Разработка теоретических и технологических основ повышения стойкости режущего и штампового инструмента за счет диффузионной металлизации из среды легкоплавких жидкометаллических растворов
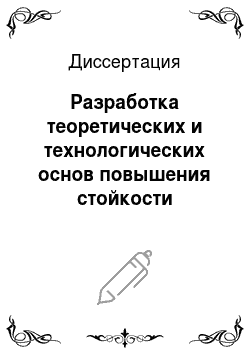
Диссертация
Работоспособность инструментов в большинстве случаев определяется свойствами их поверхностных слоев, вследствие этого диффузионной металлизацией инструмента можно значительно повышать его работоспособность. При этом, в отличие от химико-термических обработок, в основе которых лежит либо насыщение поверхности инструмента элементами внедрения, либо нанесение слоев на базе карбидов, нитридов… Читать ещё >
Список литературы
- Геллер Ю.А. Инструментальные стали. М.: Металлургия, 1983. — 527с.
- Лоладзе Т.Н. Прочность и износостойкость режущего инструмента. М.: Машиностроение, 1982. — 320 с.
- Коцаньда С. Усталостное разрушение металлов. М.: Металлургия, 1976. -225 с.
- Берштейн М.Л., Займовский В. А. Механические свойства металлов. — М.: Металлургия, 1979. -495 с.
- Михин Н.М., Ляпин К. С. Зависимость коэффициента трения от твердости и экспериментальная проверка. М.: Физика, 1970. — № 3. — С. 50−54.
- Моисеев В.Ф., Фуке-Рабинович Г.С., Быков М. В. О механизме износа штамповой стали при вырубке. Металловедение и термическая обработка в автомобилестроении, 1979. вып.1 С. 31−37.
- Похмурский В.И. Коррозионная усталость металлов. — М.: Металлургия, 1985.-206 с.
- Воробьева Г. А., Складнова Е. Е., Леонов А. Ф., Ерофеев В. К. Инструментальные материалы. СПб.: Пилитехника, 2005. — 260 с.
- Терновой Ю.Ф., Терехов В. Н., Канюка В. И., Мороз А. Н. Современные инструментальные стали и их рациональное применение // Металлургическая и горнорудная промышленность. 2006.- № 6. — С.83 -89.
- Ю.Позняк Л. А. Инструментальные стали. Киев: Наукова думка, 1996. -488 с.
- Брострем В.А., Кремнев Л. С. Теплостойкость инструментальных сталей // МиТОМ. 1973. — № 3. — С. 46 -51.
- Гработовский В.Я., Канюха В. И. Результаты разработки аустенитных штамповых сталей и сплавов для горячего деформирования металлов // МиТОМ.-2001. -№−10.-С. 31 -34.
- Патент № 2 100 456 РФ, МКИ3 В23 В 27/00. Способ упрочнения изделий из углеродистых, легированных, высоколегированных, быстрорежущих сталей и твердых сплавов / Ерофеев В. К., Григорьев В. В. Воробьева Г. А. (РФ) 27.12.97, Бюл. №−36−5с.
- Багмутов В.П., Захаров И. Н. Основные зависимости образования регулярных дискретных структур поверхностного слоя в ходе импульсной электромеханической обработки // Упрочняющие технологии и покрытия. 2005. — № 10. — С. 39 — 45.
- Дудкин Н.Г., Захаров И. Н., Ермолов B.C., Иванников М. Ю. Проблемы машиностроения и надежности машин // Российская академия наук, журнал № 5. 2006. — С. 62 — 68.
- Справочник по триботехнике / Под ред. М. Хебды, А. В. Чтчнадзе.- М.: Машиностроение. Т. 1.- 1989. — 400 с.
- Электромеханическая обработка: технологические и физические основы, свойства, реализация / В. П. Багмутов, С. Н. Паршев, Н. Г. Дудкина, И. Н. Захаров. Новосибирск: Наука, 2003. — 318 с.
- Дудкина Н.Г., Арисова В. Н., Захаров И. Н. Исследование структуры поверхностного слоя при электромеханическом упрочнении углеродистых сталей // Металлы. 2003. — № 1. — С.78−83.
- Дудкина Н.Г., Захаров И. Н. Исследование микротвердости поверхностного слоя сталей после электромеханической обработки // Металлы. 2004. — № 4. — С.64 — 70.
- Калита В.И., Комлев Д. И. К вопросу формирования металлов в аморфном состоянии // Металлы. 2003. — № 6. — С. ЗО — 37.
- Шатов Ю.С. Свойства композиционных электрохомических покрытий на основе хрома со сверхтвердыми дисперсионными наполнителями // Черная металлургия. 1998. — № 7. — С.55−60.
- Бутаков Б.И. Методы динамического упрочнения металлов и сплавов // Кузнечно-штамповое производство. — 1988. № 7. — С.7 — 11.
