Другие работы
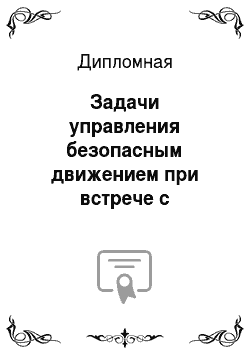
Поскольку динамическое программирование наиболее близко к получению оптимального управления в замкнутой форме, нужно подробнее остановиться на задаче синтеза систем автоматического управления, удовлетворяющего при существующих ограничениях требуемому качеству. Одним из направлений в этой области является разработанный у нас в стране А. М. Летовым подход, названный аналитическим конструированием…
Дипломная 
Интенсификация промышленного производства в ряде отраслей народного хозяйства страны непосредственно определяется новыми высокоэффективными электротехнологиями. К их числу относятся плазменные процессы в химической, металлургической, машиностроительной и других областях производства. Источниками высокотемпературных потоков, в силу простоты оборудования и возможности автоматизации технологических…
Диссертация 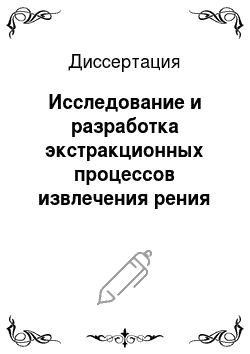
Тем не менее, в условиях промышленно-сырьевой базы России имеются потенциальные сырьевые источники этого стратегического металла. В частности, перспективным сырьевым ресурсом первичного рения являются отходы пылегазоочистки медно-никелевого производства. Несмотря на относительно низкое содержание рения в сульфидных медно-никелевых рудах, значительные объемы их переработки позволяют рассматривать…
Диссертация 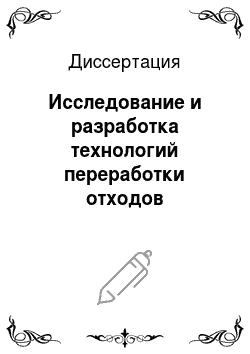
С использованием методов планирования эксперимента сформированы полиномиальные и мультипликативные уравнения регрессии, аппроксимирующие электрическую проводимость раствора электролита между двумя электродами в цилиндрическом сосуде с непроводящими стенками как функции многих переменных. Показано, что независимые переменные по убыванию силы влияния на проводимость ранжируются следующим образом…
Диссертация 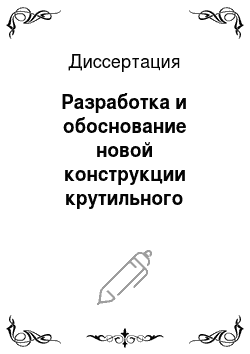
Второй вариант новой пары «кольцо-бегунок» имеет сложную систему крепления внутреннего кольца, что с одной стороны усложняет и удорожает конструкцию прядильной машины, но с другой, стороны, сложная конструкция новой пары «кольцо-бегунок» позволила создать принципиально новое взаимодействие бегунка с кольцом и бегунка с нитью. Например, впервые в мировой практике удалось нейтрализовать негативное…
Диссертация 
Одним из перспективных направлений в решении указанной проблемы является дефектоскопия изоляции оборудования, находящегося в эксплуатационном режиме под рабочим напряжением, с использованием характеристик внутренних частичных разрядов (ЧР). Проблемы, связанные с ЧР того или иного вида, известны уже более полувека. Принято считать, что ЧР являются главной причиной старения изоляции, особенно…
Диссертация 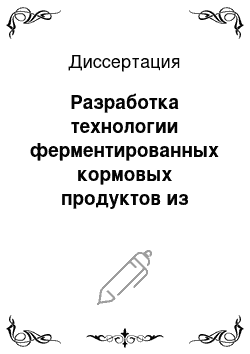
Апробация работы. Материалы диссертационной работы были представлены и обсуждены на всероссийской научной молодежной конференции-школе «Проблемы экологии морского шельфа» (Владивосток, сентябрь 2010 г.) — всероссийской молодежной конференции «Вклад молодых ученых в рыбохозяйственную науку России» (Санкт-Петербург, октябрь 2010 г.) — международной научно-технической конференции «Инновационные…
Диссертация 
Исследования на стенде и его холодной модели показали, что длина факела и его положение в рабочем пространстве печи оказывают существенное влияние на газодинамику рабочего пространства печи. Для факельно-сводового отопления при прямоточной схеме движения продуктов сгорания имеется обширная зона циркуляции газов, которая в 1,5−2 раза больше, чем при торцевом отоплении. Предложена методика оценки…
