Технологическое обеспечение прочности профильных неподвижных соединений с твердосплавным охватываемым элементом
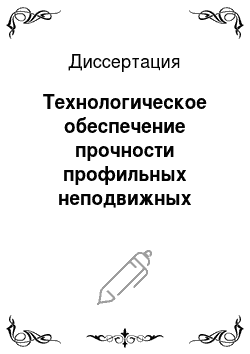
Диссертация
Цельные матрицы рекомендуется выполнять для высадки мелких и средних размеров винтов (до М10), а для более крупных размеров — из двух цилиндров, скрепленных с определенным натягом. В таких конструкциях рабочие поверхности выполняются на вставках, которые изготавливаются из дорогостоящих металлов и сплавов. Вставки, в свою очередь, помещаются в корпус, выполненный из более дешевой стали… Читать ещё >
Список литературы
- Головин, В. А. Технология ковки и объёмной штамповки. Ч. 2. Малоотходная объёмная штамповка / В. А. Головин, А. М. Дмитриев, А. Л. Воронцов. М.: Машиностроение — 1, 2004. — 434 с.
- Богатов, А. А. Исследование пластичности металлов под гидростатическим давлением / А. А. Богатов, О. И. Мижерицкий // Физика металлов и металловедение. 1978. — Т. 45. — Вып. 5. — С. 1089−1094.
- Моргунов, А. П. Технологическое обеспечение прочности профильных неподвижных соединений : монография / А. П. Моргунов, В. Б. Масягин, И. В. Ревина. М.: Технология машиностроения, 2004. — 296 с.
- Аскинази, Б. М. Упрочнение и восстановление деталей машин электромеханической обработкой / Б. М. Аскинази. М.: Машиностроение, 1989.-200 с.
- Шнейдер, Ю. Г. Технология финишной обработки давлением : справ. / Ю. Г. Шнейдер. СПб.: Политехника, 1998. — 413 с.
- Шнейдер, Ю. Г. Холодная бесштамповая обработка металлов давлением / Ю. Г. Шнейдер. М.: Машиностроение, 1967. — 352 с.
- Шнейдер, Ю. Г. Эксплуатационные свойства деталей с регулярным микрорельефом / Ю. Г. Шнейдер. Л.: Машиностроение, 1982. — 248 с.
- Высокоскоростное малоотходное деформирование металлов в штампах / Под. ред. В. Г. Кононенко. Харьков: Вища школа, 1985. — 176 с.
- Громов, Н. П. Теория обработки металлов давлением / Н. П. Громов. М.: Металлургия, 1978. — 360 с.
- Губкин, С. И. Пластическая деформация металлов. В 2 т. Т. 2 / С. И. Губкин. М.: Металлургиздат, 1961. — 466 с.
- Пат. 2 277 989 СССР, МПК В 21 Б 22/02. Способ изготовления Г-образных деталей / Евстифеев В. В., Пантюхова К. Н. — з аявитель и патентообладатель Омский гос. тех. ун-т. № 2 004 126 833/02 — заявл. 06.09.04 — опубл. 20.06.04, Бюл. № 17. — 3 с.
- Евстратов, В. А. Теория обработки металлов давлением /
- B. А. Евстратов. Харьков: Вища школа, 1981. — 248 с.
- Зубцов, М. Е. Листовая штамповка / М. Е. Зубцов. Л.: Машиностроение, 1980. -432 с.
- Изготовление деталей пластическим деформированием: сб. / под ред. К. Н. Богоявленского и П. В. Камнева. Л.: Машиностроение, 1975. -183 с.
- Колмогоров, В. Л. Механика обработки металлов давлением / В. Л. Колмогоров. -М.: Металлургия, 1986. 688 с.
- Кроха, В. А. К методике построения кривых упрочнения / В. А. Кроха // Машины и технологии кузнечно-штамповочного производства: сб. науч. тр. М.: Машиностроение, 1961. — С. 57−59.
- Охрименко, Я. М. Неравномерность деформации при ковке / Я. М. Охрименко, В. А. Тюрин. М.: Машиностроение, 1969. — 182 с.
- Хомяк, Б. С. Твердосплавный инструмент для холодной высадки и выдавливания / Б. С. Хомяк. М.: Машиностроение, 1981. — 184 с.
