Автосцепное устройство.
Основные функции автосцепки
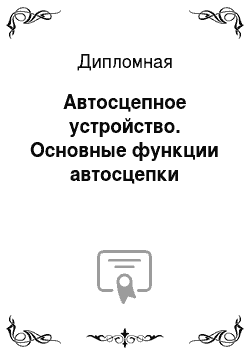
ОТПУСК ТОРМОЗА При переводе крана во 2-е положение резьбовой стакан крана управления вворачивается, прогибает вниз диафрагму, открывает питательный клапан. Воздух из НМ поступает в камеру под диафрагму крана управления и в камеру над диафрагмой реле давления. Возрастающее давление под диафрагмой крана управления прогибает ее вверх, питательный клапан закрывается. В кране управления наступает… Читать ещё >
Автосцепное устройство. Основные функции автосцепки (реферат, курсовая, диплом, контрольная)
Дипломная работа Автосцепное устройство. Основные функции автосцепки ВВЕДЕНИЕ Вагоном называется единица железнодорожного подвижного состава, предназначенная для перевозки пассажиров или грузов. При всем разнообразии типов и конструкций вагонов они имеют общие основные элементы (узлы или по-другому сборочные единицы). К ним относятся кузов, ходовые части, ударно-тяговые приборы и тормоз.
Кузов вагона предназначен для размещения пассажиров или грузов. Его конструкция зависит от типа вагона. У многих вагонов основанием кузова является рама, состоящая в основном из совокупности продольных и поперечных балок, жестко соединенных между собой. Рама кузова опирается на ходовые части, на ней размещены ударно-тяговые приборы и часть тормозного оборудования.
Ходовые части предназначены для безопасного движения вагона по рельсовому пути, с необходимой плавностью хода и наименьшим сопротивлением движению. К ходовым частям относятся колесные пары, буксы и рессорное подвешивание. В современных (имеющих более четырех колесных пар) вагонах ходовые части объединяются в самостоятельные узлы, называемые тележками. Ударно-тяговые приборы предназначены для сцепления вагонов между собой и с локомотивом, для передачи и смягчения действия растягивающих (тяговых) и сжимающих усилий от локомотива и от одного вагона к другому.
Современным ударно-тяговым прибором является автосцепное устройство, выполняющее основные функции ударных (буфера) и тяговых (сцепка) приборов.
Автосцепка, установленная на вагоне, автоматически взаимно сцепляется при нажатии или ударе с автосцепкой локомотива или другого вагона и расцепляется вручную при помощи специального рычага.
НАЗНАЧЕНИЕ, УСТРОЙСТВО И ПРИНЦИП РАБОТЫ АВТОСЦЕПКИ Автосцепка предназначена для осуществления механического сцепа вагонов, соединения воздушных магистралей и электрических цепей вагона.
Комплект автосцепки состоит:
— головки со сцепным устройством;
— электроконтактной коробки;
— ударно-тягового аппарата;
— устройства подвески автосцепки;
— узла крепления автосцепки к раме кузова вагона Две сцепленные между собой автосцепки смежных вагонов не нуждается в своих подвесках т.к. представляет собой одну прямую балку, концы которой шарнирно закреплены в рамах обоих вагонов.
Конструкция автосцепки обеспечивает возможность её поворота в горизонтальной плоскости на угол до 13°, а вертикальной до 2,5°.
ГОЛОВКА АВТОСЦЕПКИ Она представляет собой литой стальной корпус, который выполнен в виде полой прямоугольной коробки, которая спереди заканчивается буфером.
Буферэто устройство предохраняющее вагон от ударов.
На буфере имеется:
— выступающий конус с проёмом для деталей замка;
— конусообразная впадина с проёмом для деталей замка;
— два отверстия, каждый диаметром 60 мм для напорной магистрали и тормозной магистрали.
Сзади коробка корпуса расточена под цилиндр для установки двух стяжных полуколец, при помощи которых головка автосцепки соединяется с ударно-тяговым аппаратом. В сборе оба стяжных полукольца называют стяжным хомутом.
В боковой стенке корпуса имеется прямоугольное отверстие, которое предназначено для установки внутрь корпуса замка сцепного механизма в горизонтальном состояние.
Для этого верхних и нижних стенках корпуса имеется вертикальное отверстие для валика на котором и закрепляется в корпусе замок сцепного механизма, который вращается вокруг оси валика в горизонтальной плоскости.
УСТРОЙСТВО СЦЕПНОГО МЕХАНИЗМА Механизм состоит из:
— замка;
— серьги;
— валика;
— возвратной пружины
— расцепного троса с рукояткой;
— блока расцепного троса ЗАМОК СЦЕПНОГО МЕХАНИЗМА Он представляет собой равноплечий рычаг дискообразной формы. К одному из плеч в котором имеется отверстие, присоединяют серьгу. В другом плече имеется вырез, который предназначен для захода в него цапфы серьги автосцепки смежного вагона при сцеплении.
Центральная часть диска замка отлита в виде втулки вокруг которой есть канавка, в которой имеется 5 отверстий при помощи которых мы можем изменять натяг возвратной пружины. Кроме того на замке имеется отросток с отверстием к которому присоединяют расцепной трос с рукояткой.
СЕРЬГА Она имеет «П» образную конструкцию и оканчивается двумя проушинами, которые охватывают диск замка и соединяют при помощи валика серьгу с замком.
Замок, серьга и оба валика изготавливают из легированной стали и термообработаны для обеспечения сверхпрочности.
Кроме того эти детали перед сбором автосцепки и её установки на вагон подвергаются дефектоскопии.
ВОЗВРАТНАЯ ПРУЖИНА Предназначена для обеспечения поворота замка (сцепного механизма) в исходное положение после сцепления или расцепления вагонов.
Она распологается сверху замка таким образом, что один её конец закрепляется в одном из 5 отверстий находящиеся в канавке, а другой конец закрепляется за штифт (прилив) находящийся на нижней стенке верхней половины корпуса.
РАСЦЕПНОЙ ТРОС С РУКОЯТКОЙ Служит для расцепления автосцепок смежных вагонов. Заводится внутрь корпуса через специальный блок.