Диссертация 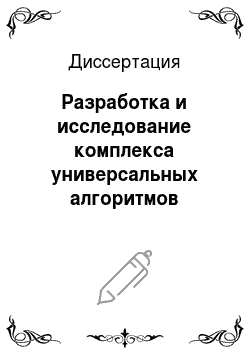
Вопросы управления такими ОУ разрабатывались в работах Красовского А. А., Петрова Б. Н., Райбмана Н. С. и др. Однако проблема адаптивного управления многорежимными объектами, особенно при фиксированном разбиении областей, с включением алгоритмов оценивания, собственно управления и адаптации к изменяющимся характеристикам ОУ еще не решена. Среди многорежимных объектов можно выделить широкий…
Диссертация 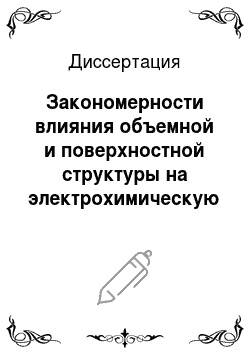
В процессе изготовления медицинские изделия из сплавов на основе титана и никелида титана подвергают термической и термомеханической обработке, а также различным финишным обработкам поверхности для формирования объемной и поверхностной структуры, позволяющей обеспечить необходимый уровень функциональных свойств имплантатов. В частности, при изготовлении головок эндопротезов тазобедренного сустава…
Диссертация 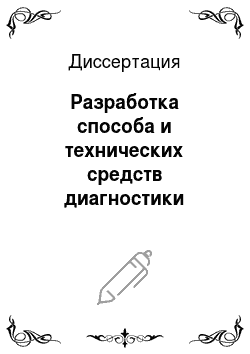
Головных светильников шахтного назначения, базируемая на запатентованном автором способе определения энергетических их характеристик, основанном на измерении падения напряжения на аккумуляторе, при его подключении к известному сопротивлению в фиксированные моменты времени до 0.4 с. Для решения этой задачи с использованием математической модели «аккумулятор-нагрузка» разработана методика…
Диссертация 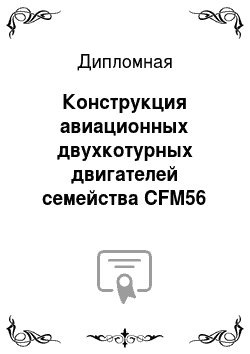
Под воздействием факторов научно-технического прогресса: морального и физического устаревания АД; потребности в более экономичных, бесшумных и надёжных двигателях с малым уровнем выбросов вредных веществ, конструкция двигателя в процессе эволюции претерпевала некоторые изменения. В первую очередь эти изменения обуславливались потребностями рынка и заключались в том, что двигатели рассчитывались…
Дипломная 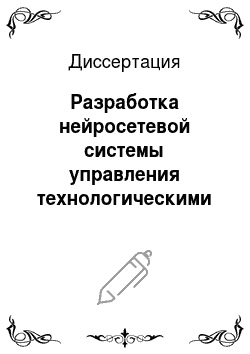
Степень разработанности проблемы. Диссертационное исследование основано на работах отечественных и зарубежных ученых в области нейросетевых технологий и автоматизированных систем управления. В настоящее время аппарат ИНС и методы его использования постоянно развиваются и совершенствуются. Активные разработки и исследования в области создания систем проектирования ИНС связаны с деятельностью таких…
Диссертация 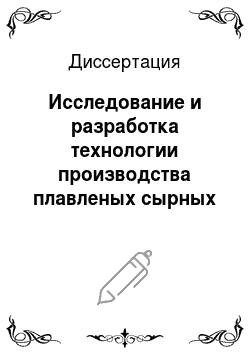
Он указывает, что создание комбинированных молочных продуктов с сырьем животного и растительного происхождения, а также комбинированные пищевые продукты с молочными компонентами в XXI веке будет одним из главных направлений развития молочной промышленности. По его мнению, комбинированные молочные продукты, фракционирование основных компонентов (жира, лактозы, белка), использование…
Диссертация 
Крышку 10 (Рис.6) нижней головки шатуна крепят к нему двумя болтами, изготовленными из высококачественной стали. Гайки болтов шатуна затягивают динамометрическим ключом и тщательно шплинтуют или стопорят специальными стопорными шайбами. Нижнюю головку шатуна и крышку растачивают вместе для получения отверстия правильной цилиндрической формы. Поэтому крышку нельзя перевертывать или переставлять…
Контрольная