Структурный синтез поточных линий для обработки древесного сырья
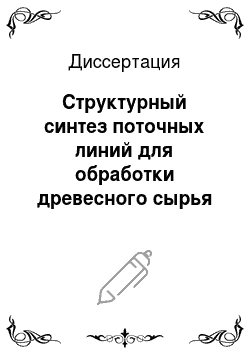
Подводя итоги обзора литературных источников по моделированию технологических процессов нижних складов и раскряжевочных линий можно сделать следующие выводы: — при моделировании процессов нижнескладских работ в обязательном порядке учитываются размерно-качественные характеристики предмета труда— при исследовании раскряжевочных участков в основном охватываются узконаправленные аспекты проблемы… Читать ещё >
Структурный синтез поточных линий для обработки древесного сырья (реферат, курсовая, диплом, контрольная)
Содержание
- 1. Состояние вопроса и постановка задачи
- 1. 1. Предпосылки для совершенствования ресурсосберегающих технологий первичной обработки древесного сырья
- 1. ^.Характеристики предмета труда и факторы, влияющие на размерно -качественные параметры продукта труда первичной обработки
- 1. 3. Предметная область проведения исследований
- 1. 4. Влияние переместительных операций на качество и выход деловой древесины
- 1. 5. Обзор теоретических и экспериментальных исследований технических средств для реализации первичной обработки древесного сырья
- 1. 5. 1. Исследования по моделированию размерно — качественных характеристик объекта труда первичной обработки
- 1. 5. 2. Исследования по моделированию технологического процесса первичной обработки древесного сырья
- 1. 5. 3. Обзор исследований взаимодействия предмета труда первичной обработки древесного сырья с рабочим оборудованием
- 1. 5. 4. Влияние упругости хлыстов на свойства системы «хлысты — рабочее оборудование»
- 1. 6. Выводы по главе
- 1. 7. Цель и задачи исследований
- 2. Моделирование хлыстов как динамической подсистемы с распределенными параметрами
- 2. 1. Особенности взаимодействия предмета труда первичной обработки древесины с технологическим оборудованием
- 2. 2. Определение упругих характеристик хлыстов применительно к технологическим операциям первичной обработки древесного сырья
- 2. 3. Теоретическое обоснование динамических эквивалентных расчетных схем хлыстов применительно к технологическому процессу первичной обработки древесного сырья
- 3. Взаимодействие хлыстов с рабочим оборудованием для первичной обработки древесного сырья
- 3. 1. Продольное перемещение хлыстов: комлевая консоль переменной длины
- 3. 1. 1. Расчетные схемы взаимодействия гусеничного протаскивающего устройства (ГПУ) с хлыстами
- 3. 1. 2. Определение амплитуды и частоты возмущения системы
- 3. 1. Продольное перемещение хлыстов: комлевая консоль переменной длины
- 3. 1. 3. Описание движения одной гусеницы ГПУ при помощи дифференциальных уравнений
- 3. 1. 4. Деформации ведущих валов привода при взаимодействии ствола дерева с верхней и нижней гусеницами
- 3. 1. 5. Амплитуды и период колебаний при биениях в системе
- 3. 2. Поперечное перемещение хлыстов: взаимодействие с раскряжевочными агрегатами поточных линий для первичной обработки древесины
- 4. 1. Задачи экспериментальных исследований
- 4. 2. Место, условия и подготовка к проведению экспериментальных исследований
- 4. 3. Аппаратура, приборы и тензометрическая оснастка
- 4. 4. Порядок проведения экспериментальных исследований
- 4. 5. Программа экспериментальных исследований
- 4. 6. Обработка результатов экспериментальных исследований
- 5. 1. Результаты экспериментальных исследований динамических характеристик хлыстов
- 5. 2. Результаты экспериментальных исследований гусеничного протаскивающего устройства линии ППЛ — 4 м
- 6. 1. Описание элементарных перемещений при выполнении технологических операций методом матричных преобразований координат
- 6. 2. 0. писание матричным методом перемещений манипуляторов
- 7. 1. Структурное представление поточных линий
- 7. 2. Обоснование определения скоростей перемещений предмета труда агрегатами поточных линий для первичной обработки древесного сырья
- 8. 1. Моделирование технологии первичной обработки древесного сырья на линиях циклического действия
- 8. 2. Моделирование технологического процесса первичной обработки древесного сырья поточных линий
- 8. 3. Графоаналитическое моделирование технологического процесса
- 8. 4. Анализ существующих поточных линий и оборудования для первичной обработки древесного сырья
- 8. 4. 1. Структурный анализ поточных линий и оборудования
- 8. 5. Результаты моделирования существующих поточных линий
Лесная промышленность играет значительную роль в экономике развитых стран. Ее доля в общем промышленном производстве развитых стран составляет около 9%, что ставит ее на уровень с такими крупными отраслями, как пищевая, легкая промышленность, металлургия. На древесное сырье приходится более 10% всех предметов труда, используемых в промышленности. Для сравнения, следует отметить, что на все виды минерального топлива приходится 40%, на сельскохозяйственную продукцию 25%, на рудное металлическое сырье 5%. Эффективность использования сырья повышается за счет постоянного увеличения выхода готовой продукции, вовлечения в переработку более широкого набора пород, изменения размеров и качества лесоматериалов, создания условий для утилизации.
Бурное развитие информационных технологий, автоматизации и компьютеризации смежных отраслей, обеспечивающие существенную модификацию исходного сырья в отраслях глубокой переработки древесины (целлюлозно-бумажная, фанерная, древесноплитная) неизменно накладывает отпечаток и на лесозаготовительную отрасль. Созданы теоретические основы для автоматизированного оптимального раскроя предмета труда (хлыстов) на стадии первичной переработки. Глубоко исследованы размерно-качественные характеристики и закономерности протекания технологических операций на нижних складах. До последнего времени парк и номенклатура технологических машин на лесозаготовках бурно расширялся, а сами машины постоянно совершенствовались в соответствии с прогрессом технологии, техники и организации труда. За последние годы накоплен богатый опыт по созданию автоматических и полуавтоматических линий для раскроя сырья, в деревообработке и в отраслях потребителях.
Вопросам моделирования предмета труда, моделирования технологических процессов, исследованию операций нижнескладских работ, исследаваниям взаимосвязей между отдельными технологическим участками нижних складов, процессов динамического взаимодействия предмета труда первичной обработки древесины с рабочим оборудованием, процессам автоматизированной оптимизации раскроя предмета труда, структурному синтезу автоматизированных технологических структур посвятили свои труды: И. В. Батин, С. П. Бойков, Д. К. Воевода, Ю. И. Верхов, Б. Г. Гастев, В. А. Дорошенко, JI.C. Ильницкий, Р. Н. Ковалев, J1.B. Коротяев, Д. Л. Дудюк, A.B. Жуков, Ф. Е. Захаренков, В. К. Захаров, Б. Г. Залегаллер, П. В. Ласточкин, B.C. Петровский, В. Ф. Полетайкин, А. К. Редькин, Г. А. Степаков, A.C. Торопов и многие другие. Трудом многих коллективов в стране была создана развитая сеть лесозаготовительных иперерабатывающих предприятий, которые заготавливали и перерабатывали огромное количество древесины. Изменившиеся взаимоотношения в экономике страны требуют пересмотра традиционных технологий для первичной обработки древесного сырья, основой которых являются системы машин 1НС и 2НС. Воспроизводство устаревшего оборудования с поперечной подачей индивидуального изготовления на сегодняшний день дорого, серийно выпускаемая линия ЛО-15С с продольной подачей также не устраивает ни мелкого, ни крупного производителя как по цене, так и по производительности. Большой разрыв в производительностях между линиями с продольной подачей и поперечным перемещением хлыстов является сдерживающим фактором при проектировании новых производств. Отсутствие унификации и агрегатно — блочного принципа компоновки технологических схем не позволяет создать унифицированные ряды оборудования для первичной обработки древесного сырья. Компоновка поточных линий отдельными агрегатами от разных поточных линий, прошедшими проверку в производственных условиях, ведет к нарушению программных связей (кинематической несогласованности) между агрегатами, что сказывается на ритмичности технологических потоков и ведет к снижению производительности. Проведение эффективных научных исследований по совершенствованию исполнительных технологий и оборудования не мыслимо без моделирования технологических процессов с использованием ЭВМ, которые позволяют решать многоуровневые и многокритериальные задачи с эффективным использованием имеющихся научных разработок по параметрам предмета труда (хлыстов), тем более, что стоимость таких исследований в 10 — 15 раз ниже стоимости натурных и статистических исследований. Совершенствование теоретической базы для моделирования, анализа, синтеза и использование ЭВМ — необходимое условие для реализации основных принципов ресурсосбережения и совершенствования исполнительных технологий и оборудования. С развитием автоматизации и компьютеризации на базе накопленного опыта проектирования и теоретических исследований необходимо создать теоретическую базу для синтеза технологий, обеспечивающих реализацию автоматизированных принципов раскроя сырья, на базе программного управления в функциях положения или времени. На сегодняшний день осуществить программное управление на устаревшем исполнительном оборудовании и станках не представляется возможным. Необходимо создание принципиально новых технологий с исполнительными механизмами наиболее пригодными для реализации прогрессивных принципов управления и программирования раскроя. Поскольку интенсификация режимов (т.е. сокращение циклов длительности операций) неизбежно влечет за собой увеличение скоростей, совмещение во времени пространственных перемещений и требуют обязательного приборного контроля.
Исполнительное оборудование на первичной обработке древесины активно взаимодействует с предметом труда (хлыстами, сортиментами). Предмет труда, в свою очередь, имеет размерно-качественные и динамические характеристики. Размерно-качественные характеристики учитываются при проектировании исполнительных технологий, а характер взаимодействия с оборудованием зависит от требуемых (заданных) размерно-качественных характеристик продукта труда (сортиментов). Динамические характеристики (масса, жесткость, частотные характеристики) учитываются практически на всех стадиях первичной обработки древесного сырья (валка, трелевка, обрезка сучьев, погрузка) и активно влияют на протекание технологического процесса при раскряжевке, а также влияют на нагруженность рабочего оборудования.
Переход от устаревших конструкций и исполнительных технологий к более прогрессивным затрудняется тем, что отсутствует, с точки зрения автоматизированной оптимизации раскроя лесоматериалов, формализованный анализ и синтез технологических структур для первичной обработки древесины с теоретическим обоснованием динамического и технологического взаимодействия предмета груда с исполнительным оборудованием в процессе перемещений.
В целом необходимо решить проблему, заключающаяся в разработке теоретической базы для анализа существующих и синтеза перспективных технологий, отвечающих принципам ресурсосбережения, однотипности оборудования и технологических потоков с расширенными функциональными возможностями, возможности агрегатно-блочного принципа развития технологических исполнительных схем.
Вышеуказанная направленность работы реализуется на базе системного подхода с решением частных вопросов при помощи методов интегрального и дифференциального исчисления с использованием основных понятий теоретической механики, теории колебаний, сопротивления материалов, статистической математики, математической логики и матричного метода преобразования координат.
В рамках научного направления — «Процессы, технология и оборудование по первичной обработке и переработке древесины» разрабатывалась госбюджетная тема — «Совершенствование поточных линий для первичной обработки хлыстов (деревьев) с поперечным перемещением» .
Представленные в диссертации теоретические разработки по моделированию хлыстов как подсистем динамических систем являются обобщающими для систем с произвольным и периодическим возмущением, в которых хлысты представлены как подсистемы с распределенными параметрамиРазработанный метод описания перемещений предмета труда в процессе выполнения технологических операций позволяет формализоватьпротекание технологического процесса в удобной форме, пригодной как для ручного, так и машинного расчета.
Предложенный впервые метод моделирования технологического процесса первичной обработки древесины на стадии раскроя на базе матричных преобразований координат позволяет представлять результаты в математической и графической формах.
Моделирование при помощи предложенных методов формализации технологического процесса первичной обработки древесины позволяет проводить структурный анализ, например, раскряжевочных потоков с декомпозицией систем на функциональные элементы по перемещениям. В работе проведен структурный анализ, введены понятия минимального уровня оснащенности технологического процесса, достигнутого и требуемого.
В работе впервые произведен формализованный синтез перспективных технологических структур для первичной обработки хлыстов с выходом на гамму конкретных технологических структур с расширенными функциональными возможностями по сравнению с существующими технологическими структурами.
Впервые предложен и реализован при помощи имитационного моделирования принцип сортировки и подсортировки продукта труда в процессе раскроя без использования специального сортировочного оборудования.
В работе разработан метод расстановки пильных агрегатов, обеспечивающий программную раскряжевку по картам раскроя.
Разработанный принцип совмещения переместительных операций при синтезе, позволяет использовать предложенные исполнительные технологии для автоматической оптимизации раскроя хлыстов с использованием теоретических разработок проф. B.C. Петровского, Г. А. Степакова и A.C. Торопова.
Разработанное обобщающее теоретическое обоснование построения эквивалентных расчетных динамических схем при взаимодействии предмета труда с рабочим оборудованием позволяет перейти от частных случаев определения жесткости и приведенных масс к единой методике, что позволяет базировать дальнейшие исследования на фундаментальных теоретических разработках в ведущих разделах науки.
Моделирование технологического процесса на основе теоретически обоснованных структурных формул и графоаналитического анализа позволяет исследовать технологическую структуру с любым количеством стохастических воздействий в кратчайшие сроки со снижением затрат в 15 -20 раз, поскольку обычно стохастические воздействия на технологические структуры исследовались на опытных образцах техники натурными измерениями со статистической обработкой.
Синтезированные технологические структуры в отличие от существующих отечественных структур на базе поперечного метода перемещений предмета труда наиболее приспособлены к использованию автоматической оптимизации раскроя хлыстов.
В процессе выполнения работы внедрено в производство изобретение по без зажимному пилению в процессе раскроя на слешерной линии СТИ-3 в Чернореченском ЛПХ. При проектировании сучкорезной машины с гусеничным протаскивающим устройством (ГПУ) в КФ ВНИИСДМ использованы рекомендации по уменьшению динамических нагрузок на ведущих валах, по синхронизации движения верхней и нижней гусениц и по конструктивному исполнению ГПУ с учетом настройки на более экономичный и менее нагруженный в динамическом отношении режим движения гусениц.
Разработанные автором теоретические основы моделирования предмета труда, рабочего оборудования, а также методы моделирования технологических операций и технологических структур используются в учебном процессе кафедры ТОЛЗ СибГТУ при дипломном проектировании. Апробация в учебном процессе в 1997, 1998, 1999 г. г. показала, что моделирование технологических процессов не ограничивается поточными линиями для первичной обработки хлыстов, то есть возможно более широкое применение, например, при моделировании технологического потока подачи сырья к высокопроизводительному фрезерно — пильному станку 11−200 на Красноярском лесоперевалочном комбинате.
Рекомендации по динамическим нагрузкам и расчетным динамическим схемам используются при проектировании челюстных погрузчиков на заводе «Краслесмаш» .
Результаты исследований доложены на ежегодных научнотехнических конференциях факультетов по итогам научноисследовательских работ за 1973 — 1979 гг. СибТИ, г. Красноярскна пятой научно — технической конференции аспирантов и молодых специалистов лесной промышленности за 1975 г., ЦНИИМЭ, г. Химкина краевой научно — технической конференции «Пути повышения выхода деловой древесины в лесной отрасли» 15 апреля 1988 г.- на ежегодных научно — технических конференциях 1976;1989 г. г. СТИ, КГТАна ежегодных научнопрактических конференциях «Проблемы химико — лесного комплекса» КГТА, СибГТУ 1989 — 1999 г. г.
Теоретические разработки, обработка результатов исследований, моделирование, обработка результатов моделирования выполнены автором единолично. Экспериментальные исследования проведены под личным руководством и личном участии автора.
1.СОСТОЯНИЕ ВОПРОСА И ПОСТАНОВКА ЗАДАЧИ1.1. Предпосылки для совершенствования ресурсосберегающих технологий первичной обработки древесного сырья.
Федеральная программа развития лесопромышленного комплекса Российской Федерации (1995;2005 гг.) предусматривает увеличение заготовок леса до 300 миллионов кубических метров, т. е. в 2.5 раза больше, чем фактически потребленных в 1994 году. Наряду с эксплуатацией лесных массивов в Европейской части, в программе планируется освоение богатейших высокопродуктивных хвойных лесов Восточной Сибири с реконструкцией и обновлением существующих целлюлозно-бумажных и химических производств. В программе развития лесопромышленного комплекса (ЛПК) Российской Федерации указывается на необходимость завершения нового строительства лесозаготовительных предприятий в нижнем приангарье суммарной мощностью 3−4 млн. м3 в год, лесопильных 0.6 млн. м3 в год.
В 1983;1992 г. г. в нашей стране на 1646 из 1750 нижних складов поступало сырье в виде хлыстов. 40 складов получали деревья, 24 склададеревья и хлысты, 3 склада полухлысты, 16 складов получали сортименты. То есть хлыстовая вывозка является традиционной [13]. Вид поступающего сырья на нижние склады или пункты глубокой переработки зависит от конкретных природно-производственных условий, однако он изменяется во времени в связи с общим развитием технологий. Это предусмотрено в Программе [1] развития ЛПК в виде альтернативной сортиментной технологии. На сегодняшний день очевидно, что традиционная хлыстовая технология будет совершенствоваться, а альтернативная — сортиментная, при благоприятных природно-производственных условиях и наличии необходимого комплекса лесосечных машин будет внедряться в производство.
Хлыстовая технология лесозаготовок предусматривает получение продукта труда первичной переработки древесного сырья в виде сортиментов на нижних складах или пунктах глубокой переработки. При этом неизбежно возникает вопрос рациональной или оптимальной раскряжевки хлыстов [3,4,5] с целью получения максимально — возможного выхода деловой древесины с заданными качественными показателями.
Основными признаками качества лесоматериалов являются [14]: порода древесиныразмеры сортиментовобработкапороки древесины и их допускаемые размерытехнические свойства самой древесины без пороков. Необходимые качественные признаки сортиментов получают, за исключением породы, при раскрое хлыста. Раскрой хлыста может быть ручным (индивидуальный) или машинный (при помощи различных раскряжевочных линий). Машинный, также, делится на индивидуальный (поштучный), групповой и другие методы раскроя.
Как при ручной, так и при машинной раскряжевке должны выпиливаться лесоматериалы определенных размеров и качества, что является основой наилучшего использования ресурсов древесины.
При раскрое хлыстов на сортименты руководствуются следующими принципами [4,14]• максимально возможное полное и качественное использование объема выделенного лесосечного фонда для производства специальных высококачественных и рядовых лесоматериалов-• получение наибольшего количества деловых сортиментов в общем выходе лесоматериалов, т. е. тщательное отделение деловой древесины от дровяной-• постоянная работа по повышению сортности и качества заготовленных деловых сортиментов, т. е. получение наиболее дорогих в ценностном выражении лесоматериалов.
Как показывают исследования [4], при ручной разделке хлыстов (где должны в наибольшей степени реализовываться принципы рационального раскроя предмета труда первичной обработки древесины) не получают необходимого результата в силу присутствия тяжелого физического труда.
Наибольший выход запрограммированных сортиментов по качеству и назначению получается при применении карт раскроя [4].
Машинная первичная обработка древесины на линиях с продольной подачей типа ПЛХ-ЗАС, ЛО-15С, ЛО-ЗО ППЛ-4, ЛО-68 увеличивают возможности соблюдения вышеуказанных принципов раскроя, но в силу отсутствия автоматизации процесса оптимизации параметров сортиментов по методу проф. Петровского B.C., раскрой ведется на уровне рациональной раскряжевки. Понятия рациональная и оптимальная раскряжевка лесоматериалов очень близки между собой однако оптимальный автоматизированный метод раскроя хлыстов по методу проф. Петровского B.C. более широк и включает математическое обеспечение и возможность аналитического выражения параметров продукта и предмета труда первичной переработки древесины [4] с реализацией обработки в автоматическом режиме.
Линии с поперечной подачей типа СТИ-2, СТИ-3, СЛ-4, ЛО-Ю5,ЛО-26К, ЛО-65 спроектированы в основном для получения высокой производительности — более 300 м3/смену.
При этом возможности линий этого типа по рационализации и оптимизации раскроя ограничены или отсутствуют полностью.
Предшествующие поточные линии для раскряжевки хлыстов с поперечной подачей (до линии ЛО-Ю5) как правило индивидуального изготовления. Насчитывается более 20 видов линий с различной компоновкой, при этом ни одного унифицированного узла. Линия ЛО-Ю5 была рекомендована к серийному производству, но так и не была востребована рядовыми леспромхозами из-за высокой стоимости и высокой производительности. Пункты глубокой переработки древесины (например, Усть-Илимский ЛПК) предпочли поточные линии Финского производства фирмы «Раума Репола» или собственной конструкции (Братский Целлюлозно-бумажный комбинат).
Велик разрыв в производительностях линий, с продольной подачей (в среднем 140 м3/смену) и линий с поперечным перемещением (450−750 м3/смену).
Компоновка линий с поперечной подачей такими агрегатами, как поперечный транспортер ЛТ-53, продольный ориентирующий транспортер ЛТ-75, разобщитель хлыстов ЛТХ-80 и др. конечно повышает надежность линий. Однако наблюдается другой эффект — ни одна из поточных линий не имеет расчетный коэффициент заполнения упоров надвигания на пилы слешера равный единице. Это заведомо снижает производительность, даже расчетную, а при наличии стохастических воздействий, линии значительно теряют в производительности, этого не наблюдается в раскряжевочно-сортировочной линии «Раума Репола» .
Вариант линии ЛО-Ю5, рекомендованный к серийному производству, имеет выдвижные пилы. Назначение «выдвижения пил» — исключение зажима пил при раскряжевке. Причина зажима пил — упругие свойства хлыстов и конструктивные особенности пильных агрегатов [15].
Разобщение и подача хлыстов в полуавтоматических раскряжевочных линиях, продольного типа, поправка хлыстов на слешерных и триммерных линиях, сортировка сортиментов в последние годы все чаще осуществляется гидроманипуляторами. При этом зачастую гидроманипуляторы совершают последовательные элементарные перемещения, что сказывается на их производительности. То есть практически не используются совмещенные операции.
Бурная компьютеризация смежных областей показывает, что имеющаяся практика совершенствования технологических процессов на базе применения компьютерной техники и методов автоматизированной оптимизации параметров оборудования сокращает сроки проектирования технологических процессов в 10−15 раз, технологической оснастки в 10−12 раз [8].
В практике анализа и проектирования технологических процессов раскряжевки хлыстов отсутствуют формализованные методы моделирования с выражением перемещений в явном виде, Отсутствуют методы моделирования, которые на стадии проектирования позволяли бы закладывать программируемость технологического процесса.
1.2. Характеристики предмета труда и факторы, влияющие на размерно-качественные параметры продукта труда первичной обработкиРазмерно-качественные характеристики продукта труда первичной обработки зависят от множества факторов. Например, природно-климатические факторы, при которых формируются пороки роста. Как показывает практика, только лесоматериалы небольших размеров могут быть без пороков, сортименты же более или менее крупных размеров, особеннокруглые лесоматериалы, всегда имеют те или иные пороки (сучки, трещины, гниль, и др.) — комбинации, в которых могут встречаться пороки древесины в сортиментах, и степень их развития очень разнообразны [16]. Оценка качества круглых лесоматериалов производится по породе, размерам, обработке и по наличию и размерам имеющихся в них пороков [ 14,16].
Пороками считают недостатки отдельных участков древесины, снижающие ее качество и ограничивающие возможность ее использования.
Дефектами называют пороки древесины механического происхождения, возникающими в ней в процессе заготовки, транспортировки, сортировки, штабелевки, и механической обработки (обдир, заруб, запил, карра, скол, вырыв, скос пропила).
Ряд пороков древесины зависит от самой природы дерева. Нельзя, например, представить себе дерево без сучков. Поэтому во всех лесоматериалах, как неизбежное, приходится допускать в том или ином размере пороки древесины.
От пороков, образовавшихся в процессе роста дерева (сучки, внутренние гнили, кривизна и др.), необходимо отличать пороки, получающиеся в процессе заготовки, транспортировки, обработки, хранения, и потребления древесины (запилы, зарубы, сколы, синева и др.)Пороки первой группы (пороки растущего дерева) не зависят от деятельности человека, а пороки второй группы (пороки срубленного дерева) в значительной мере есть результат несоблюдения технологических требований заготовки, транспортировки, хранения и обработки древесины. Поэтому необходимо принимать все меры, сводящие до минимума эту группу пороков древесины.
Например, раскряжевка хлыстов без разделения пачек (имеется в виду ручная) ведет к значительному увеличению в сортиментах механических повреждений (запилы, сколы), удельный вес которых, как сортоопределяющих пороков, по отдельным лесозаготовительным объединениям в последние годы достигает 15−20%. Это ведет к снижению сортности сортиментов, а в рудничной стойке механические повреждения совершенно не допустимы, так как резко снижают сопротивление продольному изгибу (в расчетную формулу диаметр входит в четвертой степени) [14].
Влияние пороков на качество древесины зависит от многих фактороввида порока, размеров поражения древесины, места его расположения в сортименте и назначения сортимента. Один и тот же порок в одних сортиментах совершенно недопустим, а в других может быть допущен с теми или иными ограничениями. Например, боковые трещины, запилы, зарубы, и сколы в фанерных кряжах или зарубы, запилы и сколы в рудничной стойке, как указано выше, безусловно являются пороками (дефектами), а в балансах они не имеют никакого значения.
В настоящее время основная масса сортиментов круглых лесоматериалов лиственных и хвойных пород заготовляется по двум унифицированнымстандартам: по ГОСТ 9462–88 и ГОСТ 9463–88. По ГОСТ 9462–88 ведется заготовка сортиментов лиственных пород, по ГОСТ 9463–88-хвойных. Принципиальные основы построения обоих ГОСТ аналогичны. Все лесоматериалы хвойных и лиственных пород по толщине ГОСТ подразделены на три класса крупности: мелкие — для хвойных от 6 до 13 см и для лиственных — от 8 до 14, средние — от 14 до 24 см, и крупныеот 26 см и выше. По признаку назначения сортименты круглых лесоматериалов подразделены на четыре основные группы:• для распиловки и строгания-• для лущения-• для выработки целлюлозы и древесной массы (балансы)-• для использования в круглом виде-Указанные деления сортиментов крупных лесоматериалов на группы по толщине и видам назначения позволяют лучшим образом маневрировать лесными ресурсами применительно к их товарным и хозяйственным особенностям, обусловленным различием качественных зон стволовой древесины и развитием вторичных пороков в процессе длительного хранения, транспортировки, заготовки и обработки древесины.
В ГОСТ 9462–88 и ГОСТ 9463–88 сетка сортов, разделяющих древесину по ее технологическим и биологическим свойствам, построена из учета возможного разделения ствола дерева, по его длине на три основные зоны. качества, установленные по массовому виду биологического порока древесины — сучкам (1-комлевая, П-срединная, Ш-вершинная.) Основные направления использования древесины каждой из зон: I зона — бессучковая с глубоким залеганием мелких заросших сучковмелкие заросшие сучки глубокого залегания диаметром 10−15 мм могут быть гнилыми, реже табачными (с выходом на поверхность) — лесоматериалы высшего качества для выработки высококачественной пилопродукции, заготовок, лущеного шпона, строганной фанеры и др. II зона — зона открытых, отмерших сучьев стабильных размеров. Отмершие сучья стабильных размеров диаметром 20−50−60 мм, преимущественно загнивающие и гнилые, а также табачные. Лесоматериалы используются для выработки обычных пиломатериалов шпал, брусьев и мелких заготовок, для лущения и строгания, для выработки целлюлозы, а также для использования в круглом виде. III зона — вершина с преобладанием крупных сучков.
Здоровые живые крупные сучки диаметром 70−100 мм и более. Лесоматериалы для разделки на рудничную стойку и балансы, шпалы, а также для использования в круглом виде.
Применительно к этим качественным зонам ствола, исходя из технических и технологических свойств древесины [4,16] этих зон в стандартах установлены три основные качественные категории (сорта) и одна (четвертая) дополнительная, в которой объединены сортименты круглых лесоматериалов более низкого качества с нормами допуска пороков, превышающими принятые нормы для основных трех сортов стволовойдревесины. Лесоматериалы последней группы могут быть выработаны из любой зоны стволовой древесины.
Указанная структура построения ГОСТ 9462–88 и ГОСТ 9463–88 существенно облегчает задачу объективной оценки (разметчикам при ручной раскряжевке и операторам линий при машинной раскряжевке) качества стволовой древесины при разметке и рациональной раскряжевке каждого отдельного хлыста хвойных и лиственных пород разных размерностей и кондиций.
Механические повреждения и дефекты обработки — затеска, заруб, запил, скол у торца, отщеп, скос пропила, разрыв недопила при раскряжевке на слешерных линиях, запилы, образующиеся при возврате хлыстов, зажавших пильный диск на слешерных линиях, отщепы при прокатывании сортиментов в процессе раскроя на слешерных линиях, а для лесоматериалов, предназначенных для распиловки и лущения, также и обдир коры [14,16] -являются технологическим браком производства. При этом механические повреждения при глубине более 1/10 диаметра в месте повреждения переводят лесоматериалы в низкий (4-ый сорт).
Скос пропила при величине, большей 1/10 диаметра соответствующего торца, ведет к потере древесины, так как в случае косореза длина лесоматериала измеряется по наименьшему протяжению, что приводит к укорочению длины сортимента при учете потребителем против номинальной на 1 кратную единицу и потере древесины.
Обдир коры, особенно в значительном размере, при длительном хранении лесоматериалов в летний период ведет к появлению трещин усушки (торцовых, наружных боковых) и побурению (задыханию), возникающим в древесине безъядровых породв результате лесоматериал теряет качество и не может быть использован по назначению.
В лиственных фанерных кряжах 1-ого сорта обдир коры не должен превышать 15% общей боковой поверхности кряжа. Размер обдира коры определяется следующим образом:(1.1)лёегде: Бплощадь обдира коры %-Аобдир коры по окружности сортимента, сме- обдир коры по длине сортимента, см-Ьдлина сортимента, смё- диаметр сортимента, см.
