфра-М, 2007, 98с.
Ильевич А. П. Машины и оборудование для заводов по производству керамики и огнеупоров, М.: Высшая школа, 1979 — 342с.
Стрелов В.Г., Кащеев И. Д. Технический контроль производства огнеупоров, М., Металлургия, 1986 — 214с.
Стрелов К.К., Мамыкин П. С. Технология огнеупоров, М.: Металлургия, 1978 — 376с.
Стрелов К.К., Мамыкин П. С, Кащеев И. Д. Технология огнеупоров, М.: Металлургия, 1988 — 528с.
8. Стрелов К. К. Теоретические основы технологии огнеупорных материалов, М.: Металлургия, 1985 — 321с.
ССЫЛКИ
[1]. Стрелов К. К., Мамыкин П. С. Технология огнеупоров, М.: Металлургия, 1978, с. 96−104.
[2]. Стрелов К. К. Теоретические основы технологии огнеупорных материалов, М.: Металлургия, 1985, с. 35−43.
[3]. Будников П. П. Химическая технология керамики и огнеупоров. М. Металлургия, 1979 — 547с
[4]. Аристов Г. Г. Шамотное производство. М.: Металлургия, 1975, с. 5−10,33−37.
[5]. Стрелов В. Г., Кащеев И. Д. Технический контроль производства огнеупоров, М., Металлургия, 1986, с 12,13.
[6]. Стрелов К. К., Мамыкин П. С, Кащеев И. Д. Технология огнеупоров, М.: Металлургия, 1988, с. 98,100−106.
[7]. Ильевич А. П. Машины и оборудование для заводов по производству керамики и огнеупоров, М.: Высшая школа, 1979, с. 148−153.
[8]. Девисимов В. А. Охрана окружающей среды, М.:Форум-Инфра-М, 2007, с.44−46