- Бабей Ю.И., Бутаков Б. И., Сысоев В. Г. Поверхностное упрочнение металлов. Киев: Наукова Думка, 1995. — 256 с.
- Аскинази Б.М. Упрочнение и восстановление деталей электромеханической обработкой. — М.: Машиностроение, 1968. — 164 с
- Коваленко B.C. Лазерное и электроэрозионное упрочнение материалов. — М.: Наука, 1986.-192с.
- Гуреев.Д. М. Структурообразование при лазерно-звуковом расплавлении поверхности быстрорежущих сталей // Физика и химия обработки материалов. 1998. — № 2. — С. 41 — 44.
- Коваленко B.C. Лазерное и электроэрозионное упрочнение материалов. -М.: Наука, 1986.- 192с.
- Зубков Н.С., Булкин Д. В., Золотов А. А. Наплавленная инструментальная штамповая сталь повышенной износостойкости. Вестник ТГТУ. Тверь, 2004.
- Изготовление, восстановление и упрочнение металлорежущего инструмента // Сборник научных трудов. Тверь: ТГТУ, 1997. — 96 с.
- Yilbas В. Laser cutting quality assessment and thermal efficiency analysis // Journal of Materials Processing Technology. 2004.V. 155 156. P.2106 -2115.
- Основы трибологии (трение, износ, смазка) /Э.Д. Браун, Н. А. Буше, И. А. Буяновский и др. / Под ред. А. В. Чичинадзе М.: «Наука и техника», 1995.-778 с.
- Справочник по конструкционным материалам. Под ред. Б. Н. Арзамасова, Т. В. Соловьевой. -М.: изд. МГТУ имени Н. Э. Баумана, 2005. -320 с.
- Романов С.Р., Каргин А. В., Копылов Д. Ю., Перевезенцев Б. Н. Технология плазменно-порошковой наплавки выпускных клапанов двигателей автомобиля «ВАЗ» // Сварочное производство. 2005. — № 2.- С. 33 — 40.
- Мусина К.И., Жаткин С. С. Исследование процесса плазменной наплавки покрытий на сталь 19ХГНМА-В // Высокие технологии в машиностроении: Тез. докл. Самара, 2006. С. 56 — 60
- IIyasov V., Zhdanova Т., Nikiforov I. Electronic Structure and X-ray Spectra of the System SiC-(Al, Ti, C) // Phys. stat/sol. (b), 2002, Vol. 229, № 3, 1187 -1190.
- Зверев А.И., Шаривекер С. Ю., Астахов E.A. Детонационное напыление покрытий. Л.: Судостроение, 1979.
- Гавриленко Т.П., Кирякин А. Л., Николавев Ю. А., Ульяницкий В. Ю. Автомотизированный детонационный комплекс «Обь» для нанесенияпорошковых покрытий // Современные технологии автомотизации. — 2006. № 4. — С. 47 — 52.
- Ульяницкий В.Ю., Штерцер А. А., Злобин С. Б. Структура и трибологичеекие свойства износостойких детонационных покрытий // Физическая мезомеханика. 2006. — Т.9. — № 4. — С. 87 — 92.
- Гладков В.Ю., Кравцев С. В., Кравченко И. Н. Ресурсосбережение при восстанослении и упрочнении деталей строительных и дорожных машин пламенными покрытиями. М.: изд-во ВТУ, 2005 230 с.
- Лавро В.Н. Прогнозирование надежности режущего инструмента с износостойкими ионно-плазменными покрытиями // Актуальность проблем надежности технологических, энергетических и транспортных машин: Тез. докл. — Самара, 2003. — С. 23−25.
- Аль-Тибби В. Х. Влияние диспертности микроструктуры покрытий, получаемых методом электроакустического напыления на износостойкость режущего инструмента. Дисс. На соискание ученой степени кандидата технических наук. Ростов-на-Дону, 2006. — 177 с.
- Лавро В. Н. Лавро И.В. Совершенствование технологии упрочнения и прогнозирования работоспособности режущего инструмента с ионно-плазменными покрытиями //8 международная практическая конференция-выставка. 4.2. СПБ.: СПбГПУ. 2006. — С.71−74.
- Тополянский П.А., Ермаков С. А., Соснин Н. А. Твердость тонкопленочного покрытия, наносимого методом финишного плазменного упрочнения // 7 международная практическая конференция-выставка. СПБ.: СПбГПУ. 2005. — С.291−301.
- Карапетян К.Г. Химико-термическая обработка титановольфрамовых твердых сплавов // Актуальные проблемы современной науки. М.- 2003. — № 5 (14). — С.199−201.
- Криштал М.А., Гринберг Е. М. Изменение структуры железа при диффузии бора // МИТОМ. 1974. — № 4. — С.2 — 6.
- Лебедев В.А., Подольский М. А. Оценка эффективности упрочнения деталей методами ППД на основе термодинамических представленений процесса // Вестник машиностроения. 2004. — № 6. — С.34 -40
- Криштал М.А., Гринберг Е. М. Изменение структуры железа при диффузии бора // МИТОМ. 1974. — № 4. — С.2 — 6.
