Технологический процесс восстановления вилки включения гидронасоса
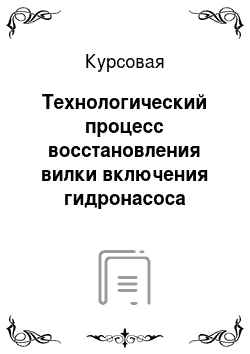
Ввиду малых размеров изношенных поверхностей и относительно сложной формы детали в данном случае применимы лишь способы слесарно-механической обработки. Отверстия под ось сухарика ремонтируются развёртыванием до ремонтного размера, оси сухарей и сухари при этом заменяются. Отверстие под ось рычага включения гидронасоса также развёртывается до ремонтного размера, до которого увеличится и диаметр… Читать ещё >
Технологический процесс восстановления вилки включения гидронасоса (реферат, курсовая, диплом, контрольная)
Вятская государственная сельскохозяйственная академия Инженерный факультет Кафедра ремонта машин Основы технологии производства и ремонта автомобилей Курсовая работа Технологический процесс восстановления вилки включения гидронасоса Выполнил Романов А.А.
Группа ИАу-532
Киров 2006
Содержание Введение
1. Общие положения
1.1 Функциональное назначение, техническая характеристика и условия работы агрегата
1.2 Программа выпуска ремонтируемых изделий
2. Технологический процесс ремонта детали
2.1 Функциональное назначение, технические требования и условия работы детали
2.2 Выбор способов устранения дефектов детали
2.3 Выбор технологических баз и схем установки детали при ремонте
2.4 Маршрутный технологический процесс ремонта детали
2.5 Технологические операции ремонта детали
2.6 Расчёт режимов обработки
3. Технологическая документация Заключение Список литературы Приложение А. Технологические карты
Введение
При длительной эксплуатации автомобили достигают такого состояния, когда затраты средств и труда, связанные с поддержанием их в работоспособном состоянии в условиях АТП, становятся больше прибыли, которую они приносят в эксплуатации. Такое техническое состояние автомобилей считается предельным, и они направляются в капитальный ремонт (КР). Задача КР состоит в том, чтобы с оптимальными затратами восстановить утраченные автомобилем работоспособность и ресурс до уровня, нового или близкого к нему.
Ремонт автомобилей имеет большое экономическое значение. Основными источниками экономической эффективности ремонта автомобилей является использование остаточного ресурса их деталей. Около 70…75% деталей автомобилей, прошедших срок службы до первого КР, имеют остаточный ресурс и могут быть использованы повторно либо без ремонта, либо после небольшого ремонтного воздействия.
Повышение качества ремонта машин при одновременном снижении его себестоимости — главная проблема ремонтного производства. В структуре себестоимости капитального ремонта машин 60…70% затрат приходится на покупку запасных частей, которые даже в условиях рынка остаются дефицитными при росте цен. Основной путь снижения себестоимости ремонта машин — сокращение затрат на запасные части. Частично этого можно добиться за счёт бережного и грамотного разборки машин и дефектации деталей. Однако главный резерв — восстановление и повторное использование изношенных деталей, т.к. восстановление изношенных деталей, не превышает 20…60% цены новой детали. Кроме того, восстановление деталей — один из основных путей экономии материально — сырьевых и энергетических ресурсов, решение экологических проблем, так как затраты энергии, металлов и других материалов в 25…30 раз меньше, чем затраты при изготовлении новых деталей. При переплавке изношенных деталей также безвозвратно теряется до 30% металла.
В процессе восстановления детали можно не только снизить себестоимость ремонта машин, но и во многих случаях повысить его качество, так как многие из способов восстановления значительно упрочняют восстанавливаемые поверхности, повышают их износостойкость.
вилка деталь ремонт дефект
1. Общие положения
1.1 Функциональное назначение, техническая характеристика и условия работы агрегата Привод гидронасоса предназначен для передачи крутящего момента к гидронасосу, а также для включения и отключения его.
Крутящий момент подаётся на зубчатое колесо, находящееся в постоянном зацеплении с шестерней. Зубчатое колесо установлено на двух шарикоподшипниках на неподвижной оси.
