Диффузионное хромирование горячедеформированных порошковых материалов на основе железа
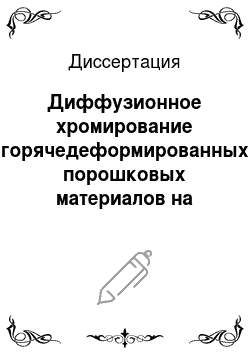
Диссертация
Следует однако отметить, что такой известный и высокоэффективный способ повышения эксплуатационных характеристик деталей, каковым является химико-термическая обработка (ХТО), в ПМ используется не в полной мере. На практике получили развитие лишь нитроцементация и парооксидирование и в значительно меньшей степени — диффузионное хромирование (ДХ) из состава засыпок. В то же время существует… Читать ещё >
Список литературы
- Kneringer G., Stickler R. Powder metallurgy in Austria// The 1. ternational journal of Powder Metallurgy/ -1996. -Vol.32. -P.213−220
- White D.G. Challenges for the 21st Century// The International journal of Powder Metallurgy. -1997. -Vol.33. -No5. -P.45−54.
- Kuhn H.A., Ferguson B.L. Powder Forging. -Princeton, New jersey: Metal Powder Industries Federation, 1990. -270 p.
- Capus J.M. Warm compacted turbine hub leads new PM thrust // Metal Powder Report. -1997. -Vol.52. -No9. -P. 19.
- Huppmann W.J. The Technical and Economic Development of Powder Forging// Powder Metallurgy International -1992. -Vol.24. -No3. -P. 186−193.
- Johnson P.K. European Conference on Advances in Structural P/M Component Production (CEURO PM97)// The International journal of Powder Metallurgy. -1998. -Vol.34. -Nol. -P.67−68.
- Jones P., Buckley-Golder K., Lawcock R., Shivanath R. Densification Strategies for High Endurance P/M Components// The International journal of Powder Metallurgy. -1997. -Vol.33. -No3. -P.37−44.
- Кидин И.Н., Андрюшечкин В. И., Волков B.A., Холин А. С. Электрохимическая обработка металлов и сплавов. -М.: Металлургия, 1978. -320с.
- Анциферов В.Н., Черепанова Т. Г. Структура спеченных сталей. -М.: Металлургия, 1981. -112с.
- Ю.Мельник П. И. Технология защитных покрытий. -Киев: Техника, 1978. -151с.
- П.Дубинин Т. Н. Диффузионное хромирование сплавов. -М.: Машиностроение, 1964. -452с.
- Бокштейн Б.С. Диффузия в металлах. -М.: Металлургия, 1978. -248с.
- ГегузинЯ.Е. Диффузионная зона. -М.: Наука, 1979. -344с.
- Манинг Дж. Кинетика диффузии атомов в кристаллах. -М.: Мир, 1971. -251с.
- Мельник П.И. Диффузионное насыщение железа и твердофазные превращения в сплавах. -М.: Металлургия, 1993. -128с.
- Криштал М.А. Диффузионные процессы в железных сплавах. -М.: Металлургия, 1963. -278с.
- Криштал М.А. Механизм диффузии в железных сплавах. -М.: Металлургия, 1972. -400с.
- Криштал М.А. Многокомпонентная диффузия в металлах. М: Металлургия, 1985. -176с.
- Блантер М.Е. Физические основы химико-термической обработки. -М.: Машгиз, 1949. -32с.
- Лахтин Ю. М. Коган Я.Д. Азотирование стали. -М.: Машиностроение, 1976. -256с.
- Самсонов Г. В., Упадхая Г. Ш., Непторов B.C. Физическое материаловедение карбидов. -Киев: Наукова думка, 1974. -455с.
- Старк Дж. Диффузия в твердых телах. -М.: Энергия, 1980. -239с.
- Архаров В.И. Основные проблемы механизма взаимодействия металлов с газами// Механизм взаимодействия металлов с газами. -М.: Металлургия, 1964. -С.24−36.
- Архаров В.И., Баланаева H.A., Богословский В. Н., Стафеева Н. М. Развитие представлений о механизме реакционной диффузии// Защитные покрытия на металлах.- 1971. -Вып 5. -С.5−11.
- Дубинин Г. Н. Хромирование стали. -М.: Металлургидат, 1950. -59с.
- Самсонов Г. В., Жунковский Г. П. Некоторые закономерности начальной стадии реакционной диффузии// Защитные покрытия на металлах. -1973. -Вып.1. -С.21−33.
