Металловедение и термообработка
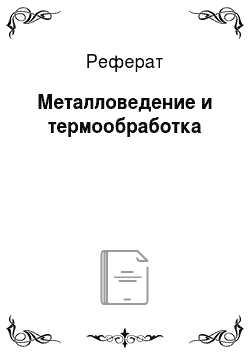
Перлитное превращение. Перлитная область распространяется на интервал температур от критической точки Л! до изгиба С-кривой (-550В° С). Распад аустенита с образованием перлита (эвтектоидный распад) является диффузионным процессом и развивается в результате флуктуации состава (неоднородности в распределении углерода в аустените). Перед распадом углерод диффундирует внутри аустенита (рис. 6, а… Читать ещё >
Металловедение и термообработка (реферат, курсовая, диплом, контрольная)
Задание Построить диаграмму изотермического распада аустенита с указанием структур. Превращение П—-А. Условия протекания этого процесса и его природа. Фазы, участвующие в прекращении. Кинетика этого процесса Что такое отжиг? Его разновидности, цели и основные параметры процесса Сталь 30А и У10. Охарактеризовать эти стали по:
- -качеству;
- -структуре в равновесном состоянии;
- -содержанию углерода;
- -назначению аустенит сталь термический отжиг
Рекомендовать термическую обработку стали. Как будет изменяться структура этой стали в процессе термической обработки? Свойства этой стали до и после рекомендуемой термической обработки. Чем отличаются структура и свойства стали после нормализации от структуры и свойств после рекомендуемой термической обработки Виды отпуска, назначение, структура и механические свойства стали после отпуска Ответ № 1.
Распад переохлажденного аустенита (диаграмма изотермического превращения аустенита). Распад аустенита может происходить только при температурах ниже 727В° С (критическая точка А1), когда свободная энергия аустенита выше свободной энергии продуктов его превращения (см. рис. 1). Следовательно, для распада аустенит должен быть переохлажден. От степени переохлаждения, т. е. от температуры, при которой происходит распад аустенита, зависят скорость превращения и строение продуктов распада аустенита. Закономерности этого процесса характеризуются диаграммой изотермического превращения аустенита, т. е. распадом аустенита при постоянной температуре.
Рис. 1. Изменение свободной энергии аустенита и перлита в зависимости от температуры.

Если нагретую до состояния аустенита сталь быстро охладить до температуры ниже температуры в критической точке А1 и затем выдержать при данной температуре, то превращение аустенита в феррито-цементитную смесь будет проходить в течение определенного времени. Такой процесс превращения аустенита при постоянной температуре (изотермический процесс) можно охарактеризовать зависимостями, приведенными на рис. 11. После охлаждения стали до температуры t ниже температуры в критической точке А1 аустенит сохраняется нераспавшимся некоторое время (отрезок о-а на рис. 2, а). Этот период времени называется инкубационным периодом. По истечении инкубационного периода начинается распад аустенита на феррито-цементитную смесь. С течением времени аустенит распадается все больше (отрезок а-б). Полный распад аустенита заканчивается по истечении времени, равного отрезку а-в (рис. 2, б). Следовательно, для распада аустенита на феррито-цементитную смесь при какой-то определенной температуре требуется определенное время.
Рис. 2. График (а) и кинетическая кривая (б) изотермического превращения аустенита.

Кривые изотермического распада переохлажденного аустенита приведены на рис. 3. Кривая превращения аустенита в ферритоцементитную смесь при температуре t1 более низкой, чем температура А1 приведена на рис. 3, а. При температуре t2 более низкой, чем температура t1 уменьшается время как инкубационного периода, так и распада аустенита на феррито-цементитную смесь (рис. 3, б), что объясняется увеличением разности свободных энергий аустенита и перлита (фактор, ускоряющий превращение), а скорость диффузии хотя и снижается (фактор, замедляющий превращение), но еще достаточно велика.
