Оптимизация состава, дисперсности и химических свойств поверхности компонентов рецептур анодной массы
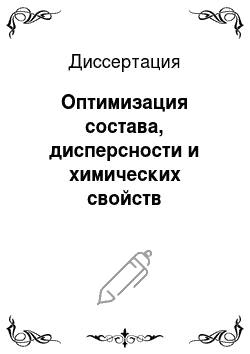
Диссертация
Основной целью работы является оптимизация физико-химических свойств компонентов анодной массы для технологии самообжигающегося анода с верхним токоподводом, используемой Братским алюминиевым заводом (БраЗ). Это позволит снизить расход пека на производство анодной массы и повысить ее качество. При этом снижение содержания пека, а значит и летучих веществ в массе, должно обеспечить также… Читать ещё >
Список литературы
- Фиалков А. С. Формирование структуры и свойств углеграфитовых материалов.-М.: Металлургия, 1965.-286 с.
- Ребиндер П. А. Адсорбционные слои и их влияние на свойства дисперсных систем. // Известия АН СССР, ОМЕН, Серия химическая, -1936, -№ 5, -с. 639−706.
- Емельянов А. Н., Сюняев 3. И., Долматов JI. В. Аналитический метод определения расхода связующего для приготовления анодной мас-сы./ЯДветные металлы, -1970, -№ 10, -с. 42−45.
- Mallison H. Zur Frage der Verteilung des Pechs im Stcin-kohlenbrikett.//Brennstotf-Chemie, -1958, Bd 39, -№ ½, -S. 13—14.
- О формировании пластических свойств анодной массы/ Янко Э. А., Лазарев В. Д., Анохин Ю. М, Потапова В. И.//Цветные металлы, -1972, -№ 10, -с. 33−36.
- Бикерман Я. О. Новые представления о прочности адгезионных свя-зей.//Успехи химии, -1972, т. 41, 8, с. 1431—1464.
- Lewis J. В. Thermal gas reaction.// Modem aspects of graphite technology. London: Academic Press, -1970.-pp. 346−354.
- Липатов Ю. С. Физико-химия наполненных полимеров. -Киев: Нау-кова думка, 1967, -322 с.
- Greenhaigh Е. and Moyse M. Е. Contact angle of pitch or carbon surfaces.// Third conference industrial carbon and graphite. London: Society Chemical Industry, -1970,-p. 539—549.
- Mason C. R. Correlation between pitch binder properties and properties of Soderberg electrodes. // Fuel, -1970, vol. 49, -№ 2, -p. 165−174.
- Емельянов A. H. Исследование влияния технологических параметров на качество облагороженных нефтяных коксов и расход связующего приизготовлении из них анодной массы: Дис.канд. техн. наук. -Уфа:. Уфимский нефт. институт, 1969.- 185 с.
- Сюняев 3. И. Облагораживание и применение нефтяного кокса. -М.: Химия, 1966.-134 с.
- Jakob R. R. Соке quality and how to make it.//Hydrocarbon Process., -1971, vol. 50, -№ 9, -p. 132—136.
- Brooks J., Taylor G. The formation of graphitizing carbons from the liquid phase.// Carbon, -1965, vol. 3, -№ 2, -p. 185—193.
- Степаненко M. А., Брон Я. А., Кулаков Н. К. Производство пеково-го кокса. -Харьков: Металлургиздат, 1961.-239 с.
- Фиалков А. С. Технология и оборудование электроугольного производства. М.—Л.: Госэнергоиздат, 1958.-187 с.
- Nellensteyn F. J., Kuipers J. Р. Die Mikronenzatil. //Teer und Bitumen, -1933, Bd 31,-№ 26, -S. 309 -312.
- Schafer H. G. Einige physikalische und technische Eigen-schaften von Steinkohlenteerpech in ihrer Abhangigkeit von der chemischen Zusammensetzung. // Erdol und Kohle—Erdgas Petrochemie, -1967, — № 6, -S. 416−419.
- Hugel G. Untersuchungen an Sleinkohlenteerpech.//Brenn-stoff-Chemie, -1958, Bd 39, -№ 13/14, -S. 213—217.
- Thomas В. E. High resolution triples tar mass spectra peaks. // Chemical Engineering, -1967, -№ 9, -p. 37.
- Малинский Ю.М. О влиянии твердой поверхности на процессы релаксации и структурообразования в пристенных слоях полимеров.//Успехи химии, -1970. т.29 -№ 8, -с. 1511−1535.
- Фиалков A.C., Галеев Г. С., Тян JI.C. Электронный парамагнитный резонанс в каменноуголном пеке.//Химия твердого топлива, -1967, -№ 2. -с. 108−110.
- Thomas В. Е. Electrode pitch. // The Gas World-Coking, -1960, -2, April, -p. 51—66.
- Puri B.R. Surface complexes of carbon.// Chemistry and physics of carbon. New York: M. Dekker Inc., -1970, vol. 6, -pp. 191−282.
- Лазарев В.Д., Тюменцев B.M., Богатырев B.P. Роль пеков-связующих в формировании пластических свойств анодной массы./ЯДветные металлы, № 3, 1999-С.44−48.
- Коробов М.А., Дмитриев А. А. Самообжигающиеся аноды алюминиевых электролизеров М.: Металлургия, 1972, 205 с.
- Джонсон Д.А. Обзор результатов внедрения технологии сухой анодной массы Кайзер // Технико-экономический вестник, КрАЗ Кайзер -ВАМИ, Красноярск, 1997, с. 12−18.