Скос пропила. Концы лесоматериалов опиливаются под прямым углом к продольной оси сортимента. Не перпендикулярность обрезки торцов обычно ограничивается определенными размерами, так по ГОСТ 9462–88 и ГОСТ 9463–88 скос пропила не должен превышать 0.1 диаметра торца. Особое внимание уделяется правильности обрезки торцов рудничных стоек, у которых скос пропила не должен превышать 1 см в стойках толщиной более 12 см и 0.5 см — в стойках толщиной 12 см и менее. Например, сосновое бревно длиной 6.5 м и толщиной 50 см по стандарту с припуском должноиметь длину 6.53 м. Объем такого бревна по ГОСТ 2708–44 равен 1.64 м3. При раскряжевке хлыста был сделан допускаемый по стандарту скос пропила 1/16 диаметра, или 5 см. В этом случае длина бревна по наименьшему расстоянию между торцами будет 6.48 м такое бревно относится к 6-метровомукубатура его-1.41 м3, а потеря для поставщика деловой древесины составит около 8%. На слешерных линиях, например, JIO-65 в Игирминском ЛПХ подается древесина обезличено, с предварительной подсортировкой хлыстов на лесосеке. Но подсортировка не ориентирует хлысты. При очень высокой производительности (720−850 м3/смену) выход деловой древесины составляет 80% [17] при этом между упорами оказывается 2−3 хлыста, что способствует появлению косорезов, с косорезом раскряжевывается до 15% хлыстов. При рассмотрении характеристик предмета труда видно, что методы раскроя тесно связаны с геометрическими характеристиками хлыстов. При раскрое хлыстов на сортименты учитывается, например, начало пиловочной зоны по наименьшему диаметру, допускаемому в пиловочном сырье. Поэтому принципу работает триммерная линия МР-8. Финская линия также использует для программирования раскроя начало пиловочных и балансовых зон по допускаемым диаметрам.
Большое значение для пиловочного сырья имеет сбежистость хлыстов. Имеется понятие наибольшего цилиндрического выхода древесины при поперечном раскрое [4]. Получение сортиментов с меньшей сбежистостью влияет на выход пиломатериалов при продольном раскрое пиловочника. Качественные зоны связаны с длиной хлыста. Поэтому четкое разграничение качественных зон и правильная разметка хлыста по длине обеспечивают оптимальный выход деловой древесины.
Методы поперечного раскроя достаточно хорошо освещены в литературе [3,4,5,6,7,14,16]. Влияние применяемого метода раскряжевки хлыстов на выход и качество сортиментов очень большое. От того насколько машинная раскряжевка близка к программному методу раскряжевки зависит качество и выход деловой древесины на данном предприятии [9].
Динамические характеристики хлыстов [15, 176, 178, 179, 180, 181, 182, 186, 194], характеризуемые жесткостью, модулем упругости, распределением массы хлыста по длине, частотными характеристиками, занимают также значительную роль в формировании прежде всего размерно-качественных характеристик самих хлыстов. При переместительных операциях с определенными скоростями возникают динамические нагрузки которые зачастую приводят к поломке хлыстов, особенно вершинной части. Например, при валке деревьев поломка стволов на 2−3 части (особенно в зимнее время), облом вершинной части в пределах 6−7 метров — частое явление при ручной заготовке. Провисы хлыстов длиной 25−32 м достигают значительных величин от 0.5 м до 2 м. Заклинивание пильных дисков при раскряжевке в основном зависит от такой динамической характеристики хлыстов, как упругость (жесткость).
При этом резко повышается мощность, расходуемая на пиление в зависимости от диаметра, длины получаемого сортимента, и диаметра пильного диска[17,18]. Для пильного диска диаметром 1,7 м и длине полухлыста 13 м мощность пиления возрастает в 2.25 раза. При окончании пиления, например, на слешере часто происходит разрыв недопила или отщеп (скол) древесины, поскольку отпиленные отрезки стремятся прокатиться по ходу движения. Сколы и отщепы, также как и разрывы недопила относятся к дефектам раскряжевки и влияют на качество.
Повреждение коры и древесины сортиментов при протаскивании гусеничным протаскивающим устройством, например, линии ППЛ-4, происходит из-за динамических нагрузок и не синхронности скоростей верхней и нижней гусениц [180]. Динамические нагрузки (вертикальные). способствуют углублению зацепов гусениц в кору до древесины ствола. Отставание одной из гусениц, из-за не синхронности движения, способствует сдвигу коры в продольном направлении.
В области первичной переработки древесного сырья динамические характеристики могут играть решающую роль, например, калибровочный станок для оцилиндровки бревен, установленный в начале 90-х годов на лесоперевалочном комбинате, не был запущен в работу из-за резонансных явлений. Резонанс наступал в процессе обработки бревна вращающейся роторной фрезерной головкой, которая перемещалась вдоль продольной оси бревна и вызывала кинематические возмущения бревен, в результате которых бревна вырывало из торцевых зажимов.
В соответствии с вышеизложенным, по разделу можно сделать следующие выводы: на качество и выход деловой древесины при раскряжевке (поперечном раскрое) влияют следующие факторы и характеристики предмета труда:• основные пороки, образующиеся при росте дерева (закомелистость, гниль, кривизна ствола, и др.)• геометрические характеристики (длина, диаметр как функция длины, сбежистость как функция длины)• динамические характеристики (жесткость, распределенная масса, удерживающие связи)• механические повреждения в процессе технологических воздействий механизмов и оборудования (сколы, отщепы, разрывы недопила, косорезы, повреждения коры и древесины по длине ствола)• методы поперечного раскроя в процессе первичной обработки.
1.3. Предметная область проведения исследованийРазмерно-качественные характеристики предмета труда (хлыстов) первичной обработки древесины в основном формируются в зависимости от природно-климатических условий. С момента повала дерева до сортировкисортиментов, хлысты проходят различные технологические фазы, которые в той или иной мере влияют в основном на размерные характеристики (облом, обруб вершин), возможны механические повреждения. Но размерно-качественные характеристики заложенные природой остаются неизменными. При всех типах технологического процесса первичной обработки древесины (вывозка хлыстами, вывозка сортиментами) ключевой фазой является раскряжевка. На этой фазе производства совершаются необратимые изменения предмета труда, закладываются основные качественные характеристики продукта труда первичной переработки древесного сырья, определяется назначение сортимента.
При более подробном рассмотрении фаз технологического процесса лесозаготовок можно определить, что характерной особенностью всех типов технологий первичной обработки древесины являются технологические операции в основе, которых лежат перемещения.
Для лесосечных работ характерны пространственные перемещения предмета труда. Почти на всех фазах заготовки леса лесосечное оборудование имеет гидроманипуляторы, которые имеют три-пять степеней свободы. Наличие трех степеней свободы обеспечивает попадание в заданную точку пространства и ориентацию рабочего органа в одной плоскости. Ориентация рабочего органа в одной плоскости затрудняет его использование с большой эффективностью. Например, для валочной машины типа ЛП-19 возможны при валке косорезы, не достаточно удобно валить деревья с наклоном и т. д. То есть предпосылки к перерасходу древесины могут закладываться изначально — при первой технологической операции. Деревья и хлысты перемещаются на лесосечных работах как в пакетах так и поштучно.
Штучное (одиночное) перемещение предмета труда осуществляется при валке, в зависимости от типа трелевочного механизма, грузятся штучно или пакетом. Обрезка сучьев преимущественно штучная. Погрузка, вывозка, разгрузка хлыстов, деревьев, сортиментов осуществляется пакетами. Величина пакета при погрузке зависит от грузоподъемности погрузочного механизма. То есть можно считать, что одиночные хлысты и пакеты хлыстов участвуют в технологических операциях в равных пропорциях.
Нижнескладские работы также характеризуются наличием основной операции — перемещения предмета труда. Существуют операции, которые присущи линиям с продольной подачей и с поперечной. Это — разобщение пакетов хлыстов, раскряжевка, сортировка сортиментов. Как те, так и другие линии преимущественно ведут штучную обработку хлыстов.
Раскряжевочные агрегаты — преимущественно круглопильные. Типы раскряжевочных агрегатов для продольных линий — балансирные и маятниковые, или комбинированные с цепными пилами, с нижним или верхним расположением оси вращения пильных дисков относительно плоскости перемещения (размещения) предмета труда.
Для линий с поперечным перемещением используются круглопильные стационарные, в триммерных линиях используются маятниковые ибалансирные агрегаты. В слешерах используются выдвижные маятникового типа. Основой технологических операций для линий с поперечной подачей также являются перемещения предмета труда. Дальнейший анализ переместительных операций показывает, что предмет труда как в линиях с продольной подачей, так и в линиях с поперечным перемещением, перемещается в основном в горизонтальной плоскости. Наряду с агрегатами типа транспортеров, при раскрое хлыстов используются гидроманипуляторы, обеспечивающие пространственное перемещение предмета труда.
Разобщение хлыстов осуществляется разгрузочно-растаскивающими устройствами (РРУ). РРУ плюс гидроманипулятор, разобщители хлыстов типа ЛТХ-80. Подача на раскряжевку осуществляется на линиях с продольным перемещением продольными транспортерами, гусеничными протаскивающими устройствами (ГПУ), гидрополистпастовым приводом протаскивающей каретки (ЛО-ЗО). В линиях с поперечной подачей добавляется еще одна операция — ориентация хлыстов. Ориентация осуществляется продольными транспортерами, шнековыми транспортерами, продольными рольгангами. Подача на раскряжевку осуществляется в основном поперечными транспортерами.
Операция удаления сортиментов в линиях с продольной подачей осуществляется поперечными сбрасывателями различного типа. В линиях с поперечной подачей эту операцию выполняет в основном транспортер надвигания или продольный транспортер.
Сортировка для обоих типов линий осуществляется в основном на продольных транспортерах (полуавтоматического типа, ручного) с поперечным сбрасыванием сбрасывателями гравитационного типа.
Как для лесосечных, так и для нижнескладских операций характерно то, что предмет труда (хлысты), как упругая балка переменного сечения проходит через все операции перемещений. Особо следует отметить операции выполняемые гидроманипуляторами, погрузчиками и раскряжевочными агрегатами [10,12,15], на которых особенно ярко проявляются упругие свойства предмета труда и происходит активное влияние упругих свойств хлыстров на технологический процесс, оборудование и, оказывает влияние на формирование размернокачественных характеристик сортиментов в процессе раскряжевки.
Вышеизложенное позволяет сделать следующие выводы по разделу: — формирование основных размерно-качественных характеристик продукта труда первичной обработки древесины осуществляется на стадии раскряжевки хлыстов.- основой технологических операций при первичной обработке древесины являются перемещения.- гидроманипуляторные системы осуществляют пространственное перемещение предмета труда— раскряжевочные линии, как продольного, так и поперечного направления подачи предмета труда осуществляют перемещения преимущественно в горизонтальной плоскости.
Вышеуказанные выводы, позволяют дать формулировку предметной области исследований: Предметной областью исследований в данной работе является технологический процесс первичной обработки предмета труда лесозаготовок (хлыстов), совершающего активное взаимодействие с технологическим оборудованием при переместительных и других технологических операциях, обеспечивающих необратимые размерно-качественные изменения предмета труда для получения первичного продукта труда (круглых лесоматериалов).
1.4. Влияние переместительных операций на качество и выход деловойдревесиныПеремещения предмета труда (хлыстов) при первичной обработке древесины являются основой технологических операций. На долю перемещений при обработке на линиях с продольной подачей типа ПЛХ-ЗАС, ЛО-15С, ЛО-ЗО, ППЛ-4, ЛО-68 приходится около 95% от всех операций. Для потоков с поперечной подачей (например на слешерных линиях) доля переместительных операций составляют 100%. При ручной раскряжевке переместительные операции занимают «75% от общего числа операции. Меньшее число перемещений при ручной раскряжевке очевидно связано с тяжелым физическим трудом.
Зависимость выхода деловой древесины и качества сортиментов при ручной раскряжевке от перемещений отмечена в работах [4,14]. Ручная раскряжевка электромотоинструментом требует ручного разобщения пакета хлыстов, разметки хлыстов и раскряжевки. Раскряжевка без разобщения пакета ведет к появлению запилов, зарезов, а также ведет к снижению выхода деловой древесины. Для увеличения производительности, зачастую раскряжевываются 2−3 хлыста при разметке одного хлыста. При этом комлевые срезы могут лежать не в одной плоскости (в разбег), что ведет к снижению выхода деловой древесины, а при наличии гнили, к снижению сортности.
Полуавтоматические линии с продольной подачей в общем случае имеют в своем составе следующие агрегаты [19,20]-разгрузочно-растаскивающее устройство—гидроманипулятор—подающие транспортеры—приемно-отмеривающе-сбрасывющие устройства- -сортировочные транспортеры.
Разгрузочно-растаскивающие устройства частично разобщают и подготавливают пакет хлыстов к разобщению.
Гидроманипуляторы разобщают и подают хлысты на подающий транспортер. Подающий транспортер подает хлысты на длину сортимента, которая зависит от качественной зоны и назначения сортимента.
Приемный стол имеет отмеривающее устройство для формирования размерных характеристик сортиментов. После поперечной распиловки сортимент сбрасывается на сортировочный транспортер. Сортировочный транспортер осуществляет сортировку сортиментов по диаметрам, длинам, породам.
Все операции, за исключением операции раскряжевки — переместительные. Не трудно заметить, что они подразделяются на операции:1) Перемещения подготовки пакета к разобщению или частичного разобщения.
2) Перемещение разобщения пакета.
3) Перемещение подачи хлыста на подающий транспортер.
4) Перемещение подачи хлыста на раскряжевку.
5) Перемещение сбрасывания на сортировочный транспортер.
6) Перемещение к лесонакопителям.
7) Перемещение сбрасывания в лесонакопитель.
Четвертое перемещение является перемещением формирования размерно-качественных признаков сортиментов. Шестое и седьмое перемещения являются перемещениями формирования назначения и оптимального использования групп продукта труда первичной переработки древесины. Сортировка является перемещениями, влияющими, например, на выход продукции лесопиления. Поскольку сортировка по диаметрам с градацией в 1 см повышает выход пиломатериалов «на 10%. То есть, распиловка бревен не поставных диаметров вызывает снижение выхода: больше у тонкомерных бревен и меньше с увеличением диаметра [21].
Поточные линии с поперечным перемещением хлыстов в основном имеют следующий состав технологических операций по перемещениям (на примере линии ЛО-105) [19,25]1) Перемещение подготовки пакета к разобщению и частичное разобщение.
2) Перемещение разобщения пакета.
3) Перемещение ориентации хлыста.
4) Перемещение надвигания на слешерные пилы.
5) Перемещение сбрасывания на сортировочный транспортер.
6) Перемещение подачи к лесонакопителям.
7) Перемещение сбрасывания в лесонакопители.
Третье и четвертое перемещения являются перемещениями формирования размерно-качественных характеристик продукта труда. Шестое и седьмое перемещения являются перемещениями формирования размерно-качественных признаков для использования по назначению, полученных сортиментов. Перемещения до формирования размерно-качественных характеристик сортиментов являются подготовительными. Перемещения на сортировкуявляются перемещениями формирования групп сортиментов по назначению и оптимального использования продукта труда при последующей обработке.
Таким образом, выход деловой древесины зависит от определенных какой-то сложной или простой программой перемещений, как на линиях с продольной подачей, так и на линиях с поперечным перемещением хлыстов.
Выход деловой древесины зависит от многих факторов, которые рассмотрены в разделе 1.2. Для разных регионов выход деловой древесины различен. Например по данным [22,25] программный раскрой на слешерных линиях в Красноярском крае давал выход деловой древесины до 89%. На линиях с продольной подачей в тех же условиях 90,5−91%. На ручной раскряжевке 85%. Во всех трех случаях выход деловой древесины обеспечивался теми или иными перемещениями. Таким образом, переместительные операции при первичной переработке хлыстов на стадии раскряжевки являются размерно-качественно-формирующими. При этом следует подразделять перемещения на подготовительные, размерно-качественно формирующие и перемещения продукта труда формирующие качественные показатели групп сортиментов для их эффективного использования при последующей обработке.
1.5.Обзор теоретических и экспериментальных исследований технических средств для реализации первичной обработки древесного сырья1.5.1. Исследования по моделированию размерно-качественных характеристик объекта труда первичной обработки древесного сырьяБольшое внимание в лесозаготовительной промышленности нашей страны и за рубежом уделяется размерно-качественным характеристикам предмета труда. Исследования возможности автоматизации процесса оптимальной раскряжевки хлыстов проведены проф. Петровским B.C. [3, 4, 28, 29, 30, 31, 32, 33]. В основных работах проф. Петровского B.C. указывается, что экономическая эффективность автоматической оптимизации раскряжевки хлыстов слагается из улучшения показателей выхода сортиментов и повышения производительности первичной обработки.
В работах Петровского B.C. были проведены экспериментальные исследования на большом количестве хлыстов различных пород. При этом раскряжевку проводили в различных регионах нашей страны с различным качеством лесфонда. Качество лесфонда оказывает очень большое влияние на выход деловой древесины. В частности оптимизация раскряжевки увеличивает выход деловых стандартных бревен на 1−31%. Чем хуже качество древесины хлыстов, тем больше выход деловых сортиментов [4]. Как указывает автор, при оптимизации раскряжевки хлыстов выход цилиндрического объема древесины сортиментов увеличивается на 3.2%. Это существенно улучшает качество и товарный вид лесоматериалов. При увеличении цилиндрического объема пиловочных бревен на 3,2% выходобрезных пиломатериалов возрастает на 2,2−2,4%, что значительно повышает эффективность лесопильного производства и соответствует программе развития лесопромышленного комплекса до 2002 года Российской Федерацией. В которой планируется увеличить выход пиломатериалов на 1,5%.
В работе [4] определены четыре критерия оптимальности раскряжевки: -общий объемный выход деловой древесины- -выход лесоматериалов плановых сортиментов- -товарный выход сортиментов в денежном выражении- -цилиндрический объем древесины бревен-Как указывается в работе [4], полная и одновременная максимизация четырех критериев оптимальности раскряжевки на каждом хлысте практически невозможна. При большом количестве заготавливаемых сортиментов в соответствии с таксационными характеристиками лесосечного фонда лесозаготовительное предприятие стоит перед сложной задачейобеспечить выполнение весьма сложного по составу сортиментного плана. С минимальным выпуском дровяной древесины получить сортименты по размерам в соответствии с ГОСТом и с повышенным цилиндрическим объемом. Разнообразие заготовляемых сортиментов требует детального изучения лесосечного фонда, установления его товарной структуры. В работе [4] рекомендуется все поступающие на раскряжевку хлысты разделить на три категории: крупные, средние, тонкомерные.
Определить оптимальную схему раскряжевки трудно даже теоретическислишком много вариантов. Однако на количество схем раскряжевки накладывается ряд ограничений, которые значительно уменьшают количество схем:1) Сортименты заготавливаются не произвольной длины, а строго в соответствии с ГОСТ.
2) Пиловочные бревна длиной менее 4 м не пользуются спросом у потребителя или имеют стоимость меньшую, чем длинные сортименты.
3) Длины сортиментов, перевозимых по Ж.Д. должны быть кратными длинам железно-дорожных платформ и вагонов.
4) Для сплава в плотах сортименты в одном пучке длиной менее 4 м или разной длины также не пригодны.
5) Допуски или ограничения по диаметрам для целлюлозо-бумажной промышленности.
6) Ограничения на сортименты связанные с породным составом и таксационной характеристикой лесосырьевой базы.
Проф. Петровский подтвердил и развил гипотезу проф. Захарова В. К [34], о единстве средней формы стволов одной породы в относительных величинах по относительным высотам и предложил использовать математическую модель образующей стволов, поступающих на раскряжевку.
Практическое применение уравнения образующей показало большую эффективность раскряжевки по картам раскроя. Применение замера диаметрав середине ствола облегчает задачу получения размерных характеристик по длине хлыста и создает предпосылки для создания автоматизированных комплексов по первичной переработке древесины [8]. Таким образом, проектирование лесообрабатывающих потоков, оборудования, и агрегатов, составляющих поточные линии, невозможно без учета размерно-качественных и других характеристик предмета труда, (хлыстов).
Изучение характеристик предмета труда является предметной областью во многих направлениях исследований лесозаготовительных процессов. В работах [5, 6, 7] исследования производились с помощью моделирования технологических процессов по технико-экономическим показателям с учетом влияния вероятностных факторов и с использованием теории массового обслуживания. Разработанные технико-экономические модели рекомендуется использовать при проектировании новых лесозаготовительных предприятий, а также при реконструкции существующих. Кроме того, указанные показатели определяются при обосновании областей рационального применения видов и существующих систем лесообрабатывающих машин и их количественного соотношения.
Наиболее экономичные для данного предприятия виды лесозаготовительных машин определяют по минимуму приведенных затрат. При этом для сравнения вариантов необходимо знать следующие показатели: годовой объем производстварежимы работытехнологический процесспроизводительность лесообрабатывающих машин с учетом конкретных природно-производственных условийэкономические показатели. При определении перспективного выпуска лесообрабатывающих машин необходимо прежде всего знать общий ожидаемый объем обработки или переработки древесины в отрасли и природно-производственные условия на расчетный период. На основании расчетных данных можно установить годовой объем выработки систем лесообрабатывающих машин и путем технико-экономических сравнений определить наиболее экономичные системы для определенных регионов. При этом рассчитываются приведенные затраты, по которым выбирают лесообрабатывающие машины, с учетом всех факторов и выявляют в результате технико-экономических сравнений по минимуму приведенных затрат. Основная задача, которая решается, например, для раскряжевочных установок — определение области эффективного применения по сравнению технико-экономических показателей с учетом вероятностных размерно-качественных характеристик предмета труда первичной переработки (деревьев, хлыстов) [6].
Исследования проведенные Редькиным А. К, Дудюк Д. Л, Чувелевым A.M., Захариковым В. М., Рахманиновым Г. А, Залегаллером Б. Г., Ласточкиным П. В, Бойковым С. П. [5, 6, 7, 11, 19, 20, 35, 13] показали, что функциональные связи в лесной промышленности в большинстве своем имеют стохастический характер. Моделирование таких сложных систем как нижний склад, лесозаготовительное предприятие в целом, и, наконец, моделирование лесопромышленного комплекса невозможно без учетаггвероятностного характера свойств предмета труда и связей между отдельными участками лесопромышленного комплекса.
1.5.2. Исследования по моделированию технологического процесса первичной обработки древесного сырьяМатематическое описание производственных процессов нижних складов вероятностными методами изложено в работе [35]. Технологическое оборудование представляется как система массового обслуживания с описанием потоков объектов труда в виде распределения вероятностей. Наряду с этим производится описание входящего потока требований продолжительностью времени обслуживания, как функции распределения продолжительности обслуживания. Качество функционирования производственных систем, как систем массового обслуживания, определяется полнотой загрузки производственных агрегатов и характеристиками (вероятностными) очереди объектов труда перед ними. В этой же работе даны определения технологического процесса с последовательным, разветвленным и параллельным агрегатированием. Теоретические основы проектирования механизмов посвящены способам ориентирования заготовок, определению основных параметров механизмов питания поточных линий с учетом динамической и статической разрешающей способности.
Ресурсосберегающим, малоотходным технологиям посвящена работа Дорошенко В. А. [8]. Где рассмотрены технологии первичной обработки древесины, производств и лесопромышленных предприятий, при модернизации существующих производств.
Процесс переработки древесины представлен с точки зрения системного подхода в виде автоматизированного технологического комплекса (АТК) в состав которого входит управляемый технологический комплекс и система управления. Основой управляемого технологического комплекса является технологический объект управления (ТОУ), система устройств автоматизации измерений (СУАИ), система автоматизированных исполнительных устройств. В состав ТОУ входит множество технологических операций первичной обработки круглого леса. В работе [8] решается задача многокритериального синтеза технологической структуры первичной обработки древесины (автоматизированного технологического комплекса) и синтез структуры систем устройств автоматизации измерений (СУАИ) геометрических размеров хлыстов и круглых лесоматериалов для систем автоматизированного раскроя, сортировки, учета хлыстов и круглых лесоматериалов для систем автоматизированного раскроя сортировки, учета хлыстов, и круглых лесоматериалов. Круглый лес как технологический объект механической первичной обработки представлен множествами состояний поверхностей обработки от начального состояния (исходного сырья) до конечного состояния (продукция, изделие). За исходное сырье дляпервичной обработки в целом и для производства подготовки древесного сырья являются деревья и хлысты.
Среди поверхностей хлыста определены: базовая (торцовая комлевая поверхность), непосредственно поверхность хлыста включающая поверхность зоны откомлевки, бессучковой зоны, поверхность зоны сучьев, поверхность вершинной зоны. Из состава этих зон выделены поверхности, которые являются базовыми для получения сортиментов.
Технологическое оборудование, как элемент технологической структуры, представлено в виде конечного множества действующего технологического оборудования. Множество технологического оборудования и его модификаций, параметров технологического оборудования и их значений, способов агрегатирования технологических потоков производств, видов связи в технологических потоках определяет множество исходных вариантов технологических комплексов производств и технологических структур лесопромышленных предприятий в целом. За базовую основу приняты системы 1НС, 2НС, ЗНС и др. Наряду с технологическим оборудованием и сырьем в работе рассмотрены СУАИ параметров управляемого технологического комплекса, в виде множеств условий, признаков и параметров синтезированной технологической структуры. Для синтеза технологических структур и СУАИ выбрана теория графов и связанный с ней матричный аппарат.
В качестве математической модели используются ориентированные графы. В графах используются бинарные отношения вершин. Для выявления формальных преобразований над графами использовалось матричное задание графов в виде матрицы смежностей или матриц инциденций. Модель технологической структуры для решения многокритериальной задачи представлена в виде множества МК={Т3, Мэ, Ск> Рп} где Т3 — тип многокритериальных задачМэмножество оцениваемых элементов технологической структуры и СУАИСк-состав вектора показателей эффективности технологической структуры и СУАИРп-решающее правило (критерий) задающий на Мэ отношение предпочтения. Множества, входящие в модель синтеза, являются дискретными конечными замкнутыми множествами, образующими в ш-мерном пространстве показателей эффективности дискретное конечное множество допустимых вариантов (МДВ). Задача синтеза при этом заключается в выборе такой точки из МДВ, которой соответствует наилучшее значение вектора К.
Выделение требуемой степени упорядоченности сравниваемых вариантов и показателей эффективности позволило сформулировать следующие задачи синтеза технологических структур:1. Частичное упорядочение сравниваемых вариантов на основе отношения не строгого порядка, при отношении толерантности относительно упорядочения показателей эффективности по важности.
2. Строгое упорядочение сравниваемых вариантов и показателей эффективности.
3.Комбинированное упорядочение сравниваемых вариантов и показателейэффективности.
В первой многокритериальной задаче для выделения лучших вариантов технологических структур используется безусловный критерий предпочтения (критерий Парето), который позволяет на ранней стадии синтеза произвести отсев множества худших вариантов. Основное достоинство безусловного критерия является его объективность при выделении не худших вариантов и отсеве худших, без введения дополнительных условий, но при этом задача определения оптимального варианта (единственного варианта) не решена до конца. Выделение не худших вариантов является удовлетворительным.
Введение
дополнительных условий и на их основе условных критериев предпочтения позволило автору свести сравниваемые варианты к строгому упорядочению, т. е. решение задачи сводится к лексикографическому отношению предпочтения, при котором все показатели эффективности (частные критерии) образующие векторный показатель, строго упорядочены по важности. В процессе сравнения вариантов в первую очередь используется первый по важности показатель, за счет любых потерь по остальным показателям. При равенстве значений первого показателя для двух и более вариантов используется второй показатель и т. д.
Формирование показателей эффективности рассмотрено исходя из поставленной задачи синтеза и предложенных для этой цели модели синтеза и математической модели технологической структуры. Переход от геометрической модели заготовки и изделия к технологической осуществляется с помощью графа размерных связей, в котором вершинами являются значения параметров поверхностей, а ребрами технологическое оборудование, преобразующее поверхность до получения требуемых значений параметров. При этом используется показатель избыточности, сформированный в виде отношения числа возможных значений параметров поверхностей хлыстов и лесоматериалов, преобразуемых технологическим оборудованием к числу требуемых значений параметров поверхностей, которые необходимо получить в результате обработки. По значению показателя избыточности осуществляется компоновка раскряжевочных и сортировочных установок в составе поточных линий первичной обработки древесины. В работе предложен метод количественной оценки сложности технологической структуры путем представления информации, содержащейся в графе в алгебраическом виде, матрицей отношений, то есть структурные особенности переводятся на язык чисел. Этот метод позволяет вычислить показатель сложности для любого ориентированного графа.
Синтез технологической структуры на основе комбинированного метода, когда на первом этапе синтеза применяется безусловный критерий предпочтения, а на втором этапе — условные критерии предпочтения, осуществляется выбор допустимых вариантов технологического оборудования, как основного элемента технологической структуры сдальнейшим выбором не худших вариантов и единственного с использованием множества технико-экономических показателей, коэффициентов избыточности и сложности.
Основы оптимизации поточных линий по первичной обработке древесного сырья изложены в работе И. И. Гуслицера, В. П. Шмакова, А. П, Мешыпикова [36]. В работе дана оценка нижнего склада лесозаготовительного предприятия как системы. Дано определение технологии лесоскладских работ, нижние склады «с достаточной степенью условности» классифицируются по способу перемещения предмета труда" в ходе его обработки. Этот же признак определяет соответствующую систему машин и оборудования: с продольной, поперечной и с пачковой (групповой). Дана классификация операций для систем машин 1НС и 2НС. Условия эффективного функционирования поточных линий описаны на примере линий ЛО-26, ЛО-26П и СТИ-3. Моделирование процессов первичной обработки древесного сырья представлено подробной классификацией возможных моделей. Из классификации спонтанно выбрано физическое моделирование через константы и масштабы подобия. К сожалению примера моделирования технологической системы в этом разделе не приведено. Далее рассмотрены графические и буквенные модели трансформации предмета труда при первичной обработке.
Особое внимание уделено графическим моделям динамических систем, при этом указывается, что на основе кинематических схем разрабатываются динамические схемы, которые также представляют собой графические модели, раскрывающие взаимодействие масс, рабочих поверхностей и упругих элементов рабочих машин и предметов труда.
Условия эффективного функционирования поточных линий (в работе [36]) определяется соотношением производительностейП,>П2>.> Пп, 1>Пп<�Пп+1<.<�Пп (1.2)где П, — производительность рабочих машин систем, мПп — производительность лимитирующего звена поточной линиип — число агрегатов в поточной линии-К сожалению соотношение (1.2) далее не раскрывается — насколько должны быть производительности предшествующих агрегатов, перед лимитирующим агрегатом больше, то же касается и агрегатов ПП+1.ПП. Как найти оптимальные производительности для соотношения (1"&-)также не указано.
Как следствие интенсификации работы поточных линий в работе [36], является увеличение скоростей и «увеличение движущихся масс на единицу пути перемещаемого предмета труда и рост динамичности системы».
