Проект участка приготовления резиновых смесей для производства формовых армированных изделий и уплотнителя годовой производительностью 5 и 4 тыс. т. издели
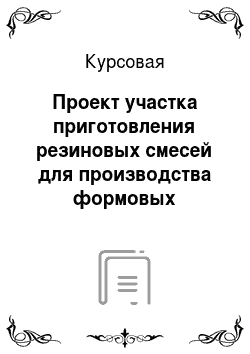
Контролировать, чтобы все материалы полностью загружались в резиносмеситель. В случае застревания резиновой смеси в воронке резиносмесителя, сообщить оператору САУ и принимать меры по устранению застревания, соблюдая правила охраны труда. В случае налипания резиновой смеси на нижний затвор необходимо остановить резиносмеситель, нажав последовательно кнопки «Резиносмеситель — стоп… Читать ещё >
Проект участка приготовления резиновых смесей для производства формовых армированных изделий и уплотнителя годовой производительностью 5 и 4 тыс. т. издели (реферат, курсовая, диплом, контрольная)
Министерство образования и науки Российской Федерации Федеральное государственное бюджетное образовательное учреждение высшего профессионального образования
«Ярославский государственный технический университет»
Кафедра «Химическая технология биологически активных веществ и полимерных материалов»
Курсовой проект ПРОЕКТ УЧАСТКА ПРИГОТОВЛЕНИЯ РЕЗИНОВЫХ СМЕСЕЙ ДЛЯ ПРОИЗВОДСТВА ФОРМОВЫХ АРМИРОВАННЫХ ИЗДЕЛИЙ И УПЛОТНИТЕЛЯ ГОДОВОЙ ПРОИЗВОДИТЕЛЬНОСТЬЮ 5 И 4 ТЫС. Т. ИЗДЕЛИЙ СООТВЕТСТВЕННО Проект выполнила студентка гр. ХТК-47
Гончарова М.Н.
Реферат РЕЗИНОВЫЕ ИЗДЕЛИЯ, УПЛОТНИТЕЛЬ СТЕКЛА, ФОРМОВЫЕ ИЗДЕЛИЯ, НЕФОРМОВЫЕ ИЗДЕЛИЯ, РЕЦЕПТУРА, ТЕХНОЛОГИЧЕСКИЙ ПРОЦЕСС, ОБОРУДОВАНИЕ, ОХРАНА ТРУДА.
Выполнен проект участка завода РТИ по приготовлению резиновых смесей для опорных частей резиновых армированных и уплотнителя стекла. Рецептуры приняты на основе данных базового предприятия, что полностью удовлетворяет эксплуатационным требованиям: для опорных частей высокая морозостойкость, высокая теплостойкость, прочность, износостойкость, стойкость к трещинам, стойкость к расслоению за счет адгезии между резиной и армирующим элементом; для уплотнителя стекла высокая теплостойкость, высокая морозостойкость, стойкость к износу и высокая эластичность.
Приготовление резиновых смесей осуществляется в одну стадию, доработка осуществляется на агрегате из трех вальцев и фестонной установке.
Подача каучука осуществляется после предварительной подготовки в виде готовых навесок, развеска ингредиентов предусмотрена как децентрализованная, так и централизованная.
При работе над проектом были использованы материалы базового предприятия ОАО «Ярославский завод РТИ», различные научно-технические источники.
Графическая часть выполнена с помощью конструкторского пакета KOMPAS-3D v.11.0. Расчёт и оформление произведены с использованием программных средств Microsoft Office Word и Microsoft Office Excel.
Введение
Отличительной особенностью производства РТИ является чрезвычайно широкий ассортимент (около 100 тыс. наименований), поскольку изделия находят применение практически во всех сферах деятельности современного общества. В связи с быстро растущими требованиями к РТИ решается комплекс сложнейших научно — технических задач, включающий наряду с использованием новых полимеров разработку специфических способов создания эластомерных композиционных материалов, высокомеханизированных и автоматизированных процессов, более совершенных конструкций и методов продления срока службы изделий путем дополнительной обработки.
Особенностью резиновой промышленности является высокая стоимость применяемого сырья, чаще всего являющегося продуктом других отраслей химической и нефтехимической индустрии. Доля труда сотрудников самой резиновой промышленности в себестоимости важнейших изделий составляет всего 6−7%. Поэтому огромное значение имеют экономия сырья и материалов, разработка безотходных технологий, продление сроков эксплуатации изделий.
Развитие современной резиновой промышленности характеризуется следующими основными особенностями:
• расширением областей применения и ассортимента резиновых изделий
• ужесточение условий эксплуатации изделий (температуры, нагрузки, скорости, агрессивные среды и т. д.)
• стремление использовать наиболее дешевые и доступные армирующие материалы, каучуки и ингредиенты при невозможности беспредельного увеличения их ассортимента
• необходимостью снижения материалоемкости изделий и трудоемкости их изготовления
• требованиями охраны здоровья и защиты окружающей среды Очевидно, что одновременное выполнение всех этих требований невозможно, и реальное решение всегда является компромиссным. Особенно резко стоимость изделий возрастает при их создании для предельных условий эксплуатации — для работы в условиях сильно агрессивных сред, при температурах выше 250 градусов или ниже минус 100 градусов, так как для этого требуются очень дорогие каучуки и химические добавки. Хотя стоимость комплектующих резиновых изделий в сравнении со стоимостью машин и механизмов, в которых они используются, обычно невелика, трудность замены резиновых деталей часто так высока, что для потребителя их долговечность является основным показателем. Для резиновой промышленности это оборачивается увеличением трудоемкости, снижением рентабельности, так как стоимость переработки составляет небольшую долю стоимости изделий.
Продукция должна соответствовать требованиям заказчика. Достигаться это может за счет повышения качества резин и резиновых смесей. Качество можно поднять за счет расширения сырьевой базы, путем совершенствования технологии их изготовления. Используют автоматические и полуавтоматические системы развески материалов. Внедряются системы автоматизации управления процессами смешения — это позволяет увеличить производительность основного технологического оборудования, исключить влияние человеческого фактора, что в свое время ведет к росту качества резиновых смесей. На современных предприятиях необходимо постоянно совершенствовать системы организации труда таким образом, чтобы усиливать заинтересованность работника в результатах своего труда.
1. Выбор и обоснование конструкции изделий Проектом предусмотрен выпуск формовых и неформовых резинотехнических изделий.
К формовым относятся части опорные резиновые армированные (РОЧ), к неформовым — уплотнитель стекла УС-1.
Части опорные резиновые армированные предназначены для мостовых сооружений, расположенных на автомобильных дорогах в горах и других населенных пунктах России.
РОЧ представляют собой несущие элементы мостового сооружения, передающие опорные давления пролетного строения на опоры и обеспечивающие линейные угловые перемещения пролетного строения за счет упругого сдвига резины. Основные характеристики РОЧ представлены в табл. 1.
Таблица 1 — Основные характеристики опорных частей (ТУ 2539−008−149 334−96)
Наименование показателя | Значение показателя | |
Длина L, мм | ||
Ширина В, мм | ||
Высота h, мм | ||
Масса, кг | 24,7 | |
РОЧ производятся из твердой резины путем вулканизации синтетического каучука. Резины армируются высококачественными стальными листами, соединяющимися в процессе термической вулканизации со слоями резины, полностью их охватывающими, и таким образом защищающими от коррозии. Части опорные должны обладать высокой стойкостью к деформациям, прочностью, озоностойкостью и др.
Рисунок 1 — Часть опорная резиновая армированная: 1 — Резина; 2 — Стальная арматура.
Уплотнитель стекла УС-1
Предназначен для уплотнения окон, кузовов автомобилей, автобусов, тракторов, комбайнов, строительных и дорожных машин.
Основные характеристики уплотнителя стекла представлены в табл. 2.
Таблица 2 — Основные характеристики уплотнителя стекла.
Наименование показателя | Значение показателя | |
Ширина H1, мм | 9,5 | |
Высота H2, мм | 12,5 | |
Масса 1 пог. м, г | ||
Рисунок 2 — Уплотнитель стекла 1 — резина.
Уплотнитель стекла УС-1 используется для обеспечения пылебрызгозащиты в автомобильной промышленности, машиностроении и сельском хозяйстве.
Уплотнитель стекла УС-1 должен обладать высокой озоностойкостью, морозостойкостью, стойкостью к деформациям и др.
резина каучук ингредиент
2. Выбор и обоснование рецептуры резиновых смесей
2.1 Выбор рецептуры резиновых смесей осуществляется, исходя из требований к резинам и резиновым смесям При выборе рецептуры резиновых смесей учитывали необходимость:
1. обеспечения высоких технологических свойств резиновых смесей;
2. обеспечения наилучших эксплуатационных характеристик изделий путем применения резин с лучшими физико-механическими показателями;
3. применения наиболее экологически чистых видов сырья и материалов;
4. применения экономически выгодных видов сырья и материалов.
2.1.1 Резиновая смесь для изготовления РОЧ Резиновая смесь для изготовления частей опорных резиновых армированных должна соответствовать предъявляемым к ним требованиям.
Выбор рецептуры резиновой смеси для РОЧ Основные требования, предъявляемые к техническим свойствам резин для опорных частей, следующие.
Резины, используемые при изготовлении опорных частей должны обладать комплексом технических свойств, необходимых для долговременной эксплуатации изделия: высокой устойчивостью к механическим нагрузкам и химико-физическим воздействиям.
Резины для РОЧ должны иметь следующие технические свойства.
· высокую прочность,
· высокую озоностойкость,
· высокую морозостойкость,
· заданную твердость,
· стойкость к расслоению за счет адгезии между резиной и армирующим элементом.
Резиновые смеси для РОЧ должны иметь следующие технологические свойства:
· хорошо обрабатываться на вальцах;
· шприцуемость;
· клейкость;
· низкая усадка;
· высокая стойкость к подвулканизации.
Нормируемые физико-механические показатели резины для РОЧ должны иметь значения, представленные в таблице 3.
Таблица 3 — Физико-механические показатели резин для опорных частей.
Показатели | Нормы физико-механических показателей резины для РОЧ | Физико-механические показатели резины шифра 7-ИПР-1347 | Физико-механические показатели резины шифра 7-ИПР-1347−1 | |
Условная прочность при растяжении, МПа | не менее 16,7 | 16,8 | 17,0 | |
Твердость по Шору А, ед. Шора А | 47−57 | |||
Относительное удлинение при разрыве %, | не менее 550 | |||
Температурный предел хрупкости, 0С, | не выше — 55 | — 55 | — 60 | |
Прочность связи резины с металлом при отрыве, МПа | не менее 2,45 | 2,6 | 3,0 | |
Основные требования, предъявляемые к резиновым смесям, представлены в таблице 4. Резины для опорных частей шифров 7-ИПР-1347 и 7-ИПР-1347−1, рецептуры резиновых смесей которых приведены в таблицах 5 и 6, имеют физико-механические показатели в пределах нормативных значений (табл. 5).
Таблица 4 — Технологические свойства резиновых смесей для опорных частей.
Показатели | Нормы физико-механических показателей резиновой смеси для РОЧ | Физико-механические показатели резиновой смеси шифра 7-ИПР-1347 | Физико-механические показатели резиновой смеси шифра 7-ИПР-1347−1 | |
Кольцевой модуль, груз/деление 1/3 | 2,5−5,5 | 3,2 | 4,5 | |
Плотность, кг/м3 | 1140±50 | |||
Пластичность по ГОСТ 415–75 | 0,40−0,60 | 0,40−0,60 | 0,40−0,60 | |
Таблица 5 — Рецептура резиновой смеси шифра 7-ИПР-1347 для изготовления опорных частей.
№ | Наименование компонентов | Содержание ингредиентов | Цена ингредиента, руб/кг | Ст-ть ингредиента в 1 т | ||
мас. ч. | массовые доли, % | |||||
Каучук СКИ-3 | 75,00 | 48,39 | 23 711,1 | |||
Каучук СКД | 25,00 | 16,13 | 8548,9 | |||
Сера | 2,00 | 1,29 | 8,2 | 105,78 | ||
Сульфенамид Ц | 1,00 | 0,64 | 614,4 | |||
Белила цинковые | 15,00 | 9,68 | 3678,4 | |||
Диафен ФП | 2,00 | 1,29 | 1496,4 | |||
Нафтам | 1,00 | 0,64 | 614,4 | |||
Воск ЗВ-П | 1,00 | 0,64 | 179,2 | |||
Техуглерод П 803 | 15,00 | 9,68 | 10,7 | 1035,76 | ||
Техуглерод П 234 | 15,00 | 9,68 | 18,2 | 1761,76 | ||
Кислота стеариновая | 1,00 | 0,65 | ||||
Битум нефтяной | 2,00 | 1,29 | 7,2 | 92,88 | ||
Итого: | 155,00 | 100,00 | 42 167,98 | |||
Таблица 6 — Рецептура резиновой смеси шифра 7-ИПР-1347−1 для изготовления опорных частей.
№ | Наименование компонентов | Содержание ингредиентов, | Цена ингредиента, руб/кг | Стоимость ингредиента в 1 т, руб | ||
мас. ч. | массовые доли, % | |||||
Каучук СКИ-3 | 75,00 | 48,7 | ||||
Каучук СКД | 25,00 | 16,23 | 8601,9 | |||
Сера | 2,00 | 10,66 | 8,2 | 106,6 | ||
Сульфенамид Ц | 1,00 | 0,65 | ||||
Белила цинковые | 15,00 | 9,74 | 3701,2 | |||
Диафен ФП | 2,00 | 1,3 | ||||
Нафтам | 1,00 | 0,65 | ||||
Техуглерод П 803 | 15,00 | 9,74 | 10,7 | 1042,18 | ||
Техуглерод К 354 | 15,00 | 9,74 | 35,4 | 3447,96 | ||
Кислота стеариновая | 1,00 | 0,65 | ||||
Битум нефтяной | 2,00 | 1,3 | 7,2 | 93,6 | ||
Итого: | 154,00 | 100,00 | 44 000,44 | |||
По уровню физико-механических свойств резины практически идентичны, однако стоимость резиновой смеси 7-ИПР-1347 ниже стоимости резиновой смеси 7-ИПР-1347−1.
С учётом рассмотренных факторов для изготовления опорных частей в проекте принимается резиновая смесь шифра 7-ИПР-1347.
2.1.2 Обоснование рецептуры выбранной резиновой смеси для опорных частей
Исходя из требований, предъявляемых к резинам для опорных частей, в основе рецепта резиновой смеси в качестве полимерной основы взята комбинация двух каучуков общего назначения СКИ-3 и СКД, каждый из которых вносит свой вклад в обеспечение требуемых свойств будущего изделия.
С химической точки зрения каучук СКИ-3 характеризуется достаточно высокой активностью, выпускается с достаточно высокой пластичностью, поэтому при изготовлении резиновых смесей не требуется предварительной пластикации. Способность СКИ-3 кристаллизоваться при растяжении и гибкость его макромолекул обуславливают высокую эластичность и прочность наполненных резин, а также хорошие динамические свойства. Наполненные резины на основе СКИ-3 обладают высоким сопротивлением раздиру, высоким напряжением при заданном удлинении.
Каучук СКИ-3 легко смешивается с ингредиентами и другими каучуками. Смеси, изготовленные на его основе, легко каландруются и шприцуются, имеют гладкую глянцевую поверхность и обладают высокой клейкостью.
Каучук СКД — стереорегулярный каучук. Его макромолекулы характеризуются высокой гибкостью, следствием чего является низкая, по сравнению с другими каучуками общего назначения, температура стеклования (от минус 95 до минус 110 С.), низкие гистерезисные потери в резинах. Смеси на его основе плохо вальцуются, шприцуются и имеют большую усадку, пониженную когезионную прочность и плохую клейкость. Компенсировать эти недостатки позволяет комбинирование каучука СКД с кристаллизующимся при растяжении каучуком (в данном случае с каучуком СКИ-3) и введение активных наполнителей. Резины из каучука СКД имеют низкий коэффициент трения, чем обусловлена их высокая износостойкость. Сочетание каучуков СКД с СКИ-3 позволяет обеспечить оптимальное значение коэффициента трения. Каучук СКИ-3 отличается высокой склонностью к деструкции под действием высоких температур и в условиях термоокисления. В значительной мере скрыть этот недостаток позволяет введение каучука СКД, характеризующегося значительно более высокой стойкостью к термои окислительной деструкции. Резины на основе комбинации каучуков СКД с СКИ-3 характеризуются более высокими выносливостью и сопротивлением разрастанию трещин, чем резины на основе каждого из каучуков, вследствие релаксации перенапряжений на границе раздела фаз.