- Шатинский В.Ф., Збожная О. М., Максимович Г. Г. Получение диффузионных покрытий в среде легкоплавких металлов. — Киев: Наукова Думка, 1976. 202 с.
- Лахтин Ю.М., Неустроев Г. Н., Иванов Ю. П. МиТОМ, 1973, № 12, с. 27 -31.
- Карпов Л.П. Применение двойной химико-термической обработки при изготовлении инструмента из конструкционных сталей. МиТОМ № 1 2003.
- Тарасов А.Н., Колина Т. П. Структура и свойства нитроцементованных сталей 4Х5МФС и 20X13, используемых для изготовления режущего инструмента. МиТОМ, № 5, 2003.
- Семенова Л.М., Семенов Е. В., Крайнова С. Н. Химико-термическая обработка стали 20Х в условиях циклического изменения температуры. -МиТОМ, № 1,2003.
- Котляренко Л.А., ЭпикА.П. — Защитные покрытия на металлах. 1970, № 3, с. 31−35.
- Бельевский Е.И., Ситкевич М. В., Рогов В. А., Крюков В. П. МиТОМ, 1980, № 6, с. 17−19.
- Химико-термическая обработка металлов и сплавов: Справочник. М., Машиностроение, 1981. 424 с. с ил.
- Баландин Ю.А. Боразотирование штамповых сталей в псевдосжиженом слое. МиТОМ, № 9 2004.
- Баландин Ю.А. Упрочнение поверхности штамповых сталей борирование, бормеднением и борхромированием в псеводосжиженом слое. МиТОМ, № 3 2005.
- Геллер Ю.А., Павлова Л. П., Сорокин Г. М. МиТОМ, 1972, № 1, с.48 — 54.
- KosterK. Tew. Techn. Ber., Bd 1, № 2, S. 136−141.
- Верещака A.C. Работоспособность режущего инструмента с износостойкими покрытиями. М.: Машиностроение, 1993. — 336 с.
- Аксенов И. И. Хороших В.М. Потоки частиц и их массоперенос в вакуумной дуге: Обзор. М.: ЦНИИ атоминформ, 1984. — 392 с.
- Ионная имплантация / Под ред. Хирвонена Дж. К.: Пер. с англ. М.: Металлургия, 1985. 392 с.
- Исследование влияния давления газа в объеме на параметры капельной фазы эрозии катода стационарной вакуумной дуги / И. И. Аксенов, Е. Е. Кудрявцева, В. В. Кунченко и др. ХФТИ АНУССР 84−18. М.: ЦНИИ атоминформ, 1984. 17с.
- О плазменном нанесении покрытий на упрочненную сталь с низкой температурой отпуска / А. А. Андропов, В. Г. Брель, А. Т. Калинин и др. // Защита металлов. Т. XIV. 1978. № 5. С. 551−557.
- Сато Синдзо. Новые способы быстрого низкотемпературного азотирования угледодистых сталей. Киндзоку дзайре, Metals in Engineering, 1973, vol. 13, № 1. p. 85 — 102.
- Дубинин Г. Н. Диффузионное хромирование сплавов.- М.: Машиностроение, 1964. -452 с.
- Carter G.F. Diffusion Coatings Formed in Molten Cflcium Impart High Corrosion Resistance. Metal Progress, 1968, 93, 6.
- Максимович Г. Г., Шатинский В. Ф., Копылов В. И. Физико-химические процессы при плазменном напылении и разрушении материалов с покрытиями. Киев: Наукова думка, 1983. — 248 с.
- Шатинский В.Ф., Артемьев В. П., Чаевский М. И. Процессы, происходящие на межфазной границе твердый — жидкий металлы з эвтектическим расплаве свинец-висмут // Адгезия расплавов и пайка материалов. Киев: Наукова Думка. — 1987. — Вып. 18. — С. 55 — 58 .
- Терешин В.А., Дубовенко В. П., Шатинский В. Ф., Борисов А. В. Критерий возможности получения защитных покрытий из жидкой фазы / В кн.: Диффузионные процессы в металлах. Тула: ТПИ, 1975.- Вып.З. — С.136 — 139.
- Попаль С.И., Павлов В. В. Термодинамический расчет поверхностного натяжения растворов / В кн.: Поверхностные явления в расплавах и возникающие из них твердых фаз. Нальчик: 1965. — С. 41 — 50.
- Способ химико-термической обработки изделий спрессованных из металлических порошков / Артемьев В. П., Соколов Е. Г., Юрчик С. М. -Патент РФ № 2 174 059. 11.01.2000. -Б.И. № 27.
- Самсонов Г. В., Эпик А. П. Тугоплавкие покрытия. М.: Металлургия, 1973.-398 с.