В работе [36] приведен анализ технологических операций с использованием методов топологии — раздела геометрии, который изучает свойства фигур, устанавливаемые (без измерения и сравнения линейных и угловых величин). Что по мнению авторов может оказать значительную помощь в разработке лесообрабатывающего оборудования. В дальнейшем изложении анализа и синтеза установок для разгрузки подвижного состававводятся буквенно-цифровые обозначения. При этом для наименования процессов введены цифровые символы, а для обозначения технических средств — буквенные символы. Подобным образом зашифрованы критерии целесообразности существования устройств для разделения хлыстов и сконструированы матрицы соответствия устройств для разделения хлыстов заданным критериям. В работе также подробно рассмотрены вопросы ориентации хлыстов на слешерных линиях. При этом отмечается, что для продольных ориентирующих транспортеров характерно недостаточное быстродействие (при этом анализа совместной работы со слешером не приведено). Отмечается высокая технологичность и соответствие основным критериям существования [36] транспортер — манипулятор в линии ЛО-26А.
Обобщение авторов отмечает, что большая расчетная производительность исключает использование продольных ориентирующих транспортеров при сменной производительности поточных линий более 300 400 м³.
Анализируя работу [36] можно сказать, что при анализе и синтезе используются существующие механизмы и оборудование, что затрудняет подбор скоростей смежных агрегатов. Анализ не дает представления о поточных линиях как систем, со сложными функциональными связями. Не указано, что кроме коэффициентов использования по времени, технической готовности, на производительность слешерных линий влияет коэффициент заполнения упоров транспортера надвигания, которые ни для одной известной слешерной линии при стабилизированных параметрах функционирования всех агрегатов не равен единице. Другими словами — расчетные коэффициенты заполнения упоров не равны единице. Это говорит о том, что слешерная линия заведомо обречена на резкое снижение производительности.
Обзор исследований по моделированию технологических процессов нижних складов, показал, что все исследователи большое внимание уделяют влиянию размерно-качественных характеристик предмета труда на технологический процесс нижних складов. В исследованиях технологического процесса нижних складов ключевым разделом везде является раскряжевочный участок нижних складов. Движение потоков древесины прослеживается от разгрузки хлыстов до сортировки сортиментов. Главным теоретическим инструментом при моделировании являются теория вероятности и теория массового обслуживания.
Основной участок нижних складов (раскряжевочный) в моделях рассматривается, как участок с известными параметрами, находящийся под воздействием вероятностных факторов, без углубления в сущность некоторых явлений, которые имеют детерменированный характер. То есть имеются малоизученные факторы, которые закладываются при проектировании поточных линий систематически.
Поточные линии как с продольной, так и с поперечной подачей в последние годы являлись объектом пристального внимания многихисследователей. Это объясняется значительной ролью раскряжевочных участков в хозяйственной деятельности лесозаготовительных производств.
Работа В. И. Кондратьева [37], посвященная процессу раскряжевки хлыстов на многопильных установках типа «слешер», была одной из первых по многопильным установкам. Основные задачи, поставленные В. И. Кондратьевым, заключались в следующем: — обоснование оптимальной схемы размещения пил на слешере— разработка методики расчета некоторых линейных и силовых параметров слешера.- экспериментальные исследования зависимости удельной работы сил трения пильного диска о стенки пропила от последовательности раскряжевки хлыстов и одновременности пиления смежными пилами слешера.
При теоретических разработках в работе [37] обоснован выбор диаметров пильных дисков, и определена рациональная схема размещения пил на слешере из условий наименьшей возможности заклинивания пильных дисков при раскряжевке. Автор объясняет, что зажим пильного диска при раскряжевке на многопильном агрегате происходит из-за смещения концов отрезков в вертикальной плоскости, причинами которых являются неровности поверхности хлыста: сучки, наплывы, кора, кривизна и т. п.
При этом даны рекомендации по размещению пил. Рекомендовано сначала распиливать хлыст пополам. Пилы расставляются углом вперед. Сделан анализ влияния формы хлыста и места размещения пропила на силовые показатели пиления. В результате анализа сделан вывод: «основными причинами заклинивания пил являются кривизна хлыста в плоскости стола слешера, обращенная выпуклостью к пильному диску (53,3%) и пространственная двухсторонняя кривизна, на которую приходится от 31.9 до 59.6% от общего числа заклиниваний.» (конец цитаты).
Процесс раскряжевки на многопильных установках исследовался Н. Ф. Клименко [38], который в своей работе поставил следующие цели: исследовать процесс поперечной распиловки хлыстов и сортиментного долготья различной геометрической формы на установках с поперечным перемещением леса при комплексном рассмотрении совместного взаимодействия геометрических параметров хлыстов, кинематики их движения, конструктивных особенностей раскряжевочных установок, условия беззажимного пиления на рассматриваемых установках.
При этом решались следующие задачи: — обоснование значения угла подьема стола раскряжевочной установки, исключающего прокатывание отпиленных отрезков и их осевой сдвиг, ведущий к зажимам пил стенками пропилов— обоснование взаиморасположения пильных дисков, подающих цепей и толкателей на них, обеспечивающих пиление без зажима — оценка вариантов устранения зажимов за счет других возможных факторовразработка рекомендаций по устранению зажимов пил в пропилах.
При выборе угла наклона слешерного стола автор работы [38] делает вывод: выпиленный из кривого хлыста отрезок, имеющий собственную кривизну и расположенный под углом, а к линии толкателей, под действием веса смещенного центра тяжести, стремясь занять устойчивое положение, совершает угловые перемещения на столе раскряжевочной установки. Эти перемещения будут наибольшими для отрезка, расположенного на двух направляющих поперечного транспортера. И представляют собой затухающие колебания с прокатыванием его по направляющим.
Далее автор обосновывает следующее: в процессе резания на не допиленный хлыст действуют силы: сила резания и сила отжимасоставляющая от веса хлыста, обусловленная наличием угла подъема направляющих усила трения о направляющие поперечного транспортера. Под действием этих сил происходит деформация недопила, что ведет к схождению его стенок и зажиму пильного диска в пропиле. Критическая высота недопила при которой деформация его достигает значений, соответствующих схождению стенок пропила до касания ими пильного диска находится расчетным путем по предлагаемому автором уравнению. Решение уравнения, предложенного автором, относительно высоты недопила Ьн свидетельствует о том, что высота недопила, при которой происходит зажим пильного диска в пропиле, является функцией длины и диаметра распиливаемого отрезка и может достигать Ьн<9 см. Зажим пильного диска обусловлен появлением деформации недопила (конец цитаты).
Из выводов автора [38] следует, что ни при каких значениях угловподъема слешерного стола & скоростях надвигания и и формах зубьев пилы исключить зажимы пильных дисков невозможно. Решение вопроса найдено за счет придания искусственной кривизны хлыста с выпуклостью в сторону пильных дисков.
Интересной работой представляется работа Ф. Е. Захаренкова [11], посвященная оптимизации производственных процессов береговых складов. В книге даны теоретические основы и практические рекомендации по выбору оптимальных параметров и режимов работы технологического оборудования и лесного склада в целом. В книге излагается схема расчета основных параметров склада, представляется метод обобщенной оценки производственного процесса береговых складов как совокупности взаимосвязанных многофакторных явлений.
Береговые склады имеют свою специфику, которая главным образом связана со сплавными, рейдовыми, сезонными работами, работами по выгрузке материалов из воды, со сплоточными работами и др. Но если предприятие заготовительное, то основными участками являются: участок раскряжевки, сплотки и хранения сортиментов перед сплавом. Вопрос раскряжевки естественно в книге [11] также рассмотрен. Рассмотрены поточные линии на базе многопильных раскряжевочных установок. Представлены структурные схемы раскряжевочных потоков с учетомспецифики береговых складов. При этом не обойден вопрос без зажимного пиления на многопильных установках, который в период расцвета слешерных линий, очевидно волновал многих. Автор прямо указывает, что -«Работа слешерной установки зависит главным образом от того, насколько полно при ее проектировании учтены факторы, влияющие на заклинивание пильных дисков в пропиле. Не имея возможности подробно рассмотреть решение задачи ликвидации явления заклинивания пильных дисков, ограничимся здесь рассмотрением лишь основных аспектов этой проблемы» (конец цитаты).
Далее автор дает описание основных аспектов процесса заклинивания дисков при распиловке, основными из которых являются: — зажим пильных дисков в пропиле происходит в следствии осевого смещения хлыстов на опорах подающего транспортера— положение центра тяжести заготовок на протяжении всего процесса раскряжевки постоянно меняется— процесс является дискретным, во времени совмещается с окончанием пропила, т. е. с моментом, когда заканчивается очередное поперечное деление хлыстов на отрезки заданной длины— отрезки хлыста, полученные в процессе поперечной распиловки, могут иметь различные пороки формы, различное первоначальное положение относительно цепей и упоров транспортера и вследствие этого могут поворачиваться на упорах и смещаться в горизонтальной и вертикальной плоскостях.
В книге [39] авторами визуально-константного метода раскряжевки хлыстов, Кондратьевым В. И. и Дегерменджи Г. А. дана технико-экономическая оценка использования многопильных раскряжевочных установок.
В работе рассмотрены вопросы программирования раскряжевки хлыстов на установках типа «Слешер»., Определено число возможных реализаций программ при раскряжевке на многопильных агрегатах. При этом сделан акцент на качественные характеристики получаемых сортиментов и выход деловой древесины. Для выявления качественных показателей были проведены теоретические исследования и поставлен эксперимент в производственных условиях, в котором были задействованы линии СТИ-1, ПЛХ-1 и переносные механические пилы.
Результаты исследований показали, что общий выход деловой древесины на многопильной установке СТИ-1 ниже на 1.2−1.9% чем на установке ПЛХ-1 с продольной подачей, но на 4% выше, чем при раскряжевке переносными пилами. Это объясняется тем, что автоматизированные линии позволяют без использования ручного труда и при незначительном снижении производительности потока производить раскряжевку по более рациональной программе и получать больший выход деловой древесины. На эстакадах при работе переносными пилами раскряжевка связана со значительным физическим напряжением рабочего, и, как правило, по своей технологии приближается к обезличенной. По этой причине рабочийзачастую, не произведя откомлевки, переводит первый комлевой сортимент в дрова.
Полученные СТИ результаты подтверждаются данными предприятий. На Чернореченском ЛПХ на линии СТИ-2 выход деловой древесины на 3−9% выше по сравнению с раскряжевкой хлыстов переносными пилами [39]. Работа [39] содержит подробное описание технологических потоков первичной раскряжевки хлыстов на базе СТИ-1, СТИ-2, СТИ-3, СЛ-4 (многопильные раскряжевочные установки), а также других поточных линий ЛО-26, ЛО-65, Раума Репола и др. Проблематичность расстановки пил по глубине слешерного стола также связана в этой работе с заклиниванием пил в процессе распиловки. При этом отмечено, что сложность формы хлыста, возможная кривизна, различные неровности поверхности создают неплотнотность его прилегания к цепям и упорам (захватам) поперечного лесотранспортера слешера. Наличие не плотностей прилегания получаемых сортиментов от действия собственной массы и силы резания в процессе пиления. В работе [39] также отмечается, что в слешерах встречаются открытые и закрытые столы. При раскряжевке хлыстов на короткомерные сортименты столы делают обычно закрытыми, предпочтение отдают обычно открытым столам, поскольку это облегчает перестройку основной программы раскряжевки.
До 1977 года исследованиями, касающимися беззажимного пиления занимались лишь В. И. Кондратьев (СТИ) и Н. А. Вячеславов (ЦНИИМЭ). Н. А. Вячеславов исследовал возможность беззажимного пиления тонкомерных хлыстов на многопильных установках с рядовым расположением пил и установил, что раскряжевка кривых хлыстов сопровождается зажимом пил в пропилах и, что целесообразнее исключить их появление за счет дополнительных устройств устраняющих смещения распиливаемого хлыста, чем преодолевать усилие зажима за счет мощности привода пил, но рекомендаций по конструктивному исполнению таких устройств не дано [38].
При этом уже по рекомендациям предшествующих исследователей [39] пилы по глубине слешерного стола располагались углом вперед на встречу надвигания хлыста, (прим.авт.)В работе [40] Н. А. Вячеславов изложил результаты сравнительных испытаний пильных блоков на линии ЛО-Ю5, пил СТИ, ЦНИИМЭ. Выявлена их работоспособность, определены мощности, расходуемые на пиление. По расположению пил указано, что при расположении пил углом вперед навстречу надвигания наблюдается большее число заклиниваний пил, чем углом назад.
Наиболее полно, с точки зрения мощности, процесс заклинивания пил слешерных установок изучен в работе Г. С. Миронова [18]. В этой работе графически изображен процесс распиловки хлыста пильным диском совмещенный с диаграммой изменения мощности пиления. На основе экспериментальных данных по замеру мощности с вариацией диаметров, размера распиливаемых отрезков и диаметра пил даны рекомендации попоправочным коэффициентам, которые необходимо применять при расчете мощности привода пильных блоков (табл. 1.1)Таблица. 1.1Значения поправочного коэффициента к0Длина Диаметр пропила, м. отрезка, м. 0.16 0.24 0.32 0.40 Диаметр пильного диска 1.5м. 6.5 1.2 1.4 1.5 1.4 13.0 1.65 1.9 1.85 1.7 Диаметр пильного диска 1.7м 6.5 1.5 1.7 1.75 1.6 13.0 2.25 2.5 2.4 2.25 К более поздним исследованиям, посвященным поперечной распиловке лесоматериалов, относится работа A.C. Торопова [41]. В работе приведены исследования таких параметров хлыстов как плотность, геометрические размеры, которые изменяются по закону относительного (аллометрического) роста (изменения).у = с + а-хв (1.3)где у, х — величины переменных факторов, а, с-константы начального состояния-В — константа равновесияпередающая темп изменения у относительно х.
Согласно закону относительного роста зависимость диаметра лесоматериала от его длины может быть представлена в виде (1.4)d = d0+al? (1.4)Исследования по методу аллометрического роста, проведенные автором [41] показали, что можно получить уравнения формы образующей хлыста с достаточной точностью, причем адекватность математической модели может быть достаточно высокой, используя кусочную аллометрию, т. е. определяя уравнение (1.3) на характерных участках лесоматериала, например зон качества 1,2,3. Точность результатов при использовании метода аллометрического роста значительно повышается по сравнению с получением образующей ствола с помощью полинома 4-го порядка. И как указывает автор [41] регрессионная зависимость не пригодна после выполнения откомлевки и формирования полухлыста.
Особенности взаимодействия предмета труда первичной переработки (хлыстов) с рабочим оборудованием отмечены в большом количестве работ по исследованиям в области лесозаготовок. К этим особенностям авторы относят такие характерные свойства: как упругость, неравномерное распределение массы по длине, влияние породы, влажности, неравномерное распределение по длине упругих констант (модуля упругости при изгибе).
Такие свойства хлыстов как упругость, наличие неравномерно-распределенной массы, способность хлыстов колебаться при различных воздействиях называется динамическими свойствами или характеристиками.
Большое внимание уделено в работе [41] проблемным вопросам процесса поперечной распиловки круглыми пилами. С использованием метода элементного взаимодействия, сущность которого заключается в следующем: фиксируется положение траектории резания пильного механизма в системе координат (плоскости пропила) — траектория резания разбивается на элементарные участки однородной древесины с постоянной плотностью, влажностью, температурой (конечные элементы фиксированной связи зубьев механизма резанья с предметом пиления в конкретный момент взаимодействия). Моделирование процесса и обобщенные схемы основных (пильных и подающих) механизмов для поперечной распиловки определены с помощью морфологических исследований.
Подводя итоги обзора литературных источников по моделированию технологических процессов нижних складов и раскряжевочных линий можно сделать следующие выводы: — при моделировании процессов нижнескладских работ в обязательном порядке учитываются размерно-качественные характеристики предмета труда— при исследовании раскряжевочных участков в основном охватываются узконаправленные аспекты проблемы, отсутствует комплексный подход при решении технологических и конструктивных задач— узким местом «в установках с поперечным перемещением хлыстов, несмотря на многочисленные исследования было и остается заклинивание пильных дисков при раскряжевке хлыстов. Подтверждением этому служит последняя линия рекомендованная к серийному производству ЛО-Ю5, в состав которой входят выдвижные пильные блоки, предназначенные для поперечной распиловки и вывода из пропила при заклинивании путем опускания пильного диска вниз, под транспортер надвигания— обзор литературных источников показал, что авторы [37, 38, 39, 40] считают заклинивание пильных дисков — результатом воздействия различных пороков на положение хлыста по отношению к упорам и направляющих цепей слешерного стола, при этом одни исследователи считают, что диски пил заклиниваются после прокатывания отрезков вперед, другие — до прокатывания в процессе смыкания стенок пропила— в источнике [38] автор предположил, что заклинивание дисков пил происходит в результате смещения ц.т. от кривизны и угловых перемещений с затухающими колебаниями, имеются в виду упругие собственные затухающие колебания отрезков или хлыстов— автор книги [11] предполагает, что положение центра тяжести заготовок при поперечной распиловке постоянно меняется, а процесс является дискретным— более поздние работы [17,18] не настаивают на зависимости природы заклинивания пил при раскряжевке на установках с поперечным перемещением в основном от кривизны и других пороков. В этих работах результат анализа процесса зажима пил воплощается в проверенные практикой коэффициенты перегрузки двигателей по мощности.
1.5.3. Обзор исследований взаимодействия предмета труда первичной обработки древесного сырья с рабочим оборудованиемДинамические характеристики хлыстов являются неотъемлемой частью основных характеристик предмета труда первичной переработки древесины не только на стадии раскряжевки, но и на протяжении всех перемещений в технологическом процессе. На стадии раскряжевки число исследований динамических характеристик не значительно. Это труды Г. М. Васильева, посвященные раскряжевочным установкам с продольной подачей. В своих работах Г. М. Васильев обосновал теоретически подачу хлыстов подающим транспортером с исследованием переходных и установившихся режимов движения.
Г. С.Татаренко исследовал ударное взаимодействие хлыстов с упорами отмеривающих устройств с учетом коэффициента восстановления. При этом хлыст рассмотрен как упругое тело в продольном направлении. A.M. Бельмач исследовал безопорное пиление, возможные скорости надвигания, которые позволили бы отпиливать сортимент без отщепа.
Основные исследования динамических характеристик хлыстов проведены в области погрузочно — разгрузочного и транспортного оборудования. Из этих работ известно, что помимо статических нагрузок от воздействия на рабочие органы предмета труда действуют и динамические, которые зависят от многих факторов: скорости движения, упругих характеристик подвески транспортных машин, рабочего оборудования и, наконец, от упругих характеристик хлыстов, деревьев.
Так результаты эксперимента в работе В. П. Мельникова [42, 43, 44] свидетельствуют, что колеблющиеся хлысты при подъеме их челюстным погрузчиком оказывают существенное динамическое воздействие на рабочее оборудование. Так при скорости подъема 0.4 м/с динамическое воздействие определяется коэффициентом динамичности Кд=1.21. При увеличении скорости подъема до 1.2 м/с Кд увеличивается до 1.65, то есть на 37,5%. Увеличение коэффициента динамичности при вертикальных нагрузках, действующих на стрелу погрузчика с жестким и гибким грузом очень наглядно определено в работах В. Ф. Полетайкина [45,46,47]. В этом случае возмущающие силы, вызывающие колебания упругих элементов погрузчика (в том числе и хлыстов) зависят от скорости движения погрузчика с грузом. С изменением скорости погрузчика с гибким грузом от 60 см/с до 91 см/с коэффициент динамичности погрузчика изменяется от 2,94 до 5,93. Дляжесткого груза Кд изменялся от 2.68 до 4,78 то есть гибкий груз увеличивает динамические нагрузки на стрелу на 20—24%. Экспериментальные данные в этой работе показывают, что при всех сочетаниях рода груза и конструкций подвески, коэффициент динамичности в стреле в 1.7 — 2.7 раза выше, чем в передней подвеске [45]. Это говорит о том, что рабочее оборудование, непосредственно взаимодействующее с предметом труда, наиболее нагружено в динамическом отношении.
В работе В. Ф. Полетайкина [10] рассмотрены вопросы исследования динамики и моделирования рабочих режимов тракторных лесопогрузчиков, оптимизация параметров кинематики технологического оборудования, процессы взаимодействия ходовой системы с опорной поверхностью, расчеты параметров системы виброизоляции рабочего места оператора. Лесопогрузчик рассматривается в движении с поднятым в транспортное положение грузом, при этом учитываются воздействия на ходовую часть и корпус реакции поверхности пути, и упругих колебаний корпуса. Динамические расчетные схемы учитывают продольно-угловые и вертикальные колебания корпуса, рабочего оборудования и груза. При разгоне и остановке машины расчетные схемы учитывают силы инерции масс в продольном направлении, возбуждающие продольно-угловые колебания. При этом приняты следующие допущения: — траектории движения масс прямолинейны— характеристики упругих элементов линейны— гусеничная лента и опорные катки постоянно контактируют с опорной поверхностью— массы подвижных частей гидроагрегатов не учитываются— масса длинномерного груза сосредоточена в трех точках: в захвате, центре масс вершинной и комлевой частей дерева или пакета деревьев, при этом последние две подвешены на упругих элементах-Упругими элементами в системах являются рессоры передней и задней подвесок корпуса, металлоконструкция и гидросистема рабочего оборудования, вершинная и комлевая части длинномерного груза. Влияние массы элементов конструкции на динамическую нагруженность системы определяется кинетической энергией, поэтому в работе [10] приведение масс подвижных частей рабочего оборудования проводится на основе равенства кинетической энергии приведенной массы и суммы кинетических энергий приводимых масс, движущихся с разными скоростями. В частности подвижные части навесного оборудования приводятся к точке крепления захвата. За центр приведенной массы неподвижных частей рабочего оборудования и подрессоренной силы тяжести базы принят центр масс трактора, эксплуатационные характеристика расчетных деревьев, в частности жесткость определялась по формулам работы [182] с учетом породы и сбежистости. Жесткости комлей и вершин хлыстов приводились в центры масс комлевой щ и вершинной консолей т2. Приведенные значения жесткостей определялись по выражениямгде С 2-приведенная жесткость вершинной консолиС 2-приведенная жесткость комлевой консоли- 1 В, 1к — длина, соответственно, вершинной и комлевой частей, хв, хкрасстояния от захвата до центра тяжести вершинной и комлевой частей.
При этом деревья рассматриваются как упругие элементы, соединенные между собой параллельно. В этом случае приведенная жесткость пакета равна сумме соответствующих жесткостей отдельных деревьев. В экспериментальной части с целью определения жесткостей С 2, Сг и логарифмических декрементов затухания производились запись затухающих колебаний упругих элементов рабочего оборудования и подвески корпуса трактора. Угловая частота колебаний определялась по выражению= 2я77], где Pi — угловая частота, Т— период колебаний-Жесткость упругого элемента определялась по формуле С, = ЩР? где С ¡—жесткость ьго элемента, тг масса ¡—того элемента, Ргугловая частота затухающих колебаний.
Практическое значение коэффициентов динамичности при расчетах конструкций трудно переоценить. Однако, кроме этого, необходимо знать закономерности изменения динамических усилий, позволяющие производить расчеты систем «хлысты — рабочее оборудование» на резонансные состояния. Б. Г. Гастев [48, 49] исследовал вопросы колебаний пакетов хлыстов при вывозке леса. В работе посвященной теории перевозок древесины в хлыстах, Б. Г. Гастев показал, что пакеты хлыстов приводятся к расчетным схемам, принятым в теории сопротивления материалов. В своих работах он рассмотрел формы и виды динамического воздействия транспортируемых пакетов на подвижной состав с учетом упругости пакетов хлыстов.
З.С.Цофин [50, 51, 52, 53] исследовал характер изменения интенсивности нагрузки от собственного веса хлыстов, перевозимых по лесовозным дорогам, поскольку эта характеристика входит в расчеты при определении изгибающих моментов, моментов инерции сечений и деформации пакетов хлыстов. Далее, исследуя колебания перевозимых лесовозным транспортом хлыстов, З. С. Цофин определял физико — механические характеристики пакетов хлыстов. Особенность названных работ состоит в том, что они рассматривают колебательные характеристики таких конструкций пакетов и таких расчетных схем, которые характерны для вывозки хлыстов. В частности, расстояние между опорами пакетов берется в пределах 10−15 мрассматриваются расчетные схемы на более чем двух опорах. Иногда при укладке хлыстов вразнокомелицу, а в некоторых случаях с пренебрежением в расчетах консолями. Полученные результаты могут быть учтены в дальнейшем для исследования вертикальной динамики лесовозного транспорта. Учет специфики лесных грузов при динамических расчетах уже доказанная необходимость. Этому вопросу посвящены работы, связанные с валкой, трелевкой, погрузкой, обрезкой сучьев [55, 56, 57, 58 59, 60, 61, 62, 63] и при вывозке хлыстов лесовозным подвижным составом.
Так в работах [57, 60, 61] отмечено, что на устойчивость движения машин влияют: характеристика подвесок, микрорельеф поверхности пути, параметры упругости груза и др. В зависимости от назначения машины и ее конструкции влияние этих факторов может по — разному сказываться на ее колебаниях и устойчивости при движении. Также рассмотрены вопросы динамики лесотранспортных машин при размещении пакета хлыстов поперек их оси, для которых, в отличие от машин с продольным расположением хлыстов (где рассматриваются параметры кручения пакетов) должны учитываться колебания консолей, зависящие от упругости хлыстов и конструкции машины. Эти колебания имеют характер вертикальных и продольно — угловых перемещений масс пакета, которые сильно влияют на продольную устойчивость машины с короткой базой. В этих работах составлена расчетная схема продольно — угловых колебаний челюстного погрузчика с полужестким ходовым устройством, где масса пакета хлыстов распределена на три равные дискретные массы. Выведены дифференциальные уравнения, из которых после преобразования получены амплитудно — частотные характеристики (АЧХ) системы. Из этих характеристик видно что при некоторых значениях частот колебаний системы, кривая АЧХ имеет два явно выраженных максимума, что объясняется наличием упругих элементов в динамической системе — хлысты и рабочее оборудование с подвеской. По приведенным графикам можно подобрать оптимальные значения жесткости пакета хлыстов для заданных условий движения. Проведенный в этих работах анализ показывает, что динамика машины в сильной степени зависит от места захвата хлыстов по длине [66]. Некоторый сдвиг хлыстов в направлении их комлевой части улучшает динамические показатели. Жесткость пакетов хлыстов при изгибе оказывает существенное влияние на динамику лесотранспортных систем. Однако при определенном соотношении параметров лесотранспортных систем и пакетов хлыстов коэффициент динамичности может быть снижен.
В инженерной практике чаще всего приходится сталкиваться с вынужденными колебаниями при воздействии периодических возмущающих усилий, или с деформациями от ударных импульсов, а также произвольных возмущающих сил. Свободные колебания сами по себе мало интересны, тем более, что в реальных условиях они быстро затухают. Но во всех случаях исследования колебательной системы начинается с изучения свободных (собственных) колебаний [67, 68]. Это объясняется тем, что такой порядок позволяет глубже понять сущность явлений при колебаниях, так как сложные виды движения, в частности вынужденные колебания, физически связаны с собственными и для их изучения необходимо во всех случаях предварительное определение частот собственных колебаний.
Исследование собственных колебаний стволов деревьев, хлыстовпроводилось рядом авторов в связи с изучением валочных, валочно-пакетирующих, валочно-трелевочных машин. При этом определялись частоты колебаний ствола дерева в полупогруженном состоянии, динамические усилия на манипулятор от поперечных колебаний ствола дерева или хлыста [68, 69,70,71,72,73,74,75].
В работах Ю. И. Верхова [12, 65, 66, 76], посвященных динамическим взаимодействиям рабочего оборудования колесных погрузчиков с лесными грузами доказано, что влияние гибкого груза на динамические нагрузки значительно. В разной степени это влияние сказывается на отдельные узлы погрузчиков, при этом также отмечается, что наиболее нагруженными являются элементы конструкций непосредственным образом прилегающие к грузозахватному органу.
В работе Ю. В. Верхова [12] при расчетах лесных погрузочно-транспортных машин длинномерный груз (хлысты) рассмотрен как груз с распределенными параметрами. Изгибные колебания груза консольных частей хлыстов описаны дифференциальным уравнением поперечных колебаний с учетом функциональной зависимости момента инерции поперечного сечения от сбежистости хлыстов. Приближением по собственным формам колебаний по методу Фурье получена динамическая модель в наибольшей степени приближенная к реальной схеме закрепления и расположения гибкого груза относительно базовой машины. Далее в работе рассмотрено динамическое взаимодействие элементов динамической системы: опорного массива, и колесного движителя, ПТМ, грузозахватного органа и длинномерных лесных грузов, гидросистемы навесного оборудования. Установлены зависимости между амплитудами, частотными значениями динамических нагрузок в навесном оборудовании и элементах конструкции ПТМ и технологическими, конструктивными, эксплуатационными факторами.
Следует отметить, что все исследования проводились авторами различными методами. Методы определялись задачами и целями поставленными авторами работ. Единой методики, например, по моделированию хлыстов с целью получения многоцелевой модели пригодной как для систем с одной степенью свободы, так и для систем с несколькими степенями нет. То есть нет единого подхода, который бы обеспечил и удовлетворил бы большинство задач, связанных с изучением динамических свойств лесозаготовительной техники. Отсутствие единой методики по представлению хлыстов как гибкого груза в динамических расчетных схемах влечет за собой неоправданные затраты как времени, так и материально — финансовые. Поскольку динамические свойства хлыстов определяют обычно в результате дорогостоящих натурных экспериментов, которые наряду с прочими затратами отвлекают от решения основных задач.
В настоящее время существует подробно разработанная методика определения динамических нагрузок при возмущениях периодического характера [12,45, 48, 58, 67, 76 ] и др. при этом необходимо представлениегибкого груза как подсистемы, которая играет не последнюю роль в формировании динамических нагрузок и которую труднее всего представить на сегодняшний день в виде универсальной модели в связи с многообразием факторов, влияющих на динамические характеристики гибкого груза растительного происхождения.
Малоизученными и перспективными [124] в общем технологическом потоке являются сучкорезное оборудование типа ЛО-69, ЛО-76, сучкорезно-раскряжевочные линии типа ППЛ-4 с гусеничным протаскивающим устройством (ГПУ). Последние широко применяются в Красноярском крае.