Рис. 3. Кинетические кривые изотермического превращения аустенита при различных температурах.

При температуре t3 это время наименьшее, аустенит наименее устойчив и распад его происходит наиболее быстро (рис. 3, в). С понижением температуры ниже температуры t3 (при температурах t4 и t5) время инкубационного периода и время распада аустенита на ферритоцементитную смесь увеличивается (рис. 3, г и д), что объясняется малой скоростью диффузии. Таким образом, с понижением температуры (т. е. с повышением степени переохлаждения) от А1 до t3 время как инкубационного периода, так и распада аустенита на феррито-цементитную смесь уменьшается, а затем с понижением температуры ниже t3 увеличивается.
По экспериментальным кривым, полученным для многих температур переохлаждения (t1 t2 и т. д.), можно построить диаграмму изотермического превращения аустенита.
Построение такой диаграммы производится следующим образом. Экспериментальные кривые (см. рис. 3) совмещают на одной диаграмме (рис. 4, а). По осям координат диаграммы (рис. 4, б) откладывают время (ось абсцисс) и температуру распада аустенита (ось ординат). В связи с тем, что время распада аустенита может изменяться от нескольких секунд до нескольких часов, для удобства построения применяется логарифмическая шкала времени (In ф).
Затем проводят линии, соответствующие температуре в точке A1 и температуре начала мартенситного превращения (точка Мн *). Точки, а (начала распада аустенита) и б (окончания распада) для каждой температуры превращения переносят на соответствующие горизонтали температур. Затем точки a1 а2 и т. д. соединяют, в результате чего получается левая кривая диаграммы. После переноса и соединения точек б1, б2 и т. д. получается правая кривая диаграммы.

Рис. 4. Схема построения диаграммы изотремического превращения аустенита.
Получившиеся кривые похожи на русскую букву С, поэтому их и называют С-кривыми. Левая кривая характеризует начало распада, а правая — окончание распада аустенита на феррито-цементитную смесь. В области между вертикальной осью и левой кривой аустенит находится в переохлажденном состоянии (инкубационный период). Приведенная на рис. 4, б диаграмма изотермического распада аустенита характерна для эвтектоидной стали. Если заменить условно обозначенные температуры конкретными д анными, то такая диаграмма будет иметь вид, приведенный на рис. 5.
Рис. 5. Диаграмма изотермического превращения аустенита эвтектоидной стали.

В зависимости от степени переохлаждения аустенита различают три температурные области превращения:
- — перлитную,
- — промежуточного превращения,
- — мартенситную.
Перлитное превращение. Перлитная область распространяется на интервал температур от критической точки Л! до изгиба С-кривой (-550В° С). Распад аустенита с образованием перлита (эвтектоидный распад) является диффузионным процессом и развивается в результате флуктуации состава (неоднородности в распределении углерода в аустените). Перед распадом углерод диффундирует внутри аустенита (рис. 6, а) и скапливается в определенных местах, прежде всего на границах зерен аустенита, в результате чего образуются зародыши цементита (рис. 6, б). Рост зародышей цементита происходит из-за диффузии углерода из прилегающего аустенита, что приводит к обеднению углеродом аустенита, окружающего образовавшиеся пластинки цементита, и способствует превращению его в феррит.
Поэтому рядом с пластинками цементита образуются пластинки феррита (рис. 6, е). Дальнейшее утолщение ферритных пластинок ведет к обогащению окружающего аустенита углеродом, что приводит к зарождению новых пластинок цементита (вдоль границы аустенита) или к росту уже имеющихся. Таким образом, возникают участки перлита, называемые перлитными колониями, в которых пластинки цементита и феррита расположены параллельно.
Рис. 6. Последовательные стадии образования перлитных зерен в зерне аустенита (схема).