Валик гидронасоса входит в шлицевую втулку, расположенную внутри зубчатого колеса. По периметру втулки расположены углубления, а в соответствующей части зубчатого колеса сквозные отверстия, в которых находятся свободные шарики. Во включенном состоянии привода шарики удерживаются муфтой включения гидронасоса и соединяют собой зубчатое колесо со втулкой. При отключении гидронасоса муфта перемещается по выступу колеса 6, освобождая шарики, которые под действием окружного усилия на их поверхность выходят из углублений во втулке в расширение на конце муфты, тем самым разъединяя насос и зубчатое колесо.
Перемещение муфты осуществляется поворотом вилки, неподвижно закреплённой на оси рычага включения. Вилка соединяется с муфтой шарнирно через сухари на осях. Ось рычага включения через втулку установлена в корпусе привода и зафиксирована от осевого перемещения штифтом. На конце оси, выходящем из корпуса, неподвижно закреплён рычаг включения гидронасоса. Для фиксации положений рычага, соответствующих включенному и полностью выключенному положениям муфты, предназначен подпружиненный фиксатор, входящий в специальные отверстия в корпусе.
Корпус привода гидронасоса крепится к насосу болтами через плиту и шпильками.
Наиболее нагруженными местами узла являются поверхности муфты и втулки валика, соприкасающиеся с шариками. Также износу подвержены зубья колеса, посадочные места под подшипники, втулка, шарнирные соединения вилки с муфтой.
1.2 Программа выпуска ремонтируемых изделий Годовой объем выпуска деталей определяют по формуле:
(1.1)
где — годовой объем выпуска агрегата (сборочной единицы), шт;
n — количество деталей данного наименования в агрегате (сборочной единице), шт.;
Кр — коэффициент ремонта детали, показывающий, какая часть деталей требует ремонта (Кр=0,8).
.
Исходя из годовой программы выпуска агрегатов, определяют квартальное, месячное и суточное задания. Тип производства устанавливают ориентировочно, исходя из массы деталей и программы выпуска агрегата (сборочной единицы).
Т.к. масса детали менее 1 кг. а годовой объем выпуска деталей 5400шт, то на основании данных таблицы 5.1 принимается среднесерийный тип производства.
Тип производства определяет форму его организации, принципиальные решения при проектировании технологических процессов, используемые средства технологического оснащения и др.
2. Технологический процесс ремонта детали
2.1 Функциональное назначение, технические требования и условия работы детали Вилка включения гидронасоса предназначена для перемещения муфты включения гидронасоса в осевом направлении. Она крепится на оси рычага с помощью болта и фиксирующей втулки. Соединение неподвижное, но тем не менее возможен износ поверхности отверстия под ось рычага в результате вибраций и переменно действующих сил. Вилка соединяется с муфтой через два сухаря, вращающиеся вокруг осей, расположенных в отверстиях на концах вилки. Так как это подвижное соединение, к тому же работающее без смазки, то вероятность возникновения износа отверстий под оси сухарей довольно высока. Сильный износ данного соединения может привести к несоответствию положения муфты положению рычага включения, например, к непостоянному соединению насоса с зубчатым колесом.
Таблица 2.1 — Карта технических условий на дефектацию
Наименование и обозначение контролируемой детали | Контролируемый дефект | Размеры, мм | Способы и средства контроля | заключение | |||||
№ | наименование | По чертежу | Доп. в сопряжении с деталями | Наименование | Обозначение или погрешность измерения | ||||
бывшими в экспл. | Новыми | ||||||||
Износ поверхности отверстия под ось рычага включения гидронасоса | 11,15 | 11,18 | Нутромер | НИ 10−18 | Ремонтировать | ||||
Износ поверхности отверстия под ось сухаря | 6,10 | 6,12 | Нутромер | НИ 6−10 | Ремонтировать | ||||
Сведения, касающиеся дефектов детали, берутся из технических условий на ремонт, приведённых в дефектовочных картах.