Вертикальное расположение гусениц одна над другой и одиночный хлыст, подаваемый под раскряжевку в сочетании с обрезкой сучьев, создают в ГПУ динамические нагрузки, чередующимися с временными спокойными циклами. Большие переменные вибрации, видимые на глаз, колеблющаяся консоль ствола дерева между гусеницами, все это позволяет предположить, что на динамику узлов ГПУ большое влияние оказывает протаскиваемый одиночный хлыст. Отчего страдают несущие элементы конструкции ГПУ, например, в эксплуатируемых ГПУ в Ново-Козульском ЛПХ объединения «Ачинск-Лес» место крепления штока гидроцилиндра подъема верхней гусеницы подвержено постоянному разрушению в виде трещин по основному металлув течении наблюдаемых шести месяцев эксплуатации на ГПУ несколько раз менялись ведущие валы верхней или нижней гусениц из-за их скручивания. Возникновение периодических колебаний всего ГПУ говорит о наличии резонанса или биений, причина возникновения которых не ясна. Наличие резонанса или биений в динамических системах, кроме повышенных деформационных явлений, влечет за собой перерасход энергии, которая неизбежно расходуется на поддержание вредных колебаний.
Индивидуальная обработка круглого леса производится не только на стадии обрезки сучьев или раскроя. Обрабатываются кряжи на корообдирающих станках, особенно ярко динамические характеристики круглых лесоматериалов проявляются при колибровке 4, 6, 8 метровых бревен для придания им правильной цилиндрической формы. На Красноярском лесоперевалочном комбинате в 90-х не был запущен в работу новый калибровочный станок отечественного производства из-за невозможности обрабатывать бревна пихтовые и еловые. Поскольку зажатое с торцов бревно обрабатывалось перемещающейся вдоль бревна фрезерной головкой роторного типа. Кинематическое возмущение от фрезы вызывало резонансные колебания бревна и бревно вырывало из торцовых зажимов. Отстройка собственных частот возмущающих сил от собственных частот колебаний бревен позволило бы исключить резонанс и запустить станок в работу, но для этого необходимо знать динамические характеристики обрабатываемых лесоматериалов.
Обзор исследований динамического взаимодействия круглых гибких лесоматериалов с рабочим оборудованием лесозаготовительных машин показал, что вопросы исследования взаимодействия предмета труда с рабочим оборудованием, при выполнении лесозаготовительными машинами технологических операций являются актуальными. Наряду с широко исследованными лесозаготовительными машинами имеется еще малоизученная область в технологическом процессе — сучкорезно-раскряжевочные линии с ГПУ, в которых наиболее ярко проявляется индивидуальность обработки ствола каждого дерева.
Из обзора видно, что существует несколько методов решения вопроса взаимодействия предмета труда с рабочим оборудованием, и при этом, очевидно, предполагается существование различных методик составления эквивалентных расчетных схем с учетом специфических особенностей предмета труда. К таким особенностям следует отнести, прежде всего, упругие свойства и распределение масс. Влияние этих особенностей на характер взаимодействия предмета труда с рабочим оборудованием рассмотрим в следующих разделах.
1.5.4. Влияние упругости хлыстов на свойства системы «хлысты — рабочее оборудование"При решении задач динамики в различных областях техники приходится сталкиваться с необходимостью определения динамических характеристик систем. Прежде всего определим основные положения из теории динамических систем, которые будут применяться при рассмотрении тех или иных вопросов, связанных с деформацией системы, у которых элементы, составляющие систему, абсолютно жесткие, (предполагаются абсолютно жесткими) и не деформируются при воздействии сил или моментов. Системы, имеющие упругие связи между отдельными жесткими элементами или передающие движение, а так же несущие части машин называются упругимипри это деформации элементов не превышают предела упругости, то есть остаточные деформации отсутствуют [67].
Жесткость, как и масса, является основной динамической характеристикой любой динамической системы, представляющей собой совокупность тел и упругих элементов, которые находятся во взаимной связи друг с другом и при том так, что состояние или расположение одного из элементов системы сказывается на состоянии или расположении других и, таким образом, на свойствах всей системы в целом [80].
Под жесткостью механической системы или ее отдельного элемента понимается отношение нагрузки к вызываемой ею деформации. Динамические характеристики систем принимаются линейными.
В данном разделе рассматриваются вопросы влияния упругих свойств подсистемы в виде специфических лесных грузов (хлыстов) на динамические свойства системы в целом.
Вышеприведенные определения указывают, что изменения любого параметра системы приводит к изменению свойств системы в целом. При исследованиях динамических нагрузок в различных узлах лесозаготовительных машин, в частности машин с поперечным расположением длинномерного груза, для упрощения расчетных схем исследователи прибегают к наиболее распространенному способу упрощения — приведению масс, жесткостей, моментов инерций. Так в работах, посвященных исследованиям динамических нагрузок в рабочем оборудовании, гидросистеме, а также ходовой части лесопогрузчиков, исследованиях колебаний древесного ствола при обрезке сучьев на сучкорезной машине с «рубящим полем» и др. исследованиях [55,79], жесткость хлыстов определяется при помощи формулы, выводимой из классической формулы определения собственной частоты колебаний системы с одной степенью свободыС = (2я/)2-М, (1.5)где с — приведенная жесткость хлыстов, н/см-f — собственная частота колебаний хлыстов, определенная экспериментальным путем, гц-ш — масса одной из частей хлыстов (вершинной, комлевой, или хлыста в целом, кг.
По своей простоте метод приведения по формуле (1.5) намного облегчает решение задач исследования динамических систем с конечным числом степеней свободы (одна, две, три). Однако, при определении жесткости хлыстов экспериментальным путем, нами было замечено, что реальная жесткость хлыстов отличается от жесткости, получаемой по формуле (1.5). Ниже нами дается теоретическое объяснение физической сущности явления, определяющего различие в численных значениях жесткостей, а также влияние этих различий на свойства динамической системы в целом. Объяснение базируется на фундаментальных исследованиях в области теории колебаний.
На рис. 1.1 (а, б, в) приведены три расчетные схемы, которые соответствуют следующим расчетным случаям: — на схеме «а» показана масса, ть установленная на упругом элементе с жесткостью с^- схеме «б» соответствует сосредоточенная масса Ш2 на упругом элементе в виде балки, которая считается невесомой, жесткость балки С2 и длина 1— х) схеме «в» соответствует цилиндрическая балка с распределенной массой т3=т01,где т0 — погонная масса. X + СО XО, (1.6)где х — перемещение массы — со — круговая частота. Не трудно убедиться, что если С1=С2 и т1=т2,то собственную частоту обеих систем определим из формулы, 1 /чГ/1.2=— 4/— > (1.7)2 кт1,2то есть жесткость С^С2(2л:/)гщ 7.
Следовательно системы «а» и «б» эквивалентны и мы можем, рассматривая схему «в» с распределенными параметрами, обращаться к любой из этих схем для сравнения или для упрощения. Вернувшись к схеме «в» с распределенными параметрами, мы можем точным методом, известным из теории колебаний систем с распределенными параметрами, определить собственную частоту колебаний [81 82 83 84 85 86]/з =а2 кЕ Iт1(1.8)где fз — частота собственных колебаний балки, гц-ЛЕ — модуль упругости материала балки, н/м — I — момент инерции поперечного сечения, м4-акорень соответствующего трансцендентного уравнения частот, зависящий от граничных условий закрепления балки [81, 82, 83, 110, 123].
Сравним формулы (1.7) и (1.8)к 2Рассматривая системы «а» и «б», можно определить, что движение этих систем с одной степенью свободы при свободных колебаниях описывается одним и тем же уравнением [68]кг =С, игЗЕ14 т12л Ак 1т1,2(1.9)/з2 =а 4 Е I4 я 21А т (1.10)х) для упрощения выкладок в примере взят не реальный хлыст со сбежистостью, а цилиндрическая балкадальнейшие выкладки будут вестись только с учетом особенностей хлыстовпреобразуем формулу (1.10) заменив, а и1 следующим образома4=3п, 14=Ы3, подставим значение (1.11) в формулу (1.10)2 ЪЕЗпJ3 =4л2131т,(1.11)(1.12)В формуле (1.12) 1ш0=шз, записать в таком виде// =3 EJ— с, 1,2 >тогда выражение (1.12) мы можемслп 4 тг2т, п (1.13)Из выражения (1.13) видно, что при т,=т2=тз частота собственных колебаний системы с распределенными параметрами будет Вл/яраз больше, чем систем «а» и «б» с сосредоточенными массами. Следовательно, системы «б» и «в» (рис. 1.5) при равных массах Ш2=Шз не эквивалентны в частотном отношении. Для эквивалентности этих систем необходимо произвести приведение массы Шз=т01 на основе равенства кинетических энергий этих систем к концу консольной балки. Используя выражение (1.13) можно пойти другим путем: получив значения частоты fз экспериментальным путем, перейдем к системе «а» или «б», которые эквивалентны. Для этого мы должны в схеме «б» получить илисосредоточенную массут. или, оставив массу такой же, увеличитьжесткость в п раз, что и происходит при применении формулы (1.5). Таким образом получив экспериментально частоту свободных колебаний балки с распределенными параметрами, исследователи в работах [55,78,79] получают жесткость по формуле (1.5), соответствующую системе с сосредоточенной массой. Но далее, решая задачу динамики, принимают, что и в расчетной схеме (например, схема «а», рис. 1.1) сохраняется частота Т3, полученная экспериментальным путем, а также сохраняется значение массы. На первый взгляд все выглядит логичным: системам с сосредоточенными массами, для того чтобы сохранить частоту (так как приведение производится на основе равенства частот) необходимо увеличить свою жесткость в п раз, сохранив сосредоточенную массу, равную распределенной, таким образом исследователи получают систему «а» на упругом элементе, жесткость которого в п раз больше жесткости реальной системы с распределенными параметрами.
Частота собственных колебаний системы (рис. 1.2) с жесткостью с2 будет иметь следующие значения: ki=5.13 с'1, k2=27.37cl. А с жесткостью с2', k,=10.53 с" 1 k2=28.97c1.
Для наименьшей и наиболее опасной частоты kt разница получается более чем в два раза. При расчете на резонансные состояния такая ошибка в определении собственной частоты динамической системы будет способствовать занижению действительных значений амплитуд вынужденных колебаний системы, так как различие в частотах вынужденных колебаний и собственных частот в пределах 12 — 25% обеспечивает работу системы вне резонанса[68, 88].
Приведенный расчет показывает, что использование разных моделей хлыстов при расчетах частотных характеристик самой простой динамической системы, дает значительное расхождение в частотах собственных колебаний системы.
Очевидно, что для динамических систем в которых превалируют вертикальные колебания необходимо избегать обезличивания упругойподсистемы, каковой являются хлысты. Необходим индивидуальный подход с учетом специфики хлыстов: сбежистости, распределения массы по длине, учет модуля упругости древесины (породы) и особенностей динамических систем.
1.6. Выводы по главеОбзор литературных источников показал, что : — технология основанная на хлыстовой вывозке древесного сырья в нашей стране является традиционной. Сортиментная заготовка, как альтернативная (конкурирующая) технология развивается в соответствии с природно-производственными условиями лесозаготовительных зон и зависит от наличия высокопроизводительных комплексов оборудования для лесосечных работ, глубины переработки древесного сырья, концентрации перерабатывающих химико-механических производств, развитости автодорожной сети и объемов заготовок предприятий— технология основанная на вывозке деревьев и хлыстов предусматривает первичную переработку древесного сырья на нижних складах при помощи автоматизированных раскряжевочных линий с применением автоматической оптимизации раскряжевки или, на ранних стадиях автоматизации, в режиме «Советчик» с применением карт раскроя, составленных для данной породы и конкретной лесозаготовительной зоны— моделирование технологического процесса лесозаготовительных работ получило в последние годы широкое развитие с применением методов оптимизации технико-экономических и отдельных технических параметров. В частности разработаны схемы оптимизации вместимостей складов древесного сырья и лесопродукции, компоновки систем лесосечных машин и лесообрабатывающих линий, транспортных операций. Основой моделирования технологических процессов является аппарат теории вероятностей, математической статистики, теории надежности, имитационное моделирование в сочетании с непосредственными наблюдениями и измерениями размерно-качественных характеристик предмета труда, параметров потоков древесного сырья в производственных условиях— в последние годы созданы предпосылки для создания автоматизированных технологических комплексов на основе развития теории метода многоуровневого синтеза технологических структур, теории выбора и принятия решений и методов дискретного программирования. Разработан метод поэтапного многокритериального синтеза технологической структуры первичной обработки древесины и структуры устройств автоматизации измерения геометрических размеровдревесины для системы раскроя, сортировки, учета хлыстов и круглых лесоматериалов, управления поточными линиями и установками-в ряде работ созданы теоретические основы рассредоточения пакета хлыстов и бревен, определены основные параметры многорядных и винтовых буферных устройств, приведены теоретические основы проектирования механизмов питания, с динамическим анализом разрешающей способности узлов передачи. изучению размерно-качественных характеристик предмета труда первичной переработки древесины посвящено большое количество работ, достигнуты результаты, которые уже на данном этапе технического развития лесопромышленного комплекса используются в практике. Создана теоретическая база автоматического контроля за качеством продукции. Исследования размерно-качественных характеристик предмета труда показали, что это не отьемлемая часть комплекса задач, при широкой автоматизации технологического процессанепосредственно исполнительным технологиям и оборудованию лесозаготовительных предприятий также посвящено значительное число работ, которые решают частные вопросы: для линий с поперечной подачей решается проблема расстановки пил, проблема заклинивания пильных дисков при раскряжевке, проблемы компоновки линий на базы существующих агрегатов и блоков-перемещения являются основой технологических операций, которые подразделяются на вспомогательные, размернокачественно — формирующие, а также перемещения формирующие качественные показатели продукта труда (сортиментов)-при исследованиях раскряжевочных линий и потоков в основном охватываются узконаправленные аспекты проблемы, отсутствует комплексный подход при решении технологических и конструктивных задач-«узким местом» в установках с поперечным перемещением хлыста, несмотря на многочисленные исследования было и остается заклинивание пильных дисков при раскряжевке хлыстов. Подтверждением этому служит последняя линия с поперечной подачей рекомендованная к серийному производству — ЛО-Ю5. В состав которой входят выдвижные пильные блоки, предназначенные для поперечной распиловки и вывода пил из пропила при заклинивании пильного дискаНе окончательно решен вопрос физической сущности заклинивания пильных дисков. малоизученной областью остаются упругие и другие характеристики предмета труда, активно взаимодействующего с рабочим оборудованием. Отсутствует общий подход в составлении эквивалентных расчетных динамических схем хлыстов при различных схемах закрепленияза предшествующий период научно-технического развития отрасли было создано более 20 типов раскряжевочных автоматизированных поточных линий с поперечной подачей хлыстов типа «слешер», «триммер». Все поточные линии единичного исполнения, при этом наблюдается полное отсутствие унифицированных узлов и агрегатоввсе линии, изготовленные и внедренные в производство имеют ограниченную программируемость раскряжевки, ведущую к снижению выхода деловой древесины и качества продукта труданет методов формализации структурно-кинематических схем технологических потоков на стадии проектированияпоточные линии представляют собой ряд последовательных агрегатов, совершающих элементарные переместительные операции. То есть слабо используются совмещения перемещений в пространстве для сокращения циклов технологических операций и сокращения числа агрегатов, составляющих поточные линии-не разработаны формализованные методы структурного анализа и кинематической совмещенности смежных агрегатов и поточных линий в целом-нет формализованных методов синтеза перспективных исполнительных технологических агрегатов и потоков, отсутствуют формализованные методы расстановки пил в многопильных раскряжевочных линиях в соответствии с разработанными рядом авторов рекомендациями по автоматической оптимизации раскряжевки-в поточных линиях для первичной переработки древесины используются в основном высокопроизводительные круглопильные раскряжевочные агрегаты различных типов: балансирные, и маятниковыекоторые в свою очередь подразделяются на пильные агрегаты: а) ось вращения пильного диска располагается над плоскостью перемещения предмета трудаб) ось вращения пильного диска располагается под плоскостью перемещения хлыстов. Т. е. пильные агрегаты с верхним и нижним положением пильного диска. При этом не обнаружено рекомендаций по применимости вышеуказанных агрегатов в процессе проектирования и выбора технологических схем линий для первичной обработки древесины.
1.7.Цель и задачи исследованийВ основу исследований в настоящей работе положен системный подход, который в отличие от классического (индуктивного) подхода предполагает последовательный переход от общего к частному, когда в основе рассмотрения лежит цель, причем исследуемый объект выделяется из окружающей среды [142]. При этом система 8 — целенаправленное множество взаимосвязанных элементов любой природы. Внешняя среда Е — множество существующих вне системы элементов любой природы, оказывающих влияние на систему или находящихся под ее воздействием.
При системном подходе к моделированию систем определяется четко цель моделирования. Поскольку невозможно полностью смоделировать реально функционирующую систему (систему — оригинал или первую систему), создается модель (система — модель или вторая система) под поставленную проблему. Таким образом, применительно к вопросам моделирования цель возникает из требуемых задач моделирования, что позволяет подойти к выбору критерия и оценить, какие элементы войдут в создаваемую модель М. Важным для системного подхода является определение структуры системы — совокупность связей между элементами системы, отражающую их взаимодействие [140, 141, 142, 195]. Структура системы может изучаться извне, с точки зрения состава отдельных подсистем и отношений между ними, а также изнутри, когда анализируются отдельные свойства, позволяющие системе достигать заданной цели, то есть когда изучаются функции системы.
При структурном подходе выявляются состав выделенных элементов системы 8 и связи между ними. Совокупность элементов и связей между ними позволяют судить о структуре системы. Последняя в зависимости от цели исследования может быть описана на разных уровнях рассмотрения. Наиболее общее описание структуры — это топологическое описание, позволяющее определить в самых общих понятиях составные части системы и хорошо формализуемые на базе теории графов.
На основе исходных данных Д, которые известны из анализа литературных источников, ограничений, которые накладываются на систему сверху либо исходя из возможностей ее реализации и на основе цели функционирования Ц формулируются исходные требования Т к модели М, на базе этих требований формируются ориентировочно некоторые подсистемы П, элементы Э и осуществляется наиболее сложный этап синтеза выбор В составляющих системы, для чего используются специальные критерии выбора КВ.
Составляющая этапа Д (исходные данные) на основании анализа литературных источников подразделяются на Д1 и Д2: Д1 — исходные данные удовлетворяющие своей полнотой на начальном этапе выбора требований-Д2 — неполные исходные данные, требующие дополнительных исследований или теоретического обоснования. К Д1 относятся следующие исходные данные: а) перемещения — основа технологии первичной обработки древесины-б) элементарные перемещения по одной координате — преобладающий тип перемещений в существующих технологических потоках-в) размерно — качественные характеристики предмета труда — основные характеристики для обеспечения программного раскроя-г) строгая последовательность выполнения операций — основополагающий принцип технологии первичной обработки хлыстов.
К Д2 относятся: динамические характеристики предмета труда (хлыстов), которые активно влияют на технологический процесс поперечного раскроя, но недостаточно исследованы вопросы взаимодействия хлыстов с исполнительным оборудованием.
Составляющие этапа Т (требования) получены также на основании анализа литературных источников и производственного опыта и формулируются в соответствии с исходными данными):а) максимально использовать преимущества совмещения перемещений по нескольким координатам-б) обеспечить беззажимное пиление при поперечном раскрое-в) синтезированные технологические структуры должны обеспечивать программный раскрой-г) обеспечить относительно плавное наращивание производительности синтезированных структур из расчета 50 — 80 м древесины в смену на одну пилу-д) обеспечить возможность агрегатно — блочной компоновки технологических структур-е) перемещения, структура потоков, структурный синтез должны быть формализованы на единой теоретической базе.
Этап П (подсистемы) формируется при предварительном анализе по обезличенным по оборудованию перемещениям: а) подсистема разобщения, подачи, ориентации, которая может состоять из одного, двух, трех перемещений-б) подсистема по перемещению, количеству пильных агрегатов и типу пильных агрегатов-в) подсистема удаления продукта труда из зоны раскряжевки с сортировкой, подсортировкой и без таковых.
Остальные этапы Э (элементы), В (выбор), М (моделирование) решаются после выбора теоретической базы для описания перемещений в процессе выполнения технологических операций, после создания формализованных методов моделирования технологического процесса, формализации и проведения структурного анализа.
Таким образом, целью работы является создание теоретических основ моделирования, структурного анализа и синтеза технологических структур для первичной обработки древесного сырья. В целом необходимо решитьпроблему, заключающуюся в разработке теоретической базы для анализа существующих и синтеза перспективных технологий с расширенными функциональными возможностями, отвечающих принципам ресурсосбережения, однотипности оборудования и возможности агрегатноблочного принципа развития технологических исполнительных схем.
Для достижения поставленной цели необходимо решить следующие задачи:• Разработать теоретически обоснованные модели предмета труда (хлыстов), отображающие с достаточной степенью точности реальный процесс взаимодействия с рабочим оборудованием при продольном и поперечном перемещениях.• Определить закономерность замещения распределенных масс подсистемы «хлысты «дискретными массами в эквивалентных расчетных схемах.• Теоретически обосновать определение упругих характеристик хлыстов с учетом сбежистости, породы и наложенных связей.• Провести теоретические исследования процесса взаимодействия хлыстов с пильными агрегатами поточных линий в процессе раскряжевки с целью определения применимости существующих компоновочных схем в синтезируемых структурах.• Осуществить экспериментальную проверку разработанных теоретических положений по моделированию предмета труда (хлыстов), активно взаимодействующего с исполнительным оборудованием.• Разработать формализованный метод структурно — кинематического анализа поточных линий и установок для первичной обработки древесины.• Разработать формализованный метод моделирования технологических процессов первичной обработки древесины.• Провести структурный анализ существующих поточных линий и оригинального оборудования с целью определения предпочтительных принципов выполнения технологических операций.• Разработать формализованный принцип синтеза технологических структур для первичной обработки хлыстов.• Провести имитационное моделирование некоторых синтезированных технологических структур с целью выявления их функциональных возможностей.
2.МОДЕЛИРОВАНИЕ ХЛЫСТОВ КАКДИНАМИЧЕСКОЙ ПОДСИСТЕМЫ СРАСПРЕДЕЛЕННЫМИ ПАРАМЕТРАМИ2 Л. Особенности взаимодействия предмета труда первичной обработки древесины с технологическим оборудованиемПредмет труда первичной обработки древесного сырья (хлысты) до основной азмерно — качественно — формирующей операции (раскряжевки) представляет собой пругое тело со специфическими геометрическими характеристиками: ачительная длина (15−35 м) различные диаметры комля, вершин, срединной части, азнопородность и др., которые на сегодняшний день довольно хорошо изучены, оскольку хлыст не является жестким телом, то он обладает своей жесткостью одатливостью), частотными характеристиками (зависящими от распределения асс, сбежистости, породы, удерживающих связей, жесткости этих связей и собенностей силовых воздействий рабочего оборудования).
2.2.Определение упругих характеристик хлыстов применительно к переместительным операциям технологии первичной обработки древесного сырьяРасчетные схемы для определения жесткости одиночныххлыстовПредварительные эксперименты показали, что при любых усилиях зажима диночного хлыста, например, в челюстном захвате лесопогрузчика без блокировки едней зажатой части исключаются вертикальные перемещения хлыстов над порами, но всегда остаются угловые перемещения. Для пакетов хлыстов при ольших усилиях зажима хлысты блокируют друг друга, при этом жесткость локированной части на расстоянии до 3 метров становится настолько большой, что ожно сделать допущение об исключении для пакетов хлыстов угловых и ертикальных перемещений. Решение этого вопроса имеет важное значение при определении условий крепления балок (хлыстов) в челюстях захвата лесопогрузчиков, сучкорезных ашин, слешерных линий и др., которые определяют тип расчетной схемы. То есть ожно рассматривать свободно лежащий на опорах хлыст и хлыст с условно есткой заделкой, которая исключает как вертикальные, так и угловые перемещения заделке.
Из вышесказанного можно сделать следующие выводы :1.При колебания свободно лежащего хлыста ограничиваются вертикальные перемещения, но имеются угловые перемещения.
2.В колебаниях при возбуждении комля или вершины свободно лежащего хлыста участвует не только консольная часть, но и часть хлыста расположенная между опор.
3.Блокирование зажимаемой части хлыста исключает угловые и вертикальные перемещения в заделке. сходя из сделанных выводов, принимаем следующие расчетные схемы:-хлыст на двух опорах, исключены вертикальные перемещения относительно опор (в заделке) и возможны угловые. Определение жесткости комлевой и вершинной частей хлыста (рис. 2.1а) —хлыст на двух опорах, исключены вертикальные и угловые перемещения относительно опор (в заделке) путем исключения из колебаний части хлыста между опорами (рис. 2.16). Определение жесткости вершины и комля.
Таким образом наши расчетные схемы в совокупности являются универсальными.
Определение жесткости консольной комлевой части одиночных хлыстовВ соответствии со схемой (рис. 2.2) определяем жесткость комлевой части хлыста, которая определится из следующего известного в прикладной динамике соотношениягде Сжесткость хлыста, Н/мР -сила, под действием которой деформируется хлыст, Н/мУпрогиб (деформация) комлевой или вершинной части хлыста под действием силы Р, м.
Прогиб определяется с учетом сбежистости хлыста и в соответствии с принятой расчетной схемой на рис. 2.2. Сбежистость хлыста будем определять отдельно для комлевой и вершинной консоли, так как по исследованиям Анучина П. Щ98] ствол возможно представить как тело, состоящее из различных конусообразных тел. Согласно схеме, предлагаемой ввышеуказанной работе и во многих работах других авторов, ствол дерева имеет границу резкого изменения сбежистости в середине ствола.
Рисунок 2.2.Расчетная схема к определению жесткости комлевой част хлыста.
Опорные реакции, А и В здесь будут равныл = рф-а+Г) в Р (а-Ь+Г)II (2.23)рогиб точки К, точки расположения центра тяжести хлыста будет равенди с МЩдРУск+ |МШ-ск+ [• — - JМШсЬс.(2.24)(а) ½Щх^ ?}2Щх$р ?Щх^дрНе трудно заметить, что равенство (2.24) состоит из интегралов (2.10) и (2.20), оторые определяют жесткость комлевой и вершинной частей хлыста ответственно. Следовательно, наши выкладки по определению жесткости хлыста в елом согласуются с данными [14, 45, 87] и общая жесткость хлыста запишется ким образомС0бщ= ск+ Св (2.25)де С0бщ — жесткость хлыста в целом, Н/м-Ск — жесткость комлевой части хлыста, Н/м-Св — жесткость вершинной части хлыста, Н/мЗажатый хлыст с исключением угловых перемещений (рис. 2.1,6) является частным случаем предыдущих схем, только внутренняя часть (часть хлыста между опорами) в этом случае блокирована и не имеет возможности деформироваться (изгибаться), то есть отсутствуют угловые перемещения части хлыста между опор. Жесткость будет вычисляться по интегралам (2.10) и (2.20) только с исключением интеграла берущегося по (по расстоянию между опор).
2.3.Теоретическое обоснование динамических эквивалентных расчетных схем хлыстов применительно к технологическому процессу первичной обработкидревесного сырьяРасчетные эквивалентные схемы хлыстовРассмотрим хлыст имеющий массу т, центр тяжести (ц.т.) которого расположен ад опорой, А (рис. 2.5). Если рассматривать его как жесткое тело, то при колебаниях оры, А динамические усилия, воспринимаемые опорой, будут соответствовать инамическим усилиям возникающим при воздействии на массу ш ускорения У. ели же рассматривать хлыст как упругое тело, то картина несколько усложнится, так к центр тяжести будет совершать вынужденные колебания с частотой и амплитудой оры А, консоли же вершинной и комлевой частей могут иметь амплитудыолебаний опоры А, а также и отличные от амплитуды опоры А, большие или еныиие. То есть все будет зависеть от соотношения собственных частот хлыста и шужденной частоты опоры. Первая в свою очередь зависит от соотношения масс и есткости хлыста. Активные массы, формирующие собственные частоты колебаний эквивалентных расчетных схемах хлыстов (именуемые в дальнейшем риведенными) будем определять на основе равенства кинетических энергий риведенных и реальных масс [67,91]. Приведенные массы будем определять тдельно для вершинных и комлевых частей хлыстов. Под комлевой частью хлыста онимается часть хлыста от ц.т. до комлевого среза с распределенной массой и ежистостью. Аналогично понятие вершинной части.
Для того, чтобы определить дискретные массы замещающей модели, необходимо ать распределение массы по длины хлыста, а также плотность древесины и объем ыста. Для упрощения расчетов определение массы по длине хлыста будем роизводить при следующих допущениях: а) образующую стволов принимаем, как образующую тела вращения (усеченный конус)-б) плотность древесины равномерна по объему той части хлыста, которая рассматривается в данный момент.
Первое допущение связано с понятием образующей ствола [98]. Большинство сследователей для упрощения исходят из предположения, что ствол есть тело ащения [71, 72, 98]. Ошибка в определении объема ствола, принятого за тело ащения не превышает допускаемой при таксации погрешности [98]. Это во-первых, о-вторых, нам понадобится кроме понятия образующей ствола, понятие сбега ствола, ыражая образующую ствола сложными математическими выражениями, мы обязаны такой же точностью описать сбег ствола, что при форме ствола из нескольких тел ащения, описанных разными кривыми, не представляется возможным сделать не азбивая ствол на части.
По исследованиям П. Б. Закревского [113] известно, что фактическая плотность ревесины ели, сосны до 0.4−0.5 высоты равна средней плотности и начинает овышаться к вершине, превышая среднюю плотность на 19−30%. Исследования роведены для сосны и ели, для ели сибирской, пихты, кедра такие исследования не публикованы. За недостаточностью исследований по этому вопросу, примем лотность вершинных частей также равной средней плотности древесины ствола. В связи с нашими допущениями и задачей обратимся к рис. 2.6. асса хлыста будет равнат — Уст, (2.26)е шмасса хлыста, кг-У-объем хлыста, м — сг-плотность (средняя) древесины, кг/м3.
Кинетическая энергия элементарного участка с1х хлыста с массой с1т (х)к будет равна<*ГХ=—1 (2.32)где Ухскорость движения элемента массой ёгп (х) в любом сечении х.
Для того чтобы определить скорость движения Ух необходимо знать перемещение ух. Выражение перемещения для конусной балки имеет сложный вид, например, выражение (2.11). Для упрощения введем понятие эквивалентной балки, которое широко используется в других областях техники, например, в краностроении. Система сложной конфигурации, для которой сложно производить расчеты, заменяется эквивалентной ей балкой постоянного сечения. Из равенства прогибов реальной системы и эквивалентной балки, для данных условий закрепления и нагрузки, определяется момент инерции сечения эквивалентной балки, который затем используется в дальнейших расчетах [93].
Анализируя схемы на рис. 2.7 а, б можно сказать, что условия эквивалентности расчетной схемы реальной соблюдены, т. е. суммы приведенных масс равны реальной массе, кинетическая энергия масс в эквивалентной схеме равна кинетической энергии реальной подсистемы «хлыст».