При дальнейшем росте перлитной колонии эти пластинки удлиняются (краевой рост) и присоединяют новые пары пластинок (цементита и феррита), параллельные исходным (боковой рост, рис. 6, г и д). При краевом росте вблизи фронта распада АБ аустенит неоднороден: у торца цементитной пластинки концентрация углерода низкая, а у торца ферритной пластинки — высокая. Такой перепад концентраций в аустените обеспечивает диффузионный перенос углерода вдоль фронта распада путем его диффузии в аустените от мест обогащения возле феррита к местам обеднения возле цементита, что обеспечивает продолжение роста пластинок цементита и феррита. Такой процесс роста (краевого и бокового) перлитных колоний происходит до их столкновения, срастания и превращения всего аустенита в перлит (рис. 6, е).
Ответ № 2.
Отжиг — вид термической обработки металлов и сплавов, заключающийся в нагреве до определённой температуры, выдержке и последующем, обычно медленном, охлаждении. При отжиге осуществляются процессы возврата (отдыха металлов), рекристаллизации и гомогенизации. Цели отжига — снижение твёрдости для повышения обрабатываемости, улучшение структуры и достижение большей однородности металла, снятие внутренних напряжений.
По классификации А. А. Бочвара различают 2 вида отжига:
Отжиг 1-го рода — без фазовой перекристаллизации — применяется для приведения металла в более равновесное структурное состояние: снимается наклёп, понижается твёрдость, возрастают пластичность и ударная вязкость, снимаются внутренние напряжения (в связи с процессами отдыха и рекристаллизации).
Отжиг 2-го рода осуществляется с фазовой перекристаллизацией: сталь нагревается до температуры выше критических точек, затем следует выдержка различной продолжительности и последующее сравнительно медленное охлаждение.
Полный и неполный отжиг:
Полный отжиг заключается в нагреве стали на 30—50 °C выше верхней критической точки для полного превращения структуры стали в аустенит и последующем медленном охлаждении до 500—600 °C для образования феррита и перлита. Скорость охлаждения для углеродистых сталей около 50—100 °C/ч. Если охлаждение ведётся на воздухе, происходит нормализация.
Неполный отжиг заключается в нагреве до температур между нижней и верхней критическими точками и последующем медленном охлаждении.
Изотермический отжиг:
Для легированных сталей применяют изотермический отжиг, состоящий в нагреве выше верхней критической точки А3 область избыточного аустенита, выдержке, охлаждении до температуры ниже нижней критической точки А1, выдержке, достаточной для полного превращения аустенита в перлит, и охлаждении до комнатной температуры.
Диффузионный отжиг:
Диффузионный отжиг состоит в нагреве до температур, значительно превосходящих критические точки, и продолжительной выдержке; используется для выравнивания неоднородностей распределения элементов по объёму изделия. Диффузионный отжиг приводит к достижению более однородных свойств по объёму изделия и особенно улучшению механических свойств в поперечном (по отношению к прокатке) направлении. В необходимых случаях для предотвращения обезуглероживания стали производят отжиг в защитных атмосферах.
Температура нагрева зависит от температуры плавления Тн = 0.7−0.8 Тпл Рекристаллизационный отжиг:
Рекристаллизационный отжиг — нагрев до температуры на 100−200 °C выше температуры рекристаллизации, выдержка и последующее охлаждение. Вследствие процесса рекристаллизации происходит снятие наклепа, и свойства металла соответствуют равновесному состоянию Гомогенизационный отжиг:
Гомогенизационный отжиг — термообработка литого материала, обеспечивающая получение равновесной структуры. При гомогенизационном отжиге идут следующие процессы:
- -выравнивание химического состава до равновесного;
- -растворение избыточных фаз;
- -выделение фаз из пересыщенного твердого раствора — особый случай — гетерогенизация во время гомогенизации, наблюдается в алюминиевых сплавах, содержащих хром, цирконий и скандий;
- -рост зерна;
- -образование и рост пор.