- Головин, В. А. Технология холодной штамповки выдавливанием / В. А. Головин, А. Н. Митькин, А. Г. Резников. М.: Машиностроение, 1970. -152 с.
- Головин, В. А. Технология и оборудование холодной штамповки /
- B. А. Головин, Г. С. Ракошиц, А. Г. Навроцкий. М.: Машиностроение, 1987. -352 с.
- ГОСТ 2590–88. Прокат стальной горячекатаный круглый. М.: Издательство стандартов, 1988. — 6 с.
- Миропольский, Ю. А. Холодная объемная штамповка на автоматах / Ю. А. Миропольский. М.: Машиностроение, 2001. — 456 с.
- Головин, В. А. Деформируемость металлов при холодной объемной штамповке / В. А. Головин // Пути совершенствования технологии холодной объемной штамповки и высадки. Омск, 1978. — С. 179−184.
- Губкин, С. И. Пластическая деформация металлов. В 2 т. Т. 1 /
- C. И. Губкин. М.: Металлургиздат, 1961. — 466 с.
- Дель, Г. Д. Технологическая механика / Г. Д. Дель. М.: Машиностроение, 1978. — 174 с.
- Ланской, Е. Н. Автоматизация проектирования процессов холодной объёмной штамповки и создание систем автоматизированного производства / Е. Н. Ланской, В. В. Евстифеев, В. В. Грязнов. М.: Машиностроение, 1988. -68 с.
- Миропольский, Ю. А. Технология холодной объемной штамповки на многопозиционных автоматах / Ю. А. Миропольский, Ю. К. Филиппов. -М.: Машиностроение, 1986. 72 с.
- Мокринский, В. И. Производство болтов холодной объемной штамповкой / В. И. Мокринский. М.: Металлургия, 1978. — 71 с.
- Новик, Ф. С. Оптимизация процессов технологии металлов методами планирования экспериментов / Ф. С. Новик, Я. Б. Арсов. М.: Машиностроение — София: Техника, 1980. — 304 с.
- Волков, Д. А. Производство высокопрочных деталей в машиностроении / Д. А. Волков, В. Г. Шибаков, А. П. Андреев // Кузиечно-штамповочное производство. Обработка материалов давлением. 2009. — № 8. -С. 35−39.
- Блесман, А. И. Ионно-лучевая обработка некоторых конструкционных материалов / А. И. Блесман, А. М. Ласица, Ю. К. Машков // сб. матер. IV Всерос. науч.-практ. конф. Ч. 2. Пенза, 2001. — С. 54−57.
- Брюхов, В. В. Повышение стойкости инструмента методом ионной имплантации / В. В. Брюхов Томск: Изд-во HTJI, 2003. — 120 с.
- Ивановский, Г. Ф. Ионно-плазменная обработка материалов / Г. Ф. Ивановский, В. И. Петров. М.: Радио и связь, 1986. — 232 с.
- Технологические методы повышения долговечности машин микрокриогенной техники / Б. Т. Грязнов и др. Новосибирск: Наука. Сиб. предприятие РАН, 1999. — 272 с.
- Исследование зависимости износостойкости гильз цилиндров от микрорельефа рабочей поверхности / Ю. Г. Шнейдер и др. // Автомобильная промышленность. 1970. — № 2. — С. 41−42.
- Машков, Ю. К. Повышение износостойкости трибосопряжения фрикционно-электрическим модифицированием поверхностей тренияповерхностно-активными модификаторами // Ю. К. Машков, 3. Н. Овчар,
- B. Р. Эдигаров // Омский научный вестник. 2006. — № 2(35). — С. 73−77.
- Сердобинцев, Ю. П. Технология избирательной лазерной закалки для повышения нагрузочной способности и сдвигоустойчивости соединений с натягом / Ю. П. Сердобинцев, А. Т. Алехин // Сборка в машиностроении, приборостроении. 2005. — № 2. — С. 4−8.
- Коржова, О. П. Технология формообразования и сборки профильных неподвижных и подвижных соединений : дис.. канд. техн. наук/ О. П. Коржова. Омск, 2008. — 137 с.