В рабочем состояние ручка троса должна находится в специальном держателе, который находится на верхней половине тыльной стороны буфера.
Трос с ручкой проходит динамическое испытание и должен выдерживать динамическое усилие до 2кН (200 кгс).
РАБОТА СЦЕПНОГО МЕХАНИЗМА При сближении головок смежных вагонов, выступающие серьги начинают скользить по поверхности конусных впадин встречных буферов смежных головок.
Серьги упираясь в замок своими проушинами одной стороной, а другой цапфой упираются во встречные замки смежных автосцепок при этом происходит поворот замков вокруг своих валиков в горизонтальной плоскости до того момента как цапфы серёг не войдут в вырезы замков.
При этом произойдёт громкий характерный щелчёк, буфера смежных головок коснуться друг друга и замки под действием своих возвратных пружин вернутся в исходное положение, т. е. произойдёт смежное сцепление вагонов.
ПРИЗНАКИ ПРАВИЛЬНОГО СЦЕПЛЕНИЯ
— между ударными плоскостями двух головок автосцепок должен быть средний зазор не более 5 мм., при расхождении осевой линии головок возможно изменение этого зазора, но не свыше 1 мм (с одной стороны 4 мм, а с другой 6 мм);
— между тягой и рычагом блокировки должен быть острый угол — 60?. Если этот угол будет свыше 90?, то это означает, что цапфы серег не вошли в зацепление с захватами встречных замков и замки не развернулись обратно в исходное положение;
— короткое плечо рычага блокировки и сектор блокировки на наконечнике крана управления пневмоприводом ЭКК должны располагаться друг против друга. Это означает, что кран управления пневмоприводом в положении «включено», и электрические пальцы (штепсельные разъемы) находятся в выдвинутом положении. При попытке расцепа (или сцепления) двух автосцепок, сегмент рычага упрется в сектор блокировки, не давая сцепить (или расцепить) автосцепки.
Расцепить или сцепить автосцепки можно только когда кран управления пневмоприводом находится в положении «Выключено» .
Рукоятка от расцепного тросика должна быть надежно закреплена на головке хомутом. В случае маневровых передвижений не закрепленная на головке рукоятка от расцепного тросика может зацепиться за выступающие части оборудования и, если электрическая часть двух вагонов не соединялась, может произойти саморасцеп.
УДАРНО-ТЯГОВЫЙ АППАРАТ Предназначен для смягчения ударов при сцеплении и упругого соединения вагона; также служит амортизатором, т.к. поглощает продольные ударные усилия, которые возникают при неодновременном пуске и торможения вагонов в составе.
Он состоит из:
— литого стального хомута;
— водила;
— двух стальных цилиндрических пружин;
— промежуточной шайбы, которая находится между пружинами;
— двух направляющих втулок для пружин;
— втулки водила;
— корончатая гайка
— шплинта ХОМУТ Имеет прямоугольную конструкцию, отливается из стали. Его концевые части выполняются в виде втулок с отверстиями для прохождения через них водила. С головкой автосцепки хомут соединяется двумя полукольцами, который в собранном состоянии называется стяжным хомутом. В нижней части хомута устанавливают скользун из дубового бруса, который прикрепляется к металлической планке. Этот скользун служит как опора автосцепки при её перемещении по балансиру узла подвешивания автосцепки.
В хомут вставлены две пружины, которые по концам водила имеют направляющие втулки, а между ними находится промежуточная шайба.
ВОДИЛО Изготавливается из легированной стали и имеет форму бруса круглого сечения, один конец которого имеет форму бруса круглого сечения, один конец которого имеет проушину для установки валика, а другой мелкую резьбу под установку корончатой гайки.
ПЕРЕДАЧА ТЯГОВОГО УСИЛИЯ Тяговые усилия с головки автосцепки через стяжные полукольца (стяжного хомута) передаются на сам хомут, с хомута на заднюю направляющую втулку, затем на пружины далее на корончатую гайку, резьбу водила, водило, валик проушина, далее на узел крепления автосцепки к раме кузова вагона, кузов вагона.
Валик, который соединяет водило с узлом крепления автосцепки к раме кузова вагона подвергается дефектоскопии.
Недостатком ударно-тягового аппарата является применение в нём цилиндрических витых пружин, которые плохо самоуспокаиваются, поэтому при неодновременном пуске и торможение возможны рывки и продольное раскачивание вагонов.
УЗЕЛ ПОДВЕШИВАНИЯ АВТОСЦЕПКИ Автосцепка в свободном состоянии опирается на подвеску (только на головных вагонах).
Подвеска состоит из:
— балки балансира;
— двух подвесных штырей;
— двух верхних пружин;
— двух упорных шайб;
— двух стаканов;
— двух пружин, которые устанавливаются в стаканы;
— двух втулок, которые устанавливаются в отверстия по краям Каждый стакан состоит из двух штампованных цилиндров, стянутых шестью болтами. В стакане расположена втулка, под ней помещена пружина.
После установки стаканов на штыри ставят гайки, которыми регулируют расстояние от головки автосцепки до головок рельсов. Это расстояние при новых бандажах равно 829 мм. После окончания регулировки ставят контргайки и шплинты.
В случае обрыва одного или двух штырей подвески, свободная автосцепка опустится на предохранительную «П» — образную скобу, выполненную из уголка с размерами 50×50×5мм. Скобу укрепляют на раме кузова четырьмя болтами. Для ограничения поворота свободной автосцепки и предотвращения удара о предохранительную скобу к балансиру приваривают упоры.
ПНЕВМАТИЧЕСКАЯ ЧАСТЬ АВТОСЦЕПКИ К ней относятся клапана воздухопроводов напорной магистрали и тормозной магистрали, также пневмопривод электроконтактной коробки.
Клапан воздухопровода служит для исключения утечек сжатого воздуха при сцеплении автосцепок.
На буфере автосцепки имеется два отверстия диаметром 60 мм. Каждая для установки в них клапанов воздухопроводов напорной магистрали и тормозной магистрали (верхний клапан НМ, а нижний ТМ).