2.2 Выбор способов устранения дефектов детали При выборе рациональных способов устранения дефектов детали используются приложения к методическим указаниям для выполнения курсовой работы. Целесообразные способы восстановления устанавливают на основе конструктивно-технологических характеристик детали.
К ним относят вид основного материала детали, вид восстанавливаемой поверхности, материал покрытия, предельно (минимально) допустимый диаметр восстанавливаемой поверхности (наружный), минимально допустимый диаметр восстанавливаемой поверхности (внутренний), минимальная толщина (глубина) наращивания (упрочнения), максимальная толщина (глубина) наращивания (упрочнения), сопряжения или посадки восстанавливаемой поверхности, вид нагрузки на восстанавливаемую поверхность. С учетом номенклатуры деталей-представителей, рекомендуемых для восстановления тем или иным способом выбираем ряд альтернативных способов восстановления ремонтируемой детали.
Выбранные способы оцениваем по показателям физико-механических свойств деталей: коэффициент износостойкости, коэффициент выносливости, коэффициент сцепляемости, коэффициент долговечности, микротвердость. Окончательный выбор способов восстановления производим исходя из технико-экономических показателей каждого способа: удельный расход материала, удельная трудоемкость наращивания, удельная трудоемкость подготовительно-заключительной обработки, удельная суммарная трудоемкость, коэффициент производительности процесса, удельная стоимость восстановления, показатель технико-экономической оценки, удельная энергоемкость.
1. Слесарно — механическая обработка: обработка под ремонтный размер, постановка дополнительной ремонтной детали, обработка до выведения следов износа и придание правильной геометрической формы.
2. Пластическое деформирование: вытяжка, оттяжка, правка, механическая раздача, гидротермическая раздача, электрогидравлическая раздача, раскатка, механическое обжатие, термопластическое обжатие, осадка, выдавливание, накатка, электромеханическая высадка.
3. Нанесение полимерных материалов: напыление (газопламенное, в псевдосжиженном слое), опрессовка, литьё под давлением, нанесение шпателем, валиком, кистью.
4. Ручная сварка и наплавка: газовая, дуговая, аргонодуговая, кузнечная, плазменная, термитная, контактная.
5. Гальванические и химические покрытия: железнение постоянным током, железнение периодическим током, железнение проточное, железнение местное, хромирование, хромирование проточное (струйное), меднение, цинкование, нанесение сплавов, нанесение композиционных покрытий, электроконтактное нанесение, гальваномеханический способ, химическое никелирование.
6. Другие способы: заливка жидким металлом, намораживание, напекание, пайка, пайкосварка, электроискровое наращивание и легирование и другие способы восстановления.
С учетом недостатков способов восстановления выбираем экономически целесообразные, обеспечивающие необходимый уровень качества.
Ввиду малых размеров изношенных поверхностей и относительно сложной формы детали в данном случае применимы лишь способы слесарно-механической обработки. Отверстия под ось сухарика ремонтируются развёртыванием до ремонтного размера, оси сухарей и сухари при этом заменяются. Отверстие под ось рычага включения гидронасоса также развёртывается до ремонтного размера, до которого увеличится и диаметр новой оси рычага. Постановка дополнительной детали — втулки нецелесообразна ввиду того, что изношенную ось всё равно бракуют, способ более трудоёмкий. Также во втулке придётся сделать продольный разрез, что вызовет снижение прочности посадки.
2.3 Выбор технологических баз и схем установки детали при ремонте Выбор технологических баз в значительной степени определяет точность получения линейных и угловых размеров детали в процессе ремонта. При выборе технологических баз руководствуются следующими положениями:
— в качестве технологических баз при ремонте рекомендуют принимать поверхности (оси), служившие технологическими базами при изготовлении детали и не воспринимающие значительные воздействия в процессе эксплуатации;
— при прочих равных условиях меньшие погрешности имеют место, когда используют на всех операциях одни и те же базы, т. е. когда соблюдается принцип единства баз;
— желательно совмещать технологические базы с конструкторскими базами проектируемой детали, т. е. использовать принцип совмещения баз;
— поверхности, используемые в качестве технологических баз на операциях окончательной обработки должны отличаться наибольшей точностью;
— при отсутствии у ремонтируемой детали надежных технологических баз можно создавать искусственные технологические базы, включив в технологический процесс дополнительные операции, на которых эти базы обрабатывают.