- Косилова, А. Г. Отделочная обработка внутренних поверхностей пластическим деформированием / А. Г. Косилова // Прогрессивные методы изготовления, отделка и упрочнение металлических деталей пластическим деформированием. -М.: Машгиз, 1962.-С. 154−161.
- Моргунов, А. П. Технологическое обеспечение прочности профильных неподвижных соединений деформирующим протягиванием /
- A. П. Моргунов // Прикладные задачи механики: сб. науч. тр. Омск, 2003.1. C. 16−19.
- Моргунов, А. П. Применение дорнования при образовании соединений деталей типа втулка-корпус / А. П. Моргунов, В. Б. Масягин // Нефть и газ Западной Сибири: тезисы докладов Междунар. конф. Тюмень, 1996,-С. 17.
- Проскуряков, Ю. Г. Тяговые усилия к деформации при дорновании отверстий запрессованных втулок / Ю. Г. Проскуряков, А. И. Осколков,
- B. М. Роговой // Упрочняюще-калибрующая и формообразующая обработка металлов: труды АНИ-ИТМ. Вып. 8. Барнаул: Алт. кн. изд-во, 1973.1. C. 87−91.
- Проскуряков, Ю. Г. Фактическая площадь контакта обработанных дорнованием поверхностей / Ю. Г. Проскуряков, И. В. Позднякова //
- Технология чистовой и отделочной обработки поверхностей деталей. -Челябинск: Изд-во ЧПИ, i960. № 47. — С. 50−54.
- Проскуряков, Ю. Г. Объемное дорнование отверстий / Ю. Г. Проскуряков, В. Н. Романов, А. Н. Исаев. М.: Машиностроение, 1984. -224 с.
- Розенберг, А. М. Обработка отверстий твердосплавными выглаживающими протяжками / А. М. Розенберг. М.: Машиностроение, 1976.-208 с.
- Сивцев, Н. С. Сборка прессовых соединений с применением процесса дорнования / Н. С. Сивцев // Сборка в машиностроении, приборостроении 2001. № 12. — С. 14−20.
- A.c. 1 298 032, СССР. Способ изготовления неразъемных соединений деталей / Кравченко Ю. Г., Ворохов А. А. // Открытия. Изобретения. 1987. -№ 11.
- Андреев, Ю. В. Технология повышения качества прессовых соединений дорнованием / Ю. В. Андреев, О. Б. Миндрул // Новые технологические процессы и оборудование для поверхностной пластической обработки материалов: тезисы докладов. Брянск, 1986. — С. 63.
- A.c. 1 782 690 СССР, МКИ5 В 21 D 39/04. Способ крепления трубы в отверстии детали / Васин В. И., Доний В. Г., Тарасов Б. А. // Открытия. Изобретения. 1992. — № 47.
- Заявка 4 134 552 ФРГ, МКИ5 Fl6 Н57/00. Прессовое шлицевое соединение Ritzel-Befestung bei insbesondere Planetengetrieben/Orlowski Bernhard.
- Пат. 2 094 153 Российская Федерация, МКИ6 В 21 D 26/10. Электрогидроимпульсный способ крепления втулки в глухом отверстии корпусной детали / Суркаев А. Д., Слепцов О. А. — Волгогр. техн. ун-т. // Открытия. Изобретения. 1997. -№ 30.
- Чистосердов, П. С. Повышение качества прессового соединения / П. С. Чистосердов, Ю. В. Андреев // Машиностроитель. 1987. — № 4. -С. 28−29.
- Горохов, В. А. Двухуровневая регуляризация микрогеометрии технических поверхностей и ее обеспечение / В. А. Горохов // Вестник машиностроения. 1994. — № 5. — С. 29−32.
- Заявка 2 670 541 Франция, МКИЭ F 16 В 7/00. Соединение трубчатых деталей. Asemblage de deux pieces notamment fubulaires/Pinet Armand.
- Киричек, П. А. Способ получения неподвижного соединения / П. А. Киричек // Машиностроитель. 1994. — № 10. — С. 10.
- Моргунов, А. П. Разработка и обеспечение прочности профильных неподвижных неразъемных соединений: авто реф. д ис. .д-ра техн. наук/ А. П. Моргунов. Омск, 1998. — 38 с.