Клапан воздухопровода состоит из:
— стального корпуса в форме цилиндра, который устанавливается заподлицо с наружной плоскостью буферного фланца и слегка запрессованной в это отверстие с втулкой
— резиновой трубки
— резинового уплотняющего кольца, которое является продолжением резиновой трубки
— упорного латунного кольца, которое выступает за поверхность буфера
— пружины, которая прижимает латунное кольцо к выходному буртику отверстия 60 мм.
— литого угольника, при помощи которого к клапану присоединяют воздухопровод НМ и ТМ
— двух болтов с гайками при помощи которых угольник крепится к тыльной стороне буферного фланца.
Рис. Клапан воздухопровода: 1 стальной корпус; 2- пружина; 3- резиновое уплотнительное кольцо; 4- упорное латунное кольцо; 5- литой угольник; 6- резиновая трубка; 7- два болта; 8- буферный фланец НЕИСПРАВНОСТИ АВТОСЦЕПКИ
1. Износ балансира подвески.
2. Износ зева замка и цапфы серьги.
3. Выпадение валика.
4. Срыв резьбы водила и гаек.
5. Ослабление затяжек гаек на водиле.
ТЕХНИЧЕСКОЕ ОБСЛУЖИВАНИЕ И РЕМОНТ АВТОСЦЕПКИ К демонтажу автосцепки приступают после снятия электроконтактных коробок и отсоединения труб воздухопроводов.
Для снятия автосцепки с вагона расшплинтовывают два шплинта диаметром 6×70мм., отворачивают две гайки со штырей, снимают два стакана с пружинами, балансир автосцепки и две верхние пружины с шайбами. После этого с помощью пневматического подъемника, предварительно расшплинтовав шплинт 8×90мм. и сняв шайбы валика и валик, автосцепку демонтируют с вагона.
Перед дальнейшим демонтажём на участке разборки автосцепку направляют для очистки в выварочную ванну с 3−5% раствором каустической соды при температуре 60−700С.
Разборку головки автосцепки выполняют в следующем порядке:
— с головки автосцепки снимают кронштейны электрической части и запорного механизма, а также блок с корпусом головки автосцепки;
— разбирают блок, снимают державку рукоятки торса;
— вынимают валик сцепного механизма с крышкой, а из корпуса головкисцепной механизм;
— расшплинтовав валик, снимают тягу блокировки и трос замка;
— выворачивают штифт возвратной пружины;
— разбирают сцепной механизм;
— снимают возвратную пружину;
— спрессовывают расклепанную часть валика и разъединяют серьгу с замком Отсоединение головки автосцепки от ударно-тягового аппарата производят в следующем порядке:
— вынимают шплинты и отворачивают гайки болтов крепления хомутов;
— снимают болты крепления хомута головки автосцепки Для разборки тягового аппарата необходимо:
— расшплинтовать корончатую гайку водила автосцепки и отвернуть её
— выпрессовать на специальном стенде водило с направляющей втулкой из хомута, а затем пружины тягового аппарата, опорные шайбы и направляющую втулку Далее производят внешний осмотр и дефектоскопию деталей согласно установленному перечню. Детали, имеющие трещины (кроме хомута тягового аппарата и корпуса головки), должны быть заменены новыми.
Трещины необходимо накернить по всей длине. Заварку трещин выполняют согласно инструкции.
Ремонт головки автосцепки осуществляют в следующем порядке:
— заваривают трещины в корпусе головки автосцепки с последующей механической обработкой;
— проверяют геометрические размеры головки после механической обработки;
— контролируют состояние втулок головки автосцепки;
— осматривают и проверяют отверстие в корпусе головки под валик сцепного механизма;
— прогоняют резьбу в корпусе головки автосцепки;
— промеряют серьгу автосцепки и осматривают возвратную пружину;
— замеряют валики сцепного механизма При осмотре и ремонте тягового аппарата осуществляют заварку трещин в стенках хомута тягового аппарата с последующей дефектоскопией, проверку геометрических размеров хомута, замер диаметра шейки, а также диаметра высоты бурта, выработки в отверстиях под водила. Далее производят осмотр и проверку размеров водила, контролируют резьбовую часть хвостовика.
На заключительном этапе перед сборкой проверяют состояние пружин тягового аппарата автосцепки, стопорных шайб, дополнительных шайб, направляющей втулки, корончатой гайки хвостовика, водила, а также плиту скользуна, болты и гайки его крепления.
Сборку тягового аппарата выполняют в такой же последовательности:
— на специальном стенде устанавливают хомут тягового аппарата, в который запрессовывают комплект пружин с опорными шайбами;
— предварительно отцентровав направляющие втулки, вставляют водило в хомут, затем одевают на хвостовик водила круглую корончатую гайку;
— закрепляют гайку и зашплинтовывают хвостовик водила;
— устанавливают плиту скользуна и закрепляют ее болтами.
При сборке головки автосцепки сначала соединяют ее корпус с тяговым аппаратом, установив хомут головки и закрепив его болтами, гайками и шплинтами. После этого совмещают замок с серьгой при помощи валика и присоединяют к замку трос и тягу блокировки с валиком. Далее в корпус головки заводят сцепной механизм с возвратной пружиной. Крючок пружины одевают на штифт, вставляют валик замка с крышкой и собирают блок головки автосцепки.
Для этого выполняют следующие операции:
— одевают на ось блок и шайбу;
— вставляют ось в кронштейн;
— одевают предохранитель, навертывают гайку и закрепляют ее;
— зашплинтовывают ось;
— блок и державку рукоятки устанавливают на корпус головки автосцепки;
— сборка фиксатора путем установки стержня с пружиной и шплинта;
— монтаж кронштейна запорной тяги вместе со всеми деталями, для этого устанавливают правую щетку с кронштейном и закрепляют ее болтами с гайками;
— размещают в прорези кронштейна запорную тягу вместе со всеми деталями, для этого устанавливают правую щетку с кронштейном и закрепляют ее болтами с гайками;
— в прорези кронштейна размещают запорную тягу и крепят на ней упор;
— на корпусе головки автосцепки устанавливают левую щетку и закрепляют ее.