В качестве вулканизующего агента резиновой смеси применяется сера. Она является наиболее распространённым вулканизующим агентом и применяется для вулканизации непредельных каучуков. При вулканизации серой происходит образование сшивок между отдельными макромолекулами каучука, в результате чего образуется единая статистическая сетка.
Сера обеспечивает высокие прочностные свойства резин, высокую эластичность и выносливость при многократных деформациях.
В качестве ускорителя серной вулканизации применяют сульфенамид Ц. Сульфенамидные ускорители имеют повышенную критическую температуру действия (около 120 С). Резиновые смеси с этими ускорителями характеризуются замедленным начальным периодом вулканизации (большим индукционным периодом) и, как следствие повышенной устойчивостью к преждевременной вулканизации. Благодаря этому, резиновые смеси могут длительное время находиться в вязкотекучем состоянии и поэтому хорошо формуются при вулканизации. По этой же причине эти ускорители обеспечивают повышенную прочность многослойных соединений.
Применение оксида цинка приводит к увеличению активной доли сетки, что увеличивает прочность и улучшает другие физико-механические показатели резин. В его присутствии снижается степень сульфидности поперечных связей, что способствует повышению теплостойкости резин. Наиболее эффективно оксид цинка действует в присутствии жирной кислоты — стеариновой, которую относят к вторичным активаторам вулканизации. Сера, ускоритель и активаторы вулканизации образуют так называемый сульфидирующий комплекс, являющийся действительным агентом вулканизации. Помимо активирующего действия стеариновая кислота выполняет функции пластификатора и диспергатора порошкообразных ингредиентов. Повышение дисперсности порошков обусловлено поверхностно-активными свойствами стеариновой кислоты.
Противостаритель диафен ФП относится к противостарителям химического действия. Защищает резины от теплового и озонного старения, а также от утомления. Диафен ФП значительно активирует ускорители серной вулканизации.
Нафтам-2-Антиоксидант общего назначения, эффективно защищает каучуки и резины от теплового старения, повышает сопротивление резин разрушению при многократных деформациях. Применяется в качестве стабилизатора синтетических каучуков и для защиты резин на основе каучуков общего назначения.
В качестве наполнителя используется технический углерод марки П234. Активный техуглерод П234 вводится в резиновую смесь для повышения прочности, сопротивления раздиру, образованию проколов, порезов и других механических дефектов, повышения износостойкости, стойкости к тепловому старению и атмосферостойкости.
Введение
активного техуглерода сопровождается повышением вязкости, когезионной прочности, а так же понижением усадки. Также используем малоактивный техуглерод П803. Резиновые смеси, наполненные малоактивным техническим углеродом, имеют низкую усадку.
Воск защитный относится к ингредиентам многофункционального действия. Он является физическим противостарителем, защищает резину от светоозонного и атмосферного старения. Его действие основано на миграции к поверхности резины и образовании на ней защитной пленки, препятствующей взаимодействию озона с каучуком. Особенно эффективен при совместном применении с антиозонантами. Кроме того, защитный воск является пластифицирующим агентом.
При введении битума в резиновые смеси на основе непредельных неполярных каучуков их вязкость практически не меняется, но улучшается формование за счет уменьшения эластического восстановления и повышения каркасности смесей.
В резиновые смеси, наполненные техническим углеродом, вводят 5−10 мас.ч. битума, который является разбавителем (так уменьшается содержание каучука за счет дешевого продукта) и придает резинам стойкость к набуханию в воде.
2.2 Выбор рецептуры резиновой смеси для производства уплотнителя стекла УС-1
Основные требования, предъявляемые к техническим свойствам резин для уплотнителя стекла, следующие:
Резины, используемые при изготовлении уплотнителей стекла должны обладать комплексом технических свойств, необходимых для долговременной эксплуатации изделия: высокой устойчивостью к механическим нагрузкам и химико-физическим воздействиям.
Резины для уплотнителей стекла должны иметь следующие технические свойства:
· высокую износостойкость,
· высокую озоностойкость,
· высокую морозостойкость,
· высокую эластичность Резиновые смеси для уплотнителей стекла должны иметь следующие технологические свойства:
· хорошо обрабатываться на вальцах;
· шприцуемость;
· низкая усадка;
· высокая стойкость к подвулканизации.
Основные требования, применяемые к резиновым смесям, представлены в таблице 7.
Таблица 7 — Технологические свойства резиновых смесей для уплотнителей стекла.
Показатели | Физико-механические показатели резиновой смеси шифра 7−6190П | Физико-механические показатели резиновой смеси шифра 7−6190П-20 | |
Кольцевой модуль, груз/деление 1/3 | 1,5−5,5 | 1,5−5,0 | |
Плотность, кг/м3 | 1260±50 | 1260±50 | |
Пластичность | 0,25−0,40 | 0,30−0,50 | |
Резина для уплотнителей стекла УС-1 должна отвечать требованиям, представленным в таблице 8.
Таблица 8 — Физико-механические показатели резины для уплотнителей стекла УС-1.
Показатели | Нормы физико-механических показателей резиновой смеси для уплотнителя стекла | Физико-механические показатели резиновой смеси шифра 7−6190П | Физико-механические показатели резиновой смеси шифра 7−6190П-20 | |
Условная прочность при растяжении, МПа | не менее 4,4 | 4,4 | 3,9 | |
Твердость по Шору А, ед. Шора А | 60−75 | 60−75 | 65−75 | |
Относительное удлинение при разрыве %, | не менее 300 | |||
Температура хрупкости при замораживании, С, | не выше — 40 | — 40 | — 40 | |
Относительная остаточная деформация после старения в воздухе при постоянной величине сжатия 20% при 100С в течении 24 часов, | не более 70 | |||
Таблица 9 — Рецептура резиновой смеси шифра 7−6190П для изготовления уплотнителя стекла УС-1.
№ | Наименование компонентов | Содержание ингредиентов, | Цена ингредиента, руб/кг | Стоимость ингредиента в 1 т | ||
мас. ч. | массовые доли, % | |||||
Каучук СКМС-30 АРКМ-15 2гр | 100,00 | 31,42 | 13 510,6 | |||
Резина дробленая | 15,00 | 4,71 | 235,5 | |||
Сера | 2,50 | 0,79 | 8,2 | 64,78 | ||
2-меркаптобензтиазол | 1,50 | 0,47 | 573,4 | |||
Тиурам Д | 0,30 | 0,1 | ||||
Белила цинковые | 2,00 | 0,63 | 239,4 | |||
АцетонанилР (Н) | 3,00 | 0,94 | 49,5 | 465,3 | ||
Паралайт 17 | 3,00 | 0,94 | 3,85 | 36,19 | ||
Кислота стеариновая | 1,00 | 0,31 | 161,2 | |||
Техуглерод П 514 | 100,00 | 31,42 | 16,3 | 5121,46 | ||
Каолин | 51,00 | 16,02 | 2,7 | 432,54 | ||
Битум нефтяной | 10,00 | 3,14 | 7,2 | 226,08 | ||
Масло ПН-6ш | 29,00 | 9,11 | 89,47 | 8150,72 | ||
Итого: | 318,30 | 100,00 | 29 338,17 | |||
Таблица 10 — Рецептура резиновой смеси шифра 7−6190П-20 для изготовления уплотнителя стекла УС-1.
№ | Наименование компонентов | Содержание ингредиентов, | Цена ингредиента, руб/кг | Стоимость ингредиента в 1 т | ||
мас. ч. | массовые доли, % | |||||
Каучук СКМС-30 АРКМ-15 2гр | 100,00 | 34,64 | 14 895,2 | |||
Сера | 0,20 | 0,07 | 8,2 | 5,74 | ||
Тиурам Д | 2,40 | 0,83 | 1004,3 | |||
Сульфенамид Ц | 0,20 | 0,07 | 67,2 | |||
Белила цинковые | 3,00 | 1,04 | 395,2 | |||
Ацетонанил Р (Н) | 3,00 | 1,04 | 49,5 | 514,8 | ||
Паралайт 17 | 3,00 | 1,04 | 3,85 | 40,04 | ||
Кислота стеариновая | 2,00 | 0,69 | 358,8 | |||
Техуглерод П 803 | 120,00 | 41,57 | 10,7 | 4447,99 | ||
Техуглерод Т 900 | 15,40 | 5,33 | 13,5 | 719,55 | ||
Битум нефтяной | 15,40 | 5,33 | 7,2 | 383,76 | ||
Масло индустриальное И-12А | 23,08 | 8,00 | 17,5 | |||
N-нитрозодифениламин | 1,00 | 0,35 | 117,6 | 411,6 | ||
Итого: | 288,68 | 100,00 | 24 644,18 | |||
По уровню физико-механических свойств резины практически идентичны, однако стоимость резиновой смеси 7−6190П-20 ниже стоимости резиновой смеси 7−6190П.
С учётом рассмотренных факторов для уплотнителей стекла в проекте принимается резиновая смесь шифра 7−6190П-20.
2.2.1 Обоснование выбранной рецептуры резиновой смеси для уплотнителей стекла УС-1
Исходя из требований, предъявляемых к уплотнителям стекла, в основе рецепта резиновой смеси в качестве полимерной основы каучук СКМС-30АРКМ-15.
СКМС-30АРКМ-15 относится к бутадиен-стирольным каучукам. Благодаря наличию двойных связей в основной цепи бутадиен-стирольных каучуков, резиновые смеси на их основе хорошо вулканизуются серой в присутствии органических ускорителей.
В качестве вулканизующего агента резиновой смеси применяется сера. Она является наиболее распространённым вулканизующим агентом и применяется для вулканизации непредельных каучуков. При вулканизации серой происходит образование сшивок между отдельными макромолекулами каучука, в результате чего образуется единая статистическая сетка.
Сера обеспечивает высокие прочностные свойства резин, высокую эластичность и выносливость при многократных деформациях.
Тиурам Д — ускоритель вулканизации высокой активности. Кинетика вулканизации резиновых смесей с тиурамом Д характеризуется практическим отсутствием индукционного периода и высокой скоростью в главном периоде. При вулканизации серой совместно с тиурамом Д образуются вулканизаты с набором поперечных связей низкой степени сульфидности, которые довольно устойчивые при тепловом старении.
В качестве ускорителя используется сульфенамид Ц. Он является ускорителем высокой активности. Резиновой смеси придает замедленный начальный период вулканизации (широкий индукционный период), поэтому смесь обладает повышенной устойчивостью к преждевременной вулканизации. Ускоритель обеспечивает широкое плато вулканизации. В присутствии сульфенамидаЦ образовывается набор связей разной степени сульфидности, что обеспечивает высокий уровень упруго-гистерезисных свойств при нормальных и повышенных температурах. Кроме того, данный тип ускорителя способствует повышению сопротивления истиранию, раздиру.
В качестве активаторов вулканизации применяют белила цинковые и кислоту стеариновую. Кислота стеариновая активирует вулканизацию, а также способствует лучшему диспергированию порошкообразных ингредиентов. При введении уменьшается вязкость и улучшается обрабатываемость резиновых смесей. Применение оксида цинка в качестве активатора вулканизации приводит к увеличению активной доли сетки, что увеличивает прочность и улучшает другие физико-механические показатели резин. В его присутствии снижается степень сульфидности поперечных связей, что способствует повышению теплостойкости резин.
АцетонанилР используется в качестве химического противостарителя, он оказывает пластифицирующее действие. АцетонанилР способствует увеличению срока службы изделия и играет роль антиоксиданта.
Для повышения прочности некристаллизующихся при комнатной температуре каучуков вводят наполнители. Поскольку к резине не предъявляется высоких требований по уровню прочностных свойств, возможно допустить использование в ее составе больших дозировок малоактивных наполнителей. В данном случае это техуглерод П 803 и техуглерод Т 900. Применение техуглерода пониженной активности позволяет уменьшить теплообразование при изготовлении и переработке смесей. В присутствии малоактивных наполнителей при динамических нагрузках для резин характерно меньшее теплообразование по сравнению с вулканизатами, содержащими высокоактивные наполнители.
При введении битума в резиновые смеси на основе непредельных неполярных каучуков их вязкость практически не меняется, но улучшается формование за счет уменьшения эластического восстановления и повышения каркасности смесей, придает резинам стойкость к набуханию в воде.
Пластификатор масло индустриальное И-12А используют для облегчения введения ингредиентов в смесь, так как они меняют структуру резиновой смеси, улучшают технологические свойства резиновых смесей.
N-нитрозодифениламинзамедлитель преждевременной вулканизации. Особенно эффективен в смесях, содержащих сульфенамидные ускорители. Замедляет вулканизацию при температурах технологической обработке смесей и частично активирует протекание реакции вулканизации при высоких температурах.
В качестве физического противостарителя используется микровоск паралайт-17, который образуя плотный защитный слой на поверхности резины, препятствует сорбции и диффузии озона и кислорода в резину.
3. Характеристика каучуков и ингредиентов
3.1 Характеристика каучуков
Каучук СКИ-3 (ГОСТ 14 925−79)
Каучук СКИ-3 неполярный с параметром растворимости при температуре 25 0С — 16,2−17,0 (МДж/м3)½.Кристаллизуется при переохлаждении и растяжении.
Синтетические изопреновые каучуки являются аналогами натурального каучука. Это — продукты ионно-координационной полимеризации изопрена. Их получают в растворе в присутствии комплексных (координационных) катализаторов Циглера-Натта,
Структура. По содержанию звеньев в той или иной изомерной форме стереорегулярные изопреновые каучуки аналогичны натуральному каучуку. Несмотря на близкое химическое строение природных и синтетических полиизопренов, между ними существуют определенные различия, которые находят отражение в различии физических и химических свойств. Так, в синтетических полиизопренах отсутствуют некаучуковые вещества (природные белковые соединения др.), их макромолекулы, содержащие большее количество 3,4-звеньев, уступают по стереорегулярности макромолекулам НК. В то же время синтетические полиизопрены превосходят природный каучук по чистоте, их состав не зависит от погодных и климатических условий.
В таблице 11 приведена характеристика изопреновых каучуков.
Таблица 11 — Характеристика изопреновых каучуков
Показатель | Тип катализатора комплексный | |
Параметры молекулярной структуры | ||
Содержание звеньев, %: | ||
1,4-цис | 94−97 | |
1,4-транс | 2−4 | |
3,4 | 1−2 | |
Доля звеньев аномального строения («голова к голове», «хвост к хвосту») | ||
Молекулярная масса золь-фракции: средневязкостная, среднемассовая, среднечисловая | (0,55−1)106 | |
Коэффициент полидисперсности | 2,5−4,0 | |
Непредельность, % (мол.) | 95−98 | |
Массовая доля геля, % | ||
Физические свойства. Изопреновые каучуки аморфны при комнатной температуре. Подобно натуральному каучуку, они кристаллизуются при растяжении (выше 0 С) или при температурах ниже 0 С. Скорость кристаллизации снижается по мере уменьшения степени регулярности каучука.
Плотность изопреновых каучуков составляет 910−920 кг/м3, температура стеклования около минус 70 С. Изопреновые каучуки растворимы в четыреххлористом углероде, хлороформе, циклогексане, сероуглероде, бензоле, монохлорбензоле и толуоле; не растворимы в спиртах и кетонах. Набухание изопреновых каучуков в ароматических маслах достигает 500%.
Химические свойства. Химические превращения изопреновых каучуков аналогичны превращениям натурального каучука. Под влиянием компонентов комплексного катализатора полимеризации изопрена или облучения они претерпевают цис-транс-изомеризацию, которая в некоторых случаях сопровождается реакциями сшивания и циклизации, что приводит к уменьшению непредельности каучука. Изопреновые каучуки способны к циклизации при нагревании в присутствии P2O5 или SnCl4, реагируют с малеиновым ангидридом, склонны к окислительной деструкции, которая ускоряется под действием металлов переменной валентности (Cu, Fe и др.). Склонность к окислению синтетических изопреновых каучуков выше, чем НК. Это может быть связано с отсутствием в СКИ естественных природных примесей, выполняющих в НК функцию противостарителей, и наличием остатков катализаторов, ускоряющих окисление. Высокая склонность к окислению обусловливает пониженную водостойкость каучука.
Синтетические изопреновые каучуки не стойки к действию концентрированных кислот и щелочей.
Основным вулканизующим агентом, используемым для вулканизации изопреновых каучуков, является сера. Ускорителями вулканизации служат соединения класса тиазолов, сульфенамидов, тиурамсульфидов, гуанидинов, а также продукты конденсации альдегидов с аминами. Количество ускорителей в смесях их синтетических изопреновых каучуков на 10% больше, чем в смесях из НК. Помимо серы, вулканизующими агентами для изопреновых каучуков могут служить доноры серы (тиурам), органические перекиси (которые используются редко для получения прозрачных резин), алкилфенолоформальдегидные смолы.
Синтетические изопреновые каучуки используются для изготовления широкого ассортимента резиновых изделий.
