Повышение долговечности стальных цилиндров электромеханической обработкой
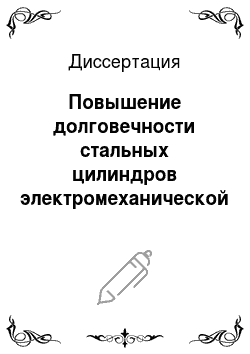
Диссертация
Точность обработки деталей при ЭМО определяется точностью, достигнутой на предварительной операции, и находится в пределах 7−8 квалитета. Изменения формы и размеров детали не превышают величины исходной шероховатости поверхности. Развальцовка торцов при ЭМО по сравнению с поверхностным пластическим деформированием в 4−5 раз меньше, а длина развальцованной части торца в два раза короче. Исходная… Читать ещё >
Список литературы
- Азаревич Г. М. Упрочняющая обработка деталей сельхозмашин. М., ЩИИТЭИ Тракторсельхозмаш, 1971, 158 с.
- Александров Ю.Д. Влияние некоторых параметров на чистоту поверхности при электромеханическом сглаживании. Сб. «Исследование и применение процессов электромеханической обработки металлов». Ульяновск, 1970, 35−41 с.
- Алексеев П.Г. Машинам быть долговечными. Тула, Приоское из-во, 1973, 136 с.
- Аскинази Б.М. Упрочнение и восстановление деталей электромеханической обработкой. Л., Машиностроение, 1979, 296 с.
- Аскинази Б.М. Упрочняемость деталей машин электромеханической обработкой. «Вестник машиностроения», 1981, № I, 19−21 с.
- Аскинази Б.М., Веретенников Н. В. Чистовая электромеханическая обработка чугунных цилиндров. Сб. «Исследование и применение процессов электромеханической обработки металлов», Ульяновск, 1970, 128−137 с.
- Аскинази Б.М. Чистовая электромеханическая обработка деталей машин. «Машиностроитель», 1971, № 9, 17 с.
- Аскинази Б.М., Веретенников Н. В. Упрочнение цилиндров двигателей внутреннего сгорания электромеханическим методом. Сб. «Исследование и применение процессов электромеханической обработки металлов». Ульяновск, 1970, 137 150 с.
- Аскинази Б. М, Технологические возможности и эффективность электромеханической обработки металлов (ЭМО), Сб. «Исследование электромеханической обработки металлов и ее применение в сельскохозяйственном ремонтном производстве». Ульяновск, 1981, 5−16 с.
- Атрощенко А.П., Богоявленский К, Н. Термомеханическая обработкакак эффективный способ повышения механических свойств сталей. Сб. «Повышение эффективности технологических процессов и качества продукции машиностроения. Л., 1981, 83−86 с.
- Бащенко А.П., Изотов В. М. Влияние формоизменения зерна при ВТМО на прочность стади. „МиТМО“, 1981, № 9, 12−14 с.
- Бернштейн М.Л. Термомеханическая обработка металлов и сплавов. М., Металлургия, 1968, 1172 с.
- Бернштейн М.Л. и др. Влияние деформации аустенита при ВТМО на стабильность высокоуглеродистого мартенсита при низком отпуске. „МиТОМ“, 1977, 22−24 с.
- Бернштейн М.Л. Структура и механические свойства металлов. М., Металлургия, 1970, 472 с.
- Бетанелли А.И. Твердость стальных и твердых сплавов при повышенных температурах. М., Машиностроение, 1973, 92 с.
- Бетанелли А.И., Нанашидзе В. Г. Основы классификации методов обработки поверхностным пластическим деформированием. Сб. „Резание и инструмент“, Харьков, 1981, № 26, 149−152 с.
- Биргер И.А. Определение остаточных напряжений. М., Машиностроение, 1973, 283 с.
- Блох Л.С. Практическая номография. М., Высшая школа, 1971, 328 с.
- Блантер М.Е. Мартенситные превращения и механическое состояние фаз. „МиТМО“, 1975, № 5, 7−10 с.
- Бобылев А.В. Механические и технологические свойства металлов. М., Металлургия, 1980, 296 с.
- Боршукова С.Н. Касательные нагружения боковой поверхности цилиндра и цилиндрической полости. М., В.Ц. АН СССР, 1972, 58 с.
- Бражюнас А.Ф. Исследование износостойкости сталей, упрочненных электромеханическим методом. Сб. Исследование и применение процессов электромеханической обработки металлов. Ульяновск, 1970, 63−72 с.
- Бражюнас А.Ф. Тепловое состояние инструмента при электромеханической обработке. „Вестник машиностроения“, 1972, № 12, 56−57 с.
- Браславский В.М. Расчет глубины наклепа с учетом формы пластически деформированной поверхности. „Вестник машиностроения“, 1977, № 4, 62−63 с.