- Ляхович Л.С., Ворошнин Л. Г., Щербаков Э. Д., Панич Г. Г. Силицирование металлов и сплавов. Минск: Наука и техника, 1972. -279 с.
- Бледнова Ж.М. Восстановление сплошности селективным осаждением легирующего компонента из жидкой фазы / Сопротивление материалов в 1 агрессивных средах, Краснодар, 1986. — С. 28−49.
- Пат. 964.323 Великобритания С 23 с 1/00. Improvements in or relating to the Formation of Coatings on Ferrous Articles / E.J. du Pont de Nemours and Company (США) -№ 28 138/60- Заявлено 15.08.60- Опубл. 22.07.1964.
- Пат. 1.386.172 Франция С 23 с. Prjcede pour entrober dearticles en metal ferreux par diffusion / Jhon J. Rauch, Ray J. Van Thynt E.I. DU PONT DE NEMOURS AND CO. residant aux Etats-Unis d' Amerique № 968.718- Заявлено 07. 12. 64- Опубл. 1965.
- Пат. 3.620.816 США С 23 с 1/00. Metod of diffusion coating metal substrates using molten lead AS transport medium / Alfred L. Leavitt, J.R. Batten № 763.187- Заявлено 16.10.68- Опубл. 16.11.71.
- Пат. 3.467.545 США С 23 с 1/10 Alloy diffusion coating process / F. Carter- Заявлено 29.05.63- Опубл. 16.09.69.
- Пат. 3.481.770 С 23 с 1/10 Process for preparing alloy diffusion coatings / Charles H. Lemke, Niagara Falss. № 539.299- Заявлено 01.04.66- Опубл. 02.12.69.
- Пат. 118 052 С 23 с 1/10 Fremgansmade til diffusions overtrxhning of emner of uxdle, tugtameltelige metaller / Argyriades D., Carter F. Опубл. 28.12.70.
- Пат. 3.251.719 С 23 с 1/00 Frederick Tepper, John Wilson Maustaller, John G/ Gerken. Опубл. 17.05.66.
- A.c. 298 701 СССР. МКИ С 23 с 9/10. Способ получения покрытий на основе молибдена / М. И. Чаевский., М. С. Гойхман. № 128 697- Заявлено 29.11.68- Опубл. 23.03.71. Бюл. № 11. — 2 с.
- А.с. 802 398 СССР. МКИ С 23 с 9/10. Способ получения многокомпонентных покрытий / М. И. Чаевский, В. П. Артемьев. — № 2 633 456- Заявлено 27.06.78- Опубл. 07.02.81. -Б.И. № 5.-5 с.
- А.с. 1 594 800 СССР. Способ химико-термической обработки изделий / В. П. Артемьев, В. Ф. Шатинский, М. М. Кицак, Е. М. Рудковский, П. М. Худык. Заявлено 27.01.88- Опубл. 06.09.91, ДСП № 6. -3 с.
- Способ получения диффузионных многокомпонентных защитных покрытий / М. И. Чаевский, В. П. Артемьев, С. М. Пилюгин. А.с. 644 869 СССР. — 1979.-Б.И. № 4.
- Карпман М.Г. Выбор метода и способа диффузионного насыщения поверхности изделий // «Металловедение и термическая обработка металлов». 1982. — № 4. — С. 19−20.
- Способ химико-термической обработки стальных изделий / В. П. Артемьев, М. И. Чаевский. А. с. 954 502 СССР. — 1982. — Б.И. № 32.
- Влияние диффузионных покрытий на прочность стальных изделий / Карпенко Г. В. и др. Киев: Наукова думка, 1971. — 250 с.
- Смольников Е.А. Термическая и химико-термическая обработка инструмента в соляных ваннах. 2-е изд., перераб. и доп. — М.: Машиностроение, 1989. -312 е.: ил.
- Артемьев В.П. Формирование диффузионных вольфрамовых покрытий на сталях / В сб.: Температуроустойчивые функциональные покрытия. Тула, 2001.
- Артемьев В.П. Разработка научных и технологических основ химико-термической обработки сталей в жидкометаллических расплавах : Дис. д-ра техн. наук: 05.01.02. Краснодар, 2001. — 352 с.
- Бокштейн B.C. Диффузия в металлах.- М.: Металлургия, 1978. -248с.
- Гальванотехника / Ажогин Ф. Ф., Беленький М. А., Галль И. Е. и др. М.: Металлургия, 1987. 736 с.
- Глухов В.П. Боридные покрытия на железе и сталях. — Киев: Наукова думка, 1970. 205 с.
- Тушинский JI.И. Теория и технология упрочнения металлических сплавов. Новосибирск: Наука, 1990. — 306 с.
- Самсонов Г. В. Тугоплавкие соединения. / Винницкий И. М. М.: Металлургия, 1976. — 560 с.
- Соколов А.Г. Трещиностойкость поверхностно-упрочненных конструкционных сплавов: дис. канд.техн.наук: 05.02.01. — Ленинград, 1982.-206 с.
