Другие работы
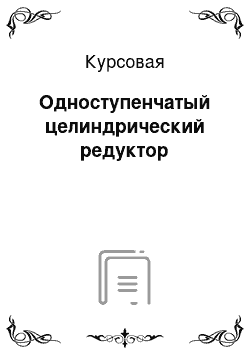
На ведущий вал насаживают шарикоподшипники, предварительно нагретые в масле до 80−100оС; Курсовой проект Лист 37 Изм. Лист № докум. Подпись Дата в ведомый вал закладывают шпонку 16×10×50 и напрессовывают зубчатое колесо до упора в бурт вала; затем надевают распорную втулку и устанавливают шарикоподшипники, предварительно нагретые в масле. Курсовой проект Лист 36 Изм. Лист № докум. Подпись Дата…
Курсовая 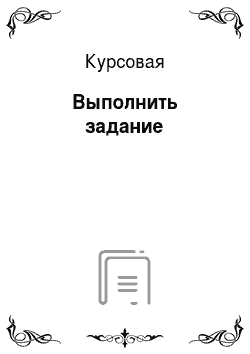
При выполнении сварочных работ необходимо строго соблюдать правила пожарной безопасности. За обеспечение мероприятий, предотвращающих возможность возникновения пожаров, ответственен начальник соответствующего цеха, участка. Ответственные за состояние противопожарных средств и за выполнение противопожарного режима по каждому участку назначаются приказом руководителя предприятия. Рабочее место…
Курсовая 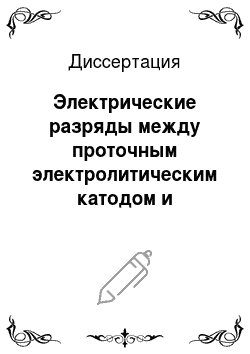
Однако, в настоящее время, электрические разряды между проточным электролитическим катодом и металлическим анодом изучены недостаточно, слабо изучено взаимодействие неравновесной плазмы электрического разряда между проточным электролитическим катодом и металлическим анодом с поверхностями материалов при пониженных давлениях. Всё это сдерживает разработку плазменных установок с использованием…
Диссертация 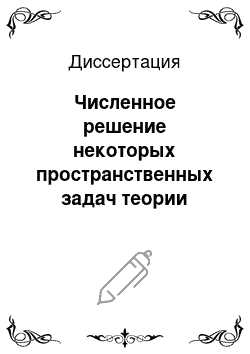
В УПРУГОМ ПАРАЛЛЕЛЕПИПЕДЕ1. Аппроксимация «функционала энергии» для упругого параллелепипеда. Глава I. КВАЗИСТА1ИЧЕСКАЯ ЗАДАЧА ЛИНЕЙНОЙ ТЕОРИИ ВЯЗКОУП РУГОСТИ В НАПРЯЖЕНИЯХ1. О новой постановке задачи в напряжениях (задача. Решение разностных уравнений итерационным методом. Об условиях симметрии (антисимметрии) напряжений. Упругий параллелепипед под действием сосредоточенных сил. Метод численной…
Диссертация 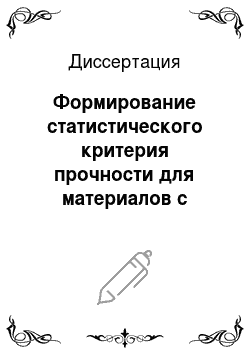
Четвёртая глава посвящена исследованию влияния полученных статистических параметров распределения микронапряжений на форму предельной поверхности разрушения для ГПУ материалов, и проведены исследования поверхностей разрушения в девиаторном и меридианных сечениях с целью определения возможного интервала изменения величин параметров, с использованием статистических, физических и геометрических…
Диссертация 
Как указывает Л. В. Овсянников, это объясняется несколькими обстоятельствами. Во-первых, задача нахождения группы преобразований, допускаемой системой обыкновенных дифференциальных уравнений, оказалась, вообще говоря, не проще, чем задача интегрирования этой системы. Во-вторых, аппарат С. Ли не позволял решать краевые задачи теории дифференциальных уравнений, поскольку изучению в нем подвергались…
Диссертация 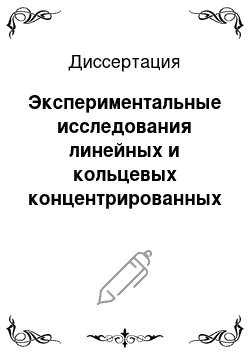
Исследовано явление формирования концентрированных вихрей во вращающемся водном бассейне с наклонным дном после резкого замедления его вращения. Показано, что при этом в бассейне формируется система из нескольких вертикальных линейных вихрей, и происходит своеобразная кумуляция завихренности, заключающаяся в том, что первоначально одинаковая во всем бассейне завихренность в процессе эволюции…
Диссертация 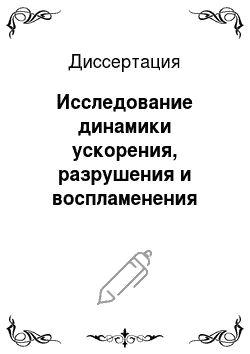