- Анциферов В.Н., Акименко В. Б., Гревнов JI.M. Порошковые легированные стали. -М.: Металлургия, 1991. -318с.
- Дубинин Г. Н., Саперов В. П. Диффузионное хромирование листовых сталей//МиТОМ. -1972. -№ 6. -С. 18−23.
- Ворошнин Л.Г., Хусид Б. М. Диффузионный массоперенос в многокомпонентных системах. -Минск: наука и техника, 1979. -255 с.
- Дубинин Г. Н. О механизме формирования диффузионного слоя// Защитные покрытия на металлах. -1976. -Вып. 10. -С. 12−17.
- Анциферов В.Н., Черепанова Т. Г., Яблоновская P.P. Влияние хрома на структурные превращения в поверхностных слоях при трении спеченных материалов//Порошковая металлургия. -1975. -№ 3. -С.51−55.
- Радомысельский И.Д., Дымченко В. А. Механизм и кинетика растворения СгзСг в железе// Порошковая металлургия. -1971. -№ 3. -С.88−92.
- Минкевич А.Н. Химико-термическая обработка металлов и сплавов. -М.: Машиностроение, 1965. -492с.
- Карякина Н.В., Дубинин Г. Н. Рентгеновское исследование поверхности железа и стали после диффузионного хромирования методом порошков// ФММ.-1960. -Т.9. -С.49−51.
- Дубинин Г. Н., Ушаков Б. А. Применение алитирования и диффузионного хромирования сталей Х18Н10Т и Х12Н22ТЗмр с целью защиты поверхностей от схватывания: В сб.: Защитные покрытия на металлах. 1975, вып.9, с. 177−179.
- Лоскутков В.Ф., Хижняк В. Г., Куницкий Ю. А. Диффузионные карбидные покрытия. -Киев: Техшка, 1991. -324с.
- Салли А.Х., Брэндз Э. А. Хром. -М.: Металлургия, 1971. -360с.
- Дубинин Г. Н. Диффузионное хромирование сплавов// Металловедение и термическая обработка. -М.: Металлургия, 1962. -С. 18−23.
- Самсонов Г. В., Эпик А. П. Тугоплавкие покрытия на железе и сали. -М.: АН СССР, 1973. -399с.
- Горбунов Н.С. Диффузионное покрытие на железе и стали. -М.: АН СССР, 1958. -208с.
- Делимарский Ю.К. Теоретические основы электролиза ионных расплавов. -М.: Металлургия, 1986. -234с.
- Ворошнин Л.Г., Ляхович Л. С., Ловшенко Ф. Г., Протасевич Г. Ф. Химико-термическая обработка металлокерамических материалов. -Минск.: Наука и техника, 1977. -272с.
- Ляхович Л.С., Протасевич Г. Ф., Ворошнин Л. Г., Ловшенко Ф. Г. Особенности химико-термической обработки спеченных материалов// Химико-термическая обработка металлов и сплавов: Тез. Докл. II Всесоюз. Конф. -Минск, 1974. -С.96−104.
- Скороходов В. В./Исследование и разработка теоритических проблем в облости порошковой металлургии и защитных покрытий: Материалы всесоюзной конференции Минск, 1983. чП. -Минск.: Минвуз СССР и БССР, 1984. -с.56−61.
- Смольников Е.А. Термическая обработка инструмента в соляных ваннах. -М.: Машиностроение, 1981. -271с.
- Барабошкин А.Н. Электрокристаллизация металлов из расплавленных солей. -М.: Наука, 1976. -280с.
- Баймаков Ю.В., Ветюков М. М. Электролиз расплавленных солей. -М.: Металлургия, 1966. -560с.
- Вишняков Д.Я. Свойства расплавленных солей, применяемых в ванных печах// Труды московского ин-та стали, вып. XXVII. -М.: Металлургиз-дат, 1949.-С.126−176.
- Михайлов JI.A., Кауфман В. Г., Пылаев В. М. Методика расчета электрических параметров соляных ванн. -М.: ВНИИЭМ, 1966. -36с.
- Смольников Е.А., Жданова Ф. И. Соляные ванны для термической обработки изделий. Справочник. -М.: Машгиз, 1963. -124с.
- Смольников Е.А. Соляные ванны для нагрева металлов//МиТОМ. -1970. -№ 11. -С.71−78.
- Морочевский А.Г. Термодинамика расплавленных металлических и солевых систем. -М.: Металлургия, 1987. -240с.