После этого выполняют блокировку на корпусе головки автосцепки и соединяют ее с тягой блокировки. Собранную автосцепку снимают со стенда и транспортируют на стенд проверки, а также на сцепку и расцепку.
Собранную автосцепку предъявляют мастеру отдела технического контроля (ОТК). После проверки ОТК автосцепку транспортируют к вагону.
ОХРАНА ТРУДА Рабочим местом называют участок производственной площади, цеха, мастерской, закрепленной за данным рабочим (или бригадой рабочих), предназначенный для выполнения определенной работы и оснащенный в соответствии с характером этой работы оборудованием, приспособлениями, инструментами и материалами.
Одним из основных элементов организации рабочего места является его планировка, т. е. расположение его относительно других рабочих мест в мастерской, относительно оборудования оснастки, приспособлений, инструментов, местоположения рабочего.
При организации рабочего места используют основные достижения научной организации труда (НОТ).
Расстояния от тары с заготовками и готовой продукции и от оборудования (верстака) до рабочего должны быть такими, чтобы рабочий мог использовать преимущественно движение рук, т. е. при этом не наклоняться сильно, не приседать, не тянуться высоко.
При планировке рабочего места учитывают зоны досягаемости рук в горизонтальной и вертикальной плоскостях.
Эти зоны определяют, на каком расстоянии от корпуса рабочего должны быть размещены предметы, которыми он пользуется в процессе работы. Оптимальная зона (наиболее удобная) определяется полудугой радиусом примерно 400 мм. для каждой руки. Максимальная зона досягаемости составляет 500 мм. без наклона корпуса и 650 мм. с наклоном корпуса не более 30° для рабочего среднего роста. Расположение предметов дальше указанных пределов повлечет дополнительные, а следовательно, лишние движения, т. е. вызовет ненужную затрату рабочего времени, ускорит утомляемость работающего и снизит производительность труда.
сигнальный вагонный тормозной кран Рис. Рабочее место слесаря Оптимальной зоной досягаемости рук в вертикальной плоскости является зона от уровня плеча до пояса.
Рабочее место слесаря организуется в зависимости от содержания производственного задания и типа производства (единичное, серийное, массовое), однако рабочее место оборудуют, как правило, слесарным верстаком, на котором закрепляют слесарные тиски.
Верстак должен быть прочным и устойчивым, его высота должна соответствовать росту работающего. На верстаке устанавливают сменный (убирающийся) сетчатый экран для защиты от осколков, отлетающих при рубке.
Тиски должны быть исправны и прочно закреплены на верстаке.
Ходовой винт должен вращаться в гайке легко, губки иметь четкую насечку, которая обеспечивает надежное закрепление заготовки.
Подставку (решетку) под ноги, используют в том случае, когда высота установки тисков не соответствует росту рабочего. Подставка должна плотно прилегать к полу, не скользить.
Для экономии движений и устранения ненужных поисков предметы на рабочем месте делят на предметы постоянного и временного пользования, за которыми постоянно закреплены места их расположения и хранения.
ОСНОВНЫЕ ПРАВИЛА ОРГАНИЗАЦИИ РАБОЧЕГО МЕСТА СОСТОЯТ В СЛЕДУЮЩЕМ
— Все необходимое для работы должно находиться под рукой, чтобы можно было быстро найти нужный предмет.
— Все предметы располагают примерно на высоте пояса. Инструменты и материалы, требующиеся при работе чаще, размещают ближе к работающему, а используемые режедальше.
— Инструменты и приспособления, которые берут правой рукой, располагают справа, те, что берут левой рукой слева.
— Чертежи, технологические карты, наряды и другую документацию держат в удобном для пользования и гарантированном от загрязнения месте.
— Недопустимо класть один предмет на другой или на отделанную поверхность изделия.
— Заготовки и готовые детали хранят так, чтобы они не загромождали проходы, и чтобы рабочему не приходилось часто нагибаться, складывая или беря заготовку или деталь.
— Легкие предметы кладут выше тяжелых.
ПРАВИЛА БЕЗОПАСНОЙ РАБОТЫ С ИНСТРУМЕНТАМИ И ЭЛЕКТРИЧЕСКИМИ ПРИСПОСОБЛЕНИЯМИ К работе с переносным электрическим инструментом допускаются только те рабочие, которые обучены обращению с ним и ознакомлены с безопасными приемами пользования. Контроль за сохранность и исправным состоянием инструмента должен осуществляться специально уполномоченным лицом. Не реже одного раза в месяц электрический инструмент проверяют, убеждаются в отсутствии замыкания на корпус, обрыва заземляющего провода; проверяют также состояние изоляции проводов.
Перед тем как электроинструмент выдадут для работы, его проверяют в присутствии рабочего на стенде или специальным прибором (например, мегомметром) на исправность заземляющего провода и отсутствие замыкания на корпус. Электроинструмент, имеющий дефекты, выдавать для работы запрещается.
Корпус электрических переносных инструментов (электродрелей, шлифовальных машин, напильников, вибраторов и др.) должны быть заземлены. Работать инструментом с незаземленным корпусом воспрещается.
Для питания электрического инструмента в помещениях без повышенной опасности допускается применять напряжение не выше 220 В, в смотровых канавах, тоннелях, колодцах, и других опасных помещениях, а также вне помещений не выше 36 В Если невозможно обеспечить работу инструмента при напряжении 36 В допускается использовать инструмент на напряжении 220 В, но с обязательным применением защитных средств (диэлектрических перчаток, ковриков и др.) и надежным заземлением корпуса электроинструмента. Пользоваться защитными средствами с просроченными сроками запрещается.
Испытания диэлектрических перчаток и галош производят один раз в 6 месяцев, ковриков один раз в 24 месяца.
Электрические инструменты снабжают проводами в защитных резиновых шлангах, оканчивающимися вилками для включения. Включающая вилка должна быть устроена таким образом, чтобы заземляющий контакт включался раньше контактов, находящихся под напряжением, и была исключена возможность ошибочного присоединения заземляющего провода к контакту, находящемуся под напряжение.