Бутадиеновый каучук СКД (ТУ 2294−100−5 766 801−2003)
Получают на катализаторах Циглера-Натта с «титановой» и «кобальтовой» основой. В настоящее время молекулярная масса полимера достигает 200 тыс., при Mw/Mn=1,5−5.
Химические свойства полибутадиена определяются микроструктурой цепей: с увеличением доли 1,4-звеньев каучуки становятся более химически активными: благодаря наличию С=С связей полимеры хорошо взаимодействуют с хлором, бромом, галогенсодержащими соединениями.
1,4- цис каучуки имеют самые низкие температуры стеклования (минус 105-минус 110 0С). Каучук кристаллизуется и степень кристалличности может достигать в среднем 55%. Плотность 900−920 кг/м3.
Каучуки СКД растворимы в нефтепродуктах, неполярных растворителях, устойчивы к действию полярных растворителей. Каучук СКД выпускают под различными марками, в зависимости от вязкости. В настоящее время также налажен выпуск полибутадиена марки СКДМ, который наполнен маслом.
Все бутадиеновые каучуки выпускаются с определенной пластичностью (от 0,20 до 0,66). Узкое ММР обуславливает крайне неудовлетворительные технологические свойства. Незначительная разветвленность молекулярных цепей и небольшое изменение вязкости полимера с температурой определяют высокую хладотекучесть каучука СКД. Также дивиниловый каучук имеет низкую когезионную прочность, низкую адгезию к металлу, что затрудняет переработку.
Из-за плохих технологических свойств бутадиеновые каучуки применяются в комбинации с другими полимерами, например НК, СКИ, БСК.
По скорости вулканизации полимер уступает только каучукам НК и СКИ. Вулканизуется в присутствии серы и обычно применяемых ускорителей. Так как вулканизаты бутадиеновых каучуков не способны кристаллизоваться при деформации, то в ненаполненном состоянии они имеют низкие показатели механических свойств. Резины на основе каучука СКД имеют высокую износостойкость, эластичность, морозостойкость. Однако резины обладают низким коэффициентом трения.
Совмещение каучука СКД с другими каучуками приводит к получению резин с высокой динамической выносливостью и износостойкостью.
Каучук СКМС-30АРКМ-15(ГОСТ 11 138−78)
Каучук СКМС-30-АРКМ-15 — бутадиен-метилстирольный каучук. После названия марки цифры и буквы указывают на отличительные особенности сополимера данного типа. Каучук марки СКМС-30-АРКМ-15 является сополимером бутадиена и стирола, взятых в соотношении 70:30 по массе, который получен при низкотемпературной полимеризации (буква А) с регулированием молекулярной массы (буква Р) в присутствии мыл кислот канифоли (буква К). Каучук является маслонаполненным (М) с массовой долей масла 15%.
Получение каучуков осуществляется в водных эмульсиях по механизму радикальной полимеризации при температуре 5С («низкотемпературные»), а также при температуре 50 С («высокотемпературные» каучуки). Соотношения бутадиена и стирола по массе составляют 90:10, 70:30, 50:50.
«Низкотемпературные» бутадиен-стирольные каучуки получают с использованием для инициирования окислительно-восстановительных систем. В качестве регулятора молекулярной массы применяют трет-додецилмеркаптан, агента обрыва при полимеризации (стоппера) — диметилдитиокарбамата натрия, в качестве эмульгатора — мыла высших жирных кислот или кислот канифоли.
Высокотемпературные бутадиен-стирольные каучуки получают с применением для инициирования персульфата калия. Регулятор молекулярной массы — н-додецилмеркаптан или диизопропилксантогендисульфид (дипроксид). В качестве эмульгаторов применяют смесь натриевых солей дибутилнафталинсульфокислоты и синтетических жирных кислот или натриевую соль жирных кислот кокосового масла.
Массовая доля звеньев в положении 1,4-цис в макромолекулах эмульсионных каучуков составляет 10%, в положении 1,4-транс — примерно 70% и в положении 1,2 — около 20%. Звенья бутадиена разных изомерных форм и стирола в макромолекулах распределены статистически, вследствие чего каучуки имеют нерегулярную структуру. Каучуки «низкотемпературной» полимеризации отличаются повышенным содержанием 1,4-транс-звеньев, пониженной разветвленностью. Массовая доля связанного стирола в каучуках, полученных при соотношениях бутадиена и стирола, равных 90:10, 70:30, 50:50, составляет соответственно около 8, 23 и 45%. Непредельность каучуков составляет 89% от теоретической. Средневязкостная молекулярная масса лежит в пределах 150 000 — 400 000. Каучук имеет широкое ММР с максимумом в области 200 000, показатель полидисперсности (Мw/Mn)4. При выпуске маслонаполненных каучуков обеспечивают более высокие значения молекулярной массы, что дает возможность в значительной степени компенсировать неблагоприятное влияние масла на прочность резины.
В зависимости от условий полимеризации бутадиен-стирольные каучуки имеют разный химический состав. Массовая доля полимера в них составляет 92−95%.
Вследствие нерегулярного строения бутадиен-стирольные каучуки не кристаллизуются при охлаждении или растяжении. Они растворяются в ароматических и алифатических углеводородах, вследствие низкой полярности (неполярности) не стойки к действию смазочных масел, являются достаточно стойкими к действию разбавленных и концентрированных кислот и кетонов, имеют достаточно высокую газои водонепроницаемость.
Химическая активность бутадиен-стирольных каучуков в основном определяется содержанием и типом двойных связей в бутадиеновых звеньях, и поэтому она существенно ниже химической активности полибутадиена и особенно полиизопрена.
3.2 Характеристика ингредиентов Сера (ГОСТ 127.1−93)
Сера применяется как вулканизующий агент для ненасыщенных каучуков. Она представляет собой порошок, комки, гранулы или водная дисперсия желтого, серо-желтого или зеленоватого цвета. Применяют природную (молотую, тонкодисперсную) серу. Кристаллы серы имеют ромбическую ?- или ?-форму, а молекула серы — стабильный восьмичленный цикл. Плотность серы 2050;2070 кг/м3, температура плавления 114 °C. Сера растворяется в сероуглероде, горячем бензине, горячем диэтиловом эфире, ограниченно растворима в бензоле и этаноле, не растворяется в воде. Сера горюча, пылевоздушные смеси взрывоопасны. В виде пыли раздражает органы дыхания и слизистые оболочки.
Белила цинковые (ГОСТ 202−84)
Белила цинковые представляют собой белый порошок с размером частиц 0,11- 0,30 мк. Плотность 5470−5660 кг/м3, температура плавления 1800 °C. Выпускается также в виде гранул и суспензии.
Растворяются в минеральных кислотах, водных растворах щелочей, аммиаке. Не растворим в этаноле и воде. Токсичны. ПДК составляет 0,5 мг/м3. Склонны к агломерированию. В небольших количествах действуют как усилитель, снижающий теплообразование вулканизатов. Несколько замедляют действие ускорителей вулканизации щелочного характера, уменьшает опасность подвулканизации.
Цинковые белила пожарои взрывобезопасны.
Белила цинковые марка, А Белила цинковые марки, А представляют собой окись цинка, получаемую возгонкой и окислением металлического цинка и цинкосодержащих отходов. Массовая доля соединений Zn в пересчете на ZnO не менее 98%.
Белила цинковые БЦО Белила цинковые БЦОизготавливают муфельным способом. Массовая доля соединений Zn в пересчете на ZnO не менее 99,7%.
Тиурам Д (ГОСТ 740−76)
Тиурам Д — тетраметилтиурамдисульфид представляет собой светло-желтый порошок с плотностью 1400 кг/м3 и температурой плавления 140−142 0С.
Тиурамы получают окислением дитиокарбрнатов окислами азота, хлором, бромом или йидом.
Тиурам является ультроускорителем, его критическая температура действия около 105−125 0С, поэтому резиновые смеси с тиурамом обладают склонностью к подвулканизации.
Применяют в количестве от 0,1% до 0,75% от массы каучука. Активируется оксидом цинка. Технический углерод, коалин и регенерат понижают активность тиурама.
Вулканизаты отличаются хорошим сопротивлением старению.
Сульфенамид Ц (ТУ 113−00−5 761 637−02−95)
Сульфенамид Ц-N-циклогексил-2-бензотиазолилсульфенамид. Это твердое кристаллическое вещество кремовоили желто-белого цвета с температурой плавления 103С и плотностью 1280 кг/м3. Выпускается в виде гранул. Сульфенамид Ц растворим почти во всех органических растворителях, не растворим в воде и разбавленных кислотах и щелочах. Растворимость в воде 0.32 кг/м3 (рН 7, 21 °C). Запах слабый, амино подобный. Точка вспышки 177 °C. Объемная плотность 455−495 кг/м3.
Ацетонанил Р (Н) (ТУ 6−00−4 691 277−202−97)
АцетонанилР (Н) (полимеризованный 2,2,4-триметил 1,2-дигидрохинолин) — продукт конденсации ацетона с анилином. Желто-коричневый порошок. Плотность 1080 кг/м3. Температура плавления не менее 114 °C. Растворим в ароматических углеводородах, незначительно растворяется в бензине, нерастворим в воде. Относительно малотоксичен. Может использоваться в резинах из всех каучуков общего назначения.
Стеариновая кислота (ГОСТ 6484−96) CH3(CH2)16COOH
Стеариновая кислота — это твердый продукт, светло-желтого цвета. Производят его в виде чешуек, хлопьев. Получают омылением растительного масла, представляющего собой триглецерид стеариновой кислоты.
Кислота стеариновая — активирует вулканизацию, а также способствует лучшему диспергированию порошкообразных ингредиентов. Очень незначительно растворима в каучуках, склонна к выцветанию на поверхность. При введении уменьшается вязкость и улучшается обрабатываемость резиновых смесей.
Температура самовоспламенения — 320 0С. Температура плавления — 69,6 °C. Температура кипения — 376,1 °C. Плотность — 960 кг/м3.
Масло индустриальное И-12А (ГОСТ 20 799−88)
Плотность при 20? С, кг/м3 не более — 880. Вязкость кинематическая, мм2/с, при температуре 40? С, в пределах — 13−18. Температура вспышки в открытом тигле, ?С, не ниже — 170. Температура застывания, ?С, не выше — минус 15. Зольность, %, не более — 0,005. Массовая доля серы в маслах из сернистых нефтей, %, не более — 1,0. Содержание механических примесей — отсутствие. Содержание воды — следы.
N-нитрозодифениламин (ТУ 6−14−907−88)
Внешний вид — чешуйки от жёлтого до коричневого цвета. Температура кристаллизации не ниже 64,5 ?С. Массовая доля влаги не более 0,1%. Массовая доля золы не более 0,1%. Толщина чешуек не более 1,5 мм.
Воск защитный ЗВ-П (ТУ 38 101−1290−90)
Воск представляет однородную массу от светло-желтого до коричневого цвета — фракция твердых углеводородов. Вязкость по Муни при температуре 100 0С- 4,5−7,5 мм2/с. Температура вспышки > 180 0С, плотность — 810 кг/м3.
Нафтам-2 (ТУ 38.101−617−80)
Светло-серый порошок или кристаллы, стабилен, но не совместим с окислителями. Растворяется в ацетоне, хлороформе, спирте и четыреххлористом углероде, не растворяется в бензине и воде. Мало летуч. Обладает окрашивающей способностью.
Температура начала плавления, град. С: 105,30 Содержание 2-нафтанола в %, не более: 0,23 Массовая доля летучих веществ, % не более: 0,1 Массовая доля золы,% не более: 0,18 Вреден при вдыхании, попадании на кожу и проглатывании.
Диафен ФП
N-фенил-N1-изопропмл-n-фенилендиамин представляет собой чешуйки от серовато-розового до темно-фиолетового-коричневого цвета. Его получают замещением радикала в аминогруппе дифениламина.
Структурная формула:
Температура воспламенения — 225 0С; температура самовоспламенения — 523 0С, плотность — 1170 кг/м3. Диафен ФП относится к противостарителям химического действия. Защищает резины от теплового и озонного старения, а также от утомления. Отличается сравнительно высокой летучестью и легко экстрагируется из резин водой (особенно подкисленной). Диафен ФП значительно активирует ускорители серной вулканизации и может вызвать подвулканизацию резиновых смесей.
Применяется в количестве от 0,5 — 2,5% от массы каучука. Особенно эффективен этот противостаритель в сочетании с защитными восками и другими противостарителями — неозоном Д, хинолом ЭД.
Битум нефтяной Продукт окисления высокосмолистых нефтяных остатков, а также экстрактов селективной очистки масел. Представляет собой смесь высокомолекуляных углеводородов и их производных, богатых кислородом. Главная составная часть битумов — асфальтены, кроме того, в состав входят масла и смолы.
Битум нефтяной — черный, смолообразный твердый продукт с температурой размягчения 125 — 135 0С (марка А) и 135 — 150 0С (марка Б).
При введении битума вязкость резиновых смесей практически не меняется, но улучшается формование за счет уменьшения эластического восстановления и повышения каркасности смеси.
При содержании рубракса в резинах на основе непредельных неполярных каучуков до 10 мас.ч. их прочностные свойства практически не меняются, однако снижается эластичность и повышается твердость. В резиновые смеси, наполненные техническим углеродом, вводят 5 -10 масс.ч. Битума, который является разбавителем и придает резинам стойкость к набуханию в воде.
Паралайт-17
Однородная масса от светло-желтого до светло-коричневого цвета. Температура плавления, С 60 — 68, Вязкость кинематическая при 100 С, сСт 4.5 — 6.5, Массовая доля масла %, не более 4, Показатель преломления при 90 С 1.4280 — 1.4325.
Защитный воск «Паралайт-17» состоит из смеси парафинов, церезина и стеарина технического.
Технический углерод (ГОСТ 7885−86)
Технический углерод — наполнитель, высокодисперсный углеродный материал, продукт термоокислительного или термического разложения углеводородов.
Технический углерод характеризуется дисперсностью и шероховатостью, структурностью, химическими свойствами поверхности, чистотой, содержанием влаги и плотностью. В его состав входят углерод (не менее 94%), водород (0,3−0,9%), хемосорбированный кислород (0,1—5%), сера и минеральные примеси.
Кислотность поверхности характеризуют значением рН водной суспензии. Для различных типов технического углерода значение рН может изменяться в пределах 3−9,5. При повышении значения рН (снижении кислотности поверхности технического углерода) скорость вулканизации резиновых смесей возрастает. Химическую активность поверхности технического углерода характеризуют показателем поглощения дифенилгуанидина. Чем выше его значение, тем активней поверхность технического углерода. Содержание золы не должно превышать 0,05−0,5% для различных марок технического углерода. В зависимости от марки технического углерода допускается: доля общей серы не более 0,7−1,1%; массовая доля остатка после просева через сито с сеткой 0045К не более 0,08−0,10% и сито с сеткой 014К не более 0,01−0,02%; массовая доля пыли в гранулированном техническом углероде не более 5−8%; сопротивление гранул истиранию 87−95%. Содержание летучих веществ в различных типах технического углерода составляет 0,1−17%, массовая доля потерь при 105 °C — 0,1−1,5%. Плотность технического углерода в зависимости от марки составляет 1800−1900 кг/м3, насыпная плотность от 280 до 450 кг/м3. ПДК пыли технического углерода в воздухе рабочей зоны производственных помещений составляет 4 мг/м3.
Согласно стандарту ASTMD1765 принято четырехзначное обозначение технического углерода, состоящее из буквы и трех цифр. Буква характеризует влияние технического углерода на скорость вулканизации (N — нормальная скорость, S — замедленная скорость). Первая цифра обозначает номер группы по среднему размеру частиц технического углерода. Последние две цифры произвольные, проставляются предприятием-изготовителем в соответствии с маркой технического углерода.
Технический углерод П 803
Печной, малоактивный техуглерод, получаемый при термоокислительном разложении жидкого углеводородного сырья, с низким показателем дисперсности и средним показателем структурности.
Технический углерод Т900
Термический, малоактивный техуглерод, получаемый при термоокислительном разложении жидкого углеводородного сырья, с низким показателем дисперсности и средним показателем структурности.
Удельная условная поверхность 12 — 16 м2/г, потери при нагревании при 105 0С не более0,4%, зольность не более 0,15%.
Технический углерод П-234
Печной, активный, получаемый при термоокислительном разложении жидкого углеводородного сырья, с высоким показателем дисперсности и средним показателем структурности.
Резины, наполненные активным техническим углеродом, характеризуются высокой прочностью и износостойкостью, высокими гистерезисными потерями, а резиновые смеси — низкой усадкой.
Характеристика ингредиентов представлена в таблице 12.
