Разборка механизма автосцепки и неисправность полочки
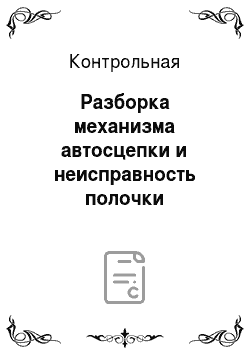
После ремонта и проверки клеймению подлежат: замок, замкодержа-тель, предохранитель, подъемник, валик подъемника, тяговый хомут, валик, клин тягового хомута, ударная розетка, балочка центрирующего прибора, маятниковые подвески, упорная плита, корпус поглощающего аппарата, собранная автосцепка, вкладыш и поддерживающая плита центрирующего прибора. Наплавка передней поверхности полочки Д, для… Читать ещё >
Разборка механизма автосцепки и неисправность полочки (реферат, курсовая, диплом, контрольная)
КОНТРОЛЬНАЯ РАБОТА ПО ДИСЦИПЛИНЕ «ТЕХНОЛОГИЯ ПРОИЗВОДСТВА И РЕМОНТА ВАГОНОВ»
На тему: «Разборка механизма автосцепки и неисправность полочки»
1. Назначение узла, его конструкция, процесс ремонта Назначение и типы автосцепного устройства. Автосцепное устройство относится к ударно-тяговому оборудованию вагона и предназначено для сцепления вагонов между собой и локомотивом, удержания их на определенном расстоянии друг от друга, восприятия передачи и смягчения воздействия растягивающих и сжимающих усилий, возникающих во время движения. От исправного состояния этого оборудования во многом зависит безопасность движения поездов.
Это оборудование относится к объединенным устройствам, где совмещаются все функции ударных и тягово-сценных приборов. До перевода подвижного состава железных дорог на автосцепку он оборудовался раздельными приборами, когда в качестве ударных приборов устанавливали буферные комплекты, а сцепных — винтовую упряжь. На каждом вагоне современной конструкции установлено два комплекта автосцепного устройства, размещенных, но концам вагонной рамы.
Автосцепное устройство четырехосных вагонов. Автосцепное устройство типа СА-3 грузовых вагонов размещается в консольной части хребтовой балки рамы кузова.
Рисунок 1 — Корпус автосцепки в сборе Корпус автосцепки с механизмом предназначен для сцепления и расцепления вагонов, восприятия и передачи ударно-тяговых усилий упряжному устройству. Корпус автосцепки (рис. 1) представляет собой пустотелую фасонную отливку, состоящую из головной части и хвостовика. Внутри головной части размещены детали механизма автосцепки. Она имеет большой 7 и малый 4 зубья, которые, соединяясь, образуют зев. Торцовые поверхности малого зуба и зева воспринимают сжимающие усилия, а тяговые усилия передаются задними поверхностями большого и малого зубьев. На вертикальной стенке зева возле малого зуба имеется окно для замка 3, а рядом — окно для замкодержателя 2. В верхней части головы отлит выступ 5, который воспринимает жесткий удар при полном сжатии поглощающего аппарата и передает его через розетку на раму вагона. Со стороны малого зуба внутри головы отлита полочка для верхнего плеча предохранителя замка от саморасцепа, а со стороны большого зуба имеется шип для навешивания замкодержателя. В нижней части головы выполнены отверстия для выступов замка автосцепки и горизонтальное отверстие для постановки валика подъемника. В пустотелом хвостовике сделано продолговатое отверстие 6 для клина, соединяющего корпус с тяговым хомутом. Торец хвостовика 7 служит для передачи ударных нагрузок и имеет цилиндрическую поверхность, обеспечивающую горизонтальные повороты автосцепки. Горизонтальная проекция зубьев, зева и выступающей части замка называется контуром зацепления.
Порядок разборки автосцепного устройства следующий:
1. Отгибают предохранительные шайбы с головки запорного болта и гайки.
2. Откручивают гайку и вытаскивают запорый болт.
3. Вытаскивают валик подъемника из отверстия в корпусе атосцепки.
4. Извлекают замок из корпуса и снимают с шипа замка предохранитель от саморасцепа.
5. Снимают с шипа в корпусе автосцепки и извлекают замкодержатель.
6. Извлекают подъемник замка.
Сборка автосцепного устройства производится в обратном порядке.
Перед сборкой необходимо осмотреть карман корпуса и убедиться, что в нем нет никаких посторонних предметов и приливы для деталей находятся в исправном состоянии.
2. Условия эксплуатации детали В эксплуатации полочка работает в условиях невысоких нагрузок и неблагоприятных воздействий окружающей среды (перепады температур, влияние атмосферных явлений, что приводит к коррозии).
Полочка предохранителя автосцепного устройства и силы на него действующие показаны на рисунке 2, где:
F — ударная нагрузка;
Fтр, Fтр, — силы трения действующие на полочку.