- Бурдин В.В. и др. Влияние электромеханического способа упрочнения (ЭМО) на износостойкость стали 45. Сб. „Прогрессивные технологические методы повышения надежности и долговечности деталей машин и инструмента“, Куйбышев, 1980, 78−82 с.
- Гетия И.Г. Математическая обработка результатов энергосиловых параметров процессов винтовой прокатки. Сб. „Обработка металлов давлением“, М., ВЗМИ, 1979, 40−53 с.
- Гинье А. Рентгенография кристаллов. М., Физмат, 1971, 604 с.
- Глазов В.М., Вигдорович В. Н. Микротвердость металлов. М., Металлургия, 1972, 224 с.
- Глазунов Е.И. Установка для обкатывания цилиндрических поверхностей с электроподогревом. Сб. Вопросы прочности и пластичности металлов. Минск, „Наука и техника“, 1972, 94−96 с.
- Гласс Дж., Стэнли Дж. Статистические методы в педагогике и психологии. М., „Прогресс“, 1976, 495 с.
- Головин Г. Ф. Поверхностная закалка как средство повышения долговечности деталей машин. Сб. „Труды Всесоюзного науно-иссле-довательского института токов высокой частоты“, 1973, вып.13, 30−39 с.
- Гончаренко Т.И. и др. Структура и свойства поверхностного слоя стали У8 после электромеханической обработки. Сб. „Вопросы металловедения и физики металлов“, Тула, 1977, 99−104 с.
- Горбунов Б.И. Обработка металлов резанием, металлорежущий инструмент и станки. М., Машиностроение, 1981, 287 с.
- Горелик С.С. Рентгенографический и электродамштический анализ. М., Металлургия, 1970, 107 с.
- Гуляев А.П., Гузовская М. А. Мартенситные превращения в железе. „МиТОМ“, 1977, № 6, 2−4 с.
- Гурьев А.В.и др. К вопросу о формировании поверхностного слоя в процессе электромеханической обработки. Сб."Научные труды Волгоградского политехнического института, 1979, № 9, 23−28 с.
- Дашевский Б.Д. Опыт Рязанского завода тяжелого кузнечно-прес-сового оборудования по применению электромеханической обработки. Сб. „Исследование и применение процессов электромеханической обработки металлов“. Ульяновск, 1970, 184−189 с.
- Джанилидзе ШЛИ. Применение электромеханического метода при восстановлении автомобильных поворотных цапф. Труды УСХИ, том 17, вып. I, 1970, 184−189 с.
- Демкин Н.Б., Рыжев Э. В. Качество поверхности и контакт деталей машин. М., Машиностроение, 1981″ 244 с.
- Дроздов В.М., Казанцев А. С. Оценка механических методов определения остаточных напряжений. Сб. „Новые методы испытания и обработки металлов“, Минск, „Наука и техника“, 1975, 23−29 с.
- Дривотин И.Г. Применение поляризационно-оптического метода при исследовании процесса поверхностного деформирования. Сб. „Новые методы испытания и обработки металлов“. Минск, „Наука и техника“, 1975, II8-I2I с.
- Дуденков В.Г., Аверченков В. И. Упрочнение легированных сталей электромеханическим методом. Сб. „Технология машиностроения“. Брянск- 1973, 100−104 с.
- Евсютин М.Н. и др. Способ выявления пятна контакта алмазного инструмента с обрабатываемой деталью. Авт. свид. СССР, кл.01, 3/58 № 564 576.
- Емельянов В.Н. и др. Исследование процесса раскатывания с использованием эксперимента. „Вестник машиностроения“, 1978,2, 73−74 с.
- Илюшин Л.М. и др. Упруго-пластическая деформация полых цилиндров. М., МГУ, 1970, 138 с.
- Калачев М.И. Деформационное упрочнение металлов. Минск, „Наука и техника“, 1980, 256 с.
- Карпенко Н.В. и др. Применение токарной обработки для поверхностной ТМО. Сб. „Прочность металла при циклических нагрузках“. М., „Наука“, 1977, 18−21 с.
- Карпенко Н.В. и др. Коррозионно-усталостная прочность стальных труб после электромеханического упрочнения. Сб."Повышение качества, надежности и долговечности деталей машин технологическими методами». Пермь, ППИ, 1971, 10—II с.
- Кацев П.Г. Статистические методы исследования режущего инструмент. М., Машиностроение, 1976, 226 с.
- Кидин И.Н. Исследование механизма упрочнения проволоки при электротермо механической обработке. «Черная металлургия», 1971, № 3, 129−132 с.
- Кириленко Г. Б. К вопросу упрочнения поверхностного слоя электромеханической обработкой. Винница, ВПИ, 1980, 9 с. (депонирована 'в Укр НИИНТИ, 2207).