Таблица 12 — Характеристика ингредиентов
Наименование ингредиентов | Назначение | Выпускная форма | Вид упаковки | Возможный способ развески | |
Каучук СКД | Синтетический цис-бутадиеновый | Брикеты по 30кг | Полиэтиленовая оболочка | Электрокар, электропогрузчик | |
Каучук СКИ-3 | Синтетический каучук | темно-коричневый брикет (30 ± 1) кг | Полиэтиленовая оболочка | Электрокар, электропогрузчик | |
Каучук СКС-30АРК | Сополимерный каучук общего назначения | стандартный контейнер | Электрокар, электропогрузчик | ||
Сера полимерная | Вулканизующий агент | Порошок желтого цвета | Бумажные мешки | Электрокар, электропогрузчик | |
Сульфенамид Ц | Ускоритель вулканизации | Гранулы бледно-желтого цвета | Бумажные мешки | Электрокар, электропогрузчик | |
Белила цинковые | Первичный активатор | Порошок белого цвета | Бумажные мешки | Электрокар, электропогрузчик | |
Кислота стеариновая | Вторичный активатор | Чешуйки серо-белого цвета | Бумажные мешки | Электрокар, электропогрузчик | |
Масло индустриальное И-12А | Пластификатор | Вязкая жидкость | Цистерны, бочки | Система кольцевых обогреваемых трубопроводов | |
Диафен ФП | Противостаритель | Гранулы серо-коричневого цвета | Бумажные мешки | Электрокар, электропогрузчик | |
Ацетонанил Р (Н) | Противостаритель | Чешуйки темно-янтарного цвета | Бумажные мешки | Электрокар, электро-погрузчик | |
Битум нефтяной | Пластификатор | Твердый продукт | Бумажные мешки | Электрокар, электропогрузчик | |
Воск защитный паралайт-17 | Противостаритель | Твёрдое вещество от жёлтого до коричневого цвета | Четырехслойные бумажные мешки 25 кг | Электрокар, электропогрузчик | |
Воск защитный ЗВ-П | Противостаритель | Твёрдое вещество от жёлтого до коричневого цвета | Четырехслойные бумажные мешки 25 кг | Электрокар, электропогрузчик | |
N-нитрозодифениламин | Замедлитель преждевременной вулканизации | Чешуйки от жёлтого до коричневого цвета | Четырехслойные бумажные мешки 25 кг | Электрокар, электропогрузчик | |
Нафтам-2 | Антиоксидант | Светло-серый порошок или кристаллы | Четырехслойные бумажные мешки 25 кг | Электрокар, электропогрузчик | |
Тиурам Д | Ускоритель вулканизации | Порошок белого цвета с сероватым или желтоватым оттенком | Четырехслойные бумажные мешки с полиэтиленовым вкладышем 25 кг | Электрокар, электропогрузчик | |
Технический углерод П 803 | Неактивный наполнитель, краситель | Порошок черного цвета | Бункер ные железнодорожные вагоны | Скребковый конвейер | |
Технический углерод Т 900 | Неактивный наполнитель | Порошок черного цвета | Бункер ные железнодорожные вагоны | Скребковый конвейер | |
Технический углерод П 234 | Активный наполнитель | Порошок черного цвета | Бункерные железнодорожные вагоны | Скребковый конвейер | |
4. Выбор и описание технологической схемы проектируемого производства
Производство резиновых смесей для производства формовых и неформовых резиновых изделий размещается в трехэтажном производственном корпусе.
В данном проекте производство резиновых смесей включает:
— подготовительное производство;
Подготовительное производство размещается в трехэтажной части здания с целью механизации подачи материалов и автоматизации развески. Трехэтажная часть производственного корпуса имеет сетку колон 6?6 м и монтажный пролет 24 м.
Подготовительное производство включает: прием, хранение, подготовку и подачу в производство каучуков и ингредиентов, развеску материалов, приготовление резиновых смесей, контроль их качества.
На участке подготовки имеется система бункеров, емкостей, трубопроводов, взвешивающих устройств, питателей, транспортирующих средств и другого оборудования в связи с наличием большого количества компонентов, входящих в состав резиновой смеси, в том числе жидких, порошкообразных, кусковых. На участке подготовки сырья также проводится декристаллизация каучуков.
Этажи корпуса имеют определенные рабочие функции.
Третий этаж используется для размещения таких устройств и оборудования, как транспортная система подачи технического углерода, расходные бункеры для технического углерода, укомплектованные заслонками и ленточными транспортерами-питателями, устройства для дозирования и взвешивания, загрузочные транспортеры, загрузочные шкафы. Кроме того, на третьем этаже монтируются циклоны и другие пылеуловители, вентиляционные системы, установки дробления.
На втором этаже помимо весового хозяйства, располагаются емкости для хранения мягчителей, пульт управления работой резиносмесителей.
Первый этаж занимает оборудование для обработки, охлаждения и складирования резиновых смесей и пластикации каучуков, контрольная лаборатория цеха.
Резиносмесители установлены на отдельно стоящей в монтажном пролете эстакаде с целью удобства их монтирования и ремонта, предотвращения передачи на железобетонный остов здания значительных вибраций от мощного привода резиносмесителей. Уровень эстакады ниже пола второго этажа, что облегчает подачу материалов ленточным транспортером в загрузочную воронку резиносмесителя. Под резиносмесителями на первом этаже располагаются дорабатывающие смесь машины — в данном случае агрегаты из 3-х вальцов, поскольку смеси, выгружаемой в виде бесформенной груды, необходимо придать удобную для транспортировки форму листов. Далее располагается устройство для транспортировки резиновой смеси, фестонные установки для отбора, охлаждения и укладки резиновой смеси.
Для подъема грузов на второй и третий этажи предусмотрены грузовые лифты грузоподъемностью пять тонн, а для осуществления ремонта и монтажа оборудования под крышей цеха установлен мостовой кран грузоподъемностью тридцать тонн, обслуживающий весь объем корпуса.
Технологическая схема, принятая в проекте, представлена на рис. 3.
4.1 Описание технологического процесса изготовления резиновых смесей Технологический процесс изготовления резиновых смесей состоит из следующих операций:
1. Подготовка ингредиентов резиновых смесей к производству.
2. Развеска материалов.
3. Смешение.
Рисунок 3 — Технологическая схема изготовления резиновых смесей Прием, хранение, подготовка, подача в производство каучуков и ингредиентов Каучуки и другие материалы, поступающие на завод, принимаются в соответствии с требованиями ГОСТ и технических условий (ТУ).
Все ингредиенты, поступающие на завод, делят на 4 группы:
— каучуки;
— сыпучие ингредиенты, в том числе вулканизующие агенты и ускорители вулканизации;
— технический углерод;
— жидкие мягчители Все эти группы должны соответствовать требованиям ГОСТ и технических условий и при выборе того или иного ингредиента необходимо, чтобы они не меняли химический состав и физические свойства при длительном хранении. Необходимо, чтобы они характеризовались высокой дисперсностью, не ухудшали технологических свойств, легко диспергировались. В рамках каждой группы применяется определенный набор методов испытания.
Для приема, хранения и предварительной подготовки материалов предусмотрены складские помещения, в том числе обогреваемые, и необходимое оборудование.
В проектируемом производстве используются каучуки: цис-изопреновый СКИ-3, бутадиеновый каучук СКД, бутадиен-стирольный каучук СКМС-30АРКМ-15.
Синтетические каучуки поступают на завод в железнодорожных вагонах, в виде брикетов массой 30 кг, упакованные в два полиэтиленовых пакета и в трехслойный бумажный мешок. Каучуки разгружают на поддоны и с помощью электропогрузчиков их отвозят на склад, где они хранятся на стеллажах в 5−6 ярусов. Синтетические каучуки перед подачей их в производство подвергаются растарке и резке. С помощью напольного электротранспорта брикеты синтетических каучуков подаются на участок подготовки. Снятие упаковочной тары производится вручную на ленточном конвейере. Удаляют четырёхслойный бумажный мешок и внешний полиэтиленовый пакет, далее режут дисковыми ножами, а затем их укладывают в контейнер и напольным транспортом через грузовой лифт подают на второй этаж в дальнейшее производство.
Гранулированный технический углерод поступает на завод в железнодорожных вагонах-хопперах, а так же в бумажных или полиэтиленовых пакетах, которые складируются и по надобности подаются в расходные бункера, расположенные на участке приготовления резиновых смесей. Из вагонов по гибким соединительным рукавам технический углерод выгружается в приемные устройства расположенные, под рельсовыми путями и по системе закрытых скребковых транспортеров и элеватора подается в основные складские бункера, из которых поступает в расходные бункера скребковыми транспортерами, расположенными на участке приготовления резиновых смесей.
Сыпучие порошкообразные и гранулированные материалы, поступают на завод в бумажных трехслойных пакетах, загружают на поддоны, и напольным транспортом отвозят на склад, где хранятся отдельными партиями. Сыпучие материалы полностью соответствуют требованиям ГОСТ и ТУ. Сыпучие ингредиенты со склада напольным транспортом через грузовой лифт подаются на третий этаж производственного корпуса к загрузочным шкафам, через которые загружаются в расходные бункера.
Жидкие материалы поступают на завод в железнодорожных цистернах. При выгрузке пластификаторы разогреваются с помощью циркуляционных установок и по обогреваемым трубопроводам перекачиваются в складские обогреваемые емкости. Из складских емкостей жидкие материалы по обогреваемым кольцевым трубопроводам подаются на участок приготовления резиновых смесей к автоматическим весам.
Твердоплавкие материалы поступают на завод в бумажной упаковке. Перед подачей в производство его предварительно очищают и измельчают на молотковых дробилках, затем пакуется в контейнеры и отправляется на участок централизованной развески. Куски битума с остатками упаковки плавятся и фильтруются через металлические решетки, после чего материал вновь подвергается дроблению.
Развеска ингредиентов На заводе принята смешанная централизованно-децентрализованная система развески ингредиентов. Основная масса каучуков и небольшая часть ингредиентов развешивается непосредственно у резиносмесителя.
Материалы, неподдающиеся автоматической развеске или используемые в малых количествах, развешиваются на участке централизованной развески, пакуются в разноцветные сэвиленовые пакеты, укладываются в контейнеры и напольным транспортом развозятся к загрузочным транспортерам, по которым поступает в резиносмеситель.
Сэвилен (сополимер этилена с винилацетатом) по сравнению с полиэтиленом имеет более низкую температуру плавления. Имеется возможность окраски пакетов в разные цвета, чтобы резиносмесильщику было легче отличить навески различных ингредиентов.
Каучуки напольным транспортом при помощи грузового лифта поступают к полуавтоматическим ленточным весам, расположенным на втором этаже подготовительного цеха, режутся дисковыми ножами, взвешиваются и по основному загрузочному транспортёру поступают в резиносмеситель.
Технический углерод из заводского бункерного склада скребковыми транспортерами подается в расходные бункера, из которых скребковыми питателями подается на автоматические весы, взвешивается и ссыпается в сборочную емкость, из которой загружается непосредственно в резиносмеситель через окно в задней стенке корпуса.
Сыпучие ингредиенты со склада напольным транспортом через грузовой лифт подаются к загрузочным шкафам, расположенным на третьем этаже подготовительного производства. Из загрузочных шкафов ссыпаются в расходный бункер, откуда шнековыми питателями подаются на автоматические весы, взвешиваются, ссыпаются на загрузочный транспортер, по которому поступают через воронку в камеру резиносмесителя. Материалы, расходуемые в небольшом количестве, из автоматических весов поступают в сборную емкость, и направляются в камеру.
Жидкие и легкоплавкие материалы из обогреваемых складских емкостей подаются на участок смешения по обогреваемым кольцевым трубопроводам, через автоматические клапаны, выполняющие роль питателей подаются в автоматические весы, взвешиваются и сливаются в обогреваемую сборную емкость, из которой сжатым воздухом впрыскиваются в камеру резиносмесителя.
Приготовление резиновых смесей Изготовление резиновых смесей осуществляется в резиносмесителях в одну и две стадии, что вызвано необходимостью обеспечения нормального температурного режима и качества.
Процесс смешения состоит в том, что различные ингредиенты механическим способом смешивают с каучуком. Качество смеси зависит от равномерности распределения ингредиентов в каучуке. Этого добиваются выполнением режима смешения, установленного для каждой резиновой смеси.
При смешении необходимо строго соблюдать установленный порядок введения ингредиентов, температурный режим и следить за положением верхнего затвора в камере смесителя.
При заполнении объема рабочей камеры на 53 — 65% гребни роторов несут избыточный материал, не прошедший через зазоры, к верхней части камеры и к верхнему затвору резиносмесителя. Здесь потоки встречаются, при этом создается давление, за счет которого верхний затвор (при недостаточном пневматическом давлении) поднимается, и материал входит в загрузочное окно, выбывая из общего процесса смешения. Поэтому чтобы избежать такого нежелательного явления, необходимо следить за пневматическим давлением на верхний затвор.
Для каждого типа смеси устанавливается индивидуальный режим смешения, однако существует определенная последовательность введения ингредиентов, которой следует в основном придерживаться при изготовлении любых смесей. Так, если в смесь входят противостарители их смешивают с каучуком. В первую очередь одновременно вводят диспергирующие агенты (жирные кислоты) и другие мелкие ингредиенты. Затем в смесь добавляют усиливающие наполнители. Так как лучшее диспергирование наблюдается в более вязкой среде, жидкие пластификаторы, снижающие вязкость резиновых смесей, вводят обычно в конце смешения каучука с усиливающими наполнителями. С целью предотвращения вулканизации, серу вводят на последней минуте. Малоактивные ускорители подают в смеситель в начале цикла, а ускорители высокой активности так же на последней минуте, как и серу.
В качестве основного смесительного оборудования в проекте приняты резиносмесители с объёмом смесительной камеры 270 л и скоростью вращения роторов 20об/мин марки РС 270−20. Некоторые резиновые смеси основаны на пластикатах каучуков.
После выгрузки из резиносмесителя смесь подается на агрегат из трёх вальцев См 2100 660/660, где охлаждается, дорабатывается, листуется. После доработки резиновая смесь срезается с валка непрерывной лентой и подается в установку фестонного типа АФТ-15М, где охлаждается и укладывается на поддоны, которые напольным электротранспортом отвозятся на склад резиновых смесей.
В лаборатории производится ускоренный контроль резиновой смеси. Определение физико-механических показателей резиновых смесей проводят в случае неудовлетворительных результатов анализа по первичному контролю.
4.1.1 Изготовление резиновой смеси для опорных частей Изготовление резиновой смеси для опорных частей осуществляется в закрытом резиносмесителе типа РС-270−20 с объемом смесительной камеры 270 литров и частотой вращения роторов 20 мин-1.
Исходя из величины свободного объема резиносмесителя, рассчитаны общая масса навески резиновой смеси и массы навесок ингредиентов резиновой смеси на одну загрузку резиносмесителя. Результаты расчета приведены в таблице 13.
Таблица 13- Расчёт рецепта резиновой смеси для опорных частей шифра 7-ИПР-1347 с расчётом навесок ингредиентов на одну загрузку резиносмесителя
№ | Наименование компонентов | Содержание ингредиентов | Навеска, кг | ||||
Мас. ч. | Массовые доли, % | Объемные части | Объемные доли, % | ||||
Каучук СКИ-3 | 48,39 | 81,52 | 59,84 | 90,00 | |||
Каучук СКД | 16,13 | 27,17 | 19,95 | 30,00 | |||
Сера | 1,29 | 0,98 | 0,72 | 2,40 | |||
Сульфенамид Ц | 0,65 | 0,77 | 0,56 | 1,20 | |||
Белила цинковые марка | 9,68 | 2,74 | 2,01 | 18,00 | |||
Диафен ФП | 1,29 | 1,72 | 1,27 | 2,40 | |||
Нафтам 2 | 0,65 | 0,77 | 0,56 | 1,20 | |||
Воск ЗВ-П | 0,65 | 1,11 | 0,82 | 1,20 | |||
Технический углерод П 234 | 9,68 | 8,15 | 5,98 | 18,00 | |||
Технический углерод П 803 | 9,68 | 8,24 | 6,05 | 18,00 | |||
Кислота стеариновая | 0,65 | 1,04 | 0,76 | 1,20 | |||
Битум нефтяной | 1,29 | 2,00 | 1,47 | 2,40 | |||
Итого | 100,00 | 136,22 | 100,00 | 186,00 | |||
Теоретическая плотность резиновой смеси — 1138 кг/м3.
Режим смешения резиновой смеси для опорных частей шифра 7-ИПР-1347 в резиносмесителе РС-270−20 приведен в таблице 14.