693.ВЗАИМОДЕЙСТВИЕ ХЛЫСТОВ С РАБОЧИМ ОБОРУДОВАНИЕМ ДЛЯ ПЕРВИЧНОЙ ОБРАБОТКИ ДРЕВЕСНОГО СЫРЬЯ3.1.Продольное перемещение хлыстов: комлевая консоль переменной длиныВ связи с разработкой эквивалентной расчетной схемы хлыстов, которая существенно отличается от предлагаемых для использования ранее различными авторами, необходимо проверить соответствие предлагаемой модели условиям взаимодействия с рабочим оборудованием при различных условиях взаимодействия. К таким факторам при классификации машин мы отнесли: количество хлыстов, активно взаимодействующих с рабочим оборудованиемхарактер возмущающего воздействиярасположение хлыстов (деревьев) относительно рабочих органов базовой машины. Гусеничное протаскивающее устройство (ГПУ) линии ППЛ-4, с точки зрения сочетания факторов, наиболее подходит, при рассмотрении вертикальных колебаний каретки с верхней гусеницей ГПУ и хлыстом, имеем колеблющуюся консоль переменной длины.
Гусеничный движитель (ГД), как таковой широко используется в транспортных машинах (ТМ). Известны работы, посвященные исследованиям ГД как сельскохозяйственных, так и машин общегоназначения. ГПУ имеет много общего с ГД транспортных и сельскохозяйственных машин, но наряду с этим имеется ряд существенных различий, которые коренным образом меняют традиционный подход к решению вопросов, связанных с гусеничным протаскивающим устройством: а) гусеничные обводы ГПУ работают в паре в вертикальной плоскости друг над другом (в транспортных машинах параллельно в горизонтальной)-б) гусеницы ГПУ имеют между собой упругую консоль дерева (гусеницы ТМ несут на себе обычно жесткий, иногда подрессоренный остов машины, обладающий, как правило, большой массой)-в) как следствие первых двух пунктов, нахождение гусениц друг над другом, наличие ствола дерева между ними вызывают сложные вертикальные возмущающие силы (в ТМ машинах такие силы поглощаются грунтом или демпфирующей подвеской). Эти три основных различия и предопределяют задачи исследований, которые могут быть сформулированы следующим образом: — определить влияние упругого элемента (консоль ствола дерева) на динамические нагрузки в ГПУ— определить влияние возмущений от верхней и нижней гусениц (в силу их звенчатости) на динамические нагрузки в ГПУ.
70Рисунок ЗЛ. Схема действующих сил в ГПУ: РЬР2 — силы трения Р4 — силы резания сучьев Р2, Рз — вес верхней гусеницы и хлыста.
Рисунок 3.2.Схема системы «ГПУ — ствол дерева»: ш (х)пр — приведенная переменная масса консоли хлыста, С (х) — переменная жесткость консоли хлыста — Ъ. демпфирующее сопротивление Намплитуда кинематического возмущения.
3.1.1.Расчетные схемы взаимодействия гусеничного протаскивающегоустройства (ГПУ) с хлыстамиПри обрезке сучьев с деревьев в гусеничном протаскивающем устройств (ГПУ) действуют в горизонтальной плоскости следующие внешние силы (рис. 3.1):а) силы трения между копирами сучкорезных ножей и стволом дерева, плюс сила резания сучьев, сумма которых обозначена Рьб) силы трения гусениц верхней и нижней о направляющие, плюссилы трения в кинематических парах приводов, суммы которых для верхней и нижней гусениц обозначена и Бг соответственно.
Реальная система ГПУ во взаимодействии со стволом дерева представляет собой систему с бесконечным числом степеней свободы, так как в реальности нет абсолютно твердых и жестких тел.
Но параметры основных узлов и их элементов в силу различных характеристик могут быть сведены к системам с ограниченным числом степеней свободы. Таким образом может быть достигнуто значительное упрощение решения ряда вопросов динамики. Рассмотрим и обоснуем основные допущения.
Из ряда работ по динамике ГД [99,100] известно, что в силу звенчатости гусеничного обвода, существует кинематическая неравномерность движения гусеничной ленты в вертикальной и горизонтальной плоскостях, которое обусловлено хордальным расположением звеньев гусеницы на ведущем и ведомом колесах[99,100,101]. В связи с этим сделаем следующие допущения: 1. Отрезки гусеничной ленты (рис. 3.1) верхней и нижней гусениц опускаются и поднимаются без провисания, то есть при движении верхней ветви в вертикальной плоскости они рассматриваются как жесткие. Это допущение возможно, так как в теории деталей машин при расчетах цепных передач вводится понятие четырехзвенника, где имеется шатун длиной равный радиусу ведущей звездочки, а ведущая ветвь цепи или гусеницы рассматривается как кривошип [95,101].
2.Гусеницы при протаскивании ствола дерева не отрываются от него, то есть отсутствуют ударные эффекты.
3.Гусеничная лента принимается упруго недеформируемой.
Это допущение приемлемо, так как цепные транспортеры и цепные передачидлиной менее 50 м в расчетах обычно принимаются жесткими в продольномнаправлении [95,101].
Частота этой силы при самом простом взаимодействии (одновременном вхождении в зацепление верхней и нижней ведущих звездочек), а также при равных скоростях движения верхней и нижней гусениц, будет равнагде f — частота возмущающей силы гцVскорость движения гусеницы м/с- ^ - шаг звена гусеницы, м.
Таким образом, динамическая система «дерево — ГПУ» будет состоять из подсистемы с упругим элементом — консоли ствола, которая совершает вертикальные колебания с вынужденной частотой совместно с кареткой и верхней гусеницей. Расчетная схема системы будет состоять из приведенной массы консоли ствола на упругом элементе и массы верхней гусеницы с кареткой (рис. 3.2).
Зная амплитуду и частоту массы т (х)кпр можем определить ускорение исилу инерции действующую на массух = Асо2. (3.7) Силу инерции определим, зная массу т (х)кпр и ускорения движенияРип=м{х)кпрх. (3.8)Такая сила будет возникать при колебаниях консоли ствола дерева под действием кинематического возбуждения, обусловленного звенчатостью гусеничных цепей.
Если преобразовать расчетную схему, заменив консольную невесомую балку с массой т (х)кП11 на сосредоточенную (рис. 3.3), то можно проследить как эта сила будет действовать на ГПУ. Прежде всего об условиях, обеспечивающих работоспособность схемы на рис. 3.3:а) упругие элементы С (х) и демпфирующие сопротивления «работают» только в одном направлении, т. е. при сжатии упругих элементов-б) гусеничные ленты в совокупности с ведущими звездочками рассматриваются как четырехзвенники с шатунами-в) элементы ВВ и СС жесткие, шарнирно — закрепленные опоры, имитирующие находящийся между гусениц ствол дерева.
При этих условиях масса т (х)1?, совершая движение, например, вниз сускорением W воздействует на звездочку нижней гусеницы с силой Рин (3.8), создавая момент Мш на валу нижней гусеницы PlfflRsin cot, где R sincot = а. Через плечо «а» с передаточным отношением i = 1 сила воздействует через ВВ и СС на вал нижней гусеницы, создавая момент сопротивленияMc^-PhhR sin (oHt. (3.9)При аналогичных рассуждениях и движении приведенной массы вверх на валу верхней гусеницы создается момент сопротивленияМСБ= -Рин R sin coBt. (3.10)Однако для того, чтобы определить значение силы инерции от колебаний консоли необходимо иметь численные значения амплитуды возмущающей силы «Н» и частоты возмущения со, которые в реальной ГПУ не однозначны. В литературных источниках данных по определению этих параметров не имеется, поскольку в основном рассматриваются горизонтальные динамические нагрузки.
3.1.2. Определение амплитуды и частоты возмущения системы «ГПУ — ствол дерева «Значение частоты возмущающей силы в реальной установке с течением времени изменяется в силу неравенства скоростей движения верхней и нижней гусениц, которое имеет место в производственных условиях. Различие ва) синфазное движение обеих гусеницодна гусеница в синфазном другая в асинфазном движении-верхняя и нижняя гусеницы в асинфазном движении-Рисунок 3.4.Схемы расположения траков в ГПУ при различном сочетании движений.
77скоростях гусениц обычно невелико. Так в Ново-Козульском ЛПХ Красноярского края были обследованы три стационарных ГПУ, в которых различие в скоростях движения гусениц составило: 4,69%- 3,25%- 4,25% в среднем 4,06%. Вероятно, различие в скоростях имеет место из-за погрешностей в кинематических цепях приводов верхних и нижних гусениц и, немаловажное значение имеет то, что приводы верхней и нижней гусениц индивидуальные. Разность скоростей движения приводит к отставанию одной из гусениц. Во всех трех случаях приведенного примера отставала верхняя гусеница, поэтому в дальнейшем будем считать, что верхняя гусеница имеет меньшую скорость движения. Отставание не может компенсироваться увеличением скорости вращения ротора электродвигателя, так как асинхронные двигатели имеют жесткую характеристику. На практике наблюдается некоторое пробуксовывание верхней гусеницы со сдвигом коры дерева на величину большую чем толщина зацепов гусеницы. То есть происходит скольжение (дрейф) зацепов верхней гусеницы по древесине относительно зацепов нижней гусеницы.
В дальнейшем нам необходимо будет различать сочетания совмещения и расположение зацепов верхней и нижней гусениц относительно друг друга. Для краткости позаимствуем термин из расчетов цепных передач: синфазное движение гусеницы и асинфазное движение гусеницы [101]. Но поскольку у нас в ГПУ ведущая звездочка зубчатая, а натяжное колесо (ведомое) гладкое, то этот термин, если рассматривать движение в горизонтальной плоскости, несколько не подходит, так как относительно гладкого не приводного колеса синфазность и асинфазность движения теряет свой смысл. Но в вертикальной плоскости характер движения гусеницы наиболее четко определяется вышеуказанной терминологией. Поэтому под синфазным движением гусеницы мы понимаем движение гусеничной ленты вверх или вниз (в зависимости от того, какая гусеница рассматривается), когда в отрезке «1» (рис. 3.4а) укладывается целое число п шагов и наоборот, асинфазным движением гусеницы в вертикальной плоскости мы называем движение ленты при числе шагов 1 в отрезке «1» равным п + 1/21, где X — шаг звена гусеницы (рис. 3.4 б). При синфазном движении, то есть когда траки верхней и нижней гусениц расположены как на рис. 3.4 а, частота вхождения зацепов в соприкосновение со стволом дерева с учетом скольжения верхней гусеницы будет изменяться в соответствии с временной диаграммой на рис. 3.5 Где расстояния между вертикальными линиями соответствуют периоду Тв=Ттах верхней гусеницы и Тн=Ттш нижней гусеницы. Линиям двойной длины соответствуют совпадения зацепов верхней и нижней гусениц в вертикальной плоскости. По диаграмме не трудно вычислить значения частоты в гц., которая изменяется в зависимости от времени, начиная с нуля, когда зацепы в начальный момент совпадали. Значения частоты будут повторяться в зависимости от разности скоростей и шага звеньев, то есть череза)1 Гн^? Гз ТмЛТмЛ Т# ^ 1 т*. (е> N Гв «й- /А Рисунок3.5.Диаграмма изменения периодов вхождения в зацепление траков со стволом: асинфазное движение обеих гусеницб- асинфазное движение одной из гусеницв- асинфазное движение обеих гусениц.
Рисунок 3.6.Схема определения амплитуды колебаний ствола дерева и верхней гусеницы с кареткой. т, h h (3.11)АУ Ух-У2'где Товремя, через которое зацепы периодически совпадают — ^ - шаг между зацепамиVI — скорость движения гусеницы (нижней) — У 2 — скорость движения гусеницы (верхней) — ДУ — разность скоростей V] и У2.
Из этой же диаграммы видно, что максимальный период между входом в зацепление будет равенТщах =ТВ — (ТВ-ТН)= Тн. (3.12)Обозначив ТВ-ТН=ЛТ, получим Ттах= ТВ-АТ, минимальное значение Ттш = Т. Минимальному периоду или промежутку времени соответствует максимальная частота с очень малой амплитудой колебаний. В нашем случае интерес представляют низкие частоты, которым соответствуют максимально-возможные перемещения траков в вертикальном направлении, то есть частота с периодомТтах=ТгАТ (3.13)Частными случаями будут движения гусениц с расположением траков как на рис. 3.46,в, где движение будет у одной из гусениц синфазным, а у другой асинфазным. Или у обеих гусениц асинфазное движение.
Не трудно заметить, что циклы повторяются с наиболее характерными частотами. Представляющими интерес частоты будут с периодамиТ1тах=Тв-АТ, (3.14)(3.15)т2тах л. 'Т =Зтах2т.
А Т (3.16)то есть^по формуле (3.16) число зацепов, входящих в зацепление равно четырем, эти зацепы будут чередоваться через 1, У2 и! Л максимального периода. Амплитуда колебаний в смысле пути, проходимого шарниром или зацепом в вертикальном направлении, будет для одного режима постоянной. Это видно из рис. 3.6, где Л-радиус зацепления, Ъ — число зубьев ведущих звездочека = —, (3.17)R =ltZ2 кИз треугольников ОВС, О" В С, АСВ, АС В' определим значения отрезков АС и АС которые соответствуют амплитудам колебаний. АСствола дерева, АС или АС-КАС" каретки в зависимости от характера движения (рис. 3.4 а, б, в). Это максимально возможные амплитуды, которые возникают при движении гусениц без учета различного рода возмущений. Целый ряд амплитуд в зависимости от частоты вхождения в зацепление траков будет иметь меньшие значения, которые не играют решающей роли в нашем случае.
803.1.3.Описание движения одной гусеницы при помощи дифференциальных уравненийДля определения нагрузок определим амплитуды силы возмущения, которые зависят от целого ряда факторов. Вернувшись к рис. 3.1, мы к силам, обозначенным на этом рисунке, должны добавить силы инерции, которые неизбежны при неравномерном движении звеньев гусеничной ленты. Из исследований ГД и цепных передач [99,100,101,102,103,104] известно, что звенчатость цепи или гусеницы являются основными источниками возникновения динамических нагрузок при установившемся движении в горизонтальной и вертикальной плоскостях. Исследование возникновения динамических нагрузок в ГПУ усложняется вертикальным расположением гусениц одна над другой со стволом дерева между ними. Поэтому для начала упростим задачу и определим условия возникновения динамических нагрузок для одной нижней гусеницы с расположенным на ней стволом дерева без активного влияния верхней гусеницы.
Из работ по динамике машин известно, что если механизм содержит движущиеся поступательно и вращающиеся массы, то приведенную массу можно выразить через момент инерции, а момент инерции через массу [67,102]. Массу ствола дерева и массу гусеницы выразим через момент инерции, приведенный к валу ведущей звездочки нижней гусеницы1Н =т Я2 + I] +12,где 1н — приведенный к валу ведущей звездочки нижней гусеницы момент инерции-т — сумма масс дерева и гусеницы, движущихся поступательноII — момент инерции ведущей звездочки-12- момент инерции направляющего колеса. Таким образом мы учли вращающиеся и движущиеся поступательно массы нижней гусеницы и лежащего на ней ствола дерева в горизонтальной плоскости.
Общий момент инерции, приведенный к обобщенной координате будет равен (3.18)1 = 11+12 + тЯ2. (3.18)Вертикальная и горизонтальная скорости перемещения звеньев гусеницы будут равныУу=сдЯ<$>таЛ, Ух=соЯсо^Ш1 (3.19)где Уу — вертикальная составляющая скорости движения звена гусеницы, м/с-Ух — горизонтальная составляющая скорости движениягусеницы, м/с — со — угловая скорость вращения ведущей звездочки, с" 1- Ирадиус зацепления, м-Рисунок3.7.Расчетная схема нижней гусеницы: Сфжесткость нижнего приводного вала сон-угловая скорость нижней ведущей звездочки, Мс сопротивление от протаскивания ствола Ускорость нижней гусеницы 1" — приведенный момент инерции.
Рисунок 3−8 (.Расчетная схема верхней и нижней гусениц821 — текущее время.
Ускорение ствола дерева и каретки с верхней гусеницей в вертикальной плоскости будет равно? К ?—^ = со211со$М. (3.20)ШПри определении упругих элементов будем исходить из допущения, что гусеница ГПУ является абсолютно жестким элементом. Для систем с вращающимися массами приведенная угловая жесткость определяется как отношение приведенного момента к угловой жесткости, то естьМпр (3.21)9где Сер — угловая жесткость ведущего вала, нм/радМпрприведенный момент от нагрузок, действующих на вал, нм-(р — угловая деформация ведущего вала, рад.
При наличии в кинематической цепи редуктора необходимо сделать приведение жесткостей валов редуктора к ведущему валу гусеницы ГПУ по формуле [67]с" =-—2—-. (3.22)1е а7Г±7Г- +.где Спр — приведенная жесткость валов редуктора к ведущему валу-С1 С2 — угловые жесткости валов редуктора- 11,12 — предаточные числа между ступенями редукторат}1,г|2 — коэффициент полезного действия ступеней редуктора. Эквивалентную динамическую схему нижней гусеницы, а также верхней гусеницы мы можем представить в виде системы с одной степенью свободы (рис. 3.7). Эта схема представляет собой приведенные массы по одну сторону от ведущего вала нижней гусеницывращающиеся массы редуктора, ротора электродвигателя мы не учитываем, поскольку сумма их масс намного меньше масс каретки с гусеницей, ствола дерева, направляющих колес и ведущих звездочек.
На схеме (рис. 3.7) на ведомую массу действует момент сопротивления, который включает в себя сопротивления от сил трения и сил резания сучьев. Применив энергетический метод Лагранжа с подстановкой значенийаг а/7 д (р' дф* д<�рд dtггКд (р.дТ дП л н—= О (3.23)д (р дфПодставив в правую часть момент сопротивления от срезания сучьев и момент сопротивления от сил инерции, действующие на массу дерева и ведущий вал через плечо «а «равное ЫзтсМ, получим уравнение движения системы в следующем виде<РгI (щ —<р2)С = -Мс - mco2R2 cos cot sin cotdt2(3.24)где/приведенный суммарный момент инерции всех вращающихся и поступательно движущихся массq> i — изменение угла поворота вала ведущей звездочки, равное cot-ср2 — суммарное изменение угла поворота ведущей звездочки включающее в себя упругую деформацию вала-2 7Гt — текущее время (период зацепления Т = —)-О) Zm — сумма масс ствола дерева и массы гусеницы, движущейся поступательно.
В правой части уравнения (3.24) второй член представляет собой периодически изменяющийся момент в течении времени t, проявляющийся при действии на массы ускорений в вертикальной плоскости. Ускорения возникают вследствии неравномерного движения звеньев гусеницы. Первый член правой части — момент сопротивления от сил срезания сучьев и сил трения.
3.1.4.Деформации ведущих валов привода при взаимодействии ствола деревас верхней и нижней гусеницамиПри протаскивании ствола дерева через сучкорезную головку без прижима к нижней гусенице не обеспечивается необходимое сцепление ствола с зацепами. Поэтому для прижима ствола, а также для разгрузки нижней гусеницы применяется верхняя с индивидуальным приводом. Из практики исследований сельскохозяйственных и транспортных гусеничных машин известно, что распределение нагрузок на гусеницы машин неравномерно. Так при исследованиях сельскохозяйственных тракторов [99,104] при прямолинейном движении нагрузки на каждую гусеницу на пути 1−2 м изменяются на 20−50%. Аналогичное явление наблюдается и в ГПУ, имеющее более ярко выраженный характер в силу индивидуальности приводов, а также кинематических погрешностей, которые проявляются в виде разности скоростей перемещения гусениц. Указанные причины являютсяглавными при неравномерном распределении нагрузок верхней и нижней гусениц.
84Перераспределение нагрузок достигает 100%. Это обстоятельство позволяет нам в расчетах принимать нижнюю гусеницу за ведущее звено, на которое передается воздействие верхней гусеницы в виде гармонических возмущений. При исследовании взаимодействия верхней и нижней гусениц со стволом дерева необходимо учесть следующее: при совместной работе верхней и нижней гусениц со скоростями отличающимися на малую величину AV, наблюдается пробуксовывание траков верхней гусеницы по древесине. Это немаловажное обстоятельство позволяет сделать следующие выводы: а) наличие систематического пробуксовывания верхних траков в горизонтальной плоскости не позволяет рассматривать верхнюю и нижнюю гусеницы как единую динамическую систему-б) пробуксовывание верхней гусеницы исключает взаимное влияние верхней и нижней гусениц в горизонтальной плоскости, так как деформируется наиболее податливое звено в этой системе — кора дерева.
Для верхней гусеницы, которая при распределении нагрузки не воспринимает сопротивлений от срезания сучьев, получимIiba2(<�он,<�ов — угловая скорость нижней и верхней ведущих звездочек.
4. «2 + РФ 2 =dvIДля первого частного случая имеем при t = Оd2<P-> Л л-$¦ = 0. 1Для второго — четвертого частных случаев решение ищем в виде (р2 = +i? COSДифференцируя дважды имеем, 2. п 2 —^-=-Асой smcot-Вю costo"/.
Для нижней гусеницы по уравнению (3.28) имеем883.1.5.Амплитуды и период колебаний при биениях в системе «ГПУ — ствол дерева» Определив силы, которые в данном случае являются возмущающими силами, воздействующими на ствол дерева между верхней и нижней гусеницами, мы должны учесть то, что в вертикальной плоскости действуют две возмущающие силы. Эти силы воздействуют на ствол дерева с частотами 6) Hz u) ez—— и —— весьма близкими друг к другу. 2 п 2 пЗдесь мы сталкиваемся с одним из нежелательных явлений в техникебиениями. В транспортных машинах (ТМ), цепных передачах, цепных транспортерах гибкий тяговый орган, а также всю динамическую систему исследуют на резонансные состояния с целью отстройки собственных частот колебаний от частот кинематического возбуждения. Расположение гусениц одна над другой и наличие незначительной разности в скоростях движения гусениц, вызывают явление, которое требует такого же внимания как и резонанс. Рассмотрим механизм появления биений в ГПУ.
2.При исследованиях ГПУ необходимо учитывать специфику кинематической схемы ГПУрасположение гусениц в вертикальной плоскости и наличие между ними ствола дерева, что является причиной усложнения динамических явлений в данной схеме.
3.Теоретические исследования динамики ГПУ возможно вести на основе дифференциальных уравнений, теории цепных передач и гусеничных движителей. Однако, при этом необходимо учесть сложности взаимодействия верхней и нижней гусениц через промежуточное звено, каковым является ствол дерева, путем введения в уравнения дополнительных инерционных сил от вертикальных перемещений каретки с гусеничной лентой как от воздействия нижней гусеницы, так и от воздействия индивидуального привода верхней гусеницы и колебаний консоли ствола между гусениц.
4.Теоретические исследования показали, что наличие двух индивидуальных приводов верхней и нижней гусениц, обладающих в силу своей звенчатости неравномерностью движения, наличие незначительного различия в скоростях вращения приводных звездочек, и, наконец, самое важное — расположение гусениц друг над другом с промежуточным звеном (ствол дерева) все это вызывает нежелательное явление — биения. Что не наблюдается так явно в обычных транспортирующих устройствах, в которых основное влияние оказывает горизонтальная динамика.
Рисунок 3.9.График незатухающих биений вызванных двумя возмущающими силами с частотами со&bdquo-2 и о) вг близкими к друг другу.3.2.Поперечное перемещение хлыстов: взаимодействие с раскряжевочными агрегатами поточных линий для первичной обработки древесного сырьяВлияние упругих свойств хлыстов на процесс поперечного раскрояОсобенности взаимодействия хлыстов в процессе первичной обработки при раскрое на сортименты заключаются в упругих деформациях стволов при поперечной распиловке, которые протекают во времени от начала пиления до завершения. Особенно ярко эти деформации проявляются на раскряжевочных установках типа «слешер». В таких поточных линиях как СТИ -1, СТИ-2, СТИ-3, СЛ-4, ЛО-65, ЛО-Ю5 на базе «слешера» с самого начала зарождения направления развития раскряжевочных линий велась борьба с заклиниванием пильных дисков в процессе надвигания хлыстов на пилы. Подробный анализ исследований по этому вопросу дан в 1 главе. В настоящем разделе приводится теоретическое обоснование физической сущности явления заклинивания пильных дисков при раскряжевке агрегатами, у которых оси вращения пильных дисков расположены под плоскостью перемещения хлыстов.
Производительность слешерных раскряжевочных установок зависит от различных факторов, в том числе и от того как решен вопрос исключения зажима пильных дисков при пилении. Тем более, что структурный анализ поточных линий и оборудования для первичной обработки древесины невозможно провести без учета раскряжевочных агрегатов, поскольку нет рекомендаций и критериев, которые позволят определить преимущества того или иного типа раскряжевочных агрегатов — с нижним расположением осей вращения пильных дисков или с верхним расположением пильных агрегатов вообще.
Время простоев слешера из-за заклиниваний дисков пил, приходящихся на один хлыст, составляет 12% от расчетного цикла раскряжевки. Или около 4% от чистого времени работы установки [17,18,37,38].
Опыт эксплуатации и конструирования слешерных установок в Красноярском крае показал, что изменением угла наклона стола слешера, различными вариантами расстановки пил исключить зажимы не удается. Интересным, с точки зрения исследователя, является факт, основанный на многочисленных наблюдениях различных авторов [15,17,18,37,38,40] -сортименты после завершения пиления или после образования скола, разрыва недопила (что является дефектом раскряжевки) имеют тенденцию прокатываться вперед по ходу надвигания на пильные диски. Имея разные диаметры комлевого и вершинного торцов сортименты получают перекос, что вызывает пиление сортиментов обратной стороной пильного диска. Исследования, проведенные на кафедре механизациилесоразработок СибТИ, показали, что раскатывание отрезков хлыстов после раскряжевки явление не случайное. Раскатывается исключительное большинство сортиментов [15]. Это говорит о том, что кривизна, развилки, пасынки, нацлывы и прочие пороки по работам [11,37,38,39] не являются основной причиной раскатывания сортиментов в процессе раскряжевки на слешере, поскольку эти факторы, на наш взгляд являются частными случаями, которые увеличивают или уменьшают вероятность заклинивания пильных дисков и прокатывания вперед по ходу надвигания отрезанных сортиментов. Во-вторых, заклинивание пильных дисков происходит не в момент раскатывания и перекосов отрезков, а при некотором недопиле. Этот факт подтверждается многочисленными наблюдениями, например, [15,17,18]. В-третьих, заклинивание происходит наиболее часто при получении отрезков максимальной длины, например, на пиле, которая распиливает хлыст пополам. Все перечисленные факты показывают, что заклинивание пил обусловлено упругими деформациями1 хлыстов, перемещаемых по столу слешера.
Хлыст при надвигании на пилу слешера лежит на четырех опорах (цепи транспортера надвигания) А, В, С, Д. Длина пролета между опорами АВ и СД 4−1 Зм. Пролет ВС около 1 м. Естественно, при таких пролетах имеются изгибные деформации хлыстов, которые фиксируются в виде прогибов. Если вести отсчет от нейтральной оси балки (каковой является хлыст), то эти прогибы до раскряжевки У] и У2 (рис. 3.10а). Потенциальная энергия изгиба балки при действии собственной силы тяжести хлыста будеттт г М2(х,)<&- и-, = ——) 2 Е1(х2)I 2Е1(х1)где иьи2 — потенциальная энергия деформации (изгиба)балки в сечениях X] и Х2 — М1(х]), М2(х2) -изгибающий момент в сечениях XI и х2: Е — модуль упругости материала балки 1(х1)Д (х2) -момент инерции сечения X) и X}. Продифференцировав выражения (3.57) имеемд11 с Мх (д-,)сЬсдМ] (х}) 31/ М2сЬсдМ2(х2) Е1(х])дР{(3.57)дРIдР Е1(х2)дР2-т (3.58)где Р) Р2 -результирующая сил тяжести отрезков АВ и ВС.
В случае полной раскряжевки связь между точками В и С нарушается, а прогибы У] и У2 увеличатся до У1 и У2.
Но процесс зажима пил начинается до полной раскряжевки, т. е. при наличии недопила. Это говорит о том, что устойчивый хлыст до некоторой величины недопила Н1 (рис. 3.12) теряет устойчивость и переходит в другое более устойчивое положение. Это явление обусловлено тем, что недопилпредставляет собой тонкую перемычку (по исследованиям [17,18,38] Н] - 5−9 см), относительно оси симметрии этой стенки приложена эксцентричная нагрузка от отрезков хлыста. В свою очередь перемычка — недопил имеет малую жесткость по оси Ъ и значительную жесткость по оси У. Таким образом отрезки должны получить дополнительный прогиб Д^ Х — У], Д2= У2 — У. Но перемычка — недопил, имея высокую жесткость не позволяет ц.т. отрезков опуститься до отметки У' и У2. По аналогии с устойчивостью плоской формы изгиба балок [94] вместо работы на изгиб в плоскости наибольшей жесткости, хлыст в сечениях между пролетами АВ и СД (рис. 3.10) «работает» на косой изгиб, что компенсирует недобор деформации до У1 и У'2. С появлением боковых деформаций потенциальная энергия возрастает за счет изгиба в боковом направлении, например, для первого сечения 2Е1(х1)(3.59)Теперь важно установить в каком направлении будет происходить выпучивание отрезков. При пилении диском пилы различных по диаметрам хлыстов недопилы располагаются под определенным углом ср, к направлению надвигания (рис. 3.11 а), т. е.= f (d).
Наиболее вероятным направлением выпучивания будет то, при котором сопротивление боковому изгибу будет наименьшим. Этим направлением будет выпучивание под углом ср, поскольку пропил нарушил связь между отрезками хлыста. Таким образом отрезки хлыста при недопиле Н] будут деформироваться (изгибаться) в вертикальном направлении, стремясь занять положение Y’i, Y’i, а также выпучиваться в сторону надвигания под углом ф. Центр тяжести отрезков при этом будет стремиться занять положение Yi и У2 поскольку выпучивание происходит не по оси Y, а в сторону под углом (р. То есть, ц.т. будет, смещаясь в сторону, опускаться (рис. 3.10 а, сечение В-В). При этом вертикальное смещение составитУГ= Y]Ssin (p Y2″ =Y2Ssin (р. (3.60)Выпучивание в сторону отрезков хлыстов влечет за собой поворот сечений, в частности поворот стенок пропила, что ведет к их смыканию и заклиниванию пильных дисков. Естественно, деформации хлыстов различных диаметров и пород будут различными.
Горизонтальное смещение стенок пропила КС и К’С (рис. 3.10, вид К) при повороте сечений будет функцией диаметров хлыстов и углов поворота сечений. Например, при диаметре 60 см, длине сортимента 13 м достаточно поворота сечения на 0,3 град. чтобы КС составило 3 мм. Для диаметра 20 см и той же длине сортимента поворот сечения на 1 град, смыкание КС составит 3,5 мм.