При работе с электрическим инструментом необходимо постоянно наблюдать за исправностью проводов, не допускать их оплетение и перекручивания. Если рабочий отошел от места работы, инструмент необходимо отключить от электросети.
Лицам, пользующимся электрическим инструментом, категорически запрещается:
— передавать инструмент хотя бы на непродолжительное время другим лицам;
— разбирать либо производить какой либо ремонт;
— держаться за провод электроинструмента или касаться режущего вращающегося инструмента;
— удалять руками стружки или опилки во время работы инструмента до полной его остановки;
— работать на высоте более 2,5 м. с приставной лестницы.
РАБОТА СО СЛЕСАРНЫМ ИНСТРУМЕНТОМ Слесарный инструмент должен быть исправным. У слесарного молотка поверхность бойка должна быть слегка выпуклой, не сбитой, без надломов и трещин, рукоятка молотка прочной из твердых и вязких пород дерева (кизил, молодой дуб, рябина, бук, граб и др.) овального сечения, гладко выструганной, не иметь надломов и трещин.
Молоток закрепляют на рукоятке, забивая металлический клин в торец ручки под некоторыми углом к её оси.
Использовать для работы зубило, крейцмейсель, бородок, имеющие разбитую ударную поверхность или заусенцы, нельзя. При рубке зубилом или крейсмейселем следует обязательно надевать предохранительные очки. При обрубке деталей из твердого и хрупкого металла и срубке заклепок необходимо ограждать рабочие места щитами или сетками.
Недопустимо работать напильниками без рукояток или с треснувшими рукоятками. Рукоятки должны соответствовать размерам и быть прочно насажены на их хвостовики.
Тиски должны иметь губки с наработанной насечкой, расположенные строго параллельно одна от другой, тогда они крепко зажимают обрабатываемую деталь. Тиски устанавливают по росту работающего, прочно укрепляют.
Образующиеся при работе на тисках металлические опилки удаляют металлической щеткой, а не рукой; нельзя сдувать опилки.
Верстак на котором закрепляют тиски должен иметь ровную поверхность, покрытую листовым железом без дыр и разрывов. Ширина рабочего места у верстака должна иметь не менее 1 м. Слесарный верстак, установленный вблизи других рабочих мест или прохода, ограждают предохранительной сеткой (длина стороны ячейки не более 3мм) высотой не менее 800 мм.
Поверхность пола около верстака, на котором закреплены тиски, должна быть ровной, нескользкой. На цементных полах необходимо уложить деревянные настилы.
Гаечные ключи подбирают по размерам гаек. Запрещается вставлять прокладки между гранями гайки и ключа и наращивать ключи, удлиняя их плечи газовыми трубами или другими рычагами.
РАБОТА С ПАЯЛЬНЫМИ ЛАМПАМИ Эти лампы можно выдавать только рабочим, знакомых с их устройством и обучены безопасным приемам работы с ними.
Поэтому в инструментальном цехе вывешивают подписанные начальниками других цехов списки рабочих, которые могут быть выданы паяльные лампы.
Паяльные лампы не должны иметь течи; змеевики горелки и предохранители должны быть исправными. Для заправки паяльных ламп следует использовать только-то горючее, на которое рассчитана лампа. Во избежание взрыва резервуара лампы не следует накачивать в него чрезмерно много воздуха, допускать повышенный нагрев. Можно пользоваться только теми паяльными лампами, которые не реже одного раза в год, а также после каждого ремонта были испытаны давлением, превышающим рабочее в 2 раза.
На лампе должен стоять штамп с обозначением ее номера и даты испытания.
Разжигать паяльные лампы следует в специально оборудованных шкафах, обеспечивающих вытяжку образующихся при этом газов.
РАБОТА С ПНЕВМАТИЧЕСКИМ ИНСТРУМЕНТОМ Клапаны на рукоятках пневматического инструмента должна быть плотно пригнаны и не пропускать воздуха в закрытом состоянии (при прекращении нажима на управляющую рукоятку). Необходимо, чтобы клапаны легко открывались и быстро закрывались. В местах присоединения воздушного шланга к пневматическому инструменту и соединения шлангов друг с другом не должно быть пропусков воздуха.
Для крепления шлангов следует применять кольца и зажимы.
Крепить шланги проволокой запрещается. Присоединять и отсоединять шланги пневматического инструмента можно только после прекращения подачи воздуха.
Работая с пневматическим зубилом или молотком, необходимо соблюдать особую осторожность. При перерыве в работе или переходе на другое место работы с не отключенным инструментом запрещается держать его дулом вверх и класть большой палец на курок.
Перед началом работы с пневматическим инструментом необходимо убедиться в исправности курков. После этого следует тщательно протереть инструмент, чтобы в нем не оставалось масла.
При отводе молотка после окончания работы или при перерыве в работе необходимо строго следить за тем, чтобы дуло не было направлено на кого-нибудь их находящихся рядом.
Запрещается работать пневматическим инструментом с приставной лестницы.
В случае обнаружения каких-либо неисправностей работа с пневматическим инструментом должна быть прекращена, о неисправности следует доложить мастеру.
ПРАВИЛА БЕЗОПАСНОСТИ ПРИ ОСМОТРЕ И РЕМОНТЕ ВАГОННОГО ОБОРУДОВАНИЯ Все работы на электроподвижном составе во время ремонта депо и пункте технического обслуживания, производят при снятом с контактного рельса напряжения и отключенных аккумуляторных батареях на всех вагонах состава. Перед производством работ на подвижном составе обязательно следует убедиться в отсутствии высокого напряжения.
Об отсутствии высокого напряжения на вагонах свидетельствует следующее:
— передвижные кабели (удочки контактной шины) не надеты на выводы токоприемников вагонов; разъединители отключены и заперты;
— не горят красные сигнальные лампы в канаве и над канавой (отстойным путем), занятой составом.
Не горящие лампы освещения в вагоне не свидетельствует об отсутствии высокого напряжения, так как на ряде вагонов лампы в салоне, а также белые сигнальные фары могут полностью выключаться.