Таблица 14 — Режим смешения резиновой смеси для опорных частей шифра 7-ИПР-1347 в резиносмесителеРС-270−20
Операция (порядок введения ингредиента) | Время, мин. | ||
начала операции | окончания операции | ||
Загрузка каучуков, битума нефтяного, воска ЗВ-П, кислоты стеариновой, диафена ФП, нафтама 2, сульфенамида Ц, белил цинковых, технического углерода П 803 | |||
Введениетехнического углерода П-234 | |||
Выгрузка смеси | |||
Общая продолжительность цикла, мин — 10 | |||
В соответствии с режимом смешения в резиносмеситель РС-270−20 по загрузочному ленточному транспортеру через загрузочное окно подаются каучуки (СКИ-3, СКД), сыпучие ингредиенты.
После загрузки ингредиентов откидная дверка загрузочного окна закрывается.
Через загрузочную емкость в резиносмеситель РС-270−30 засыпается технический углерод маркиП 803 и П 514.
Обработка смеси после резиносмесителя, включающая доработку смеси, ее охлаждение и листование, происходит на агрегате из трех вальцов 2130 660/660, фрикция 1:1,07.
На приемных вальцах, используя выносной транспортер, смесь перемешивается и по перекидному транспортеру передается на питательные вальцы. На питательных вальцах смесь обрабатывается и в виде ленты подается в агрегат фестонного типа АФТ-15.
Режим обработки смеси на агрегате из трех вальцов вальцах приведен в таблице 15.
Таблица 15- Обработка смеси на вальцах после выгрузки из резиносмесителя
Наименование операции | Время, мин | ||
Начала операции | Продолжительность операции | ||
Принять смеси на вальцы пропустить через зазор 2−3 раза, срезать до малого запаса | |||
Ввести равномерно серу по всей длине валка, сделать 3−4 подреза | |||
Добавить срезанную смесь, сделать 2−3 подреза с каждой стороны, пропустить рулоном через зазор 3−4 раза | |||
Срез смеси листами | |||
Общая продолжительность цикла, мин — 8 | |||
В агрегате фестонного типа АФТ-15 лента резиновой смеси охлаждается обдувом воздуха с помощью осевых вентиляторов. Температура смеси после охлаждения в агрегате фестонного типа АФТ-15 не должна превышать 50 °C.
Охлажденная резиновая лента автоматически укладывается на паллету, взвешивается с регистрацией данных по массе, затем от каждой заправки паллеты на уровне отметок, указанных на линейке с диапазоном измерения от 0 до 1000 миллиметров, отбирают образцы для анализа в контрольной лаборатории.
Периодичность контроля: каждая загрузка.
Паллеты с резиновой смесью электропогрузчиком устанавливают в ячейки склада резиновых смесей для хранения. Продолжительность вылежки смеси перед пуском в производство не менее 4 ч.
При получении результатов анализа из контрольной лаборатории «годен» смесь передают в производство, «брак» изолируют от годной продукции и отправляют в изолятор брака.
4.1.2 Изготовление резиновой смеси для уплотнителя стекла Изготовление резиновой смеси для уплотнителя стекла осуществляется в закрытом резиносмесителе типа РС-270−20 с объемом смесительной камеры 270 литров и частотой вращения роторов 20 мин-1.
Исходя из величины свободного объема резиносмесителя, рассчитаны общая масса навески резиновой смеси и массы навесок ингредиентов резиновой смеси на одну загрузку резиносмесителя. Результаты расчета приведены в таблице 16.
Таблица 16 — Расчёт рецепта резиновой смеси для уплотнителя стекла шифра 7−6190П с расчётом навесок на одну загрузку резиносмесителя
№ | Наименование компонентов | Содержание ингредиентов | Навеска, кг | ||||
мас.ч. | массовые доли, % | Объемные части | объемные доли, % | ||||
СКМС-30 АРКМ-15 | 930,00 | 34,64 | 107,53 | 45,99 | 65,00 | ||
Сера | 2050,00 | 0,07 | 0,10 | 0,04 | 0,13 | ||
Тиурам Д | 1440,00 | 0,83 | 1,67 | 0,71 | 1,56 | ||
Сульфенамид Ц | 1300,00 | 0,07 | 0,15 | 0,07 | 0,13 | ||
Белила цинковые БЦП-А | 5470,00 | 1,04 | 0,55 | 0,23 | 2,00 | ||
Ацетонанил Р (Н) | 1120,00 | 1,04 | 2,68 | 1,15 | 3,00 | ||
Паралайт-17 | 1500,00 | 1,04 | 2,00 | 0,86 | 2,00 | ||
Кислота стеариновая | 960,00 | 0,69 | 2,08 | 0,89 | 1,30 | ||
ТУ П 803 | 1820,00 | 41,57 | 65,93 | 28,20 | 78,00 | ||
ТУ Т-900 | 1900,00 | 5,33 | 8,11 | 3,47 | 10,00 | ||
Битум нефтяной | 1000,00 | 5,33 | 15,40 | 6,59 | 10,00 | ||
Масло индустиральное И-12А | 860,00 | 8,00 | 26,84 | 11,48 | 15,00 | ||
N-нитрозодифениламин | 1260,00 | 0,35 | 0,79 | 0,34 | 0,65 | ||
ИТОГО | 100,00 | 233,83 | 100,00 | 187,77 | |||
Теоретическая плотность резиновой смеси — 1235 кг/м3.
В соответствии с режимом смешения в резиносмеситель РС-270−20 по загрузочному ленточному транспортеру через загрузочное окно подается каучук (СКМС-30 АРКМ-15), сыпучие ингредиенты. Из обогреваемой сборной емкости сжатым воздухом в камеру резиносмесителяРС-270−20 впрыскивается масло индустриальное И-12А.Через загрузочную емкость в резиносмесительРС-270−20 засыпается технический углерод марки П 803 и Т 900. После загрузки ингредиентов откидная дверка загрузочного окна закрывается.
Режим изготовления резиновой смеси для уплотнителя стекла шифра 7−6190Ппредставлен в таблице 17.
Таблица 17 — Режим смешения резиновой смеси для уплотнителя стекла шифра 7−6190Пв резиносмесителеРС-270−20
Операция (порядок введения ингредиентов) | Время, мин. | ||
Начала операции | Продолжительность операции | ||
Охлаждение резиносмесителя | |||
Загрузка каучука, битума нефтяного, ацетонанила Р, N-нитрозодифениламина, белил цинковых, паралайта 17, сульфенамида ц, кислоты стеариновой, постепенно технического углерода Т 900 | |||
Введение? технического углерода П 803, масла индустриального И-12А | |||
Введение? технического углерода П 803 | |||
Введениесеры и тиурама Д | |||
Выгрузка смеси | |||
Общая продолжительность цикла, мин — 13 | |||
Обработка смеси после резиносмесителя происходит на агрегате из трех вальцов 2130 660/660, фрикция 1:1,07.
На приемных вальцах, используя выносной транспортер, смесь перемешивается и по перекидному транспортеру передается на питательные вальцы. На питательных вальцах смесь обрабатывается и в виде ленты подается в агрегат фестонного типаАФТ-15.
Режим обработки смеси на агрегате из трех вальцов вальцах приведен в таблице 18.
Таблица 18- Обработка смеси после резиносмесителя
Наименование операции | Время, мин | ||
Начала операции | Продолжительность операции | ||
Принять смеси на вальцы пропустить через зазор 2−3 раза, срезать до малого запаса | |||
Добавить срезанную смесь, сделать 2−3 подреза с каждой стороны, пропустить рулоном через зазор 3−4 раза | |||
Срез смеси листами | |||
Общая продолжительность цикла, мин — 8 | |||
В агрегате фестонного типа АФТ-15 лента резиновой смеси охлаждается обдувом воздуха с помощью осевых вентиляторов. Температура смеси после охлаждения в агрегате фестонного типа АФТ-15 не должна превышать 50 °C.
Охлажденная резиновая лента автоматически укладывается на паллету, взвешивается с регистрацией данных по массе, затем от каждой заправки паллеты на уровне отметок указанных на линейке с диапазоном измерения от 0 до 1000 миллиметров отбирают образцы для анализа в контрольной лаборатории.
Периодичность контроля: каждая загрузка.
Паллеты с резиновой смесью электропогрузчиком устанавливают в ячейки склада резиновых смесей для хранения. Продолжительность вылежки смеси перед пуском в производство не менее 4 ч.
При получении результатов анализа из контрольной лаборатории «годен» смесь передают в производство, «брак» изолируют от годной продукции и отправляют в изолятор брака.
4.2 Контроль качества
Основной целью контроля является проверка соответствия сырья, материалов, полуфабрикатов и готовой продукции установленным требованиям в нормативной документации.
В проекте применяются следующие виды контроля:
— входной контроль сырья и материалов;
— контроль технологических процессов;
— контроль готовой продукции.
Сырьё и материалы, поступающие на завод проверяются на соответствие нормам контроля, предусмотренными нормативной документацией.
Система контроля технологических параметров складывается из:
— самоконтроля и взаимного контроля непосредственных исполнителей;
— контроля со стороны мастеров и работников цехов за исполнением рабочих инструкций и требований технологического регламента;
— специального контроля, организуемого инженерно-технической службой завода.
Контроль технологических параметров (температура, продолжительность смешения) при изготовлении резиновых смесей проводится в соответствии с технологической картой.
Готовые резиновые смеси должны отвечать требованиям норм экспресс-контроля и физико-механических испытаний резин. Смеси передают в производство только после положительного заключения инженерно-технической службы завода.
Качество смесей определяют по изменению показателей физических или механических свойств сырой смеси или ее вулканизатов при сравнении их с эталонами или средними статистическими результатами. Наиболее часто качество смеси оценивают экспресс-методом по плотности смеси, кольцевому модулю, пластичности, изменению модуля сдвига. Качество смеси можно также охарактеризовать по свойствам вулканизатов: по прочности при растяжении, относительному и остаточному удлинениям, твердости и другим факторам, а также по разбросу показателей (дисперсии) при испытании.
Нормы контроля технологического процесса приведены в таблице 19.
Таблица 19 — Нормы контроля технологического процесса
Наименование технологической операции | Контролируемый параметр | Норма | Периодичность контроля | Метод контроля | Контролирует | План реагирования на несоответствия | |
Входной контроль | Соответствие ТУ и стандартам | В соответствии с картой входного контроля | В соответствии с картой входного контроля | В соответствии с ТУ и стандартами | Контролер ОТК, лаборант ЦЗЛ | Повторный контроль сырья, выборочный контроль сырья перед развеской | |
Декристализация СКИ-3 | Температура | 60−80°С | Периодически в течении смены | Измерение потенциометром | Мастер смены | Привести в соответствие | |
Один раз в сутки | Контролер ОТК | Поставить в известность мастера смены | |||||
Время | В секционной камере 3−5 часов, в распарочной камере не менее 24 часов | Каждая загрузка | Измерение по часам | Мастер смены. Запись в журнале | Привести в соответствие | ||
Выборочно, но не реже 1 раза в неделю | Контролер ОТК | Поставить в известность мастера смены | |||||
Развеска каучуков | Масса загрузки | В соответствии с ТР и производственным рецептом на рез. смеси | Сплошной контроль | Взвешивание на весах | Составитель навесчик | Поставить в известность мастера цеха | |
Выборочно 2 загрузки в смену | Мастер цеха | Привести в соответствие | |||||
Контролер ОТК | Поставить в известность мастера цеха | ||||||
Разогрев и фильтрация мягчителей | Внешний вид | Исправность сетки | Периодически в течении смены | Визуально | Мастер смены | Привести в соответствие (замена сетки) | |
Развеска мягчите лей | Масса загрузки | В соответствии с ТР и производственным рецептом на рез. смеси | Сплошной контроль | Взвешивание на весах | Составитель навесчик | Поставить в известность мастера цеха | |
Выборочно 2 загрузки в смену | Мастер цеха | Привести в соответствие | |||||
Контролер ОТК | Поставить в известность мастера цеха | ||||||
Просев сыпучих ингредиентов | Наличие отсева | Отсутствие отсева | Сплошной контроль | Протирка вручную через контрольное сито | Составитель навесчик | Поставить в известность мастера цеха | |
Выборочно 2 загрузки в смену | Мастер цеха | Привести в соответствие | |||||
Контролер ОТК | Поставить в известность мастера цеха | ||||||
Развеска сыпучих ингредиентов | Масса загрузки | В соответствии с ТР и производственным рецептом на рез. смеси | Сплошной контроль | Взвешивание на весах | Составитель навесчик | Поставить в известность мастера цеха | |
Мастер цеха | Привести в соответствие | ||||||
Выборочно 2 загрузки в смену | Контролер ОТК | Поставить в известность мастера цеха | |||||
Изготовление резиновых смесей | Время | В соответствии с ТР и произвоственным рецептом на рез. смеси | Каждая загрузка | Измерение по режимным часам | Машинист резиносмесителя, вальцовщик | Поставить в известность мастера цеха | |
Толщина снимаемого листа | В соответствии с ТР и производственным рецептом на рез. смеси | Выборочно 2 загрузки в смену | Измерение толщиномером | Мастер цеха | Привести в соответствие | ||
Контролер ОТК | Поставить в известность мастера цеха | ||||||
Температура охлаждающей воды в ванне охлаждения | В соответствии с ТР и производственным рецептом на рез. смеси | При переходе на летние-зимние режимы в течении 2 недель | Измерение термометром | Контролер ОТК | Поставить в известность начальника ЦЗЛ | ||
Экспресс контроль | В соответствии с ТР и производственным рецептом на рез. смеси | В соответствии с ТР, РК на рез. смеси | В соответствии со стандартами на контролируемые показатели | Лаборант ЦЗЛ | Поставить в известность начальника физ.-мех. сектора ЦЗЛ | ||
Физико-механические показатели | В соответствии с ТР и производственным рецептом на рез. смеси | В соответствии с ТР, РК на рез. смеси | В соответствии со стандартами на контролируемые показатели | Лаборант ЦЗЛ | Поставить в известность начальника физ.-мех. сектора ЦЗЛ | ||
Внешний вид | В соответствии с ТУ | Выборочно 2 загрузки в смену | Визуально | Мастер смены | Возвратить на переработку | ||
Контролер ОТК | Поставить в известность мастера цеха | ||||||
Таблица 20 — Нормы контроля по физико-механическим показателям резин для изготовления опорных частей.
Показатель | Марка смеси 7-ИПР-1347 | |
Условная прочность при растяжении, МПа | не менее 16,7 | |
Твердость по Шору А, ед. Шора А | 47−57 | |
Относительное удлинение при разрыве %, | не менее 550 | |
Температурный предел хрупкости, 0С, | не выше минус 55 | |
Прочность связи резины с металлом при отрыве, МПа | не менее 2,45 | |
Таблица 21 — Нормы контроля по физико-механическим показателям резин для изготовления уплотнителя стекла.
Показатель | Марка смеси 7−6190П | |
Условная прочность при растяжении, МПа | 4,4 | |
Твердость по Шору А, ед. Шора А | 60−75 | |
Относительное удлинение при разрыве %, | ||
Температура хрупкости при замораживании, С, не выше | Минус 40 | |
Относительная остаточная деформация после старения в воздухе при постоянной величине сжатия 20% при 100С в течении 24 часов, не более | ||
5. Материальный баланс
Расчет годового и суточного выпуска каждого вида продукции с учетом испытаний готовых изделий.
Таблица 22 — Расчет объема выпуска изделий
Вид изделия | Объем выпускаемой продукции, тонн | Отбор изделий на анализы и испытания в год | Объем выпуска с учетом испытаний и анализа готовой продукции, тонн | ||||
в год | в сутки | % | шт. | в год | в сутки | ||
РОЧ | 20,08 | 0,1 | 5,00 | 20,10 | |||
Уплотнитель стекла | 16,06 | 0,00 | 16,06 | ||||
итого | 36,16 | ||||||
Расчет норм расхода резиновых смесей представлен в таблице 23.