- Ахметов М.М., Тюменцев В. М., Богатырев В. Р., Борзилова В. В., Карпинская H.H. Пути снижения расхода кокса в производстве алюминия// Химия и технология топлива и масел, № 4 1999- с. 10−11.
- Привалов В.В., Степаненко М. А. Каменноугольный пек. М.: Металлургия. 1981. — 208 с.
- Чалик С.М., Ласукова Л. П., Свердлин В. А. // Цветные металлы. 1974. № 1. с. 45−50.
- Янко Э.А., Лазарев В. Д., Воропаев В. Н., Тугарин C.B. // Цветныеметаллы. 1976. № 6. с.48−51.
- Крысин В.П. Исследование по модификации свойств пека с температурой размягчения 110−120°С и разработка конструкции аппарата для охлаждения и грануляции высокотемпературного пека. Отчет НИР по договору № 64, Свердловск, УХИН, 1989 Г.-186 с.
- Янко Э.А., Лазарев В. Д., Воронков М. Г., Дерягина E.H. Исследование влияния добавок в анодную массу на ее физико-химические свойства//Цветные металлы. 1975. № 10. с. 38−42.
- Янко Э.А., Лазарев В. Д., Потапова В. И., Анохин Ю. М. // Кокс ихимия. 1973, № 6. с. 32−36.
- Красюков А.Ф. Нефтяной кокс М.: Химия, 1966. -274 с.
- Лазарев В.Д., Янко Э. А., Маркелова Л. И., Сенюта С. А., Ахметов М. М. О формировании физико-химических свойств пеко-коксовых композиций //Цветные металлы. 1979, № 5 с. 46−50.
- Янко Э.А., Лазарев В. Д., Анохин Ю. М., Потапова В. И. О формировании пластических свойств анодной массы// Цветные металлы. 1972, № 10. с. 33−36.
- Усовершенствование производства электродной продукции для алюминиевой промышленности. Отчет о НИР ВАМИ- Руковод. Ведерников Г. Ф., Копельман М.И.- № 5−65−070,-Л, 1969.-142 с.
- Капелянов В.Н. // Цветные металлы. -1990, -№ 7, -с. 75.
- Балыкин В.П. и др. // Химия твердого топлива, -1983. -№ 6 -с. 118 123.
- Маркина Н.Б., Балыкин В. П. // Цветные металлы. -1991, -№ 4, -с.29.31.
- Сюняев З.И. Нефтяной углерод. М.: Химия, 1980 г. — 272 с.
- Лазарев В.Д., Янко Э. А. Исследование некоторых физико-химических процессов в пеко-коксовых композициях // Химия твердого топлива. 1976.-№ I.e. 77−80.
- Фиалков A.C. Углеводородистые материалы. М., Энергия, 1989,320 с.
- Долматов A.B. Способы повышения плотности электродных пеков // Цветные металлы. 1991. — № 3. — с. 42−44.
- Янко Э.А., Лазарев В. Д. и др. О формировании пластических свойств анодной массы // Цветные металлы. 1972. — № 10.-е. 33−36.
- Балыкин В.П. и др. // Химия твердого топлива. 1993. — № 6. — с. 113−123.
- Маркина Н.В., Балыкин В. П. // Цветные металлы. 1991. — № 4. — с.29.31.
- Санников А.К., Балыкин В. П. и др. Исследование модифицирования поверхности углеродистого наполнителя в процессе его тонкого измельчения. Сб. научных трудов. — Производство электродной продукции. НИИГрафит. -М., 1984.325 с.
- Лазарев В.Д., Чалых В. И., Тюменцев В. М., Богатырев В. Р. Влияние источника кокса на формирование и стабильность свойств анодной мас-сы.//Цветные металлы, № 12, 1999-C.25−30.
- Колодин Э.П., Вишнев В. Г., Никитин В. Я. Взаимосвязь коксового сырья и эксплуатационных свойств анодной массы и обожженных анодов.// Труды ВАМИ, Л., 1984 Г.-388 с.
- Колодин Э.П., Никитин В. Я. //Цветные металлы, 1982 г., № 8, с. 44.45.171
- Лазарев В.Д., Янко Э. А. и др.// Цветные металлы, 1982 г., № 1, с. 49.52.
- Лазарев В.Д., Полевой Б. Н. //Цветные металлы, 1993, № 6, с. 59−61.
- Билицкус Д.Л. //Цветные металлы. 1995, № 9, с. 42−45.
- Патент РФ 2 064 483 МКИ 6 С 10 В 39/10. Барабанный холодильник для охлаждения кокса / Ахметов М. М., Юсупов Э. А., Тюменцев В.М.-№ 93 052 988/26- заявлено 23.11.93- опубл. Б.И.№ 21,1998.-c.194.
- Патент РФ 2 080 418 С1 МКИ С 25 С 3/12 Способ производства анодной массы алюминиевых электролизеров / Лазарев В. Д., Махалова Н. П., Тюменцев В.М.-№ 93 025 933/02- заявлено 30.04.93- опубл. Б.И. № 15, 1997.-е. 131.
- Патент РФ 2 128 246 С1 МКИ 6 С 25 С 3/12 Способ подготовки коксов разных поставщиков перед прокалкой для производства анодной массы / Лазарев В. Д., Баранцев А. Г., Тюменцев В.М.-№ 97 120 677/02- заявлено 02.12.97- опубл. Б.И. № 9,1999.-е. 359.
- Лазарев В.Д., Маркелова Л. И., Бессонов Г. Л., Тюменцев В. М. Пути улучшения качества анодной массы, изготовленной на основе нестандартных каменноугольных пеков // Цветные металлы № 6,1996-е. 27−32.