Если невозможно снять напряжение с контактного рельса как исключение, работы можно производить, отключив разъединители всех вагонов поезда и РЦУ на вагоне, где производиться работа.
При этом должно быть не менее двух разрывов в высоковольтной цепи и один разрыв в цепи следующих электрических аппаратов и машин, расположенных под кузовом вагона: реостатного контроллера; переключателя положений, реверсора, электрической части авторежима, индуктивного шунта, пускотормозных реостатов резисторов ослабления возбуждения, мотор-компрессор, тяговых двигателей.
Например, чтобы выполнить работы на мотор — компрессоре, необходимо отключить автоматический выключатель и вынуть силовой предохранитель в цепи мотор — компрессора. Для работы на тяговом двигателе необходимо отключить автоматический выключатель и вынуть предохранитель в цепи обмоток подмагничивания.
Категорически запрещается производить работы при наличии напряжения в контактном рельсе на следующем электрическом оборудовании: линейных контакторах, токоприемниках, силовых коробках, главном предохранители, главном разъединителе, автоматическом выключателе, выключателе батареи, реле перегрузки, нулевом реле.
Разрешается производить работы при отключенных батареях и вынутых плавких вставках «Батарея» и «Подзаряд»: на щитке с низковольтным предохранителями, дверном воздухораспределителе, панели и индикаторными лампами и кнопками, электроконтактных коробках, выключателях управления поездом, дверных блокировках, рейках зажимов, кнопках дверной сигнализации, контроллере машиниста.
Категорически запрещается выполнять работы на механическом оборудовании тележек (смене рессор, регулировок рычажно-тормозной передачи, смене колодок и т. п.) при наличии напряжения в контактном рельсе.
АВТОТОРМОЗА. КРАН МАШИНИСТА 013
Предназначен для управления пневматическими тормозами путем изменения давления в тормозной магистрали.
Кран машиниста усл. 013 разработан с целью замены устаревшего крана машиниста усл. № 334, который имел ряд недостатков:
— отсутствие питания в положении перекрыша;
— отсутствие фиксированных ступеней разрядки и зарядки тормозной магистрали;
— наличие притираемых элементов, не обладающих повышенной надежностью и требующих значительных трудовых затрат в изготовлении, обслуживании и ремонте.
По конструкции кран машиниста клапанно-диафрагменный, прямодействующий, т.к. у него автоматическая перекрыша.
Состоит из следующих узлов:
— крана управления, который установлен в кабине управления головного вагона и в правом головном торцевом отсеке промежуточного вагона.
— разобщительного устройства, установлено под кабиной управления головного вагона справа. На промежуточном вагоне разобщительного устройства нет. Оно заменено кранами 2-й тяги, которые установлены под сидением 3-х местного правого головного дивана. Отсутствие разобщительного устройства — это отличие крана машиниста промежуточного вагона от головного.
— реле давления, которое установлено на раме кузова под головной частью вагона с правой стороны.
КРАН УПРАВЛЕНИЯ КМ усл.№ 013
Кран управления предназначен для изменения управляющего давления в полости над диафрагмой реле давления.
Кран управления состоит из разъемного корпуса, в верхней части которого установлена резиновая диафрагма. Сверху диафрагма нагружена пружинами. Регулировка начального усилия пружин (при техническом обслуживании) осуществляется винтом, который стопорится гайкой.
Рис. Кран машиниста 013: 1- рукоятка со шпилькой; 2- пружина с шариком фиксатора; 3- корпус; 4- винт с атмосферным каналом; 5- питательный клапан; 6- диафрагма; 7- толкатель; 8- стакан с резьбой; 9- регулировочные пружины; 10- регулировочный винт с контргайкой; 11- колпачок Кран машиниста 013 имеет 7 положений:
Положение 1: Зарядка тормозной магистрали.
Обеспечивает зарядку ТМ до 6.0 — 6,5 атм.
Положение 2: Поездное положение. Обеспечивает зарядку ТМ до 5,0 — 5,2атм. Темп зарядки ТМ и в 1-м и 2-м положении крана одинаковый — 1 атм./сек, но т.к. 1-е положение перепитывает ТМ до давления выше рабочего — оно практически не применяется.
Положение 3, 4, 5: ступени торможения:
— 3-е положение обеспечивает разрядку ТМ до 4,3 атм.
— 4-е положение обеспечивает разрядку ТМ до 4,0 атм.
— 5-е положение обеспечивает разрядку ТМ до 3,7 атм.
Положение 6: Полное служебное положение. Обеспечивает разрядку ТМ до 3 атм.
Положение 7: Экстренное торможение. Обеспечивает разрядку ТМ до 0.
ОСОБЕННОСТИ ТОРМОЗНОЙ РАБОТЫ КРАНА
— Экстренный темп разрядки тормозной магистрали при всех тормозных позициях крана машиниста.
— Автоматическая перекрыша при всех позициях крана, кроме 7-й.
— При выключении крана из действия перекрытием 3-х ходового разобщительного крана обеспечивает дополнительную разрядку ТМ на 0,7 атм.
РАБОТА КРАНА МАШИНИСТА. ЗАРЯДКА При 2-м положении крана машиниста и открытии 3-х ходового разобщительного крана, воздух из НМ через открытый питательный клапан крана управления поступает в камеру под диафрагму крана управления, в камеру над диафрагмой реле давления и в камеры под клапана разобщительного устройства. Клапана разобщительного устройства открываются и соединяют НМ и ТМ с реле давления. Возрастающее давление в камере крана управления прогибает диафрагму вверх, преодолевая усилие режимных пружин и питательный клапан закрывается. В кране управления наступает «перекрыша», прекращая зарядку камеры реле давления. Повышение давления в камере над диафрагмой реле давления прогибает диафрагму вниз, открывается питательный клапан и НМ через открытый клапан НМ разобщительного устройства, открытый питательный клапан реле давления и открытый клапан ТМ разобщительного устройства соединяется с ТМ. Повышается давление в ТМ и одновременно повышается давление в камере под диафрагмой РД. Диафрагма прогибается вверх и питательный клапан РД закрывается, прекращая зарядку ТМ.