Таблица 23 — Расчет норм расхода резиновых смесей
Изделия | Чистый расход на 1 т, кг | Потери от веса готовой продукции, % | Итого потерь на 1000 изделий, кг | Нормы расхода с учетом потерь, кг | |||||||
смешение | вулканизация | разогрев | Шприцевание | анализ смеси | Каландрование | Итого | |||||
РОЧ | 0,6 | 0,2 | 0,1 | 0,2 | 3,1 | 31,00 | 1031,0 | ||||
Уплотнитель стекла | 0,6 | 0,2 | 0,2 | 10,00 | 1010,0 | ||||||
Таблица 24 — Потребность в каучуках и ингредиентах на годовую программу
Наименование ингредиентов | Потребность материалов по рецептам, т | Всего, т | потери, % | Потребность с учетом потерь, т | |||||
РОЧ | уплотнитель стекла | ||||||||
Содержание в смеси по рецепту, % | 5160,16 | Содержание в смеси по рецепту, % | 4040,00 | В год | В сутки | ||||
Каучук СКМС-30АРКМ-15 | 34,64 | 1399,5 | 1434,10 | 0,1 | 1435,53 | 5,77 | |||
Каучук СКИ-3 | 48,39 | 2497,0 | 2545,39 | 0,1 | 2547,93 | 10,23 | |||
СКД | 16,13 | 832,33 | 848,46 | 0,1 | 849,31 | 3,41 | |||
Белила цинковые А | 9,68 | 499,50 | 1,04 | 42,02 | 552,24 | 563,28 | 2,26 | ||
Сера | 1,29 | 66,57 | 0,07 | 2,83 | 70,75 | 1,5 | 71,82 | 0,29 | |
Сульфенамид Ц | 0,64 | 33,02 | 0,07 | 2,83 | 36,56 | 1,5 | 37,11 | 0,15 | |
Диафен ФП | 1,29 | 66,57 | 67,86 | 69,21 | 0,28 | ||||
Тиурам Д | 0,83 | 33,53 | 34,36 | 35,05 | 0,14 | ||||
Стеарин | 0,65 | 33,54 | 0,69 | 27,88 | 62,76 | 64,01 | 0,26 | ||
Техуглерод Т 900 | 5,33 | 215,33 | 220,66 | 227,28 | 0,91 | ||||
Техуглерод П 803 | 9,68 | 499,50 | 41,57 | 1679,4 | 2230,18 | 2297,09 | 9,23 | ||
Техуглерод П 234 | 9,68 | 499,50 | 509,18 | 524,46 | 2,11 | ||||
Нафтам-2 | 0,64 | 33,02 | 33,66 | 34,34 | 0,14 | ||||
Масло И-12А | 8,00 | 323,20 | 331,20 | 337,82 | 1,36 | ||||
N-нитрозо-дифениламин | 0,35 | 14,14 | 14,49 | 1,5 | 14,71 | 0,06 | |||
Ацетонанил Н | 1,04 | 42,02 | 43,06 | 43,92 | 0,18 | ||||
Паралайт-17 | 1,04 | 42,02 | 43,06 | 1,5 | 43,70 | 0,18 | |||
Воск ЗВ-П | 0,64 | 33,02 | 33,66 | 1,5 | 34,17 | 0,14 | |||
Битум нефтяной | 1,29 | 66,57 | 5,33 | 215,33 | 288,52 | 294,29 | 1,18 | ||
Итого | 100,00 | 5160,2 | 100,00 | 4040,0 | 9400,16 | 32,8 | 9525,03 | 38,25 | |
6. Расчет потребного количества оборудования
Расчет количества резиносмесителей для приготовления резиновой смеси для опорных частей, требуемой для выпуска 5000 т изделий в год.
Исходные данные:
· потери при изготовлении резиновой смеси — 3,1%;
· масса загрузки в резиносмеситель РС-270−20M = 183,6 кг;
· продолжительность изготовления резиновой смеси ?1 = 10 мин.
Расчет номинального фонда времени работы оборудования:
Фн=(D-d)*c; (1)
где D — количество календарных дней в году, дни;
d — количество выходных дней в году включая праздники, дни;
c — время работы оборудования в сутки, ч.
По формуле (1) определяем количество часов работы оборудования в год:
Фн=(365-(2*52+12+10))*23=5497 ч.
Расчет времени на остановки оборудования на капитальный, планово-предупредительный и текущие ремонты в год рассчитывается по формуле:
Трем=(Фн*4,3%)/100%; (2)
где 4,3% - отраслевые нормативы остановок на ремонты.
По формуле (2) находим количество часов на остановку оборудования на ремонт:
Тост=5497*4,3/100=236,4 ч.
Эффективное время работы оборудования рассчитываем по формуле:
Фэф=Фн-Тост; (3)
По формуле (3) находят эффективное время работы оборудования:
Фэф=5497−236,4=5260,6 ч
Расчет количества резиновой смеси, необходимого для выпуска заданного количества изделий:
Общее число изделий, производимых в год:
Nобщ=N+Nпот; (4)
По формуле (4) рассчитываем общее число изделий в год:
Nобщ = 5 000 000 кг.
Количество резиновой смеси, теряемой при изготовлении, определяется по формуле:
Рпот=(Р*3,1) /100; (5)
где 3,1% - процент потерь резиновой смеси при изготовлении.
По формуле (5) рассчитываем потери резиновой смеси:
Рпот = (5 000 000*3,1)/100 = 160 000 кг
Общее количество резиновой смеси находим по формуле:
Робщ = Р+Рпот; (6)
По формуле (6) рассчитываем общее количество резиновой смеси
Робщ = 5 000 000+160000 =5 160 000 кг
Рассчитываем производительность оборудования по изготовлению резиновой смеси по формуле:
Q=М*0,95/?i (7)
где 0,95- коэффициент использования машинного времени;
?i — продолжительность изготовления резиновой смеси, мин.
По формуле (7) находим производительность оборудования:
Q = М*0,95/?1 = (183,6*0,95*60)/10 = 1046,52 кг/ч;
Расчет количества часов работы оборудования:
Тмаш.ч=Робщ/Q; (8)
По формуле (8) рассчитываем количество часов работы оборудования:
Тмаш.ч = Робщ/Q = 5 160 000/1046,52 = 4930,62 маш.ч.;
Расчет количества смесителей:
n= Tмаш.ч/Фэф; (9)
По формуле (9) рассчитываем количество резиносмесителей:
n= Tмаш.ч/Фэф = 4930,62/5260,6 = 0,94;
Расчет количества резиносмесителей для приготовления резиновой смеси для уплотнителя стекла, требуемой для выпуска 4000 т изделий в год.
Исходные данные:
· потери при изготовлении резиновой смеси — 1,1%;
· масса загрузки в резиносмеситель РС-270−20M = 187,77 кг;
· продолжительность изготовления резиновой смеси ?1 = 13 мин.
Расчет номинального фонда времени работы оборудования:
По формуле (1) определяем количество часов работы оборудования в год:
Фн=(365-(2*52+12+10))*23=5497 ч.
Расчет времени на остановки оборудования на капитальный, планово-предупредительный и текущие ремонты в год рассчитывается по формуле:
По формуле (2) находим количество часов на остановку оборудования на ремонт:
Трем=5497*4,3/100=236,4 ч.
По формуле (3) находят эффективное время работы оборудования:
Фэф=5497−236,4=5260,6 ч
По формуле (4) рассчитываем общее число изделий в год:
Nобщ = 4 000 000 кг.
По формуле (5) рассчитываем потери резиновой смеси:
Рпот = (4 000 000*1,1)/100 = 44 000 кг
По формуле (6) рассчитываем общее количество резиновой смеси
Робщ = 4 000 000+44000 =4 044 000 кг
По формуле (7) находим производительность оборудования:
Q = М*0,95/?1 = (187,77*0,95*60)/13 = 823,3 кг/ч;
По формуле (8) рассчитываем количество часов работы оборудования:
Тмаш.ч = Робщ/Q = 4 044 000/823,3 = 4911,94маш.ч.;
По формуле (9) рассчитываем количество резиносмесителей:
n= Tмаш.ч/Фэф = 4911,94/5260,6 = 0,93.
Результаты расчетов приведены в таблице 25.
Таблица 25 — Рассчитанное количество резиносмесителей.
Резиновая смесь для опорных частей | Резиновая смесь для уплотнителя стекла | |
0,94 | 0,93 | |
По результатам, приведенным в таблице 24, можно сделать вывод, что необходимо два резиносмесителя для приготовления данных резиновых смесей.
Таблица 26 — Подбор весов для автоматической развески ингредиентов для изготовления опорных частей
Ингредиенты | Навеска, кг | Тип весов | Пределы взвешивания, кг | Класс точности | Погрешность, % | |
СКИ-3 | 90,00 | ДТКЧ-120 | 20−120 | +0,1 | ||
СКД | 30,00 | |||||
сера | 2,400 | ОДСС-10 | 1−10 | +0,1 | ||
Сульфенамид Ц | 1,200 | ОДСС-5 | 0,5−5 | +0,1 | ||
Белила цинковые А | 18,00 | ОДСС-20 | 2−20 | +0,1 | ||
Кислота стеариновая | 1,200 | ОДСС-5 | 0,5−5 | +0,1 | ||
Диафен ФП | 2,400 | ОДСС-10 | 1−10 | +0,1 | ||
Техуглерод П 803 | 18,00 | ОДПК-80 | 20−80 | +0,1 | ||
Техуглерод П 234 | 18,00 | |||||
Воск ЗВ-П | 1,200 | ОДСС-5 | 0,5−5 | +0,1 | ||
Битум нефтяной | 2,400 | ОДСС-10 | 1−10 | +0,1 | ||
Нафтам-2 | 1,200 | ОДСС-5 | 0,5−5 | +0,1 | ||
Таблица 27 — Подбор весов для автоматической развески ингредиентов для изготовления уплотнителя стекла
Ингредиенты | Навеска, кг | Тип весов | Пределы взвешивания | Класс точности | Погрешность | |
СКМС-30АРКМ-15 | 65,00 | ДТКЧ-120 | 20−120 | +0,1 | ||
сера | 0,130 | ДСС-1 | 0,2−1 | +0,1 | ||
Тиурам Д | 1,560 | ОДСС-5 | 0,5−5 | +0,1 | ||
СульфенамидЦ | 0,130 | ДСС-1 | 0,2−1 | +0,1 | ||
Белила цинковые А | 2,000 | ОДСС-5 | 0,5−5 | +0,1 | ||
Ацетонанил-Н | 3,000 | ОДСС-10 | 1−10 | +0,1 | ||
Кислота стеариновая | 1,300 | ОДСС-5 | 0,5−5 | +0,1 | ||
N-нитрозоди-фениламин | 0,650 | ДСС-1 | 0,2−1 | +0,1 | ||
Техуглерод Т 900 | 10,00 | ОДПК-80 | 20−80 | +0,1 | ||
Техуглерод П 803 | 78,00 | ОДПК-80 | 20−80 | 1,5 | +0,15 | |
Масло И-12А | 15,00 | 4ДПС-15 | 1−15 | +0,1 | ||
Паралайт-17 | 2,000 | ОДСС-10 | 1−10 | +0,1 | ||
Битум нефтяной | 10,00 | ОДСС-10 | 1−20 | +0,1 | ||
Таблица 28 — Подбор бункеров для сыпучих ингредиентов для изготовления опорных частей.
Наименование ингредиента | Потребность в год, т | Машино-часы | Расход, кг/ч | Рабочий объём бункера, м3 | Насыпная плотность материала, кг/м3 | Максимальная масса запасн. материала в бункере, кг | Время между загрузками, ч | |
Сера | 66,57 | 15,16 | 0,9 | 708,3 | 46,72 | |||
Сульфенамид Ц | 33,02 | 7,52 | 0,9 | 63,42 | ||||
Белила цинковые А | 499,50 | 113,8 | 0,9 | 555,3 | 4,88 | |||
Диафен ФП | 66,57 | 15,16 | 0,9 | 576,9 | 38,05 | |||
Нафтам-2 | 33,02 | 7,52 | 0,9 | 62,22 | ||||
Технический углерод П803 | 499,50 | 113,7 | 0,9 | 170,1 | 1,50 | |||
Технический углерод П234 | 499,50 | 113,8 | 0,9 | 170,1 | 1,50 | |||
Кислота стеариновая | 33,54 | 7,64 | 0,9 | 457,2 | 59,85 | |||
Таблица 29 — Подбор бункеров для сыпучих ингредиентов для изготовления уплотнителей стекла.
Наименование ингредиента | Потребность в год, т | Машино-часы | Рас ход, кг/ч | Рабо чий объём бункера, м3 | Насыпная плотность материала кг/м3 | Максимальная масса запас. материала в бункере, кг | Время между загрузками, ч | |
Cера | 2,83 | 4911,94 | 0,58 | 0,9 | 708,3 | 1230,24 | ||
Тиурам Д | 33,53 | 4911,94 | 6,83 | 0,9 | 327,6 | 47,99 | ||
СульфенамидЦ | 2,83 | 4911,94 | 0,58 | 0,9 | 828,50 | |||
Белила цинковые А | 42,02 | 4911,94 | 8,55 | 0,9 | 555,3 | 64,92 | ||
Ацетонанил-Н | 42,02 | 4911,94 | 8,55 | 0,9 | 476,1 | 55,66 | ||
Кислота стеариновая | 27,88 | 4911,94 | 5,68 | 0,9 | 457,2 | 80,56 | ||
Технический углерод П 803 | 1679,4 | 4911,94 | 341,9 | 0,9 | 170,1 | 0,50 | ||
Технический углерод Т 900 | 215,33 | 4911,94 | 43,84 | 0,9 | 170,1 | 3,88 | ||
N-нитрозоди-фениламин | 14,14 | 4911,94 | 2,88 | 5,36 | 1136,32 | 394,73 | ||
7. Характеристика оборудования
Характеристика оборудования представлена в таблице 29.
Таблица 30 — Сводная ведомость установленного технологического оборудования
Наименование оборудования | Принято к установке, единиц | Коэффициент использования | Техническая характеристика | Габаритные размеры, мм | Масса, т | |
Резиносмеситель 270−20 | 0,97 | Объем камеры 270 дм3, мощность электродвигателя 315 кВт, расход воды 10 м3/ч, расход воздуха 90 м3/ч | 7800×4400×5900 | 6,5 | ||
Агрегат резинообрабатывающих вальцев СМ 2100−660/660 Л3 | 0,92 | Мощность привода 400 кВт, производительность 140−200 дм3/цикл, расход воды 24 м3/ч | 20 950×4200×2495 | 90,6 | ||
Агрегат для отбора и охлаждения резиновой смеси АФТ-15М | 0,92 | Мощность двигателей 19,2 кВт, производительность 2,5 т/ч, расход воды 0,022 м3/ч | 12 000×3400×2900 | 8,5 | ||
Питатель | 0,98 | Размеры исходной ленты 600×6?12 мм, скорость транспортера 1?10 м/мин, ширина нарезаемой зигзагообразной ленточки 60?100 мм, установленная мощность эл/двигателей 3 кВт, давление воздуха в пневмосистеме 0,4?0,6 МПа | 270×1500×3200 | 1,6 | ||
Транспортер отборочный | 0,91 | Линейная скорость транспортерной ленты 1,5?15 м/мин, ширина транспортерной ленты 150 мм, мощность привода 1,1 кВт | 2895×430×3115 | 0,3 | ||
8. Должностные обязанности К самостоятельной работе допускаются рабочие, обученные безопасным методам работы, правилам охраны труда, технологии производства, сдавшие экзамен квалификационной комиссии и прошедшие стажировку на рабочем месте.
8.1 Обязанности помощника машиниста резиносмесителя
До начала работы
— Принять рабочее место, которое должно быть чистым, свободным от посторонних предметов, хорошо освещенным.
— Проверить наличие и исправность ограждений на приводах питающей установки внешним осмотром.
— Узнать у машиниста резиносмесителя задание по приготовлению резиновых смесей на смену.
— Визуально убедиться в целостности кнопочных пультов управления.
— При обнаружении недостатков сообщить оператору САУ о принятии мер к их устранению, а в случае невозможности устранения своими силами, доложить мастеру и к работе не приступать.
Во время работы
— Следить за чистотой и порядком на рабочем месте.
— Контролировать в течение смены соответствие шифра смеси по паспорту (аншлагу), сопровождаемому навески сыпучих ингредиентов с участка централизованной развески, шифру смеси, подписанному на пакетах с навесками сыпучих ингредиентов, и массу навесок по показаниям, высвечивающимся на сенсорном экране пульта управления развеской при комплектовании общей навески на весовом транспортере.
— С целью усреднения резиновых смесей заправлять ленты резиновой смеси при подаче на питающий транспортер с двух платформ, соблюдая требования охраны труда.
— Следить за внешним видом резиновой смеси, не допуская попадания смеси загрязненной, с посторонними или заварными включениями.
— Выполнять требования настоящей инструкции и инструкции по охране труда.
По окончании работы
— Произвести уборку на рабочем месте, вычистить оборудование.
— О замеченных недостатках в работе оборудования сообщить сменщику и мастеру.
8.2 Обязанности машиниста резиносмесителя
Обязанности машиниста резиносмесителя до начала работы.
— Принять рабочее место, которое должно быть чистым, свободным от посторонних предметов, хорошо освещенным.
— Проверить наличие и исправность ограждений на приводах резиносмесителя, весового и загрузочного транспортеров, весовых площадок, лестниц проверить внешним осмотром.
— Проверить работу систем аспирации и вентиляции.
— Проверить чистоту весового транспортера.
— Проверить работу системы охлаждения резиносмесителя. Должны быть открыты:
* главная агрегатная задвижка оборотной воды;
* вентили переднего и заднего роторов смесительной камеры, стенок камеры, нижнего затвора, верхнего затвора;
— Убедиться в наличии воды, поступающей на охлаждение резиносмесителя.