- Соколов А.Г. Новый способ сварки режущего инструмента из разнородных материалов с одновременным нанесением покрытия. / Иванова Т. И., Куркова О. П., Сивенков А. В. Л.: ЛДНТП, 1989. — 20 е., ил.
- Похмурский В.И. Повышение долговечности деталей машин с помощью диффузионных покрытий / Далисов В. Б., Голубец В. М. — Киев: Наукова думка, 1980. 188 с.
- Вол А. Е. Строение и свойство двойных металлических систем. -М.: Физматгиз, 1962. 300с.
- Диагрммы состояния двойных и многокомпонентных систем на основе железа. Справочник / Под ред. О. А. Банных и М. Е. Дрица. М.: Металлургия, 1986. — 439 с.
- Заявка 200 512 724 РФ, МКИ7 С23 С28/02. Устройство для диффузионной металлизации в среде легкоплавких жидкометаллических растворов / А. Г. Соколов, В. П. Артемьев (РФ) — Заявлено 29.08.05- Опубл. От4.08.06 -Юс.
- Заявка 2 005 131 664 РФ, МКИ7 С23 G 1/14. Способ очистки стальных изделий от следов свинцовых расплавов и устройство для его осуществления / А. Г. Соколов (РФ) Заявлено 12.10.05 — 10 с.
- Беккерт М., Клемм X. Справочник по металлографическому травлению. М.: Металлургия, 1979. — 336 с.
- Дунин-Барковский И.В., Карташов А. Н. Измерение и анализ шероховатости, волнистости и некруглости поверхности. М.: Машиностроение, 1978. — 229 с.
- Максимович Г. Г., Шатинский В. Ф., Гойхман М. С. Диффузионные покрытия драгоценными металлами. Киев: Наукова Думка, 1978. — 168 с.
- Никитин В.И. Физико-химические явления при воздействии жидких металлов на твердые . — М.: Атомиздат, 1967. 320 с.
- Глухов В.П. Боридные покрытия на железе и сталях. — Киев: Наукова думка, 1970. 205 с.
- Дубинин Г. Н. Диффузионное хромирование сплавов. М.: ' Машиностроение, 1964. — 452 с.
- Никитин В.И. Взаимодействие конструкционных материалов с жидкими металлами // Теплоэнергетика. 1962. — № 2 — С. 90 — 92.
- Горбунов Н.С. Диффузионные покрытия на железе и стали. М.: Изд-во АН СССР, 1958. — 207 с.
- Самсонов Г. В., Кайдаш Н. Г. Состояние и перспективы создания многокомпонентных диффузионных покрытий на металлах и сплавах / В кн.: Защитные покрытия на металлах и сплавах. Киев: Наукова думка, 1976.-Вып. 10.-С.5−12.
- Рябов В.Р. Алитирование стали. М.: Металлургия, 1973. — 239 с.
- Силицирование металлов и сплавов / JI.C. Ляхович, Л. Г. Ворошнин, Э. Ю. Щербаков, Г. Г. Панич. — Минск: Наука и техника, 1972. 279 с.
- А.с. 298 701. Способ получения покрытий на основе молибдена / Чаевский М. И., Гойхман М. С. Опубл. 15.01.71.
- А.с. 280 158. Способ химико-термической обработки/ Чаевский М. И., Гойхман М. С. Опубл. 9.11.71.
- Щербинский Г. В. Диффузия в многокомпонентных системах / В кн.: Диффузионные процессы в металлах. Тула, 1973. с. 62 — 68.
- Земсков Г. В., Коган P.JI. Многокомпонентное диффузионное насыщение металлов и сплавов. М.: Металлургия, 1978. — 208 с.
- Герцрикен С.Д., Дехтяр И. Я. Диффузия в металлах и сплавах в твёрдой фазе. М.: Физматгиз, 1969. — 564 с.
- Carter G.F. Diffusion coating fromed in molten calcium impart high corrosion resistance. Metal Progr., 1968, 93 № 6 p. 1123 — 1128.
- Carter G. F., Fleming R.A. Diffusion coatings formed in molten calcium systems/ Reactions in Ca Fe — Cr systems. — J. Less-Common Metals, 1968. 14 № 2 .p. 328−336.
- Miyooski Yasuhiko, Kado Satoshi, Otoguro Yasuv, Muda Noboru/ Bosyoku gyutsu. Gross. Eng., 1975, 24, № 4. P. 177 — 182.
- Артемьев В.П., Шатинский В. Ф. О диффузии в металлах. Изв. Высш. Учеб. Завед. Технические науки. — № 4. — 1997. — С. 46 — 48. J
- А.с.1 338 988 СССР, МКИ3 В 23 К 1/00. Способ высокотемпературного диффузионного соединения материалов / А. Г. Соколов, Т. И. Иванова, В. В. Соколов, В. Я. Поручиков № 4 016 535/31−27- Заявлено 31.01.86- Опублик. 23.09.87, Бюл. № 35. -2 с.