- Андреев, Г. Я. Распределение контактных давлений в напряженных посадках / Г. Я. Андреев, И. И. Шатько // Вестник машиностроения. 1967. -№ 5.-С. 36−38.
- Гребенников, А. В. Поверхностное упрочнение штамповой оснастки газопламенной закалкой / А. В. Гребенников, Е. М. Черников // Кузнечно-штамповочное производство. Обработка материалов давлением. -2007.-№ ю.-С. 24−27.
- Тимченко, А. И. Профильные бесшпоночные соединения с равноосным контуром, их достоинства, недостатки, область применения и этапы внедрения / А. И. Тимченко // Вестник машиностроения. 1990. — № 11. -С. 43−50.
- Тимченко, А. И. Профильные соединения валов и втулок в машиностроении / А. И. Тимченко // Вестник машиностроения. 1981. — № 1. -С. 33−37
- Зенин, В. Технологические методы формообразования поверхностей бесшпоночных соединений / В. Зенин, М. С. Камсюк // Сборка в машиностроении, приборостроении. 2005. — № 9. — С. 35−40.
- Берникер, Е. И. Посадки с натягом в машиностроении / Е. И. Берникер. M.-J1.: Машиностроение, 1966. — 167 с.
- Монченко, В. П. Эффективная технология производства полых цилиндров / В. П. Монченко. М.: Машиностроение, 1980. — 248 с.
- Пинегин, С. В. Контактная прочность и сопротивление качению / С. В. Пинегин. -М.: Машиностроение, 1969. 244 с.
- Григорьева, О. А. Технологическое обеспечение прочности профильных неподвижных соединений упругопластическим деформированием элементов соединения : дис.. канд. техн. наук: 01.02.06 / О. А. Григорьева. -Омск: ОмГТУ, 2004. 138 с.
- Напалков, А. В. Рифление как один из элементов крепежных деталей Электронный ресурс. URL: http://www.nav.t-k.ru/ (дата обращения: 12.10.2010).
- Напалков, А. В. Опыт холодновысадочного производства болтов Электронный ресурс. URL: http://www.nav.t-k.ru/ (дата обращения: 12.10.2010).
- Андреев, Г. Я. Тепловая сборка колесных пар / Г. Я. Андреев. -Харьков: Изд-во Харьковского университета, 1965. 227 с.
- A.c. 1 773 663 СССР МКИ5 В 23 Р 19/02. Способ термического соединения с натягом охватываемой и охватывающей деталей / И. JI. Оборский, А. И. Бибиков, И. А. Казанцев и др. // Открытия. Изобретения. 1992. — № 41.
- Дука, А. К. Расчет теплового режима составных соединений, собираемых с нагревом / А. К. Дука, Б. М. Арпентьев // Известия вузов. М.: Машиностроение, 1989. — С. 68−73.
- Технологическое обеспечение точности сборки соединений с натягом, осуществляемым с термовоздействием / А. К. Зенкин и др. // Вестник машиностроения. 1988. — № 10. — С. 43−45.
- Зенкин, А. С. Оценка и прогнозирование напряженно-деформированного состояния соединений с натягом при термических методах сборки / А. К. Зенкин, Н. А. Зубрецкая // Сборка в машиностроении, приборостроении. 2003. — № 6. — С. 9−12.
- Резниченко, Н. К. Качество сборки соединений с натягом при использовании нагрева / Н. К. Резниченко, А. К. Дука // Сборка в машиностроении, приборостроении. 2005. -№ 8. — С. 34−37.
- Новиков, М. П. Основы технологии сборки машин и механизмов / М. П. Новиков. М.: Машиностроение, 1980. — 592 с.
- Зенкин, А. С. Расчет технологически-сборочных параметров при формировании соединений с натягом с использованием глубокого холода / А. С. Зенкин, О. В. Лабутина, В. Н. Павленко // Сборка в машиностроении, приборостроении. 2001. — № 10.-С. 7−11.
- Зенкин, А. С. Сборка неподвижных соединений термическими методами / А. С. Зенкин, Б. М. Арпентьев. М.: Машиностроение, 1987. -128 с.
- Холодкова, А. Г. Особенности выполнения цилиндрических соединений с натягом комбинированным клеетепловым методом / А. Г. Холодкова, Д. В. Князев // Сборка в машиностроении, приборостроении. -2005,-№ 4.-С. 18−20.