Методы выполнения гомогенизационного отжига:
При начале гомогенизационного отжига сначала растворяются самые легкоплавкие эвтектики (тройные, четверные), потом нагревают до двойной эвтектики, а затем нагревают под температуру метастабильного солидуса. Основная задача — сократить время обработки. Для этого нужно нагреть на возможно более высокую температуру. При этом материал не должен испытывать:
- -перегрева — чрезмерного роста зерен,
- -пережога — окисления границ зёрен.
Высокотемпературная гомогенизация:
Нагревать до температуры между температурами метастабильного и стабильного солидуса, заранее обрекая материал на частичное расплавление. Если объем легкоплавких фаз менее 1%, то эта жидкость позднее рассосется, и влияния на свойства не окажет.
Синеломкость:
Синеломкость — снижение пластичности стали при одновременном повышении прочности, наблюдаемое при деформации в интервале температур, вызывающих синий цвет побежалости (200—300 °C).
Ответ № 3.
Отпуском называется нагрев закаленной стали до температур ниже критической точки Ас1 выдержка при этой температуре с последующим охлаждением (обычно на воздухе). Отпуск является окончательной термической обработкой. Целью отпуска является изменение строения и свойств закаленной стали: повышение вязкости и пластичности, уменьшение твердости, снижение внутренних напряжений.
С повышением температуры нагрева прочность обычно уменьшается, а удлинение, сужение, а также ударная вязкость растут (рис. 1). Температуру отпуска выбирают, конкретной детали.

Рис 1. Влияние температуры отпуска на механические свойства стали с 0,4% С
В зависимости от температуры нагрева различают три вида отпуска:
- -низкотемпературный,
- -среднетемпературный
- -высокотемпературный.
При низкотемпературном отпуске закаленную сталь нагревают до 150—250 °С. После выдержки при этой температуре (обычно 1—3 ч) в детали получают структуру отпущенного (кубического) мартенсита При низком отпуске частично снимаются закалочные напряжения. Если в стали было значительное количество остаточного аустенита, то в результате его превращения в кубический мартенсит твердость после низкого отпуска может увеличиться на 2—3 единицы и HRC.
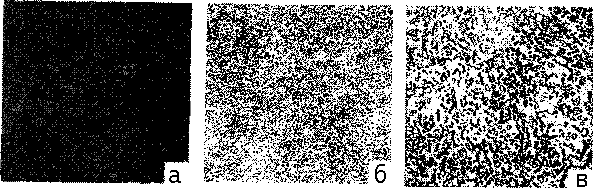
Рис. 2. Структура закаленной стали после различных видов отпуска, Х500: a — среднетемпературного (350−400 °С, бейнит); б — высокотемпературного (450 — 600 °C, сорбит); в — 650—700 °С
Низкий отпуск применяют для инструментальных сталей после цементации, поверхностной закалки и т. д. При среднетемпературном отпуске закаленную сталь нагревают до 350—400 °С. В результате получается структура троостита (бейнит). После такого отпуска в изделиях получается сочетание сравнительно высокой твердости (НRС 40— 45) и прочности с хорошей упругостью и достаточной вязкостью поэтому среднему отпуску подвергают пружины и рессоры.
При высокотемпературном отпуске закаленные изделия нагревают до 450—650 °С. После такого нагрева и соответствующей выдержки в изделиях получается структура сорбита. В отличие от сорбита, образующегося после нормализации, когда цементит пластинчатый, после высокого отпуска цементит приобретает зернистую форму (рис. 2, б). Это существенно повышает ударную вязкость при одинаковой (или даже более высокой) твердости по сравнению с нормализованной сталью. Поэтому такой отпуск применяют для деталей машин, испытывающих при эксплуатации ударные нагрузки. Закалку с высоким отпуском часто называют улучшением. При нагреве 650—700 °С получают структуру зернистого перлита (рис. 2, в). Поскольку в легированных сталях все диффузионные процессы протекают медленнее, время выдержки при отпуске таких сталей больше по сравнению с углеродистыми. Кроме того, карбидообразующие элементы замедляют коагуляцию карбидов, в результате чего они сохраняются мелкодисперсными до более высоких температур. Это одна из причин наблюдающегося явления так называемой вторичной твердости, т. е. увеличения твердости после отпуска в интервале 500— 600 °C (наблюдается в сталях, легированных хромом, молибденом, ванадием и некоторыми другими элементами).