а) б) Рисунок 2 — Силы действующие на полочку предохранителя: а) в момент сцепления и при действии сжимающих сил; б) при расцеплении.
При действии силы тяги на полочку предохранителя не действует никаких сил.
3. Требования технических указаний и руководства по ремонту вагонов Грузовые вагоны колеи 1520 мм. Руководство по деповскому ремонту ЦВ-587:
Осмотр, ремонт и клеймение автосцепного устройства производится в соответствии с Инструкцией по ремонту и обслуживанию автосцепного устройства подвижного состава железных дорог Российской Федераций (приложение В).
Съемные узлы и детали автосцепного устройства: головки автосцепок, поглощающие аппараты, тяговые хомуты, центрирующие балочки, упорные и поддерживающие плиты, маятниковые болты, клинья тягового хомута снимают с вагонов и отправляют в ремонт.
Упорные угольники, розетки, расцепные рычаги, кронштейны расцепных рычагов осматривают, неисправные ремонтируют. Разрешается производить проверку к ударной розетке отбитых частей согласно технологической «Инструкции по сварке передних упоров», № 317 ПКБ ЦВ.
После ремонта и проверки клеймению подлежат: замок, замкодержа-тель, предохранитель, подъемник, валик подъемника, тяговый хомут, валик, клин тягового хомута, ударная розетка, балочка центрирующего прибора, маятниковые подвески, упорная плита, корпус поглощающего аппарата, собранная автосцепка, вкладыш и поддерживающая плита центрирующего прибора.
Детали, не имеющие маркировку предприятия-изготовителя, ремонту не подлежат и сдаются в металлолом.
Инструкция по ремонту и обслуживанию автосцепного устройства подвижного состава железных дорог от 31.09.97 № ЦВ-ВНИИЖТ-494:
Положение полочки для верхнего плеча предохранителя в корпусе относительно шипа для замкодержателя и контура зацепления проверяют шаблоном 834р (рис. 2), после того, как будет установлено, что шип для навешивания замкодержателя удовлетворяет требованиям проверки шаблонами 849р-1,806р и 816р.
Для проверки шаблон 834р нужно взять за основание б, ввести в карман корпуса и установить так, чтобы упоры 3 и выступы 4 были плотно прижаты к неизнашиваемой части ударной поверхности зева и внутренней стенке малого зуба, а прямоугольная опора 1 опиралась на шип для замкодержателя.
Рисунок 2 — Проверка положения полочки для верхнего плеча предохранителя относительно шипа для замкодержателя и контура зацепления автосцепки шаблоном 834р После такой установки шаблона положение полочки по вертикали проверяют поворотом стрелки 2, заостренный конец которой поднимают вверх до тех пор, пока ее задний конец не упрется в верхнюю поверхность полочки. Положение полочки по горизонтали проверяют с помощью движка 5, который передвигают до упора в переднюю кромку полочки. Если острие стрелки 2, опирающейся другим своим концом на рабочую поверхность полочки, располагается вне пределов обеих ступеней контрольного выреза б, значит положение полочки по вертикали неправильное (поз. А). Если указатель движка 5, упирающегося в полочку, располагается вне пределов обеих ступеней контрольного выреза г, то это указывает на неправильное положение полочки по горизонтали (поз. Б). Для правильного показания шаблона при проверке положения полочки по вертикали необходимо поворачивать стрелку 2 при полностью выдвинутом на себя движке 5, а положение полочки по горизонтали проверять при крайнем нижнем положении указателя стрелки 2.
Полочка, не удовлетворяющая требованиям проверки шаблоном 834р, должна быть отремонтирована или заменена новой.
Новую или отремонтированную полочку также проверяют шаблоном 834р, как описано выше. Но при этом предъявляются повышенные требования, а именно: положение полочки считается правильным, когда указатели стрелки и движка располагаются соответственно в пределах более глубоких вырезов, а и в.
Инструкция по сварке и наплавке при ремонте грузовых вагонов ЦВ-201−98:
Корпус автосцепки отливается из сталей 15ГЛ, 20Л, 20ГЛ, 20ФЛ по ГОСТ 977–88 или из сталей 20ГТЛ, 20ПФЛ, 20ФТЛ и 20ГФТЛ по ГОСТ 22 703–91.