- Никитин В.И. Взаимодействие конструкционных материалов с 1 жидкими металлами // Теплоэнергетика. 1962. — № 2 — С. 90 — 92.
- Балашенко Д.Ю. Явление переноса в жидких металлах и полупроводниках. М.: Атомиздат, 1970. — 399 с.
- Хансен М., Андерко К. Структуры двойных сплавов. М.: Металлургиздат, 1962. — 456 с.
- Термодинамические свойства неорганических веществ. Справочник / Под ред. А. П. Зефирова. М.: Атомиздат, 1965. — 457 с.
- А.с. 1 772 215 СССР, МКИ3 С23 СЮ/22. Способ нанесения диффузионных покрытий на стальные изделия / А. Г. Соколов, Т.И.
- Иванова, А.В. Севенков № 4 928 593/02- Заявлено 30.10.91- Опублик. 30.10.92, Бюл. № 40.-2 с.
- А.с. 1 504 286 СССР, МКИ3 С23 СЮ/22. Способ нанесения диффузионных покрытий на стальные изделия / А. Г. Соколов, Т. И. Иванова, А. В. Севенков № 428 182/31−02- Заявлено 04.05.87- Опублик. 30.08.89, Бюл. № 32. — 2 с.
- Соколов А.Г., Тимофеев Б. Т. Влияние введения добавок лития и олова на свойства свинцовых и свинцово-висмутовых расплавов // Вопросы материаловедения.- 2007. № 3. С.293−300.
- А.с. 1 505 698 СССР, МКИ3 В 23 К1/00. Способ высокотемпературного диффузионного соединения материалов / А. Г. Соколов, Т. И. Иванова, А. В. Сивенков № 4 286 394/31−27- Заявлено 20.07.87- Опублик. 07.09.89, Бюл. № 33. — 2 с.
- Справочник по пайке: Справочник / Под ред. И. Е. Петрунина, 2-е изд., перераб. и доп. — М.: Машиностроение, 1984. — 400 е., ил.
- Задумкин С.Н. Связь между поверхностными энергиями в твердой и жидкой фазах В кн.: Поверхностные явления в расплавах и возникающих из них твердых фаз. Нальчик, 1965. С. 98 104.
- Лахтин Ю.М., Арзамасов В. Н. Химико-термическая обработка металлов. М.: Металлургия, 1984. 256 с.
- Артемьев В.П., Шатинский В. Ф. Ускорение диффузии в металлах // Тез. докл. 3-го Собрания металловедов России. — Рязань, 1996. С. 27 -28.
- Смольников Е.А., Сарманова JI.M. Борирование стали в экономичных по составу солевых расплавах // МиТОМ, 1987. № 1. С 41 -45.
- Соколов А.Г. Новые технологии повышения работоспособности инструмента / В кн.: Труды Кубанского государственного технологического университета. Том XX. Серия: Механика и машиностроение. Краснодар, 2004. С. 223 — 227.
- Архаров В.И., Конев В. Н. Исследование по жаропрочным сплавам. -М.: 1971.-Т.7.-221 с.
- Архаров В.И., Конев В. Н. Жаростойкие материалы Киев: Наукова думка, 1970.-Т.7.-221 с.
- Ляхович Л.С. Многокомпонентные диффузионные покрытия. -Минск: Наука и техника, 1974. 288 с.
- Пат. № 2 293 792 МПК С23С 12/00. Способ повышения износостойкости стальных изделий / А. Г. Соколов, В. П. Артемьев (РФ). — Заявлено 04.07.05- Опубл. 20.02.07, Бюл. № 5 -4с.
- А.с. № 994 171 СССР, МКИ3 В 23 К 1/00. Способ высокотемпературного диффузионного соединения материалов / М. И. Чаевский, А. Г. Соколов № 3 241 859/25−27- Заявлено 26.01.81- Опублик. 07.02.83, Бюл. № 5.-2 с.
- А.с. № 994 909 СССР, МКИ3 В 23 К 1/00. Устройство для определения остаточных напряжений / М. И. Чаевский, А. Г. Соколов (РФ) № 3 241 859/25−27- Заявлено 26.01.81- Опублик. 07.02.83, Бюл. № 5. -2 с.
- Патент № 2 271 265 РФ, МКИ3 В23 В 27/00. Инструмент для обработки резанием и давлением / Соколов А. Г., Артемьев В. П., Соколов Е. Г., Чалов А. А. (РФ) 5с. ,
- Sokolov A.G. Influence of Nature of Metal Elements Dissolved in Lead Melt on Mechanism of their Diffusion Interaction with Steel Placed into Lead Melt / Proceedings of International Conference. Mechanika. 2006 p. 320−323.
- Покрытия для деталей машиностроения / Т. И. Иванова, А. Г. Соколов, С. К. Конев, А. В. Сивенков. -Л.:ЛМИ, 1989. 89с.