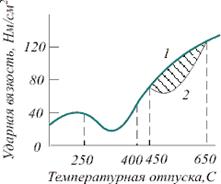
Рис. 3. Влияние температуры отпуска на ударную вязкость стали с высокой восприимчивостью к отпускной хрупкости:1 — быстрое охлаждение в воде или масле; 2 — медленное охлаждение.
Поэтому в результате высокотемпературного отпуска при одной и той же температуре, а следовательно, при одной и той же структуре, легированные конструкционные стали имеют более высокую прочность и пластичность, чем углеродистые. Это и является одной из основных причин применения легированных сталей для изготовления деталей ответственного назначения, испытывающих сложные напряжения при эксплуатации.
Обычно ударная вязкость с температурой отпуска увеличивается, а скорость охлаждения после отпуска не влияет на свойства. Но для некоторых конструкционных сталей наблюдается уменьшение ударной вязкости (рис. 3). Этот дефект называется отпускной хрупкостью. Различают отпускную хрупкость I и II рода.
Отпускная хрупкость I рода наблюдается при отпуске в области 300 °C у легированных, а также углеродистых сталей. Не зависит от скорости охлаждения. Это явление связывают с неравномерностью превращений отпущенного мартенсита. Процесс протекает быстрее вблизи границ зерен по сравнению с объемами внутри зерна. Благодаря этому вблизи границ создаются концентрации напряжений, границы становятся хрупкими. Отпускная хрупкость I рода «необратима», т. е. при повторных нагревах тех же деталей она в них не наблюдается.
Отпускная хрупкость II рода наблюдается у легированных сталей при медленном охлаждении после отпуска в области 450— 650 °C (штриховая линия на рис. 3). Существует несколько объяснений природы этого дефекта. Рассмотрим наиболее распространенное. При высоком отпуске по границам зерен происходит образование и выделение дисперсных включений карбидов. Приграничная зона обедняется легирующими элементами. При последующем медленном охлаждении происходит восходящая диффузия фосфора из внутренних объемов зерна к границам. Приграничные зоны зерна обогащаются фосфором, прочность границ понижается, ударная вязкость падает. Этому дефекту способствуют хром, марганец и фосфор (>0,001%). Уменьшают склонность к отпускной хрупкости II рода молибден и вольфрам (до 0,5%) и быстрое охлаждение после отпуска (сплошная линия на рис.3). Отпускная хрупкость II рода «обратима», т. е. при повторных нагревах и медленном охлаждении тех же сталей в опасном интервале температур этот дефект может повториться. Поэтому стали, склонные к отпускной хрупкости II рода, нельзя использовать для работы с нагревом до 650 °C без последующего быстрого охлаждения (например, штампы для горячей штамповки).
Ответ № 4.
Сталь У10 Сталь инструментальная углеродистая Углерод (С) — 1%.
Применение: инструмент, работающий в условиях, не вызывающих разогрева режущей кромки: метчики ручные, рашпили, надфили, пилы для обработки древесины, матрицы для холодной штамповки, гладкие калибры, топоры.
Химический состав.
Химический элемент. | %. |
Кремний (Si). | 0.17 -0.33. |
Медь (Cu), не более. | 0.25. |
Марганец (Mn). | 0.17 -0.33. |
Никель (Ni), не более. | 0.25. |
Фосфор (P), не более. | 0.030. |
Хром (Cr), не более. | 0.20. |
Сера (S), не более. | 0.028. |
Структура в равновесном состоянии: перлит + цементит вторичный.