ТОРМОЖЕНИЕ
3-е — 4-е — 5-е положение крана — это ступени торможения. Обеспечивают разрядку ТМ до 4,3 — 4.0 — 3,7 атм.
Глубина разрядки ТМ обеспечивается различным остаточным усилием пружин крана управления на его диафрагму. Чем выше это усилие, тем меньше глубина разрядки ТМ. Во всем остальном работа крана при 3 — 4 — 5 и 6-м положениях крана машиниста аналогична.
ПОЛНОЕ СЛУЖЕБНОЕ ТОРМОЖЕНИЕ При переводе ручки крана управления в 6-е положение выворачивается резьбовой стакан, поднимаясь вверх, и уменьшается усилие режимных пружин на диафрагму крана управления. Диафрагма давлением воздуха снизу прогибается вверх, вместе с диафрагмой поднимается полый толкатель, открывается атмосферный клапан и камеры под диафрагмой крана управления и над диафрагмой реле давления соединяются с атмосферой. При понижении давления в камере под диафрагмой крана управления, диафрагма прогибается вниз остаточным усилием режимных пружин и атмосферный клапан закрывается. В кране управления наступает «перекрыша», которая прекращает разрядку камеры над диафрагмой реле давления.
Понижение давления в камере над диафрагмой реле давления вызывает прогиб диафрагмы вверх давлением ТМ, открывается плавающий атмосферный клапан реле давления и ТМ соединяется с атмосферой. При понижении давления в ТМ диафрагма реле давления прогибается вниз и плавающий атмосферный клапан закрывается. В реле давления наступает «перекрыша», прекращая разрядку ТМ.
ЭКСТРЕННОЕ ТОРМОЖЕНИЕ При переводе ручки крана управления в 7-е положение резьбовой стакан выворачивается полностью вверх и исключает воздействие режимных пружин на диафрагму крана управления.
Диафрагма прогибается вверх, открывается атмосферный клапан, соединяя с атмосферой камеру крана управления и камеру над диафрагмой реле давления. Обе камеры разряжаются до «0 «. Диафрагма реле давления прогибается вверх, открывается плавающий атмосферный клапан, и ТМ, соединяясь с атмосферой разряжается до «0 «.
Особенностью работы крана машиниста при ЭТ является отсутствие «перекрыши» в реле давления, а значит и в кране машиниста. При одинаковом давлении в камерах над и под диафрагмой реле давления из-за усилия пружины снизу на диафрагму она вниз не прогибается, плавающий атмосферный клапан не закрывается и разряженная до «0 «ТМ остается соединенная с атмосферой.
ОТПУСК ТОРМОЗА При переводе крана во 2-е положение резьбовой стакан крана управления вворачивается, прогибает вниз диафрагму, открывает питательный клапан. Воздух из НМ поступает в камеру под диафрагму крана управления и в камеру над диафрагмой реле давления. Возрастающее давление под диафрагмой крана управления прогибает ее вверх, питательный клапан закрывается. В кране управления наступает «перекрыша», прекращая зарядку камеры над диафрагмой РД. Повышение давления в камере над диафрагмой РД прогибает ее вниз, открывается питательный клапан РД и НМ соединяется с ТМ. Начинается зарядка ТМ и камеры под диафрагмой РД. Повышение давления в камере под диафрагмой РД прогибает диафрагму вверх, питательный клапан закрывается, прекращая зарядку ТМ.
При перекрытии 3-х ходового разобщительного крана и выключении крана машиниста из действия обеспечивается дополнительная разрядка ТМ на 0,7 атм. Перекрытый 3-х ходовой разобщительный кран отсоединяет НМ от крана машиниста и соединяет с атмосферой камеру питательного клапана крана управления и камеры клапанов разобщительного устройства.
Камера питательного клапана крана управления разряжается до «0» и давлением сверху питательный клапан открывается, соединяя камеру РД с атмосферой и разряжая ее до «0» .
Диафрагма РД прогибается вверх, открывается плавающий атмосферный клапан, соединяя ТМ с атмосферой. ТМ начинает разряжаться через открытый атмосферный клапан и открытый клапан ТМ разобщительного устройства, т.к. зауженный канал разрядки диаметром 2,5 мм приводит к медленной разрядке камеры клапана ТМ разобщительного устройства и он закрывается не сразу. После разрядки камеры клапана ТМ разобщительного устройства клапан закрывается, прекращая разрядку ТМ.
РАБОТА ЭПВ АРС ЭПВ АРС представляет собой обычный электромагнитный вентиль включающего типа. Нижнее отверстие его закрыто заглушкой. Он подключен к трубопроводу, ведущему в камеру над диафрагмой реле давления через трехходовой разобщительный кран ЭПВ.
При нормальной работе системы АРС катушка вентиля всегда находится под питанием и атмосферный канал вентиля перекрыт клапаном.
По команде, полученной от системы АРС, катушка вентиля теряет питание и камера над диафрагмой реле давления сообщается с атмосферой через атмосферное отверстие вентиля. Так как камера над диафрагмой реле давления разряжается до 0 АТ, происходит экстренное пневматическое торможение с разрядкой тормозной магистрали также до 0 АТ.
ПТЭ И ИНСТРУКЦИИ. ПОСТОЯННЫЕ СИГНАЛЬНЫЕ ЗНАКИ Предельные столбики или рейки указывают место, далее которого на пути нельзя устанавливать подвижной состав в направлении стрелочного перевода или глухого пересечения.
Предельные столбики устанавливаются посередине междупутья, а предельные рейки — в междупутье, в местах, где расстояние между осями сходящихся путей достигает размеров, предусмотренных Правилами технической эксплуатации.
— Знаки «Граница станции» устанавливаются на границах станции с перегоном, соединительной ветвью.