- Смителз К. Дж. Металлы. М.: Металлургия, 1980. — 456 с.
- Прокошкин Д.А., Супов А. В., Кошенков В. Н., Богомолов A.M. -МиТОМ, 1981, № 4, С. 21−23.
- Свойства элементов. Справочник: В 2 т. Т.1. Физические свойства элементов / Под ред. Г. В. Самсонова. М.: Металлургия, 1976. 600с.
- Болтон У. Конструкционные материалы: металлы, сплавы, полимеры, керамика, композиты. Справочник. 2-е изд., стер./ Пер. с анг. -М.: «Додэка- XXI», 2007. 320с.
- Машиностроение. Энциклопедия. Цветные металлы и сплавы. Композиционные металлические материалы. / Под общ. Ред. И. Н. Фридляндера. М.: Машиностроение, 2001. 880 с
- Болтон У. Конструкционные материалы: металлы, сплавы, полимеры, керамика, композиты. Справочник. 2-е изд., стер./ Пер. с анг. — М.: «Додэка- XXI», 2007. 320с.
- Машиностроение. Энциклопедия. Цветные металлы и сплавы. Композиционные металлические материалы. / Под общ. Ред. И. Н. Фридляндера. М.: Машиностроение, 2001. 880 с
- Архаров В.И., Борисов B.C., Тагиров Д. М. Регулирование механических свойств сплавов никеля внутренним окислением // МиТОМ. 1966. — № 2. — С. 11−13.
- Колчаев Б. А., Елагин В. Н., Ливанов В. А. Металловедение и термическая обработка цветных металлов и сплавов. М.: МИСиС. 2001. 416 с.
- Новые материалы / Под ред. Ю. С Карабасова. М5: МИСиС, 2002. 736.
- Смирягин А.П., Смирягина Н. А., Белова А. В. Промышленные цветные металлы и сплавы. М.: Металлургия, 1974. 448 с Тихонов Б. С. Тяжелые цветные металлы: Справочник. М.: Цветметинформация, 1999. 416 с.
- Физическое металловедение: В 3 т. Под ред. Р. У. Канна и П. Хаазена. Т. 1: Атомное строение металлов и сплавов. М.: Металлургия, 1987. 640 с.
- Осинцев О.Е., Федоров В. Н. Медь и медные сплавы. Отечественные и зарубежные марки: Справочник. М.: Машиностроение, 2004. — 336с., ил. Двойные и многокомпонентные системы на основе меди: Справочник / Под ред. Н. Х. Абрикосова. М.: Наука, 1979. 248 с.
- Соколов А.Г., Артемьев В. П. Влияние технологических факторов и химического состава сталей на структуру и свойства диффузионных никельсодержащих покрытий // МиТО.- 2007, № 4
- Пат. № 62 654 РФ, МКИ7 С23 G 1/14. Режущий инструмент для гидромеханических скважинных перфораторов / Соколов А. Г., Артемьев В. П., Соколов Е. Г., Чалов А. А. (РФ) Заявлено 20.12.2006- опубл. от 27.04.07, бюл. № 12.
- Пат. № 2 312 164 РФ, МПК С23 С 2/08 (2006.01). Способ нанесения покрытий на стальные изделия / А. Г. Соколов (РФ) Заявлено 02.05.2006- опубл. от 10.12.2007, бюл. № 34.
- Артемьев В.П., Соколов А. Г., Чалов А. А., Соколов Е. Г., Макарова И. В. Кинетика формирования медно-никелевых диффузионных покрытий на сталях // Инновации в машиностроении.: Тез.докл.науч.-тех.конф. -Пенза. 2004. С. 12−15.
- Sokolov A. Influence of Nature of Metal Elements Dissolved in Lead Melt on Mechanism of their Diffusion Interaction with Steel Placed into Lead Melt // Proceeding of International Conference. Mechanika.2006.- P. 320−323.
- Чалов A.A., Артемьев В. П., Соколов А. Г., Соколов Е. Г. Упрочнение режущих накатных роликов гидромеханических скаженных перфораторов методом химико-термической обработки //"Нефтегазовое дело" Уфа, 2006. http: ogbus.ru/authors/ Chalov/Chalovl .pdf
- Соколов А.Г., Артемьев В. П. Повышение работоспособности инструмента методами диффузионной металлизации. Ростов-на-Дону: Изд-во СКНЦ ВШ, 2006. 228 е.: ил.
- Соколов А.Г., Артемьев В. П. Влияние диффузионной металлизации в среде легкоплавких растворов на коррозионное растрескивание конструкционных сталей // Вопросы материаловедения.- 2007. № 3.1. С.286−292.
- Гафаров Н.А., Гончаров А. А., Кушнаренко В. М. Коррозия и защита оборудования сероводородсодержащих нефтегазовых месторождений. Под ред. В. М. Кушнаренко. М.: ОАО «Издательство «Недра», 1998. -437 с.