Достоинство углеродистых инструментальных сталей состоит в основном в их малой стоимости и достаточно высокой твёрдости по сравнению с другими инструментальными материалами. К недостаткам следует отнести малую износостойкость и низкую теплостойкость.
Рекомендованная термическая обработка:
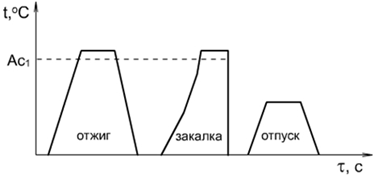
Отжиг заключается в нагреве изделия на 20 — 40° свыше критической точки (для заэвтектоидной стали), выдержке при этой температуре и последующем медленном охлаждении. Отжиг применяется неполный при температуре 750 — 770°. В состоянии нагрева структура представляет собой аустенит с частицами не растворившегося при этих температурах цементита.(перлит зернистый + цементит вторичный) (~HB 197).
Отжиг инструментальной стали производят в следующих случаях:
- -перед ковкой и прокаткой с целью измельчения и улучшения литой структуры и подготовки стали к ковке и прокатке;
- -после окончательной ковки заготовок для понижения твердости с целью улучшения обрабатываемости стали и для перекристаллизации и подготовки структуры стали к закалке;
- -после закалки и отпуска при необходимости произвести вторичную закалку инструмента для исправления брака во время термообработки при восстановлении изношенного инструмента и пр.;
- -после сварки, наварки и наплавки — для снятия напряжений и подготовки структуры стали к последующей закалке.
Закалка состоит в нагреве изделий до определенной температуры и последующем быстром охлаждении. Закалка инструментальной стали производится с целью получения наивысших режущих свойств — определенной высокой твердости и красностойкости стали. Закалка стали У10 проводиться при температуре 770−810°(неполная закалка) и среда охлаждения вода. В результате образуется структура мартенсита закалки и вторичного цементита.
Отпуск заключается в выдерживании стали при определенной температуре и последующем охлаждении. Доведение стали до температуры отпуска производятся или за счет внутреннего тепла, сохранившегося после закалки, или за счет внешнего нагрева. Отпуск применяют однократный и многократный. Отпуск стали должен проводиться немедленно после ее закалки. Цель отпуска — снятие значительных остаточных напряжений, возникающих в стали в процессе закалки и предупреждение образования трещин. Отпуск быстрорежущей стали, кроме этого, имеет целью, во-первых, перевести остаточный аустенит закаленной стали в мартенсит и повысить твердость стали до 62−65 Rс, во-вторых, перевести мартенсит, образующийся при закалке, в более вязкий мартенсит отпуска. Проводиться низкотемпературный отпуск 150−160°. Структура при этом мартенсит отпуска и цементит вторичный. Микроструктура мартенсита отпуска напоминает структуру мартенсита закалки, но отличается повышенной травимостью. (~HRC 63).
Сталь 30А высококачественная конструкционная сталь Углерод (С) — 0,3%.
Применение: изготовления самых разнообразных деталей машин. Тяги, серьги, траверсы, рычаги, валы, звездочки, шпиндели, цилиндры прессов, соединительные муфты и другие детали невысокой прочности.
Химический состав.
Химический элемент. | %. |
Кремний (Si). | 0.17 -0.37. |
Медь (Cu), не более. | 0.25. |
Мышьяк (As), не более. | 0.08. |
Марганец (Mn). | 0.50 -0.80. |
Никель (Ni), не более. | 0.25. |
Фосфор (P), не более. | 0.025. |
Хром (Cr), не более. | 0.25. |
Сера (S), не более. | 0.025. |
Структура в равновесном состоянии: феррит + перлит.