Выбор технологических баз при ремонте детали сопровождают расчетом погрешностей базирования еб (погрешностей несовмещения баз), что является основой для обоснования выбранной схемы установки детали.
Схема установки считается приемлемой, если производственная погрешность еу, равная сумме погрешности базирования еб и погрешности технологической системы етс, не превышает допуска Т на размер, выдерживаемый на выполняемом технологическом переходе или операции, т. е.
При выполнении последнего технологического перехода обработки поверхностей, являющихся границами какого-либо размера, производственная погрешность еу не должна превышать величины допуска Т, указанного на ремонтном чертеже.
Базирование при развёртывании отверстия под ось рычага включения гидронасоса осуществляется по двум параллельным боковым сторонам вилки и по наружному торцу одной из проушин под ось сухаря. При развёртывании отверстий под оси сухарей можно принять эти же базы. Для обеспечения жёсткости при этом между проушинами нужно вставить специальную проставку, изготовление которой целесообразно при заданной производственной программе.
2.4 Маршрутный технологический процесс ремонта детали Технологический процесс ремонта детали разрабатывают исходя из необходимости устранения всех дефектов детали, либо их части, если деталь сложная, а число устраняемых дефектов велико.
В начале технологического процесса выполняем подготовительные операции: очистку, обезжиривание, правку и восстановление базовых поверхностей. Затем производим наращивание изношенных поверхностей. При этом, в первую очередь, выполняют операции связанные с нагревом детали до высокой температуры. При необходимости детали подвергают вторичной правке. После наращивания выполняем операции механической обработки ремонтируемой детали.
Контрольные операции выполняем в конце технологического процесса ремонта детали и после выполнения наиболее ответственных операций.
Выбор технологического оборудования во многом зависит от типа производства. Так как у нас серийное производство, то применяем универсальные станки.
Одним из критериев выбора маршрута технологического процесса служит анализ точности ремонта, в соответствие с которым для реализации принимают маршрут, обеспечивающий получение детали с заданными параметрами качества (точности).
Таблица 2.2 — Технологический маршрут восстановления вилки включения гидронасоса
Номер операции | Наименование и содержание операции | Оборудование | |
Моечная Промыть и очистить деталь от грязи | Моечная ванна | ||
Дефектовочная Выявить износ поверхностей отверстий под ось рычага включения гидронасоса и под оси сухариков | Нутромеры | ||
Сверлильная Развернуть отверстие под ось рычага включения гидронасоса | Сверлильный станок | ||
Сверлильная Развернуть отверстия под оси сухариков | Сверлильный станок | ||
Контрольная | Калибры | ||
2.5 Технологические операции ремонта детали Структура операций и последовательность выполнения переходов тесно связаны с выбором средств технологического оснащения. К средствам технологического оснащения относят технологическое оборудование, технологическую оснастку, а также средства механизации и автоматизации производственных процессов.
Выбор технологического оборудования зависит от конструктивных особенностей, размеров и точности ремонтируемых деталей, технологических возможностей оборудования и экономической целесообразности его применения.
При выборе приспособлений руководствуемся стандартами на приспособления и их детали, альбомами типовых конструкций приспособлений и справочниками. При выборе типа и конструкции режущего инструмента учитываем метод обработки, тип станка, размеры, конфигурацию, материал обрабатываемой детали, качественные характеристики детали. Особое значение уделяем выбору материала режущей части инструмента. Параллельно с выбором режущего инструмента выбираем вспомогательный инструмент. При выборе режущего и вспомогательного инструмента отдаем предпочтение стандартным инструментам.
Методы и средства контроля в процессе ремонта выбираем на стадии анализа и разработки технических требований к ремонтируемой детали.
Требования к точности обработки ремонтируемых поверхностей позволяют добиться нужного результата однократным сверлением без дальнейшего развёртывания.