- Крагельский и др. Основы расчетов на трение-И износ. М., Машиностроение, 1977, 286 с.
- Красноярский В.В. и др. Коррозия и защита металлов. М., Металлургия, 1979, 302 с.
- Котин Б.Л. Опыт работы по электромеханической обработке ремонта о-механическ ого цеха № I, Череповецкого ордена Ленина металлургического завода. Труды УСХИ, 1970, № 17, вып.1, 189−195 с.
- Кудрявцев И.В., Кудрявцев П. И. Поверхностный наклеп как средство повышения сопротивления малоцикловой усталости деталей машин. «Проблемы прочности», 1972, № 4, 22−24 с.
- Кудрявцев И.В. Современное состояние изучения и практического применения поверхностного пластического деформирования. Сб. «Повышение качества, надежности и долговечности деталей машин технологическими методами», Пермь, 1977, 5−7 с.
- Кудрявцев И.В. Упрочнение деталей поверхностным пластическим деформированием. «Вестник машиностроения», 1977, № 3, 32−34 с.
- Кальнер В.Д. и др. Применение сканирующей и просвечивающей электронной микроскопии для фрактографического анализа изломов стали. «МиТОМ», 1974, № 8, 32−33 с.
- Лазаренко В.К., Прейс Г. А. Износостойкость металлов. Киев, Машиностроение, 1970, 218 с.
- Левицкий И.С. Организация ремонта и проектирования сельскохозяйственных ремонтных предприятий. М., «Колос», 1977, 240 с.
- Лившиц Л.Г., Полянченко А. В. Восстановление автотракторных деталей. М., «Колос», 1976, 480 с.
- Линчин Н.Н. Фазовые и структурные превращения при нагреве металлов и сплавов. «МиТОМ», 1974, № 8, 26−27 с.
- Лисичкин В.А. Теория и практика прогностики. М., «Физмат», 1972, 283 с.
- Лоладзе А.В. Особенности процесса резания металлов. М., Машиностроение, 1973, 348 с.
- Лукьянов В.Ф. и др. Влияние давления коррозионной среды на развитие разрушения при малоцикловом нагружении. «Изв. Высш. школы. Машиностроение», 1978, № 8 50−51 с.
- Мелков М.Г. Твердое осталивание автотракторных деталей. М., Транспорт, 1971, 212 с.
- Мильман В.М., Танатаров Р. А. Исследование влияния электромеханического метода упрочнения на долговечность. Ульяновск, Труды УСХИ, 1970, том 17, вып.1, 176−184 с.
- Михайлов А.А. Обработка деталей с гальваническими покрытиями, М., Машиностроение, 1981, 144 с.
- Михайлов А.А., Сафронов В. В. Инструмент для электромеханической обработки. Сб. «Прогрессивные методы обработки зубчатых колес», Орел, Приокс. из-во, 1982, 73−78 с.
- Монченко В.П. Эффективная технология производства полых цилиндров. М., Машиностроение, 1980, 248 с.
- Надольский В.О., Шиленков В. Ф. Экспериментальное исследование теплового поля в поверхностном слое при электромеханической обработке. Ульяновск, «Труды УСХИ», 1970, том 17, вып.1, 52−63 с.
- Папшев Д.Д. Упрочнение деталей обкаткой. М., Машиностроение, 1978, 224 с.
- Паустовский А.В. Износ электрод-инструментов при электромеханической обработке. «Порошковая металлургия», 1970, № 4, 61−66 с.
- Проскуряков Ю.Г., Валяев Ф. Ф. Условия контактного взаимодействия при поверхностном пластическом деформировании деталей типа втулок. Сб. «Микрогеометрия и эксплуатационные свойства машин», — 165 -Рига, 1980, вып.8, 3−12 с.
- Проскуряков Ю.Г. Новая технология обработки втулок совместным дорнованием и редуцированием. «Вестник машиностроения», 1977, № 3, 35−36 с.
- Проскуряков Ю.Г. Технология упрочняюще колибрующей и формообразующей обработки металлов. М., Машиностроение, 1971, 208 с.
- Пятосин Е.И. Исследование контактных условий и расчета напряжений и усилий деформирования при упрочняющей обработке методом обкатывания роликовым инструментом. Сб. «Новые методы исследования и обработки», Минск, «Наука и техника», 1975, 68−85 с.
- Пятосин Е^И., Глазунов Е. И. Основные температурные зависимости при поверхностном пластическом деформировании с электроподогревом. Сб. «Новые методы испытания и обработки металлов». Минс^,"Наука и техника", 1975, 87−98 с.
- Репина Л.Д. Исследование тонкой структуры упрочненных деталей. Сб. «Научные труды Кузбасского политехнического института». 1972, № 49, 1−7 с.