— Проверить связь с оператором системы автоматического управления (САУ).
— Проверить наличие на рабочем месте инструкций, рецептов.
— Визуально убедиться в исправности кнопочных пультов управления.
— Убедиться в наличии материалов в бункерах (серы, ускорителей, модификатора и сантогарда), для чего на пульте управления развеской ингредиентов нажать кнопку «сборники весы». При уровне материала в бункере выше заданного минимального значения, на сенсорном экране высвечивается «ДА» на зеленом фоне, если уровень материала находится ниже минимального уровня — высвечивается «НЕТ» на красном фоне, в этом случае необходимо сообщить оператору САУ о необходимости засыпки ингредиентов в расходные бункера.
— Сообщить оператору САУ данные по используемым промежуточным стадиям (шифр смеси, дата, смена изготовления, номер резиносмесителя, номер платформы) и навескам материалов, добавляемым вручную (наименование материала, дата и смена комплектования навески).
— Обнулить ленточные весы, нажав кнопку «Тара».
— При обнаружении недостатков сообщить оператору САУ и принять меры к их устранению путем управления операциями в ручном режиме. В случае невозможности устранения неполадок своими силами доложить мастеру, к работе не приступать до их устранения.
Во время работы
— Следить за чистотой и порядком на рабочем месте.
— Контролировать, чтобы все материалы полностью загружались в резиносмеситель. В случае застревания резиновой смеси в воронке резиносмесителя, сообщить оператору САУ и принимать меры по устранению застревания, соблюдая правила охраны труда. В случае налипания резиновой смеси на нижний затвор необходимо остановить резиносмеситель, нажав последовательно кнопки «Резиносмеситель — стоп», и «подготовка — стоп», вывешивает на пульт управления табличку «Не включать — работают люди». Сообщитьоператору о необходимости вызова дежурного слесаря. Слесарь, с помощью шестигранного ключа, на гидростанции отводит до нужного положения нижний затвор. Машинист резиносмесителя приступает к чистке нижнего затвора. По окончании чистки, машинист резиносмесителя включает подготовку, и нажимает кнопку «нижний затворзакрыть». В случае успешной фиксации нижнего затвора загорается лампа «нижний затворзакрыт», в противном случае необходимо продолжить чистку.
— Контролировать в течение смены правильность навешивания материалов. В случае нарушения дозирования (недовес, перевес) принять меры для внесения поправок путем управления операциями в ручном режиме.
— Контролировать в течение смены соответствие шифра используемых промежуточных стадий рецепту изготавливаемого шифра резиновой смеси, соответствие оттиска на используемой резиновой смеси шифру, указанному в паспорте на резиновую смесь.
— Паспорта на использованную резиновую смесь хранить в специально отведенном месте у питательной установки. При неполном использовании паспорта должны быть приложены к остатку резиновой смеси на платформе, на остатке на верхнем листе должна быть сделана запись мелом дата, смены, шифр резины.
— Своевременно и правильно срабатывать возвратные детали, согласно рецептам резиновых смесей.
— Периодически в течение смены проверять работу всех механизмов, системы охлаждения резиносмесителя и системы аспирации. При обнаружении неисправностей немедленно сообщить мастеру смены.
— При переходе с одного шифра на другой, заранее подготовить необходимые резиновые смеси.
— Забракованные промежуточные стадии резиновых смесей и возвратные детали резиновых смесей, хранить в только в изоляторе брака;
— Не допускать в работу резиновые смеси, имеющие видовые дефекты, не имеющие паспортов и маркировки;
По окончанию работы
— Убрать рабочее место и закрепленное оборудование.
— Остановить резиносмеситель кнопкой «стоп», затем нажать на кнопку «подготовка — СТОП» и сообщить оператору САУ об окончании работы.
— Перекрыть вентили системы охлаждения.
— Почистить нижний затвор и место выгрузки резиновой смеси.
— Сдать рабочее место сменщику, сообщив обо всех замеченных недостатках за истекшую смену. Работающее оборудование без присмотра оставлять запрещается.
8.3 Обязанности оператора
Обязанности оператора САУ до начала работы
— Принять в чистоте и порядке рабочие панели и пультовый зал.
— Принять журнал учёта простоев оборудования, журнал учёта изготовления резиновых смесей, журнал учёта выработки резиновых смесей по шифрам, журнал регистрации работы прибора PPA у оператора, сдающего смену, сделать запись о выявленных замечаниях и поставить свою подпись о приеме смены.
— Узнать у сдающего смену оператора произошедшие изменения в работе питателей, прибора PPA и обо всех других замечаниях и неисправностях, которые встречались во время работы и как они устранялись.
— Ознакомиться под роспись со всеми технологическими распоряжениями в журнале регистрации технологических указаний по работе производства.
— Проверить наличие рабочих рецептурных карт и соответствие рецептов и режимов согласно последним технологическим распоряжениям, в случае наличия указаний на рецептурные изменения, произвести соответствующие изменения в САУ.
— При приеме смены проверить правильность выставленного рецепта и режима изготовления, для чего необходимо выбрать «F6 — Рецептура». Сверить фактические данные с заданными (рецепт, режим смешения, параметры настройки оборудования: температуру охлаждающей воды, аварийную температуру выгрузки, периодичность смазки сальников).
Обязанности оператора САУ во время работы
— Осуществлять проверку правильности взвешивания материалов на экране управления резиносмесителем (первые три заправки и при смене шифра) и по отчётам SQL.
— Поддерживать связь с рабочим местом машиниста резиносмесителя, вальцовщика, холодильщика, составителя навесок ингредиентов.
— Следить за чистотой рабочего места и пультового зала.
— Своевременно при переходе на изготовление резиновых смесей нового шифра сменить задание в программе управления, выбрав «F6- Рецептура», при необходимости произвести перестройку рецепта или режима изготовления и установить температуру выгрузки смеси согласно выданным режимам с учетом технологических распоряжений, сообщить холодильщику о массе заправки резиновой смеси.
— По информации от холодильщика изменять задание в программе управления прибором PPA.
— Регулярно и своевременно вносить в журнал учёта выработки резиновых смесей по шифрам:
*дату, смену;
*шифр изготавливаемой смеси;
*количество заправок изготовленной резиновой смеси данного шифра;
*партии используемых каучуков, продуктов переработки;
*дату, смену и номер платформы используемых «циклов» резиновых смесей, используемых возвратных отходов;
*дату и смену комплектования используемых «красок».
— Регулярно и своевременно вносить в журнал учета простоев оборудования:
*дату, смену;
*шифр изготавливаемой смеси;
*количество заправок изготовленной резиновой смеси данного шифра;
*время начала и конца простоя и причины простоя;
*другие замечания по работе.
— Регулярно и своевременно вносить в журнал регистрации работы прибора PPA:
*дату, смену;
*шифр анализируемой резиновой смеси;
*номер паллеты и количество заправок на паллете;
*отмечать надписью «брак» те заправки, которые вышли браком по прибору PPA
*замечания по работе.
— Внимательно следить за работой всей аппаратуры САУ по экрану монитора.
— Внимательно следить за результатами анализа резиновых смесей на приборе PPA
— Своевременно и четко давать указания составителю навесок ингредиентов на заправку бункеров РС необходимыми ингредиентами.
— Обо всех замечаниях в работе резиносмесителей и приборов PPA докладывать старшему оператору, мастеру смены и сменному наладчику ЦПЭиЭА.
— Содержать в порядке и чистоте рабочее место.
— Не допускать присутствия в пультовом зале посторонних лиц без сопровождения ответственных работников цеха.
По окончании работы
— Привести в порядок рабочее место и панели управления.
— Сдать смену оператору, принимающему смену, с сообщением обо всех изменениях в рецептах, работе питателей, весов, а также сообщить обо всех неисправностях, встречающихся во время работы, и как они устранялись.
8.4 Обязанности вальцовщика
До начала работы
— Принять рабочее место, которое должно быть чистым, свободным от посторонних предметов, хорошо освещенным.
— Проверить наличие и исправность инструмента (щетки-сметки, совка), дисковых пневмоножей и их крепления, ограждений вращающихся частей оборудования, целостность кнопочных выключателей и пультов управления.
— Внешним осмотром проверить отсутствие в зазоре посторонних предметов, а также отсутствие просыпавшихся ингредиентов за стрелами вальцов.
— Убедиться, что вентили на системе охлаждения открыты.
— Включить насос подачи охлаждающей воды, для чего на щите управления насосной установкой нажать зеленую кнопку «I».
— Убедиться в отсутствии на барабанах, роликах, транспортерной ленте налипшей резиновой смеси, при наличии — вычистить.
— Включить в работу систему вентиляции УФТ и систему циркуляции изолирующего состава в ванне.
— Проверить уровень изолирующего состава. В случае, низкого уровня эмульсии в расходной емкости, долить требуемое количество изолирующего состава, при помощи передвижного насоса. Проверить наличие уровня эмульсии в стакане (показывает заполнение насосной линии эмульсией) передвижного насоса, в случае отсутствия, заливать эмульсию до заполнения. Включить насос. Следить за повышением уровня эмульсии в расходной емкости УФТ. В случае, если насос не качает изолирующий состав, вызвать дежурного слесаря.
— Работа аварийного выключателя проверяется на холостом ходу в соответствии с требованиями инструкции по охране труда. Результаты проверки исправности работы аварийных устройств на вальцах заносятся в специальный журнал с подписью мастера смены, дежурного электрика и вальцовщика.
— Проверить исправность работы транспортеров на холостом ходу.
— Запустить перемешивающее устройство, для чего необходимо нажать кнопку «сток-блендер-пуск» и проверить работу выносного валка и роликов на холостом ходу.
— Установить требуемый зазор на вальцах, контролируя заданное значение на дисплее пульта управления.
— В случае обнаружения неисправностей оборудования или аварийного выключателя доложить мастеру и к работе не приступать до их устранения.
Обязанности вальцовщика во время работы
— Сохранять чистоту и порядок на рабочем месте.
— Соблюдать режим обработки смесей на вальцах.
— Не допускать к работе на вальцах посторонних лиц.
— Соблюдать требования инструкций по охране труда.
— При работе на вальцах с перемешивающим устройством (сток-блендером) не допускать наматывания резиновой смеси на выносной валок. При наматывании резиновой смеси необходимо, остановить вальцы, выключить привод перемешивающего устройства, для чего необходимо нажать кнопку «сток-блендер-стоп», и срезать резиновую смесь с выносного валка.
— При возникновении в процессе работы неисправностей остановить оборудование и доложить мастеру.
По окончании работы
— Отвести дисковые дисковые ножи в нерабочее положение, для чего необходимо на пульте управления дисковыми ножами тумблеры 1,2,3,4 опустить вниз.
— Остановить вальцы кнопкой «стоп» на пультах управления, затем нажать кнопку «подготовка — стоп».
— Вычистить оборудование и навести порядок на рабочем месте. Обо всех недостатках в работе доложить мастеру и сменщику.
8.5 Должностные обязанности мастера участка Мастер участка обязан:
1 Производить расстановку рабочих на участке в соответствии с технологическим процессом.
2 Руководить на своём участке производства, организовать выполнение участком производственного плана по заданной номенклатуре.
3 Обеспечивать выполнение участком плановых заданий по объёму производства, номенклатуре и ассортименту изделий, изготовление качественной продукции.
4 Обеспечивать максимальное использование производственных мощностей, полную загрузку и правильную эксплуатацию оборудования, производственную работу своего рабочего участка на протяжении всей смены.
5 Обеспечивать своевременную подготовку производства материалами, полуфабрикатами, инструментом, приспособлениями, технологической документацией и др., и равномерную работу участка в соответствии с установленным заданием.
6 Систематически проверять выполнение заданий бригадами и отдельными рабочим, своевременно организовывать устранение возникающих неполадок, мешающих нормальному ходу производственного процесса.
7 Организовать решение производственных и социальных вопросов деятельности подразделения в соответствии с КЗоТ.
8 Систематически повышать свою квалификацию на курсах повышения квалификации и т. д.
9 Осуществлять контроль за правильностью и своевременным оформлением первичных документов в части приёма и выдачи работы (наряды, сменные задания и др.), простои рабочих и оборудования, наряды на сверхурочную работу, сведения о выполнении производственной программы.
10 Оказывать подчинённым рабочим необходимую помощь в освоении норм выработки и выполнении производственных заданий, особое внимание уделять инструктажу рабочих в случаях сложности или ответственности выполняемой работы, освоения новых работ.
11 Проверять соблюдение рабочими технологических процессов и прекращать работы в случаях их несоответствия установленным технологическим процессам, техническим условиям, режимам требования охраны труда, промышленной и пожарной безопасности.
12 Обеспечивать безопасное выполнение работ при соблюдении правил охраны труда, промышленной и противопожарной безопасности.
13 Участвовать в перетарификации работ и пересмотре норм выработки.
14 Систематически проверять состояние оборудования и ограждений, проводить инструктаж рабочих и проверку их знаний правил охраны труда, промышленной санитарии, пожарной безопасности и правил пользования средствами индивидуальной защиты, контролировать соблюдение правил и инструкций по охране труда.
15 Проводить своевременный инструктаж и обучение персонала безопасным методам труда. Не допускать к самостоятельной работе лиц, не прошедших проверку знаний по вопросам охраны труда.
16 Проверять состояние особо опасных мест, рабочих мест, оборудования и средств автоматики, соблюдение технологических параметров, требование правил и инструкций по охране труда персоналом участка, с записью выявленных замечаний в журнале трёхступенчатого контроля. Принимать необходимые меры по устранению выявленных нарушений.
17 Отстранять от работы работников участка за нарушение правил охраны труда, промышленной и противопожарной безопасности и нарушение технологии с обязательным сообщением начальнику цеха.
18 Обеспечивать наличие на рабочих местах инструкций, средств индивидуальной защиты, средств пожаротушения и правильное их использование.
19 Обеспечивать соблюдение рабочими трудовой и производственной дисциплины. Контролировать своевременный вывоз отходов и готовой продукции.
20 Привлекать рабочих к участию в работе производственных совещаний и обсуждению вопросов выполнения установленных участку заданий, к освоению приёмов работы передовых рабочих.
21 Создавать в коллективе обстановку взаимной помощи и взыскательности, развивать у рабочих чувство высокой ответственности за выполнение производственных планов (заданий).
22 Давать предложения по повышению квалификации и профессионального мастерства рабочих и бригадиров из числа опытных работников смены.
23 Составлять графики ежегодных отпусков работников всего участка в соответствии с действующим законодательством и коллективным договором.
24 Готовить вопросы и участвовать в работе цеховых дней качества.
25 Оказывать помощь в своевременном расследовании несчастных случаев, пожаров, аварий и инцидентов, и для выявления причин их вызывающих. Принимать участие в разработке и внедрении мероприятий, направленных на предупреждение производственного травматизма, пожаров и аварий в смене.
26 В случае производственной необходимости выполнение работ, не предусмотренных настоящей должностной инструкцией, по указанию начальника цеха или его заместителя.
Права:
Мастер участка имеет право:
1 В случае производственной необходимости временно переводить рабочих на другие рабочие места.
2 Начальнику цеха отличившихся рабочих участка к поощрению по действующим премиальным положениям.
3 Представлять начальнику цеха предложения о наложении дисциплинарных взысканий за нарушение трудовой и производственной дисциплины, нарушение правил охраны труда, промышленной и пожарной безопасности, увольнении в соответствии с трудовым законодательством.
4 Не допускать выполнения работы на неисправном оборудовании и с применением неисправного инструмента, приспособлений и контрольно измерительных приборов, с нарушением правил охраны труда, промышленной и пожарной безопасности, а также на оборудовании, не имеющем ограждений, блокировок и прочих предохранительных средств.
5 Не допускать использования в производстве материалов и полуфабрикатов, не отвечающих техническим требованиям.
6 Не допускать к работе рабочих, не знающих правил и инструкций по охране труда и пожарной безопасности к самостоятельной работе, тех, кто не имеет доступа к самостоятельной работе.
7 Не допускать выполнения работ при использовании сырья и материалов, не отвечающих техническим условиям.
8 Требовать своевременного выполнения плана ремонта оборудования и мероприятий по охране труда, промышленной и пожарной безопасности.
9 Требовать от руководства цеха своевременной выдачи месячных производственных заданий и других планируемых количественных и качественных показателей.
10 Требовать от руководства цеха своевременного обеспечения участка необходимыми материалами, технической документацией и др. для нормального хода производства.
11 Требовать от подчинённых ему работников выполнения распоряжений и указаний по всем вопросам производственной деятельности участка.
12 Участвовать в разработке и обсуждении текущих и перспективных планов исходя из задач наиболее полного использования возможностей и резервов производства, ускорения технического прогресса и совершенствования организации производства и труда.