Для наглядности выбранное оборудование, инструмент, материалы и оснастку представляем в виде ведомости.
Таблица 2.3 — Сводная ведомость оборудования
Номер операции | Наименование | Наименование и модель | Мощность, кВт | |
Сверлильная | Станок вертикально-сверлильный 2Н135 | 4,5 | ||
Сверлильная | Станок вертикально-сверлильный 2Н135 | 4,5 | ||
Таблица 2.4 — Сводная ведомость приспособлений и вспомогательного инструмента
Номер | Наименование | Наименование | Обозначение, номер стандарта | |
Операции | Приспособления и вспомогательный инструмент | |||
Сверлильная | Тисы слесарные | ГОСТ 46 039–86 | ||
Сверлильная | Тисы слесарные | ГОСТ 46 039–86 | ||
Таблица 2.5 — Сводная ведомость режущего и слесарного инструмента
Номер | Наименование | Наименование | Материал режущей части | Обозначение и номер стандарта | |
Операции | Инструмент | ||||
Сверлильная | Развёртка | Р9 | ГОСТ 10 902–77 | ||
Сверлильная | Развёртка | Р9 | ГОСТ 10 902–77 | ||
Припуск на обработку поверхностей ремонтируемых деталей может быть назначен по справочным таблицам или рассчитан расчетно-аналитическим методом. Расчетной величиной является минимальный припуск на обработку, достаточный для устранения на выполняемом переходе погрешностей или дефектов поверхностного слоя, полученных на предшествующем переходе или операции, и компенсации погрешностей, возникающих на выполняемом переходе.
В настоящее время отсутствует достаточный объем статистических данных, необходимых для расчета припусков в случае восстановления деталей различными методами, поэтому соответствующие припуски назначаем, используя табличные данные.
В данном случае для всех операций весь слой металла снимается за один проход.
2.6 Расчёт режимов обработки Методику назначения и расчета режимов резания применяют в индивидуальном, мелкосерийном и серийном производстве. Режимы резания выбирают в следующем порядке.
Изучив рабочий чертёж детали и конкретный обрабатываемый элемент заготовки, определяют длину рабочего хода инструмента. Выбирают режущий инструмент и его стойкость, учитывая при этом свойства обрабатываемого материала, точность обработки, жесткость системы СПИД, величину припуска и т. п.
Руководствуясь справочной литературой, находят глубину резания t мм. Нужно стремиться к тому, чтобы глубина резания равнялась припуску на обработку, т. е.: t=z.
Если по технологическим причинам (точность обработки, шероховатость поверхности и т. д.) такого соотношения добиться не удаётся, то при первом проходе глубина резания должна быть t1=(0,8…0,9)z, при втором проходе t2=(0,2…0,1)z.
Затем выбирают подачу s мм. Чтобы получить максимальную производительность, стремятся использовать наибольшую подачу станка, учитывая при этом заданную точность и шероховатость поверхности после обработки, жесткость системы СПИД и материал режущего инструмента.
Зная t и s для конкретной операции, определённого инструмента, материала обрабатываемой детали и условий обработки, выбирают или рассчитывают скорость резания v. Если инструмент затачивают алмазными кругами, то полученную расчетную скорость резания нужно умножить на поправочный коэффициент. Имея скорость резания, определяют расчетную частоту вращения шпинделя станка либо число двойных ходов стола и резца. Сверяя полученное значение nД с паспортными данными станка устанавливают фактическую частоту вращения шпинделя nФ максимально приближенную к расчетной. Определив силу резания РР по справочным данным, подсчитывают эффективную мощность резания NЭ. Значение NЭ должно быть меньшим либо равным мощности электродвигателя станка, т. е. NЭ< NДВ. В этом случае обработка детали возможна.
Развёртывание отверстий под оси сухариков:
Глубина резания t при развёртывании
(2.1)
где — диаметр развёртки, мм;
— диаметр отверстия, мм.
.
Подача выбирается по таблице 58 [2], S=0,65 мм/об.
Скорость резания по таблице 60 [2], v=17,4 м/мин.