- Герасимов Я.И., Гейдерих В. А. Термодинамика растворов. -М.: МГУ, 1980.-181с.
- Кубашевский О., Олкокк С. Б. Металлургическая термохимия: Пер. с англ. М.: Металлургия, 1982. -390с.
- Вагромян А.Т., Соловьева З. А. Методы исследования электроосаждения металлов. -М.: Изд-во АН СССР, 1960. 350с.
- Делимарский Ю.К. Химия ионных расплавов. -Киев.: Наукова думка, 1980. -327с.
- Бобылев A.B. Механические и технологические свойства металлов: Справ, изд. -М.: Металлургия, 1987. -208с.
- Ермаков С.С., Вязников Н. Ф. Порошковые стали и изделия -Л.: Машиностроение, 1990. -319с.
- Гегузин Я.Е. Очерки о диффузии в кристаллах -М.: Наука, 1970. -176с.
- Гегузин Я.Е. Очерки о диффузии в кристаллах -М.: Наука, 1974. -253с.
- Пористые проницаемые материалы/ Под ред. С. В Белова. М.: Металлургия, 1987. -335с.
- Пугин B.C., Корниенко А. П., Павленко Н. П., Буссель О. Д. Диффузионное хромирование пористых проницаемых материалов из спеченного порошка железа// Порошковая металлургия. -1979. -№ 8. -С.32−34.
- Пугин B.C., Корниенко П. А., Павленко Н. П., Буссель О. Д. Диффузионное хромирование пористых проницаемых материалов// Химико-термическая обработка металлов и сплавов: Тез. докл. IV Всесоюз. конф. -Минск, 1981.-С. 195−196.
- Гребнев Н.П., Худокормов Д. Н., Куцур М. Я. Некоторые особенности диффузии углерода при цементации материалов, спеченных на основе железа// Химико-термическая обработка металлов и сплавов: Тез. докл. II Всесоюзн. конф. -Минск, 1974. -С.105−109.
- Герцрикен С.Д., Дехтяр И. Я. Диффузия в металлах и сплавах в твердой фазе. -М.: Физматгиз, 1960. -564с.
- Бокштейн С.З. Диффузия и структура металлов. -М.: Металлургия, 1973. -208с.
- Слысь И.Г., Горбатов И. Н., Ткаченко Ю. Г. Особенности получения и свойства порошкового сплава на основе хрома// Порошковая металлургия.-1981.-№ 10.-С.66−70.
- Федорченко И.М., Иванова И. И., Фущич О. Н. Исследование влияния диффузионных процессов на спекание металлических порошков// Порошковая металлургия. -1970. -№ 1. -С.30−37.
- Райченко А. И Математическая теория диффузии в приложениях. -Киев: Наукова думка, 1981. -396с.
- Процессы массопереноса при спекании/ ХермельВ., Кийбак О., Шатт В. и др. -Киев.: Наукова думка, 1987. -152с.
- Гегузин Я.Е. Физика спекания. -М.: Наука, 1984 -309с.
- Карпенко Г. В. Влияние диффузионных покрытий на прочность стальных изделий. -Киев.: Наукова думка, 1971. -56с.
- Пахмурский В.И., Карпенко Г. В. Устранение дефектов типа открытых трещин на стальных деталях методом диффузионной металлизации. -ФХММ. -1967. -Т.З. -№ 4. -С.376−378.
- Сивачек М. Методы активированного спекания с использованием хлора// Порошковая металлургия. -1964. -№ 1. -С. 13−15.
- Федорченко И.М., Андриевский P.A. Основы порошковой металлургии. -Киев.: АН УССР, 1961. -420с.
- Эпик А.П., Маджид А. Химико-термическая обработка порошковых материалов на железной основе// Порошковая металлургия. -1993. -№ 8. -С.37−43.
- Химико-термическая обработка металлов и сплавов: Справ./Под.ред. JI.C. Ляховича. -М.: Металлургия, 1981. -520с.
- Эпик А.П., Белицкий М. Е. и др. Борирование и хромирование спеченных деталей на основе железа// Технология и организация производства. -1984. -№ 2. -С.41−42.
- Сычев А.Г. Исследование процесса диффузионного хромирования, структуры и свойств материалов, полученных методом динамического горячего прессования: Автореф. дис. канд. техн. наук. -Новочеркасск, 1982.-16с.