13 Выдвигать из числа передовых рабочих кандидатуры для назначения распоряжением по структурному подразделению бригадиром, а также вносить предложения об освобождении его от обязанностей бригадира.
14 Принимать участие в присвоении в установленном порядке тарифных разрядов в соответствии с тарифно-квалификационным справочником.
15 Принимать участие в приёмке законченных работ по реконструкции участка, ремонту технологического оборудования, механизации и автоматизации производственных процессов.
Ответственность:
Мастер участка несёт ответственность:
1 За невыполнение производственного задания по количественным и качественным показателям в соответствии с установленным графиком выпуска продукции участком.
2 За качество выпускаемой продукции и соблюдение ГОСТов, технических условий и стандартов СК предприятия.
3 За необеспечение сохранности оборудования, противопожарного и хозяйственного инвентаря.
4 За невыполнение приказов и распоряжений руководства ОАО «ЯШЗ» и указаний начальника цеха. Использование и хранение в рабочем состоянии технологической документации.
5 За экономное расходование сырья, материалов, топлива, электроэнергии и снижение затрат на единицу выпущенной продукции, использования фонда заработной платы.
6 За правильную организацию и достоверность учёта рабочего времени, использования поступающих материалов и полуфабрикатов, выработки готовой продукции с правильным отражением в журналах, нарядах и др. документации.
7 За выполнение всех обязанностей и прав, возложенных на него настоящей должностной инструкцией.
9. Техника безопасности и противопожарная профилактика
В шинном производстве могут возникать опасности для работающих вследствие непредусмотренного контакта людей с оборудованием и материалами, оказывающими вредное действие на человеческий организм, а также нарушений технологического процесса, нежелательного влияния тех или иных условий.
В процессе производства шин применяется большое количество горючих твёрдых, порошкообразных веществ и ЛВЖ (в основном бензин), которые при определённых условиях представляют пожарную опасность для производства.
Большинство применяемых порошкообразных материалов, являющихся ингредиентами резиновых смесей, таких как сера, Н-нитрозодифениламин, тиурам Д, диазоаминобензол, неозон Д, каптакс, альтакс и др. — взрывоопасны и имеют значение нижнего концентрационного предела воспламенения менее 65 г/м3.
Пары бензина с воздухом также могут образовывать опасные концентрации (нижний и верхний концентрационные пределы воспламенения соответственно 1,1 и 5,4% об). При изготовлении клеёв на бензиновой основе и ряде других процессов возможно образование зарядов статического электричества.
Большинство материалов, применяемых в рецептурах резиновых смесей являются токсичными. При несоблюдении установленных правил обращения с такими материалами как фталевый ангидрид, тиурам, ацетонанил Р, бензин и др. у рабочих могут возникнуть профессиональные заболевания.
Производство шин насыщено большим количеством травмоопасного оборудования, с использованием которого рабочие выполняют производственные операции по изготовлению шин. При этом, несмотря на постоянное повышение уровня механизации работ, многие производственные операции выполняются вручную, что создаёт условия, при которых из-за несоблюдения безопасных условий работы возможно травмирование работающих.
При изготовлении резиновых смесей, вальцевании, каландрования, сборке автопокрышек, их вулканизации и других операциях существует целый ряд опасностей и неблагоприятных факторов, влияющих на условия труда работающих.
Опасные и вредные производственные факторы, существующие в шинном производстве, можно подразделить на физические, химические и физико-химические.
К физически опасным и вредным производственным факторам относится следующее:
1 Движущиеся части машин и механизмов. Защита от травмирования движущимся оборудованием выполняется ограждением опасных зон и узлов и различными аварийно-блокировочными устройствами.
2 Микроклимат производственных помещений. При вулканизации автопокрышек используются энергетические ресурсы, такие как сжатый воздух, перегретая вода и пар, охлаждающая вода с давлением 10 кгс/см2 и более. Такие теплоносители, кроме угрозы травмирования работающих, создают неблагоприятные микроклиматические условия производственных помещений.
Для создания нормальных микроклиматических условий в производственных помещениях устраиваются вентиляционные системы. Устройство приточной вентиляции с подачей тёплого воздуха, тамбуров, защитных стенок, воздушных тепловых завес, а также совершенствование технологии, механизация и автоматизация производственных процессов в сочетании с оздоровительными мероприятиями предупреждают работающих от воздействия этого опасного производственного фактора.
3 Производственный шум, защитой от которого является применение более современной технологии, рациональное размещение оборудования, применение звукоизолирующих, звукопоглощающих конструкций и материалов и использование ср едств индивидуальной защиты.
4 Электробезопасность установок. При неисправности электрооборудования или нарушении правил его эксплуатации происходить электротравмы, а также возникать его перегрев или появление искровых разрядов, которые при наличии горючей среды приведут к пожару или взрыву. Защита от поражения электрическим током обеспечивается различными путями, но главная роль отводится качеству изоляции токоведущих частей.
5 Статическое электричество. Заряды статического электричества представляют серьёзную пожарную опасность, оказывают неблагоприятное биологическое воздействие на работающих, ухудшают условия труда. Для борьбы со статическим электричеством используется комплекс мероприятий, определяемых «Правилами защиты от статического электричества».
Вновь прибывшего на завод рабочего сначала инструктируют по технике безопасности. Затем обучающий рассказывает рабочему теоретические основы его работы, безопасные приёмы. Потом собирается комиссия и рабочий, прошедший обучение, сдаёт экзамен. Только после этого пишется приказ о допуске его к работе.
Трудовой распорядок:
— запрещается принимать алкогольные напитки;
— нельзя выполнять работу, которой не обучен или которую не поручали;
— если рабочий получил травму, он обязан сообщить об этом мастеру или обратиться в медпункт.
Существуют цеховые здравпункт и центральный здравпункт, работающий круглосуточно.
Классификация несчастных случаев.
1) Производственная травма. Может быть получена на рабочем месте, если выполняется работа по заданию администрации или получена в рабочее время.
2) Травма связанная с работой, то есть по пути на работу, с работы; с выполнением общественных обязанностей.
3) Бытовые травмы. Эти травмы не оплачиваются в течение пяти дней, а с шестого оплачивается определенный процент от заработанной платы.
Противопожарная техника безопасности Противопожарной техникой безопасности является система мероприятий по предупреждению пожаров и борьбе с ними. Цех должен быть обеспечен первичными средствами пожаротушения и пожарным инвентарем, таким как:
— асбестовые одеяла;
— огнетушители;
— звуковые пожарные извещатели.
Расположение первичных средств пожаротушения и пожарного инвентаря должно быть согласованно с местными органами пожарной охраны.
Необходимые пожарные мероприятия:
— первичный пожарный инструктаж, а затем инструктаж на рабочем месте;
— курение допускается только в специально отведённых и оборудованных местах с надписью «место для курения».
— для хранения резиновой смеси необходимо предусматривать специальные места, согласованные с пожарной охраной.
Общие положения
Ответственность за обеспечение мер пожарной безопасности и проведение профилактических мероприятий в цехах, отделах, лабораториях и мастерских несут их руководители, а во время отсутствия последних — лица, исполняющие их обязанности. Начальники смен, мастера несут ответственность за соблюдение противопожарного режима в цехе (на участке), сохранность противопожарного инвентаря и боеготовность цеховых противопожарных расчётов.
Члены боевого противопожарного расчёта должны чётко знать, соблюдать сами и требовать от других выполнения правил пожарной безопасности, следить за исправностью средств пожаротушения и связи, а в случае возникновения пожара активно выполнять обязанности по его тушению.
Все рабочие, инженерно-технические работники и служащие при поступлении на работу должны получать первичный инструктаж в пожарной части объекта, а так же повторный непосредственно на рабочем месте.
Периодический инструктаж всех рабочих и служащих проводится два раза в год лицом, ответственным за пожарную безопасность цеха, причём этот инструктаж обязательно должен проводиться при перемещении рабочих и служащих с одного рабочего места на другое.
Все рабочие, ИТР и служащие должны проходить специальную противопожарную подготовку в системе производственного обучения по специальной программе, утверждённой главным инженером завода, с периодичностью один раз в три года.
По окончании прохождения инструктажа и занятии по пожарно-техническому минимуму у рабочих, ИТР и служащих должны быть приняты зачёты с оформлением соответствующих документов.
Каждый работающий на заводе обязан чётко знать и строго выполнять установленные правила пожарной безопасности, не допускать действий, могущих привести к пожару или загоранию.
Лица, виновные в нарушении настоящих правил, в зависимости от характера нарушений и их последствий, несут ответственность в дисциплинарном, административном и судебном порядке.
Действия при возникновении пожара (загорания) Исход пожара во многом зависит от того, насколько своевременно была вызвана пожарная помощь, как обеспечен объект первичными средствами пожаротушения, их состоянием и готовностью к действию рабочих, ИТР и служащих по тушению очага пожара.
Каждый рабочий или служащий обнаруживший загорание, обязан:
· Немедленно сообщить об этом в пожарную часть по телефону 01 или по извещателю электрической пожарной сигнализации;
· Приступить к тушению очага пожара имеющемся в цехе, на складе или рабочем месте средствами пожаротушения (огнетушитель, внутренний пожарный кран, песок, абсоткань, стационарная установка пожаротушения) с привлечением рабочих;
· Срочно вызвать к месту пожара начальника цеха, смены, участка или другое должностное лицо, известить ст. диспетчера завода по телефону 15−82.
· Начальник цеха, смены или другое должностное лицо, прибывшее к месту пожара, обязано:
· Проверить, вызвана ли пожарная помощь;
· Поставить в известность о пожаре руководство завода;
· Возглавить руководство тушением пожара до прибытия пожарной помощи;
· Организовать встречу пожарных подразделений;
· Проверить включение и работу автоматических систем пожаротушения;
· Организовать при необходимости отключение электроэнергии, остановку транспортирующих устройств и оборудования, перекрытие сырьевых, паровых и водяных коммуникаций, остановку системы вентиляции и осуществление других мероприятий, способствующих предотвращению распространения пожара;
· Удалить из помещения за пределы цеха или опасной зоны рабочих и служащих, не занятых ликвидацией пожара;
· В случае угрозы для жизни людей, немедленно организовать их спасение, исползуя для этого все имеющиеся силы и средства; при необходимости вызвать медицинскую службу. Прекратить все работы, не связанные с пожаротушением;
· Обеспечить защиту людей, принимающих участие в тушении пожара, от возможных взрывов, обрушений конструкций, поражений электрическим током, отравлений, ожогов.
По прибытии подразделений пожарной охраны должностное лицо, руководившее тушением пожара, обязано сообщить старшему начальнику подразделений пожарной охраны все необходимые сведения об очаге пожара, мерах, принятых по его ликвидации, а также о наличии в помещениях людей, занятых ликвидацией пожара.
При организации руководителем тушения пожара оперативного штаба пожаротушения представители завода (гл. инженер, гл. механик, гл. энергетик, гл. технолог, начальник цеха или другое ответственное лицо) обязаны:
o Консультировать руководителя тушения пожара по вопросам технологического процесса производства и по специфическим особенностям горящего объекта;
o Обеспечить штаб рабочей силой и инженерно-техническим персоналом для выполнения работ, связанных с тушением пожара и эвакуацией имущества;
o Предоставить автотранспорт для подвоза средств, которые могут быть использованы для тушения пожара;
o Корректировать действия инженерно-технического персонала при выполнении работ, связанных с тушением пожара.
Вызов пожарной охраны При возникновении очага пожара (загорания) или при наличии признаков его возникновения каждый рабочий, ИТР и служащий обязан немедленно сообщить в пожарную охрану. Для вызова пожарной помощи на нашем объекте имеется достаточно технических средств — телефонная связь, электрическая пожарная сигнализация, автоматическая пожарная сигнализация.
Телефонная связь — одно из надёжных и общедоступных средств связи. Достаточно набрать две цифры 0 и 1, и вы можете передать сообщение о пожаре. Вызывая пожарную помощь по телефону, необходимо, услышав ответ дежурного радиотелефониста, четко назвать адрес (место пожара), т. е. указать завод, цех, участок, что горит и сообщить свою фамилию. Например: «С вами говорят с шинного завода, в цехе № 2, корпус П — пожар, горит в сушильной камере КЛК-4, сообщает мастер смены Иванов».
Кроме телефонной связи, на объекте имеется электрическая пожарная сигнализация с ручными извещателями ПКИЛ-9, которые установлены в цехах на основных путях эвакуации и снаружи при входе в здание. При сообщении о пожаре по извещателю ПКИЛ-9 необходимо разбить стекло и нажать кнопку, при поступлении ответного гудка убедиться, что сигнализация исправна и сообщение принято.
В тех случаях, когда нет ответного гудка, необходимо воспользоваться другим извещателем или телефонной связью (отсутствие ответного гудка свидетельствует о неисправности сигнализации).
Кроме вышеперечисленных средств оповещения о пожаре на объекте имеются автоматические пожарные сигнализации, извещатели, которые реагируют на такие факторы пожара, как дым, повышение температуры окружающей среды. Для своевременного вызова пожарной помощи следует не только уметь правильно пользоваться средствами связи, но и знать их ближайшее местонахождение в цехе (на участке).
Средства пожаротушения На нашем объекте для тушения пожара используются такие средства, как вода, водяной пар, химическая и воздушно-механическая пена, углекислый газ, сыпучие материалы (песок, каолин), асбестовые покрывала.
Установка водотушения Вода как основное средство для тушения большинства горючих материалов, применяемых в производстве, в очаг пожара подаётся в виде компактных распылённых струй. Все цехи завода имеют внутренний пожарный водопровод с кранами, оборудованный рукавами и стволами.
Порядок использования внутреннего пожарного крана следующий: раскатать рукав в направлении очага загорания, присоединить его к крану и стволу (если это не сделано заранее) и открыть вентиль крана для пуска воды. Во время работы со стволом необходимо следить, чтобы рукав был расправлен и не имел «заломов».
Не допускается применять воду для тушения ЛВЖ и ГЖ (бензин, клей и смазки на его основе, керосин, масла), а также Эл. Установки, находящиеся под напряжением.
Для тушения взрывоопасных сыпучих ингредиентов (сера, сажа, альтакс, тиурам, неозон, канифоль, крахмал, дифенилгуанидин, кумароновая смола, стеаррат цинка, фталевый ангидрид и др.) необходимо использовать специальные стволы, создающие распыленную струю воды.
Для ликвидации пожаров в закрытых помещениях (бензокладовые, маслосклады, сушильные камеры) объёмом до 500 куб. м применяется водяной пар.
Установка и аппараты пенного тушения Пена как огнегасительное средство применяется очень широко. Основным огнегасительным свойством её является то, что она легче многих ЛВЖ и ГЖ, поэтому удерживается на их поверхности, изолируя доступ свежего воздуха в зону горения, и способствует тем самым прекращению горения. Пена может быть химической, получаемой в результате химической реакции щелочных и кислотных веществ, и воздушно-механической, получаемой из смеси воды с пенообразователем при помощи специальных аппаратов.
Заключение
Выполнен проект участка подготовительного цеха для изготовления резиновых смесей для опорных частей резиновых армированных РОЧ и уплотнителя стекла. В представленном проекте произведён выбор и обоснование рецептуры резиновых смесей. Приведено описание конструкции изделия, технологического процесса.
При выполнении расчётов использовался пакет электронных таблиц Microsoft Excel, графическая часть выполнена в конструкторском пакете KOMPAS-3D v.11.0.
Список использованных источников
1 Овчинников В. Н. Проектирование заводов резинотехнических изделий / Кострыкина Г. И.- Ярославль, 1987. — 72 с.
2 Вещев А. А. Пособие по дипломному проектированию цехов заводов РТИ / В. А. Немытков — Ярославль. ЯПИ, 1984. — 49 с.
3 Кошелев Ф. Ф. Общая технология резины / А. Е. Корнев, A.M. Буканов — М.: Химия, 1978.-528 с.
4 Соловьев Н. В. Основы техники безопасности и противопожарной техники химической промышленности / Н. А. Стрельчук, П. И. Еремилов и др. — М.: Химия, 1966. — 532 с.
5 Лепетов В. А. Расчеты и конструирование резиновых изделий: Учеб. пособие для вузов / Л.Н. ЮрцевЛ.: Химия, 1987. — 408 с.
6 Лепетов В. А. Резиновые технические изделия / - Л.: Химия, 1976. — 440 с.
7 Андрашников Б. И. Справочник по автоматизации и механизации производства шин и РТИ. — М.: Химия, 1981. 294 с.
8 Справочник резинщика / П. И. Захарченко, Ф. И. Яшунская, В. Ф. Евстратов. — М.: Химия, 1971. 608 с.
9 Технологический регламент завода ЯЗРТИ.