Эффект раскатывания также объясняется потерей устойчивости95хлыста при недопиле Н (. При выпучивании отрезка хлыста боковая деформация происходит под углом ср, т. е. создается эксцентриситет приложения сил тяжести. Подобная модель рассмотрена в работе [38] при искусственном создании изгиба в сторону надвигания для исключения зажимов пильных дисков, при этом за главный критерий взяты различные пороки хлыстов без учета прогибов хлыстов в процессе раскряжевки.
Предлагаемое теоретическое обоснование заклинивания пильных дисков, на наш взгляд универсально. При прогибе хлыста вниз под углом <р (рис. 3.11 а) или под углом у (рис. 3.10, сечения А-А, В-В)всегда имеется предпосылка к смыканию стенок пропила. А пороки (кривизна, наплывы, развилки, и т. п.)могут только ослаблять или усиливать эффект заклинивания. Таким образом, с точки зрения упругой деформации хлыстов при раскряжевке на слешерных установках объясняются такие явления как заклинивание пильных дисков и раскатывание отрезков, которые очень тесно взаимосвязаны. Потенциально, в силу конструктивных особенностей размещения раскряжевочных агрегатов на слешерных линиях, каждый распиливаемый хлыст имеет упругие деформации и, следовательно, имеется для каждого хлыста потенциальная предрасположенность к заклиниванию пильных дисков.
Определение потенциальных точек контакта с поверхностью пильных дисков в процессе раскряжевкиПри деформации хлыста в направлении вектора, проходящего через точки С Oi К Огфис.З.П а), вектор направлен под углом у к поверхности разделочного стола. Определим аналитическое выражение угла у через основные параметры раскряжевочной установки. Начальная стадия пиления показана на рис. 3.11 а. Расстояние между центрами пильного диска и сечения хлыста выразим через начальный уголуо: LcfOi02 cos у0 = (r+R)cosy0, (3.61)где Loрасстояние между центрами сечения хлыста и пильного диска, м-градиус сечения хлыста, мR -радиус пильного диска, м-уоугол наклона вектора, проходящего через точки О^Ог, рад. Из треугольника О1АО2 (рис. 3.11 а) определим/ + гsmy0 =-(3.62)r + Rгде 1 — превышение стола разделки над центром вращения пильного диска, м.
Существенное влияние на технологический процесс раскряжевки явления заклинивания пильных дисков требует дальнейшей конкретизации технологических условий применимости различных типов раскряжевочныхРисунок3.15.Варианты взаимодействия пильных агрегатов поточных линий со свободно лежащим хлыстом-а, бцентр вращения пильного диска расположен под плоскостью перемещения хлыстов — в, гцентр вращения пильного диска расположен над плоскостью надвигания хлыста-д — центры пильного диска и сечения хлыста в одной горизонтальной или параллельных плоскостях.№агрегатов, что позволит принимать решения при анализе и синтезе технологических структур.
Прежде чем перейти к анализу типов раскряжевочных установок необходимо определиться с понятием свободно лежащего хлыста.
Свободно лежащий хлыст имеет возможность в точках опор совершать угловые и продольные перемещения. При этом в пролете между опорами не ограничиваются упругие деформации.
Не свободно лежащий хлыст — хлыст, который имеет ограничения по угловым и продольным перемещениям над точками опор. Достигаются эти условия, во-первых, ограничением упругих деформаций в пролетах между точками опор, во-вторых, при помощи создания условий статической неопределимости, т. е. искусственное ограничение угловых и продольных перемещений при помощи прижимов, неподвижных в продольном направлении хлыста опор с одновременным повышением коэффициента сцепления хлыста с опорой. Теоретические исследования показали, что в процессе раскряжевки, например, на слешерных установках с «открытыми» пролетами между фермами поперечного транспортера, угол ф (угол направления бокового выпучивания изменяется непрерывно от (рпцП до фтах с упругими деформациями вниз и под углом ф в сторону направления надвигания. Эту стадию упругих деформаций проходит каждый свободно лежащий хлыст, раскряжевываемый пильными агрегатами с центром вращения диска пилы, расположенным ниже плоскости перемещения хлыста. При этом факторы пороков древесины: наплывы, кривизна и др. играют вероятностную роль при проявлении явления заклинивания пильных дисков. Для свободно лежащего хлыста, в соответствии с изложенным выше, имеется возможность определить устойчивые и не устойчивые положения (рис. 3.15).
Рис. 3.15 а соответствует надвиганию хлыста на пильный агрегат типа «слешер» .Этот принцип подробно рассмотрен ранее.
Рис. 3.15 б соответствует надвиганию пильного диска на свободно лежащий хлыст снизу вверх. Этот принцип надвигания для свободно лежащего хлыста наиболее неблагоприятен с точки зрения смыкания стенок пропила, то есть необходимы специальные меры по предотвращению заклиниваний пильных дисков.
Рис. 3.15 в, г соответствует надвиганию на свободно лежащий хлыст пильного диска сверху вниз. Вероятность заклинивания диска мала поскольку выпучивание хлыста в пролете способствует" раскрытию" стенок пропила. Основными факторами риска являются естественные пороки ствола. Это положение подтверждается производственным опытом. В установках типа ЛО-15С, ЛО-68, ПЛХ-1 практически заклиниваний пильных дисков не происходит.
На рис. 3.15 д надвигание осуществляется пильным диском или лесоматериалом горизонтально. [Хлыст в неустойчивом положении. Факторами риска заклинивания являются естественные пороки. На практике апробировано значительное количество устройств, приспособлений, принципов для исключения зажима пильных дисков. ножевые острые кромки (а.с.988 551) ограничивают продольные перемещения отрезков хлыста в процессе раскряжевки на слешерных установках. Внедрено в Чернореченском леспромхозе Красноярского края- -перепад по высоте между опорами использован в установках типа ЛО-65. Здесь использован принцип предварительного напряжения хлыста, что противостоит смыканию стенок пропила— в линиях Раума Репола использовано сразу два принципа: закрытый стол слешера способствует ограничению упругих деформаций хлыста между пролетамиискусственное напряжение хлыста посредством крупнозвенных цепей свисающих с поперечной надслешерной фермы создают надежный прижим хлыста к упорам и исключает влияние случайного фактора риска — кривизны. Однако только с определенной направленностью. При этом полностью исключить зажимы пильных дисков не удается— рекомендованная к серийному производству слешерная линия ЛО-105, это уже отмечалось ранее, оснащена выдвижными пильными дисками для уменьшения потерь времени на ликвидацию заклинивания пильного диска и исключения появления брака при выпиливании сортиментов.
Учет закономерностей и физической сущности явления заклинивания пильных дисков при раскряжевке хлыстов позволяет при проектировании, анализе и, в конечном итоге, синтезе технологических структур для первичной переработки древесины обосновать выбор раскряжевочных агрегатов.
Выводы поразделу 1. Результаты теоретического анализа взаимодействия хлыстов с пильными агрегатами в процессе раскряжевки показывают, что при раскряжевке хлыстов на раскряжевочных агрегатах с пильными дисками, у которых ось вращения расположена ниже плоскости надвигания хлыстов, заклинивание пильных дисков происходит из-за упругих деформаций хлыстов.
2.Упругие деформации хлыстов при раскряжевке на агрегатах типа «слешер» имеют направление зависящее от кинематического угла встречи.
3.Каждый хлыст раскраиваемый на установках типа «слешер» потенциально предрасположен (в силу конструктивных особенностей раскряжевочных агрегатов) к упругим деформациям и смыканию стенок пропила при недопиле Ь.
5.Наиболее благоприятным направлением надвигания пильного диска на хлыст или хлыста на диск (с точки зрения заклинивания пильных дисков) является сверху вниз, что подтверждается производственным опытом. Наиболее нежелательным направлением надвигания на свободно лежащий хлыст является направление снизу вверх пильным диском ось вращения которого расположена ниже плоскости размещения хлыста.
4. ЭКСПЕРИМЕНТАЛЬНЫЕ ИССЛЕДОВАНИЯ4.1.Задачи экспериментальных исследованийОсновной задачей, стоящей перед экспериментальной частью данной работы, является подтверждение основных теоретических положений, разработанных в методике определения динамических характеристик хлыстов как предмета труда первичной обработки древесного сырья и проверка допущений сделанных в процессе выполнения теоретических исследований. А также, сравнение реальных динамических подсистем (хлыстов) с эквивалентными расчетными динамическими схемами, представляющих эти подсистемы.
В связи с задачами, поставленными в первой главе, экспериментальные исследования проводились в два этапа: а) исследование динамических характеристик одиночных хлыстов-б) исследование упругих подсистем (хлыстов), в производственных условиях на натурных образцах лесозаготовительного оборудования.
Для решения этих задач определялись экспериментально для одиночных хлыстов следующие параметры: а) силу тяжести одиночных хлыстов и пакетов (Р) — б) расстояние центра тяжести отдельных хлыстов и пакетов от комлевого среза (1ц.т.)-в) диаметры комлевого среза (с1к), диаметры вершинного среза (с1в), диаметры, в сечении которых расположены центры тяжести (ёц г), диаметры на высоте груди (с!^-г) жесткость комлевой (Ск) и вершинной (Св)частей хлыстов-д) частоты собственных колебаний комлей ^к) хлыстов-е) частоты собственных колебаний вершин (1″ в) хлыстов-ж) частоты собственных колебаний (Гкв) хлыстов, при одновременном выведении из равновесия комля и вершины-з) логарифмический декремент затухания при свободных колебаниях хлыстов.
На первом этапе определялись динамические характеристики хлыстов на специальном стенде. Стендовые испытания проводились с целью исключения всевозможных посторонних влияний со стороны рабочего оборудования. Но возможности стендовых испытаний были ограничены отсутствием приспособлений или механизма, который бы обеспечил сжатие пакета или одного хлыста аналогично челюстям погрузчика. Поэтому эксперименты с зажатыми хлыстами проводились на челюстном погрузчике ЛТ-73.<08По взаимодействию стволов деревьев с ГПУ были поставлены следующие задачи: В связи с теоретическими исследованиями, проведенными ранее, в экспериментальной части перед третьим этапом были поставлены следующие задачи:1.Установить экспериментально взаимосвязь между вертикальнымиколебаниями двух гусениц, с находящимся между ними стволом дерева. 2. Определить роль ствола дерева в горизонтальных и вертикальных колебаниях ГПУ.
3.Определить влияние вынужденных колебаний в ГПУ, обусловленных звенчатостью гусениц на активную мощность протаскивания дерева. 4. Определить влияние кинематических параметров на динамические нагрузки в ГПУ.
4.2.Место, условия и подготовка к проведению экспериментальных исследований.
Экспериментальные исследования выполнены в Сибирском технологическом университете на кафедре технологиии и оборудования лесозаготовок и в лаборатории лесозаготовительного оборудования Красноярского филиала ВНИИСтройДормаша в период с 1973 по 1989 г.г.
Экспериментальные работы по исследованию динамическиххарактеристик проводились в Ново-Козульском леспромхозе в п. Кедровый и на Красноярском лесоперевалочном комбинате.
Для проведения исследований была выбрана площадка возле сезонного запаса хлыстов. Площадка была спланирована при помощи бульдозера. Стенд в виде листвяжьего сруба был собран на площадке и забутирован щебнем.
Подача хлыстов к стенду осуществлялась челюстным погрузчиком. На стенд хлысты по покотам затаскивались при помощи лебедки автомобиля ЗИЛ-157, который был оборудован под тензолабораторию. Работа выполнялась в леспромхозе Всесоюзного объединения" Краслеспром". Дополнительные исследования по выявлению влияния отрицательных температур на динамиические характеристики хлыстов, а также на натурном образце челюстного погрузчика ЛТ-73 проводились на Красноярском лесоперевалочном комбинате в сентябре — декабре 1975 г., уточняющий (проверочный)) эксперимент по определению жесткости и собственных частот колебаний с несколькими хлыстами проводились на КЛПК в 1983 -1989г.г. В 1983 — 1986 г. г. в лаборатории кафедрытехнологии и оборудования лесозаготовок СТИ проводились эксперименты по определению модуля упругости хлыстов с учетом масштабного фактора содновременной проверкой методики определения жесткости и частотных характеристик хлыстов.
При проведении экспериментальных исследований на основных этапах выдерживались следующие обязательные условия: а) эксперименальные исследования динамических характеристик хлыстов и процессов с их участием проводились при положительных температурах-б) стенд и тензометрические опоры для хлыстов выставлялись по уровню, чтобы обеспечить равномерность распределения статических нагрузок от хлыстов-в)лесопогрузчик при экспериментальных исследованиях устанавливался на горизонтальную бетонную площадку.
4.3.Аппаратура, приборы и тензометрическая оснастка.
Для измерения геометрических размеров хлыстов применялась рулетка длиной от 0 до 20 000 см, мерная вилка с пределами измерения диаметров от 4 до 80 см, мерный шест с прикрепленной к нему проградуированной через 1 мм металлической линейкой.
Для измерения силы тяжести хлыстов применялся динамометр и специальный стенд с тензометрическими опорами и соответствующей измерительной аппаратурой.
Измерения основных динамических характеристик хлыстовпроизводились на специальном стенде (рис. 4.1 и 4.2).Необходимость в проведении стендовых испытаний была вызвана тем, что получение достоверных сведений о динамических нагрузках при колебаниях хлыстов непосредственно на погрузчике или какой другой машине связано с проблемами, которые выражаются, во — первых, в косвенном методе тарировки тензоэлементов, что, как известно, влечет за собой увеличение ошибок измерений.
Во — вторых, наличие связей через гидросистему, челюсти, стрелу, грунт может внести существенные погрешности при определении динамических характеристик гибкого груза, рассматриваемого нами в данный момент как изолированная подсистема сложной упругой системы.
Устройство представляет собой (рис. 4.1) основание (1), изготовленное в виде сруба из листвяжьих бревен. Верх основания закрыт брусом (2), который укладывается на поперечные стенки основания (3). Над поперечными стенками, которые обеспечивают необходимую жесткость в вертикальном направлении, устанавливаются тензометрические опоры № 1, № 2, № 3, № 4. Пара № 1 и № 2 образуют комлевую опору, пара № 3 и № 4-вершинную опору. На пары элементов устанавливаются металлические траверсы (4), обеспечивающие укладку одного — трех хлыстов. Расстояние между опорами может регулироваться.
Рисунок 4.2.Стенд ддя исследования динамических характеристик хлыстов и элементарных пакетов.
При записи динамических характеристик хлыстов использовалсясветолучевой осциллограф Н — 700 и суммирующий четырехканальный блок усиления БУС — 68.
Применение БУС-68 позволило получить суммарную нагрузку на валы комлевой и вершинной опор.
Суммирование нагрузки с валов 1,2,3,4 попарно, позволило исключить ошибки, которые могли возникнуть при расположении хлыста несимметрично относительно опор. Исследования динамического взаимодействия рабочего оборудования и гибкого груза производились также тензометрическим методом. Тензодатчики проволочного типа (2,6) наклеивались для регистрации усилия зажима на вал нижней челюсти (8) (рис. 4.3). Для регистрации изгибных деформаций в стреле (1) служили датчики (2). Колебания хлыстов регистрировались при помощи акселлерометров инерционного типа (5,9), устанавливаемых на комлевых и вершинных срезах хлыстов, также на стреле (3,4), которые регистрировали как частоту колебаний, так и действующие ускорения при остановках и трогании с места рабочего оборудования.
Запись деформаций, ускорений производилась на осциллографическую фотобумагу шириной 120 мм при помощи светолучевого осциллографа Н-700 и усилителя 8АНЧ -7М в комплекте.
Тензометрические испытания по исследованию взаимодействия стволов деревьев с ГПУ проводились с использованием тензовалов ведущих звездочек нижней и верхней гусениц, которые после предварительной тарировки с комплектом БУС-68 и Н-700, были установлены на действующую сучкорезно-раскряжевочную линию.
Для подвода питающего напряжения к тензодатчикам использовались ртутные токосъемники, присоединенные к тензовалам с торца и защищенные металлическими неподвижными кожухами. Для регистрации числа оборотов нижнего и верхнего приводных валов использовались индукционные счетчики с подачей сигнала на усилитель БУС-68.-М5Рисунок 4.6.Установка датчиков на каретке и приводном валу ГПУ: 1 — токосъемник нижнего приводного вала — 2 — акселлерометр на каретке верхней гусеницы.
Активная мощность приводных электродвигателей гусениц регистрировалась при помощи преобразователя мощности П-005, который подсоединялся к обмоткам электродвигателей через токовые трансформаторыдля регистрации колебаний верхней каретки использовался акселлерометр инерционного типа, который устанавливался на каретке верхней гусеницы (рис. 4.12).
Сигналы, от указанных датчиков, при помощи присоединительных проводов и разъемов (рис. 4.13) передавались на усилитель БУС-68. Запись сигналов производилась при помощи свето лучевого осциллографа Н-700 на светочувствительную бумагу.
Тарировка датчиков проводилась при предварительной подготовке. То есть, в условиях тензометрической лаборатории. Тензовалы в сборе со звездочками нагружались при помощи гидравлического домкрата через рычаг длиной 1 м. Данные по тарировке приводятся в приложении Г (табл.П). Акселерометры тарировались непосредственно перед каждыми измерениями методом опрокидывания, а тарировочный сигнал записывался на начало осциллограммы.
Тензометрическая аппаратура контролировалась по тарировочным данным. Все приборы, при помощи которых производилась тарировка тензоаппаратуры (гири, динамометры и др. подвергались поверке тензометрической лабораторией централизовано в Центральной метрологической лаборатории г. Красноярска по заявке КФ ВНИИСДМ.
4.4.Порядок проведения экспериментальных исследований.
Для определения жесткости хлыстов на поверхности почвы под комлевой и вершинной частями хлыста, уложенного на тензоопоры, укладывались шпалы длиной 2,5−3,0 м параллельно продольной оси хлыста. Шпалы, как и тензоопоры, выставлялись по уровню. На комлевом и вершинном срезе хлыста находился центр среза и делалась риска. Затем хлыст нагружался постоянной силой от 200 до 700 Н и при помощи мерного шеста, выставленного перпендикулярно относительно шпалы, фиксировался прогиб комля или вершины (рис. 4.14) под действием силы Р. Собственные частоты хлыстов, как при одновременном выведении комлей и вершин из равновесия, так и комлей, вершин в отдельности, получались путем выведения из равновесия консольных частей хлыстов постоянной силой и резким освобождением консолей от этой силы. Изменение сил инерции при колебаниях передавалось на тензоопоры и фиксировалось осциллографом на фотобумаге.
Сила тяжести хлыстов определялась путем суммирования опорных реакций, А и В (рис. 4.7), определяемых при помощи тензометрических опор. Контролировалось определение этой величины при помощи динамометра. ДОтб) Рисунок 4.8.Во время проведения экспериментальных исследований — передвижная тензолаборатория на испытаниях — б| - определение прогиба комлевой части хлыста. mКонструкция опор позволяла фиксировать как статические, так и динамические нагрузки.
Таким образом перед записью собственных колебаний хлыстов, сила тяжести автоматически фиксировалась на фотобумаге (рис. 4.11 а, б, в).
Определение собственной частоты колебаний зажатых хлыстов и не зажатых проводилось в горизонтальном положении стрелы погрузчика при резкой остановке на упоры при помощи акселлерометров (3, 4) рис. 4.3, а также датчика (2). Для определения собственных частот колебаний хлыстов (пакетов) в зажатом состоянии, последние зажимались в челюстном захвате при трех положениях нижней челюсти: -зажим с максимальным усилием на валу челюсти—усилие зажима среднее то есть на валу нижней челюсти регистрируется усилие, равное половине максимального—усилие зажима нуль, то есть на валу нижней челюсти регистрируется только вес хлыстов.
Сила тяжести хлыстов и центр тяжести определялись при помощи лесопогрузчика и динамометра ДПУ-5−2. Центр тяжести хлыстов определялся методом подбора.
Для замера силы тяжести хлыст при помощи тросовой петли, которая крепилась за динамометр, поднимался вверх на 1,5 -2,0 м стрелой лесопогрузчика (рис. 4.9). Высота подъема регламентировалась стрелой прогиба комля и вершины.
Порядок испытаний гусеничного протаскивающего устройства (ГПУ) при взаимодействии со стволом дерева выдерживался следующий: обмеривались и нумеровались стволы каждого нового воза на приемной эстакадепроизводилась запись на светочувствительную бумагу нулевых линий каналов при ненагруженном ГПУпроизводилась запись на холостом режиме ГПУ-производилась запись деформаций приводных валов, ускорений каретки, мощности развиваемой электродвигателями при протаскивании стволов различного объема.
Объемы стволов варьировались от 0,2 до 4,78 м³. Все операции повторялись в вышеприведенной последовательности для различных сочетаний синфазности и асинфазности движения верхней и нижней гусениц. Синфазность и асинфазность задавлись изменением количества траков и вариациями межцентровым расстоянием между ведущей звездочкой и натяжным колесом ГПУ при помощи натяжного устройства с увеличенным ходом. шРисунок 4.11.Определение центра тяжести и силы тяжести хлыстов с помощью погрузчика ЛТ- 73. ш4.5.Программа экспериментальных исследований.
К факторам, которые влияют на процесс взаимодействия хлыстов с рабочим оборудованием лесных машин следует отнести: 1. Жесткость хлыста (зависит от длины диаметров породы).
2.Масса хлыста (зависит от объема, плотности древесины и влажности)-3.Масса оборудования — конструктивный параметр.
4.Жесткость оборудования-конструктивный параметр.
5.Произвольные возмущающие силы — зависят от ускорений, возникающих, например, при остановке или трогании с места.
6.Периодические или гармонические возмущающие силы — зависят от кинематических параметров, например, в ГПУ.
В данной работе проведен пассивный эксперимент, поскольку главной задачей является сравнение расчетных значений параметров хлыстов, полученных по аналитическим зависимостям, которые получены на базе фундаментальных исследований теории колебаний.
При определении статических и динамических характеристик хлыстов нами были взяты породы деревьев, заготавливаемые в районе исследований: ель, пихта, сосна, осина, кедр. По каждой породе исследовалось не менее пяти хлыстов, соответствующих градации диаметров на высоте груди -28,36,44,52,60 см. Хлысты укладывались на стенд, центр тяжести находился между опор, но не ориентировался по середине межопорного расстояния.
Для десяти хлыстов одной породы (ель), одного класса диаметров на высоте груди и одного класса длины центр тяжести размещался симметрично относительно опор. При следовании указанной схеме испытаний должен быть выполнен объем замеров (наблюдений), указанный в таблице, А 13. В указанной таблице указаны параметры, которые фиксировались при проведении испытаний: с! к-диаметр комляс!] з-диаметр на высоте груди- (?0К-диаметр над комлевой опоройс! оБ-диаметр над вершинной опоройёв-диаметр вершиныЬ-длина хлыста- 1цт-расстояние от комлевого среза до центра тяжести хлыста (ц.т.) — Рв, Рк-сила тяжести вершинной и комлевой частей хлыста соответственно — ув, ук-прогибы вершинной и комлевой консоли соответственно- 4,-частоты собственных колебаний комлевой, вершинной консолей и комля с вершиной совместно.
Экспериментальные исследования на погрузчике проводились при силе тяжести хлыстов от 65 500 до 1750 Н. При этом фиксировались следующие величины: fз-coбcтвeннaя частота колебаний не загруженного оборудованияГг-первая и вторая собственные частоты колебаний комлевой и вершинной консолей соответственно нагруженного оборудованиясобственные частотыкомлевых, вершинных консолей хлыстоваугол наклона стрелы, при промежуточных положениях стрелы- ^¥—ускорения при остановках — Мкр №крутящий момент на валу нижней челюстиf, f — первые собственные частоты колебаний системы «хлысты — рабочее оборудование» при зажатом и не зажатом положении захвата.
Экспериментальные исследования взаимодействия хлыстов с ГПУ проводились по следующей схеме:-объемы стволов варьировались от 0,2 до 4,78 м³, т. е.протаскивались наиболее часто встречаемые объемы в районе испытаний: 0,2 — 0.28 — 0,54- 0.74- 0,83 -0,87 — 0,98- 1,10- 1,15 — 1,24 — 1.35 -1,42- 1,78 -1.92 -2,00−2,50- 3,85- 4,45−4,78 м³.
Порода — ель. При проведении испытаний объемы были разбиты на классы: 0,48 — 0,92 — 1,25 — 1,99 — 2,50 м³. Во время испытаний фиксировались следующие параметры: Уд-объем ствола деревафв, (ркдеформации приводных валов верхней и нижней гусеницWKускорения верхней каретки с гусеницейNi-мощность развиваемая электродвигателем нижней гусеницы при протаскивании стволов ели различного объемаТн-период колебаний нижнего валаТв-период колебаний верхнего вала — Tq-период биений.
4.6.Обработка результатов экспериментальных исследованийОбработка результатов экспериментальных исследований включает несколько важных этапов, каждый из которых может по своему влиять на точность полученных результатов: а)статистическая обработка результатов, полученных непосредственными замерами-б)расшифровка записей осциллограмм-в)обработка осциллограмм-г)статистическая обработка численных значений параметров исследуемого процесса, записанного на осциллограмму.
Расшифровка осциллограмм производилась в следующей последовательности: -проявлялись и просушивались осциллограммы- -устанавливалось и помечалось на осциллограмме расположение каждого канала- -используя журнал наблюдений на каждом кадре отмечали: а) порядковый номер-б) род записанного процесса-в) диапазон чувствительности каждого канала, на котором производилась запись данного кадра-г)определялся масштаб М каждого измерения, которым учитывается коэффициент усиления в момент измерения и чувствительность датчиков, с которыми производились измерения.
Необходимое количество вычислений определялось количеством пиков п между максимумами. Таким образом, формула для вычислений текущего значения длины консоли во время прохождения моментов биений будет выглядеть следующим образом (рис. 4.116).где Ьтахрасстояние между максимальными значениями деформаций в момент биений, мм-пколичество пиков деформаций между двумя максимумам ¡-=1,2,.птекущая координата-ЬПуск — расстояние между пусковым моментом и первым максимумомV — скорость протаскивания ствола дерева м/с.
В выражении (4.5) в скобках получаем время в с, так как знаменатель каждого слагаемого делится на число равное масштабу 0,1 с на осциллограмм, выраженное в мм (рис. 4.11).(4.5)№Таким образом, мы в любой момент биений будем знать длину консоли. Для проверки частоты колебаний ствола дерева между гусениц нами был поставлен дополнительный эксперимент: на консоль дерева устанавливался второй акселлерометр, который во время протаскивания фиксировал колебания ствола дерева. Образец осциллограммы показан на рис. 4.12. Осциллографическая запись на рис. 4.12 соответствует прохождению ствола на длину 1,8 м.
Обработка осциллограмм производилась способами амплитудной классификации и пересечения уровней [ 107 ]. В осциллограммах процесса протаскивания ГПУ при определении коэффициентов динамичности измерялись максимальные пики крутящего момента при биениях и без биений. Соответственно им пики ускорений каретки. Кривую мощности обрабатывали при помощи линейного планиметра (геодезического). Среднюю мощность определяли по формуле?/¦М.(4.6)где8 — площадь диаграммы, мм -1 -длина диаграммы мм-Ммасштаб записи, квт/мм. Диаграмма крутящего момента обрабатывалась при помощи квантовальной решетки [107 ] с подсчетом крайних точек впадин и вершин кривой 2 (рис. 4.11), попавших в границы интервалов квантования. При квантовании по уровню величину ординаты, попавшей в { -ый интервал, относили к средней линии интервала. Таким образом, предельная погрешность квантования по уровню была равна половине интервала квантования. Это являлось критерием выбора величины интервала квантования (величины классного промежутка). Начало и конец биенийПри проведении испытаний был произведен расчет погрешностей при измерении геометрических размеров хлыстов, прогибов консолей хлыстов при нагружении силой Р, рабочего оборудования, параметров, характеризующих процесс взаимодействия хлыстов с рабочим оборудованием лесопогрузчика и ГПУ: КДЭ-КД тах-Кд 1шп-№ - М с и др.
Расчет сделан по методике [109], составленной на основании теории ошибок. Расчет приведен в приложении Ь.
5. СРАВНИТЕЛЬНАЯ ОЦЕНКА РЕЗУЛЬТАТОВ ЭКСПЕРИМЕНТАЛЬНЫХ И ТЕОРЕТИЧЕСКИХ ИССЛЕДОВАНИЙ5.1.Результаты экспериментальных исследований динамических характеристикхлыстовВ результате экспериментальных и теоретических исследований динамических характеристик хлыстов были получены данные, позволяющие произвести оценку правильности выводов и допущений, сделанных в процессе исследований. Как уже отмечалось нами в предыдущих главах и разделах, мы производили исследования, разделив сложную динамическую систему на подсистемы. К одной из таких подсистем относятся хлысты. Для этой упругой подсистемы мы определяли экспериментально жесткость и собственные частоты колебаний. В приложении, А (таблица А3) приведены численные значения жесткости комлевых частей хлыстов, полученные экспериментальным путем (Сэ), а также значения жесткости, вычисленные по формулам предлагаемым в настоящей работе (Ск) и, жесткости (СК]), вычисленные по методике, применявшейся, например, в работах [78,79].
В таблице АЗ приведены жесткости хлыстов различных пород: осины, кедра, пихты, сосны, ели. Геометрические характеристики указанных хлыстов приведены в приложении А1.
Таблица А6 содержит данные по жесткости комлевых консольных частей хлыстов ели, подобранных по одному классу диаметров на высоте груди, а также по длине.
Сравнение полученных результатов показывает, что формула (2.12), выведенная автором в результате теоретических исследований, дает более точные результаты, чем формула (1.5).Так жесткость Ск (приложение А, таблица АЗ), полученная по формуле (2.12), отличается от экспериментальных значений Сэ в среднем от 2 до 55% в сторону завышения и 5−40% в сторону занижения. В то время как использование частотного метода (подстановка экспериментальных значений собственных частот колебаний в формулу (1.5) дает ошибку в сторону завышения порой в 5−9 раз, в среднем в 4−6 раз).
Аналогичная картина для вершинных консольных частей хлыстов. (Приложение А, таблица А.5). Максимальное верхнее отклонение Св от экспериментальных значений составило 58%, нижнее максимальное 81%. Отклонение С1 В от экспериментальных значенийзначений в сторону завышения в 14 раз и в сторону занижения на 25% единичные случаи. В среднем значения жесткости завышаются в 7 раз.
Более стабильные результаты получены для хлыстов одной породы (ель) (приложение А, таблица А4). При этом выбраны хлысты с одной лесосеки, одного класса диаметров и длины. Отклонение расчетных значений жесткости по выведенным в данной работе формулам в сторону занижения в среднем составило от 18 до 28%.