- Акименко, Ю. А. Исследование процесса дорнования отверстий тонкостенных деталей в обойме : автореф. дис.. канд. техн. наук / Ю. А. Акименко. Брянск: Брянский политехнический институт, 1975. — 26 с.
- А. с. 1 488 176 СССР, МКИ4 В 23 Р 11/02. Способ соединения охватываемой и охватывающей деталей / В. А. Беляев, С. С. Комаров, В. Н. Голубев и др. // Открытия. Изобретения. 1989. — № 23.
- Детинко, Ф. М. Посадка короткой втулки на цилиндрическую оболочку / Ф. М. Детинко, В. М. Фастовский // Вестник машиностроения. -1967. -№ 7.-С. 42−45.
- Гречишный, И. Г. Об образовании неразъемного соединения магнитно-импульсным способом / И. Г. Гречишный // Самолетостроение и техника воздушного флота: респ. межвед. науч.-техн. сб. Вып. 18. Харьков, 1970. — С. 113−117.
- Заявка 4 134 552 ФРГ, МКИ5 Fl6 Н57/00. Прессовое шлицевое соединение Ritzel-Befestung bei insbesondere Planetengetrieben/Orlowski Bernhard.
- Повышение эффективности сборки прессовых соединений путем применения ультразвука / Б. Л. Штриков и др. // Сборка в машиностроении, приборостроении. 2002. — № 8. — С. 2−6.
- Николаев, В. А. Ультразвуковая запрессовка деталей /
- B. А. Николаев, Б. Л. Штриков // Вестник машиностроения. 1994. — № 8.1. C. 24−26.
- Штриков, Б. Л. Информационно-технологическое обеспечение эксплуатационных свойств прессовых соединений при ультразвуковой сборке / Б. Л. Штриков, В. Г. Шуваев // Сборка в машиностроении, приборостроении. -2004.-№ 11.-С. 34−36.
- Штриков, Б. Л. Физико-технологические особенности ультразвуковой сборки / Б. Л. Штриков // Сборка в машиностроении, приборостроении. -2002.-№ 1.-С. 14−20.
- Шуваев В. Г. Формирование прессовых соединений гарантированного качества при ультразвуковой сборке / В. Г. Шуваев // Сборка в машиностроении, приборостроении. 2004. — № 10. — С. 28−31.
- Масягин, В. Б. Исследование прочности профильных неподвижных неразъемных соединений : дис. канд. техн. наук: 01.02.06 / В. Б. Масягин. -Омск: ОмГТУ, 1999. 288 с.
- Навроцкий, Г. А. Высадочные и обрезные прессы-автоматы / Г. А. Навроцкий. М.: МАШГИЗ, 1949. — 254 с.
- Попов, В. А. Оснастка автоматизированного холодновысадочного производства / В. А. Попов. М.: Машиностроение, 1965. — 175 с.
- Навроцкий, Г. А. Технология объемной штамповки на автоматах / Г. А. Навроцкий, Ю. А. Миропольский, В. В. Лебедев. М.: Машиностроение, 1972.-96 с.
- Новиков, М. П. Основы технологии сборки машин и механизмов / М. П. Новиков. М.: Машиностроение, 1969. — 632 с.
- Зенкевич, О. Метод конечных элементов в технике / О. Зенкевич — под ред Б. Е. Победря. М.: Мир, 1975.-271 с.
- Норри, Д. Введение в метод конечных элементов / Д. Норри — пер. с англ.-М.: Мир, 1981.-304 с.
- Сегерлинд, JI. Применение метода конечных элементов / Л. Сегерлинд — под ред Б. Е. Победря. М.: Мир, 1975. — 392 с.
- Математическая энциклопедия / Под ред. И. М. Виноградова. М.: Советская энциклопедия, 1985. — 1248 с.
- Шалашилин, В. И. Метод продолжения решения по параметру и наилучшая параметритизация (в прикладной математике и механике) /
- B. И. Шалашилин, Е. Б. Кузнецов. М.: Эдиториал УРСС, 1999. — 224 с.
- Роботнов, Ю. Н. Механика деформируемого твердого тела : учеб. пособие для вузов / Ю Н. Роботнов. 2-е изд., испр. — М.: Наука, 1988. — 712 с.