- NACE MR0175−97. Material requirements. Sulfide stress cracking resistance metallic materials for oil field equipment. 1997. 47 p.
- Biefer G.I. The stepwise cracking of pipe line steel in sour environments / Materials performance, 1982. — June. — P. 19−34.
- Иино И. Водородное вспучивание и растрескивание. Перевод ВЦП N В-27 457, Босеку гидзюцу. Т. 27. — № 8, 1978. — С. 312−424.
- Townsend Н. Hydrogen sulfide stress corrosion cracking of high stranght steel wire / Corrosion, 1972. V.28. — № 2. — P. 39−46.
- Яковлев А.И. Коррозионное воздействие сероводорода на металлы., М.: ВНИИЭгазпром, 1972. 42 с.
- Marvin C.W. Determining the strength of corroded pipe. / Materials protection and performance, 1972. V. 11. — P. 34−40.
- Дьяков В.Г., Шрейдер А. В. Защита от сероводородной коррозии оборудования нефтеперерабатывающей и нефтехимической промышленности. М.: ЦНЕВДТЭнефтехим, 1984. — 35 с.
- Шрейдер А.В., Шпарбер И. С., Арчаков Ю. И. Влияние водорода на нефтяное и химическое оборудование. М.: Машиностроение, 1979. -144 с.
- Terasaki F., Ikeda A., Tekejama М., Okamoto S. The hydrogen indu-ced cracking susceptibilities of various kinds of commerc. Rolled steels under wethydrogen sulfide / Environment. The sumitomo search, 1978. № 19. — P. 103— 111.
- Дубовой В.Я., Романов B.A. Влияние водорода на механические свойства стали / Сталь, 1974. Т.7. — № 8. — С. 727−732.
- Андрейкин А.Е., Панасюк В. В. Механика водородного охрупчивания металлов и расчет элементов конструкций на прочность / АН УССР. Физ. -мех. инс-т. Львов, 1987. — 50 с.
- Швед М.М. Изменение эксплуатационных свойств железа и стали под влиянием водорода. Киев: Наукова думка, 1985. — 120 с.
- Smialawski М. Hydrogening steel. Pergam press. 1962. 152 p.
- Карпенко Г. В., Крипякевич Р. И. Влияние водорода на свойства стали. — М.: Металлургиздат. 1962.-198с.
- Петров Н.А. Предупреждение образования трещин подземных трубопроводов при катодной поляризации. М.: ВНИИОЭНГ, 1974. — 131 с.
- Захаров Ю.В. Влияние напряжений на пластичность стали в растворе сероводорода. / Коррозия и защита в нефтегазовой промышленности. -№ 10. 1975. — С. 18−20.
- Мирочник В.А., Окенко А. П., Саррак В. И. Зарождение трещины разрушения в феррито-перлитных сталях в присутствии водорода / ФХММ.- 1984.-№−3,-С. 14−20.
- Саррак В.И. Водородная хрупкость и структурное состояние стали / МиТОМ. 1982. — № 5. — С. 11−17.
- Лившиц Л.С., Бахрах Л. П., Стромова Р. П. и др. Сульфидное растрескивание низкоуглеродистых легированных сталей // Коррозия и защита трубопроводов, скважин, газопромыслового ч газоперерабатывающего оборудования, 1977. № 5. — С. 23−30.
- Саркисов Н.М., Шишов С. В. Совершенствование технологии щелевой перфорации. Нефтяное хозяйство, № 3, 1995.
- К.Ю. Богачев. Методы приближения функций. М.: МГУ, 1998. — 129с.
- Б. Страструп. Язык программирования С++. Специальное издание / Пер. с англ. М.: ООО «Бином-Пресс», 2006. — 1104 е.: ил.
- Свидетельство об официальной регистрации программы для ЭВМ № 2 007 613 513 от 20.08.07. Программа прогнозирования содержания карбида титана в диффузионных титановых покрытиях / А. Г. Соколов, В. П. Артемьев, Д. А. Соколов.
- Свидетельство об официальной регистрации программы для ЭВМ № 2 007 613 572 от 22.08.07Программа прогнозирования толщины никель-медных покрытий в зависимости от режимов диффузионной металлизации / А. Г. Соколов, В. П. Артемьев, Д. А. Соколов.
- Свидетельство об официальной регистрации программы для ЭВМ № 2 007 613 656 от 27.07.07. Программа прогнозирования состава никель-медных покрытий в зависимости от режимов диффузионной металлизации / А. Г. Соколов, В. П. Артемьев, Д.А. Соколов
- Свидетельство об официальной регистрации программы для ЭВМ № 2 007 613 512 от 20.08.07. Программа прогнозирования состава никель-хромовых покрытий в зависимости от режимов диффузионной металлизации / А. Г. Соколов, В. П. Артемьев, Д.А. Соколов