- Розенфельд И.Л., Персианцева В. П. Механизм защиты металловот коррозии. Сб. «Коррозия металлов и сплавов». М., Металлургия, 1972. 305−315 с.
- Румшинский Л.З. Математическая обработка результатов эксперимента. М., «Наука», 1971, 192 с.
- Русов К.Д. и др. Установка для поверхностной термомеханической обработки. «Вестник машиностроения», 1976, № 3, 83 с.
- Рыжов Э.В. и др. Контактная жесткость плоских стыков после электромеханической обработки. Сб. «Технология машиностроения». Брянск, 1973, 77−82 с.
- Рыкалин Н"Н. Тепловые явления при сварке. М., Энергия, 1970, 286 с.
- Рыкалин Н.Н. и др. Тепловые процессы при лазерной обработке. М., Энергия, 1977, 386 с.
- Сафронов В.В. Электромеханическая обработка внутренних поверхностей стальных цилиндров. Сб. «Исследование и применение процессов электромеханической обработки металлов». Ульяновск, 1970, I50−161 с.
- Севернев М.М. и др. Износ деталей сельскохозяйственных машин. Л., Колос, 1972, 288 с.
- Серегин С. А. Епифанцев Ю.А. Повышение износостойкости металлов высокоскоростным трением. «МиТОМ», № II, 1974, 62−63 с.
- Страшков А, Н. Обработка резанием труднообрабатываемых материалов с нагревом. М., Машиностроение, 1977, 142 с.
- Торбило В.М. Алмазное выглаживание. М., Машиностроение, 1972, 104 с.
- Терешко А, А. Экспериментальные исследования распределения температур в рабочем валке при холодной прокатке. «Черная металлургия», 1971, № 3, 98−102 с.
- Тимошенко С.П., Войновский-Кригер С. Пластинки и оболочки. М., Физмат, 1973, 635 с.
- Тимошенко Б.И. Упрочнение деталей электрокомбинированным методом. «Электронная обработка материалов», 1977, № 4, 82−84 с.
- Томашов Н.Д. Электрохимическое исследование атмосферной коррозии металлов. Сб. «Коррозия и защита стадей». М., Машиностроение, 1979, I58−171 с.
- Томашов И.Д. Теория коррозии и пути повышения коррозионнойустойчивости металлических сплавов. Сб. «Коррозия и защита сталей». М., Машиностроение, 1978, 5−29 с.
- Утевский Л.М. Дифракционная электронная микроскопия в металловедении. М., Металлургия, 1973, 583 с.
- Фарбер В.М. Методы исследования тонкой структуры сплавов. «МиТОМ», 1974, № 12, 56−62 с.
- Хейденрайх Р. Основы просвечивающей электронной микроскопии. М., «Мир», 1978, 265 с.
- Хрущев М.М., Бабичев М. А. Абразивное изнашивание. М., «Наука», 1970, 252 с.
- Цап М. В. Повышение качества поверхности и долговечности направляющих станков электромеханической обработкой. Сб. «Технология заготовительного и механосборочного производства». Краматорск, 1980, 93−99 с.
- Шнейдер Ю.Г. Инструмент для чистовой обработки металлов давлением. Л., Машиностроение, 1971, 284 с.
- Щур Е.А. и др. Высокотемпературная термомеханическая обработка легированной конструкционной стали. Сб. «Надежность и долговечность металлов и материалов для машиностроения и приборостроения». Л., 1972, 5−12 с.
- Щур Е.А., Зонов П. Н. Прокаливаемость при термомеханической обработке стали. «МиТОМ», 1974, № 2, 32−34 с.
- Черниговцев Н.Н. Исследование восстановления деталей неподвижных сопряжений электромеханическим методом. М., Труды1. ВСХИЗО, 1974, 31−36 с.
- Эндрюс К. и pp. Электронограммы и их интерпретация. М., «Мир», 1971, 252 с.
- Ярославцев В.М., Евченко Н. Л. Применение метода источников тепла для расчета температурных полей с учетом теплообмена. «Известия выс.учеб.завед. Машиностроение», 1979, 104−106 с.
- Яковлев Б, Я. Коррозия деталей машин под действием туков. «Техника в сельском хозяйстве», 1970, № 3, 21−24 с.
- Azrin М., Olson B., Cula Е., Marley j.
- Soviet Progress in thermomechanical treatment of metals «J Appl. Metal-work», 1980, I, 2, 3−34 p.
- J.Hich 6-th ASM Heat Treating Conference / Workshop/. «Heat Treating Metals», 1982, 9, I, I-I6 p.
- Tybielewier Krzysztof Nicktore vlasci worci warstwy wicrrohnies powstalis po nagniatanin eleetromeehanicrnym. «Zesz nouk Pezest. Nouki Techn, 1981, 16, 135−147 c.