- Грязнов, Б. Т. Технологические методы улучшения эксплуатационных свойств деталей машин криогенной и микрокриогенной техники / Б. Т. Грязнов. Новосибирск: Наука — Сибирская издательская фирма, 1993.-208 с.
- Тетельбаум, Д. И. Эффект дальнодействия / Д. И. Тетельбаум, В. Я. Баянкин // Природа. 2005. — № 4. — С. 9−17.
- Шаркеев, Ю. П. Эффект дальнодействия в ионно-имплантированных металлических материалах: дислокационные структуры, свойства, напряжения, механизмы: дис. д-ра физ.-мат. наук / Ю. П. Шаркеев. -Томск, 2000. 425 с.
- Чуранкин, В. Г. Комплексная технология улучшения физико-механических свойств поверхностей деталей ионной имплантацией с предварительным накатыванием / В. Г. Чуранкин. Омск, 2010. — 162 с.
- Моргунов, А. П. Технологическое обеспечение прочности профильных неподвижных соединений накатыванием / А. П. Моргунов // Механика процессов и машин: сб. науч. тр. Омск, 2000. — С. 27−29.
- Моргунов, А. П. Исследование напряженно-деформированного состояния цилиндрического кольца при внутреннем последовательном нагружении / А. П. Моргунов, В. Б. Масягин. Омск, 1994. — 7 с.
- Моргунов, А. П., Масягин В. Б. Исследование остаточных деформаций деталей профильного неподвижного соединения при сборке дорнованием. Омск 1995. — 4 с. — Деп. в ВИНИТИ.
- Моргунов, А. П. Исследование упругопластических деформаций цилиндрического кольца при внутреннем последовательном нагружении / А. П. Моргунов, В. Б. Масягин. Омск, 1995. -7 с.
- Пространственная динамическая модель установки для вибрационного накатывания / А. П. Моргунов и др. // Анализ и синтез механических систем: сб. науч. тр. / ОмГТУ. Омск, 2006. — С. 95−110.
- Вейбулл, В. Усталостные испытания и анализ их результатов / В. Вейбулл. М.: Высш. Школа, 1966. — 276 с.
- Форрест, П. Усталость материалов / П. Форрест. М.: Машиностроение, 1968. -352 с.
- Ефремов В. В. Теория и практические вопросы работоспособности элементов машин, приборов и аппаратуры / В. В. Ефремов, В. А. Наумов, А. А. Чурсин. Иркутск.: Издательство Иркутского университета, 1984. — 220 с.
- Гухман, А. А. Введение в теории подобия / А. А. Гухман. М.: Высшая школа, 1973. — 296 с.
- Иосилсвич, Г. Б. Детали машин / Г. Б. Иоселевич. М.: Машиностроение, 1988.-368 с. — ISBN 5−217−217−4.
- Материал из Википедии — свободной энциклопедии Электронный ресурс. Режим доступа: http://m.wikipedia.org/wiki/TBOpflbiecmiaBbi (дата обращения: 21.12.2010).
- Инструментальные твёрдые сплавы Электронный ресурс. Режим доступа: http://www.rostprom.com/spravochniki/stali3.html (дата обращения: 21.12.2010).
- Лейкин, А. Е. Авиационное материаловедение / А. Е. Лейкин, Э. С. Пороцкий, Б. И. Родин. М.: Машиностроение, 1964. — 459 с.
- Колчин, О. П. Твёрдые сплавы Электронный ресурс. Режим доступа: http://bse.sci-lib.com/articlel09304.html (дата: обращения 21.12.2010).
- Твердые металлокерамичеекие сплавы Электронный ресурс. -Режим доступа: http://www.info. instrumentmr.ru/instrummaterial. БЬйтШ^егс! (дата обращения: 21.12.2010).
- Машиностроительные материалы. Твердые сплавы и минералокерамические Электронный ресурс. Режим доступа: http://bibliotekar.ru/slesar/16.htm (дата обращения: 21.12.2010).
- Инструментальные твёрдые сплавы Электронный ресурс. Режим доступа: http://www.rostprom.com/spravochniki/stali3.html (дата обращения: 21.12.2010).