- Сычев А.Г., Проус Н. Г., Ермак А. И. Особенности образования диффузионного слоя на высокопористых порошковых сталях при насыщении хромом// Горячее прессование в порошковой металлургии: Тез. док. VII Всесоюзн. конф. -Новочеркасск, 1988. -С. 52−53
- Алексеенко Л.Е., Скибина Г. В., Шкретов Ю. П., Княжева В. М. Коррозионная стойкость сталей, хромированных циркуляционным методом// МиТОМ. -1996. -№ 11. -С.33−34.
- Кулу П.А. Влияние ковки и химико-термической обработки на свойства спеченного железа и стали// Порошковая металлургия. -1978. -№ 12. -С.22−25
- Метхьюз П.Е., Брэдбери С. Диффузионная обработка металлокерами-ческих изделий// Новое в порошковой металлургии: Труды 19-ой конф. Детройт США, 1970. -С.61−68.
- Буссель О.Д., Кулу П. А., Пугин B.C. Диффузионное хромирование пористого проницаемого железа// Порошковая металлургия. -1971. -№ 8. -С.41−47.
- Ермаков С.С., Калинин Ю. Г., Резников Г. Т. Влияние пористости и среды спекания на химико-термическую обработку спеченного железа// Горячее прессование. -Киев, 1975. -Вып.2. -С.228−236.
- Ловшенко Ф.Г., Ляхович Л. С., Высоцкий В. Т., Ловшенко З. М. Диффузионное хромирование спеченных сталей// Порошковая металлургия, 1976. -№ 9, -с.27−31.
- Лозовой В.И. Структура и свойства горячештампованных порошковых материалов и их поверхностных слоев, подвергнутых различной обработке: Автореф. дис. канд. техн. наук. -Новочеркасск, 1986. -16с.
- Куликов А.К., Позняк Н. З. Антикоррозионная обработка спекаемых конструкционных деталей счетно-аналитических машин// Порошковая металлургия, -1972. № 9, -с.31−35.
- Дорофеев Ю.Г., Жердицкий Н. Т., Мищенко В. Н. Химико-термическая обработка металлокерамических изделий, полученных методом динамического горячего прессования.// Металлокерамические конструкционные материалы. Киев: ИПМ АН УССР, 1972. -С. 135−139
- Роман О.В., Дубовская Г. Н., Кирилюк Л. М., Дедовец В. А. Свойства TiN покрытий на порошковых изделиях// Защитные покрытия на металлах. -1982. -Вып. 16. -С.76−79
- Романов Н.И., Креймер Г. С., Туликов В. И. Влияние остаточной пористости на усталостную долговечность при циклическом консольном изгибе сплавов карбид вольфрама кобальт// Порошковая металлургия. -1979. -№ 10. -С.70−72.
- Порошковая металлургия. Спеченные композиционные материалы/ Под. ред В. Шатта: пер с нем. -М., Металлургия, 1983. -520с.
- Богодухов С.И. Исследование нагрева пористых заготовок и деталей в соляных ваннах под закалку// Порошковая металлургия. Куйбышев, 1974.-Вып.1.С.171−173
- Богодухов С.М. Термическая обработка порошковых низколегированных сталей с использованием нагрева в соляных ваннах// Автореф. дис.. канд. техн. наук. -Оренбург, 1990. -17с.
- Исследование процесса хромирования спеченных сплавов в предварительно спеченных алюминотермических смесях. /Ф.Г. Ловшенко, В. Т. Высоцкий, З. М. Ловшенко и др.// Порошковая металлургия. -1977. -№ 8. -С.1−8
- Анциферов В.Н., Черепанова Т. Г., Яблоновская P.P. Влияние хрома на структуру превращений в поверхностных слоях при трении спеченных материалов//Порошковая металлургия. -1975. -№ 3. -С.51−55.
- Ю2.Делимарский Ю. К., Фишман И. Р., Зарубицкий О. Г. Электрохимическая очистка отливок в ионных расплавах -М.: Машиностроение. -1976. -208с.
- Ю4.Металлографические реактивы. Справочник/ B.C. Коваленко. -М.: Металлургия, 1973. -121 с.
- Павленко Е.В., Скачков Ю. А., Кример Б. И., Арсентьев П. П., Попов К. В., Пвилинг М. Я. Лаборатория металлографии. -М.: Металлургия, 1965.-440 с.
- Юб.Пшеничнов Ю. П. Выявление тонкой структуры кристаллов. -М.: Металлургия, 1974. -528 с.
- Металлография железа: Справочник. -Т.1 /Под. ред. Ф. Н. Тавадзе -М.: Металлургия, 1973. -240 с. Том.2: Металлография железа. -1977. -275 с.