При всех видах ремонта разрешается:
5) наплавка передней поверхности полочки Д, для верхнего плеча предохранителя и серповидного прилива в случае их износа или приварка серповидного прилива с полочкой в случае их излома. Перед приваркой полочка должна быть закреплена в правильном положении при помощи специального кондуктора. Подварка со стороны вершины угла разделки обязательна;
Рисунок 3 — Корпус автосцепки автосцепной вагон ремонт износ
4. Места износа и повреждений детали, их причины, способы обнаружения и устранения, допускаемые величины Таблица 1 — Места износа и повреждений детали, их причины, способы обнаружения и устранения, допускаемые величины
Место износа и повреждения | Причина износа и повреждения | Способ обнаружения | Способ устранения | Допускаемая величина износа, мм | Возможные последствия эксплуатации | ||
По инструкции ЦВ-ВНИИЖТ-494 | По инструкции ЦВ-201−98 | ||||||
1. Излом полочки для верхнего плеча предохранителя | При неиправности автосцепки | Визуально | Приваривают новую полочку. | Не допускается | Не допускается | Саморасцеп | |
2. Износ полочки для верхнего плеча предохранителя по вертикали | Естественный износ от взаимодействия с предохранителем. | Шаблон 834р | Наплавка изношенной поверхности | Остриё стрелки 2 должно находиться в пределах выреза б Износ 4 мм | Износ 7 мм | Саморасцеп | |
3. Износ полочки для верхнего плеча предохранителя по горизонтали | Тоже, что 2 | Шаблон 834р | Наплавка изношенной поверхности | Указатель движка 5, упирающегося в полочку располагается в пределах обеих ступеней контрольного выреза г Износ 7 мм | Износ 14 мм | Саморасцеп | |
5. Разработка технологической карты Таблица 2 — Технологическая карта
Технологическая карта | ||
Наименование операции | Наименование оборудование, приспособлений, инструмента | |
Контроль магнитопорошковый хвостовика корпуса автосцепки СА-3 | Поворотный стенд для закрепления корпуса автосцепки, кронштейн для подвешивания и перемещения соленоида вдоль хвостовика корпуса автосцепки; Дефектоскоп МД-12ПШ (длина зоны ДН — 120…160 мм); магнитные индикаторы | |
Подготовительные операции: 1. Очистить деталь от грязи, ржевчины, шлаков, смазки и других покрытий; 2. Осмотреть контролируемую поверхность с целью выявления видимых глазом дефектов. Операции контроля: 1. Закрепить корпус автосцепки на поворотном стенде так, чтобы одна из плоскостей хвостовика была расположена под углом не менее 10° к горизонтали. 2. Установить соленоид у перемычки под углом (35±5)° к оси хвостовика так, чтобы хвостовик частично входил в отверстие соленоида, включить соленоид. 3. Нанести суспензию на все открытые для осмотра поверхности хвостовика в зоне перемычки. 4. После стекания суспензии в течение 5…10 с, осмотреть поверхность перемычки и торец хвостовика, выключить соленоид. 5. Надеть соленоид на хвостовик в зоне перемычки, максимально приподняв его. 6. Включить соленоид. 7. Нанести суспензию в пределах зоны ДН на две верхние плоскости. 8. После стекания суспензии в течение 5…10 с, осмотреть две верхние плоскости в пределах зоны ДН. | ||
9. Медленно перемещать соленоид вдоль хвостовика, одновременно нанося перед ним суспензию на две верхние плоскости хвостовика. 10. Остановить соленоид, по возможности приблизив его к головке. 11. Нанести суспензию на участки, примыкающие к головке, включая переход от хвостовика к головке, и прекратить нанесение суспензии. 12. После стекания суспензии в течение 5…10 с осмотреть две верхние плоскости хвостовика, обращая внимание на зоны перехода от хвостовика к голове, выключить соленоид и вернуть его к перемычке. 13. Повернуть корпус автосцепки на 180° и повторить контроль по п. п. 6 — 12. | ||
6. Приспособления и инструмент Таблица 3 — Перечень приспособлений и инструмента
Магнитопорошковая дефектоскопия хвостовика корпуса автосцепки | ||||
Приспособление | Назначение | Инструмент | Назначение | |
Распылитель | Нанесение суспензии на контролируемую поверхность | Щетка волосяная | Очистка хвостовика | |
Лампа переносная, 12В | Освещение контролируемой поверхности | Лупа х4 | Выявление дефектов | |
1. Инструкция по сварке и наплавке при ремонте грузовых вагонов. ЦВ 201−98. М.: Транспорт, 1998.-255 с.
2. Грузрвые вагоны колеи 1520 мм. Руководство по деповскому ремонту ЦВ-587. — М.: Транспорт, 1999. — 155 с.
3. Инструкция по ремонту и обслуживанию автосцепного устройства подвижного состава железных дорог. ЦВ-ВНИИЖТ-494. — М.: Транспорт, 1999.-143с.
4. Магнитопорошковый метод неразрушающего контроля деталей вагонов. РД 32.159 — 2000. — М., 2000. — 120 с.
5. В. В. Коломийченко. Техническое обслуживание и ремонт автосцепного устройств подвижного состава железных дорог — М.: Трансинфо, 2004. — 192 с.