Частотный метод определения жесткости дает завышение значений жесткости в среднем в 2,5 раза. Физическая сущность завышения значений жесткости при использовании экспериментальных значений собственных частот колебаний хлыстов рассмотрена с необходимым теоретическим обоснованием в первой главе данной работы.
Дальнейшие исследования, проведенные с одиночными хлыстами и пакетами подтверждают допущение в теоретической части и в работах [10,12] о том, что жесткость пакета равна сумме жесткостей отдельных хлыстов. В приложении А, таблицы А7 и А8 содержатся значения приведенных к концу консоли масс хлыстов гПпрК и шпрв (комлевых и вершинных соответственно) и собственных частот колебаний шк, сов, С0кв (круговая частота комля, вершины, вершины с комлем одновременно). Поскольку приведенная масса является величиной абстрактной и проверить правильность ее вычисления непосредственными измерениями не представляется возможным, в данной работе применен косвенный метод проверки: вычислялась и экспериментально проверялась жесткость Ск, Св, С^- вычислялась приведенная масса комля, вершины, хлыста в целом mnpK, mI[pB, m1® по формулам (2.43, 2.45) для вершины, комля и хлыста в целом определялись круговые частоты, которые сравнивались с экспериментальными значениями. Таким образом проверялась правильность определения приведенной массы и жесткости как одиночного хлыста, так и элементарного пакета. Сравнение экспериментальных значений собственных частот колебаний комлевых и вершинных частей одиночных хлыстов, а также хлыста в целом с расчетными значениями показывает, что среднее отклонение расчетных значений собственных частот от экспериментальных составляет в среднем 29,8%. Более точные результаты в пределах 21% в среднем получены для хлыстов ели одного класса диаметров на высоте груди (приложение А, таблица А8).
Большое различие в экспериментальных и расчетных значениях частот собственных колебаний хлыстов, по сравнению с исследованиями собственных частот колебаний, например, балок из материалов с изотропными свойствами [81, 82, 83, 84], объясняется свойствами древесины. Известно, что древесинаприродный полимер с нестабильными физико-механическими характеристиками, которые зависят от ярко выраженной анизотропии, породы, условий произрастания, климатических условий и др. факторов. В частности модуль упругости изгиба, который необходим для определения жесткости хлыстов нами использовался табличный с проверкой по различным источникам [127, 128, 129, 130, 131] с пересчетом на 30% влажность. Изучение литературных источников показало, что модуль упругости при изгибе варьирует довольно в широких пределах. Например, в разных источниках при 15% влажности приводятся разные значения модуля упругости. Для ели модуль упругости рекомендуется разными авторами от 126* 103 до 105 кгс/см2. Сосна от 9*104 до 105 кгс/см2, береза от 120*103 до 151*103 и т. д.
При этом модуль упругости определялся по образцам малых размеров, которые не сравнимы с размерами хлыстов. То есть, не учтен масштабный фактор. Наряду с этим на жесткость влияют вероятностные факторы: изгиб (кривизна) наплывы, сучья, гниль (скрытая), неравномерная сбежистость, известно что вершинная часть может иметь модуль упругости больший по значению, чем комлевая часть. Например, пересчитанный на 30% влажность модульА Оупругости при изгибе для сосны составляет 7*10 кгс/см. Предварительный эксперимент поставленный с целью уточнения значений модуля упругости при изгибных колебаниях в 1997 году в Решетинском районе Красноярского края дал значения модуля упругости при изгибных колебаниях хлыстов сосны в пределах 5,3 *103 кгс/см2. Очевидно, что возникла необходимость в проведении исследований модуля упругости при изгибных колебаниях с учетом масштабного фактора, то есть необходима методика проведения исследований модуля упругости применительно к колебаниям хлыстов.
На челюстном погрузчике проверено влияние зажима пакета хлыстов на частоту собственных колебаний. Достоверные результаты получились только при крайних положениях зажима, то есть при максимальном усилии зажима пакета и в положении «не зажато». Промежуточное положение дает результат такой же, как и в положении «не зажато». Так для груза 65 550 Н при зажатом положении челюстей среднее значение собственной частоты равно 1,69 гц при коэффициенте вариации 13,7%, показатель точности равен 3,41%. В не зажатом положении челюстей захвата среднее значение собственной частоты получено равным в среднем 0,99 гц при коэффициенте вариации 27,7%, показатель точности 3,13%. Разница составила около 70%.
Средняя собственная частота колебаний комлевой части пакетов составила 12,6 сГ1 (расчетная рекомендуемая для этого класса погрузчиков[10] - 12,36 с1). Средняя собственная частота вершинной части пакета 6,37 с4 (расчетная рекомендуемая для этого класса погрузчиков[10] - 4,49 с'1).
11 — % • сравниваемых графиков (рис. 5.1 и 5.2), характер экспериментальной кривой и расчетной одинаков. Расхождение расчетных значений с экспериментальными не превышает 15−17%. Далее по осциллограммам нами были получены значения приведенного к ведущему валу ГПУ момента сопротивления, получаемого при протаскивании дерева через сучкорезную головку (Мс), поскольку его значение входит в расчетную формулу по определению деформации ведущего вала нижней гусеницы.
На рис. 5.3 приведен график изменения момента сопротивления при протаскивании стволов ели различного объема. Полученные значения моментов сопротивления протаскиванию были использованы при вычислении коэффициента динамичности на ведущем валу нижней гусеницы, а также для получения значений максимального момента на валу той же гусеницы. На рис. 5.4 приведен график изменения коэффициента динамичности при асинфазном движении верхней и нижней гусениц. Кривая 1 — расчетная. Кривая II — экспериментальные значения. Значения Кдмах по этим кривым соответствуют максимальным значениям при биениях. Расхождение между экспериментальными и расчетными значениями не превышает 15−20%. Третья и четвертая кривые соответствуют значениям минимального коэффициента К К™т динамичности, соответственно расчетные и экспериментальные значения. Кривые К™т соответствуют изменениям коэффициента динамичности в зависимости от объема стволов без биений. тушахПо 1−2 кривым можно судить, что ^ д при асинфазном движении верхней и нижней гусениц изменяются с изменением объемов стволов от 0,5до 2.5 м соответственно от 1,55 до 1,87, т. е. имеется ростд на21,3%. (кривые 3 и 4) изменяется для тех же объемов от 1,12 до 1,3,т.е. возрастает на 16,1%. Динамические нагрузки при возникновении биений возрастают для объемов 0,5 — 2,5 м на 38,4% и на 43,8% соответственно, т. е. при исключении биений имеется возможность снизить динамические нагрузки в среднем на 42%.
Рассмотрим еще один график (рис. 5.5), который соответствуеттакже К™ах (кривые 1,2) ид (кривые 3,4). Этот график относится ксинфазному движению обеих гусениц. Расчетные значения {Кд) кривая 1 имеют расхождения с экспериментальными значениями при больших объемах•5 л (1,8 -2,5 м) до 22%, для малых (0,5−1,8 м) в пределах 8−12%. В среднем расхождение составляет 14−15%. Как говорилось в теоретической и экспериментальных частях настоящей работы, возможны и другие сочетания работы гусениц: синфазное движение нижней гусеницы, асинфазное движение верхней или наоборот. Но при проведении экспериментов промежуточныев7Мс, кГм? ппОт 2 м3Рисунок 5.5.Моменты сопротивлений (Мс) протаскивания стволов различного объема через сучкорезную головку.
7 -1——-1ЧО 0,5 Т, 0 15 г, О 2,5 У. м3Рисунок 5.6.Зависимость мощности протаскивания стволовот объема при наличии биений (кривая I) и при отсутствии биений (кривая И).значения получились «размытые», то есть большой разброс значений в пределах двух графиков (рис. 5.4 и 5.5). Поэтому и были взяты за основу два экстремальных случая. Этим же можно объяснить увеличенный процент ошибки для К™х при синфазном движении обеих гусениц, так как большие объемы имеют, во-первых, наплывы и неровности, во — вторых, увеличенная сбежистость от комля к центру стволов, все это вместе взятое сыграло роль в том, что одна из гусениц работала то в синфазном, то в асинфазном режиме. Анализируя далее графики можно сказать, что синфазное движение по сравнению с асинфазным дает увеличение Кд до 20%, судя по экспериментальным значениям.
Таким образом, если гусеницы имеют разность скоростей движения AV и настроены на синфазный режим, то исключив путем синхронизации гусеницбиения, мы получим понижение Кд от Кдмах до К™10 (рис. 5.5) в среднем на 33%- далее, настроив гусеницы на асинфазный режим движения, мы имеемminвозможность понизить Кд до д (рис. 5.4)в среднем на 17%. В сумме мы имеем реальную возможность снизить Кдшх при синфазном движении доr^ minЛ, а при асинфазном движении на 50%.
В наличии биений не приходится сомневаться, так как это очень наглядно подтверждено осциллографической записью процесса протаскивания ствола дерева ГПУ, к тому же теоретические расчеты дают хорошую сходимость результатов с экспериментальными данными. Экспериментальные значения периода колебаний на нижнем валу гусеницы равныТм=0,234 с, Tq=8,94 с.
ТеоретическиеTN=0,228 c, Tq=9,05 с, где Tn — период вхождения зацепов гусениц в контакт со стволом-Tq — период биений, вызванных разностью скоростей движения верхней и нижней гусениц. Расхождение составляет 2,6 и 1,23%.
В результате экспериментальных исследований нами было замечено, что мощность, развиваемая электродвигателем при протаскивании стволов деревьев в значительной степени зависит не только от объема протаскиваемого ствола, но и от характера взаимодействия гусениц со стволом: с биениями или без биений. Анализируя график на рис. 5.6 можно сказать, что при изменении объема ствола от 0,5 до 2,5 м³ мощность протаскивания увеличивается на 24,5% (кривая 1-биения).
По второй кривой (без биений)-38,7%.Разница в развиваемой мощности при биениях и без биений составляет в среднем 26,8%, то есть для поддержания биений необходима мощность почти такая же, как для протаскивания ствола дерева объемом в 2,5 м. Результаты теоретических исследований динамического взаимодействия ГПУ с протаскиваемыми стволами деревьев, согласующиеся сэкспериментальными данными, позволили нам произвести более широкие исследования с применением ЭВМ. Используя расчетные формулы, выведенные в данной работе, мы исследовали влияние на динамику ГПУ таких факторов, как скорость движения гусениц, жесткость приводных валов, усилия прижима верхней гусеницы к стволу дерева, разность скоростей движения гусениц, колебания консоли ствола между гусеницами.
Расчеты показали, что уменьшение жесткости валов в 5 раз дает увеличение динамических нагрузок (при существующей скорости движения гусениц) на 0,34%.Увеличение жесткости валов в 5 раз (при тех же скоростях) дает увеличение динамических нагрузок всего на 0,06%. Увеличение скорости протаскивания до 2,5 м/с дает уменьшение динамических нагрузок на 8,51% в смысле влияния биений и характера движения гусениц.
Увеличение силы прижима верхней гусеницы до 50 000 Н дает увеличение динамической нагрузки на приводные валы на 44,7%." Этот факт говорит о том что прижим верхней гусеницы к нижней должен быть регламентирован в автоматическом режиме, поскольку на практике наблюдается «сворачивание» приводных валов ГПУ при чрезмерном прижиме.
Теоретические расчеты показали, что в процессе протаскивания ствола дерева, прирост динамических сил за счет колебаний консоли ствола незначителен и составляет 10−16%, что согласуется с экспериментальными данными. Таким образом, наше предположение о том, что в развитии динамических нагрузок колебания ствола дерева между гусениц ГПУ играют превалирующую роль, не подтвердилось. Хотя прирост динамических нагрузок на 10−16% также нежелателен. Но этого можно легко избежать, обеспечив контакт комлевой консоли ствола (во время протаскивания) с плоскостью приемного ствола.
Как показали исследования, собственные частоты колебаний консолей ствола в момент биений имеют значения отличные от вынужденных частот, то есть чисто резонансных колебаний ствола дерева на происходит. Этот факт говорит о том, что в момент биений консоль находится вне резонанса и развитие амплитуды биений происходит под влиянием таких факторов как разность скоростей движения верхней и нижней гусениц, соотношения масс и жесткостей ГП, синфазности и асинфазности движения гусениц. Изменение коэффициента динамичности Кд в зависимости от объема протаскиваемого ствола очень наглядно показывает влияние указанных факторов на динамические нагрузки в ГПУ.
Анализ экспериментальных и теоретических исследований показал следующее:1.Основание консоли (ствола между верхней и нижней гусеницами совершает вынужденные колебания с частотой вхождения траков в зацепление с приводными звездочками.
2.Колебания комлевой консоли между гусеницами ГПУ дают прирост динамических нагрузок на 15−16%.
3.Ввиду того, что колебания ствола дерева между гусеницами ГПУ способствуют увеличению вертикальных динамических нагрузок, рекомендуется в стационарных сучкорезнораскряжевочных линиях с ГПУ приемный стол конструировать с таким расчетом, чтобы комлевая консоль при протаскивании постоянно была в контакте с плоскостью приемного стола.
4.Для передвижных сучкорезно — раскряжевочных машин с ГПУ, где обычно приемный стол отсутствует, рекомендуется увеличение скорости протаскивания до 1,8−2,0 м/с, что будет способствовать увеличению разности между значениями собственных частот колебаний ствола и вынужденной частотой, а также рекомендуется синхронизировать движение гусениц с одновременной настройкой их на асинфазный режим движения.
5. В результате взаимодействия верхней и нижней гусениц со стволом дерева в динамической системе «верхняя гусеница — ствол дерева — нижняя гусеница» при наличии разности скоростей движения между верхней и нижней гусеницами, возникают биения которые увеличивают динамические нагрузки на 25 — 33%.
6.Максимальный коэффициент динамичности на приводном валу нижней гусеницы ГПУ с индивидуальным приводом верхней и нижней гусениц при изменении объема протаскиваемого ствола от 0,5 до 2,5 м³ рекомендуется в пределах 1,76 -2,3. Исследование характера движения гусениц показало, что синфазное движение гусениц дает увеличение коэффициента динамичности до 20%, по сравнению с асинфазным режимом. При проектировании новых конструкций ГПУ необходимо предусмотреть специальное устройство для настройки гусен на асинфазный режим движения При эксплуатации существующих линий с ГПУ рекомендуется операторам настраивать верхнюю и нижнюю гусеницы на асинфазный режим при помощи натяжного устройства изменением количества траков в верхней и нижней гусеницах.
7.Одной из актуальнейших задач, которую необходимо решить при конструировании сучкорезно-раскряжевочных линий с ГПУ являетсяисключение вредных колебаний — биений. Решение этой задачи заключается в обеспечении асинфазности движения обеих гусениц и созданиежесткой или программной связи между верхней и нижней гусеницами (для исключения относительных смещений зацепов в горизонтальной плоскости). Последнее мероприятие обеспечит несовпадение зацепов верхней и нижней гусениц. Соблюдение этих условий даст снижение Кдмах до Кдшш, то есть обеспечит снижение динамических нагрузок на 50−60%.
8.Поскольку резонансные явления и, в том числе, биения вдинамической системе не могут поддерживаться без затрат энергии, то в нашем случае также происходит дополнительный расход энергии, идущий на поддержание биений. При наличиии биений во время протаскивания ГПУ ствола дерева вшэксплуатируемой ППЛ-4 м развиваемая мощность приводного электродвигателя увеличивается на 26,8%.То есть, исключение вредных колебаний в виде биений обеспечивает не только снижение динамических воздействия на конструкцию линии, но и снижает расход энергии.
6. МАТЕМАТИЧЕСКОЕ И ГРАФИЧЕСКОЕ ПРЕДСТАВЛЕНИЕ ПЕРЕМЕСТИТЕЛЬНЫХ ОПЕРАЦИЙ ПЕРВИЧНОЙ ОБРАБОТКИДРЕВЕСНОГО СЫРЬЯ.
Выводы по главе.
1 .В результате теоретического обоснования моделирования, анализа и синтеза поточных линий для первичной обработки древесины получены обобщающие структурные формулы (модели) для описания технологий существующих (на основе деструктуризированных элементов поточных линий) и перспективных линий (на основе предпочтительных принципов выполнения технологических операций).
2.Теоретически обоснованный синтез технологических структур поточных линий позволил исключить известные варианты технологических схем и провести направленный и обоснованный поиск новых технологических структур.
3.Синтезированая гамма технологических структур представляется в виде ряда условных формул, которые могут быть расшифрованы и изображены графически, в виде графов перемещений, в виде структурных формул, в виде.
277 матриц, описывающих технологический процесс и в виде графической модели технологического процесса.
4. Синтез технологических структур поточных линий проводится с переходом от однопильных к многопильным линиям на базе одних и тех же агрегатов, что позволит создавать поточные линии для первичной обработки древесины агрегатно — блочной компоновки .
5 .Имитационное табличное моделирование показало возможность совмещения раскряжевки с сортировкой древесины по диаметрам с исключением дополнительного сортировочного оборудования .
6.Имитационное моделирование, проведенное по раскряжевке древесины с использованием карт раскроя, показало возможность эффективной расстановки пильных агрегатов для проведения раскроя хлыстов по оптимальным схемам с целью увеличения качества и выхода деловой древесины.
7.Предложенный многоуровневый анализ технологических структур позволил дать количественную оценку технической оснащенности существующих и вновь создаваемых технологических потоков. т.
ЗАКЛЮЧЕНИЕ
.
В диссертационной работе изложено решение научно — практической проблемы, которое заключается в разработке основ моделирования, анализа существующего оборудования и синтеза перспективных технологий, отвечающих принципам ресурсосбережения, расширения функциональных возможностей, однотипности оборудования и возможности агрегатно — блочного принципа развития технологических исполнительных схем.
Созданные теоретические основы позволили разработать на базе системного подхода формализованный метод анализа и синтеза технологических структур поточных линий для первичной обработки древесины на стадии поперечного раскроя. Синтезированные на основе предпочтительных принципов выполнения технологических операций технологические структуры обладают расширенными функциональными возможностями, которые заключаются в возможности организации оптимальной раскряжевки хлыстов на многопильных раскряжевочных линиях с использованием известных теоретически обоснованных методов определения типоразмеров предмета труда (хлыстов). Структурное построение синтезированных технологий таково, что позволяет организовать на многопильных установках подсортировку и сортировку по диаметрам продукта труда (сортиментов) в процессе выполнения операции удаления сортиментов из зоны раскряжевки. При этом синтезированные технологические структуры типовых рядов гаммы технологических структур конструируются их однотипных агрегатов, что создает предпосылки для создания агрегатно — блочных конструкций с дискретным наращиванием производительности с шагом 50 — 80 м /смену.
Разработанные методики определения жесткости и размещения масс в динамических расчетных схемах хлыстов носят обобщающий характер, распространяются на большинство случаев размещения, закрепления и перемещений хлыстов при выполнении технологических операций и позволяют проводить моделирование динамических процессов при различных возмущающих воздействиях, что подтверждено экспериментальными исследованиями. Теоретические исследования взаимодействия раскряжевочных агрегатов с хлыстами на многопильных поточных линиях позволили раскрыть физическую сущность явления заклиниваний (зажима) пильных дисков в процессе пиления, обусловленную упругими свойствами хлыстов и конструктивными особенностями раскряжевочных агрегатов. При этом результаты теоретических исследований совпадают с многочисленными производственными наблюдениями и экспериментальными исследованиями различных авторов. Определение природы заклиниваний пильных дисков позволило на стадии анализа технологических потоков.
79 определить критерий выбора пильных агрегатов для синтезируемых технологических структур.
Формализация процессов перемещения предмета труда при выполнении технологических операций позволяет описывать структуру технологических потоков и моделировать технологический процесс с введением стохастических воздействий в любом месте технологической цепи с учетом геометрических характеристик предмета труда.
В итоге, в соответствии с поставленной целью и задачами, получены следующие теоретические, практические результаты и выводы: 1. Установлено, что при исследованиях процессов взаимодействия хлыстов с технологическим оборудованием необходимо учитывать особенности выполнения технологических операций, к которым следует отнести: расположение предмета труда на рабочем оборудованиихарактер движения исполнительных органоврасположение рабочих органов относительно обрабатываемых хлыстов, характер возникающих возмущений при перемещениях предмета труда.
2. Доказано, что применение частотного метода определения жесткости длинномерного гибкого предмета труда с применением экспериментальных значений собственных частот колебаний приводит к завышению численных значений жесткости в среднем 2−4 раза.
3.Теоретически обоснована методика определения жесткости хлыстов с учетом сбежистости, породы и связей, накладываемы на подсистему «хлысты» .
4. Установлено, что механическое разбиение массы длинномерного упругого предмета труда (хлыстов) на равные и не равные части при составлении эквивалентных динамических схем подсистемы «хлысты» не позволяет перейти от вычисленных значений жесткости или экспериментальных значений, определенных классическим методом, к вычислению численных значений собственных частот колебаний как подсистемы с распределенными параметрами.
5. Разработана методика определения приведенных масс гибкого длинномерного предмета труда с распределенными параметрами на основе равенства кинетических энергий приводимых и реальных масс.
6. Определен круг проблемных вопросов, к которым отнесено: необходимость проведения комплекса исследований по определению модуля упругости при изгибных колебаниях хлыстов с учетом масштабного фактора, качества, породы, геометрических пороков и температуры окружающей среды.
7.Разработана динамическая расчетная схема гусеничного протаскивающего устройства с математическим описанием процесса взаимодействия ГПУ со стволом дерева, при этом расчетами, подтвержденными экспериментальными данными установлено:
— максимальный коэффициент динамичности наиболее нагруженного приводного вала нижней гусеницы при наличии биений и установившемся режиме движения находится в пределах 1.8−2.3 ;
— колебания ствола дерева между гусениц повышает вертикальные динамические нагрузки на 10 -16% ;
— увеличение силы прижима верхней гусеницы к хлысту приводит к увеличению динамических нагрузок. Так при увеличении силы прижима с 30 000 до 50 000 Н динамические нагрузки возрастают на 40 -50%.
8.Доказано теоретически, подтверждено экспериментально наличие в ГПУ при протаскивании ствола дерева вредных колебаний (биений), вызываемых двумя возмущающими силами периодического характера с незначительной разницей в частотах воздействия на ствол дерева.
9. Введено понятие синфазности и асинфазности движения верхней и нижней гусениц ГПУ в вертикальной плоскости при динамическом взаимодействии со столом дерева, которое раскрывает сущность возникновения разночастотных вынужденных колебаний в ГПУ.
10.Практическое использование результатов исследований в производстве показало:
— расход электроэнергии при исключении биений в ГПУ снижается на 1820%;
— синхронизация приводов верхней и нижней гусениц в сочетании с настройкой гусениц на асинфазный режим в передвижной сучкорезной машине позволили уменьшить внутренние динамические эффекты, то есть исключить биения и снизить динамические нагрузки на 45 — 50%;
— при настройке гусениц в эксплуатируемых ГПУ на асинфазный режим движения коэффициент динамичности снижается на 17−20%.
11. Доказано, что при раскрое (раскряжевке) хлыстов на раскряжевочных агрегатах с пильными дисками, у которых ось вращения расположена ниже плоскости надвигания хлыстов зажим пильных дисков происходит в следствии упругих изгибных деформаций и поворота стенок пропила в процессе пиления.
12. Установлено, что упругие изгибные деформации хлыстов при раскряжевке на агрегатах типа «слешер» имеют направление, зависящее от угла кинематической встречи при пилении.
13. Доказано, что каждый хлыст, раскряжевываемый на установках типа «слешер» потенциально предрасположен (в силу конструктивных особенностей раскряжевочного агрегата) к упругим деформациям и смыканию стенок пропила при некотором недопиле высотой Н.
14. Установлено, что рекомендации по углу наклона слешерного стола в пределах 10−15° не могут обеспечить 100% исключение зажима пильных дисков.
15. Внедрено в производство устройство для исключения зажима пильных дисков при раскрое хлыстов на слешерной линии в Чернореченском ЛПХ а.с.988 551). Внедрение показало, что универсальных методов борьбы с заклиниванием пильных дисков нет, методы должны быть для каждго типа линий индивидуальными в зависимости от конструктивных особенностей.
16.Предложен метод формализации переместительных технологических операций независимо от типа оборудования на базе матричных преобразований координат.
17.Разработан метод математического и графического представлениятехнологических структур для первичной обработки древесины.
18.Разработан метод графо — аналитического моделирования технологических процессов первичной обработки древесины, который в режиме реального времени позволяет на любой стадии протекания технологического процесса вводить стохастические воздействия с последующим контролем за результатом воздействия.
19.Предложен метод определения оптимальных скоростей перемещений предмета труда на агрегатах поточных линий.
20.Проведено моделирование наиболее совершенных в конструктивном отношении поточных линий (отечественного производстваЛО-65, ЛО-Ю5- финского производства — Раума-Репола), которое показало, что существующие поточные линии отечественного производства при стабильных параметрах имеют расчетный коэффициент заполнения упоров ниже единицы. Финская линия при стабильных параметрах имеет расчетный коэффициент заполнения упоров равный единице.
21.Проведен структурный анализ существующих поточных линий, который позволил получить обобщенную структуру (модель) существующего технологического процесса первичной обработки древесного сырья.
22.Предложен многоуровневый анализ технологических структур, который позволяет количественно оценить показатель избыточности с определением достигнутого, минимально возможного и требуемого уровня технической оснащенности технологического процесса.
23.Получена обобщенная структура (модель) на основе упорядоченной последовательности групп агрегатов, которая позволяет произвести методом перебора вариантов синтез технологических структур с учетом совмещения операций, программируемое&tradeраскроя хлыстов и сортировки сортиментов в процессе удаления из зоны раскроя.
24. Разработан метод структурного синтеза технологических потоков для первичной обработки древесины, позволяющий на основе обобщенной структуры, созданной с учетом предпочтительных принципов выполнения операций, с учетом рекомендаций по выбору раскряжевочных агрегатов, методом наслоения пильных агрегатов производить синтез технологических структур с переходом от однопильных установок к многопильным на базе однотипных агрегатов и оборудования.
25. Введено понятие коэффициента установочных перемещений при описании структур синтезированных линий, которое позволило представить структуру типового ряда синтезируемой гаммы технологических структур в формализованном виде.
26, Имитационное моделирование организации технологии сортировки, совмещенной с удалением сортиментов из зоны раскряжевки показало:
— синтезированные технологические схемы обладают дополнительными функциональными возможностями проведения подсортировки (не специализированные линии) и сортировки (специализированные раскряжевочносортировочные линии (PCJI)) продукта труда первичной обработки древесины по диаметрам;
— принцип раскряжевки совмещенной с сортировкой по диаметрам заключается в раскряжевке каждого типоразмера хлыстов по диаметру в своей конкретной зоне, при этом зона конкретного типоразмера перекрывается смежным типоразмером;
— точность сортировки зависит от количества типоразмеров хлыстов, длины раскряжевочно — сортировочной зоны и количества пильных агрегатовимитация раскряжевки с сортировкой на двенадцатипильной линии показала, что разброс диаметров в лесонакопителях PCJI составил ±1−3 см — имитациия раскряжевки на ЛО — 105 тех же хлыстов дала разброс диаметров в лесонакопителях ± 6−8 см.
— длина фронта раскряжевки — сортировки на РСЛ в 2.6−3.0 раза меньше по сравнению, например, с комплексом ЛО-15С — ЛТ-86(с одной секцией), при этом отпадает необходимость в специализированном дорогостоящем оборудовании для сортировки.
27 .Разработан метод расстановки пильных агрегатов в синтезированных многопильных установках, который позволяет учитывать региональные особенности сырьевой базы при помощи карт раскроя по методу проф. B.C. Петровского .
28.Создана гамма синтезированных технологических структур поточных линий для первичной обработки древесины, состоящая из рядов которые на основе агрегатно — блочного принципа компоновки развиваются от одно пильных к многопильным с возможностью адаптации к региональным размерно — качественным характеристиками древесного сырья.
Список литературы
- Волков В.О. Лесная промышленность зарубежных стран: -М.: Лесная промышленность, 1987, — 200 с.
- Петровский В. С. Компьютеризация технологий лесного комплекса.- М.: Журн. «Лесная промышленность», 1993, № 3.
- Петровский B.C. Оптимальная раскряжевка лесоматериалов: -2 -е изд. Перераб. и доп М.:Лесн.пром., 1989. -288с.
- Редькин А. К. Управление операциями на лесных складах. М.: Лесн. пром-сть, 1979, -208 с.
- Редькин А.К., Чувелев А. Я. Методика выбора машин для нижних складов: — М.:МЛТИ. Научные труды. № 53, 1974, -с. 15−18.
- Редькин А.К., Чувелев А. Я. Выбор лесоскладских машин и технологий в зависимости от размерно качественных характеристик обрабатываемого сырья: Учебн. пособие. М.: МЛТИ, 1981,78 с.
- Дорошенко В.А. Синтез технологической структуры Автоматизированных технологических процессов первичной обработки древесины: Монография. -Красноярск: КГТА, 1996. -229 с.
- Люманов Р., Машинная валка леса. М., Лесн. пром-сть, 1990 — 280 с.
- Полетайкин В.Ф. Моделирование рабочих режимов тракторных лесопогрузчиков: Монография. Красноярск: КГТА, 1996. -248 с.
- Захаренков Ф.Е. Оптимизация производственного процесса береговых складов. -М., Лесн. пром-сть, 1978. 184 с.
- Верхов Ю.И. Теоретические основы проектирования лесных погрузочно-транспортных машин. Красноярск- Изд-во Красноярского ун-та, 1984. — 267 с.
- Ильницкий Л.С., Рахманин Г. А., Нижние склады. Состояние и тенденции развития. -М.: Лесн. пром-сть, 1983 160 с.
- Леонтьев Н.Л., Акиндинов М. В., и др., Лесоматериалы круглые, — М., Лесная пром-сть, 1975, 128
- Лозовой В.А., Миронов Г. С., Влияние упругих характеристик хлыстов на процесс их раскряжевки на слешерной установке, аб., «Комплексная механизация лесозаготовок и транспорт леса»., Межвузовск. сб. ЛТА., Л., 1986. с.93−98.
- Леонтьев Н.Л., Оценка качества круглых лесоматериалов. М., — Лесная пром-сть, 1977, 96 с.
- Миронов Г. С. Опыт эксплуатации многопильных раскряжевочных установок . Лесоэксплуатация и лесосплав. Экспресс — информация, ВНИИНИЭП леспром. вып.23 -М. 1987, 2 -24 е.
- Миронов Г. С. Многопильные установки для раскряжевки хлыстов : Учебн. пособие. КПИ., Красноярск, 71с.