Выбранная скорость резания корректируется коэффициентами из таблиц 12,13,14,15.
м/мин.
Число оборотов шпинделя
(2.2)
об/мин.
Согласно паспорта станка принимается n=630 об/мин.
Развёртывание отверстия под ось рычага:
.
S=0,9 мм/об., v=11,1•1•0,8•1•1=8,9 м/мин.
об/мин.
Принимается n=250 об/мин.
Норма времени определяется по формуле
(2.3)
где — основное время, мин;
— вспомогательное время, мин;
— дополнительное время (время на организационно-техническое обслуживание, на отдых, на физиологические надобности), мин;
— подготовительно-заключительное время, мин;
— число деталей.
(2.4)
где — глубина обработки с учётом врезания и выхода инструмента, мм.
Величина врезания и выхода инструмента определяется по таблице 64.
Вспомогательное время определяется по таблицам 65 и 66.
Дополнительное время определяется по формуле:
(2.5)
где К — коэффициент, выбирается по таблице 7 [2], К=6.
Подготовительно-заключительное время принимается по таблице 67.
мин, мин, мин, мин.
Так как у детали два отверстия под оси сухариков, то значения времён увеличиваются в два раза.
мин, мин.
3. Технологическая документация К технологической документации относятся технологические карты, чертежи приспособлений, специального инструмента. Наиболее важным документом считается технологическая карта. Существуют три степени детализации описания технологических процессов: маршрутное, операционное и маршрутно-операционное. Соответственно применяют маршрутные и операционные технологические карты. В маршрутной карте делают описание всех технологических операций в последовательности их выполнения.
Операционная карта для механической обработки детали содержит данные об обрабатываемой детали, заготовке, номере и наименовании операций и переходов, применяемом оборудовании, приспособлениях, инструменте, режимах резанья, машинном и штучном времени, разряде работ. При операционном описании технологического процесса составляют полное описание всех технологических операций в последовательности их выполнения с указанием переходов и технологических режимов, и на каждую операцию разрабатывают технологическую карту и маршрутную карту. При маршрутно-операционном описании сокращенно указывают технологические операции в маршрутной карте в последовательности их выполнения с полным описанием отдельных, более важных операций в операционных картах.
Документы на технологические процессы ремонта изделий выполнены с учетом требований рекомендаций Р 50−60−88 «ЕСТД. Правила оформления документов на технологические процессы ремонта».
Заключение
Содержание и направленность данного курсовой работы по дисциплине «Основы технологии производства и ремонта автомобилей» нацелена на практическое усвоение и закрепление теоретических знаний, полученных при изучении данной и других инженерных дисциплин.
При выполнении данной курсовой работы мы научились методам оценки качества изделий, расчета и анализа технологических и размерных цепей, анализу технологических процессов, выбору рациональных схем базирования заготовок, расчету погрешностей, определяющих точность механической обработки, расчету припусков, оптимальных режимов обработки, обеспечивающих получение заданных параметров качества деталей, а также студенты должны научиться расчету норм времени и себестоимости получения деталей.
Также получили практический навык по проектированию технологических процессов и механической обработки для получения заданных параметров детали.
1 Баранов Н. Ф., Шишканов Е. А. Разработка технологического процесса восстановления деталей машин: Методические указания для студентов инженерного факультета.- Киров: Вятская ГСХА, 2005.-67с.
2 Матвеев В. А., Пустовалов И. И. Техническое нормирование ремонтных работ в сельском хозяйстве.- М.: Колос, 1979.-288с.
3 Шадричев В. А. Основы технологии автостроения и ремонт автомобилей, — Л: Машиностроение, 1976 — 560с.
4 Обработка металлов резанием: Справочник технолога / А. А. Панов, В. В. Аникин, Н. Г. Бейм и др. Под ред. А. А. Панова. М: Машиностроение, 1988 — 736с.
5 Надёжность и ремонт машин /В.В. Курчаткин, Н. Ф. Тельнов, К. А. Ачкасов и др.; Под ред. В. В. Курчаткина. — М.: Колос, 2000. — 776с.: ил.