Практическая и научная ценность работы"Результаты исследования процессов взаимодействия ударных волн с мелкими частицами могут быть использованы для построения и совершенствования физических и математических моделей гетерогенной детонации, при разработке методов предотвращения взрывоопасных ситуаций, возникающих при производстве и транспортировке тонкодисперсных горючих материалов, а также при…
Диссертация 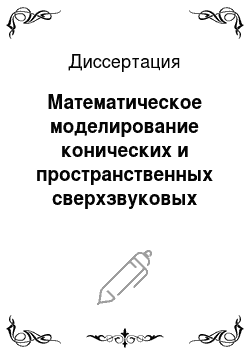
В силу сказанного, ясно, что одним из действенных способов повышения эффективности численных методов является выделение, если не всех разрывов, то хотя бы тех, которые оказывают наибольшее влияние на исследуемое течение. Связанное с этим усложнение алгоритмов оправдывается не только ростом точности, но и, как правило, одновременным сокращением времени счета за счет уменьшения расчетной области…
Диссертация 
С помощью критерия инкубационного времени электрического пробоя получено хорошее соответствие расчетных данных экспериментальным при описании временной зависимости электрической прочности (вольт-секундная характеристика) и температурной зависимости электрической прочности. Показано, что критерий инкубационного времени позволяет объяснить эффект внедрения разряда в твердое тело в параллельной…
Диссертация 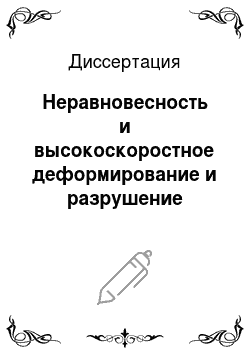
Динамическом нагружении в субмикросекундном диапазоне длительностей (100−10нс) выявилось следующее. Относительная плотность дислокаций остается неизменной и не выходит за пределы статистического разброса значений конкретной серии образцов вплоть до пороговых значений растягивающих напряжений. За время достижения растягивающими напряжениями разрушающей величины (первая стадия разрушения…
Диссертация 
В третьем параграфе кратко изложена история развития методов расчета балок и плит. Основной вклад в развитие методов расчета было сделано Е. А. Палатниковым, Б. Г. Кореневым, М.И. Горбуновым-Посадовым, A.A. Гвоздевым, А. П. Синицыным, Н. Нильсеном, А. Р. Ржаницыным, Г. А. Раппопорт, и др. Большое значение для решения данной задачи имеют различные эффективные методы, такие как методы Ритца…
Диссертация 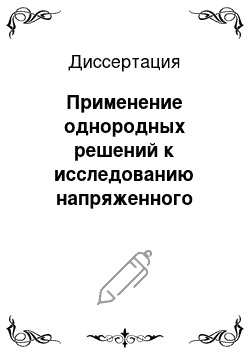
Ряд весьма интересных статей по приложению однородных решений принадлежит К. А. Китоверу /32−34/. В работе /32/ приведены некоторые конкретные примеры расчета тонких прямоугольных плит. В работе /34/ рассмотрена плоская задача теории упругости для квадрата при задании напряжений на 2-х противоположных его сторонахграничные условия на 2-х других сторонах квадрата удовлетворяются путем минимизации…
Диссертация 
Во второй главе диссертации рассматриваются вопросы теории повреждаемости. Основой континуальной теории накопления повреждений является уравнение повреждаемости типа Качанова-Работнова, представляющее собой результат обобщения экспериментов по накоплению повреждений, причем набор определяющих параметров, входящих в это уравнение, каждый раз выбирается исходя из соображения наилучшего приближения…
Диссертация 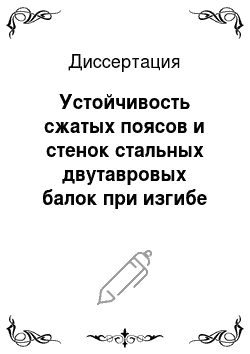
Конструктивное решение БГС с ребрами жесткости, соединенными только с поясами (бесконтактные ребра-стойки) было предложено Пога-даевым И. К. Трудозатраты на изготовление этих балок меньше, чем на изготовление балок с обычными ребрами жесткости, хотя всеми преимуществами последних они обладают. Особенностью балок с ребрами-стойками является то, что ребра жесткости не прерывают поле напряжений…
Диссертация