- Воевода Д.К., Алябьев В. И. и др. Нижние лесные склады: Справочник, -М.: Лесн. пром-ть, 1972, 288 с.
- Воевода Д.К., Назаров В. В. Технология нижнескладских работ. М.: Лесн. пром-ть, 1981 — 88 с.
- Коршунов А.Н. Сортировка пиловочных бревен. М.: Лесн. пром-ть, 1979. — 104 с.
- Кондратьев В.И., Дегермендин Ю. А. и др. Пути повышения производительности раскряжевочной линии с поперечной подачей хлыстов. ВНИПИЭИЛеспром. вып.14. 1979, с.1−25.
- Вячеславов H.A., Песоцкий А. Г. Автоматизированная многопильная раскряжевочная установка ЛО-Ю5. М.: ВНИПИЭИЛесПром. Вып.23, 1987.,-25−35 с.
- Ступнев Г. К. Пути совершенствования лесозаготовительного процесса: — «Лесн. пром-ть», М.: 1971 — 199 с.
- Орлов С.Ф. Теория применения агрегатных машин на лесозаготовках. -М.: «Гослесбумиздат», 1963. -270 с.
- Шабалин В.Л., Катургин Л. И., Мальцев Г. Е. и др. Совершенствование конструкций раскряжевочных установок. М.: Лесная промышленность. 1996, N4, с.20−25
- Белоусов В.И. Сучкорезно-раскряжевочные машины. Экспресс-информация по зарубежным источникам. -М.: ВНИПИЭИЛ еспром, вып. 11, 1984−28-е.
- Петровский B.C. Математические модели лиственничных пород, точность и применение- Сб. «Лиственница», -вып. III, Красноярск, 1988.- с.21
- Петровский B.C. Оптимизация раскряжевки хлыстов. «Лесная промышленность», 196. -N2. с.7
- Петровский B.C. Автоматическая оптимизация раскроя древесных стволов. -М.: Лесная пром-сть, 1970. 183 с.
- Петровский B.C. Вопросы теории раскроя древесных стволов/ИВУЗ,
- Лесной журнал, 1963. N3. — с. 11.
- Захаров В.К. Лесная таксация. -М.: Наука, 1961. 240 с.
- Батин И.В., Дудюк Д. Л. Основы теории и расчета автоматических линий лесопромышленных предприятий. «Лесная промышленность», 1 975 176 с.
- Кондратьев В .И. Исследование процесса раскряжевки хлыстов на многопильных установках типа «слешер». Автореферат диссертации на соискание ученой степени к.т.н. Красноярск. СТИ .-1973. -25 с.
- Клименко Н.Ф. Исследование процесса поперечной распиловки хлыстов и сортиментного долготья на установках с поперечным перемещением леса. Автореферат диссертации на соискание ученой степени к.т.н. Л: — 1977, — 19 с.
- Кондратьев В.И., Дегерменджи Г. А., Миронов Г. С. Слешерные линии для раскряжевки хлыстов: -М.: Лесн. пром-сть, 1979, 96 с.
- Вячеславов H.A. Экспериментальные исследования режимов работы пильных блоков раскряжевочных установок: Труды ЦНИИМЭ. Технология, оборудование и автоматизация нижнескладских работ. -М.: -1987. -с.68−73.
- Торопов А. С. Интенсификация производственных процессов поперечной распиловки лесоматериалов. Автореферат диссертации на соискание уч. степени д.т.н.Санкт Петербург. -1993. -31 с.
- Мельников В. П Использование грузоподъемности челюстных погрузчиков. Химки. Труды ЦНИИМЭ. № 102, 1969. -с.67 70.
- Мельников В.П. Динамическое воздействие на челюстной погрузчик колебаний хлыстов при погрузке. Труды ЦНИИМЭ, № 108, 1972. -с.57.
- Мельников В.П. О грузоподъемности челюстных погрузчиков: М.: Лесн. пром-сть, № 11, 1972. -с.7.
- Полетайкин В.Ф. Некоторые вопросы динамики конструкций гусеничного лесопрогрузчика. Диссертация на соискание ученой степени канд. техн. наук., Красноярск, СТИ, 1971. -с.71 -139.
- Полетайкин В.Ф. Проектирование лесопогрузчиков: Учебное пособие. -Красноярск: КПИ, 1991. 116 с.
- Полетайкин В.Ф. Динамика переходных режимов работы лесных погрузчиков. «Межвузовский сборник научных трудов». КГТА,-Красноярск, 1993. -с.32 -51.
- Гастев Б.Г., Мельников В. И. Основы динамики лесовозного подвижного состава : М. Лесн. пром- сть. 1967. -115 с.
- Гастев Б .Г. Некоторые вопросы теории перевозок древесины в хлыстах на лесовозных дорогах. Автореферат диссертации на соискание ученой степени д .т .н .Львов. 1955. 30 с.
- Цофин З.С. Исследование физико механических характеристик пакетов хлыстов, перевозимых по лесовозным дорогам. Автореферат диссерт. на соискание ученой степени канд. техн. наук.: М. -1964. — 19с.
- Цофин З. С. Механизация транспортировки леса за рубежом. М,-ВНИПИЭИлеспром, 1970, с. 15−18.
- Цофин З.С. Исследование изменения интенсивности нагрузки от собственного веса пакета хлыстов. Химки. Труды ЦНИИМЭ. Сб. 29, 1969. с.28−35.
- Цофин З.С. Исследование геометрических и статических характеристик пакетов хлыстов. Труды ЦНИИМЭ. Сб. 42., 1963. с. 34 -36. Коротяев JI.B. Исследование жесткости хлыстов. Изв. Вузов, Лесной журнал. № 1. 1978. -с.48 -54.
- Перельмитер В.И. Исследование колебаний древесного ствола приобрубке сучьев на сучкорезной машине с рубящим полем. Диссертацияна соискание ученой степени канд.техн. наук. МЛТИ. 1971. 21 с.
- Мельников В.И. Об изгибе балок применительно к условиям вывозкилеса в хлыстах. Сб. трудов ЛЛТИ, № 50, 1956, с. 49 -70.
- Жуков A.B., Леонович И. И. Колебания лесотранспортных машин
- Минск. Из во БГУ им. В. И. Ленина. 1973. — 239 с.
- Жуков A.B. Влияние на динамику лесотранспортных систем гибкостипакета хлыстов при его поперечном расположении. «Тракторы исельхозмашины «.№ 9. 1973. с. 45 — 56.
- Жуков A.B.О выборе расчетной модели погруженных деревьев при исследовании колебаний лесных машин. Изв. Вузов. Лесной журнал. 1977, № 4. с. 75 -78.
- Жуков A.B., Абрамович К. Б., Смеян А. И., Хегай В. К. Экспериментальное исследование ударных нагрузок при падении деревьев. Изв. Вузов, лесной журнал, № 3, 1975.
- Жуков A.B. Исследование продольной устойчивости челюстных погрузчиков с учетом гибкости хлыстов. Лесное хозяйство, бумажная, деревообрабатывающая пром сть. Республиканское межведомственное обозрение, вып., Минск, 1973 — с. 43 -47.
- Алябьев В.И. Лесные погрузочно разгрузочные и штабелевочные машины. М.: Лесная апром-сть, 1968, 183 с.
- Яблонский A.A., Норейко С. С. Курс теории колебаний: М. Высшая школа. 1966. 255 с.
- Степаков Г. А. Оптимизация производства круглых лесоматериалов. -Лесная промышленность. 1974 .: 160 с.
- Верхов Ю.И., Лозовой В. А. Динамические характеристики предмета труда лесопогрузчиков .Сб.: Надежность и долговечность строительных и дорожных машин. КПТИ. Вып.2. Красноярск, 1975 с. 4.
- Верхов Ю.И., Лозовой В. А. Исследования динамических характеристик хлыстов и деревьев. Сб.: Надежность и долговечность строительных и дорожных машин. КПТИ. Вып.2. Красноярск, 1977, — с.З.
- Комаров М.С. Динамика механизмов и машин. М.: Машиностроение. 1969.: 295 с.
- Житомирский В.К. Механические колебания и практика их устранения. М.: -Машиностроение, 1966 с. 20 — 30
- Безносенко П.Д. Расчетная модель дерева для определения динамических нагрузок на рабочее оборудование валочно -пакетирующей машины. Химки. Труды ЦНИИМЭ, № 129. 1973. с.13−23.
- Виногоров Г. К. К методике обоснования расчетных деревьев при решении лесоэксплуатацтонных задач. Химки. Труды ЦНИИМЭ, вып. № 122. 1972. -с.52.
- Кушляев В.К. Моделирование дерева как механической системы. М.: -Лесная пром-сть: 11, 1970, — с. 12 -13.
- Коротяев П.В. О положении центра тяжести стволов с кроной и хлыстов, заготовляемых в лесах Европейского Севера СССР. Изв. Вузов, Лесной журнал, № 2. 1959. с. 109 — 110.
- Неумоин Н.И. Исследование некоторых вопросов, связанных с вывозкой леса в хлыстах. Химки, Труды ЦНИИМ, № 10. 1958.
- Старков Г. И. К вопросу экспериментального определения силы сопротивления воздушной среды, действующей на дерево в период повала. Химки. Труды ЦНИИМЭ, № 49, 1964.
- Воевода Д.К., Вороницын К. И. и др. Перспективы развития нижних складов. Лесная пром сть, № 2, 1975. -с. 12−15.
- Верхов Ю.И. Исследование некоторых вопросов динамики колесных лесопогрузчиков. Диссертация на соискание ученой степени канд.техн.наук. Красноярск, СТИ, 1973. -308 с.
- Л ах Е. И. К определению вертикальных динамических нагрузок на оси автомобильной балансирной тележки: Автомобильная промышленность. -М.: 1960. с. 120 -125.
- Ивашкевич И.Н. Исследование динамики гидропривода челюстных погрузчиков в режиме грузового хода: Диссертация на соискание ученой степени кандидата технических наук: Архангельск, 1972. 230с.
- Шустов В.И. Исследование некоторых вопросов динамики погрузчика на пневмоколесном ходу, грузоподъемностью 20 тс, на перегрузке хлыстов: Диссертация на соискание ученой степени канд. техн. наук:-Свердловск: СНИИЛП, 1970.
- Тимофеев В.А. Инженерные методы расчета и исследования динамических систем .- Л.: Энергия, 1975. с. 13 -15.
- Ананьев И.В., Колбин Н. М., Серебрянский Н. П. Динамика конструкций летательных аппаратов,— М.: Машиностроение, 1972. -238 с. ж
- Ананьев И. В. Справочник по расчету собственных колебаний упругих систем. М-JI: Гостехиздат, 1946, — 124 с.
- Ананьев И.В., Беляев М. М. Техника измерения колебаний. -М.: Изд. БНТЦАГИ, 1947. -229с.
- Ананьев И.В., Тимофеев П. Г. Колебания упругих систем в авиационных конструкциях и их демпфирование. М.: Машиностроение, 1965. -234с.
- Бабаков И.М. Теория колебаний . -М.: Наука, 1965. 559 с.
- Гогенемзер К ., Прагер В. Динамика сооружений. М.: ОНТИ, 1936. -267с.
- Пановко Я.Г. Введение в теорию механических колебаний. -М.: Наука, 1971.- 136 с.
- Яблонский A.A. Курс теоретической механики. -М.: Высшая школа, 1977.-278 с.
- Алябьев В.И. Основы оптимизации лесных погрузочно разгрузочных машин: Автореферат диссертации на соискание ученой степени доктора техн. наук. -Москва, 1973. -43 с.
- Алябьев В.И. Эксплуатационно кинематические показатели и динамика исполнительных органов лесопогрузчиков /Всесоюзное научно — техническое совещание. Доклады. Часть 1.-М.: 1970. -с. 171 -183.
- Артоболевский С.И. Теория механизмов и машин. -М.: Высшая школа. 1967. -293 с.
- Анучин Н.П. Лесная таксация. М.: Лесная промышленность, 1971. -511 с.
- Казак С.А., Котов В. И., Петухов П. З., Суторихин В. Н. Расчеты металлургических кранов . -М.: Машиностроение, 1973. -217 с.
- Беляев A.M. Сопротивление материалов. -М.: Гос. издат физико -математической, 1962. 856 с.
- Таубер Б. А. Подъемно транспортные машины. -М.: Лесная промышленность, 1980. -456 с.
- Белозеров Е.Я., Гольдберг A.M., Орлов С. Ф. Исследование повала деревьев на две опоры. -М.: Журнал лесная промышленность, № 2, 1960. -с.12−17.
- Дебердеев A.A. О влиянии кроны на соударение дерева// Изв. вузов, Лесной журнал 1963. -№ 2. с.15−18.
- Дебердеев A.A. О влиянии поперечных изгибных колебаний на соударение дерева// Изв. вузов .Лесной журнал.- 1969. -№ 1. с. 21 28.
- Забавников Н. А. Основы теории транспортных машин. -М.: Машиностроение, 1968. -с.94−100.
- Платонов В. Ф. Динамика и надежность гусеничного движителя. -М.: Машиностроение, 1973. -с. 111,47.
- Детали машин. (Расчет и конструирование):Справочник. Т. З.-М.: Машинострение, 1969. -288с.
- Иванов M.H. Детали машин. -М.: Высшая школа, 1964. -299с.
- ЮЗ.Вайнсон А. А. Подъемно транспортные машины. -М.: Машиностроение, 1964. -420с.
- Медведев М.И. Гусеничное зацепление тракторов. -М.: Машгиз, 1959. -239с.
- Древесина. Показатели физикомеханических свойств. Комитет стандартов, мер и измерительных приборов при Совете Министров СССР. Руководящие технические материалы. -М.: 1962. 48с.
- Пациора П.П., Пижурин A.A., Фергин В.Р.Электрооборудование и электроснабжение лесопромышленных и деревообрабатывающих предприятий. -М.: Лесная апром-сть, 1971. с. 228 — 230.
- Лихачев B.C. Испытания трактров. -М.: Машиностроение, 1974. -286с.
- Бродский А.Д., Кан В.Л. Краткий справочник по математической обработке результатов измерений. -М.: Стандартизация, 196. -215с.
- Смирнов Н.В., Дунин Барковский И.В. Курс теории вероятностей и математической статистики. -М.: Наука, 1969. -260с.
- Тарг С.М. Краткий курс теоретической механики. -М.: Наука, 1964.-335с.
- Ш. Панкратов С. А., Ряхин В. А. Основы расчета и проектирования металлических конструкций строительных машин. -М.: Машиностроение, 196. -276 с.
- Обросов М.Я., Фомичесв А. И. Исследование процесса нагружения электродвигателей сучкорезных установок. //Тр.ЦНИИМЭ, -Химки 1975. № 14. -с.68−75.
- Закревский П.Б. Изменение объемного веса ствола и кроны растущих деревьев по высоте. //Тр.ЦНИИМЭ, 198. № 123. -с.92−102.
- Бронштейн И.Н., Семендяев К.А .Справочник по математике. -М.: Наука, 1965. -607 с.
- Усилитель 8 АНЧ 7МТО. Техническое описание и инструкция по эксплуатации. -М.: 1970. -23 с.
- Светолучевой осциллограф Н 700. Техническое описание и инструкция по эксплуатации ОПЕ. 4 666 011. -М.: Приборостроительный завод «Виброприбор». 1970. -22с.
- Кацев П.Г. Статистические методы исследования. -М.: Машиностроение, 1974. -231 с.
- Леонтьев Н.Л. О влажности и весе круглых лесоматериалов в свежесрубленном состоянии //Тр.ЦНИИМЭ, Сб.84, 1967.-е. 118 -124.
- Панкратов С.А. Динамика машин для открытых горных и земляных работ . -М.: Машиностроение, 1967. -447с.
- Инструкция по определению экономической эффективности создания новых строительных, дорожных, мелиоративных, торфяных машин, лесозаготовительного оборудования и лифтов.-М.: Минстройдормаш, 1973. -153с.290
- Вопросы экономики и организации производства//Тр.ЦНИИМЭ.-Химки. 1973. -с.55−129.
- Временные методические положения и рекомендации по определению экономической эффективности научно исследовательских и опытно-конструкторских работ лесозаготовительной промышленности. -Химки. ЦНИИМЭ, 1971. -с. 135.
- Панкратов С.А. Конструкция и основы расчета главных узлов экскаваторов и кранов. -М.: Машгиз, 1962. -539с.
- Виноградов В. А. Исследование работы гусеничного протаскивающего устройства сучкорезных машин и установок: Автореферат диссертации канд.техн.наук, /-м., 1979. -20с.
- Колчин Н.И. Механика машин. -М.: Машиностроение, 1972. -455 с.
- Вадюнина А.Ф., Корчагина З. А. Методы исследования физических почв и грунтов ,-М.:В ысшая школа 1973. -344 с.
- Древесина. Резонансный метод определения модуля упругости при растяжении, декремента колебаний. ГОСТ 16 483.31−74.-М.: Изд.стандартов. 1974. -с.2.
- Смегаев С.Н.О взаимосвязи колебаний хлыстов, перевозимых в полупогрженном состоянии. //Тр.ЦНИИМЭ, Химки, 1970. с. 19−20.
- Москалева В.Е. Строение древесины и его изменение при физических и механических воздействиях. -М.: Изд.Акад. Наук СССР, 1967. 164 с.
- Леонтьев Н.Л. Упругие деформации древесины. -М.: Гослебумиздат, 1952. 120с.
- Перелыгин Л.М. Древесиноведение. -М. Лесная пром-сть, 1969. -319с.
- Апарцев О.С. Научно-технический прогресс в повышении выхода деловой древесины: Сб.тез.докл. краевой научно практической конф. -Красноярск, 1988, — с.38−42.
- Меньшиков А.П. и др. Увеличение выхода деловой древесины при раскряжевке хлыстов на Красноярском КИСК: Сб.тез.докл. краевой научно практической конф.-Красноярск, 1988. -с.25−30.
- Михеев Л. Н. Основные показатели монтажной технологичности лесоскладского оборудования блочного изготовления. //Тр.ЦНИИМЭ.-Химки.-1987. № 59. -с.79.
- Вячеславов H.A. Определение изгибной жесткости поперечного сечения древесного ствола в плоскостях пропилов. //ТР.ЦНИИМЭ.-Химки, 1983. с.38−41.
- Заливко Б.М. Исследование выхода деловой древесины на многопильной раскряжевочной установке ЛО-Ю5. //Тр.ЦНИИМЭ, -Химки, 1983. с.47−51.
- Рабинович Ф.И. Пути повышения выхода деловой древесины в лесной отрасли края: Сб.тез.докл.краевой научно практической конф. -Красноярск, 1988. -с.45−50.294
- Долговых Г. П. Комплексная характеристика лесного фонда лесозаготовительных районов страны. //Тр.ЦНИИМЭ, -Химки, 1977-с. 11−20.
- Бусленко Н.П. Моделирование сложных систем. -М.: Наука, 1968. -355с.
- ВениковВ.А.Теория подобия и моделирования. -М.: Высшая школа, 1976. -225с.
- Броздниченко H.H., Брейтер B.C., Химич В. А. К вопросу построения математических моделей вновь проектируемых лесозаготовительных машин. //Тр.ЦНИИМЭ, -Химки, 1977.-С.86−89.
- Полищук А.П. Эксплуатационные показатели деревьев и древостоев лесного фонда СССР.//Тр.ЦНИИМЭ, -Химки, 1968. -с.4−11.
- Виногоров Г. К. К методике обоснования расчетных деревьев при решении лесоэксплуатационных задач. //Тр.ЦНИИМЭ, -Химки, 1972. № 122. -с.52−67.
- Пижурин A.A. Методы планирования экспериментов и обработка их результатов при исследовании технологических процессов в лесной и деревообрабатывающей промышленности. Ч.2.-М.: Лесная пром-сть, 1972. с. 48.
- Вознесенский В. А. Статистические методы планирования эксперимента в технико экономических исследованиях. -М.: Статистика, 1974.- 101с.
- Вороницын К.И., Брейтер B.C. Опыт экспертной оценки прогнозов развития лесозаготовок до 2000 года. -М.: Лесная пром-сть: 1973, № 1. -с.3−5.
- Воевода Д.К., Вороницын К. И. и др. Перспективы развития нижних складов. -Лесная промышленность. -№ 2. -с. 12−15.
- Вороницын К.И., Некрасов P.M., Брейтер B.C. Классификация комплексных технологических процессов и систем машин//Тр.ЦНИИМЭ, -Химки, 1974. -с.41−57.
- Вороницын К.И., Некрасов P.M. и др.К вопросу о лесопромышленном районировании.//Тр.ЦНИИМЭ,-Химки, 1974.№ 137.-с.24−29.
- Виногоров Г. К. Некоторые лесоэксплуатационные характеристики почвенно-грунтовых условия и рельефа. //Тр.ЦНИИМЭ, -Химки, 1972,-с.8−11.
- Можаев Д. В. Заготовка древесины и лесовозобновление в Канаде.-Лсоэкплуатация и лесосплав. Вып. 15. ВНИПИЭИлепрм, 1991. -с.1−28.
- Смоленцев И.И. Гидрофицированная раскряжевочная установка. -М.: ВНИПИЭИлеспром. ВЫП.2. 1979. -с.1−12.
- Теслюк А.К., Смирнов В. Я. Сучкорезно-раскряжевочная установка ЛО-30.-М.: ВНИПИЭИлеспром. Вып.З. 1985. -с. 1−19.
- Merchadiser desigh allows three log sorts (Sorensen R-Forest Industries, 1989, № 9. p.p.17−15 (англ.)
- Перспективы развития нижних складов.-Лесная пром-сть, 1976. № 2. с. 12−15.(авт.Воевода Д. К. и др.).
- Вороницын К.И., Воевода Д.К., Тизенгаузен Л. Э. Технология и системы для лесоскладских работ.//ТР.ЦНИИМЭ, -Химки, 1974, № 139. -с.5−15.
- Уикер И. Динамика простанственных механизмов//Конструирование и технология машиностроения. -М.: 1969. -с.264−278.
- Воробьев Е.И., Попов С. А., Шевелева Г. И. Механика промышленных роботов: в 3 кн. -М.: Высшая школа. Т21 988. 364с.
- Выгодский М. Я. Справочник по высшей математике. -М.: 1973, -872 с.
- Дубнов Я. С. Основы векторного исчисления.Ч.1, ГИТЛ, 1952. -242с.
- Борисенко А.И., Тарапов И. Е. Векторный анализ и начала тензорного исчисления. -М.: Высшая школа, 1966.-341с.
- Аквис М.А., Гольдберг В. В. Тензорное исчисление. -М.: Наука, 1972.-351с.
- Denavit J/, Hartenberg R.S.A kinematic notation for lower pair Mechanisms Based on Matrices.-Jounal of Applied Mechanics, vol.22 Trans, ASME, vol.77,series ЕД955, p.215−221
- Крейнин Г. В., Бессонов А. П. и др.Кинематика, динамика и точность механизмов: Справочник. -М.: Машиностроение, 1984. -224с.
- Морошкин Ю.В. Определение конфигураций механизмов//Докл.АН СССР. 1952. Т.82. № 4.
- Морошкин Ю.Ф.О формах основных уравнений механизмов//Докл.АН СССР. 1953. Т.91. № 4.
- Артоболевский И.И. Теория механизмов и машин: Учебн. для вузов. -4-е изд., переработанное и дополненное. -М.: Наука, 1988. -640 с.
- Ефимов Н.В. Квадратичные формы иматрицы. -М., 1975.-160с.
- Эпштейн Ю.П. Построение кинематических алгоритмов управления для манипуляторов лесных машин. -М.: Лесной журнал. № 6,1996. -с.57−62.
- Эпштейн Ю.П. Анализ систем управления манипуляторов лесных машин на основе имитационного моделирования.-М.: Лесной журнал.№ 1,1995, — с.76−81.
- Воробьев E.H., Попов С .А., Шевелева Г.И.Механика промышленных роботов: В 3 кн./Под ред.К. В. Фролова, Е. И. Вороьева /Кн.1.: Кинематика и динамика/,-М.: Высшая школа. 1988.-304 с.
- Воробьев Е.И. Построение уравнений программного движения пространственных механизмов с несколькими степенями свободы. //Машиноведение. 1981. № 5. с.42−46.
- Воробьев Е.И. Анализ кинематики пространственных исполнительных механизмов/Механика машин. 1978. вып. 51. с.13−18.
- Воробьев Е.И. Алгоритм моделирования динамики механизмов манипуляторов и промышленных роботов.//Механика машин. 1978. Вып.53.-с.8−16.
- Лозовой В.А. Эксприментальное исследование вертикальныхдинамических нагрузок в линии ППЛ-4м.//Лесоэксплуатация и лесосплав. ВНИПИЭИлеспром. -М.: № 9. 1978. -9с.
- Лозовой В.А. Расчеты лесозаготовительного оборудования с учетом колебаний: Учебное пособие для студентов специальностей 260 100,170400 и слушателей ФПКП. -Красноярск: СибГТУ, 1999. -140с
- Лозовой В.А. Особенности расчета собственных частот колебаний одиночных крупномерных хлыстов: Справочно-информационный фонд.ВНИПИЭИлеспром. -М.: № 6/80, 1978. -7с.
- Лозовой В.А. К определению жесткости одиночных крупномерных хлыстов. Справочно-информационный фонд.ВНИПИЭИлеспром.-М.: № 6/80, 1978. -9с.
- Лозовой В.А., Кожевников П. А. Снижение динамических нагрузок при эксплуатации линии ППЛ-4м. -М.: Лесоэксплуатация и лесосплав. № 4, 1979. с. 12 -15.
- Лозовой В. А. Влияние гибкости хлыстов на динамические характеристики лесозаготовительных машин: Сб.тез.докл. научно -практической конф. -Красноярск, 1978-с.17−18.
- Лозовой В. А. Теоретические и экспериментальные исследования взаимодействия хлыстов с рабочим оборудованием лесных машин: Автореферат диссертациии канд.техн.наук/МЛТИ,-М.: 1982. -18с.
- Лозовой В.А., Миронов Г. С. Многопильная раскряжевочная установка, а.с.№ 988 551, 1982.
- Лозовой В.А., Миронов Г. С. Многопильная установка для раскряжевки хлыстов, а.с. № 1 165 566, 1985.
- Лозовой В.А., Миронов Г. С. Расклиновающее устройство пил слешерной установки //ЦНТИ. Информация о научно технических достижениях. № 83−38,1983 ,-2с.
- Лозовой В.А., Миронов Г. С. О влиянии упругих свойств хлыстов на процесс их раскряжевки на слешере: Сб.тез.докл.краевой научно -технической конференции. -Красноярск, 1986. -2с.
- Лозовой В.А., Рудковский Ю. Н. и др. Многопильные раскряжевочные установки упрощенного типа: Сб.тез.докл.краевой научно -технической конф., 1988. -с.94−97.
- Лозовой В.А., Загоскин В. А. и др. Новая линия для нижних складов. -М.: Лесная промышленность. № 1. 1990. -с.26−28.
- Лозовой В. А. Нижние склады состояние и перспективы: Сб.тез.докл.конф. КГТА, 1994. -4с.
- Лозовой В. А. Выбор раскряжевочного агрегата для перспективных линий: Сб.тезис.докл.конф., КГТА. 1994. -4с.
- Лозовой В. А.Структурно кинематический анализ лесозаготовительного оборудования. Лесоэксплуатация: Межвузовский сборник научных трудов./КГТА, 1995. -с.150−158.
- Лозовой В.А. Определение модуля упругости хлыстов с учетоммасштабного фактора: Сб. тезисов докл.краевой научно-технической конф. 1994.
- Лозовой В. А.Определение коэффициента динамичности при экспериментах на оборудовании с распределенной массой: Сб.тез.докл.Всесоюзной научно-практической конф. -Красноярск. 1993. с.35−39.
- Лозовой В.А., Миронов Г. С. Беззажимная раскряжевка хлыстов на слешере.//Лесоэксплуатация и лесосплав: Научно технический реферативный сборник. ВНИПИЭИлеспром. Вып.5. 1985. -с.11
- Кашьяп P.A.Pao P.A. Построение динамических моделей по экспериментальным данным. /Пер.с англ.-М.: Наука, 1983. -384 с.
- Асфаль Р. Роботы и автоматизация производства./Пер.с англ.-М.: Машиностроение, 1989.-448с.
- Мини и микро — ЭВМ в управлении промышленными объектами/Л.Г.Филиппов, И. Р. Фрейдзон, А. Давидовичу, Э. Дятку- пер. с рум.-Л.: Машиностроение, Ленинградское отделение, 1984,--136 с.
- Каган Б.М. Электронные вычислительные машины и системы: Учебное пособие для вузов. -2-е изд.-М.: Энергоиздат, 1985. -552с.
- Грищенко А.З., Грищук В. П., Денисенко В. М. и др. Автоматизированные системы управления технологическими процессами (справочник).- К. Техника, 1983. -351с.
- Волкевич Л.И. и др. Комплексная автоматизация производства.-М.: Машиностроение, 1993. -269 с.
- Бусленко Н.П. Моделирование сложных систем.-М.:Наука.1978.-282с.
- Лозовой В. А. Описание перемещений предмета труда (хлыстов) раскряжевочных установок методом матричных преобразований координат.-Лесоэксплуатация: Межвузовский сборник научных трудов. Красноярск: СибГТУ, 1998. -с. 139−144.
- Лозовой В. А. Теоретическое обоснование определения скоростей перемещений хлыстов на агрегатах поточных линий. Лесоэксплуатация: Межвузовский сборник научных трудов. Красноярск: СибГТУ, 1998. -с.129−133.
- Лозовой В. А. Моделирование технологического процесса линий для первичной обработки хлыстов. Лесоэксплуатация: Межвузовский сборник научных трудов. Красноярск: СибГТУ, 1998.С.91−95.
- Лозовой В.А. Матричное преобразование координат применительно к структурному анализу раскряжевочных линий. Лесоэксплуатация: Межвузовский сборник научных трудов. Красноярск: СибГТУ, 1998. -с.133−139.235
- Лозовой В. А. Аналитическое определение упругих деформаций хлыста при раскряжевке на слешерных линиях. Лесоэксплуатация: Межвузовский сборник научных трудов. Красноярск: СибГТУ, 1998. -с. 107 -110.
- Лозовой В. А. Особенности связей между агрегатами раскряжевочных поточных линий. Лесоэксплуатация: Межвузовский сборник научных трудов. Красноярск: СибГТУ, 1998. -с. 354 -356.
- Лозовой В. А. Влияние ориентации хлыстов при раскряжевке хлыстов на количество групп сортиментов: Проблемы химико лесного комплекса. Научно — практическая конференция .Сб. тезисов докладов. Красноярск: КГТА, 1995. с 54- 55.