Предупредительными сигнальными знаками являются:
— знак «Предельно допускаемая скорость» устанавливается в местах, определяемых приказом начальника метрополитена;
— световой знак «Т сбор" — место начала сбора схемы на тормоз для поезда, оборудованного устройствами автоматического управления;
— если световой знак «Т сбор» не горитмашинист должен остановить поезд на станции, применяя электрическое или пневматическое торможение; допускается установка неосвещаемого сигнального знака «Т сбор» на линиях, не оборудованных устройствами автоматического ведения, для обозначения места начала торможения перед станцией;
— знак «С» перед кривым участком пути, стрелочным переводом, тоннелем требует подачи звукового сигнала хозяйственными поездами, первым электропоездом, а также всеми электропоездами при нахождении людей в тоннеле, при включенном освещении в тоннеле;
— знаки «Включить тяговые двигатели» и «Отключить тяговые двигатели»; в зависимости от режима вождения эти знаки могут дополняться буквами или цифрами;
— знак «Т" — начало экстренного торможения, при входе на станцию или путь оборота состава, если машинистом не было своевременно применено служебное торможение;
«Т начало" — место начала подтормаживания поезда на перегоне
«Т конец" — место конца подтормаживания поезда;
— знак «Предельное место применения экстренного торможения» устанавливается в тоннеле с правой стороны по направлению движения за сигнальным знаком «Остановка первого вагона» на таком расстоянии от него, в пределах которого применение экстренного торможения обеспечит остановку поезда (состава) перед сигнальным знаком «4», «5», «6», «7», «8» (остановка первого вагона соответственно четырех, пяти, шести, семи или восьмивагонного состава). Знак указывает конец участка пути в пределах которого машинист должен применить экстренное торможение при обнаружении загорания подвижного состава с целью остановки и последующего осаживания поезда (состава) на станцию;
— знак «Остановка первого вагона» устанавливается на пути у пассажирских платформ или на путевой стене на станциях открытого типа освещаемый знак «Остановка первого вагона» устанавливается с правой стороны по ходу движения на станциях закрытого типа с освещаемым знаком располагается табличка с названием станции и номером пути; допускается размещение освещаемого (или неосвещаемого со светоотражателями, светоотражающей поверхностью) знака «Остановка первого вагона» на путях оборота станций;
— знак «Опасно» размещается с правой стороны походу движения поезда (в правильном и в неправильном направлении) на подходах к станциям закрытого типа, а также в местах стесненного габарита опасных для нахождения людей при прохождении по этим местам поезда; цифра под знаком «Опасно» указывает длину опасной зоны; знак «Опасно» требует от машиниста принять меры к немедленной остановке поезда при нахождении людей в опасной зоне;
— знаки «4», «5», «6», «7», «8» — остановка первого вагона соответственно четырех, пяти, шести, семи или восьмивагонного состава; указанные знаки также используются для остановки головного вагона при следовании сцепа объединенных поездов для высадки пассажиров на станции;
— знак «Телефон» показывает место расположения ближайшего телефона связи;
— знаки «1уп (1о)», «2уп (2о)», «Зуп (Зо)», «4уп (4о)» — остановка первого вагона для отстоя составов. Знаки устанавливаются в случаях, когда на одном пути предусмотрен отстой составов, располагаемых один за другим;
— знак «Граница рельсовой цепи» указывает машинисту номер проследованной рельсовой цепи и место возможной смены сигнального показания АЛС в кабине управления поездом, составом знаки устанавливаются у изолирующих стыков, а на бесстыковых рельсовых цепях: — в точках подключения оборудования к рельсам; на главных путях перегонов и станций знаки устанавливаются с правой стороны по ходу движения в правильном направлении, а в пределах пассажирской платформы;
— на шпале между ходовыми рельсами; на остальных путях допускается установка знаков слева по ходу движения;
— допускается установка знака «Ограждение сходного устройства на станционный путь»; знак устанавливается на шпале между ходовыми рельсами на станции у сходных устройств с платформы на путь, а в тоннеле на расстоянии 140 м от сходного устройства для четырех, пятивагонного состава и 200 м для шести, семи, восьмивагонного состава;
— знак «Ограждение металлоконструкции (МК)» устанавливается перед металлоконструкцией с правой стороны по ходу движения в правильном направлении на расстоянии 100 м, а после МК на расстоянии 200 м.
— знак «Предел» указывает место остановки первого вагона на пути оборота. Устанавливается на путях оборота, оборудованных дублирующими электромеханическими автостопами.
В необходимых случаях в соответствии с указаниями Управления метрополитена некоторые сигнальные знаки могут быть световыми, со светоотражателями или со светоотражающей поверхностью.
1. Инструкции по сигнализации на метрополитенах РФ. Издание Москва 2006. Е. Г. Дубченко, стр.120
2.Техническое обслуживание и ремонт подвижного состава метрополитенов. Издательство «Транспорт» 1987. Э. А. Сементовский, стр.327
3. Электропоезда метрополитена. Издательский центр «Академия» 2003. Э. М. Добровольская, стр.320
4. Рабочая тетрадь по учебной дисциплине УТОРУЭ
5. УПЦ Пневматическое оборудование. Методическое пособие для машинистов электропоездов по вагонам 81−717/714. Составил преподаватель УПЦ Карпов О.П.
6. Метрополитены. Москва Транспорт 1988. В.П. Калиничев
7. Учебное пособие по изучению устройства, работы и ремонта электрического оборудования вагонов метрополитена серии 81−717.5М/81−714.5М. Сорокин Г. И, Краевянов В. А. Москва 2001 г., стр.351
8. Организация движения поездов и работа станций метрополитена. Бакулин А. С., Пронин В. А. Москва «транспорт» 1981 г.
9.Сооружения устройства и подвижной состав метрополитена. Бакулин А. С., Кудринская К. И., Москва «Транспорт» 1979 г. Стр.239
10. Комментарии к правилам технической эксплуатации метрополитенов РФ. Москва «ИКЦ академика» 2002 г.
11. Руководство по эксплуатации вагонов метрополитена 81−717.5/81−714.5. Гуревич Р. И., Годунов А. Б., Москва «Транспорт» 1993 г. Стр.446
12. Инструкция по маневровой работе. Минаев Г. И., Сухов С. Б., Москва 2003 г. Стр.150
.ur