- Ю8.Шиммель Г. Методика электронной микроскопии. -М.: Мир, 1972. -300 с.
- Ю9.Избранные методы исследования в материаловедении/ Под. ред. Г. Й. Хунгера -М.: Металлургия, 1985. -416 с.
- Ю.Горелик С. С., Расторгуев Л. И., Скаков Ю. А. Рентгенографический и электроннооптический анализ -М.: Металлургия, 1970. -336 с.
- Основы аналитической электронной микроскопии: пер. с англ. / Под ред. Д. К. Джоя -М.: Металлургия, 1990. -584 с.
- Русаков А.А. Рентгенография металлов. -М.: Атомиздат, 1977. -479 с.
- ПЗ.Миркин Л. И. Рентгеноструктурный анализ. Получение и измерение рентгенограмм: Справочник. -М.:Наука, 1976. -326 с.
- Фрактография и атлас фрактограмм: Справочник/ Под ред. Дж. Феллоуза -М.: Металлургия, 1982. -500 с.
- Металловедение и термическая обработка стали. Справочник/ Под ред. Бернштейна М. Л., Рахштадта А. Г. -4-е изд., перераб. и доп. Т.1. -М.: Металлургия, 1991.-304с.
- Морозюк А.А., Фомичева Н. Б., Рогов Н. В. Влияние толщины покрытия на упругие и неупругие характеристики стали. //Термическая обработка и физика металлов. -Свердловск, 1989. -С. 131−134.
- Горбач В.Г., Белякова А. В. Оценка прочности карбидных покрытий на металлах и сплавах по критериям разрушения.// Изв. АН СССР, -металлы. -1986. -№ 1. -С. 185−189.
- Fracture analysis of single crystal manganese zine ferrites using indentation flaws/ K. Tanaka, Y. Kitahara, Y. Ichinose, T. Iimura // Actametall/ -1984. -32, № 10. -P.1719−1729.
- Niihara K., Morena R., Hasselman D.P. Evaluation of Kic of brittle by the indentation method with low crack-to-indents ratios// J. Mat. Sci. Let. -1982. -1, № 1. -P.13−16.
- Новиков Н.В., Дуб С.Н., Булычов С. И. Методы микроиспытаний на трещиностойкость// Заводская лаборатория, -1988. -№ 7. -С.60−67.
- Сарбаш Р.И. Усталостная долговечность образцов из порошковой стали в условиях малоциклового жесткого нагружения.// Порошковая металлургия. -1988. -№ 9. -С.78−83
- Туманов А.Т. Методы испытания, контроля и исследования машиностроительных материалов//Физические методы исследования металлов. -М.: Машиностроение, 1971. -349с.
- Романов В.В. Методы исследования коррозии металлов. -М.: Металлургия, 1965.-280с.
- Структура и коррозия металлов и сплавов: Атлас. Справ, изд./ Сокол И. Я., Ульянин Е. А., Фельдгандлер Э. Г. и др. -М.: Металлургия, 1989.-400с.
- Легирование порошковой железной матрицы хромом и его соедине-ниями./Мазуренко Е.А., Сердюк Г. Г., Забора H.A. и др.// Порошковая металлургия. -1991. -№ 5. -С.23−27.
- Коррозионная стойкость сталей, хромированных циркуляционным ме-тодом/Алексеенко Л.Е., Скидина Г. В., Шкретов Ю. П. и др.// МиТОМ. -1996. -№ 11. -С.33−34.
- Новиков Ф.С., Арсов Я. Б. Оптимизация процессов технологии металлов методами планирования экспериментов. -М.: Машиностроение- София: Техника 1980. -304с.
- Адлер Ю.П., Маркова Е. В., Грановский Ю. А. планирование эксперимента при поиске оптимальных условий. -М.:Наука, 1976. -279с.
- Крагельский И.В., ДобычинМ.Н., Камалов B.C. Основы расчета на трение и износ. -М.: Машиностроение, 1977. -526с.
- Алабышев А.Ф., Лантратов М. Ф., Морачевский А. Г. Электроды сравнения в расплавленных солях. -М.: Металлургия, 1965. -430с.
- Баймаков Ю.В., Ветюков М. М. Электролиз расплавленных солей. -М.: Металлургия, 1966.-315с.
- Смирнов М.В. Электродные потенциалы в расплавленных хлоридах. -М.: Наука, 1973.-456с.