Качество конструкционных углеродистых сталей определяется наличием в стали вредных примесей фосфора (P) и серы (S). Фосфор — придаёт стали хладноломкость (хрупкость). Сера — самая вредная примесь — придаёт стали красноломкость. Содержание вредных примесей в стали.
Рекомендованная термическая обработка:
.

Отжиг состоит в нагреве сталей до определенной температуры, выдержке и затем очень медленном охлаждении, чаще всего вместе с горном или печью. Полный отжиг применяют с целью устранения дефектов структуры. Отжиг полный производиться при температуре 814−830° с последующим медленным охлаждением в остывающей печи. В этом случае происходит полная фазовая перекристаллизация стали и образуется равновесная структура, представляющая собой перлит и избыточный феррит (~HB 146).
Закалка состоит в нагреве углеродистых сталей, содержащих углерода до 0,8%, до температуры выше линии SG на 20…40 °С (см. рисунок), т. е. Ас3 + (20…40 °С), а сталей с содержанием углерода более 0,8% до температуры выше линии SK на 20…40°С, т. е. Лс, + (20…40 °С), выдержке при этих температурах и охлаждении в охлаждающей среде о соответствующей скоростью охлаждения. Производим полную закалку для стали 30А при температуре 830° с последующим охлаждением со скоростью выше критической в воде. Образуется структура мартенсит закалки. (~HB 600).
Отпуск состоит в нагревании закаленной стали до температуры ниже Ас1 (см. рисунок), выдержке при этой температуре некоторое время и быстрого или медленного охлаждения, как правило, на воздухе. В процессе отпуска в металле структурных изменений не происходит, однако уменьшаются закалочные напряжения, твердость и прочность, а пластичность и вязкость увеличиваются. В зависимости от марки стали и от предъявляемых к детали требований по твердости, прочности и пластичности применяют следующие виды отпусков. Проводим высокотемпературный отпуск при температурах 500 — 680° (~HRC 30). Образуется сорбит отпуска.
НОРМАЛИЗАЦИЯ СТАЛИ Нормализацией называют такой вид термической обработки, когда сталь нагревают на 30 — 50° выше верхних критических температур Асз или Аст и после выдержки при этих температурах охлаждают на спокойном воздухе. Таким образом, от отжига нормализация отличается более быстрым охлаждением изделия (примерно в 2 раза).
Нормализация является более дешевой операцией, чем отжиг, так как печи используются только для нагрева и выдержки изделия при температуре нагрева, а охлаждение производится вне печи. Кроме того, нормализация ускоряет процесс термической обработки. Таким образом, отжиг выгодно заменять нормализацией. Однако это не всегда возможно, так как у некоторых сталей твердость после нормализации возрастает более значительно, чем при отжиге. Малоуглеродистые стали рекомендуется подвергать нормализации, так как у них практически отсутствует разница в свойствах после отжига и нормализации.
Стали, содержащие свыше 0,4% углерода, после нормализации получают повышенную твердость. Такие стали лучше отжигать. На практике и такие стали часто подвергают нормализации вместо отжига, а затем высокому отпуску при температурах 650 — 700° для уменьшения твердости. Нормализацию применяют для получения мелкозернистой структуры в отливках и поковках, для устранения внутренних напряжений и наклепа, для подготовки структуры стали к закалке.
Для некоторых изделий нормализация является не предварительной, а окончательной операцией термической обработки. В этом случае после нормализации изделия подвергают высокому отпуску для снятия внутренних напряжений, образовавшихся при охлаждении изделия на воздухе.
В результате нормализации получают более тонкое строение эвтектоида (тонкий перлит или сорбит), уменьшаются внутренние напряжения, устраняются пороки, полученные в процессе предшествующей обработки. Твердость и прочность несколько выше чем после отжига.
В заэвтектоидных сталях нормализация устраняет грубую сетку вторичного цементита.
Нормализацию чаще применяют как промежуточную операцию, улучшающую структуру. Иногда проводят как окончательную обработку, например, при изготовлении сортового проката.